The Function of Bias Angle of Conveyor Belt & 7 Tips
Understanding the bias angle of conveyor belt splicing is crucial in ensuring the durability and efficiency of a conveyor system. This angle, pivotal in the splicing process, significantly influences the strength and longevity of a conveyor belt splice. The correct bias angle of conveyor belt splicing not only enhances the splice’s integrity but also ensures uniform stress distribution across the belt. This introduction delves into the technicalities of the bias angle, highlighting its role in optimizing conveyor belt performance and preventing premature failures. By mastering the bias angle, technicians can ensure a seamless and robust bond, essential for the smooth operation of conveyor systems in various industrial applications.
The Concept of Bias Angle of Conveyor Belt Splicing
What is the Bias Angle of Conveyor Belt
The bias angle in conveyor belt splicing is a fundamental concept that plays a crucial role in the effectiveness and durability of a conveyor belt joint. This angle is not just a mere measurement; it’s a critical aspect of conveyor belt design and maintenance that ensures the longevity and efficiency of the belt in operation.
Definition and Importance
- Definition: The bias angle in conveyor belt splicing refers to the angle at which the splice is cut in relation to the belt’s longitudinal axis. This angle is typically measured in degrees.
- Purpose: The primary purpose of the bias angle is to increase the splice length, thereby distributing the stress over a larger area. This distribution of stress is crucial for reducing the concentration of tension at the splice, which is often the weakest point in a conveyor belt.
Role in Conveyor Belt Joint Integrity
- Stress Distribution: A correctly calculated bias angle helps in even distribution of mechanical stresses across the splice, especially during the flexing of the belt over pulleys and rollers.
- Joint Longevity: By reducing stress concentration, the bias angle extends the life of the belt joint, preventing premature failures and reducing downtime for repairs.
- Efficiency in Operation: A well-spliced belt with an optimal bias angle ensures smooth operation, minimizes belt tracking issues, and maintains consistent belt tension.
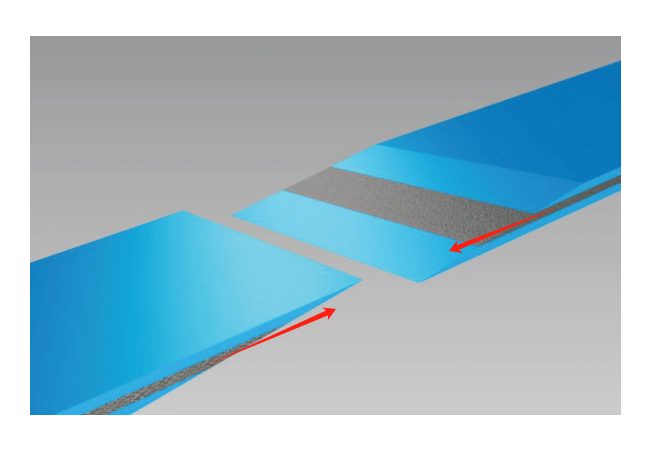
Conveyor Belt Splicing
Factors Influencing Bias Angle Selection
- Belt Thickness and Width: Thicker and wider belts require a larger bias angle to adequately distribute stress.
- Material Handled: The nature of the material being conveyed can influence the required bias angle. Heavier and more abrasive materials may necessitate a different angle compared to lighter materials.
- Conveyor Design: The design of the conveyor system, including pulley diameters and the distance between idlers, also plays a role in determining the appropriate bias angle.
The bias angle of conveyor belt is a critical factor in splicing, directly impacting the belt’s operational integrity and longevity. Understanding and correctly implementing the bias angle is essential for maintaining the efficiency and reliability of conveyor belt systems.
Measuring the Bias Angle of Conveyor Belt
Accurate Measurement of the Bias Angle in Conveyor Belt Splicing
Measuring the bias angle of conveyor belt is a critical step in the splicing process, ensuring the longevity and efficiency of the belt. This section provides a detailed guide on how to accurately measure the bias angle and underscores the importance of precision in this measurement for optimal splicing results.
Step-by-Step Guide to Measuring Bias Angle
- Preparation: Ensure the conveyor belt is clean and laid out flat. Remove any irregularities or damage from the area where the splice will be made.
- Marking the Belt: Using a straight edge, draw a line perpendicular to the belt’s edge at the point where the splice will begin. This line represents the belt’s longitudinal axis.
- Determining the Desired Angle: Based on the belt’s width, thickness, and operational parameters, determine the required bias angle (commonly between 18° to 30°).
- Drawing the Bias Line: From the point where the perpendicular line meets the belt edge, use a protractor to measure the determined bias angle and draw the bias line across the belt. This line will guide the splice cut.
- Double-Checking Measurements: Verify the angle using a second measurement method or tool to ensure accuracy.
Importance of Precision in Measurement
- Impact on Splice Strength: Inaccurate measurements can lead to uneven stress distribution along the splice, weakening the joint and increasing the risk of failure.
- Operational Efficiency: A precisely measured bias angle contributes to the smooth running of the belt, reducing maintenance needs and operational disruptions.
- Longevity of the Belt: Accurate bias angle measurement extends the life of the belt by ensuring the splice can handle the mechanical stresses during operation.
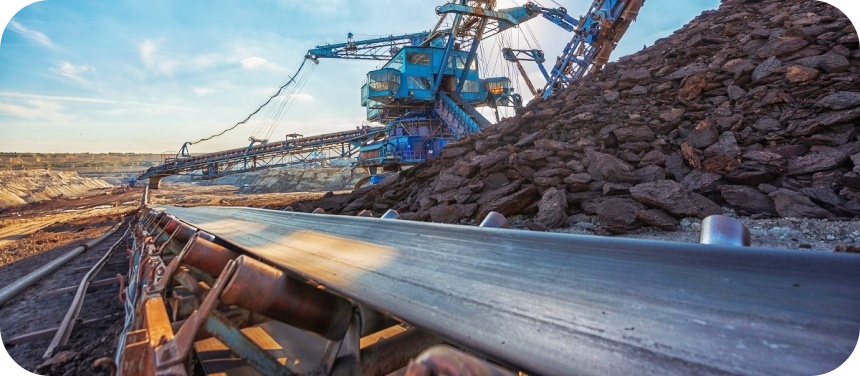
Tools and Techniques for Accurate Measurement
- Use of Protractors and Angle Finders: These tools help in accurately determining and marking the bias angle on the belt.
- Digital Measurement Tools: Advanced digital tools and software can provide more precise measurements and are particularly useful for large-scale or complex conveyor systems.
Accurate measurement of the bias angle is a fundamental aspect of conveyor belt splicing. It requires careful attention to detail and the use of appropriate tools to ensure the splice is strong, efficient, and durable. This precision directly impacts the overall performance and longevity of the conveyor belt.
Calculating the Bias Angle of Conveyor Belt: Formulas and Considerations
What is the Calculation of Bias Angle of Conveyor Belt
The calculation of the bias angle is a critical step in conveyor belt splicing, ensuring the splice’s strength and durability. This section introduces the formulas used to calculate the bias angle and discusses the factors influencing this calculation, including belt width and thickness.
Introduction to Bias Angle Calculation Formulas
- Basic Formula: The bias angle is typically calculated using the formula: Bias Angle = arctan(Belt Width / Splice Length). This formula helps determine the angle at which the splice should be cut relative to the belt’s longitudinal axis.
- Adjustments for Belt Thickness: For thicker belts, adjustments to the formula may be necessary to account for the increased material volume, which can affect the splice’s integrity.
Factors Influencing Bias Angle Calculation
- Belt Width: Wider belts generally require a larger bias angle to ensure that the splice length is sufficient to distribute stress evenly.
- Belt Thickness: Thicker belts may require a steeper bias angle to accommodate the additional material at the splice point.
- Material Handled and Operational Conditions: The type of material the conveyor belt transports and the operational conditions (e.g., speed, load) can influence the required bias angle to ensure optimal performance and longevity.
Practical Considerations in Bias Angle Calculation
- Splice Length: The desired length of the splice is a key factor in determining the bias angle. A longer splice length typically requires a larger bias angle.
- Precision in Calculation: Accurate calculation of the bias angle is crucial for the effectiveness of the splice. Errors in calculation can lead to weak points in the belt and reduced operational efficiency.
- Use of Calculation Tools: Various tools and software are available to assist in accurately calculating the bias angle, providing more precision than manual calculations.
Calculating the bias angle of conveyor belt splicing is a process that requires careful consideration of various factors, including belt width, thickness, and operational conditions. Accurate calculation is essential for creating a strong and durable splice that can withstand the demands of everyday operation.
Conveyor Belt Splicing Procedures and Bias Angle
Integrating Bias Angle of Conveyor Belt Splicing
The integration of the bias angle of conveyor belt splicing is a crucial aspect of ensuring the strength and longevity of the belt joint. This section provides a detailed overview of standard conveyor belt splicing procedures and explains how the bias angle is incorporated into these procedures for different types of conveyor belt joints.
Overview of Standard Conveyor Belt Splicing Procedures
- Preparation: This involves cleaning the belt ends, removing any damaged areas, and squaring the belt ends.
- Measuring and Cutting: Based on the calculated bias angle, the belt ends are cut at the appropriate angle to ensure a proper splice.
- Applying Splice Materials: Depending on the type of splice (mechanical or vulcanized), different materials like adhesives, fasteners, or vulcanizing materials are applied.
- Joining the Belt Ends: The belt ends are carefully aligned and joined. For vulcanized splices, this involves applying heat and pressure.
Role of Bias Angle in Splicing Procedures
- Stress Distribution: The bias angle ensures that the stress at the joint is distributed over a larger area, reducing the risk of splice failure.
- Joint Integrity: A correctly calculated and implemented bias angle contributes to the overall integrity and strength of the joint.
- Belt Alignment: Proper bias angle cutting helps maintain belt alignment, reducing tracking issues and uneven wear.
Different Types of Conveyor Belt Joints and Bias Angle
- Mechanical Fastening: In mechanical splicing, the bias angle helps ensure that the fasteners properly grip the belt, providing a secure joint.
- Vulcanized Splicing: For vulcanized splices, the bias angle is critical in ensuring a seamless and strong bond between the belt ends.
Best Practices in Splicing with Bias Angle Consideration
- Accurate Measurement and Cutting: Precision in measuring and cutting the belt at the correct bias angle is essential for a successful splice.
- Skilled Technicians: Experienced technicians are crucial in accurately applying the bias angle during the splicing process.
- Quality Control: Post-splicing inspections should verify that the bias angle was correctly implemented and that the splice meets all operational requirements.
The bias angle plays a significant role in conveyor belt splicing, impacting the joint’s strength, durability, and operational efficiency. Adhering to standard splicing procedures while accurately integrating the bias angle is key to ensuring the long-term performance of conveyor belts.
Seven Conveyor Belt Splicing Tips And Procedures
Conveyor belt splicing is a critical procedure that joins two pieces of a conveyor belt together, aiming to restore the belt to its original strength and flexibility. Proper splicing is essential for the efficiency and longevity of a conveyor system. Here are seven tips and procedures for effective conveyor belt splicing:
1. Choose the Right Splice Method
There are two main types of splicing methods: mechanical splicing and vulcanization splicing. Mechanical splicing involves using metal hinges or plates to join the belt ends, while vulcanization splicing involves the use of heat, pressure, and a vulcanizing agent to bond the belt ends together. The choice between these methods depends on various factors, including the type of belt material, the application’s demands, and the operating environment.
2. Prepare the Belt Ends Properly
Preparation of the belt ends is crucial for a successful splice. This includes squarely cutting the ends to ensure they align perfectly. For a vulcanized splice, the top and bottom surfaces of the belt ends must be carefully buffed to remove any impurities and to create a smooth surface for bonding.
3. Measure and Cut the Bias Angle Correctly
As mentioned earlier, cutting the belt ends at a bias angle increases the splice’s strength and durability. The angle typically ranges between 22 and 30 degrees. Accurate measurement and cutting are essential for ensuring the splice will be effective.
4. Apply Splicing Materials Correctly
For vulcanized splicing, applying the correct type and amount of vulcanizing agent is critical. Ensure that the adhesive is compatible with the belt material and that it is applied evenly across the entire splice area. For mechanical splicing, ensure that the fasteners are compatible with the belt material and that they are installed according to the manufacturer’s specifications.
5. Use Proper Splicing Tools and Equipment
Using the correct tools and equipment for splicing is essential for achieving a high-quality joint. This includes tools for cutting and buffing the belt, as well as presses and heating elements for vulcanized splicing. Ensure that all equipment is in good working order and that it is suitable for the specific belt material and splice method being used.
6. Follow the Correct Splicing Procedure
Each splice method and belt material has a specific procedure that must be followed to ensure the splice’s integrity. This includes the correct sequence of applying adhesives, aligning the belt ends, applying pressure and heat (for vulcanized splices), and curing times. Always follow the manufacturer’s guidelines or consult with a professional if unsure.
7. Test the Splice
After completing the splice, it is important to test it before putting the conveyor belt back into full operation. This can include visual inspections, running the belt empty to ensure it tracks correctly, and load testing to verify the splice can handle the operational stresses. Address any issues immediately to ensure the longevity and efficiency of the conveyor system.
By following these tips and procedures, you can ensure that your conveyor belt splicing is performed effectively, contributing to the smooth and efficient operation of your conveyor system.
Bias Angle of Conveyor Belt Splicing Standards and Best Practices
Adhering to Standards in Conveyor Belt Splicing
In the world of conveyor belt maintenance, splicing is a critical operation that demands adherence to specific standards and best practices. The bias angle plays a significant role in this process. This section explores the current standards and best practices in conveyor belt splicing and the importance of the bias angle in ensuring the durability and efficiency of the belt joint.
Overview of Conveyor Belt Splicing Standards
- International and Regional Standards: Standards such as ISO, DIN, and ASTM provide guidelines on conveyor belt splicing, including methods, materials, and safety considerations.
- Manufacturer Specifications: Conveyor belt manufacturers often provide specific splicing recommendations that align with the design and material of their belts.
Best Practices in Conveyor Belt Splicing
- Proper Training and Skill: Technicians performing splicing should be well-trained and experienced in the procedure, understanding the critical role of the bias angle.
- Quality of Splicing Materials: Use high-quality adhesives, fasteners, and vulcanizing materials to ensure the splice’s strength and longevity.
- Environmental Conditions: Perform splicing in a controlled environment to prevent contamination and ensure optimal adhesion and curing.
Role of Bias Angle in Meeting Standards
- Stress Distribution and Joint Integrity: A correctly calculated and applied bias angle is essential for meeting standards related to joint strength and durability.
- Alignment and Tracking: Proper implementation of the bias angle helps maintain belt alignment, reducing the risk of tracking issues and uneven wear.
- Longevity of the Splice: Adhering to standards regarding the bias angle extends the life of the splice, minimizing downtime and maintenance costs.
Trust our conveyor belts for unmatched durability and efficiency.
Ensuring Compliance with Standards
- Regular Training and Updates: Technicians should receive ongoing training and updates on the latest standards and best practices in conveyor belt splicing.
- Inspection and Quality Control: Post-splicing inspections should ensure that the splice meets all relevant standards and performs as expected under operational conditions.
- Documentation and Record-Keeping: Maintain detailed records of splicing procedures, materials used, and technicians involved for quality assurance and compliance purposes.
Bias angle of conveyor belt splicing standards and best practices are crucial for ensuring the effective operation and longevity of conveyor belts. The bias angle is a key factor in these standards, playing a vital role in the strength, alignment, and overall performance of the spliced belt.
Bias Angle of Conveyor Belt: Types of Conveyor Belt Joints and Their Bias Angles
Diversity in Conveyor Belt Joint Types and the Role of Bias Angle
Conveyor belt joints are pivotal in determining the efficiency and lifespan of a conveyor belt. The type of joint used and the corresponding bias angle can significantly impact the belt’s performance. This section describes various types of conveyor belt joints and analyzes how the bias angle varies across these joint types, affecting conveyor belt performance.
Common Types of Conveyor Belt Joints
- Mechanical Fastening: This method involves using metal fasteners to join the belt ends. The bias angle in mechanical fastening is crucial for ensuring the fasteners grip the belt properly.
- Vulcanized Splicing: Vulcanization creates a seamless joint by chemically bonding the belt ends. The bias angle in vulcanized splicing is critical for a uniform bond and stress distribution.
- Cold Bonding: This method uses adhesives to join the belt ends. The bias angle in cold bonding helps in achieving a strong bond and even stress distribution along the splice.
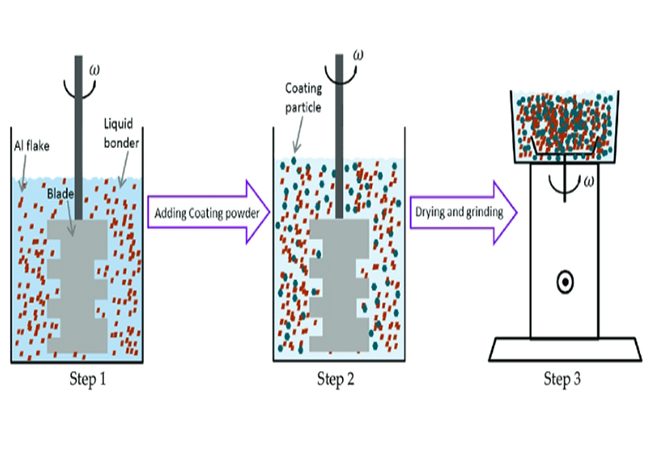
Cold Bonding
The Function of A Bias Angle in A Conveyor Belt Joint
The bias angle in a conveyor belt joint serves a crucial role in enhancing the strength and durability of the joint. When two ends of a conveyor belt are joined, cutting the ends at a bias angle (diagonally) rather than straight across has several benefits:
- Increased Splice Life: The diagonal splice spreads the stress over a larger area of the belt. This distribution of tension helps reduce the concentration of stress at any one point in the splice, leading to less wear and tear on the joint.
- Improved Flexibility: A bias-cut joint is more flexible, allowing the belt to navigate pulleys and transitions more smoothly. This flexibility is especially beneficial in systems where the belt needs to go through curves or change directions.
- Reduced Noise and Vibration: The smoother transition through rollers and pulleys also contributes to reduced noise and vibration in the conveyor system. This is because the joint does not create as much interruption as a straight-cut joint might.
- Enhanced Strength: The bias angle increases the bond area of the splice, thereby enhancing the overall strength of the joint. This is particularly important in heavy-duty applications where the belt is subject to high loads and stress.
- Minimized Risk of Edge Fraying: The angled joint helps to reduce the risk of the belt edges fraying over time. This is because the diagonal cut offers a more continuous path for the belt to flex and move without creating points of concentrated stress.
The specific bias angle chosen can vary depending on the belt material, the type of splice used, and the specific application requirements. However, common angles range between 22 and 30 degrees, optimized to balance strength, durability, and operational smoothness of the conveyor belt system.
Impact of Bias Angle on Different Joint Types
- Mechanical Fastening: A correct bias angle ensures that the fasteners provide an even clamping force across the belt width, reducing the risk of belt damage or splice failure.
- Vulcanized Splicing: The bias angle in vulcanized splicing affects the splice’s integrity, ensuring the joint can handle the belt’s tensile forces without separating.
- Cold Bonding: In cold bonding, the bias angle contributes to the overall strength of the adhesive joint, especially important in high-tension applications.
Considerations for Bias Angle in Different Joints
- Belt Thickness and Width: Thicker and wider belts may require a larger bias angle in all types of joints to accommodate the increased material volume at the splice.
- Operational Conditions: The operating conditions, such as load, speed, and material type, influence the required bias angle to ensure the joint withstands operational stresses.
The type of bias angle of conveyor belt joint and the corresponding bias angle are integral to the belt’s operational efficiency and longevity. Understanding the relationship between different joint types and the bias angle is essential for selecting the most suitable splicing method for a given application.
FAQs about Bias Angle of Conveyor Belt
The angle of a conveyor belt, often referred to as the maximum incline angle, is the steepest angle at which a belt conveyor can transport materials effectively without slippage or spillage. For flat belt conveyors, this angle typically ranges from 0 to 28 degrees. However, for large inclination belt conveyors, designed specifically for steeper angles, the conveying angle can be as much as 90 degrees.
The angle of repose in the context of a belt conveyor refers to the maximum angle at which material can rest on the conveyor belt without sliding down. This angle is determined by the properties of the material being conveyed, such as its density, size, and moisture content. The angle of repose is a critical factor in designing conveyor systems, as it affects the choice of belt type, conveyor inclination, and sidewall height.
The angle of surcharge on a conveyor belt refers to the angle to the horizontal which the surface of the material assumes while the material is at rest on a moving conveyor belt. This angle usually is 5 degrees to 15 degrees less than the angle of repose, though in some materials it may be as much as 20 degrees less. It is an important factor in determining the cross-sectional area of the load on the conveyor belt and, consequently, the belt’s capacity.
The trough angle of a belt conveyor is the angle formed by the edge of the belt in the troughed or carrying position. Common trough angles are 20, 35, and 45 degrees, although other angles are also used. The choice of trough angle is influenced by the properties of the material being conveyed, the capacity required, and the conveyor’s overall design. A larger trough angle increases the carrying capacity of the belt but may require more power to operate and can cause more wear on the belt.
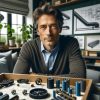
Jordan Smith, a seasoned professional with over 20 years of experience in the conveyor system industry. Jordan’s expertise lies in providing comprehensive solutions for conveyor rollers, belts, and accessories, catering to a wide range of industrial needs. From initial design and configuration to installation and meticulous troubleshooting, Jordan is adept at handling all aspects of conveyor system management. Whether you’re looking to upgrade your production line with efficient conveyor belts, require custom conveyor rollers for specific operations, or need expert advice on selecting the right conveyor accessories for your facility, Jordan is your reliable consultant. For any inquiries or assistance with conveyor system optimization, Jordan is available to share his wealth of knowledge and experience. Feel free to reach out at any time for professional guidance on all matters related to conveyor rollers, belts, and accessories.