Benefits of Troughing Idlers in Transition Idler Belt Conveyor
Transition idler belt conveyor systems are crucial components in many industries, ensuring smooth and efficient transportation of materials. These systems are designed to bridge the gap between different conveyor segments, allowing for changes in direction, height, or width. Transition idlers play a vital role in maintaining the belt’s alignment and preventing material spillage, which can lead to reduced downtime and increased productivity. By supporting the belt during transitional phases, transition idler belt conveyors help to minimize wear and tear, extend the lifespan of the conveyor system, and ensure continuous, reliable operation in various industrial applications.
The Role of Carrying Idler in Transition Idler Belt Conveyor
In a transition idler belt conveyor system, carrying idlers play a crucial role in supporting the conveyor belt and ensuring its proper alignment and smooth operation. These idlers are strategically placed along the conveyor belt, particularly in the transition areas where the belt changes direction or elevation. The following sections detail the function and importance of carrying idlers within a transition idler belt conveyor system.
Function of Carrying Idlers
Support and Stability: Carrying idlers provide essential support to the conveyor belt as it moves along its path. By ensuring the belt remains stable, carrying idlers prevent sagging and minimize the risk of damage to both the belt and the materials being transported.
Load Distribution: One of the key functions of carrying idlers is to distribute the load evenly across the width of the conveyor belt. This even distribution is critical in preventing excessive wear and tear on specific sections of the belt, thereby extending its lifespan.
Belt Alignment: Carrying idlers help maintain the alignment of the conveyor belt, which is essential for efficient operation. Misalignment can lead to various issues such as increased friction, wear, and even potential damage to the conveyor structure. Properly aligned carrying idlers ensure the belt runs smoothly and centrally along its intended path.
Minimizing Spillage: By keeping the conveyor belt properly supported and aligned, carrying idlers also play a role in minimizing material spillage. This is particularly important in industries where precise handling of materials is crucial to maintaining product quality and operational efficiency.
Placement of Carrying Idlers
In a transition idler belt conveyor system, carrying idlers are typically placed in the transition zones where the belt changes from a flat profile to a troughed profile or vice versa. These transition zones are critical points where the belt undergoes significant changes in tension and alignment. Proper placement of carrying idlers in these areas ensures a smooth transition, reducing the risk of belt damage and maintaining operational efficiency.
Transition Zones: In these zones, carrying idlers are positioned at varying angles to gradually change the belt profile. For instance, as the belt transitions from a flat to a troughed shape, the carrying idlers are arranged in a way that supports this change smoothly, preventing abrupt shifts that could lead to belt misalignment or damage.
Spacing and Angle: The spacing and angle of carrying idlers are carefully calculated based on the conveyor belt’s specifications, including its width, tension, and the type of material being transported. Proper spacing ensures that the belt remains adequately supported throughout its length, while the correct angle helps maintain the desired belt profile.
Maintenance of Carrying Idlers
Regular maintenance of carrying idlers is essential to ensure their optimal performance and longevity. Maintenance practices include routine inspections, cleaning, lubrication, and timely replacement of worn-out components.
Inspections: Regular visual inspections help identify any signs of wear or damage to the carrying idlers. This includes checking for misalignment, excessive wear on the idler rollers, and any buildup of debris that could impede their function.
Cleaning: Keeping the carrying idlers clean is crucial to prevent the buildup of materials that could cause friction and wear. Regular cleaning ensures that the idlers rotate freely and support the belt properly.
Lubrication: Proper lubrication of the idler bearings reduces friction and wear, ensuring smooth rotation and extending the life of the idlers. The frequency and type of lubrication depend on the operational conditions and the manufacturer’s recommendations.
Replacement: Timely replacement of worn-out or damaged carrying idlers is essential to maintain the efficiency and safety of the transition idler belt conveyor system. Using high-quality replacement parts ensures that the system continues to operate smoothly and efficiently.
By understanding the role and function of carrying idlers in a transition idler belt conveyor system, operators can ensure proper installation, maintenance, and operation, leading to enhanced efficiency and longevity of their conveyor systems.
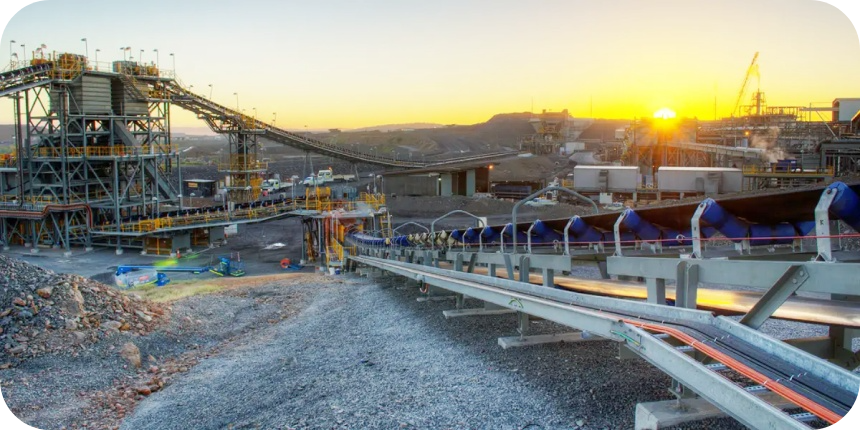
Transition Idler Belt Conveyor: Importance of Transition Distance in Conveyor Belt Systems
Transition distance is a critical factor in the design and operation of conveyor belt systems, particularly in transition idler belt conveyor setups. The transition distance refers to the length over which the conveyor belt changes from a flat profile to a troughed profile or vice versa. This section discusses the significance of transition distance in maintaining the efficiency and longevity of conveyor belt systems.
Definition of Transition Distance
Transition Distance Explained: Transition distance is the distance over which the conveyor belt transitions from a flat configuration at the tail or head pulley to the fully troughed configuration supported by troughing idlers. This distance is essential for accommodating the natural curvature of the belt as it adjusts to different profiles.
Calculation of Transition Distance: The transition distance is typically calculated based on the belt width, troughing angle, and the type of belt used. Proper calculation ensures that the belt transitions smoothly without excessive stress or bending.
Significance of Transition Distance
Belt Alignment and Tracking: Proper transition distance ensures that the belt aligns correctly as it changes profiles. This alignment is crucial for maintaining the belt’s central position and preventing misalignment issues that can lead to operational inefficiencies and increased wear.
Stress Distribution: A well-calculated transition distance helps distribute stress evenly across the belt. Sudden changes in belt profile can cause concentrated stress points, leading to premature wear or damage. A gradual transition minimizes these stress concentrations, extending the belt’s lifespan.
Material Spillage and Carryback: Effective transition distance reduces the risk of material spillage and carryback. When the belt transitions smoothly, it maintains its trough shape more effectively, preventing materials from spilling over the sides or being carried back on the return side of the belt.
Impact on Idlers and Pulleys: Proper transition distance reduces the impact on idlers and pulleys by ensuring that the belt conforms naturally to the supporting structures. This reduces the likelihood of damage to these components, leading to lower maintenance costs and longer operational life.
Factors Influencing Transition Distance
Belt Width: Wider belts require longer transition distances to accommodate the change in profile without excessive bending. The width of the belt is a primary factor in determining the appropriate transition distance.
Troughing Angle: The angle of the troughing idlers influences the transition distance. Larger troughing angles require longer transition distances to ensure a smooth change in profile.
Belt Type and Construction: The type and construction of the belt, including its flexibility and tensile strength, affect the transition distance. More flexible belts can accommodate shorter transition distances, while stiffer belts may require longer distances.
Conveyor Speed and Load: The speed at which the conveyor operates and the load it carries also influence the transition distance. Higher speeds and heavier loads necessitate longer transition distances to reduce the impact and stress on the belt and supporting structures.
Best Practices for Transition Distance
Accurate Calculations: Ensuring accurate calculations based on the specific conveyor belt system’s parameters is essential. This involves considering all relevant factors, including belt width, troughing angle, and operational conditions.
Gradual Transitions: Implementing gradual transitions by using appropriately spaced idlers and supports helps minimize stress and wear on the belt. Avoiding abrupt changes in profile ensures a smoother operation.
Regular Monitoring and Adjustments: Regular monitoring of the transition zones and making necessary adjustments based on operational feedback can help maintain optimal transition distances. This includes inspecting for signs of wear, misalignment, and material spillage.
Consulting Experts: Consulting with conveyor system experts and manufacturers can provide valuable insights into optimizing transition distances for specific applications. They can offer recommendations based on industry standards and best practices.
By understanding and properly implementing transition distances in transition idler belt conveyor systems, operators can enhance the efficiency, reliability, and longevity of their conveyor operations.
Transition Idler Belt Conveyor: Key Elements of Conveyor Belt Transition
The transition process in conveyor belt systems involves several critical elements that work together to ensure smooth and efficient operation. In a transition idler belt conveyor, these elements are designed to facilitate the change in belt profile from flat to troughed or vice versa. This section examines the key elements involved in the conveyor belt transition process, with a focus on the role of transition idlers.
Transition Idlers
Definition and Function: Transition idlers are specially designed idlers that support the conveyor belt during the transition from a flat to a troughed profile. They are placed in the transition zones and help guide the belt smoothly, preventing abrupt changes that could cause misalignment or damage.
Types of Transition Idlers: There are different types of transition idlers, including fixed and adjustable troughing idlers. Adjustable troughing idlers offer the flexibility to change the troughing angle, accommodating various belt profiles and operational conditions.
Placement of Transition Idlers: Proper placement of transition idlers is crucial for maintaining belt alignment and preventing stress concentrations. They are typically placed at the beginning and end of the transition zones, with their spacing and angle adjusted based on the belt width and operational requirements.
Carrying Idlers
Role in Transition Zones: Carrying idlers provide additional support to the belt during the transition process. They help maintain the belt’s stability and alignment, ensuring that it conforms smoothly to the desired profile.
Configuration: The configuration of carrying idlers in transition zones varies based on the belt’s specifications. They are arranged in a pattern that supports the gradual change in profile, reducing the risk of belt damage and misalignment.
Return Idlers
Support for the Return Side: Return idlers support the conveyor belt on its return journey, ensuring it remains aligned and tensioned. In transition zones, return idlers play a role in guiding the belt back to the loading point, preventing sagging and misalignment.
Types of Return Idlers: Similar to carrying idlers, return idlers come in various configurations, including flat and troughing return idlers. The
choice of return idlers depends on the belt type and operational conditions.
Transition Distance
Importance of Proper Distance: Transition distance is a key element in the conveyor belt transition process. It refers to the length over which the belt changes from a flat to a troughed profile. Proper transition distance ensures a smooth change in profile, reducing stress and wear on the belt.
Calculation: Accurate calculation of transition distance involves considering factors such as belt width, troughing angle, and belt type. Properly calculated transition distance helps maintain belt alignment and prevent damage.
Belt Tension and Alignment
Maintaining Tension: Proper belt tension is essential for efficient operation and longevity of the conveyor system. Transition zones require careful tension management to ensure the belt remains aligned and properly supported.
Alignment Techniques: Various alignment techniques, including the use of adjustable troughing idlers and regular inspections, help maintain belt alignment in transition zones. Ensuring the belt runs centrally along its intended path reduces wear and operational issues.
Impact on Idlers and Pulleys
Stress Management: The transition process can place significant stress on idlers and pulleys. Properly designed transition zones help distribute this stress evenly, reducing the risk of damage to these components.
Maintenance: Regular maintenance of idlers and pulleys in transition zones is crucial for their longevity. This includes inspections, lubrication, and timely replacement of worn-out parts.
Best Practices for Conveyor Belt Transition
Gradual Changes: Implementing gradual changes in belt profile by using appropriately spaced idlers and supports helps minimize stress and wear. Avoiding abrupt transitions ensures smoother operation and reduces the risk of belt damage.
Accurate Calculations and Adjustments: Ensuring accurate calculations for transition distance and making necessary adjustments based on operational feedback helps maintain optimal belt alignment and performance.
Regular Monitoring and Maintenance: Regular monitoring of transition zones and proactive maintenance practices help identify and address potential issues before they escalate, ensuring efficient and reliable conveyor operation.
Consulting Experts: Seeking advice from conveyor system experts and manufacturers can provide valuable insights into optimizing transition zones for specific applications. They can offer recommendations based on industry standards and best practices.
By understanding and implementing the key elements of conveyor belt transition, operators can enhance the efficiency, reliability, and longevity of their transition idler belt conveyor systems.
Installation Guidelines for Transition Idler Belt Conveyor
Proper installation of transition idlers in belt conveyor systems is crucial for ensuring smooth operation and minimal downtime. The following step-by-step instructions provide guidance on the installation process:
Step 1: Preparation
- Inspect Components: Before starting the installation, inspect all components, including the belt, idlers, and frame, for any signs of damage or wear.
- Gather Tools: Ensure you have all the necessary tools and equipment for the installation, including wrenches, measuring tape, and alignment tools.
- Safety Precautions: Follow all safety guidelines and wear appropriate protective gear, such as gloves and safety glasses.
Step 2: Positioning the Idlers
- Determine Placement: Identify the locations where the transition idlers will be installed. These should be strategic points where the belt transitions from one section to another.
- Mark Positions: Use a measuring tape to mark the positions on the conveyor frame where the idlers will be installed. Ensure the marks are evenly spaced and aligned with the frame.
Step 3: Installing the Idlers
- Attach Idlers: Secure the transition idlers to the conveyor frame using bolts and brackets. Ensure the idlers are tightly secured and aligned with the belt path.
- Adjust Angle: Adjust the angle of the idlers to match the desired belt configuration. Use alignment tools to ensure the idlers are properly aligned with the belt and frame.
Step 4: Tensioning the Belt
- Check Tension: Ensure the belt is properly tensioned to prevent sagging and misalignment. Use appropriate tensioning methods to achieve the desired tension.
- Test Movement: Run the conveyor belt to test the movement and alignment. Make any necessary adjustments to the idlers to ensure smooth operation.
Step 5: Final Inspection
- Inspect Installation: Conduct a final inspection of the installation to ensure all components are properly secured and aligned. Check for any signs of misalignment or wear.
- Make Adjustments: Make any final adjustments to the idlers and belt tension as needed to achieve optimal performance.
Step 6: Regular Maintenance
- Monitor System: Regularly monitor the conveyor system to ensure it remains in good working condition. Conduct routine inspections and maintenance to prevent issues and extend the system’s lifespan.
- Address Issues Promptly: Address any issues with the transition idlers or belt alignment promptly to prevent further damage and minimize downtime.
Transition Idler Belt Conveyor: Effective Management of Conveyor Transitions
Managing conveyor transitions effectively is critical for the smooth operation of a transition idler belt conveyor system. Proper management ensures minimal downtime, reduced maintenance costs, and prolonged equipment lifespan. This section outlines best practices for managing conveyor transitions to achieve optimal performance and efficiency.
Planning and Design
Detailed Planning: Effective management begins with meticulous planning and design. This involves understanding the specific requirements of the conveyor system, including the type of materials being transported, the belt speed, and the environmental conditions. Detailed planning helps in designing a transition idler belt conveyor system that meets operational needs and minimizes potential issues.
Custom Design: Each conveyor system is unique, and custom designing the transition zones ensures that all factors are considered. This includes the calculation of transition distances, the selection of appropriate idlers, and the determination of the optimal troughing angle. Custom design helps in creating a system that operates smoothly and efficiently.
Proper Installation
Accurate Installation: Proper installation of transition idlers is crucial for effective management. This involves ensuring that the idlers are correctly positioned and securely mounted. Accurate installation helps prevent misalignment, reduces wear and tear on the belt, and enhances the overall performance of the system.
Use of Quality Components: Using high-quality components in the installation process is essential. This includes selecting durable idlers, brackets, and bearings that can withstand the operational demands of the conveyor system. High-quality components ensure reliability and longevity.
Regular Maintenance
Routine Inspections: Conducting routine inspections is a key aspect of effective management. Regular checks help identify signs of wear and tear, misalignment, and other potential issues before they escalate. Inspections should focus on the condition of the idlers, the alignment of the belt, and the overall performance of the transition zones.
Preventive Maintenance: Implementing a preventive maintenance schedule helps in addressing potential problems proactively. This includes regular cleaning, lubrication, and timely replacement of worn-out components. Preventive maintenance minimizes downtime and ensures continuous operation.
Troubleshooting: Having a well-defined troubleshooting procedure in place is essential. This involves identifying common issues such as belt misalignment, excessive wear on idlers, and material spillage, and implementing corrective actions promptly. Effective troubleshooting helps in maintaining smooth operation and preventing disruptions.
Training and Safety
Operator Training: Training operators and maintenance personnel on the proper management of transition idler belt conveyor systems is vital. This includes educating them on best practices for installation, maintenance, and troubleshooting. Well-trained personnel can identify and address issues more effectively, ensuring optimal performance.
Safety Protocols: Implementing strict safety protocols is crucial for preventing accidents and ensuring a safe working environment. This includes using appropriate personal protective equipment (PPE), following safety guidelines during maintenance, and conducting regular safety drills. Safety protocols help in reducing risks and ensuring smooth operation.
Continuous Monitoring
Real-time Monitoring: Utilizing real-time monitoring systems helps in tracking the performance of the conveyor transitions continuously. This includes monitoring belt alignment, tension, and the condition of idlers. Real-time data provides valuable insights into the operational status and helps in making informed decisions for maintenance and improvements.
Data Analysis: Analyzing the data collected from monitoring systems helps in identifying patterns and trends. This includes tracking the wear rate of idlers, the frequency of misalignment issues, and the overall performance of the transition zones. Data analysis helps in optimizing the management practices and improving efficiency.
Implementing Best Practices
Gradual Transitions: Ensuring gradual transitions in belt profile is a best practice for managing conveyor transitions. This involves using appropriately spaced idlers and supports to prevent abrupt changes in profile, which can cause stress and damage to the belt.
Optimal Tension Management: Maintaining optimal belt tension is essential for effective management. Proper tension ensures that the belt remains aligned and supported, reducing the risk of misalignment and wear. Tension management involves regular checks and adjustments based on operational conditions.
Consulting Experts: Consulting with conveyor system experts and manufacturers provides valuable insights into best practices for managing conveyor transitions. Experts can offer recommendations based on industry standards and help in optimizing the system for better performance.
By following these best practices, operators can ensure effective management of conveyor transitions in transition idler belt conveyor systems, leading to smooth operation, minimal downtime, and enhanced efficiency.
Get reliable conveyor idlers to boost productivity.
Benefits of Adjustable Troughing Idlers in Transition Idler Belt Conveyor
Adjustable troughing idlers are an integral component of transition idler belt conveyor systems, offering numerous advantages in maintaining optimal belt alignment and performance. This section explores the benefits provided by adjustable troughing idlers and how they contribute to the efficiency and reliability of conveyor systems.
Enhanced Belt Alignment
Precise Adjustment: Adjustable troughing idlers allow for precise adjustment of the troughing angle, which is essential for maintaining proper belt alignment. By fine-tuning the angle, operators can ensure that the belt runs centrally along its intended path, reducing the risk of misalignment and associated issues.
Flexibility: The flexibility offered by adjustable troughing idlers is crucial in accommodating different belt profiles and operational conditions. This adaptability ensures that the conveyor system can handle various types of materials and changes in load without compromising alignment.
Improved Belt Support
Optimal Support: Adjustable troughing idlers provide optimal support to the conveyor belt, particularly in transition zones. Proper support ensures that the belt conforms smoothly to the desired profile, minimizing stress and wear. This support is critical in preventing sagging and maintaining the belt’s integrity.
Load Distribution: By adjusting the troughing angle, operators can achieve better load distribution across the belt’s width. Even load distribution reduces localized wear and extends the lifespan of the belt. This is particularly important in high-capacity conveyor systems where uneven loading can lead to significant issues.
Increased Efficiency
Reduced Downtime: The ability to make quick and precise adjustments with adjustable troughing idlers reduces downtime caused by belt misalignment and maintenance. Operators can address alignment issues promptly, ensuring continuous operation and improving overall efficiency.
Enhanced Performance: Properly aligned and supported belts operate more efficiently, reducing energy consumption and minimizing wear on the conveyor components. This enhanced performance translates to cost savings and increased productivity for the operation.
Simplified Maintenance
Ease of Adjustment: Adjustable troughing idlers are designed for easy adjustment, simplifying the maintenance process. Operators can quickly make necessary changes to the troughing angle without requiring extensive downtime or specialized tools. This ease of adjustment makes regular maintenance more manageable and less time-consuming.
Proactive Maintenance: The flexibility of adjustable troughing idlers allows for proactive maintenance practices. Operators can make small adjustments as part of routine maintenance to ensure optimal belt alignment and performance, preventing larger issues from developing.
Versatility
Adaptability to Different Conditions: Adjustable troughing idlers are versatile and can adapt to various operational conditions. This includes changes in material type, belt speed, and load capacity. The ability to adjust the troughing angle ensures that the conveyor system remains efficient and reliable under different conditions.
Compatibility with Various Conveyor Systems: Adjustable troughing idlers are compatible with a wide range of conveyor systems, making them a versatile solution for different industries. Their adaptability ensures that they can be integrated into existing systems or used in new installations with ease.
Enhanced Safety
Reduced Risk of Belt Damage: By maintaining proper alignment and support, adjustable troughing idlers reduce the risk of belt damage caused by misalignment and excessive wear. This enhances the safety of the conveyor system, preventing accidents and ensuring a safe working environment.
Lower Maintenance Risks: The ease of adjustment and simplified maintenance procedures reduce the risks associated with maintenance activities. Operators can make adjustments safely and efficiently, minimizing the potential for accidents and injuries.
Cost Savings
Longer Belt Life: Properly aligned and supported belts experience less wear and tear, extending their lifespan. This reduces the frequency of belt replacements, leading to significant cost savings over time.
Lower Maintenance Costs: The reduced need for extensive maintenance and the ability to make quick adjustments translate to lower maintenance costs. This includes savings on labor, replacement parts, and downtime.
Adjustable troughing idlers offer numerous benefits in transition idler belt conveyor systems, including enhanced belt alignment, improved support, increased efficiency, simplified maintenance, versatility, enhanced safety, and cost savings. By integrating adjustable troughing idlers into their conveyor systems, operators can ensure optimal performance, reliability, and longevity, ultimately leading to more efficient and cost-effective operations.
FAQs about Transition Idler Belt Conveyor
A transition conveyor is a section of a conveyor belt system that bridges the gap between different segments or components of the conveyor. This transition area is crucial for maintaining the continuity and smooth operation of the belt as it moves through various stages of its path. The primary function of a transition conveyor is to ensure that the material being transported remains stable and evenly distributed during the transition. This prevents spillage and reduces wear and tear on the belt. Transition conveyors are often equipped with transition idlers, which help guide and support the belt, ensuring it stays aligned and operates efficiently. They are commonly used in applications where the conveyor belt changes direction, height, or width.
Transition distance in a conveyor belt refers to the length over which the belt changes from one configuration to another. This can involve a change in belt width, the transition from a flat belt to a trough shape, or adjustments in the belt’s alignment. The transition distance is critical for ensuring the smooth movement of the conveyor belt and the material it carries. Properly managing the transition distance helps in reducing the stress on the belt and the associated components, thus preventing damage and extending the system’s lifespan. The calculation of transition distance takes into account factors such as the belt’s width, speed, tension, and the type of material being conveyed. Adequate transition distance ensures that the belt can accommodate these changes without causing undue stress or misalignment.
Conveyor systems use various types of idlers, each serving a specific purpose to support and guide the conveyor belt. The main types of idlers include:
Carrying Idlers: These idlers are positioned along the carrying side of the belt and support the loaded belt. They help maintain the belt’s shape and provide stability to the conveyed material.
Return Idlers: Located on the return side of the belt, these idlers support the empty belt on its way back to the tail end of the conveyor. They help reduce belt sag and ensure smooth movement.
Impact Idlers: Installed at loading points, impact idlers are designed to absorb the impact of falling material, protecting the belt from damage and extending its lifespan.
Self-Aligning Idlers: These idlers help in keeping the belt centered on the conveyor frame. They automatically adjust to correct any misalignment of the belt, preventing side spillage and reducing wear.
Transition Idlers: Used in the transition areas where the conveyor belt changes its shape, these idlers support the belt and ensure a smooth transition from one section to another.
An idler in a belt conveyor is a crucial component that supports the conveyor belt and the material carried on it. Idlers are typically cylindrical rollers that are installed at regular intervals along the length of the conveyor. They play a significant role in maintaining the belt’s alignment, reducing friction, and supporting the weight of the conveyed materials. Idlers can be categorized into different types based on their position and function within the conveyor system.
For instance, carrying idlers support the loaded belt on the carrying side, while return idlers support the empty belt on its return side. Impact idlers are placed at loading points to absorb the impact of falling material, protecting the belt from damage. Self-aligning idlers help in correcting any belt misalignment, ensuring smooth and efficient operation. Transition idlers are used in areas where the belt transitions from one shape to another, such as from a flat to a trough configuration. Overall, idlers are essential for the reliable and efficient operation of belt conveyor systems, ensuring minimal wear and tear on the belt and extending its service life.
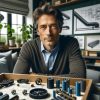
Jordan Smith, a seasoned professional with over 20 years of experience in the conveyor system industry. Jordan’s expertise lies in providing comprehensive solutions for conveyor rollers, belts, and accessories, catering to a wide range of industrial needs. From initial design and configuration to installation and meticulous troubleshooting, Jordan is adept at handling all aspects of conveyor system management. Whether you’re looking to upgrade your production line with efficient conveyor belts, require custom conveyor rollers for specific operations, or need expert advice on selecting the right conveyor accessories for your facility, Jordan is your reliable consultant. For any inquiries or assistance with conveyor system optimization, Jordan is available to share his wealth of knowledge and experience. Feel free to reach out at any time for professional guidance on all matters related to conveyor rollers, belts, and accessories.