PROK Rollers: Top Innovations in Conveyor Technology
PROK is globally recognized as a leading brand in conveyor solutions, renowned for its innovative approach and superior quality. The brand specializes in designing and manufacturing PROK Rollers, which are essential components in various industrial conveyor systems. With a robust global presence, PROK has solidified its reputation by delivering reliable and durable products tailored to meet the diverse needs of industries worldwide. Particularly in the Australian market, PROK’s commitment to excellence is evident through their rigorous quality control processes and dedication to customer satisfaction. This dedication ensures that PROK Rollers not only meet but often exceed the stringent demands of both local and international clients, making them a top choice in the industry.
The Importance of Reliable PROK Rollers
The role of reliable conveyor rollers in optimizing the performance of conveyor systems cannot be overstated. Rollers are pivotal in ensuring smooth operations, minimizing downtime, and extending the lifespan of the entire system. PROK Rollers are at the forefront of this, offering solutions that embody durability and efficiency.
- Load Support: PROK Rollers provide sturdy support for loaded belts, reducing the belt wear and tear and ensuring that materials are transported smoothly and without interruptions.
- Energy Efficiency: By reducing friction and improving rollability, PROK Rollers contribute to lower energy consumption, which is crucial for cost-effective operations and environmental sustainability.
- System Longevity: The use of high-quality materials and precise engineering in PROK Rollers enhances the overall durability of conveyor systems, decreasing the need for frequent repairs or replacements.
- Operational Reliability: In critical industrial applications, such as mining and bulk handling, the reliability of PROK Rollers ensures continuous operation, which is essential to maintaining productivity and meeting production targets.
PROK’s commitment to innovation and performance in developing top-tier rollers is evident through their continuous improvement and adaptation to industry needs.
- Material Innovation: PROK Rollers are made from advanced materials like HDPE and reinforced composites, which offer superior wear resistance and lower noise levels.
- Customized Solutions: Understanding that different industries have unique needs, PROK offers customized rollers designed to meet specific operational requirements, enhancing system efficiency.
- Technological Integration: PROK integrates the latest technology in the manufacturing process of their rollers, ensuring precision and consistency in every product.
- Global Standards: PROK Rollers are developed in compliance with international quality and safety standards, ensuring they can be integrated into systems worldwide with utmost reliability.
These initiatives reflect PROK’s dedication to maintaining its position as a leader in the field, constantly pushing the boundaries to improve the utility and effectiveness of their conveyor rollers.
The Diverse Range of PROK Rollers
PROK’s extensive catalog of conveyor rollers is a testament to their innovation and commitment to catering to a wide array of industrial requirements. This section delves into the varied lineup of PROK Rollers, showcasing the technological and material advancements that define their market leadership.
Innovations in Roller Design
PROK has developed a versatile range of conveyor rollers to suit different environments and operational demands. The array includes Low Noise Aluminium, Hybrid Steel, High-Density Polyethylene (HDPE), Polyurethane (PU) Disc, Steel, Rubber Disc, and Formed Steel Rollers. Each type is engineered to optimize performance and durability:
- Low Noise Aluminium Rollers are designed for operations where noise reduction is critical.
- Hybrid Steel Rollers offer a balance of strength and lightweight properties for energy efficiency.
- HDPE Rollers excel in environments where corrosion resistance and lower weight are beneficial.
- PU Disc and Rubber Disc Rollers provide enhanced grip and noise reduction on conveyor belts.
- Formed Steel Rollers are tailored for high-load capacities in industrial applications.
Material Advancements
The selection of materials in the manufacturing of PROK Rollers is critical to their performance. Here are four examples illustrating the benefits of these materials:
- High-Density Polyethylene (HDPE): Used in rollers for its excellent corrosion resistance and low weight, which help extend the life of the conveyor system.
- Polyurethane (PU): Employed especially in the disc rollers for its wear resistance and ability to reduce noise, making it ideal for operations in quiet environments.
- Rubber: Chosen for its natural shock absorbance and noise reduction capabilities, rubber is used in disc rollers for handling fragile materials.
- Steel: Known for its strength and durability, steel is used in various roller types to support heavy loads and withstand harsh operational conditions.
Specialized Rollers for Enhanced Functionality
In addition to standard rollers, PROK also offers specialized rollers designed to fulfill specific functions within conveyor systems:
- Weigh Rollers: These are integrated into weighing systems on the conveyor lines, enabling precise monitoring of production output without interrupting the flow of materials.
- Impact Rollers: Positioned at load zones to absorb the shock and impact from falling materials, these rollers are crucial for protecting the belt and structure of the conveyor system.
The diverse range of PROK Rollers reflects the company’s innovative approach to solving the myriad challenges faced by industries relying on conveyor systems. This versatility not only enhances the functionality of conveyors but also improves operational efficiency and safety across various sectors.
Evaluating PROK Rollers’s Idler Solutions
PROK Rollers’ excellence extends into their comprehensive range of idler solutions, which play a crucial role in enhancing the efficiency and longevity of conveyor systems. This section provides a detailed examination of PROK’s idler offerings and highlights the key considerations for selecting the appropriate idler types and dimensions to meet specific industrial requirements.
Insights into the PROK Idler Catalogue
The PROK idler catalogue is diverse, featuring a variety of idlers designed to accommodate different operational challenges across various industries. Selecting the right idler involves understanding the unique demands of each application—whether it’s handling heavy loads, operating in extreme environmental conditions, or requiring minimal maintenance. PROK’s expertise in engineering and innovation ensures that each idler solution enhances conveyor system reliability and efficiency.
The Importance of Considering Idler Dimensions
Choosing the correct idler dimensions is paramount for ensuring system compatibility and achieving optimal performance.
- Load Distribution: Proper idler spacing and sizing ensure that loads are evenly distributed across the conveyor belt, which minimizes wear and tear and extends the belt’s life.
- Belt Alignment: The right idler dimensions help maintain proper belt alignment, reducing the risk of belt slippage and misalignment that could lead to operational disruptions and increased maintenance costs.
- Energy Efficiency: Appropriately sized idlers reduce the conveyor system’s energy consumption by minimizing friction and resistance, which is particularly crucial in long-distance conveyor applications.
- Handling Capabilities: Specific idler types and sizes are designed to enhance the conveyor’s handling capabilities, such as impact idlers placed at loading zones to absorb shocks and support idlers that aid in maintaining a stable belt profile.
Through the meticulous design and manufacturing of PROK Rollers and idlers, PROK ensures that every component contributes to a system’s overall performance and durability. This commitment is evident in their tailored solutions, which meet the nuanced needs of diverse industries, thereby reinforcing system compatibility and enhancing operational efficiency.
PROK Rollers’s Engineering and Technical Services
PROK’s commitment to excellence in the conveyor industry extends beyond the manufacture of PROK Rollers and idlers. Their engineering and technical services are pivotal in supporting clients through advanced technical expertise and tailored optimization solutions, ensuring that conveyor systems operate at peak efficiency and longevity.
Engineering Services
PROK’s engineering services are designed to provide comprehensive support to customers, helping them maximize the performance and reliability of their conveyor systems. By leveraging PROK’s deep technical expertise, customers gain access to a range of services including system design consultation, performance analysis, and custom solution development. These services ensure that each aspect of the conveyor system, from the PROK Rollers to the control systems, is optimized for the specific operational conditions of the client’s industry. This not only enhances efficiency but also reduces downtime and maintenance costs.
Pulley Refurbishment
The benefits of PROK’s pulley refurbishment services are substantial, particularly in terms of extending the lifespan of conveyor equipment.
- Cost Efficiency: Refurbishing pulleys with PROK can be significantly more cost-effective than replacing them entirely. This service allows for the reuse of existing equipment, which can substantially lower capital expenditure.
- Reduced Downtime: By refurbishing pulleys, PROK ensures that the conveyor systems experience minimal downtime. This service is typically faster than replacing pulleys and can be scheduled during routine maintenance periods to further minimize operational disruption.
- Extended Equipment Life: PROK’s refurbishment services restore pulleys to their optimal condition, which can significantly extend their operational lifespan. This is achieved through the replacement of worn components, realignment, and balancing, all of which contribute to the overall health and efficiency of the conveyor system.
- Enhanced Performance: Refurbished pulleys often perform as well as new ones because PROK utilizes the latest materials and technologies in the refurbishment process. This not only ensures that the pulleys operate efficiently but also improves their suitability for the specific demands of different industrial environments.
Through their dedicated engineering and technical services, PROK provides an invaluable resource to industries relying on conveyor systems. Their approach not only focuses on maintaining and enhancing the performance of PROK Rollers and related components but also ensures that the entire system is optimized for both current and future needs.
Spotlight on PROK Rollers Mackay
PROK Mackay stands out as a critical hub within the expansive network of PROK’s facilities, specifically tailored to meet the robust demands of the conveyor industry with a strong focus on PROK Rollers. This facility not only manufactures essential components but also serves as a pivotal point for innovation and customer service in the region.
What is PROK Rollers Mackay
PROK Mackay is strategically located to cater to the burgeoning industrial needs of the mining and bulk handling sectors prevalent in the region. The facility is renowned for its expertise in producing high-quality PROK Rollers, and its role extends across various dimensions:
- Custom Manufacturing: PROK Mackay specializes in custom-made conveyor solutions, ensuring that each PROK Roller is tailored to meet the specific requirements of each application. This bespoke service is crucial for industries where standard solutions do not suffice.
- Rapid Response Services: Understanding the urgency of minimizing downtime in industrial operations, PROK Mackay offers rapid response services. This ensures that all conveyor system issues are addressed swiftly, reducing the potential for extended operational disruptions.
- Technical Support and Maintenance: Beyond manufacturing, PROK Mackay provides ongoing technical support and maintenance services. This comprehensive support helps customers optimize their conveyor systems and extend the lifespan of their PROK Rollers and other conveyor components.
- Training and Consultation: PROK Mackay also serves as a knowledge center, offering training sessions and consultation services. These programs are designed to help clients better understand their conveyor systems, enabling them to perform routine maintenance and troubleshoot minor issues, thus empowering them with the knowledge to maintain optimal operations.
Through these roles, PROK Mackay exemplifies PROK’s commitment to not just delivering high-quality products like PROK Rollers, but also to ensuring that these products continue to perform optimally through customer-focused services and support. This facility is a cornerstone in PROK’s strategy to lead and innovate within the conveyor industry, providing a local yet globally connected resource for all conveyor-related needs.
How to Choose the Right PROK Rollers
Selecting the right PROK Rollers is crucial for ensuring the efficiency, reliability, and longevity of conveyor systems. The process involves a comprehensive understanding of the specific requirements of the application, as well as the dimensions and capabilities of various PROK Rollers. Here’s a detailed guide to help you make the best choice:
Application Requirements
The first step in selecting the right PROK Rollers involves a thorough analysis of the application’s specific needs. Consider the following aspects:
- Load Requirements: Assess the weight and nature of the materials the conveyor will handle. Heavier loads might require robust steel rollers, whereas lighter or more sensitive materials might be better served by HDPE or rubber-coated rollers.
- Environmental Conditions: The operating environment is critical. For example, environments with high moisture or corrosive materials require rollers like PROK’s HDPE models that resist corrosion and wear.
- Speed of Conveyor: The speed at which the conveyor will operate can influence the type of roller needed. High-speed applications may need rollers designed to reduce vibration and noise, such as PROK’s low noise aluminium rollers.
- Maintenance Schedule: Consider how often maintenance can be performed. Some rollers, like those made from composite materials, offer longer life spans with less frequent maintenance needs.
Considering Idler Dimensions
The dimensions of the idlers play a significant role in the performance and compatibility of the rollers within the conveyor system. Key dimensional aspects to consider include:
- Diameter: The diameter of the rollers must be chosen based on the speed and the load of the conveyor. Larger diameters are typically used for higher load capacities and longer belt life.
- Length: The length of the roller should match the width of the belt to ensure proper support across its entire width.
- Bearing and Shaft Size: These should be selected based on the load and the operational speed. Properly sized bearings and shafts are crucial for the longevity and efficiency of the rollers.
- Spacing: The spacing between idlers affects the amount of sag in the conveyor belt between rollers. Optimal spacing helps in maintaining a stable belt and reduces material spillage.
Matching Rollers to Conveyor Specifications
Once the requirements and dimensions have been established, the next step is to match these specifications with the appropriate PROK Rollers. PROK offers a variety of rollers designed to meet different industrial needs, ensuring that whether you are dealing with high impact loads, abrasive conditions, or require low-maintenance solutions, there is a PROK Roller suitable for your application.
Choosing the right PROK Rollers involves careful consideration of the application’s specific requirements and the physical and operational characteristics of the rollers. By following this guide, you can ensure that your conveyor system operates efficiently, safely, and reliably with the optimal selection of PROK Rollers.
Enhancing Industrial Efficiency with PROK Rollers Conveyor Equipment
The efficiency and productivity of industrial operations are heavily influenced by the reliability and effectiveness of their conveyor systems. PROK Rollers and the broader range of PROK conveyor equipment are designed with these critical factors in mind, ensuring that industries benefit from improved operational capabilities and reduced downtime.
Key Contributions of PROK Conveyor Equipment
PROK’s comprehensive range of conveyor equipment, including their advanced rollers, idlers, and pulleys, plays a pivotal role in enhancing industrial efficiency. Here are the main ways in which PROK conveyor equipment contributes to this goal:
- Reduced Operational Downtime: PROK Rollers are engineered to require less maintenance, thereby reducing the frequency and duration of downtime needed for repairs and replacements. This reliability is crucial for industries where continuous operation is critical, such as mining, bulk materials handling, and manufacturing.
- Increased Conveyor Lifespan: The use of high-quality materials and precision engineering in PROK Rollers ensures that they last longer than standard rollers. This durability extends the life of the entire conveyor system, reducing the need for frequent overhaul and enabling consistent productivity over longer periods.
- Improved Material Handling: PROK Rollers are designed to provide smoother operations under various load conditions. This smooth operation minimizes material spillage and enhances the precision of material handling, critical for industries like agriculture and pharmaceuticals where precision is paramount.
- Energy Efficiency: PROK’s innovative designs include features that reduce the rolling resistance of conveyor belts, which in turn lowers energy consumption. Energy-efficient rollers not only cut operational costs but also contribute to a company’s sustainability goals.
- Customization for Specific Needs: Understanding that different industries have unique needs, PROK offers customized conveyor solutions that are tailored to meet specific operational requirements. This bespoke approach ensures that each component, from PROK Rollers to drive systems, is optimized for the best possible performance.
The Role of Technology and Innovation
PROK continuously invests in research and development to keep their conveyor equipment at the cutting edge of technology. Innovations such as sensor-equipped rollers that monitor system performance and health in real-time are examples of how PROK is leading the way in smart conveyor solutions. These technological advancements not only enhance the functionality of the conveyor equipment but also provide actionable data that can be used to further optimize operations and maintenance schedules.
The extensive range of PROK conveyor equipment, spearheaded by their reliable and efficient PROK Rollers, is fundamental to boosting industrial efficiency and productivity. Through superior design, technological innovation, and a focus on customer-specific solutions, PROK ensures that their equipment meets the highest standards of performance and reliability, driving forward the productivity of diverse industrial sectors.
PROK Rollers’s Global Manufacturing Facilities
PROK’s extensive network of global manufacturing facilities is pivotal in supporting both the local and international markets with high-quality conveyor components, such as PROK Rollers. These facilities enable PROK to deliver consistently superior products tailored to the specific needs of diverse industries around the world.
Worldwide Reach and Local Impact
PROK has strategically located its manufacturing facilities across various continents to effectively serve a global clientele while also catering to local market nuances. This geographical diversity not only ensures a rapid response to customer needs but also reduces delivery times and transportation costs. Here’s how PROK’s global manufacturing capabilities support markets worldwide:
- North America: In North America, PROK’s facilities focus on producing heavy-duty rollers and conveyor systems that cater to the robust mining and bulk material handling sectors prevalent in this region.
- Australia and Asia-Pacific: In Australia, where PROK is headquartered, the facilities are renowned for innovation in conveyor technology, developing some of the most advanced PROK Rollers. The proximity to the Asia-Pacific region also facilitates the servicing of emerging markets that are rapidly industrializing and requiring efficient material handling solutions.
- Europe: European facilities adapt PROK’s offerings to meet stringent EU regulations and standards, focusing on sustainability and energy efficiency, which are critical to the European market.
- South America: In South America, PROK’s facilities are equipped to deal with the demands of local mining giants, providing durable and efficient conveyor rollers that withstand harsh operational conditions.
Technological Integration
Each of PROK’s facilities is equipped with state-of-the-art manufacturing technology, ensuring that all PROK Rollers and other conveyor components are produced to the highest standards. Advanced robotics, automation, and precision engineering are integral to PROK’s manufacturing processes, enhancing product quality and consistency across all locations.
Supporting Local and Global Supply Chains
By maintaining a presence in key industrial regions around the world, PROK ensures a resilient supply chain that is less susceptible to regional disruptions. This global footprint not only supports local economies by providing jobs and utilizing local resources but also enhances the flexibility and scalability of PROK’s production capabilities.
Commitment to Quality and Innovation
PROK’s global manufacturing facilities are united by a common commitment to quality and continuous improvement. Regular audits, shared best practices, and a global quality management system ensure that regardless of where a PROK Roller is made, it upholds the company’s high standards. This commitment extends to environmental stewardship, with facilities increasingly focusing on reducing their carbon footprint and enhancing sustainability practices.
PROK’s global manufacturing facilities are crucial in supporting the widespread demand for PROK Rollers, providing tailored solutions that meet both local and international needs. This strategic positioning not only streamlines operations and enhances service delivery but also supports PROK’s vision of being a leader in conveyor technology on a global scale.
FAQs About PROK Rollers
Rollers on a conveyor are cylindrical components that rotate to facilitate the movement of the conveyor belt or directly support and move the material being transported. These rollers are mounted on the conveyor’s frame and are an essential part of the conveyor system. There are various types of rollers used in conveyor systems, each designed for specific purposes. Standard types include drive rollers, which are motorized to drive the conveyor belt, and idler rollers, which support the belt and materials passively. Rollers are typically made from metal, plastic, or rubber, depending on the application and environmental factors like load, speed, and conditions under which the conveyor will operate. Their design and quality play a crucial role in the conveyor’s efficiency, the maintenance frequency, and the system’s overall longevity.
The primary function of a roller conveyor is to transport goods across a defined pathway within a facility. Roller conveyors are widely used in various industries such as manufacturing, warehousing, and distribution. They are especially useful for handling items that are solid and rigid, like boxes, trays, or pallets. Roller conveyors facilitate the movement of these items by reducing friction, which makes it easier and more efficient to move heavy or large items over long distances. Additionally, roller conveyors can be customized with different roller sizes, materials, and spacing to handle different types of products and loads effectively. They can also be equipped with motors and sensors to automate the transport process and integrate with other automated systems within a facility.
The spacing of conveyor rollers is critical to the conveyor system’s design and efficiency. It is determined based on the size and weight of the items being transported, as well as the type of conveyor belt used. Proper roller spacing helps in achieving optimal balance and load distribution, minimizing the belt wear and the stress on the conveyor frame. Generally, the spacing is such that the largest product being transported on the conveyor can safely span three rollers. This setup ensures that the product is always in contact with at least two rollers, which helps in maintaining stability and control. Incorrect spacing can lead to material sagging between rollers, increased wear and tear on the conveyor belt, and even potential damage to the products being moved. Engineers and designers calculate the ideal roller spacing during the conveyor design phase to ensure system effectiveness and durability.
An idler roller conveyor is a type of conveyor that uses a series of non-driven rollers to support and move materials along a pathway. These rollers are called idler rollers because they do not drive the conveyor belt but instead are positioned strategically to maintain the tension and alignment of the belt. Idler roller conveyors are used extensively in bulk material handling applications, such as in mining, agriculture, and aggregate industries, where they help to convey large volumes of materials efficiently. The simplicity of the idler roller design contributes to the system’s durability and ease of maintenance. Furthermore, idler rollers can be spaced and configured according to specific operational requirements to optimize the performance and longevity of the conveyor system.
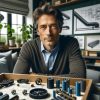
Jordan Smith, a seasoned professional with over 20 years of experience in the conveyor system industry. Jordan’s expertise lies in providing comprehensive solutions for conveyor rollers, belts, and accessories, catering to a wide range of industrial needs. From initial design and configuration to installation and meticulous troubleshooting, Jordan is adept at handling all aspects of conveyor system management. Whether you’re looking to upgrade your production line with efficient conveyor belts, require custom conveyor rollers for specific operations, or need expert advice on selecting the right conveyor accessories for your facility, Jordan is your reliable consultant. For any inquiries or assistance with conveyor system optimization, Jordan is available to share his wealth of knowledge and experience. Feel free to reach out at any time for professional guidance on all matters related to conveyor rollers, belts, and accessories.