Comprehensive Chevron Conveyor Belt Pattern Chart Explained
The chevron conveyor belt pattern is widely recognized for its distinctive V-shaped design, which enhances grip and material movement. This pattern is particularly useful in applications where incline or decline angles are involved, as it prevents materials from slipping or rolling back. Chevron conveyor belt patterns are extensively used in industries such as mining, agriculture, and construction, where efficient and reliable material handling is critical. These belts are made from high-quality rubber, ensuring durability and resistance to wear and tear. The unique pattern not only improves performance but also extends the lifespan of the conveyor belts in demanding environments.
History of Old Chevron Conveyor Belt Pattern
The chevron conveyor belt pattern has a rich history, evolving over decades to meet the diverse needs of industries requiring effective material handling solutions. This section examines the development and evolution of the old chevron conveyor belt pattern, tracing its origins and highlighting key advancements that have shaped its current form.
Early Developments
Origins of the Chevron Pattern: The chevron conveyor belt pattern traces its origins back to the early 20th century when industrialization spurred the need for more efficient material transport systems. The distinct V-shaped cleats, resembling the chevron symbol, were designed to provide enhanced grip and prevent materials from slipping, especially on inclined conveyors.
Initial Applications: Early applications of the chevron conveyor belt pattern were primarily in the agricultural and mining sectors. These industries required robust solutions for transporting bulk materials such as grain, coal, and ore over steep inclines. The chevron pattern’s ability to provide superior traction made it an ideal choice for these demanding environments.
Evolution Over the Decades
Technological Advancements: As technology advanced, so did the design and materials used in chevron conveyor belts. The introduction of synthetic materials in the mid-20th century marked a significant milestone. These materials offered improved durability, flexibility, and resistance to wear and tear compared to traditional natural rubber belts.
Design Enhancements: Over the decades, the chevron pattern itself underwent various design enhancements. The height, angle, and spacing of the cleats were optimized to cater to different types of materials and conveyor inclines. These refinements were driven by extensive research and field testing, leading to patterns that offered better performance and longer service life.
Industry-Specific Innovations: Different industries began to develop specialized chevron patterns tailored to their specific needs. For instance, the construction industry required patterns that could handle abrasive materials like sand and gravel, while the food processing industry needed belts that were easy to clean and resistant to food-grade contaminants.
Modern Developments
Advanced Materials: In recent years, the development of advanced materials such as thermoplastic elastomers and high-strength polymers has further enhanced the performance of chevron conveyor belts. These materials offer exceptional resistance to chemicals, extreme temperatures, and mechanical stress, making them suitable for a wider range of applications.
Customization and Standardization: Modern manufacturing techniques have enabled greater customization of chevron conveyor belt patterns. Customers can now specify the exact dimensions, cleat height, and spacing to match their unique requirements. At the same time, industry standards have been established to ensure consistent quality and performance across different manufacturers.
Environmental Considerations: With growing awareness of environmental sustainability, the development of eco-friendly conveyor belts has gained momentum. Recycled materials and energy-efficient manufacturing processes are increasingly being used to produce chevron conveyor belts, reducing their environmental impact.
By understanding the history and evolution of the chevron conveyor belt pattern, industries can appreciate the technological advancements that have made these belts more efficient, durable, and versatile. This historical perspective also highlights the importance of continuous innovation in meeting the ever-changing demands of material handling.
Chevron Conveyor Belt Pattern Chart
The chevron conveyor belt pattern chart is an essential tool for selecting the right belt for specific applications. This chart provides detailed information on the various patterns available, including their dimensions, specifications, and suitable applications. In this section, we take a closer look at the chevron conveyor belt pattern chart, examining common patterns and their specifications.
Common Chevron Patterns
Standard Chevron Pattern: The standard chevron pattern features V-shaped cleats arranged at regular intervals. This pattern is versatile and suitable for a wide range of applications, including transporting bulk materials on inclined conveyors. The cleat height typically ranges from 15mm to 32mm, providing adequate grip and preventing material slippage.
Open Chevron Pattern: The open chevron pattern has wider gaps between the cleats, allowing for better drainage of liquids and fine materials. This pattern is ideal for wet and sticky materials, such as wet sand or clay, as it minimizes material buildup on the belt surface.
Closed Chevron Pattern: The closed chevron pattern features closely spaced cleats, providing maximum grip for steep inclines and heavy-duty applications. This pattern is commonly used in industries such as mining and construction, where the conveyor belt needs to handle large volumes of abrasive materials.
Multi-V Chevron Pattern: The multi-V chevron pattern consists of multiple V-shaped cleats arranged in a staggered configuration. This design offers enhanced flexibility and improved material flow, making it suitable for transporting a variety of materials, including packaged goods and irregularly shaped items.
Pattern Specifications
Cleat Height and Angle: The height and angle of the cleats are critical factors in determining the performance of a chevron conveyor belt. Higher cleats provide better grip on steep inclines but may increase the wear rate of the belt. The angle of the cleats typically ranges from 15° to 45°, with steeper angles offering better traction for inclined conveyors.
Cleat Spacing: The spacing between the cleats affects the belt’s ability to handle different types of materials. Wider spacing allows for better drainage and reduces the risk of material buildup, while closer spacing provides more continuous support and is ideal for handling fine or powdery materials.
Belt Width and Thickness: The width and thickness of the conveyor belt are also important considerations. Wider belts can transport larger volumes of material, while thicker belts offer greater durability and resistance to wear. The chevron conveyor belt pattern chart typically includes information on the available widths and thicknesses for each pattern.
Material Composition: The material composition of the conveyor belt influences its performance characteristics, such as resistance to abrasion, chemicals, and extreme temperatures. The chart provides details on the types of materials used in the construction of the belt, helping customers select the right belt for their specific needs.
Applications of Chevron Patterns
Inclined Conveyors: Chevron conveyor belts are widely used on inclined conveyors to prevent material slippage and ensure smooth transport. The choice of pattern depends on the incline angle and the type of material being conveyed.
Wet and Sticky Materials: For materials that are wet or sticky, such as clay, wet sand, or agricultural products, open chevron patterns with wider cleat spacing are ideal. These patterns allow for better drainage and minimize material buildup.
Heavy-Duty Applications: In heavy-duty applications, such as mining and construction, closed chevron patterns with closely spaced cleats provide maximum grip and durability. These patterns can handle large volumes of abrasive materials without compromising performance.
Versatile Transport: Multi-V chevron patterns are suitable for transporting a variety of materials, including packaged goods, irregularly shaped items, and bulk materials. The staggered cleat configuration offers enhanced flexibility and improved material flow.
By understanding the specifications and applications of different chevron conveyor belt patterns, customers can make informed decisions when selecting the right belt for their needs. The chevron conveyor belt pattern chart serves as a valuable reference, providing detailed information on the various patterns and their performance characteristics.
Explore our extensive range of conveyor belts.
Buying Guide: Chevron Conveyor Belt Pattern for Sale
Purchasing the right chevron conveyor belt pattern requires careful consideration of various factors to ensure it meets the specific needs of the application. This buying guide provides tips and considerations for selecting chevron conveyor belt patterns for different applications, helping customers make informed decisions.
Assessing Application Requirements
Material Characteristics: The first step in selecting a chevron conveyor belt pattern is to assess the characteristics of the material being conveyed. Factors such as particle size, abrasiveness, moisture content, and temperature sensitivity will influence the choice of pattern. For example, wet and sticky materials require open chevron patterns with wider cleat spacing to prevent buildup.
Conveyor Incline: The angle of the conveyor incline is a critical factor in determining the appropriate chevron pattern. Steeper inclines require higher and more closely spaced cleats to provide adequate traction and prevent material slippage. Conversely, gentler inclines may allow for lower cleats and wider spacing.
Load Capacity: The load capacity of the conveyor system must be considered when selecting a chevron pattern. Heavier loads require belts with higher tensile strength and thicker construction to withstand the stress. The pattern should also provide sufficient grip to handle the load without slipping.
Evaluating Belt Specifications
Cleat Height and Angle: Review the cleat height and angle specifications for different chevron patterns. Higher cleats and steeper angles offer better grip but may increase wear on the belt. Selecting the right combination of cleat height and angle ensures optimal performance for the specific application.
Belt Width and Thickness: Consider the width and thickness of the belt based on the material volume and conveyor dimensions. Wider belts can transport larger quantities of material, while thicker belts provide greater durability and resistance to wear and tear.
Material Composition: Evaluate the material composition of the conveyor belt to ensure it meets the operational requirements. For applications involving abrasive materials, belts made from high-strength polymers or reinforced rubber offer better resistance to wear. For chemical or temperature-sensitive materials, select belts with appropriate resistance properties.
Manufacturer Reputation and Quality
Reputable Manufacturers: Purchase chevron conveyor belts from reputable manufacturers known for producing high-quality products. Research customer reviews, industry certifications, and the manufacturer’s track record to ensure reliability and performance.
Quality Standards: Ensure that the conveyor belt meets relevant industry standards and quality certifications. High-quality belts are designed to withstand the rigors of industrial applications and provide long-lasting performance.
Customization Options: Look for manufacturers that offer customization options to tailor the chevron pattern to specific requirements. Customization may include adjusting cleat height and spacing, selecting specific materials, and designing belts for unique applications.
Cost Considerations
Budget: Determine the budget for purchasing the conveyor belt and compare prices from different suppliers. While cost is an important factor, it should not compromise the quality and performance of the belt.
Investing in a high-quality belt can result in long-term cost savings through reduced maintenance and extended service life.
Total Cost of Ownership: Consider the total cost of ownership, including installation, maintenance, and replacement costs. High-quality belts may have a higher initial cost but offer better durability and lower maintenance requirements, leading to overall cost savings.
Installation and Maintenance
Installation Support: Ensure that the supplier provides adequate support for the installation of the chevron conveyor belt. Proper installation is crucial for optimal performance and longevity. Some manufacturers offer installation services or detailed guides to assist with the process.
Maintenance Requirements: Review the maintenance requirements for the selected conveyor belt pattern. Regular maintenance, including inspections, cleaning, and lubrication, is essential for ensuring the belt’s performance and extending its lifespan. Choose belts with maintenance requirements that align with the operational capabilities.
Environmental Considerations
Eco-Friendly Options: Look for eco-friendly conveyor belt options made from recycled materials or produced using energy-efficient processes. Choosing environmentally sustainable products can contribute to reducing the overall environmental impact of the operation.
Regulatory Compliance: Ensure that the conveyor belt complies with relevant environmental regulations and standards. This includes considerations for emissions, waste management, and material handling practices.
By considering these factors, customers can make informed decisions when purchasing chevron conveyor belt patterns for sale. Selecting the right pattern ensures efficient material handling, optimal performance, and long-term reliability, ultimately contributing to the success of the operation.
Advantages of Using Chevron Conveyor Belt Pattern
The chevron conveyor belt pattern, a design characterized by its V-shaped protrusions, has become a popular choice in material handling systems across various industries. This distinctive pattern offers a range of benefits that enhance the efficiency and effectiveness of conveyor operations.
Improved Grip and Reduced Slippage
One of the primary advantages of the chevron conveyor belt pattern is its enhanced grip. The V-shaped cleats provide additional traction, which is particularly beneficial when transporting materials up an incline. This improved grip reduces the likelihood of slippage, ensuring that materials remain securely in place during transit. This feature is especially valuable in industries such as mining and agriculture, where materials are often moved on steep slopes.
Enhanced Material Control
The chevron conveyor belt pattern aids in maintaining better control over the materials being transported. The raised cleats help to center the materials on the belt, preventing them from drifting to the sides. This controlled movement minimizes spillage and loss of materials, leading to a more efficient and cost-effective operation. Industries dealing with bulk materials, such as grain or sand, benefit significantly from this enhanced material control.
Versatility in Handling Various Materials
Chevron conveyor belts are highly versatile and capable of handling a wide range of materials. Whether dealing with loose, bulk items or packed goods, the chevron pattern ensures that the materials are transported smoothly and securely. This versatility makes chevron conveyor belts a preferred choice in industries like construction, where different types of materials, from concrete to gravel, are frequently moved.
Increased Load Capacity
The design of the chevron conveyor belt pattern also contributes to an increased load capacity. The V-shaped cleats provide additional support, allowing the belt to handle heavier loads without compromising performance. This increased capacity is particularly advantageous in industries where large quantities of materials need to be transported efficiently, such as in logistics and warehousing.
Durability and Longevity
Chevron conveyor belts are known for their durability and longevity. The raised pattern not only enhances grip and control but also provides an extra layer of protection to the belt surface. This added durability translates to a longer lifespan for the belt, reducing the frequency and cost of replacements. Industries that operate under harsh conditions, such as mining and heavy manufacturing, benefit from the robust nature of chevron conveyor belts.
Energy Efficiency
The chevron conveyor belt pattern can also contribute to energy efficiency. The enhanced grip and material control reduce the amount of power required to move materials, as the belt operates more smoothly and with less resistance. This energy efficiency can lead to lower operational costs, making it an attractive option for industries looking to reduce their energy consumption and environmental impact.
Safety Improvements
Safety is a critical consideration in any material handling operation, and the chevron conveyor belt pattern offers several safety benefits. The improved grip reduces the risk of materials slipping and causing accidents. Additionally, the controlled movement of materials minimizes the chances of spillage, which can create hazardous conditions for workers. By enhancing safety, chevron conveyor belts help to create a safer working environment.
Chevron Conveyor Belt Pattern and Rubber Material
The performance of chevron conveyor belts is heavily influenced by the type of rubber material used in their construction. The choice of rubber impacts the belt’s durability, flexibility, and overall performance. Various types of rubber materials are used in chevron conveyor belts, each offering unique advantages.
Natural Rubber
Natural rubber is a common material used in chevron conveyor belts. It is known for its excellent flexibility and resilience, making it suitable for applications where the belt needs to navigate around curves and corners. Natural rubber also offers good resistance to abrasion, ensuring that the belt can withstand the wear and tear of transporting various materials. However, natural rubber may not be suitable for environments with high temperatures or exposure to oils and chemicals, as it can degrade under these conditions.
Synthetic Rubber
Synthetic rubber, such as nitrile or neoprene, is often used in chevron conveyor belts to address the limitations of natural rubber. Nitrile rubber, for example, offers excellent resistance to oils, fuels, and other chemicals, making it ideal for industrial applications where the belt may come into contact with these substances. Neoprene, on the other hand, provides good resistance to weathering, ozone, and aging, making it suitable for outdoor applications. The use of synthetic rubber enhances the belt’s durability and extends its lifespan in challenging environments.
EPDM (Ethylene Propylene Diene Monomer) Rubber
EPDM rubber is another material commonly used in chevron conveyor belts. It is known for its excellent resistance to heat, ozone, and weathering, making it suitable for high-temperature applications and outdoor use. EPDM rubber also offers good flexibility and abrasion resistance, ensuring that the belt can handle various materials and operating conditions. This material is particularly beneficial in industries such as construction and mining, where the belt may be exposed to harsh weather and abrasive materials.
SBR (Styrene-Butadiene Rubber)
SBR is a versatile rubber material used in chevron conveyor belts. It provides good abrasion resistance and is cost-effective, making it a popular choice for general-purpose applications. SBR rubber is suitable for conveying a wide range of materials, from bulk goods to packed items. However, it may not offer the same level of chemical resistance as synthetic rubbers like nitrile or neoprene, so it may not be ideal for applications involving exposure to harsh chemicals.
Impact of Rubber Material on Performance
The choice of rubber material significantly impacts the performance of chevron conveyor belts. Factors such as abrasion resistance, flexibility, chemical resistance, and temperature tolerance all play a role in determining the belt’s suitability for different applications. By selecting the appropriate rubber material, industries can ensure that their chevron conveyor belts deliver optimal performance and longevity, even under challenging conditions.
Maintenance and Longevity
The type of rubber used in chevron conveyor belts also affects their maintenance requirements and longevity. High-quality rubber materials, such as those with good abrasion and chemical resistance, tend to require less frequent maintenance and have a longer lifespan. This reduces downtime and maintenance costs, contributing to more efficient operations. Industries can benefit from investing in chevron conveyor belts made from durable rubber materials, as this can lead to significant cost savings over time.
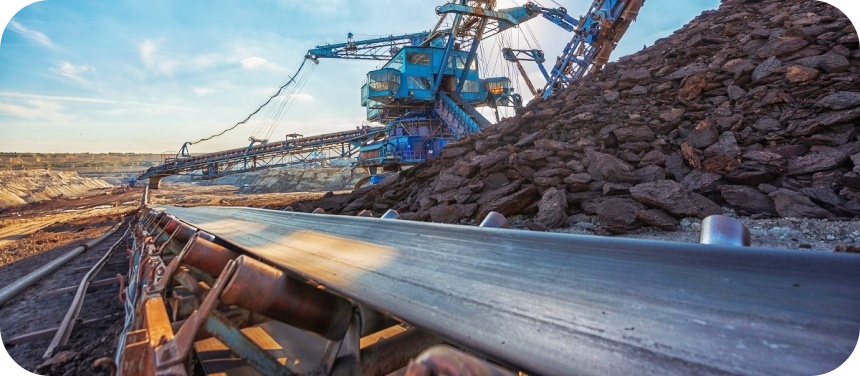
Applications of Chevron Conveyor Belts Pattern in Industries
Chevron conveyor belts are utilized across a wide range of industries, thanks to their versatility and ability to handle various materials. The unique chevron conveyor belt pattern makes them particularly suitable for specific applications where standard flat belts may fall short.
Mining and Quarrying
In the mining and quarrying industry, chevron conveyor belts are essential for transporting bulk materials such as ore, coal, and aggregates. The V-shaped cleats provide the necessary grip to move materials up steep inclines, ensuring that they reach their destination without slipping or spillage. The durability and robustness of chevron conveyor belts make them ideal for the harsh conditions typically found in mining operations.
Agriculture
Chevron conveyor belts are widely used in the agricultural sector for handling crops, grains, and other agricultural products. The enhanced grip and material control provided by the chevron pattern help to prevent spillage and ensure that the materials are transported efficiently. These belts are particularly useful during harvesting and processing, where the movement of bulk materials is critical.
Construction
The construction industry relies on chevron conveyor belts to transport building materials such as sand, gravel, and concrete. The chevron conveyor belt pattern offers the necessary traction to move these heavy and often abrasive materials over various terrains and inclines. This ensures that materials are delivered to their intended location without delays, contributing to the overall efficiency of construction projects.
Recycling
In the recycling industry, chevron conveyor belts are used to transport a variety of materials, including paper, plastic, and metal. The chevron pattern helps to keep these materials centered on the belt, reducing the risk of spillage and ensuring efficient processing. The durability of chevron conveyor belts also means they can withstand the abrasive nature of recycled materials, providing reliable performance over time.
Food Processing
Chevron conveyor belts are also employed in the food processing industry, where they handle products such as fruits, vegetables, and packaged goods. The raised cleats provide the grip needed to move items smoothly through different stages of processing, from sorting to packaging. The choice of food-grade rubber materials ensures that the belts meet hygiene standards and are safe for use in food handling applications.
Logistics and Warehousing
In logistics and warehousing, chevron conveyor belts facilitate the movement of goods and packages. The enhanced grip and material control ensure that items are transported quickly and efficiently, reducing the risk of damage or loss. Chevron conveyor belts can handle a wide range of items, from small packages to large pallets, making them a versatile solution for modern logistics operations.
Waste Management
Chevron conveyor belts play a crucial role in waste management by transporting waste materials to sorting and processing facilities. The V-shaped cleats provide the grip needed to move waste materials, including bulky and irregularly shaped items, up inclines and around curves. This ensures that waste is processed efficiently, contributing to effective waste management and recycling efforts.
Timber and Lumber Industry
In the timber and lumber industry, chevron conveyor belts are used to transport logs, timber, and wood chips. The enhanced grip and durability of the chevron pattern ensure that these heavy and often irregularly shaped materials are moved safely and efficiently. The belts’ ability to handle steep inclines is particularly beneficial in sawmills and lumber yards where materials need to be transported vertically.
Pharmaceuticals
The pharmaceutical industry also benefits from the use of chevron conveyor belts, particularly in the handling of packaged medicines and medical supplies. The controlled movement provided by the chevron pattern ensures that these sensitive items are transported without damage. The use of hygienic rubber materials ensures that the belts meet the stringent cleanliness standards required in pharmaceutical operations.
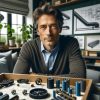
Jordan Smith, a seasoned professional with over 20 years of experience in the conveyor system industry. Jordan’s expertise lies in providing comprehensive solutions for conveyor rollers, belts, and accessories, catering to a wide range of industrial needs. From initial design and configuration to installation and meticulous troubleshooting, Jordan is adept at handling all aspects of conveyor system management. Whether you’re looking to upgrade your production line with efficient conveyor belts, require custom conveyor rollers for specific operations, or need expert advice on selecting the right conveyor accessories for your facility, Jordan is your reliable consultant. For any inquiries or assistance with conveyor system optimization, Jordan is available to share his wealth of knowledge and experience. Feel free to reach out at any time for professional guidance on all matters related to conveyor rollers, belts, and accessories.