Conveyor Roller Bearing Replacement for Conveyor Systems | Essential Tips
Conveyor roller bearings play a pivotal role in the seamless operation of industrial conveyor systems, ensuring smooth and efficient movement of goods across various sectors. These bearings are fundamental components that reduce friction between the moving parts of a conveyor, facilitating the transport of heavy loads with minimal effort. However, like all mechanical components, conveyor roller bearings are subject to wear and tear, leading to potential breakdowns and operational disruptions. Common issues that necessitate conveyor roller bearing replacement include excessive noise, decreased mobility, and visible damage or wear. Addressing these problems promptly is crucial to maintaining the productivity and safety of industrial operations, highlighting the importance of timely conveyor roller bearing replacement.
What is Conveyor Roller Bearing Replacement
Conveyor systems are the backbone of many industrial operations, and the efficiency of these systems heavily relies on the performance of conveyor roller bearings. Understanding the nuances of conveyor roller bearing replacement is essential for maintaining the longevity and effectiveness of conveyor systems. This section delves into the types of roller bearings used in conveyors, compares roller and belt conveyors, and discusses the differences between sliding and roller bearings.
Types of Roller Bearings Used in Conveyors
Type | Description | Applications |
---|---|---|
Cylindrical | Feature straight rollers, offering high radial load capacity but limited thrust load capacity. | General conveyor operations, moderate speeds. |
Spherical | Self-aligning bearings with barrel-shaped rollers, accommodating misalignments. | Heavy loads, prone to shaft misalignment. |
Tapered | Conical rollers and raceways arranged so that the rollers converge at the bearing axis. | High radial and axial loads, impact loads. |
Needle | Long, thin rollers offering a high load capacity relative to their size. | Compact spaces, high load, low speed. |
Thrust | Designed to handle primarily axial loads, with little to no radial load capacity. | Vertical shafts, low-speed, high-thrust loads. |
Understanding these types is crucial for effective conveyor roller bearing replacement, ensuring the right bearing type is selected for specific conveyor applications.
Types of Conveyor Roller Bearings for Conveyor Roller Bearing Replacement
When it comes to conveyor roller bearing replacement, understanding the types of bearings available is crucial. Different applications require specific types of bearings to ensure optimal performance and longevity. Here are the key types of conveyor roller bearings commonly used:
Heavy Duty Conveyor Roller Bearings
Heavy duty conveyor roller bearings are specifically designed for applications that involve high loads and rigorous conditions. These bearings are built to withstand the stress and strain of heavy-duty operations, making them ideal for industries such as mining, construction, and manufacturing.
- Designed for High-Load Applications
Heavy duty bearings are engineered to handle substantial weight and force, which is essential in environments where conveyors must move large or heavy items continuously. The robust construction ensures that these bearings can operate efficiently under extreme conditions without frequent failures. - Examples and Typical Usage Scenarios
Examples of heavy duty conveyor roller bearings include spherical roller bearings and cylindrical roller bearings. These bearings are often used in conveyor systems for bulk material handling, such as those found in aggregate processing plants, steel mills, and cargo handling terminals. The ability to support significant loads and resist impact makes them suitable for these demanding applications.
Tapered Conveyor Rollers
Tapered conveyor rollers feature bearings that are designed to manage both radial and axial loads. This dual capability makes them highly versatile and beneficial for a wide range of industrial applications.
- Advantages in Handling Both Radial and Axial Loads
The tapered design allows these bearings to accommodate radial loads, which act perpendicular to the shaft, as well as axial loads, which act parallel to the shaft. This makes tapered roller bearings exceptionally stable and capable of handling complex load conditions that would be challenging for other bearing types. - Specific Applications and Benefits
Tapered conveyor rollers are commonly used in applications where both thrust and radial load capacities are necessary. Typical uses include conveyor systems in the automotive industry, where components must move precisely along the production line, and in agricultural equipment, where durability and load handling are critical. The benefits of using tapered rollers include enhanced stability, reduced wear, and longer service life, contributing to fewer interruptions and maintenance needs in conveyor roller replacement cycles.
By selecting the appropriate type of bearing for your conveyor system, you can ensure smoother operation, reduced maintenance costs, and increased efficiency. Whether it’s heavy duty conveyor roller bearings for high-load environments or tapered rollers for applications requiring stability and versatility, understanding these options is key to effective conveyor roller bearing replacement.
Roller vs. Belt Conveyors: Pros and Cons
Roller Conveyors:
- Pros:
- High load capacity.
- Suitable for a wide range of materials.
- Minimal maintenance required.
- Easy to install and reconfigure.
- Efficient for accumulation and sorting.
- Durable and long-lasting.
- Can operate in various environmental conditions.
- Cons:
- Higher initial investment.
- Limited to certain product shapes and sizes.
- Noise levels can be higher.
- Requires more space.
- Less flexible in terms of conveyor path.
- Energy consumption can be higher.
- Not suitable for very small or delicate items.
Belt Conveyors:
- Pros:
- Versatile for different materials and shapes.
- Quieter operation.
- Can transport materials over long distances.
- Flexible in terms of conveyor path and inclination.
- Lower initial cost.
- Suitable for small and delicate items.
- Can be enclosed to protect materials.
- Cons:
- Lower load capacity.
- Regular maintenance of the belt is required.
- Susceptible to wear and tear.
- Materials can stick to the belt.
- Limited by belt material in harsh environments.
- Can be affected by wind if outdoors.
- Requires tensioning and tracking adjustments.
Sliding Bearing vs. Roller Bearing: Differences and Applications
Sliding Bearings:
- Differences:
- Operate on the principle of sliding motion.
- Generally simpler and cheaper.
- Higher friction compared to roller bearings.
- Can operate without lubrication (self-lubricating materials).
- Suitable for high-load, low-speed applications.
- Less sensitive to contamination.
- Can accommodate misalignment.
- Applications:
- Heavy machinery and construction equipment.
- Hydraulic cylinders.
- Automotive suspension systems.
- Bridge supports.
- Elevators and escalators.
- Telescopic guides.
- Solar tracking systems.
Roller Bearings:
- Differences:
- Utilize rolling elements to reduce friction.
- Higher precision and efficiency.
- Require lubrication for smooth operation.
- Better suited for high-speed applications.
- More sensitive to contamination.
- Higher radial and axial load capacities.
- More complex designs.
- Applications:
- Conveyor systems.
- Electric motors and generators.
- Aerospace applications.
- Automotive wheel and transmission systems.
- Industrial gearboxes.
- Wind turbines.
- Robotics and automation equipment.
In the context of conveyor roller bearing replacement, understanding these distinctions is vital for selecting the appropriate bearing type, ensuring optimal performance and longevity of the conveyor system.
Signs You Need Conveyor Roller Bearing Replacement
Recognizing the early signs of bearing failure is crucial in conveyor systems to prevent prolonged downtime and ensure operational safety. Here are key indicators that it might be time for conveyor roller bearing replacement:
- Common Causes and Effects on System Efficiency
The noise and vibration typically stem from factors such as insufficient lubrication, contamination by dust and debris, or physical damage to the bearing components. This excessive noise and vibration not only disrupts the work environment but also indicates that the bearings are not operating efficiently. Inefficient bearings can lead to increased energy consumption and put additional strain on the conveyor system, ultimately reducing its overall performance and lifespan. - Identifying Physical Signs of Deterioration
Look for signs such as cracks, pitting, or flaking on the bearing surfaces. Additionally, check for deformation or discoloration of the bearing housing. These signs suggest that the bearings have been subjected to excessive loads or inadequate maintenance. Regular visual inspections can help catch these issues early before they lead to more significant problems, such as complete bearing failure or damage to other conveyor components. - Impact on Conveyor Belt Speed and Functionality
You might notice that the conveyor belt is moving slower than usual or experiencing irregular motion. This can be due to increased friction and resistance caused by worn bearings. In severe cases, the belt may even become stuck or jammed, leading to production delays and potential damage to the conveyed materials. Ensuring that bearings are in good working order is essential for maintaining the smooth operation and optimal performance of the conveyor system.
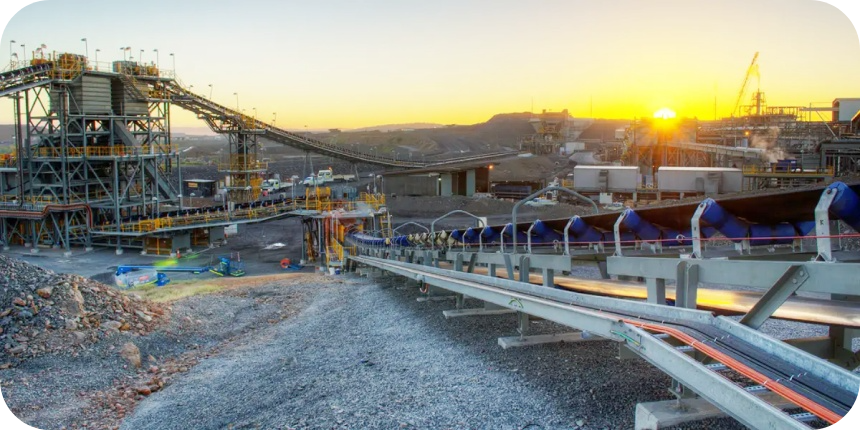
Symptoms of Bearing Failure in Conveyor Systems
- Unusual Noises: Grinding, squealing, or screeching noises from the conveyor indicate bearing issues.
- Visible Wear or Damage: Signs of wear, such as scratches or indentations on the bearing surface, suggest replacement is needed.
- Increased Vibration: Excessive vibration in the conveyor system often points to bearing failure.
- Heat Generation: Overheating bearings can be a clear sign of malfunction due to friction.
- Slowed Operation: A noticeable decrease in conveyor speed may be attributed to bearing degradation.
- Irregular Movement: Jerky or uneven roller movements can indicate bearing issues.
- Seized Rollers: Rollers that refuse to turn might have completely failed bearings.
- Contaminant Intrusion: The presence of contaminants like dirt or water around the bearing area can lead to premature failure.
Impacts of Worn-Out Bearings on Conveyor Efficiency and Safety
- Reduced Efficiency: Worn-out bearings can significantly slow down production lines, affecting overall efficiency.
- Increased Maintenance Costs: Frequent breakdowns due to bearing failures lead to higher maintenance and repair costs.
- Product Damage: Malfunctioning conveyors can cause damage to the products being transported.
- Safety Hazards: Failed bearings can pose serious safety risks to operators, including potential accidents from sudden stops or malfunctions.
- Energy Waste: Inefficient bearing operation requires more energy to maintain normal conveyor speeds, leading to increased operational costs.
- Operational Downtime: Replacing failed bearings can result in significant downtime, affecting delivery schedules and productivity.
- Premature Wear of Other Components: Faulty bearings can cause undue stress on other conveyor components, leading to their accelerated wear.
- Compliance Issues: In some industries, failing to maintain equipment such as conveyors can lead to regulatory compliance issues.
Identifying these symptoms early and undertaking timely conveyor roller bearing replacement can mitigate these impacts, ensuring the conveyor system operates smoothly, efficiently, and safely.

Replacement Kits and Parts for Conveyor Roller Bearing Replacement
When undertaking a conveyor roller bearing replacement, having the right tools and components is essential for a smooth and efficient process. Here’s a detailed look at replacement kits and parts for conveyor roller bearing replacement:
Conveyor Roller Bearing Replacement Kits
Replacement kits are designed to provide all the necessary components and tools required for a conveyor roller bearing replacement. These kits are convenient and ensure that you have everything needed for a successful installation.
- Overview of What’s Included in a Typical Kit
A standard conveyor roller bearing replacement kit typically includes: - Bearings: The primary components to be replaced, usually pre-lubricated and ready for installation.
- Bearing housings: New housings that fit the bearings perfectly, ensuring stability and proper alignment.
- Seals and gaskets: To prevent contamination and ensure smooth operation.
- Installation tools: Specialized tools such as pullers, presses, and alignment tools that facilitate the replacement process.
- Instruction manual: A detailed guide on how to perform the replacement, including safety precautions and step-by-step instructions.
- Benefits of Using Kits for Streamlined Replacement
Using a replacement kit offers several advantages: - Convenience: All necessary components are included, eliminating the need to source parts individually.
- Compatibility: Parts in the kit are designed to work together, ensuring a perfect fit and reducing the risk of installation errors.
- Time-saving: Kits streamline the replacement process, allowing for quicker and more efficient maintenance.
- Cost-effective: Purchasing a complete kit can often be more economical than buying each part separately.
Sourcing Replacement Parts
If you prefer to source parts individually rather than using a complete kit, it’s important to ensure the quality and compatibility of each component. Here are some tips for finding quality parts locally and online:
Tips for Finding Quality Parts Locally and Online
- Research Suppliers: Look for reputable suppliers with positive reviews and a track record of providing high-quality parts.
- Check Specifications: Ensure that the parts meet the required specifications for your specific conveyor system. This includes checking dimensions, load ratings, and material quality.
- Ask for Recommendations: Consult with industry professionals or colleagues to get recommendations on reliable suppliers and brands.
- Verify Warranty and Support: Choose suppliers that offer warranties and customer support to address any issues that may arise during the replacement process.
Recommended Suppliers and Brands for Reliable Replacements - Some well-known suppliers and brands that provide high-quality conveyor roller bearing replacement parts include:
- McMaster-Carr: Known for their extensive catalog and reliable products, McMaster-Carr offers a wide range of bearings and related components.
- Grainger: A trusted name in industrial supply, Grainger provides various bearing types and replacement parts suitable for different conveyor systems.
- SKF: A leading global manufacturer of bearings, SKF offers high-quality bearings known for their durability and performance.
- Timken: Renowned for their robust and reliable bearings, Timken provides products designed to withstand heavy loads and harsh environments.
- Ashland Conveyor: Specializes in conveyor components, including a variety of bearings and replacement parts tailored for different conveyor applications.
By using conveyor roller bearing replacement kits or sourcing quality parts from reputable suppliers, you can ensure a successful and efficient bearing replacement process. This not only maintains the smooth operation of your conveyor system but also extends its lifespan and reduces downtime.

Conveyor Roller Bearing Replacement Cost
Understanding the factors that influence the cost of conveyor roller bearing replacement is essential for effective budgeting and cost management. This section will explore the various elements that can affect replacement costs and provide practical tips for managing these expenses efficiently.
Factors Influencing the Cost of Bearing Replacement
- Type of Bearing: The specific type of bearing required (cylindrical, spherical, tapered, etc.) can significantly impact the cost, with more specialized bearings generally being more expensive.
- Bearing Size and Material: Larger bearings or those made from premium materials (such as stainless steel or engineered plastics) tend to be costlier.
- Manufacturer and Quality: High-quality bearings from reputable manufacturers may come with a higher price tag but often offer better longevity and performance.
- Quantity Needed: Bulk purchases may qualify for discounts, whereas buying individual bearings can be more expensive in the long run.
- Installation Complexity: Bearings that are difficult to access or require special tools for installation can increase labor costs.
- Urgency of Replacement: Emergency replacements or rush orders can incur additional costs due to expedited shipping or overtime labor charges.
Tips for Budgeting and Cost Management
- Conduct Regular Inspections: Early detection of bearing wear can prevent emergency replacements and associated costs.
- Invest in Quality: Opting for high-quality bearings can reduce the frequency of replacements and lower long-term costs.
- Bulk Purchasing: Consider buying bearings in bulk to take advantage of volume discounts.
- Negotiate with Suppliers: Don’t hesitate to negotiate prices or ask for discounts from bearing suppliers.
- Consider Total Cost of Ownership: Factor in the lifespan and maintenance requirements of bearings, not just the initial purchase price.
- Train Maintenance Staff: Proper installation and maintenance by trained personnel can extend bearing life and reduce replacement needs.
- Keep Spare Bearings in Stock: Having a small inventory of critical bearings can prevent costly downtime waiting for replacements.
- Explore Alternative Suppliers: Regularly review and compare suppliers to ensure you’re getting the best value for your conveyor roller bearing replacement needs.
- Implement a Preventive Maintenance Program: Regular maintenance can identify potential issues before they necessitate costly replacements.
- Use Technology for Monitoring: Advanced monitoring systems can predict bearing failures, allowing for planned replacements that are more budget-friendly.
By considering these factors and tips, businesses can effectively manage the costs associated with conveyor roller bearing replacement, ensuring the smooth operation of their conveyor systems without unnecessary financial strain.

Finding Conveyor Roller Bearing Replacement Services
When the time comes for conveyor roller bearing replacement, selecting a reliable service provider is crucial to ensure your conveyor system is restored to optimal performance with minimal downtime. Here’s how to find and choose the right conveyor roller bearing replacement services near you.
How to Find Conveyor Roller Bearing Replacement Near Me
- Online Search: Utilize search engines to find services in your area by typing “conveyor roller bearing replacement near me.” This should provide a list of nearby providers.
- Industry Directories: Look into online directories and databases specific to the conveyor and material handling industry. These platforms often list service providers along with their specialties and contact information.
- Trade Associations: Contact trade associations related to material handling and conveyor systems. They can often recommend reputable service providers.
- Referrals: Ask for recommendations from industry peers or colleagues who have recently undergone conveyor roller bearing replacement. Personal referrals can lead you to trusted providers.
- Social Media and Forums: Industry-specific forums and social media groups can be valuable resources for finding service providers. Members often share their experiences and recommendations.
Benefits of Professional Installation for Complex Systems
Professional installation offers numerous advantages, especially for complex conveyor system
- Expertise and Precision: Professionals have the expertise and tools to perform precise installations, ensuring that bearings are properly aligned and secured, which is crucial for optimal performance.
- Minimized Downtime: Experienced technicians can complete the replacement quickly and efficiently, reducing downtime and minimizing disruption to your operations.
- Enhanced Safety: Professionals adhere to strict safety standards, reducing the risk of accidents during the replacement process. They are also equipped to handle hazardous environments.
- Long-term Reliability: Proper installation by experts ensures the longevity and reliability of the bearings, reducing the likelihood of premature failures and additional maintenance costs.
Selecting the Right Service Provider for Your Needs
- Experience and Expertise: Look for a service provider with extensive experience and expertise in conveyor roller bearing replacement. They should have a proven track record of handling similar systems.
- Quality of Bearings: Ensure the provider uses high-quality bearings from reputable manufacturers. The durability and performance of the replacement bearings are crucial for the longevity of your conveyor system.
- Service Scope: Confirm that the service provider can handle the specific requirements of your conveyor system, including the type and size of bearings needed.
- Customer Reviews and Testimonials: Check online reviews, testimonials, and case studies to gauge the provider’s reliability and quality of service.
- Response Time and Availability: Choose a provider who can respond quickly and has the availability to minimize your system’s downtime.
- Warranty and Support: Look for providers who offer warranties on their work and ongoing support after the replacement has been completed.
- Cost: While cost shouldn’t be the sole deciding factor, it’s important to get quotes from multiple providers to ensure you’re getting competitive pricing for the conveyor roller bearing replacement services.
- Safety and Compliance: Ensure the service provider adheres to all relevant safety standards and regulations during the replacement process.
By carefully researching and considering these factors, you can find a conveyor roller bearing replacement service that meets your needs, ensuring your conveyor system operates efficiently and reliably.
Enhance your system with our robust conveyor rollers. Act today!
DIY Conveyor Roller Bearing Replacement
For those inclined to undertake maintenance tasks themselves, DIY conveyor roller bearing replacement can be a cost-effective way to ensure your conveyor system remains in top condition. This section will guide you through what’s typically included in a conveyor roller bearing replacement kit and provide a step-by-step approach to replacing the bearings yourself.
Conveyor Roller Bearing Replacement Kit: What’s Included and How to Use It
A typical conveyor roller bearing replacement kit should include the following components:
- Replacement Bearings: Precision-engineered bearings suitable for your specific type of conveyor roller.
- Bearing Pullers: Tools designed to remove the old bearings without causing damage to the roller.
- Installation Tools: These may include press-fit tools or other devices to help securely install the new bearings.
- Lubricants: High-quality lubricants to ensure smooth operation of the bearings post-installation.
- Cleaning Supplies: Solvents and cloths for cleaning the roller and bearing housing before installation.
- Instruction Manual: Detailed instructions on how to remove the old bearings and install the new ones correctly.
How to Use the Kit:
- Prepare the Area: Ensure the conveyor is turned off and properly locked out to prevent accidental startup.
- Clean the Roller: Use the provided cleaning supplies to remove any dirt or debris from the roller and bearing housing.
- Remove Old Bearings: Utilize the bearing pullers to carefully extract the old bearings from the roller.
- Install New Bearings: Follow the instruction manual to press the new bearings into place, ensuring they are seated correctly.
- Lubricate: Apply the provided lubricant to the new bearings according to the instructions.
- Reassemble: Once the new bearings are installed and lubricated, reassemble any components that were removed during the process.
Step-by-Step Guide to Replacing Conveyor Roller Bearings Yourself
- Safety First: Disconnect power to the conveyor system and apply lockout/tagout procedures.
- Access the Bearings: Remove any guards or covers that provide access to the roller bearings.
- Inspect: Before removal, inspect the bearings and surrounding components for signs of wear or damage.
- Removal: Using the bearing pullers from the kit, carefully remove the old bearings. Take care not to damage the conveyor roller shaft or housing.
- Clean: Thoroughly clean the bearing housing and shaft to ensure a smooth surface for the new bearings.
- Install New Bearings: Using the installation tools, press the new bearings into place. Ensure they are aligned correctly to avoid future issues.
- Lubrication: Apply lubricant to the new bearings, following the kit’s instructions or the manufacturer’s recommendations.
- Test: Before reapplying power, manually rotate the roller to ensure the bearings are moving smoothly.
- Power On: Once satisfied with the installation, remove lockout/tagout devices, restore power, and test the conveyor system under load to ensure proper operation.
By following these steps and utilizing a conveyor roller bearing replacement kit, you can successfully perform DIY conveyor roller bearing replacement, maintaining the efficiency and reliability of your conveyor system.
DIY vs Professional Replacement
Choosing between do-it-yourself (DIY) and professional services for conveyor roller bearing replacement depends on various factors. Here’s a comparison to help you decide:
- Pros and Cons of Do-It-Yourself vs Hiring Experts
- DIY Replacement
- Pros:
- Cost Savings: Performing the replacement yourself can save on labor costs.
- Flexibility: You can schedule the replacement at your convenience without waiting for a service appointment.
- Cons:
- Skill and Knowledge Requirements: DIY replacement requires a good understanding of the conveyor system and the specific bearings being replaced. Lack of expertise can lead to improper installation.
- Tools and Equipment: You may need specialized tools, which can be expensive to purchase or rent.
- Time-Consuming: Without experience, the replacement process can take significantly longer, leading to extended downtime.
- Risk of Errors: Incorrect installation can result in further damage to the conveyor system and additional costs for repairs.
- Professional Replacement
- Pros:
- Expertise and Efficiency: Professionals bring specialized knowledge and experience, ensuring the job is done correctly and efficiently.
- Quality Assurance: Professional services often come with warranties or guarantees on their work, providing peace of mind.
- Safety: Technicians are trained to follow safety protocols, reducing the risk of accidents.
- Long-term Benefits: Proper installation enhances the longevity and performance of the bearings, leading to fewer maintenance issues and downtime.
- Cons:
- Higher Initial Cost: Hiring professionals involves labor costs, which can be higher than DIY.
- Cost Considerations and Long-term Benefits
- Initial Costs: While professional services may have higher upfront costs, these are often outweighed by the long-term benefits of reliable and efficient operation.
- Long-term Savings: Proper installation reduces the likelihood of frequent replacements and repairs, leading to cost savings over time. It also ensures that the conveyor system operates at peak efficiency, reducing energy consumption and wear on other components.
- Return on Investment (ROI): Investing in professional services can provide a high ROI through improved system performance, reduced downtime, and extended lifespan of the bearings and conveyor system.
While DIY conveyor roller bearing replacement might seem cost-effective initially, the benefits of professional services often outweigh the costs, especially for complex systems. By choosing the right professional services, you can ensure a seamless replacement process, enhanced safety, and long-term reliability of your conveyor system.

Choosing the Right Conveyor Roller Bearings for Replacement
Selecting the appropriate bearings is a critical step in the conveyor roller bearing replacement process. The right bearings not only ensure the smooth operation of your conveyor system but also extend its service life, reducing the need for frequent replacements. This section will guide you through choosing heavy-duty conveyor roller bearings, finding the best suppliers, and understanding how to select bearings based on specific conveyor requirements.
Heavy-Duty Conveyor Roller Bearing Replacement Options
When dealing with heavy-duty applications, it’s essential to choose bearings that can withstand high loads and harsh conditions. Here are six options for heavy-duty conveyor roller bearing replacement:
- Spherical Roller Bearings: Ideal for applications requiring high load capacity and the ability to accommodate misalignment.
- Tapered Roller Bearings: Suitable for applications with heavy radial and axial loads, providing high durability and reliability.
- Cylindrical Roller Bearings: Best for high-speed applications with heavy radial loads.
- Solid Housed Roller Bearings: Designed for extreme environments, offering additional protection against contaminants.
- Sealed Roller Bearings: Provide extra defense against dust, water, and other contaminants, ideal for outdoor or dusty environments.
- High-Temperature Roller Bearings: Specifically designed to operate in high-temperature conditions, perfect for applications near heat sources.
Roller Bearing Suppliers Near Me: How to Choose the Best Supplier
Finding a reliable supplier is crucial for ensuring the quality of your conveyor roller bearing replacement. Consider the following when choosing a supplier:
- Reputation: Look for suppliers with a strong reputation in the industry, indicated by positive reviews and testimonials.
- Product Range: Choose a supplier with a wide range of bearing options to ensure they can provide the specific type you need.
- Technical Support: Good suppliers offer technical support, helping you select the right bearings for your application.
- Availability: Ensure the supplier has the bearings you need in stock, reducing downtime for your conveyor system.
- Delivery Times: Consider the supplier’s delivery times to ensure they can meet your schedule.
- After-Sales Service: Look for suppliers who provide excellent after-sales service, including returns, exchanges, and warranties.
Roller Bearing Examples: Selecting Bearings Based on Specific Conveyor Requirements
Selecting the right bearings involves understanding your conveyor’s specific needs. Here are six examples of how to match bearings to conveyor requirements:
- High Load Capacities: For conveyors carrying roller heavy loads, spherical or tapered roller bearings are ideal due to their high load capacity.
- High-Speed Operations: Cylindrical roller bearings are suitable for high-speed applications due to their design, which minimizes friction.
- Harsh Environments: Solid housed or sealed roller bearings offer the best protection against harsh environmental conditions.
- Precision Applications: For applications requiring high precision, tapered roller bearings provide excellent alignment and load distribution.
- Temperature Extremes: High-temperature roller bearings are necessary for conveyors operating in high-heat environments.
- Misalignment Tolerance: Spherical roller bearings are the best choice for systems with potential shaft misalignment issues due to their self-aligning properties.
By carefully considering these options and examples, you can ensure a successful conveyor roller bearing replacement, enhancing the efficiency and longevity of your conveyor system.
Maintenance and Prevention for Conveyor Roller Bearing Replacement
Proper maintenance and preventive measures are crucial to extending the life of conveyor roller bearings and avoiding premature failures. Implementing a comprehensive maintenance program can significantly reduce the need for frequent conveyor roller bearing replacements, ensuring your conveyor system operates efficiently and reliably. Here are ten maintenance tips and strategies to prevent premature bearing failure.
Regular Maintenance Tips to Extend the Life of Conveyor Roller Bearings
- Regular Inspections: Conduct routine inspections to check for signs of wear, damage, or overheating in the bearings.
- Lubrication Schedule: Follow a regular lubrication schedule using the correct type of lubricant as specified by the bearing manufacturer to reduce friction and wear.
- Cleanliness: Keep the conveyor and the area around the bearings clean to prevent dust, dirt, and debris from entering the bearings.
- Alignment Checks: Ensure the conveyor rollers and bearings are properly aligned to prevent uneven wear and stress.
- Load Distribution: Monitor the load distribution on the conveyor to avoid overloading bearings in certain areas.
- Bearing Adjustment: Adjust bearings as necessary to ensure proper fit and clearance, avoiding too tight or too loose bearings.
- Temperature Monitoring: Use temperature monitoring tools to detect overheating bearings, which can be a sign of overloading or lubrication issues.
- Vibration Analysis: Implement vibration analysis to detect abnormalities that could indicate bearing wear or damage.
- Replacement of Worn Parts: Promptly replace any worn or damaged parts to prevent further damage to the bearings and other conveyor components.
- Training for Maintenance Staff: Ensure that maintenance personnel are properly trained in conveyor roller bearing maintenance and replacement procedures.
How to Prevent Premature Bearing Failure in Conveyor Systems
Preventing premature bearing failure involves not only regular maintenance but also understanding and addressing the root causes of bearing issues. Here are key strategies to prevent premature failure:
- Proper Installation: Ensure bearings are installed correctly, following manufacturer guidelines to prevent damage during installation.
- Use of Correct Bearings: Select the appropriate bearings for the specific application, considering load, speed, and environmental conditions.
- Avoid Contamination: Implement seals or shields where necessary to protect bearings from contaminants.
- Monitor Environmental Conditions: Be aware of the operating environment, including temperature, humidity, and exposure to corrosive substances, and take appropriate protective measures.
- Regular Training: Conduct regular training sessions for operators and maintenance staff to ensure they are aware of best practices for operating and maintaining the conveyor system.
By adhering to these maintenance and prevention tips, you can significantly reduce the likelihood of premature conveyor roller bearing failure, ensuring your conveyor system remains productive and efficient.
Maximize productivity with our high-quality conveyor rollers!
FAQs about Conveyor Roller Bearing Replacement
Conveyor roller bearing replacement access the bearing by removing any guards or covers,pply pressure to the puller to extract the bearing from the roller.Removing bearings from rollers, particularly in conveyor systems, requires precision and care to avoid damaging the roller or the bearing housing. The process typically involves the following steps: First, ensure the conveyor system is powered off and locked out to prevent accidental activation. Next, access the bearing by removing any guards or covers. If the roller has retaining clips or setscrews, these should be removed or loosened. Using a bearing puller, carefully attach the tool to the edges of the bearing, ensuring it has a firm grip. Gradually apply pressure to the puller to extract the bearing from the roller. It’s crucial to apply force evenly to avoid tilting or jamming the bearing, which could damage the roller. In some cases, especially with stubborn bearings, applying heat around the bearing housing can expand the metal slightly, making it easier to remove the bearing. Always wear appropriate safety gear, such as gloves and eye protection, during this process.
Roller bearings are designed to carry heavy loads with minimal friction and are classified into three main types based on their shapes and applications: Cylindrical, Tapered, and Spherical. Cylindrical roller bearings consist of cylindrical rollers, allowing them to support high radial loads with moderate speed capabilities, making them suitable for a wide range of applications including electric motors and automotive transmissions. Tapered roller bearings have conical rollers and raceways, which allow them to support high radial and axial loads in one direction, making them ideal for use in vehicle hubs and gearboxes where they can handle the combination of radial and thrust loads. Spherical roller bearings feature barrel-shaped rollers within two inner ring raceways and a spherical outer ring raceway, enabling them to accommodate misalignment and shaft deflections, making them suitable for applications with severe misalignment conditions such as in wind turbines and continuous casting machines.
Removing a bearing from a conveyor roller involves a series of steps that must be executed with care to avoid damaging the roller or the bearing seat. First, ensure the conveyor system is safely powered off and locked out. Identify the type of bearing and any fastening mechanisms used, such as setscrews or retaining rings, and remove them. Employ a bearing puller tool that is appropriate for the size and type of bearing you are dealing with. Attach the puller securely to the bearing, ensuring it has a firm and even grip. Gradually apply force to the puller, ensuring the force is evenly distributed to avoid tilting the bearing, which could damage the roller. For stubborn bearings, applying a controlled amount of heat around the bearing housing can facilitate removal by expanding the metal slightly. It’s important to proceed with caution when using heat to avoid damaging the roller material. Once the bearing is removed, inspect the roller shaft and housing for any damage or wear before installing a new bearing.
Conveyors typically utilize a variety of bearings, depending on the specific requirements of the system, including load capacity, speed, and environmental conditions. The most common types of bearings used in conveyor systems are ball bearings and roller bearings. Ball bearings are used in lighter-duty applications where the conveyor carries smaller loads at higher speeds. They are known for their precision and ability to reduce friction, making them suitable for applications requiring smooth operation. Roller bearings, including cylindrical, tapered, and spherical types, are preferred in heavier-duty applications due to their higher load capacity and durability. Cylindrical roller bearings are often used for their high radial load capacity and moderate speed capabilities. Tapered roller bearings are chosen for their ability to handle combined radial and axial loads, making them suitable for inclined or vertical conveyor systems. Spherical roller bearings are used in applications where misalignment or shaft deflections may occur, providing flexibility and accommodation for such conditions. The selection of bearings is crucial for the efficiency and longevity of the conveyor system, and it should be based on the specific operational requirements of the conveyor.
Roller bearings should be replaced when they show signs of excessive wear or operational issues. Indicators include excessive noise and vibration, which suggest that the bearings are worn or damaged. Visible damage, such as cracks, pitting, flaking, or deformation, also signals the need for replacement. Additionally, decreased performance, such as slower conveyor belt speed, irregular motion, or jamming, indicates increased friction and resistance from deteriorating bearings. Even without visible issues, bearings should be replaced during scheduled maintenance if they have reached their expected lifespan or show signs of imminent failure. Timely replacement ensures optimal system performance, prevents unexpected downtime, and extends the lifespan of the equipment.
The best bearings for conveyors depend on specific system requirements such as load capacity, speed, and environmental conditions. Deep groove ball bearings are versatile and ideal for general-purpose conveyors due to their low friction and quiet operation. Tapered roller bearings handle heavy radial and axial loads, making them suitable for heavy-duty applications like mining. Spherical roller bearings are great for handling heavy loads and misalignment, perfect for industries like steel or paper. Cylindrical roller bearings, known for high radial load capacity and low friction, are ideal for high-speed conveyors. Pillow block bearings are easy to install and maintain, widely used across various applications. Needle roller bearings, compact and high-load bearing, fit well in limited space scenarios. Self-aligning ball bearings are suitable for conveyors where misalignment is a concern, handling moderate radial and light axial loads effectively. Selecting the best bearing involves assessing these factors to ensure optimal performance and longevity.
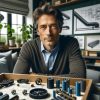
Jordan Smith, a seasoned professional with over 20 years of experience in the conveyor system industry. Jordan’s expertise lies in providing comprehensive solutions for conveyor rollers, belts, and accessories, catering to a wide range of industrial needs. From initial design and configuration to installation and meticulous troubleshooting, Jordan is adept at handling all aspects of conveyor system management. Whether you’re looking to upgrade your production line with efficient conveyor belts, require custom conveyor rollers for specific operations, or need expert advice on selecting the right conveyor accessories for your facility, Jordan is your reliable consultant. For any inquiries or assistance with conveyor system optimization, Jordan is available to share his wealth of knowledge and experience. Feel free to reach out at any time for professional guidance on all matters related to conveyor rollers, belts, and accessories.