Advanced Conveyor Belt Roller Design Innovations and Benefits
Conveyor belt roller design plays a pivotal role in various industries, offering a streamlined approach to material handling. Conveyor belt rollers facilitate the smooth movement of goods, reducing manual labor and improving efficiency. The key components of a conveyor system include belts, frames, and, crucially, rollers. Rollers, as the primary support and driving mechanism, ensure seamless transportation of items across manufacturing lines, warehouses, and distribution centers. Their design, durability, and functionality are integral to conveyor belt roller design, ultimately optimizing productivity in food processing, mining, logistics, and other sectors. Understanding these components enhances system performance and prolongs equipment lifespan.
What are Conveyor Belt Roller Design
Types of Rollers in Conveyor Belts
Conveyor belt roller design is crucial to withstand torsional forces and support the rollers adequately.Line shaft conveyors use rotating shafts, spools, and belts for efficient movement.Conveyor belt roller design encompasses various types of rollers that contribute to efficient material transportation. Key roller types include:
- Troughing Idlers: These rollers, arranged in sets of three or more, form a trough shape to guide and support the belt while transporting bulk materials. Their inclined angle ensures materials remain centered, reducing spillage and increasing stability, particularly in mining and heavy industry applications.
- Rubber Disk Idlers: With rubber rings spaced at intervals along the roller, these idlers are designed to prevent material buildup on the rollers. Their resilient nature makes them ideal for applications handling sticky or abrasive materials, commonly found in construction, quarrying, and recycling.
- Screw Idler Rollers: These rollers feature a spiral design that automatically cleans the belt by removing loose material. This self-cleaning property is crucial in applications where debris accumulation is an issue, ensuring consistent conveyor belt roller design performance in industries like agriculture and waste management.
Each roller type provides unique advantages and caters to specific applications, ultimately optimizing the conveyor system’s functionality.
Materials and Construction
Materials used in conveyor belt roller design significantly impact performance and durability:
- Steel: Steel rollers offer robust strength and load-bearing capacity, making them suitable for heavy-duty industries like mining and cement production. They are often galvanized or coated for corrosion resistance.
- Polymer: Lightweight polymer rollers reduce the overall weight of the conveyor system while providing rust-resistant properties. They are ideal for food processing and pharmaceutical industries due to their hygienic, non-corrosive characteristics.
- Rubber: Rubber-coated rollers offer superior grip and shock absorption, minimizing belt slippage and reducing noise. These rollers excel in environments where impact and vibration are common, such as quarries and material handling facilities.
Choosing the right material for conveyor belt roller design ensures optimal performance, longevity, and suitability for specific applications, balancing factors like load capacity, corrosion resistance, and environmental considerations.
Principles of Conveyor Belt Roller Design
Roller Conveyor Design Calculations
In conveyor belt roller design, accurate calculations are crucial for ensuring efficient and reliable system performance. Key factors include:
- Load Capacity: The roller’s load capacity must match or exceed the conveyor’s expected weight requirements. Calculating the static and dynamic load involves determining the weight of the materials, the belt, and any additional equipment.
- Speed: Roller speed affects the conveyor system’s throughput. It is calculated by considering the required material flow rate and the conveyor’s operational speed. Proper speed ensures a consistent material flow, optimizing the system’s efficiency.
- Power Requirements: Power calculations consider the load capacity, conveyor length, and incline. The formula involves factors like frictional resistance and belt tension. The total required power is a sum of the power needed to overcome the rolling resistance of the rollers and the weight of the conveyed material.
These calculations are essential for a well-designed conveyor belt roller design that maintains operational efficiency and meets safety standards.
Get expert advice on the right conveyor rollers here.
Conveyor Belt Roller Design PDF Resources
To delve deeper into the nuances of conveyor belt roller design, numerous resources are available online. Here are ten suggestions for downloadable PDFs that provide comprehensive insights:
- CEMA Conveyor Design Manual: A thorough handbook on conveyor design calculations and standards.
- Belt Conveyors for Bulk Materials – CEMA: Focuses on belt conveyor design for bulk material handling.
- Roller Conveyor Handbook: Contains guidelines and formulas for roller conveyor design.
- DIN 22101 Standard: Provides insights into belt conveyor design and capacity calculations.
- IS 11592 Belt Conveyor Design Guide: Offers practical approaches to belt conveyor design calculations.
- Conveyor Rollers Technical Specification Guide: Covers technical specifications and selection criteria for rollers.
- Bulk Material Handling Equipment Design Guide: Focuses on the design of bulk material handling equipment, including rollers.
- Overland Conveyor Design Considerations: Includes design principles specific to long-distance conveyors.
- Technical Paper on Idler Spacing: Discusses the optimal spacing of idlers in conveyor systems.
- Conveyor Roller Maintenance Guide: Emphasizes maintenance practices for enhancing roller lifespan.
These resources provide in-depth knowledge of the principles and intricacies involved in conveyor belt roller design, assisting engineers and designers in creating efficient and durable conveyor systems.
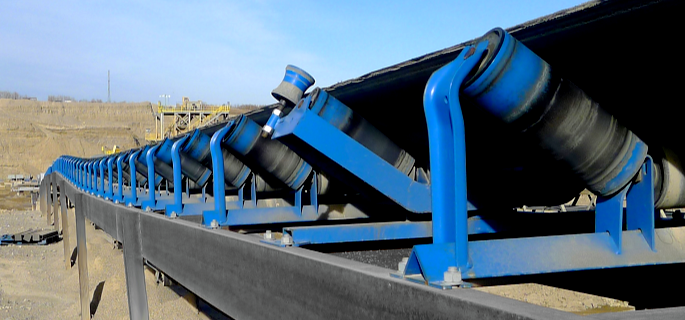
Conveyor Belt Roller Design Method
Designing a conveyor belt roller involves several key steps to ensure functionality, durability, and efficiency. Below is a general method you can follow:
Define Requirements
- Load Capacity: Determine the maximum load the roller needs to support.
- Roller Length and Diameter: Based on the width of the conveyor belt and the size of the load.
- Speed: Determine the speed at which the belt will move.
- Environmental Conditions: Consider factors like temperature, humidity, and exposure to chemicals.
Select Materials
- Shaft Material: Typically made from steel or stainless steel for strength and durability.
- Roller Shell Material: Can be made from steel, aluminum, or plastic depending on the application.
- Bearing Type: Select appropriate bearings that can handle the load and speed.
Structural Design
- Shaft Design: Calculate the shaft diameter based on the load and length to prevent bending.
- Shell Design: Ensure the roller shell is thick enough to support the load without deforming.
- Bearing Placement: Position bearings to minimize stress and ensure smooth rotation.
Stress Analysis
- Finite Element Analysis (FEA): Use FEA software to simulate and analyze stress distribution on the roller.
- Safety Factor: Ensure the design includes a safety factor to handle unexpected loads or stresses.
Prototyping and Testing
- Prototype Fabrication: Create a prototype based on your design specifications.
- Load Testing: Test the prototype under maximum load conditions.
- Performance Testing: Check the roller’s performance at different speeds and environmental conditions.
Manufacturing
- Material Procurement: Source materials according to the design specifications.
- Machining and Assembly: Machine the parts and assemble the roller.
- Quality Control: Inspect each roller for defects and ensure it meets the design requirements.
Installation and Maintenance
- Installation: Install the rollers on the conveyor system and ensure proper alignment.
- Maintenance Schedule: Develop a maintenance schedule to regularly check for wear and tear and perform necessary repairs.
By following these steps and calculations, you can design a conveyor belt roller that meets your specific needs and operational conditions.
Key Factors in Conveyor Belt Roller Design
The design of conveyor belt rollers is a fundamental aspect that influences the performance, efficiency, and reliability of conveyor systems. Several key factors must be considered to ensure the rollers meet the operational demands of various industries. These factors include material selection, surface finish, roller diameter and length, load capacity and distribution, bearing and shaft design, drive mechanism, installation and maintenance, and environmental and operational conditions. This article delves into each of these factors in detail.
Material Selection
The choice of materials for conveyor belt rollers significantly affects their durability, performance, and suitability for different applications.
Key Points:
- Types of Materials: Common materials include steel, aluminum, plastic, and rubber. Steel offers high strength and durability, plastic provides lightweight and corrosion resistance, and rubber is suitable for applications requiring impact resistance and noise reduction.
- Advantages and Disadvantages: Steel rollers are durable but heavy and prone to rust. Plastic rollers are lighter and resistant to corrosion but may not handle heavy loads as well. Rubber rollers reduce noise but may wear out faster.
- Application-Specific Criteria: Material selection should consider factors such as load capacity, environmental conditions (e.g., exposure to moisture, chemicals), and the nature of the materials being transported (e.g., abrasive, fragile).
Surface Finish
The surface finish of conveyor belt rollers impacts the friction between the belt and rollers, affecting efficiency and wear.
Key Points:
- Smooth Surfaces: Minimize friction, allowing the belt to move more freely and reducing energy consumption. They are suitable for applications where high speeds and minimal resistance are desired.
- Textured Surfaces: Increase grip, preventing belt slippage, which is beneficial in inclined or vertical conveyor systems.
- Surface Treatments: Coatings such as galvanization, anodizing, or rubber lining can enhance the roller’s resistance to wear, corrosion, and impact.
Roller Diameter and Length
The dimensions of conveyor belt rollers must be chosen based on the specific requirements of the conveyor system.
Key Points:
- Diameter: Larger diameters distribute the load over a greater area, reducing stress on the roller and the belt. They are suitable for heavy-duty applications.
- Length: The length of the rollers should match the width of the conveyor belt to provide even support across its entire width, preventing sagging and misalignment.
- Standard vs. Custom Sizes: While standard sizes may be adequate for many applications, custom sizes can be designed to meet specific operational needs.
Load Capacity and Distribution
The load capacity of conveyor belt rollers is a crucial factor that determines their ability to support the materials being transported.
Key Points:
- Calculating Load Capacity: Factors such as roller diameter, wall thickness, and material strength are considered to determine the maximum load a roller can handle.
- Even Load Distribution: Proper spacing and alignment of rollers ensure that the load is evenly distributed, preventing excessive wear on any single roller and maintaining system balance.
- Design Strategies: Reinforced rollers or additional support structures can be employed for applications involving particularly heavy or uneven loads.
Bearing and Shaft Design
Bearings and shafts are critical components that affect the performance and lifespan of conveyor belt rollers.
Key Points:
- Bearing Types: Common types include ball bearings, roller bearings, and sleeve bearings. Ball bearings are suitable for high-speed applications, roller bearings for heavy loads, and sleeve bearings for quieter operation.
- Shaft Design: The shaft must be designed to handle the torsional forces exerted by the load and the rotation of the roller. It should be made from durable materials and properly aligned to prevent bending and deformation.
- Lubrication: Proper lubrication of bearings is essential to reduce friction and wear, extending the lifespan of the rollers.
Drive Mechanism
The drive mechanism determines how the rollers are powered and how they contribute to the movement of the conveyor belt.
Key Points:
- Line Shaft Drives: Use a rotating shaft connected to rollers by spools and belts, suitable for moderate loads and speeds.
- Timing Belt Drives: Offer precise synchronization and are ideal for applications requiring accurate movement control.
- Direct Drives: Involve motors directly connected to the rollers, providing high torque and control for heavy-duty applications.
Installation and Maintenance
Proper installation and regular maintenance are essential to ensure the optimal performance and longevity of conveyor belt rollers.
Key Points:
- Installation Procedures: Rollers should be installed with precise alignment to prevent belt tracking issues and uneven wear.
- Maintenance Practices: Regular inspections, cleaning, lubrication, and timely replacement of worn-out rollers are necessary to maintain system efficiency.
- Troubleshooting: Common issues such as roller misalignment, bearing failure, and surface wear should be promptly addressed to prevent system downtime.
Environmental and Operational Conditions
Rollers must be designed to withstand the specific environmental and operational conditions of their intended application.
Key Points:
- Temperature and Humidity: Rollers should be able to operate efficiently in varying temperatures and humidity levels without degrading in performance.
- Corrosive Environments: Materials and coatings resistant to corrosion are necessary for applications involving exposure to chemicals or moisture.
- Speed and Load Variations: Rollers should be adaptable to different operational speeds and load conditions, maintaining performance consistency.
The design of conveyor belt rollers is a multifaceted process that involves careful consideration of material selection, surface finish, dimensions, load capacity, bearing and shaft design, drive mechanisms, and environmental conditions. Each of these factors plays a critical role in ensuring the efficiency, durability, and reliability of conveyor belt systems. By optimizing roller design, industries can achieve significant improvements in conveyor performance, reducing operational costs and enhancing productivity.
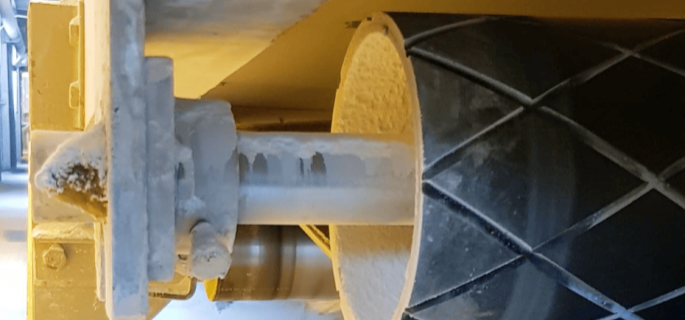
Importance of Conveyor Belt Roller Design in Conveyor Belt Performance
Conveyor belt systems are crucial components in a variety of industries, facilitating the efficient transport of materials over short and long distances. The design of conveyor belt rollers plays a significant role in the overall performance of these systems. Well-designed rollers contribute to enhanced efficiency, increased durability, superior load handling capabilities, operational stability, reduced maintenance, lower energy consumption, and greater versatility. This article explores the critical importance of roller design in optimizing conveyor belt performance.
Enhanced Efficiency
The design of conveyor belt rollers directly influences the efficiency of the conveyor system. Rollers with smooth, clean surfaces reduce friction between the belt and the roller, allowing the belt to move more freely and at higher speeds. This reduction in friction minimizes the energy required to drive the conveyor, leading to lower operational costs and increased throughput.
Key Points:
- Friction Reduction: Smooth roller surfaces minimize friction, enabling faster belt speeds.
- Energy Savings: Less energy is required to move the belt, reducing overall energy consumption.
- Increased Throughput: Higher belt speeds result in greater material handling efficiency.
Increased Durability
The durability of conveyor belt rollers is paramount for the longevity and reliability of the conveyor system. Rollers made from high-quality materials and designed with proper construction techniques can withstand the wear and tear of continuous operation. Regular maintenance of these rollers is also crucial to prevent premature failure and ensure long-term performance.
Key Points:
- Material Selection: Choosing the right materials, such as steel or reinforced plastic, enhances roller durability.
- Construction Techniques: Proper construction methods ensure rollers can handle the operational stresses.
- Maintenance: Routine maintenance extends roller life and prevents unexpected downtime.
Load Handling Capabilities
The ability of conveyor belt rollers to handle various loads is a critical design consideration. The diameter and spacing of the rollers must be carefully selected to support the weight of the materials being transported. For heavy-duty applications, rollers must be robust enough to handle significant loads without deformation or failure.
Key Points:
- Diameter and Spacing: Correct dimensions ensure adequate support for different load types.
- Heavy-Duty Design: Reinforced rollers are necessary for transporting heavy materials.
- Load Distribution: Even distribution of load across rollers prevents excessive wear and damage.
Operational Stability
Operational stability is essential for the smooth functioning of conveyor belt systems. Balanced roller design reduces vibrations and noise, leading to quieter and more stable operation. Stable systems are less prone to malfunctions, resulting in fewer disruptions and more consistent performance.
Key Points:
- Balanced Design: Properly designed rollers minimize vibrations and noise.
- Stable Operation: Reduced operational disturbances lead to fewer breakdowns.
- Noise Reduction: Quieter operation is beneficial in noise-sensitive environments.
Maintenance and Downtime Reduction
Efficient roller design simplifies maintenance tasks and reduces the frequency of required interventions. High-quality rollers that are easy to maintain can significantly lower the total cost of ownership by minimizing downtime and maintenance-related expenses.
Key Points:
- Ease of Maintenance: Well-designed rollers are easier to service and replace.
- Reduced Downtime: Reliable rollers lead to fewer maintenance interruptions.
- Cost Savings: Lower maintenance costs contribute to overall cost efficiency.
Energy Consumption
Energy consumption is a significant consideration in conveyor belt system design. Low-friction rollers reduce the amount of energy needed to move the belt, leading to substantial energy savings over time. Energy-efficient roller designs are environmentally friendly and cost-effective.
Key Points:
- Energy Efficiency: Low-friction rollers decrease energy requirements.
- Environmental Impact: Energy-efficient designs contribute to sustainability.
- Cost Reduction: Lower energy consumption translates to reduced operational costs.
Versatility and Adaptability
Versatile roller designs can be customized to meet the specific needs of different applications. Whether used in mining, manufacturing, or logistics, adaptable rollers can handle various operational conditions and material types, making them suitable for a wide range of industries.
Key Points:
- Customizability: Rollers can be tailored to specific industry requirements.
- Application Versatility: Suitable for diverse operational environments.
- Industry Examples: Custom roller designs in mining, manufacturing, and logistics.
The design of conveyor belt rollers is a critical factor in determining the overall performance and efficiency of conveyor belt systems. By focusing on enhanced efficiency, increased durability, superior load handling capabilities, operational stability, reduced maintenance, lower energy consumption, and greater versatility, companies can optimize their conveyor operations. Future advancements in roller design and technology will continue to drive improvements in conveyor belt performance, ensuring these systems remain integral to industrial operations.
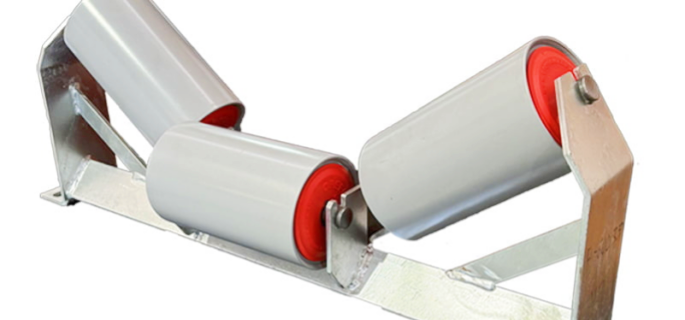
Pricing and Selection Criteria in Conveyor Belt Roller Design
Pricing Factors in Conveyor Belt Roller Design
The cost of conveyor belt rollers varies widely due to several factors involved in their production. Here are eight key factors influencing the pricing in conveyor belt roller design:
- Material: Steel rollers are typically more expensive than polymer or rubber-coated rollers due to their strength and durability. High-quality materials like stainless steel or specialized alloys can further increase costs.
- Size: Larger rollers require more material and manufacturing effort, thus driving up costs. Roller diameter and width significantly impact the overall pricing.
- Design Complexity: Custom rollers with specialized features, such as self-cleaning mechanisms or advanced sealing systems, often require additional engineering and manufacturing resources, increasing the price.
- Load Capacity: Rollers designed for higher load capacities are constructed with more robust components, which adds to the expense.
- Bearing Type: Premium bearings, like sealed-for-life or precision-grade bearings, can be costly but improve performance and longevity.
- Surface Coating or Treatment: Coatings like galvanization or specialized rubber cladding for corrosion and abrasion resistance can significantly add to the overall price.
- Production Volume: Bulk orders often result in reduced per-unit costs due to economies of scale, whereas custom, low-volume rollers are priced higher.
- Shipping and Logistics: The location of the manufacturer and the destination can impact shipping costs, especially for international orders.
Selection Criteria for Conveyor Belt Roller Design
Selecting the appropriate rollers for a conveyor system requires balancing cost-efficiency and operational requirements. Here are 12 tips for choosing the right type of roller:
- Understand Load Requirements: Choose rollers that can support the total weight of conveyed materials without bending or breaking.
- Consider Material Compatibility: Ensure the roller material is compatible with the conveyed substance to prevent contamination or degradation.
- Determine Roller Diameter: Larger diameters reduce rotational speed and wear, making them suitable for heavy loads or abrasive environments.
- Select Proper Bearing Type: Use sealed or precision bearings for harsh environments to ensure longevity and reduce maintenance.
- Choose Surface Coating Wisely: Pick a coating that resists corrosion, abrasion, or chemical exposure based on the application environment.
- Evaluate Roller Speed Requirements: Ensure the rollers can handle the conveyor belt speed without causing slippage or excessive wear.
- Match Roller Length to Belt Width: Rollers should be slightly wider than the conveyor belt to provide full support.
- Optimize Idler Spacing: Proper idler spacing reduces belt sag and improves tracking, extending belt and roller lifespan.
- Consider Self-Cleaning Features: Screw idler rollers or rubber disk idlers are ideal for systems with sticky or wet materials.
- Prioritize Energy Efficiency: Low-friction rollers reduce power consumption and operating costs.
- Review Maintenance Needs: Choose rollers with accessible bearings or self-lubricating features for easier maintenance.
- Check Compliance with Standards: Ensure the rollers meet relevant industry standards, such as CEMA or DIN, for safety and performance.
By following these guidelines, you can make an informed decision in conveyor belt roller design that aligns with your system’s operational needs and budget.
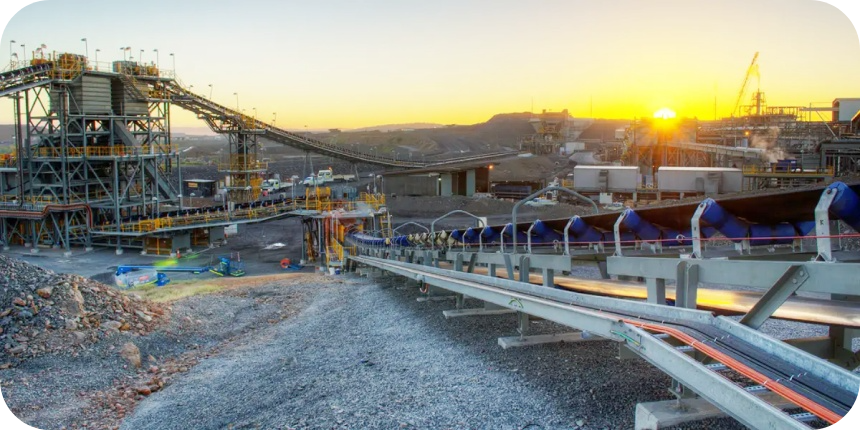
Advanced Topics in Conveyor Belt Roller Design
Conveyor Roller Design Innovations
Recent advancements in conveyor belt roller design have led to significant improvements in efficiency, safety, and reliability. Here are nine key innovations in conveyor roller technology:
- Composite Rollers: Made from lightweight, high-strength polymer composites, these rollers reduce overall system weight, energy consumption, and noise while maintaining excellent durability.
- Smart Rollers: Integrated sensors monitor vibration, temperature, and bearing health, providing real-time data to predictive maintenance systems, reducing unplanned downtime.
- Low-Friction Coatings: Advanced coatings, such as ceramic or Teflon-based, minimize rolling resistance and energy consumption, extending the lifespan of both rollers and belts.
- Self-Lubricating Bearings: Bearings with built-in lubrication reduce maintenance needs and prevent contamination, especially useful in food processing and pharmaceutical applications.
- Anti-Corrosion Treatments: Improved galvanization and specialized coatings provide superior resistance to corrosion in harsh environments like mining, chemical processing, and offshore industries.
- Dynamic Balancing: Precision dynamic balancing ensures minimal vibration at high speeds, improving belt stability and reducing roller wear.
- Self-Cleaning Rollers: Innovations like spiral idlers or rubber disc idlers automatically remove material buildup, maintaining optimal belt performance in sticky or wet conditions.
- Energy-Efficient Idler Spacing: Advanced simulation software optimizes idler spacing for minimal belt sag, reducing energy consumption and improving tracking.
- Modular Roller Systems: Modular designs enable quick replacement or customization of individual roller components, minimizing downtime and simplifying inventory management.
Examples of Cutting-Edge Systems
These advancements have led to the development of cutting-edge conveyor belt roller design systems. Here are seven examples:
- ThermoDrive® Conveyor Rollers: Incorporate low-friction coatings and dynamic balancing for reduced energy consumption and noise in food processing plants.
- Flex-Lag® Rubber Disc Idlers: Self-cleaning design prevents material buildup while providing optimal belt support, perfect for wet or abrasive material handling.
- IntelliRoll® Smart Rollers: Equipped with IoT sensors for real-time monitoring of roller performance, enabling predictive maintenance in distribution centers.
- CorroSteel™ Composite Rollers: Lightweight, corrosion-resistant composite rollers that significantly reduce energy consumption in port and mining operations.
- Rexnord® Spiral Rollers: Self-cleaning spiral rollers keep conveyor belts clean in recycling and waste management applications.
- RollX® Energy-Efficient Rollers: Feature low-friction bearings and optimized idler spacing, providing superior performance in high-speed logistics systems.
- Ultraguard™ Anti-Corrosion Coating: A proprietary coating that offers extreme corrosion resistance for conveyor systems operating in chemical processing and offshore oil platforms.
These innovations in conveyor belt roller design are setting new industry standards, offering enhanced productivity, reduced maintenance, and improved safety across various sectors. Understanding these advancements helps companies stay competitive and adopt state-of-the-art conveyor systems tailored to their specific needs.
FAQs about Conveyor Belt Roller Design
For a conveyor belt setup, the selection of rollers is crucial and varies depending on the application, load, and desired belt speed. Generally, the most common types include:
Drive Rollers: Essential for propelling the belt, often coated with materials like rubber for improved grip and reduced slippage.
Idler Rollers: Serve to support the belt and the materials it carries. These can be simple flat rollers or more specialized types such as troughing idlers or rubber disk idlers, which assist in maintaining the belt’s shape and cleanliness.
Return Rollers: These support the return path of the belt and are typically located on the underside. They can be standard rollers or equipped with rings or discs to help clean the belt.
The material construction of the rollers (steel, plastic, or coated) is selected based on the intended application, with considerations for environmental conditions, load weight, and operational needs.
Manufacturing a conveyor roller involves several stages, from design to assembly:
Design Phase: Starts with specifying the roller dimensions, load requirements, and material selection suitable for the application.
Cutting Material: Based on the design, materials (often metal tubes) are cut to the specified length.
Machining: The ends are machined to accommodate bearings and, if necessary, any additional features like sprockets for driven rollers.
Assembly: Bearings are inserted into both ends of the tube. For some designs, a shaft is passed through the bearings. The assembly may be secured with end caps.
Finishing Touches: Depending on requirements, rollers may be painted, coated, or treated to enhance durability, traction, or resistance to environmental factors.
Standard dimensions for conveyor rollers largely depend on the application but typically involve:
Diameter: Common diameters include 1.9 inches, 2.5 inches, and 3.5 inches, though the range can vary based on the conveyor scale and load requirements.
Length: This should match or slightly exceed the width of the belt to ensure adequate support and minimize belt overhang.
Bearing and Shaft Size: Chosen to suit the roller’s diameter and intended load; these are critical for ensuring the roller’s durability and efficient operation.
Custom sizes are often available or necessary depending on specific operational needs or design challenges.
Designing an effective conveyor belt system requires a comprehensive approach:
Define Operational Requirements: Start with what the conveyor needs to achieve, including the types of materials it will carry, volume, speed, and environmental conditions.
Select the Belt Material: Choose a belt material that suits the operational demands, considering factors such as strength, flexibility, and resistance to conditions like temperature and abrasion.
Design the Support Structure: This includes selecting rollers (drive, idler, and return types) and designing the frame that will support and guide the belt.
Calculate Motor and Drive Requirements: Determine the size and power of the motor needed based on the belt’s length, weight capacity, and speed requirements.
Incorporate Safety and Control Systems: Design necessary safeguards, such as emergency stops, guards, and controls for operational management.
This comprehensive planning ensures the conveyor belt is not only functional but also safe and efficient for its intended use.
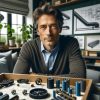
Jordan Smith, a seasoned professional with over 20 years of experience in the conveyor system industry. Jordan’s expertise lies in providing comprehensive solutions for conveyor rollers, belts, and accessories, catering to a wide range of industrial needs. From initial design and configuration to installation and meticulous troubleshooting, Jordan is adept at handling all aspects of conveyor system management. Whether you’re looking to upgrade your production line with efficient conveyor belts, require custom conveyor rollers for specific operations, or need expert advice on selecting the right conveyor accessories for your facility, Jordan is your reliable consultant. For any inquiries or assistance with conveyor system optimization, Jordan is available to share his wealth of knowledge and experience. Feel free to reach out at any time for professional guidance on all matters related to conveyor rollers, belts, and accessories.