Benefits of Tapered Conveyor Rollers in Material Handling
Tapered conveyor rollers play a crucial role in material handling systems, especially in applications involving curves and corners. These rollers are designed to maintain the alignment and orientation of items as they navigate through bends, ensuring smooth and efficient movement. Tapered conveyor rollers help in preventing products from slipping or jamming, thus enhancing the overall efficiency and reliability of conveyor systems. Various types of conveyor rollers, including straight, PVC, and custom rollers, are used depending on the specific requirements of the application. Each type offers unique benefits, but tapered conveyor rollers are particularly vital for handling turns and maintaining consistent flow in complex conveyor layouts.
Tapered Conveyor Rollers
PVC Conveyor Rollers
Overview of PVC Conveyor Rollers
PVC (Polyvinyl Chloride) conveyor rollers have gained significant popularity in various industries due to their unique benefits and versatility. One of the primary advantages of using PVC rollers is their lightweight nature, which makes them easy to handle and install. This feature reduces the overall weight of the conveyor system, leading to lower energy consumption and operational costs. Additionally, PVC is inherently corrosion-resistant, making these rollers ideal for environments where exposure to moisture, chemicals, or other corrosive elements is a concern.
Another critical advantage of PVC conveyor rollers is their cost-effectiveness. PVC material is relatively inexpensive compared to other roller materials like stainless steel or aluminum. This affordability, combined with their durability and low maintenance requirements, makes PVC rollers a highly economical choice for businesses looking to optimize their material handling systems.
PVC conveyor rollers are commonly used in a wide range of industries. In the food and beverage sector, they are ideal for applications involving the transportation of packaged goods and raw materials, thanks to their non-toxic and easy-to-clean properties. In the packaging industry, PVC rollers facilitate smooth and efficient movement of various packaging materials, enhancing productivity. Furthermore, in the retail and distribution sectors, these rollers are utilized in conveyor systems for sorting and moving products efficiently within warehouses and fulfillment centers.
Design and Manufacturing of PVC Rollers
The design and manufacturing process of PVC conveyor rollers is meticulous and geared towards ensuring high performance and longevity. The initial step involves selecting high-quality PVC material, which is then molded or extruded into the desired roller shape. The process often includes reinforcing the PVC with additional materials to enhance its strength and durability, particularly for heavy-duty applications.
Customization is a significant aspect of PVC roller manufacturing. Companies can order PVC rollers in various sizes, colors, and surface finishes to meet their specific needs. The ability to customize the size ensures that the rollers can fit seamlessly into different conveyor systems, regardless of the industry’s unique requirements. Color customization is particularly beneficial for industries that need to adhere to color-coded systems
for sorting and categorizing products, thereby enhancing operational efficiency and reducing the risk of errors.
Surface finish customization is another crucial aspect, allowing for the creation of PVC rollers with different textures and coatings to suit specific applications. For instance, smooth-surfaced PVC rollers are ideal for transporting delicate or lightweight items, while rollers with a textured or grooved surface can provide better grip and control for heavier or bulkier materials.
Incorporating tapered conveyor rollers into PVC roller designs is a specialized customization option that further enhances the functionality of conveyor systems. Tapered rollers are designed to assist with directional changes and product alignment on curved conveyor sections. This feature is particularly useful in industries where maintaining precise product orientation and alignment is critical, such as in packaging, logistics, and manufacturing.
The manufacturing process of tapered conveyor rollers involves precision engineering to ensure the taper is consistent and meets the specific angle requirements of the conveyor system. This precision ensures that products move smoothly and efficiently through curves and turns, minimizing the risk of jams and ensuring a continuous flow of materials.
Overall, the integration of tapered conveyor rollers within PVC roller systems exemplifies the adaptability and advanced engineering capabilities available to meet diverse industrial needs. By combining the inherent benefits of PVC material with the specialized design of tapered rollers, industries can achieve enhanced performance, reliability, and cost-efficiency in their conveyor operations.
Tapered Conveyor Rollers: An In-Depth Look
Taper Roller Conveyor Design
What are Tapered Conveyor Rollers?
Tapered conveyor rollers are specialized components used in conveyor systems, designed to facilitate the smooth handling of items as they navigate curves and corners within the system. Unlike standard straight rollers, tapered rollers have a conical shape, which allows them to manage the changes in direction without causing the items being transported to fall off or become misaligned.
The primary function of tapered conveyor rollers is to maintain a consistent speed and orientation of items on a conveyor belt as it turns. This is crucial for systems where precision and stability are paramount, such as in packaging, manufacturing, and distribution industries. The tapered design ensures that the inner and outer edges of the conveyor belt travel at different speeds, matching the curvature of the path. This prevents slippage and ensures that items remain in their intended positions throughout the journey.
Tapered conveyor rollers are integral to the efficiency and reliability of curved conveyor sections. They minimize the risk of product damage and reduce the likelihood of operational disruptions caused by misaligned items. By smoothly guiding products through curves, these rollers enhance the overall flow and performance of the conveyor system.
Design Considerations for Tapered Rollers
When designing tapered conveyor rollers, several critical factors need to be taken into account to ensure optimal performance and longevity. These considerations include the angle of taper, the material used, and the load capacity of the rollers.
Angle of Taper: The angle of taper is a fundamental aspect of the roller’s design. It determines how effectively the roller can guide items around curves. An optimal angle ensures that the conveyor belt and the items on it maintain the correct speed differential between the inner and outer edges. The angle must be carefully calculated based on the radius of the curve and the speed of the conveyor system to achieve the desired outcome.
Material: The material of the tapered rollers plays a significant role in their durability and performance. Common materials include steel, aluminum, and various types of plastics. Steel rollers are known for their strength and durability, making them suitable for heavy-duty applications. Aluminum rollers are lighter and resistant to corrosion, ideal for environments where weight reduction and longevity are critical. Plastic rollers are often used in applications where noise reduction and gentle handling of products are required. The choice of material depends on the specific needs of the conveyor system, including the type of products being transported and the operational environment.
Load Capacity: The load capacity of tapered conveyor rollers is another vital design consideration. This refers to the maximum weight the rollers can support without compromising performance or structural integrity. It’s essential to assess the weight of the items being conveyed and ensure that the rollers can handle this load consistently. Overloading rollers can lead to premature wear and tear, increased maintenance costs, and potential system failures.
Case Study: A Tapered Roller Conveyor System in Action
To illustrate the effectiveness of tapered conveyor rollers, consider a case study of a packaging facility that implemented a curved conveyor system to streamline its operations. The facility faced challenges in maintaining the alignment and speed of packages as they navigated sharp corners, leading to frequent jams and delays.
By integrating tapered conveyor rollers into the curved sections of the conveyor system, the facility was able to address these issues effectively. The tapered rollers ensured that packages maintained their orientation and speed throughout the curves, significantly reducing the incidence of jams. This improvement not only enhanced the overall efficiency of the packaging line but also reduced downtime and maintenance costs.
The success of this implementation was attributed to careful consideration of the angle of taper, selection of durable materials, and ensuring the rollers had adequate load capacity. The facility opted for steel tapered rollers with a precisely calculated angle to match the curvature of their conveyor path. This choice provided the necessary strength and durability to handle the weight of the packages while ensuring smooth and reliable operation.
Benefits of Tapered Conveyor Rollers
The use of tapered conveyor rollers offers several advantages, making them a preferred choice for many industries:
Improved Handling of Curves: Tapered rollers are specifically designed to manage curves efficiently. They ensure that the speed and orientation of items are maintained, reducing the risk of misalignment and product damage.
Enhanced System Reliability: By providing smooth and consistent guidance through curves, tapered rollers reduce the likelihood of jams and operational disruptions. This enhances the overall reliability of the conveyor system, leading to increased productivity.
Reduced Maintenance Costs: The durability and precision of tapered rollers minimize wear and tear, resulting in lower maintenance requirements and costs. This contributes to a longer lifespan for the conveyor system and its components.
Versatility: Tapered rollers can be made from various materials, making them suitable for a wide range of applications. Whether handling heavy-duty items or delicate products, there is a tapered roller solution to meet the specific needs of the operation.
Tapered Conveyor Rollers: Exploring the 1.9″ Diameter Roller
Conveyor Rollers
Characteristics of 1.9″ Conveyor Rollers
Tapered conveyor rollers are essential components in various material handling systems, particularly when dealing with curves and directional changes. Within this category, the 1.9″ diameter roller stands out for its versatility and efficiency. The 1.9″ diameter roller is one of the most commonly used sizes in the industry due to its balanced combination of size, strength, and adaptability.
The 1.9″ diameter roller is designed to offer a reliable and efficient solution for a wide range of applications. Its moderate size makes it suitable for handling various types of products, from small packages to larger items, without compromising on performance. These rollers are typically made from durable materials such as steel, aluminum, or high-impact plastics, each offering distinct advantages depending on the specific requirements of the conveyor system.
One of the primary benefits of using 1.9″ diameter tapered conveyor rollers is their ability to maintain product orientation and stability, especially in systems with curves. The tapered design ensures that the rollers can handle the differential speeds required by the inner and outer edges of the conveyor belt as it navigates turns. This design minimizes the risk of product slippage and ensures smooth transitions, which is crucial for maintaining the integrity and alignment of items being transported.
Additionally, 1.9″ diameter rollers are known for their durability and low maintenance requirements. Their robust construction allows them to withstand continuous use in demanding environments, reducing the need for frequent replacements and minimizing downtime. This durability translates to cost savings and increased operational efficiency for businesses that rely on conveyor systems for their daily operations.
Applications of 1.9″ Conveyor Rollers
The versatility and reliability of 1.9″ diameter tapered conveyor rollers make them ideal for a variety of industries and applications. These rollers are particularly effective in environments where precision and efficiency are paramount. Below are some of the key industries and scenarios where 1.9″ rollers are most commonly used:
Manufacturing: In manufacturing facilities, 1.9″ diameter tapered conveyor rollers are used to transport raw materials, components, and finished products through various stages of production. Their ability to handle curves and maintain product alignment ensures smooth and efficient operations, reducing the risk of bottlenecks and production delays.
Packaging: Packaging operations often involve complex conveyor systems with multiple curves and directional changes. The tapered design of 1.9″ rollers allows for the precise handling of packages, ensuring that they remain in the correct orientation for labeling, sealing, and other packaging processes. This is critical for maintaining the quality and consistency of packaged goods.
Distribution and Warehousing: In distribution centers and warehouses, the efficient movement of goods is essential for meeting delivery deadlines and optimizing storage space. 1.9″ diameter rollers are used in conveyor systems to facilitate the rapid and accurate sorting, routing, and loading of items. Their durability and low maintenance requirements make them ideal for high-throughput environments.
Food and Beverage: The food and beverage industry requires conveyor systems that can handle a wide range of product types and sizes while maintaining strict hygiene standards. 1.9″ diameter tapered rollers made from food-grade materials are used to transport products through various stages of processing, packaging, and distribution. Their smooth operation and easy-to-clean surfaces help ensure product safety and quality.
E-commerce and Retail: The rise of e-commerce has increased the demand for efficient order fulfillment and delivery systems. 1.9″ diameter rollers are used in automated conveyor systems to streamline the picking, packing, and shipping processes. Their ability to handle diverse product types and sizes makes them a valuable asset in fast-paced retail environments.
Example Use Cases and Performance Metrics
To illustrate the effectiveness of 1.9″ diameter tapered conveyor rollers, consider the following example use cases:
Case Study 1: Manufacturing Facility
A manufacturing facility producing electronic components implemented a conveyor system with 1.9″ diameter tapered rollers to transport delicate items through multiple production stages. The tapered design ensured that components remained properly aligned and oriented, reducing the risk of damage. As a result, the facility experienced a 20% increase in production efficiency and a 15% reduction in product defects.
Case Study 2: E-commerce Fulfillment Center
An e-commerce fulfillment center integrated 1.9″ diameter tapered conveyor rollers into its sorting and routing system. The rollers’ ability to handle curves and maintain product stability allowed for faster and more accurate order processing. This led to a 25% improvement in order fulfillment speed and a 10% decrease in shipping errors.
Performance Metrics
When evaluating the performance of 1.9″ diameter tapered conveyor rollers, several key metrics are typically considered:
- Load Capacity: The maximum weight the rollers can support without compromising performance. For 1.9″ diameter rollers, this typically ranges from 50 to 100 pounds per roller, depending on the material and construction.
- Speed: The operational speed at which the rollers can effectively transport items. 1.9″ diameter rollers can generally handle speeds up to 200 feet per minute, making them suitable for high-speed applications.
- Durability: The lifespan of the rollers under continuous use. High-quality 1.9″ diameter rollers can last for several years, even in demanding environments, thanks to their robust construction and materials.
Tapered Conveyor Rollers: An Essential Component in Roller Conveyor Systems
Rollers Conveyor Systems
Types of Conveyor Rollers and Their Functions
Conveyor systems are crucial for efficient material handling in various industries, and the types of rollers used play a significant role in their performance. Here, we delve into the different types of conveyor rollers, including tapered conveyor rollers, and their specific functions within a system.
Straight Rollers: Straight rollers are the most common type used in conveyor systems. They are typically cylindrical and are used for transporting items in a straight line. Their primary function is to support the belt and the items being conveyed, ensuring smooth and uninterrupted movement. They are essential in applications where direction changes are minimal.
Tapered Conveyor Rollers: Tapered conveyor rollers are designed with a conical shape to handle curves and corners in conveyor systems. Their tapered design allows for differential speeds at the inner and outer edges of the conveyor belt, maintaining product alignment and stability through turns. These rollers are crucial for systems requiring precise handling of items around bends, minimizing the risk of slippage and misalignment.
PVC Rollers: PVC rollers are lightweight and corrosion-resistant, making them ideal for environments where moisture or chemicals are present. These rollers are commonly used in food processing, pharmaceutical, and cleanroom applications. Their smooth surface ensures easy cleaning and maintenance, contributing to a hygienic conveyor system.
1.9″ Rollers: The 1.9″ diameter roller is widely used due to its versatility and balance of size and strength. These rollers can handle a variety of products, from small packages to larger items, making them suitable for general-purpose conveyor systems. Their durable construction allows them to withstand continuous use in demanding environments.
Custom Rollers: Custom rollers are designed to meet specific requirements of a conveyor system. They can be tailored in terms of size, material, and design features to accommodate unique operational needs. Custom rollers ensure that specialized items are transported efficiently and safely within the system.
Metric Rollers: Metric rollers are built to international standards, making them compatible with global conveyor systems. They are available in various diameters and lengths, providing flexibility in design and integration. Metric rollers are essential for businesses operating in multiple regions, ensuring consistency and compatibility across their operations.
Integration and Maintenance
Integrating different types of rollers, including tapered conveyor rollers, into a cohesive conveyor system requires careful planning and execution. Here are some best practices for integration and maintenance to ensure the longevity and efficiency of the rollers.
Integration Best Practices:
- System Design: Start with a thorough design plan that considers the specific needs of your operation. Identify where straight, tapered, PVC, 1.9″, custom, and metric rollers will be most effective.
- Compatibility: Ensure that all rollers are compatible with the conveyor framework and with each other. This includes matching diameters, materials, and load capacities.
- Precision Alignment: For tapered conveyor rollers, precision alignment is critical. Misalignment can lead to increased wear and operational inefficiencies. Use alignment tools and techniques to ensure proper installation.
- Testing: Before full-scale implementation, test the conveyor system with the integrated rollers to identify and address any issues. This helps in optimizing the system’s performance and reliability.
Maintenance Tips:
- Regular Inspections: Conduct routine inspections to check for signs of wear, damage, or misalignment. Early detection of issues can prevent more significant problems and extend the life of the rollers.
- Cleaning: Keep the rollers clean, especially in environments where debris or contaminants are prevalent. For PVC and other easily cleaned materials, regular wiping and washing can prevent buildup and maintain smooth operation.
- Lubrication: Proper lubrication of bearings and moving parts reduces friction and wear. Follow manufacturer recommendations for the type and frequency of lubrication.
- Replacement: Replace worn or damaged rollers promptly to avoid disruptions in the conveyor system. Keep a stock of commonly used rollers to minimize downtime during maintenance activities.
About Tapered Conveyor Rollers
The Content about Metric Conveyor Rollers
Metric Conveyor Rollers
Metric conveyor rollers are integral to modern material handling systems, especially in operations with a global reach. The adoption of metric sizing offers numerous advantages, such as enhanced compatibility and seamless integration with international equipment and standards. By standardizing measurements to the metric system, companies can streamline their procurement processes, reduce the need for custom adaptations, and improve overall efficiency.
The primary difference between metric and imperial measurements lies in their base units: metric uses meters and millimeters, while the imperial system uses inches and feet. Metric measurements are often considered more straightforward and easier to scale, which is particularly beneficial in industries requiring high precision. This standardization simplifies calculations, reduces the likelihood of errors, and ensures consistent dimensions across various components and systems.
For international companies, metric conveyor rollers provide a consistent measurement framework that eliminates the need for conversions, ensuring precise and uniform specifications. This uniformity is crucial for maintaining high-quality standards and operational efficiency across different regions, fostering smoother global operations and reducing the risk of incompatibilities.
Design and Application of Metric Rollers
Designing conveyor systems with metric conveyor rollers involves meticulous planning and a deep understanding of system requirements. The process begins with defining the dimensions and specifications of the rollers in metric units, ensuring that they align perfectly with other components like bearings, shafts, and frames. This alignment is vital for creating efficient, reliable conveyor systems that can operate seamlessly in various industrial environments.
One notable application of tapered conveyor rollers is in the automotive industry, where precision and standardization are essential. Metric rollers facilitate the efficient movement of parts and assemblies through production lines, enhancing productivity and reducing downtime caused by incompatible components. The use of standardized metric measurements ensures that all parts fit together perfectly, streamlining the manufacturing process and maintaining high-quality standards.
In the packaging and logistics sectors, metric conveyor rollers are indispensable for handling a diverse range of products. Their standardized sizing allows for easy integration with automated systems, improving the speed and accuracy of sorting, packing, and shipping processes. The global nature of these industries means that companies must adhere to international standards, and using metric rollers helps ensure compliance and operational consistency across different regions.
The benefits of metric conveyor rollers extend beyond individual industries to the broader context of international markets. By providing a universal standard, metric rollers simplify the design, manufacturing, and maintenance processes, reducing the complexity and costs associated with managing multiple systems based on different measurement units. This standardization also enhances the scalability of operations, allowing businesses to expand their global footprint without facing significant logistical challenges.
Moreover, the use of tapered conveyor rollers within metric systems further enhances their functionality. Tapered rollers are designed to help with directional changes and product alignment on curved conveyor sections, making them especially useful in industries where maintaining precise product orientation is critical. The precision engineering involved in manufacturing tapered rollers ensures consistent taper angles, which is essential for smooth and efficient product flow through curves and turns.
Call to Action
If you are looking for custom conveyor roller solutions that meet your specific needs, we invite you to contact us for more information. Our team of experts is ready to help you design and implement the perfect conveyor system for your operations. Whether you need standard metric rollers or specialized tapered conveyor rollers, we have the knowledge and experience to provide high-quality solutions.
For further insights into successful conveyor roller implementations, be sure to check out our additional resources and case studies. These documents highlight real-world applications and the tangible benefits our customers have experienced by using our conveyor roller solutions.
We also encourage you to share this post on social media and engage with us in the comments section. Your questions, experiences, and feedback are valuable to us, and we look forward to hearing from you. By participating in the discussion, you can gain deeper insights and contribute to a broader conversation about the latest advancements and best practices in conveyor roller technology.
FAQS about Tapered Conveyor Rollers
Tapered rollers are specifically designed for use in curved conveyor systems. Unlike regular rollers, which have a consistent diameter throughout their length, tapered rollers have a conical shape, with one end having a larger diameter than the other. This unique design allows the rollers to maintain the proper alignment and spacing of items as they move along a curved path. The tapering ensures that items on the conveyor are gently guided through the curve without jamming or falling off. Tapered rollers are crucial for applications where the conveyor system needs to navigate turns while maintaining a smooth flow of materials.
Conveyor rollers come in various types, each designed for specific applications and operational requirements. The main types include gravity rollers, which rely on the force of gravity to move items; powered rollers, which use motors or other mechanical means to drive the rollers and move items; tapered rollers, designed for curved conveyor sections; and impact rollers, which are reinforced to handle heavy or abrasive loads. Additionally, there are guide rollers used to keep items aligned on the conveyor, and idler rollers, which support the conveyor belt and assist in the smooth movement of materials. Each type of roller serves a distinct purpose, contributing to the efficiency and functionality of conveyor systems.
The primary difference between a drive roller and a driven roller lies in their function within a conveyor system. A drive roller is directly connected to a motor or other power source, providing the necessary force to move the conveyor belt or items on the conveyor. It is responsible for driving the motion of the conveyor. In contrast, a driven roller is not powered by itself but is moved by the friction and interaction with the conveyor belt or other rollers. Driven rollers help support and guide the belt, ensuring smooth and continuous movement. While drive rollers are the primary source of motion, driven rollers play a crucial supporting role in maintaining the conveyor system’s efficiency.
A roller conveyor is a type of conveyor system that uses rollers to transport materials or items from one location to another. The rollers are typically mounted within a frame and can be either gravity-driven or powered by motors. Roller conveyors are widely used in various industries, including manufacturing, warehousing, and distribution, due to their versatility and ability to handle a wide range of items, from small packages to heavy loads. These conveyors can be configured in straight, curved, or inclined sections, making them adaptable to different operational needs. The primary advantage of roller conveyors is their ability to facilitate efficient and automated material handling, reducing the need for manual labor and improving productivity.
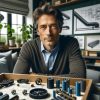
Jordan Smith, a seasoned professional with over 20 years of experience in the conveyor system industry. Jordan’s expertise lies in providing comprehensive solutions for conveyor rollers, belts, and accessories, catering to a wide range of industrial needs. From initial design and configuration to installation and meticulous troubleshooting, Jordan is adept at handling all aspects of conveyor system management. Whether you’re looking to upgrade your production line with efficient conveyor belts, require custom conveyor rollers for specific operations, or need expert advice on selecting the right conveyor accessories for your facility, Jordan is your reliable consultant. For any inquiries or assistance with conveyor system optimization, Jordan is available to share his wealth of knowledge and experience. Feel free to reach out at any time for professional guidance on all matters related to conveyor rollers, belts, and accessories.