Measuring 5 Ply Conveyor Belt Thickness
The 5 ply conveyor belt thickness is crucial for heavy-duty applications in various industries. These belts consist of five layers of synthetic fabric, providing enhanced strength, durability, and flexibility. The thickness of a 5 ply conveyor belt typically ranges from 10 mm to 20 mm, making it suitable for handling significant loads and abrasive materials. Industries such as mining, construction, and bulk material handling rely on the robust construction of 5 ply conveyor belts to ensure efficient and reliable operation. The appropriate thickness of these belts helps in maintaining performance, reducing downtime, and extending the lifespan of the conveyor system.
Construction of 5 Ply Conveyor Belt Thickness
The 5 ply conveyor belt thickness refers to the layered structure of the conveyor belt, where “ply” denotes the individual layers of material that make up the belt. The construction of a 5 ply conveyor belt involves several critical components that contribute to its durability, flexibility, and functionality.
- Base Layer (Carcass)
- The carcass of the belt is the foundation that provides structural integrity and strength. Typically, this layer is made from fabric materials such as polyester, nylon, or a blend of both. The fabric’s tensile strength and resistance to elongation are crucial for supporting the belt’s load and withstanding the operational stresses.
- Intermediate Layers
- Between the base layer and the top cover, multiple fabric layers (plies) are sandwiched. In the case of a 5 ply conveyor belt, there are five such fabric layers. Each ply is bonded to the next with a layer of rubber or adhesive, which not only holds the layers together but also enhances the belt’s overall strength and flexibility.
- Top Cover
- The top cover is made from a durable rubber compound designed to resist wear and tear from the material being transported. The thickness and composition of the top cover can vary depending on the application, such as whether the belt will be used for abrasive materials, heavy loads, or extreme temperatures.
- Bottom Cover
- The bottom cover, like the top cover, is also made from rubber. It provides additional protection to the carcass and ensures that the belt can move smoothly over the conveyor system’s rollers and pulleys. The bottom cover must be flexible and durable to minimize wear and reduce maintenance requirements.
Detailed Construction Process
- Fabric Preparation
- The construction of a 5 ply conveyor belt thickness begins with the preparation of the fabric layers. The fabric is selected based on the required tensile strength and elongation properties. Each fabric layer is treated with a rubber compound to enhance adhesion between the plies.
- Layer Assembly
- The treated fabric layers are then stacked and aligned precisely. An adhesive layer is applied between each fabric ply to bond them together. The alignment and bonding process is crucial to ensure that the belt maintains its structural integrity and performs reliably under load.
- Cover Application
- Once the fabric layers are assembled, the rubber covers are applied to both the top and bottom of the belt. The covers are bonded to the fabric layers using a high-temperature vulcanization process, which cures the rubber and creates a strong bond. The thickness of the top and bottom covers can be adjusted based on the specific requirements of the conveyor belt’s intended use.
- Final Curing
- The assembled conveyor belt is subjected to a final curing process, where it is heated to a specific temperature for a set period. This process ensures that all the layers are firmly bonded together and that the belt achieves its desired properties, such as flexibility, strength, and durability.
- Quality Control
- After curing, the belt undergoes rigorous quality control checks to ensure it meets the specified standards. The belt’s thickness, tensile strength, and other properties are measured and verified. Any defects or inconsistencies are addressed before the belt is approved for use.

Materials Used in 5 Ply Conveyor Belt Thickness
Commonly Used Materials
The materials used in the construction of a 5 ply conveyor belt thickness are selected based on the belt’s intended application, environmental conditions, and operational requirements. The primary materials include:
- Fabric Materials
- Polyester (EP)
- Polyester is a common fabric used in conveyor belts due to its high tensile strength, low elongation, and excellent resistance to abrasion and moisture. It provides the necessary strength to support heavy loads and maintain the belt’s shape and integrity.
- Nylon (NN)
- Nylon is another popular fabric material, known for its high impact resistance and flexibility. It is often used in applications where the belt needs to navigate curves and bends without compromising its structural integrity. Nylon’s excellent elasticity allows it to absorb shock loads effectively.
- Cotton
- Cotton fabric is occasionally used in conveyor belts for specific applications where its properties are advantageous. Cotton provides good adhesion to rubber and can enhance the belt’s flexibility and resistance to heat.
- Rubber Compounds
- The rubber compounds used in the top and bottom covers are critical for the belt’s performance. The specific composition of the rubber can be tailored to meet the demands of various applications, such as:
- Natural Rubber (NR)
- Natural rubber offers excellent flexibility and resilience, making it suitable for general-purpose conveyor belts. It provides good resistance to wear and tear and can handle moderate loads effectively.
- Styrene-Butadiene Rubber (SBR)
- SBR is a synthetic rubber known for its excellent abrasion resistance and durability. It is commonly used in conveyor belts that transport abrasive materials or operate in harsh environments.
- Nitrile Rubber (NBR)
- Nitrile rubber is highly resistant to oils, chemicals, and heat, making it ideal for conveyor belts used in industrial applications where exposure to these substances is common.
- Chloroprene Rubber (CR)
- Also known as neoprene, chloroprene rubber offers good resistance to heat, chemicals, and weathering. It is often used in conveyor belts that operate in outdoor environments or under extreme temperature conditions.
- Adhesives and Bonding Agents
- The adhesives and bonding agents used to bind the fabric layers and rubber covers play a crucial role in the construction of the conveyor belt. These materials must provide strong adhesion and maintain their bonding properties under varying temperatures and loads.
Material Selection Considerations
When selecting materials for a 5 ply conveyor belt thickness, several factors must be considered:
- Load Capacity
- The tensile strength and elongation properties of the fabric layers determine the belt’s load capacity. Materials with higher tensile strength and lower elongation are preferred for heavy-duty applications.
- Environmental Conditions
- The operating environment, including temperature, humidity, and exposure to chemicals, influences the choice of rubber compounds. For example, nitrile rubber is selected for applications involving oil exposure, while neoprene is chosen for outdoor use.
- Abrasion Resistance
- For applications involving abrasive materials, rubber compounds with high abrasion resistance, such as SBR, are essential to ensure the belt’s longevity and reduce maintenance costs.
- Flexibility and Elasticity
- The belt’s flexibility and ability to absorb shock loads are important for applications with curves and bends. Nylon fabric is often preferred for its excellent elasticity and impact resistance.
- Cost Considerations
- The cost of materials is also a key factor. While higher-quality materials may offer better performance and longevity, they also come at a higher cost. Balancing cost and performance is crucial for selecting the appropriate materials for a 5 ply conveyor belt thickness.

Measuring 5 Ply Conveyor Belt Thickness
Method of Measuring 5 Ply Conveyor Belt Thickness
Measuring the thickness of a 5-ply conveyor belt accurately is essential for ensuring proper installation, operation, and maintenance. Here are the methods typically used to measure the thickness of a conveyor belt:
1. Mechanical Thickness Gauge
A mechanical thickness gauge, also known as a micrometer, is a precise instrument used to measure the thickness of the conveyor belt.
Steps:
- Ensure the belt is clean and free from debris or material residue.
- Place the belt on a flat, stable surface.
- Open the micrometer and place it around the belt, making sure the anvils are perpendicular to the surface of the belt.
- Close the micrometer gently until it makes contact with the belt surface, avoiding excessive pressure that could compress the belt material.
- Read the measurement on the micrometer scale.
2. Digital Thickness Gauge
A digital thickness gauge provides an electronic reading of the belt thickness, offering greater ease and accuracy.
Steps:
- Clean the belt surface to ensure accurate measurement.
- Place the belt on a flat surface.
- Turn on the digital thickness gauge and calibrate it according to the manufacturer’s instructions.
- Place the gauge sensor on the belt surface and apply slight pressure until the sensor contacts the belt.
- Read the thickness measurement displayed on the digital screen.
3. Ultrasonic Thickness Gauge
An ultrasonic thickness gauge uses sound waves to measure the thickness of the conveyor belt. This method is non-destructive and can measure thickness without cutting or damaging the belt.
Steps:
- Clean the belt surface and apply a coupling gel to ensure proper contact between the ultrasonic probe and the belt.
- Calibrate the ultrasonic thickness gauge according to the material properties of the belt.
- Place the ultrasonic probe on the belt surface.
- Read the thickness measurement displayed on the ultrasonic gauge.
4. Calipers
Calipers are a simple and commonly used tool for measuring belt thickness. They can be either mechanical or digital.
Steps:
- Clean the belt surface to remove any debris.
- Open the calipers and place them around the belt.
- Close the calipers gently until they make contact with the belt surface.
- Read the thickness measurement on the calipers’ scale or digital display.
5. Feeler Gauges
Feeler gauges consist of a set of thin metal strips of varying thicknesses. This method is less precise but can be used for quick, approximate measurements.
Steps:
- Clean the belt surface.
- Select a feeler gauge of a known thickness and insert it between the belt layers.
- Adjust the feeler gauge until it fits snugly without compressing the belt material.
- Read the thickness indicated on the feeler gauge.
Important Considerations:
- Measurement Location: Take multiple measurements across the width and length of the belt to account for any variations in thickness.
- Calibration: Ensure that the measuring instruments are calibrated correctly before use.
- Consistency: Use the same method and instrument for all measurements to ensure consistency.
- Environmental Factors: Consider the ambient temperature and other environmental factors that might affect the belt material and measurement accuracy.
By using these methods, you can accurately determine the thickness of a 5-ply conveyor belt, ensuring optimal performance and longevity in its application.
Tools
Accurate measurement of the 5 ply conveyor belt thickness is essential for ensuring the belt meets the required specifications and performs reliably. Several methods and tools are used to measure the thickness of conveyor belts:
- Calipers
- Digital Calipers
- Digital calipers are precision measuring tools that provide accurate readings of the belt’s thickness. They are easy to use and offer high accuracy, making them suitable for measuring the thickness of conveyor belts with multiple layers.
- Vernier Calipers
- Vernier calipers are mechanical measuring tools that can also be used to measure the thickness of conveyor belts. They require manual reading but offer reliable measurements. Vernier calipers are often used in industrial settings where digital calipers may not be available.
- Micrometers
- Outside Micrometers
- Outside micrometers are used to measure the thickness of the conveyor belt by placing the belt between the micrometer’s anvil and spindle. The micrometer provides precise readings and is ideal for measuring thin belts or specific layers within the belt.
- Ultrasonic Thickness Gauges
- Ultrasonic Testing
- Ultrasonic thickness gauges use sound waves to measure the thickness of the conveyor belt. This non-destructive testing method is highly accurate and can measure the thickness of individual layers within the belt. Ultrasonic testing is especially useful for thick belts or belts with multiple plies.
- Optical Measurement Tools
- Laser Scanners
- Laser scanners can be used to measure the thickness of conveyor belts by projecting a laser beam onto the belt’s surface and measuring the reflected light. This method provides precise and continuous thickness measurements, making it suitable for monitoring the belt during operation.
Measurement Process
- Preparation
- Before measuring the 5 ply conveyor belt thickness, the belt should be cleaned to remove any dirt, dust, or debris that could affect the accuracy of the measurements. The belt should be in a relaxed state, without any tension or load.
- Measurement Points
- Measurements should be taken at multiple points along the length and width of the belt to ensure consistent thickness. Key areas to measure include the center of the belt, the edges, and any areas that show signs of wear or damage.
- Using Calipers and Micrometers
- When using calipers or micrometers, the measurement tool should be placed perpendicular to the belt’s surface. The tool’s jaws or anvil should make firm contact with the belt without compressing it. The reading should be taken and recorded for each measurement point.
- Using Ultrasonic Thickness Gauges
- For ultrasonic testing, a coupling gel is applied to the belt’s surface to ensure proper transmission of the sound waves. The ultrasonic probe is then placed on the belt, and the gauge provides a thickness reading. Multiple measurements should be taken to verify the consistency of the readings.
- Recording and Analyzing Data
- All thickness measurements should be recorded and analyzed to determine the average thickness of the belt. Any significant variations in thickness can indicate potential issues with the belt’s construction or areas that may require maintenance or replacement.
Importance of Accurate Measurement
Accurate measurement of the 5 ply conveyor belt thickness is crucial for several reasons:
- Quality Assurance
- Ensuring that the belt meets the specified thickness is essential for maintaining quality standards. Accurate measurements help verify that the belt has been manufactured correctly and will perform as expected.
- Performance Optimization
- Knowing the exact thickness of the belt allows for better optimization of the conveyor system. Properly calibrated belts can reduce energy consumption, minimize wear on the conveyor components, and improve overall system efficiency.
- Maintenance Planning
- Regular thickness measurements can help identify areas of wear and predict when the belt will need maintenance or replacement. This proactive approach can prevent unexpected downtime and extend the belt’s lifespan.
- Safety Considerations
- A conveyor belt that is too thin may not be able to handle the load, leading to potential failures and safety hazards. Accurate thickness measurements ensure that the belt is safe to operate and can handle the required load without risk of failure.
- Cost Management
- By accurately measuring and maintaining the 5 ply conveyor belt thickness, companies can avoid unnecessary replacements and reduce maintenance costs. This helps in managing operational expenses more effectively.
The construction, materials, and measurement of 5 ply conveyor belt thickness are integral to ensuring the belt’s performance, durability, and reliability. Each aspect of the construction process, from selecting the right materials to accurately measuring the belt’s thickness, plays a crucial role in creating a conveyor belt that meets the demands of various industrial applications. By understanding these factors, companies can make informed decisions and optimize their conveyor systems for maximum efficiency and longevity.

Features of 5 Ply Conveyor Belt Thickness
A 5-ply conveyor belt is designed to handle heavy-duty applications and consists of five layers of material. Here are the key features typically associated with a 5-ply conveyor belt:
- Thickness: The thickness of a 5-ply conveyor belt can vary depending on the specific application and materials used. However, it generally ranges from 10 to 15 millimeters. The thickness provides durability and strength to handle high-impact loads.
- Material Composition: The belt consists of five layers of synthetic fabric, rubber, or a combination of both. These layers are bonded together to form a strong, durable structure. The outer layers are usually made of rubber to provide abrasion resistance and grip.
- Tensile Strength: A 5-ply belt has high tensile strength, making it suitable for heavy-duty applications. The multiple layers distribute the load evenly and reduce the risk of stretching or tearing.
- Abrasion Resistance: The outer rubber layers are designed to resist wear and tear from abrasive materials. This feature is essential for industries such as mining, construction, and recycling, where the belt may come into contact with sharp or abrasive materials.
- Flexibility: Despite its thickness and strength, a 5-ply conveyor belt maintains a degree of flexibility. This flexibility allows the belt to bend around pulleys and rollers without cracking or deforming.
- Load Capacity: The multiple layers of a 5-ply belt allow it to carry heavier loads compared to belts with fewer plies. This makes it ideal for applications involving the transportation of bulky or heavy materials.
- Impact Resistance: The thick, multi-layered construction provides excellent impact resistance, protecting the belt from damage caused by heavy or sharp objects.
- Temperature Resistance: Depending on the materials used, a 5-ply conveyor belt can withstand a wide range of temperatures. Specially designed belts can handle extreme cold or heat, making them suitable for various industrial environments.
- Oil and Chemical Resistance: Some 5-ply belts are engineered to resist oils, chemicals, and other hazardous substances. This feature is crucial for industries such as food processing, chemical manufacturing, and waste management.
- Maintenance and Lifespan: Due to its robust construction, a 5-ply conveyor belt typically requires less maintenance and has a longer lifespan compared to belts with fewer plies. Regular inspection and proper maintenance can further extend its service life.
These features make 5-ply conveyor belts a reliable and durable choice for demanding industrial applications.
Benefits of 5 Ply Conveyor Belt Thickness
The 5 ply conveyor belt thickness offers numerous advantages that make it a preferred choice for various industrial applications. Its construction, consisting of five layers of synthetic fabric, provides enhanced strength, durability, and flexibility. Below, we highlight the key benefits of using 5 ply conveyor belts in different settings, emphasizing how their thickness contributes to improved performance and efficiency.
Enhanced Strength and Durability
One of the primary benefits of 5 ply conveyor belt thickness is its enhanced strength and durability. The five layers of synthetic fabric provide a robust structure that can withstand heavy loads and resist wear and tear. This makes the belt suitable for demanding applications such as mining, construction, and bulk material handling, where the belt is exposed to harsh conditions and abrasive materials. The thick construction ensures that the belt maintains its integrity and performance over extended periods, reducing the need for frequent replacements.
High Load-Bearing Capacity
The 5 ply conveyor belt thickness provides a high load-bearing capacity, making it ideal for transporting heavy and bulky materials. The multiple layers of fabric distribute the load evenly across the belt, preventing stretching and deformation. This ensures that the belt can handle substantial weights without compromising its performance. Industries that require the movement of large quantities of materials, such as mining and logistics, benefit significantly from the high load-bearing capacity of 5 ply conveyor belts.
Resistance to Abrasion and Impact
The thick construction of 5 ply conveyor belts offers excellent resistance to abrasion and impact. The top and bottom covers are designed to protect the ply layers from the friction and impact of transported materials. This resistance to wear and tear ensures that the belt can handle abrasive materials and high-impact loads without suffering damage. The durability provided by the 5 ply conveyor belt thickness leads to longer service life and reduced maintenance costs, enhancing overall operational efficiency.
Flexibility and Adaptability
Despite its robust construction, the 5 ply conveyor belt thickness offers excellent flexibility and adaptability. The belt can navigate tight turns, inclines, and other complex conveyor system configurations without cracking or breaking. This flexibility is essential for applications that require the belt to adapt to different operational environments and conveyor system designs. The ability to maintain performance in various configurations makes the 5 ply conveyor belt a versatile choice for industries such as manufacturing and food processing.
Moisture and Chemical Resistance
The materials used in the construction of 5 ply conveyor belts provide resistance to moisture and chemicals, making them suitable for environments where exposure to such elements is common. This resistance ensures that the belt maintains its performance and durability even in challenging conditions. Industries such as agriculture, food processing, and chemical processing benefit from the moisture and chemical resistance offered by the 5 ply conveyor belt thickness, as it helps prevent degradation and contamination.
Cost-Effectiveness
Investing in a 5 ply conveyor belt thickness can be cost-effective in the long run. The enhanced durability and resistance to wear and tear reduce the frequency of replacements and maintenance, leading to cost savings. Additionally, the high load-bearing capacity and flexibility of the belt contribute to improved operational efficiency, minimizing downtime and increasing productivity. Businesses can achieve significant long-term savings by choosing a high-quality 5 ply conveyor belt that meets their specific requirements.
Safety and Reliability
The 5 ply conveyor belt thickness ensures safe and reliable operation in various industrial settings. The robust construction and high load-bearing capacity minimize the risk of belt failures that could lead to accidents or operational disruptions. The belt’s resistance to abrasion, impact, moisture, and chemicals further enhances its reliability, ensuring consistent performance even in demanding environments. By providing a safe and dependable material handling solution, the 5 ply conveyor belt helps businesses maintain smooth and efficient operations.
Customization Options
Manufacturers offer customization options for 5 ply conveyor belts to meet specific application needs. These options can include variations in the thickness of the top and bottom covers, the type of synthetic fabric used for the ply layers, and special features such as anti-static or flame-resistant properties. Customization ensures that the conveyor belt thickness precisely matches the operational requirements, enhancing performance and longevity. Businesses can benefit from tailored solutions that address their unique challenges and optimize their conveyor systems.
Environmental Considerations
The 5 ply conveyor belt thickness can contribute to environmentally friendly practices. The durability and long service life of the belt reduce the need for frequent replacements, leading to less waste. Additionally, some manufacturers offer eco-friendly options, such as belts made from recycled materials or those designed to minimize energy consumption. By choosing a 5 ply conveyor belt that aligns with their sustainability goals, businesses can reduce their environmental impact while maintaining efficient operations.
The 5 ply conveyor belt thickness offers numerous benefits that make it a preferred choice for various industrial applications. Its enhanced strength, high load-bearing capacity, resistance to abrasion and impact, flexibility, and adaptability contribute to improved performance and efficiency. By understanding the advantages of using 5 ply conveyor belts, businesses can select the appropriate belt for their specific needs, achieving long-term cost savings and operational success.

Applications of 5 Ply Conveyor Belt Thickness
The 5 ply conveyor belt thickness is designed to meet the demanding requirements of various heavy-duty industrial applications. Its construction, consisting of five layers of synthetic fabric, provides enhanced strength, durability, and flexibility, making it ideal for transporting heavy and abrasive materials. Below, we explore different industrial applications where 5 ply conveyor belt thickness is utilized, emphasizing its role in ensuring efficient and reliable operations.
Mining Industry
In the mining industry, conveyor belts are essential for transporting minerals, ores, and other heavy materials over long distances. The 5 ply conveyor belt thickness is particularly well-suited for this environment due to its robustness and ability to handle substantial loads. The thick, multi-layered construction ensures that the belt can withstand the harsh conditions of mining operations, including exposure to sharp and abrasive materials, high impact loads, and extreme temperatures.
Construction Industry
The construction industry relies heavily on conveyor belts for the efficient movement of materials such as sand, gravel, concrete, and asphalt. The 5 ply conveyor belt thickness provides the necessary strength and durability to handle these heavy and abrasive materials. Its thick construction helps prevent punctures and tears, ensuring smooth and continuous operation on construction sites. The belt’s flexibility also allows it to navigate complex conveyor systems with tight turns and inclines, making it an ideal choice for various construction projects.
Bulk Material Handling
Bulk material handling involves the transportation of large quantities of loose materials, such as grains, coal, cement, and chemicals. The 5 ply conveyor belt thickness is perfect for this application, as it offers the necessary strength and durability to manage high volumes of material efficiently. The belt’s thick construction ensures minimal wear and tear, reducing the need for frequent replacements and maintenance. This leads to increased operational efficiency and cost savings for businesses involved in bulk material handling.
Recycling and Waste Management
In recycling and waste management facilities, conveyor belts are used to transport a wide range of materials, including metals, plastics, paper, and organic waste. The 5 ply conveyor belt thickness is ideal for these applications due to its ability to handle mixed and often abrasive materials. The belt’s robust construction ensures that it can withstand the rigors of waste processing, including exposure to sharp objects and varying material densities. This durability helps maintain efficient operations and reduces downtime caused by belt failures.
Agriculture
The agricultural industry uses conveyor belts for handling and transporting various products, such as grains, seeds, fruits, and vegetables. The 5 ply conveyor belt thickness provides the necessary strength and flexibility to manage these products without causing damage. The belt’s thick construction ensures that it can handle the high volumes of agricultural products typically transported during harvest and processing seasons. Additionally, the belt’s resistance to moisture and chemicals makes it suitable for use in agricultural environments where exposure to such elements is common.
Manufacturing
Manufacturing facilities utilize conveyor belts to transport raw materials, components, and finished products along production lines. The 5 ply conveyor belt thickness is beneficial in these settings due to its ability to handle heavy loads and resist wear and tear. The belt’s construction ensures that it can maintain consistent performance in high-speed manufacturing environments, reducing the risk of production delays caused by belt failures. The flexibility of the 5 ply conveyor belt also allows it to adapt to various conveyor system configurations, making it a versatile choice for different manufacturing processes.
Logistics and Distribution
In logistics and distribution centers, conveyor belts are used to move packages, pallets, and other goods efficiently. The 5 ply conveyor belt thickness is ideal for these applications due to its durability and ability to handle heavy loads. The thick construction ensures that the belt can withstand the constant use and high impact loads typical in logistics operations. This reliability helps maintain smooth and efficient operations, ensuring timely delivery of goods to customers.
Food Processing
The food processing industry requires conveyor belts that meet stringent hygiene and safety standards. The 5 ply conveyor belt thickness is suitable for food processing applications due to its robust construction and resistance to moisture and chemicals. The thick, multi-layered design ensures that the belt can handle the rigorous cleaning and sanitizing processes required in food processing facilities. Additionally, the belt’s strength and flexibility allow it to transport various food products without causing damage or contamination.
The 5 ply conveyor belt thickness is utilized in a wide range of industrial applications due to its strength, durability, and flexibility. From mining and construction to agriculture and food processing, this versatile conveyor belt ensures efficient and reliable material handling in demanding environments. By understanding the specific requirements of each application, businesses can select the appropriate 5 ply conveyor belt thickness to optimize their operations and achieve long-term cost savings.
When to Choose 5 Ply Conveyor Belt Thickness
Choosing a 5-ply conveyor belt thickness depends on various factors related to the specific application and operational requirements. Here are some scenarios and conditions where a 5-ply conveyor belt might be the best choice:
1. Heavy-Duty Applications
- When the conveyor system is required to transport heavy or bulky materials, such as in mining, construction, or bulk material handling industries.
- When the belt needs to support large loads without stretching or deforming.
2. High Abrasion Environments
- When the conveyor belt will be exposed to abrasive materials such as rocks, minerals, or other sharp objects.
- In industries like quarrying or recycling where the belt must withstand continuous contact with rough surfaces.
3. High Impact Conditions
- When the belt will be subjected to heavy impacts, such as from dropping materials from significant heights.
- In situations where the conveyed materials might have sharp edges or irregular shapes that could damage a less durable belt.
4. Long Conveyor Lengths
- For conveyor systems that span long distances, requiring a belt with enhanced strength and stability to avoid sagging and ensure efficient operation.
- In applications where the belt must maintain its integrity over extended lengths and multiple pulleys.
5. High-Tension Applications
- When the conveyor system operates under high tension, which requires a belt that can handle the stress without stretching excessively.
- In applications where precise tension control is essential for efficient operation and belt longevity.
6. Demanding Industrial Environments
- When operating in harsh environmental conditions, such as extreme temperatures, exposure to oils, chemicals, or other hazardous substances.
- In industries such as chemical processing, food processing, or waste management where the belt must resist chemical degradation.
7. Frequent Start-Stop Operations
- When the conveyor system experiences frequent start-stop cycles, which can cause additional stress and wear on the belt.
- In applications where smooth and reliable operation is critical, and the belt must endure repeated mechanical stress.
8. High-Speed Conveying
- When the conveyor system operates at high speeds, requiring a belt that can maintain stability and alignment without distortion.
- In applications where consistent and efficient material flow is essential for productivity.
Selecting a 5-ply conveyor belt thickness is ideal for applications requiring enhanced durability, strength, and resistance to various operational challenges. It is particularly suited for heavy-duty, high-impact, and high-tension environments, ensuring reliable performance and extended service life.
Maintenance Tips for 5 Ply Conveyor Belt Thickness
Proper maintenance of 5 ply conveyor belt thickness is essential for ensuring its longevity and optimal performance. Regular maintenance practices help prevent premature wear and tear, reduce downtime, and extend the belt’s service life. Below, we provide best practices for maintaining the optimal condition of 5 ply conveyor belt thickness, emphasizing the importance of routine inspections, cleaning, and timely repairs.
Regular Inspections
Conducting regular inspections is the first step in maintaining 5 ply conveyor belt thickness. Routine inspections help identify potential issues before they become major problems. Key areas to inspect include:
- Belt Surface: Check for signs of wear, cuts, and punctures on the belt’s surface. Pay attention to any unusual wear patterns that could indicate misalignment or other issues.
- Belt Edges: Inspect the edges of the belt for fraying or damage. Damaged edges can lead to belt failure and should be addressed promptly.
- Splices and Joints: Examine splices and joints for signs of weakness or separation. Properly maintained splices ensure the belt’s integrity and prevent breakage.
- Rollers and Pulleys: Inspect rollers and pulleys for wear and proper alignment. Misaligned components can cause uneven wear on the belt and reduce its lifespan.
- Tension and Tracking: Check the belt’s tension and tracking to ensure it is running smoothly on the conveyor system. Proper tension and alignment prevent slippage and excessive wear.
Cleaning and Lubrication
Keeping the 5 ply conveyor belt clean is crucial for maintaining its optimal condition. Accumulated dirt, debris, and material buildup can cause premature wear and reduce the belt’s efficiency. Regular cleaning practices include:
- Surface Cleaning: Use appropriate cleaning methods to remove dirt and debris from the belt’s surface. For belts used in food processing, ensure that cleaning agents are food-safe.
- Roller and Pulley Cleaning: Clean rollers and pulleys to remove any buildup that could affect the belt’s performance. Properly cleaned components ensure smooth operation and reduce wear.
- Lubrication: Lubricate moving parts such as bearings and rollers to reduce friction and wear. Ensure that lubricants do not come into contact with the belt itself, as they can degrade the rubber material.
Timely Repairs
Addressing minor issues promptly can prevent them from becoming major problems. Timely repairs help maintain the 5 ply conveyor belt thickness and extend its service life. Common repairs include:
- Patch Repairs: Use appropriate patching materials to repair small cuts and punctures on the belt’s surface. Ensure that the patches are securely bonded to prevent further damage.
- Splice Repairs: Repair weak or damaged splices to maintain the belt’s integrity. Properly repaired splices prevent belt separation and ensure smooth operation.
- Edge Repairs: Address frayed or damaged edges to prevent belt failure. Reinforce edges with appropriate materials to ensure their durability.
Preventive Maintenance Schedule
Implementing a preventive maintenance schedule helps ensure that maintenance tasks are carried out regularly and systematically. A well-planned maintenance schedule includes:
- Daily Checks: Conduct daily visual inspections of the belt and conveyor system components to identify any immediate issues.
- Weekly Inspections: Perform more detailed inspections of the belt surface, edges, splices, and joints on a weekly basis.
- Monthly Maintenance: Carry out thorough cleaning and lubrication of rollers, pulleys, and other moving parts every month.
- Quarterly Maintenance: Conduct comprehensive inspections and repairs, including tension and tracking adjustments, on a quarterly basis.
- Annual Maintenance: Perform a complete overhaul of the conveyor system, including replacing worn components and addressing any long-term issues, annually.
Training for Maintenance Personnel
Proper training for maintenance personnel is essential for ensuring effective maintenance practices. Maintenance staff should be trained on:
- Inspection Techniques: Learn how to conduct thorough inspections and identify potential issues.
- Repair Methods: Understand the proper techniques for repairing cuts, punctures, splices, and edges.
- Cleaning Procedures: Know the appropriate cleaning methods and agents for different types of conveyor belts.
- Safety Protocols: Follow safety protocols to prevent accidents and injuries during maintenance tasks.
Environmental Considerations
Consider the environmental conditions in which the 5 ply conveyor belt operates. Extreme temperatures, humidity, and exposure to chemicals can affect the belt’s performance and lifespan. Take appropriate measures to protect the belt from harsh environmental conditions, such as:
- Temperature Control: Ensure that the conveyor system operates within the recommended temperature range to prevent thermal degradation.
- Humidity Control: Minimize exposure to excessive moisture and humidity to prevent mold and mildew growth.
- Chemical Protection: Use protective covers or coatings to shield the belt from chemical exposure and prevent damage.
Maintaining the optimal condition of 5 ply conveyor belt thickness is essential for ensuring its longevity and performance. Regular inspections, cleaning, timely repairs, and a preventive maintenance schedule are crucial for preventing wear and tear and extending the belt’s service life. Proper training for maintenance personnel and consideration of environmental conditions further enhance the effectiveness of maintenance practices. By following these best practices, businesses can ensure the reliable and efficient operation of their 5 ply conveyor belts, reducing downtime and achieving long-term cost savings.
FAQs about 5 Ply Conveyor Belt Thickness
The thickness of a conveyor belt can vary widely depending on its type, construction, and intended use. Generally, conveyor belts range from as thin as 1/8 inch (approximately 3 mm) to over 1 inch (approximately 25 mm) thick. For example, lightweight belts used in food processing or packaging might be on the thinner side, while heavy-duty belts used in mining and bulk material handling are much thicker. The thickness of a conveyor belt is a critical factor that influences its strength, flexibility, and durability. Thicker belts generally offer greater strength and are capable of handling heavier loads and more abrasive materials, while thinner belts are more flexible and suitable for lighter applications. When selecting a conveyor belt, it is essential to consider the specific requirements of the application, including the type of material being conveyed, the operating environment, and the load capacity needed.
A 3 ply conveyor belt is constructed with three layers of synthetic fabric, providing a balance of strength and flexibility for various industrial applications. The thickness of these belts typically ranges from 6 mm to 9 mm (approximately 1/4 inch to 3/8 inch). Each layer, or ply, is usually around 1 mm to 1.5 mm thick, and the combined thickness includes the top cover, the three ply layers, and the bottom cover. The top cover, which provides protection against abrasion and impact, generally ranges from 1.5 mm to 3 mm thick. The bottom cover, which protects the belt from wear and tear on the conveyor system’s components, typically ranges from 1.5 mm to 2.5 mm thick. This construction ensures that the 3 ply conveyor belt can handle moderate to heavy loads while maintaining flexibility and durability. It is commonly used in applications such as material handling, manufacturing, and food processing.
A 2 ply conveyor belt is constructed with two layers of synthetic fabric, providing a balance of strength and flexibility suitable for various industrial applications. The thickness of a 2 ply conveyor belt generally ranges from 3/16 inch to 3/8 inch (approximately 4.5 mm to 9 mm). Each ply layer is typically around 1 mm to 1.5 mm thick, and the combined thickness includes the top cover, the two ply layers, and the bottom cover. The top cover, designed to withstand abrasion and impact, usually ranges from 1.5 mm to 3 mm thick. The bottom cover, which protects the belt from wear and tear on the conveyor system’s components, typically ranges from 1.5 mm to 2.5 mm thick. This construction ensures that the 2 ply conveyor belt can handle moderate loads while maintaining flexibility and durability. It is commonly used in applications such as packaging, warehousing, agriculture, and light manufacturing.
The standard size of a conveyor belt can vary depending on the application and industry requirements. Conveyor belts come in various widths, lengths, and thicknesses to accommodate different types of conveyor systems. Standard widths typically range from 18 inches to 72 inches (approximately 450 mm to 1,830 mm), but wider or narrower belts can also be found depending on specific needs. Lengths can vary significantly, from a few meters to several kilometers, depending on the conveyor system’s design and layout. The thickness of the belt, which can range from 1/8 inch to over 1 inch, is chosen based on the load capacity and the type of material being conveyed. When selecting the size of a conveyor belt, it is essential to consider factors such as the type of material, operating environment, load capacity, and the design of the conveyor system. Custom sizes are also available to meet specific operational requirements, ensuring optimal performance and efficiency.
The thickness of a steel cord conveyor belt can vary significantly depending on its specific design and intended use. Generally, the thickness ranges from about 10 millimeters (0.4 inches) to over 50 millimeters (2 inches). The actual thickness will depend on factors such as the diameter of the steel cords, the number of cords, the type of covering material, and the overall construction of the belt.
A conveyor belt is typically made of several layers of material known as plies. These plies are usually constructed from fabric, rubber, or a combination of both. Common materials for the plies include:
Fabric: The fabric plies are often made from synthetic fibers like polyester, nylon, or cotton. These materials provide strength, flexibility, and resistance to wear and tear.
Rubber: Rubber is used as both a covering material and as a ply material in some belts. It offers excellent resistance to abrasion, impact, and various chemicals.
Steel Cords: In steel cord conveyor belts, steel cords are used instead of fabric plies. These cords provide high tensile strength, allowing the belt to carry heavy loads over long distances without stretching.
The combination of these materials results in a conveyor belt that is strong, durable, and suitable for its specific application.
Last Updated on August 16, 2024 by Jordan Smith
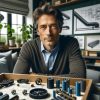
Jordan Smith, a seasoned professional with over 20 years of experience in the conveyor system industry. Jordan’s expertise lies in providing comprehensive solutions for conveyor rollers, belts, and accessories, catering to a wide range of industrial needs. From initial design and configuration to installation and meticulous troubleshooting, Jordan is adept at handling all aspects of conveyor system management. Whether you’re looking to upgrade your production line with efficient conveyor belts, require custom conveyor rollers for specific operations, or need expert advice on selecting the right conveyor accessories for your facility, Jordan is your reliable consultant. For any inquiries or assistance with conveyor system optimization, Jordan is available to share his wealth of knowledge and experience. Feel free to reach out at any time for professional guidance on all matters related to conveyor rollers, belts, and accessories.