Maintenance Tips for Chevron Conveyor Belt Material
Chevron conveyor belt material features unique “V” or “U” shaped patterns, essential for preventing material slippage on steep inclines. This design is pivotal in conveyor systems where standard flat belts fail to provide adequate grip, particularly in the mining, agriculture, and recycling industries. The selection of the right material for chevron conveyor belts is crucial, as it directly influences their efficiency and durability. Materials are chosen based on the nature of the materials transported, environmental factors, and the conveyor’s angle of operation. Optimal material selection not only maximizes the functionality of chevron conveyor belts but also extends their lifespan, ensuring they meet stringent industry demands.
What is Specifications of Chevron Conveyor Belt Material for Optimal Performance?
Chevron conveyor belt material is engineered to meet specific requirements and standards that ensure optimal functionality under diverse operational conditions. These specifications vary widely, addressing factors such as the height and width of the chevron patterns, the spacing between them, and the overall thickness and width of the belt. Each of these elements is crucial as they determine the belt’s capacity to handle varying volumes and types of materials without slippage.
Material choice in chevron conveyor belts significantly impacts their performance and durability. For instance, rubber materials are commonly used due to their resilience and ability to form high-relief patterns necessary for gripping large lumps of material. However, for environments involving oils, chemicals, or extreme temperatures, specialized materials such as PVC or polyurethane are preferred to enhance resistance and longevity. These materials are selected based on their ability to withstand wear, tear, and environmental challenges, thereby ensuring that the chevron conveyor belt material not only meets the required specifications but also exceeds the operational demands of industries reliant on efficient bulk material handling.
Identifying Top Suppliers of Chevron Conveyor Belt Material for Industry Needs
When selecting chevron conveyor belt material, identifying top suppliers who stand out in terms of material quality and innovation is crucial. These suppliers not only offer materials that meet rigorous industry standards but also bring continuous advancements in the technology and composition of their conveyor belts. Notable suppliers excel in providing durable, high-grip chevron patterns crafted from superior rubber or synthetic compounds tailored to specific environmental and operational demands.
Choosing the right supplier for chevron conveyor belt material involves considering several key factors:
- Material Quality: The supplier should have a proven track record of delivering high-quality materials that can withstand the specific conditions of your industry, whether that involves resistance to abrasion, chemicals, or temperature extremes.
- Innovation: Look for suppliers who are leaders in developing new materials and belt designs that can increase the efficiency and lifespan of conveyor systems.
- Industry Expertise: The best suppliers understand diverse industrial needs and offer customized solutions that align with particular material handling requirements.
- Customer Support: Effective suppliers provide excellent customer service, offering guidance on belt selection, installation, and maintenance.
Material Comparison and Applications: Chevron vs. Rough Top Conveyor Belt Materials
Chevron and rough top conveyor belts are designed to address different material handling challenges, each utilizing distinct material properties to optimize performance in specific environments. Chevron conveyor belt material typically features high-profile patterns such as ‘V’ or ‘U’ shapes, which provide excellent grip for transporting materials on inclines, preventing slippage and roll-back. These belts are commonly made from rubber compounds that offer flexibility and durability under stress, making them suitable for industries like mining and agriculture where large volumes of material need to be moved vertically.
On the other hand, rough top conveyor belts are characterized by a textured surface that also enhances grip but in a less aggressive manner than the chevron patterns. This texture is often achieved through materials like PVC or coated fabrics, which provide a softer interface for handling packages or delicate items in industries such as packaging or manufacturing. The rough texture ensures stability and reduces the risk of items shifting or sliding during transit on slight inclines or flat surfaces.
Choosing Between Chevron and Rough Top Conveyor Belts:
Feature | Chevron Conveyor Belt Material | Rough Top Conveyor Belt Material |
---|---|---|
Design & Pattern | High-profile 'V' or 'U' shapes for excellent grip on inclines | Textured surface for enhanced grip on slight inclines |
Material Composition | Typically rubber compounds for durability and flexibility | Often PVC or coated fabrics for softer handling |
Ideal Usage | Suitable for steep inclines in mining and agriculture | Best for gentle handling in packaging and manufacturing |
Material Handling | Prevents slippage and roll-back of materials | Reduces the risk of items shifting during transport |
Incline Suitability | Preferred for steep inclines due to high grip | More suitable for slight inclines or flat surfaces |
Handling Characteristics | Handles bulky or heavy materials effectively | Protects products from damage during transport |
Durability and Flexibility | High resilience against extreme conditions | Prioritizes surface texture over structural robustness |
Maximizing Conveyor Efficiency: The Role of Chevron Conveyor Belt Material in Cleated Belt Conveyors
Cleated belt conveyors utilize raised elements or cleats to securely transport materials at various inclines without slippage. Chevron conveyor belt material plays a critical role in the effectiveness of these conveyors, especially where high grip and precise material placement are needed. The chevron pattern, with its distinctive ‘V’ and ‘U’ shapes, is integral in providing the additional traction required to hold materials in place during transport.
The material used to make chevron conveyor belts is predominantly rubber because of its flexibility, durability, and ability to form high-relief patterns that are essential for effective cleating. The rubber’s elasticity allows the belt to adapt to various loads and resist the mechanical pressures from the movement of bulky or abrasive materials. This adaptability is crucial for applications in industries such as mining, agriculture, and construction, where the belts face rigorous operating conditions.
Impact of Material Choice on Functionality:
- Traction and Load Stability: The choice of chevron conveyor belt material impacts how well the belt can maintain traction and load stability, especially on steep inclines. The higher the quality of the rubber, the better its performance in preventing slippage and speeding up operations.
- Wear Resistance: Material choice also affects the belt’s resistance to wear and tear. High-quality rubber materials can withstand repeated contact with rough materials, thereby extending the conveyor’s lifespan and reducing maintenance costs.
- Environmental Resistance: Depending on the operating environment, the rubber used in chevron conveyor belts may need to be resistant to oils, chemicals, or extreme temperatures. Specialized compounds like neoprene or nitrile rubber can be used to enhance the belt’s resistance to such conditions.
Enhancing Textile Conveyor Belt Performance: Innovations in Chevron Conveyor Belt Material
The evolution of textile conveyor belt materials has been marked by significant advancements that cater to more complex and demanding industrial environments. Chevron conveyor belt material, with its distinct patterned design, has been at the forefront of this innovation, enhancing the functionality of traditional textile belts.
Textile conveyor belts, traditionally made from layers of fabric such as cotton, nylon, or polyester, are known for their flexibility and lightweight properties. However, these materials often require additional features to handle specific industrial tasks effectively, especially in inclined or high-load situations. This is where the chevron pattern comes into play. The inclusion of chevron patterns on textile belts provides increased traction, prevents material rollback, and ensures a more stable transport of materials at various angles.
Impact of New Material Technologies on Textile Belts:
- High-Performance Fibers: The integration of high-performance synthetic fibers like Kevlar or Twaron has significantly improved the tensile strength and durability of textile conveyor belts. These fibers resist stretching and ensure the belts can handle heavier loads.
- Coating and Treatments: Advances in materials science have led to the development of special coatings and treatments for textile conveyor belts. These enhancements include chemical-resistant coatings and heat-resistant properties, which extend the belts’ operational life and broaden their application range.
- Hybrid Materials: The combination of traditional textiles with advanced polymers or rubber composites has produced hybrid conveyor belts. These belts benefit from the flexibility of textiles and the durability of heavier-duty materials, making them suitable for a variety of challenging conditions.
Chevron patterns, when applied to these advanced materials, further enhance the belts’ efficiency by adding the necessary grip and reducing slippage in critical applications such as steep incline conveyance and heavy material transport. This synergy between innovative materials and chevron designs encapsulates the ongoing evolution in the conveyor belt industry, driving higher performance and reliability in textile conveyor belts.
Exploring the Unique Material Composition of Trellex Conveyor Belts: The Chevron Conveyor Belt Material Advantage
Trellex conveyor belts are renowned for their distinctive material composition that makes them particularly suited for chevron patterns. These belts are designed to cater to demanding material handling needs, utilizing a specialized rubber compound that is both durable and flexible. This rubber compound is engineered to form high-relief chevron patterns that are integral to the belt’s functionality, especially in applications involving steep inclines where material slippage is a concern.
The material composition of Trellex conveyor belts is carefully selected to enhance the structural integrity and longevity of the belts. The rubber used is typically of a higher quality than standard conveyor belts, incorporating resistance to wear, tear, and environmental factors like heat, cold, and chemicals. This makes Trellex belts particularly effective in harsh industrial environments where other belts might degrade more quickly.
Here is an overview of the key features of Trellex conveyor belts and the associated benefits:
Feature | Description | Benefits |
---|---|---|
Material Composition | High-quality rubber compound tailored for durability and flexibility. | Extended belt life, reducing replacement costs. |
Chevron Pattern Design | Engineered high-relief chevron patterns integral for preventing slippage on inclines. | Improved material handling efficiency and throughput. |
Environmental Resistance | Materials selected for resistance to wear, tear, heat, cold, and chemicals. | Suitable for harsh industrial environments. |
Adaptability | Customizable material properties to suit specific operational needs across various industries. | Ensures optimal performance under diverse conditions. |
The Impact of Material on Calculating Chevron Conveyor Belt Material Weight and System Efficiency
The weight of a conveyor belt is a crucial factor in the design and efficiency of a conveyor system. The material used in chevron conveyor belt material not only determines its durability and suitability for specific applications but also significantly influences its overall weight. This is especially important because the weight impacts the energy consumption and the mechanical stress placed on the conveyor system’s structure and drive components.
Chevron patterns, which provide higher grip and stability for material transport, especially on inclines, are typically made from heavier materials such as rubber. This material choice, while excellent for traction and wear resistance, contributes to a greater overall weight of the conveyor belt compared to smoother and lighter materials like PVC or fabric.
Guidelines for Calculating Weight of Chevron Conveyor Belt Material:
- Determine Material Density: Start by identifying the density of the conveyor belt material, typically expressed in pounds per cubic foot (lb/ft³) or kilograms per cubic meter (kg/m³). Rubber, for example, has a higher density compared to other materials like fabric or PVC.
- Measure Belt Dimensions: Measure the length, width, and thickness of the conveyor belt. For chevron conveyor belts, include the height of the chevron profiles as they add to the overall volume of material.
- Calculate Volume: Multiply the length, width, and total thickness (including chevron profiles) to find the volume of the material.
- Compute Weight: Multiply the volume by the density of the material to find the overall weight of the conveyor belt.
Understanding the weight of chevron conveyor belt material is essential for designing an efficient conveyor system. Heavier belts may require more powerful motors and stronger structural components to handle the added weight, impacting the system’s operational costs and energy efficiency. Conversely, optimizing the material composition and thickness can lead to significant savings in terms of energy consumption and maintenance costs.
Incorporating these calculations early in the system design process helps ensure that the conveyor is suitably equipped to handle the expected loads without excessive wear or energy use, ultimately leading to a more cost-effective and reliable system.
FAQs aobut Chevron Sonveyor Belt Material
Conveyor belts can be made from a variety of materials, each selected based on the specific requirements of the application and environment in which the belt will operate. The most commonly used materials include rubber, PVC, polyurethane, and fabric such as nylon or polyester. Rubber conveyor belts are prized for their durability and flexibility, making them suitable for a wide range of conditions, including abrasive and heavy materials. PVC belts are popular in food industry applications due to their resistance to chemicals and easy cleaning. Polyurethane belts offer excellent resistance to wear, oil, and grease, whereas fabric belts are typically used in applications that require a high degree of flexibility and are lighter in weight. Each material provides different advantages such as resistance to abrasion, chemical resistance, and suitability for food-grade applications.
Chevron rubber refers to the type of rubber used in the production of chevron conveyor belts, which are characterized by patterns of raised “V,” “U,” or “C” shapes on their surface. These patterns, or cleats, help in preventing the slippage of materials being transported on inclined planes. The rubber used in chevron belts is generally more robust and durable compared to other types of conveyor belt materials. It is designed to withstand the rough handling of materials like aggregates, coal, or minerals that could otherwise cause slippage or spillage. Chevron rubber is essential in applications where increased traction is required, making it ideal for industries such as mining, agriculture, and recycling, where belts need to handle bulk materials at inclines.
Conveyors can be constructed using a wide range of materials, depending on the specific needs of the operation and the materials being handled. The primary materials include metals such as steel and aluminum, plastics, rubber, and various textile materials. Steel is often used for its strength and durability, making it suitable for heavy-duty applications and environments with high temperatures. Aluminum offers a lighter weight alternative that is also resistant to corrosion, making it ideal for food processing applications. Plastics such as polyethylene, polypropylene, and PVC are used for their versatility and cost-effectiveness, suitable for lighter applications and where corrosion resistance is necessary. Textiles and fabrics are used in conveyor belts where flexibility is more critical than durability. Each material brings its own set of properties to the conveyor system, influencing factors like weight, speed, load capacity, and maintenance needs.
Metals used in conveyor belts primarily include steel and stainless steel. Steel is favored for its high strength and durability, making it ideal for heavy-load carrying and high-speed applications. It is commonly used in mining, milling, and heavy manufacturing industries. Stainless steel is preferred where corrosion resistance is crucial, such as in food processing or chemical industries. Stainless steel conveyor belts resist rust and are easy to clean, ensuring compliance with hygiene standards and preventing contamination. Additionally, some conveyor systems use aluminum because of its lighter weight, which reduces the load on the conveyor’s motor and can be beneficial in applications such as packaging or assembly lines where heavy strength is not a primary requirement.
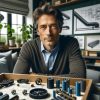
Jordan Smith, a seasoned professional with over 20 years of experience in the conveyor system industry. Jordan’s expertise lies in providing comprehensive solutions for conveyor rollers, belts, and accessories, catering to a wide range of industrial needs. From initial design and configuration to installation and meticulous troubleshooting, Jordan is adept at handling all aspects of conveyor system management. Whether you’re looking to upgrade your production line with efficient conveyor belts, require custom conveyor rollers for specific operations, or need expert advice on selecting the right conveyor accessories for your facility, Jordan is your reliable consultant. For any inquiries or assistance with conveyor system optimization, Jordan is available to share his wealth of knowledge and experience. Feel free to reach out at any time for professional guidance on all matters related to conveyor rollers, belts, and accessories.