The Essential Guide to Aggregate Conveyor Rollers
Aggregate conveyor rollers play a pivotal role in the material handling sector, serving as the backbone of conveyor systems across various industries such as mining, construction, and aggregate production. These rollers are designed to facilitate the smooth and efficient transport of materials like sand, gravel, and crushed stone, which are essential components in construction and manufacturing processes. The efficiency and productivity of conveyor systems heavily rely on the quality and performance of these rollers. By ensuring the stable and continuous movement of materials, aggregate conveyor rollers significantly reduce operational downtime and enhance the overall throughput of the conveyor system. Their importance cannot be overstated, as they directly impact the operational efficiency of industries that depend on bulk material handling.
Types of Aggregate Conveyor Rollers
The realm of material handling is diverse, and the types of aggregate conveyor rollers used can significantly impact the efficiency and longevity of a conveyor system. Here’s a closer look at the various types of aggregate conveyor rollers and their specific roles:
Type of Roller | Description | Function |
---|---|---|
Carrying Rollers | These are the most common type of aggregate conveyor rollers, positioned along the length of the conveyor to support the belt and the material being transported. | They provide a smooth surface for the belt to roll over, reducing friction and wear. |
Return Rollers | Positioned under the conveyor belt on the return side, these rollers support the belt as it loops back to the beginning of the conveyor system. | They help to maintain belt tension and prevent sagging, ensuring smooth operation. |
Self-Aligning Rollers | Designed to pivot and rotate, self-aligning rollers are used to correct any misalignment of the conveyor belt. | They ensure the belt remains centered, reducing the risk of edge damage or spillage. |
Impact Rollers | Located at loading points where material is dropped onto the belt, impact rollers are designed to absorb the shock and distribute the load, minimizing damage to the belt. | They extend the life of the conveyor belt by reducing the impact of heavy or sharp materials. |
Conveyor Troughing Rollers | These rollers are configured in a trough shape to cradle the belt, increasing its carrying capacity by keeping the material centered. | Troughing rollers are essential for maintaining belt alignment and preventing spillage, especially in bulk material handling. |
Conveyor Idlers | Idlers refer to rollers that are used in various configurations to support the belt and material load. They can be part of carrying, return, impact, or troughing roller assemblies. | They play a crucial role in the overall support and efficiency of the conveyor system, reducing wear and facilitating smooth belt movement. |
Understanding the types of aggregate conveyor rollers and their specific functions is crucial for optimizing the performance and durability of a conveyor system. Each type of roller is designed to address particular challenges in material handling, ensuring that the conveyor operates smoothly and efficiently, with minimal downtime and maintenance requirements.
Key Manufacturers and Suppliers of Aggregate Conveyor Rollers
The market for aggregate conveyor rollers is served by a number of key manufacturers and suppliers, each known for their commitment to quality, innovation, and customer service. Among these, eight stand out for their exceptional products and services in the field of material handling and conveyor systems:
- SKE Industries: Renowned for their comprehensive range of conveyor rollers and idlers, SKE Industries offers solutions tailored to various operational needs, including heavy-duty applications in the aggregate sector. Their products are designed for durability and efficiency, ensuring minimal downtime for maintenance.
- Precision Pulley & Idler (PPI): PPI is a leader in the design and manufacture of high-quality conveyor components, including an extensive range of rollers. The PPI roller catalog showcases a variety of products engineered for performance and longevity, making them a preferred choice for aggregate handling systems.
- Superior Industries: Known for innovative conveyor solutions, Superior Industries provides a wide array of conveyor rollers designed to withstand the demanding conditions of aggregate processing and handling.
- Martin Sprocket & Gear: With a focus on reliability and performance, Martin Sprocket & Gear manufactures conveyor rollers that are built to last, ensuring smooth operations in aggregate handling environments.
- Rexnord: Offering a broad spectrum of conveyor components, Rexnord’s rollers are engineered for efficiency and durability, catering to the rigorous demands of aggregate processing.
- Mellott Company: Specializing in the aggregate industry, Mellott Company supplies high-quality conveyor rollers that are designed to enhance the efficiency of material handling systems.
- Conveyor Components Company: This company is known for its comprehensive range of conveyor accessories, including rollers that are specifically designed for aggregate handling, ensuring optimal system performance.
- Douglas Manufacturing: Douglas Manufacturing offers a wide range of conveyor components, including rollers that are tailored for the aggregate industry, emphasizing durability and operational efficiency.
Each of these manufacturers and suppliers brings something unique to the table, from SKE Industries’ tailored solutions to the extensive range of products in the PPI roller catalog. Their commitment to quality and innovation ensures that businesses in the aggregate sector can find the perfect conveyor rollers to meet their specific needs, enhancing system performance and productivity.
Customization and Engineering Solutions for Aggregate Conveyor Rollers
In the realm of aggregate conveyor rollers, customization and engineering solutions play pivotal roles in optimizing system performance and addressing specific operational challenges. Companies like SKE Industries and SCG Supplies stand at the forefront of providing custom-made rollers, tailored to meet the unique requirements of each application within the aggregate industry. These bespoke solutions ensure that conveyor systems operate at peak efficiency, with minimal downtime and maximum productivity.
Here are ten critical roles that engineering solutions fulfill in enhancing the performance of aggregate conveyor systems:
- Belt Alignment: Custom-engineered rollers are designed to maintain optimal belt alignment, preventing drift and reducing wear and tear on the conveyor belt.
- Load Distribution: Engineering solutions ensure that rollers are positioned and designed to distribute the load evenly across the belt, minimizing stress and extending the life of both the belt and rollers.
- Impact Absorption: Custom impact rollers are developed to absorb the shock of heavy or sharp materials being loaded onto the conveyor, protecting the belt from damage.
- Material Compatibility: Rollers can be customized with materials and coatings that are compatible with the specific types of aggregates being transported, reducing the risk of corrosion or buildup.
- Environmental Adaptability: Engineering solutions take into account the environmental conditions in which the conveyor will operate, such as extreme temperatures or moisture, ensuring that the rollers are suited to withstand these conditions.
- Energy Efficiency: Custom rollers can be designed to reduce friction and energy consumption, contributing to more sustainable and cost-effective operations.
- Noise Reduction: Engineering advancements can lead to the development of rollers that operate more quietly, improving the working environment around the conveyor system.
- Speed Optimization: Customization allows for the precise tuning of roller and belt speeds to match the required throughput rates and operational tempo of the aggregate processing plant.
- Maintenance Reduction: By engineering rollers that are more durable and easier to service, companies can significantly reduce maintenance requirements and associated downtime.
- Use of Snubber Pulleys: Incorporating snubber pulleys as part of the engineering solution helps in tensioning and protecting the belt, especially in high-load areas, enhancing the overall reliability and longevity of the conveyor system.
Through these tailored engineering solutions and customizations, companies specializing in aggregate conveyor rollers, like SKE Industries and SCG Supplies, are able to significantly enhance the performance and reliability of conveyor systems, ensuring they meet the specific needs of the aggregate industry.
Purchasing and Availability of Aggregate Conveyor Rollers
When it comes to enhancing or maintaining your conveyor system, finding the right aggregate conveyor rollers is crucial. Whether you’re looking for new or used options, or trying to locate suppliers near you, here are some tips and advice to ensure you make informed decisions:
Finding Aggregate Conveyor Rollers for Sale
- Research Manufacturers: Start by researching reputable manufacturers known for quality aggregate conveyor rollers, such as SKE Industries and Precision Pulley & Idler (PPI).
- Online Marketplaces: Explore online industrial marketplaces that list new and used conveyor components from various suppliers.
- Trade Shows: Attend industry trade shows and expos where manufacturers and distributors showcase their latest products and technologies.
- Direct Inquiries: Contact manufacturers directly to inquire about their product range, customization options, and pricing.
- Refurbished Options: Consider refurbished rollers, which can be a cost-effective alternative to new ones, especially if they come with a warranty.
- Bulk Purchases: Look into bulk purchase options, which can often lead to better pricing and availability.
- Industry Forums: Join industry forums and online communities to get recommendations and insights from peers who have made similar purchases.
Locating Aggregate Conveyor Rollers Near You
- Local Distributors: Identify local distributors or dealers of reputable brands to ensure quick availability and support.
- Service Providers: Some conveyor maintenance and service providers also supply parts, including rollers, and may have local stock.
- Manufacturer Directories: Use manufacturer directories to find authorized dealers in your area.
- Networking: Leverage your industry network to find local suppliers known for reliable products and services.
- Local Listings: Check local business listings and directories for suppliers of conveyor components.
- Custom Fabrication: In some cases, local fabrication shops can custom-make rollers to your specifications, offering a local solution.
- After-Sales Support: Ensure that the supplier offers reliable after-sales support and maintenance services, which is crucial for minimizing downtime.
Partnering with reputable suppliers for aggregate conveyor rollers is essential, not just for the quality of the components, but also for the ongoing support and maintenance services they can provide. This ensures not only the reliability of your conveyor system but also its longevity and efficiency in handling aggregate materials.
Maintenance and Replacement of Aggregate Conveyor Rollers
Regular maintenance and timely replacement of aggregate conveyor rollers are critical to the longevity and efficiency of your conveyor system. Understanding the importance and having clear guidelines for maintenance and replacement can significantly reduce downtime and enhance operational performance.
Importance of Regular Maintenance
- Prevents Breakdowns: Regular inspections and maintenance can identify and rectify minor issues before they lead to major breakdowns.
- Extends Roller Lifespan: Proper care and timely maintenance extend the life of conveyor rollers, making your investment last longer.
- Ensures Efficiency: Well-maintained rollers ensure the conveyor operates at peak efficiency, reducing energy consumption and wear on other components.
- Improves Safety: Regular maintenance reduces the risk of accidents caused by malfunctioning or failing components.
- Minimizes Downtime: By preventing unexpected failures, regular maintenance keeps your operations running smoothly without significant interruptions.
- Optimizes Performance: Maintained rollers contribute to the optimal performance of the conveyor, ensuring materials are transported effectively.
- Reduces Replacement Costs: Regular maintenance can reduce the need for frequent replacements, saving costs in the long run.
- Compliance: Staying on top of maintenance helps ensure compliance with safety and operational standards.
Guidelines for Replacement
- Regular Inspections: Conduct regular inspections to identify wear and tear or damage to rollers.
- Listen for Noise: Unusual noises from the conveyor can indicate issues with rollers, such as misalignment or wear.
- Check for Movement: Rollers that do not spin freely or have significant lateral movement may need replacement.
- Visual Inspection: Look for visible signs of damage, such as cracks, dents, or significant wear on the roller surface.
- Monitor Load Capacity: Rollers that consistently handle loads near their maximum capacity may wear out faster and need more frequent checks.
- Assess Environmental Factors: Harsh operating environments can accelerate wear, necessitating more frequent replacements.
- Follow Manufacturer Guidelines: Adhere to the manufacturer’s recommendations for maintenance and replacement intervals.
- Use Quality Replacements: Always replace worn or damaged rollers with high-quality components from reputable suppliers.
- Train Maintenance Staff: Ensure your maintenance team is well-trained in identifying and replacing faulty rollers.
- Plan for Downtime: Schedule maintenance and replacements during off-peak hours to minimize impact on operations.
By adhering to these maintenance and replacement guidelines for aggregate conveyor rollers, you can ensure the reliability and efficiency of your conveyor system, ultimately supporting uninterrupted and productive operations.
FAQs about Aggregate Conveyor Rollers
Conveyor rollers are pivotal components of conveyor systems, facilitating the smooth movement of materials across various distances. They come in several types, each designed to fulfill specific functions within a conveyor system. The primary types include:
Carrying Rollers: These are the most common rollers, positioned along the conveyor’s length to support and carry the conveyor belt and materials transported on it.
Return Rollers: Located on the underside of the conveyor, return rollers support the belt as it cycles back to the beginning after offloading its cargo.
Impact Rollers: Positioned at loading points where materials are dropped onto the conveyor, impact rollers are designed to absorb the shock and distribute the load, protecting the belt from damage.
Self-Aligning Rollers: These rollers are used to ensure the conveyor belt remains centered, reducing the risk of belt misalignment that can lead to operational issues or damage.
Guide Rollers: Installed on the sides of the conveyor belt, guide rollers prevent the belt from slipping off the track, ensuring smooth operation.
Each type of roller plays a crucial role in the conveyor’s overall functionality, ensuring efficient and uninterrupted material transport. The choice of roller type depends on various factors, including the nature of the materials being transported, the conveyor design, and the specific operational requirements of the system.
An aggregate conveyor is a specialized conveyor system used in the construction and mining industries to transport aggregate materials such as sand, gravel, crushed stone, and other particulate substances. These conveyors are designed to handle the rugged and abrasive nature of aggregate materials, ensuring efficient transport from one point to another within processing plants, quarries, and construction sites.
Aggregate conveyors come in various configurations, including belt, roller, and chain conveyors, each suited to different types of aggregate materials and operational needs. They are essential in operations such as mining, where they transport raw materials to processing areas, and in construction, where they move aggregates to mixing plants or construction sites.
The design of an aggregate conveyor considers factors like the material’s abrasiveness, weight, and the required transport distance. These conveyors are built to withstand harsh environments and heavy-duty use, featuring durable components and robust construction to ensure reliability and longevity in demanding operational conditions.
Conveyor rollers function by providing a series of rotating cylinders over which the conveyor belt or materials can move smoothly and efficiently. These rollers are mounted on bearings and axles, allowing them to spin freely. When a conveyor belt is draped over the rollers and the system is activated, the movement of the belt or the force of gravity (in the case of non-powered conveyors) causes the rollers to rotate, facilitating the easy movement of materials along the conveyor’s length.
The efficiency of a conveyor roller system lies in its simplicity and the minimal friction it creates, which reduces the energy required to move materials. The spacing, diameter, and type of rollers used are tailored to the specific needs of the conveyor system, including the weight and type of materials being transported, the conveyor’s speed, and the environmental conditions in which it operates.
In powered conveyor systems, motors drive some of the rollers, which in turn move the belt or directly push the materials along the conveyor. In gravity conveyors, the rollers spin freely, allowing materials to move down an incline or pushed along by manual force, making them an energy-efficient option for material handling.
A roller conveyor consists of several key components that work together to transport materials efficiently. These components include:
Rollers: The cylindrical elements that spin to facilitate the movement of materials. They can be made from various materials, including metal, plastic, or rubber, depending on the application.
Frame: The structure that supports the rollers and maintains their alignment. Frames can be made from materials like steel, aluminum, or heavy-duty plastics.
Bearings: Located at the ends of the rollers, bearings allow for smooth rotation with minimal friction.
Axles: Axles connect the rollers to the frame and are the pivot points around which the rollers rotate.
Drive Mechanism: In powered roller conveyors, a drive mechanism, such as a motor and gearbox, provides the force needed to turn the rollers and move the materials.
Support Legs: These provide stability to the conveyor and can be adjustable to accommodate different heights and levels.
Guide Rails: Optional components that prevent materials from falling off the conveyor or ensure they follow a specific path.
Understanding these components is crucial for anyone involved in the design, operation, or maintenance of roller conveyors, as each plays a vital role in the system’s overall functionality and efficiency.
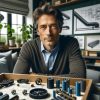
Jordan Smith, a seasoned professional with over 20 years of experience in the conveyor system industry. Jordan’s expertise lies in providing comprehensive solutions for conveyor rollers, belts, and accessories, catering to a wide range of industrial needs. From initial design and configuration to installation and meticulous troubleshooting, Jordan is adept at handling all aspects of conveyor system management. Whether you’re looking to upgrade your production line with efficient conveyor belts, require custom conveyor rollers for specific operations, or need expert advice on selecting the right conveyor accessories for your facility, Jordan is your reliable consultant. For any inquiries or assistance with conveyor system optimization, Jordan is available to share his wealth of knowledge and experience. Feel free to reach out at any time for professional guidance on all matters related to conveyor rollers, belts, and accessories.