Enhancing Operations: Rubber Return Conveyor Rollers
Rubber return conveyor rollers play a pivotal role in the efficiency and longevity of conveyor systems, marking a significant advancement in material handling technologies. These rollers are specifically designed to support the return path of the conveyor belt, ensuring smooth operation and minimizing wear. The incorporation of rubber in these rollers is a testament to the industry’s move towards more durable and less maintenance-intensive components. Their importance cannot be understated, as they directly contribute to reducing downtime and enhancing productivity across various applications. Whether in mining, agriculture, or manufacturing, the benefits of rubber return rollers extend beyond their immediate functionality, offering an improved material handling solution that emphasizes reliability and operational efficiency. This focus on rubber return rollers within conveyor systems underscores their essential role in modern industrial environments, where the demand for high-performance and cost-effective material handling solutions is ever-present.
What are Rubber Return Conveyor Rollers
Rubber return conveyor rollers are specialized components of conveyor systems designed to facilitate the smooth return of the conveyor belt to the starting point after it has transported materials to their destination. These rollers are coated or entirely made of rubber, enhancing their grip and reducing the wear on the conveyor belt due to friction.
Roles of Rubber Return Conveyor Rollers in Conveyor Systems
- Shock Absorption: Absorbs the impact of materials as they are dropped onto the conveyor, reducing wear.
- Material Shedding: Prevents material buildup by shedding sticky or wet materials that can adhere to the belt.
- Friction Management: Increases friction between the belt and roller, improving belt tracking and preventing slippage.
- Noise Reduction: The rubber material dampens operational noise, creating a quieter work environment.
- Corrosion Resistance: Offers superior resistance to corrosive substances, extending the lifespan of the conveyor system.
- Belt Protection: Minimizes the wear and tear on the conveyor belt by providing a soft contact surface.
- Energy Efficiency: Improves the energy efficiency of the conveyor system by reducing friction and enabling smoother operations.
- Versatility: Suitable for various applications, from mining to food processing, due to their non-marking and food-safe rubber options.
- Maintenance Reduction: Requires less maintenance compared to metal rollers, thanks to the durability of rubber.
- Safety: Reduces the risk of injuries associated with belt slippage or misalignment.
Difference Between Rubber Return Conveyor Rollers and Standard Conveyor Rollers
To highlight the differences between rubber return conveyor rollers and standard conveyor rollers, consider the following table:
Feature | Rubber Return Conveyor Roller | Standard Conveyor Roller |
---|---|---|
Material | Rubber coating or fully rubber | Metal, such as steel or aluminum |
Function | Specifically designed for the return path of the conveyor belt | General support for the conveying belt |
Impact Absorption | High, due to the softness of rubber | Lower, as metal is harder and less flexible |
Noise Level | Lower, thanks to rubber's sound-dampening properties | Higher, metal rollers can be noisy |
Friction & Grip | Higher friction and grip on the conveyor belt | Less grip compared to rubber |
Corrosion Resistance | Higher, especially with certain rubber compounds | Variable, depending on treatment and material |
Maintenance Requirements | Lower, due to rubber's durability and wear resistance | Higher, especially in harsh conditions |
Operational Environment | Suitable for both dry and wet environments | Best suited for dry environments |
Cost | Potentially higher initial cost, lower maintenance cost | Lower initial cost, but higher maintenance cost |
Application Versatility | Broad, thanks to rubber's adaptability to various substances | More limited, especially in food processing or corrosive environments |
Rubber return conveyor rollers are essential for enhancing the functionality, longevity, and safety of conveyor systems across a wide range of industries. Their unique properties, such as shock absorption, noise reduction, and corrosion resistance, distinguish them from standard conveyor rollers, making them a preferred choice for specific applications.
Benefits of Using Rubber Return Conveyor Rollers
The adoption of rubber return conveyor rollers in industrial and manufacturing processes brings with it a suite of advantages that significantly enhance the operation and longevity of conveyor systems. The inherent properties of rubber, combined with advanced manufacturing techniques, have resulted in rollers that stand out for their durability, efficiency, and operational benefits.
Advantages of Rubber Coating on Conveyor Rollers
- Shock Absorption: The elasticity of rubber allows these rollers to absorb shocks and impacts from heavy loads or materials dropping onto the conveyor, protecting both the conveyor belt and the materials being transported.
- Reduced Wear on Conveyor Belts: The softness of rubber minimizes the abrasive wear on conveyor belts, extending their life and reducing the need for frequent replacements.
- Increased Friction: Rubber has a higher coefficient of friction compared to metal or plastic, ensuring better grip and control of the conveyor belt, which is crucial for maintaining consistent belt speed and direction.
- Noise Reduction: Rubber’s natural sound-dampening qualities lead to quieter operation, a significant advantage in environments where noise pollution is a concern.
- Corrosion Resistance: Unlike metal rollers, rubber return conveyor rollers are resistant to corrosion caused by chemicals, moisture, and other corrosive elements, making them ideal for use in harsh environments.
- Material Shedding: Rubber’s slightly tacky surface helps to prevent material build-up by shedding unwanted debris and substances from the conveyor belt, aiding in cleaner operations and reducing maintenance.
- Energy Efficiency: The improved traction between the belt and roller can lead to lower power consumption, as the conveyor system requires less energy to move the belt smoothly.
- Vibration Damping: The rubber material is effective at absorbing vibrations, which reduces the transmission of vibration-induced stress to other components of the conveyor system, leading to fewer mechanical issues and breakdowns.
Enhanced Performance through Material Shedding and Friction
Rubber return conveyor rollers contribute significantly to material shedding, ensuring that sticky or wet materials do not adhere to the belt and cause tracking issues. This capability is particularly beneficial in industries dealing with challenging materials. Additionally, the increased friction provided by rubber enhances belt tracking, preventing slippage and misalignment that can lead to operational disruptions and safety hazards.
Durability in Corrosive Environments
The resilience of rubber in corrosive environments presents a clear advantage over traditional steel rollers. Steel, even when treated, can corrode over time when exposed to harsh chemicals, moisture, or salt, leading to weakened performance and the need for frequent replacements. In contrast, rubber maintains its integrity and functionality, offering a durable solution that can withstand the rigors of various operational conditions.
The integration of rubber return conveyor rollers into conveyor systems offers a broad spectrum of benefits, from enhanced operational efficiency to increased durability and reduced maintenance needs. Their ability to absorb shock, reduce noise, and resist corrosion makes them an invaluable component in the smooth and effective operation of conveyor systems across diverse industrial landscapes.
Types of Rubber Return Conveyor Rollers
The versatility of rubber return conveyor rollers is evident in the variety of types available, each designed to meet specific operational needs and challenges. This diversity ensures that industries can select the most suitable roller type, optimizing their conveyor systems for efficiency, longevity, and safety. Below, we detail the primary types of rubber return rollers, including the return roller tank, urethane return roller, and spiral return idler, highlighting their unique features and applications.
Overview of Rubber Return Conveyor Roller Types
Type | Design Features | Operational Benefits | Specialized Applications |
---|---|---|---|
Return Roller Tank | Features a solid rubber coating designed to withstand heavy loads. | Provides excellent shock absorption and is highly durable under significant weight. | Ideal for mining and aggregate industries where heavy, abrasive materials are common. |
Urethane Return Roller | Consists of a polyurethane coating, known for its extreme durability and resistance to abrasion. | Resists wear and tear, even in environments with abrasive materials. | Suitable for applications requiring exceptional durability and abrasion resistance, such as in recycling plants or processing abrasive materials. |
Spiral Return Idler | Incorporates a spiral design to aid in the cleaning of the conveyor belt by actively shedding material. | Helps maintain clean belt surfaces, improving tracking and reducing maintenance. | Perfect for industries dealing with sticky or wet materials that tend to cling to the belt, such as food processing or waste management. |
Detailed Analysis of Rubber Return Conveyor Roller Types
- Return Roller Tank: This roller type is specifically designed to manage and endure the stress of heavy loads. The solid rubber coating not only absorbs shocks but also ensures that the roller remains operational even under the extreme pressure of heavy materials, such as ores in mining operations. The robust design makes it an essential component in heavy-duty applications where durability and reliability are critical.
- Urethane Return Roller: Urethane rollers offer an enhanced level of durability and are particularly adept at resisting wear from abrasive materials. This makes them an excellent choice for environments where the conveyor system is exposed to harsh materials on a regular basis. Their superior wear resistance translates to longer service life and reduced maintenance costs, making them a cost-effective solution for challenging industrial applications.
- Spiral Return Idler: The unique spiral design is engineered to actively shed materials from the conveyor belt, which is crucial for maintaining optimal conveyor performance. By preventing material build-up, these rollers contribute to smoother operations, improved belt tracking, and reduced downtime for cleaning. They are especially beneficial in industries where conveyor belts are prone to collecting debris, ensuring that the system remains efficient and reducing the need for manual intervention.
Understanding the different types of rubber return conveyor rollers and their specific applications is key to optimizing conveyor system performance. Whether the priority is durability, abrasion resistance, or cleanliness, there is a rubber return roller designed to meet those needs. By selecting the appropriate roller type, industries can achieve more reliable, efficient, and cost-effective material handling solutions.
Choosing the Right Rubber Return Conveyor Roller
Selecting the appropriate rubber return conveyor roller is crucial for the efficiency, durability, and overall performance of conveyor systems. The right roller can significantly reduce maintenance costs, enhance operational efficiency, and extend the lifespan of the conveyor belt. Below, we delve into the importance of choosing the right roller and the key factors to consider during the selection process.
Importance of Selecting the Right Rubber Return Conveyor Roller
- Optimized Performance: The right roller ensures the conveyor operates at peak efficiency.
- Reduced Maintenance Costs: Appropriate rollers minimize wear and tear, reducing maintenance needs.
- Extended Belt Life: The correct roller type can significantly prolong the life of the conveyor belt.
- Improved Safety: Properly selected rollers reduce the risk of malfunctions that could lead to safety incidents.
- Enhanced Material Handling: Specific roller types can better handle certain materials, improving throughput.
- Energy Efficiency: The right roller choice can lead to reduced energy consumption by the conveyor system.
- Adaptability to Environmental Conditions: Rollers suited to the operating environment will perform better and last longer.
- Cost-effectiveness: Over time, the right rollers can lead to significant savings in operational and replacement costs.
Factors to Consider When Choosing a Rubber Return Conveyor Roller
- Material Type: Consider the types of materials the conveyor will transport to ensure compatibility.
- Load Capacity: Match the roller’s load capacity with the weight of the materials to be transported.
- Conveyor Speed: Ensure the roller can handle the operational speed of the conveyor.
- Environment: Consider factors like temperature, moisture, and exposure to corrosive substances.
- Abrasion Resistance: For handling abrasive materials, choose rollers with high abrasion resistance.
- Impact Resistance: In operations involving heavy or sharp objects, impact resistance is key.
- Chemical Compatibility: Ensure the rubber material is resistant to any chemicals it may come into contact with.
- Maintenance Requirements: Consider how easy the rollers are to maintain and replace.
- Customization Options: Look for suppliers that offer customization to meet specific operational needs.
- Cost: Balance upfront costs with long-term savings in maintenance, energy efficiency, and operational efficiency.
Customization Options and Supplier Selection
The Rulmeca rollers catalogue and Superior conveyor rollers are excellent resources for finding a wide range of rubber return conveyor rollers. Both suppliers provide extensive options for customization, allowing you to tailor the roller specifications to your conveyor system’s unique requirements. Whether it’s adapting to extreme environmental conditions, handling specific load capacities, or meeting precise speed requirements, these catalogues offer solutions designed to optimize conveyor system performance.
Choosing the right rubber return conveyor roller involves careful consideration of various operational factors. By understanding the specific needs of your conveyor system and leveraging the customization options offered by reputable suppliers like Rulmeca and Superior, you can ensure your conveyor operates efficiently, safely, and cost-effectively. This strategic approach not only enhances the immediate performance of your conveyor system but also contributes to its long-term sustainability and success.
Maintenance and Replacement Parts for Rubber Return Conveyor Rollers
Proper maintenance and timely replacement of worn parts are crucial for ensuring the longevity and optimal performance of rubber return conveyor rollers. By adhering to a comprehensive maintenance routine, you can avoid costly downtimes and extend the life of your conveyor system. Here are detailed maintenance tips, common replacement parts, and guidance on sourcing quality replacements.
Maintenance Tips for Rubber Return Conveyor Rollers
- Regular Inspections: Conduct regular visual and manual inspections to check for signs of wear, damage, or misalignment.
- Cleanliness: Keep the rollers and conveyor belt clean to prevent material buildup that can cause damage or inefficiency.
- Lubrication: Ensure that any bearings or moving parts are properly lubricated according to the manufacturer’s recommendations.
- Alignment Checks: Periodically check the alignment of the rollers to ensure that the conveyor belt tracks correctly.
- Bearing Inspection: Monitor the condition of bearings and replace them if they show signs of wear or noise.
- Tension Adjustment: Maintain proper tension on the conveyor belt to prevent slippage or excessive wear.
- Environmental Monitoring: Be aware of changes in the environment, such as temperature or humidity, that might affect the performance of the rollers.
- Load Distribution: Ensure that materials are evenly distributed across the conveyor to avoid uneven wear on the rollers.
- Replacement Scheduling: Establish a schedule for replacing rollers based on usage and condition rather than waiting for failure.
- Damage Prevention: Implement measures to prevent damage from overloading or improper use of the conveyor system.
- Training: Ensure that personnel are trained in the proper operation and maintenance of the conveyor to avoid mishandling.
- Record Keeping: Keep detailed records of maintenance, inspections, and replacements to track the performance and needs of your conveyor system.
Common Parts That May Need Replacement
- Bearings: Signs of wear include noise or movement in the roller.
- Rubber Coating: Look for cracks, wear, or areas where the rubber has begun to peel away.
- Shafts: Bent or worn shafts can cause the roller to misalign.
- Seals: Damaged seals can allow contaminants to enter the roller, leading to premature failure.
- End Caps: Cracks or damage to end caps can affect the roller’s structural integrity.
- Mounting Brackets: Wear or damage can affect the roller’s positioning.
- Spacers: Ensure spacers are not worn to maintain proper roller alignment.
- Clamps: Check for wear or damage that could lead to roller slippage.
- Retaining Rings: Inspect for wear or deformation that might allow parts to loosen.
Sourcing Quality Replacement Parts
When sourcing replacement parts for rubber return conveyor rollers, prioritize compatibility with your existing system to ensure seamless operation. It’s crucial to use parts that match the specifications of your conveyor to maintain performance and safety standards. Look for reputable suppliers who offer high-quality, durable parts designed specifically for conveyor systems. The importance of using genuine or approved replacement parts cannot be overstated, as they are crucial for maintaining the efficiency, reliability, and longevity of your conveyor system.
Regular maintenance and timely replacement of parts are essential practices for the upkeep of rubber return conveyor rollers. By following the outlined maintenance tips, being vigilant about wear and tear, and sourcing quality replacement parts, you can ensure that your conveyor system operates smoothly and efficiently over its lifetime.
Cost Considerations for Rubber Return Conveyor Rollers
When integrating or upgrading rubber return conveyor rollers within your conveyor system, understanding the cost implications is vital for budgeting and long-term financial planning. The initial purchase price of rollers is just one aspect of the overall cost; factors such as durability, maintenance requirements, and operational efficiency play crucial roles in the total cost of ownership.
Overview of Pricing for Rubber Return Conveyor Rollers
The pricing of rubber return conveyor rollers can vary widely based on several factors. Here are ten key factors that affect the cost:
- Material Quality: High-quality rubber materials may have a higher upfront cost but offer better durability and longevity.
- Size and Dimensions: Larger or custom-sized rollers typically cost more due to the increased amount of materials and customization required.
- Load Capacity: Rollers designed to support heavier loads often come at a premium because of the need for stronger materials and construction.
- Environmental Resistance: Rollers made to withstand harsh environmental conditions, such as extreme temperatures or corrosive materials, may have higher prices.
- Brand and Manufacturer: Premium brands known for quality and reliability might charge more for their rollers.
- Customization: Any customization to fit specific conveyor systems can add to the cost.
- Quantity: Purchasing in bulk can sometimes reduce the per-unit cost.
- Shipping and Handling: Depending on the location of the manufacturer and the delivery destination, shipping costs can significantly affect the overall price.
- Installation and Setup: The complexity of installation and any necessary modifications to the conveyor system can impact costs.
- Warranty and Support: Rollers that come with extended warranties or comprehensive customer support may be priced higher but offer value in long-term reliability and assistance.
Cost-Benefit Analysis of Quality Rollers
Investing in high-quality rubber return conveyor rollers upfront can lead to significant long-term savings. While the initial purchase price might be higher, quality rollers offer several financial advantages:
- Reduced Maintenance Costs: Durable rollers require less frequent replacements and can significantly lower maintenance expenses over time.
- Operational Efficiency: Quality rollers contribute to smoother operations, reducing the risk of downtime and associated costs.
- Extended Conveyor Life: By minimizing wear and tear on the conveyor belt, high-quality rollers can extend the lifespan of the entire system, delaying the need for costly overhauls or replacements.
- Energy Savings: Efficient rollers that maintain proper belt alignment and tension can lead to reduced energy consumption, lowering operational costs.
While the upfront cost of rubber return conveyor rollers is an important consideration, evaluating the total cost of ownership reveals the true value of investing in quality components. High-quality rollers may have a higher initial price tag, but their contribution to reducing maintenance costs, enhancing operational efficiency, and extending the lifespan of conveyor systems can offer significant financial benefits in the long run. This cost-benefit analysis is essential for decision-makers to ensure that their investment in conveyor components delivers the best possible return over time.
Where to Buy Rubber Return Conveyor Rollers
Purchasing rubber return conveyor rollers requires careful consideration to ensure you obtain high-quality components that meet your conveyor system’s specific needs. Whether you’re looking for new, used, or refurbished rollers, following these pieces of advice can help you make an informed decision.
Advice on Purchasing Rubber Return Conveyor Rollers
- Research Suppliers: Start by researching reputable suppliers known for quality conveyor components. Look for reviews, testimonials, and industry recommendations.
- Compare Prices: Obtain quotes from multiple suppliers to compare prices. However, remember that the cheapest option may not always be the best in terms of quality and durability.
- Check Compatibility: Ensure the rollers are compatible with your existing conveyor system to avoid operational issues.
- Inquire About Customization: If your system has specific requirements, ask suppliers about customization options.
- Assess Quality Standards: Look for suppliers that adhere to recognized quality standards and certifications.
- Consider Delivery Times: Check delivery times to ensure they align with your project timelines, especially if replacements are urgently needed.
- Warranty and Support: Prefer suppliers offering warranties and comprehensive customer support for their products.
- Explore Refurbished Options: For budget constraints, consider high-quality refurbished rollers, but verify their condition and reliability.
- Bulk Purchases: If you need a significant quantity, inquire about bulk purchase discounts.
- Sustainability Practices: Consider suppliers committed to sustainability practices if environmental impact is a concern for your operations.
Finding Reputable Suppliers
Reputable suppliers of rubber return conveyor rollers can be found through industry directories, trade shows, and professional networks. Brands like Rulmeca and Superior are known for their high-quality conveyor components. Additionally, online marketplaces and forums dedicated to industrial equipment can be valuable resources for finding both new and used rollers.
Importance of Consulting with Experts
- System Compatibility: Experts can help ensure the rollers are compatible with your system, avoiding costly mismatches.
- Operational Efficiency: Consultants can advise on the best roller types for your specific operational needs.
- Cost-Effectiveness: Professionals can help conduct a cost-benefit analysis, ensuring you invest wisely for long-term savings.
- Quality Assurance: Experts can guide you to reputable suppliers known for their quality and reliability.
- Customization Needs: They can help identify when customization is necessary and which suppliers offer such services.
- Maintenance Advice: Professionals can offer maintenance tips and best practices for extending the lifespan of your rollers.
- Regulatory Compliance: Ensure that the products comply with industry standards and regulations.
- Future-Proofing: Advice on how to select rollers that can adapt to future expansions or operational changes.
- Risk Management: Experts can help identify potential risks and recommend solutions to mitigate them.
When looking to purchase rubber return conveyor rollers, taking the time to research, compare, and consult with experts is crucial. This approach ensures you invest in components that enhance the efficiency, reliability, and longevity of your conveyor system. With the right information and resources, you can find high-quality rollers that meet your specific requirements, whether through direct suppliers, online platforms, or through industry contacts.
FAQs about Rubber Return Conveyor Roller
Conveyor rollers are diverse components crucial for the smooth functioning of conveyor systems. They are primarily categorized based on their application and the type of load they carry. The common types include:
Straight Rollers: These are the standard rollers designed to transport material across a flat area.
Tapered Rollers: Ideal for curved sections of conveyors, helping maintain the alignment of the materials.
Impact Rollers: Positioned at loading points to absorb the forces exerted by falling materials.
Return Rollers: They support the return side of the conveyor belt after it has released the conveyed materials.
Rubber-Coated Rollers: These have a rubber coating for added grip and to reduce wear on the conveyor belt.
Grooved Rollers: Specifically designed for moving belts and can be used to drive the belt under certain conditions.
Each type serves a specific function within the conveyor system, and the right selection can enhance the efficiency and longevity of the conveyor belt operation.
A return idler is a specific type of conveyor roller that is situated on the underside or return side of the conveyor belt. Its main purpose is to provide support to the belt as it travels back to the beginning of the conveyor system for another cycle. Return idlers help to maintain the structural integrity of the conveyor belt, reducing sagging and ensuring that the belt remains clean and intact during its return trip. They are strategically spaced along the conveyor framework and are essential for the longevity and efficiency of the belt. Return idlers can be flat or may incorporate rubber discs to help clean the belt and minimize the buildup of materials.
Conveyor idler rollers are cylindrical rods that function as part of the support system for conveyor belts. They are called “idlers” because they do not directly drive or move the belt but rather idly spin as the belt moves over them. There are several types of idler rollers that serve different purposes within the conveyor system:
Carrying Idlers: Support the weight of the belt and the material being transported.
Return Idlers: Support the empty belt on its return journey.
Impact Idlers: Absorb the shock of materials falling onto the belt.
Guide Idlers: Help to keep the belt aligned and prevent it from wandering off course.
Self-Aligning Idlers: Automatically adjust the belt alignment to prevent misalignment issues.
The selection and placement of idler rollers are crucial for the operational efficiency and maintenance requirements of the conveyor system.
Impact rollers in a belt conveyor are specialized rollers designed to absorb the shock and impact of falling materials at the loading and transfer points on the conveyor belt. They are typically located beneath the belt at these points and are constructed with a series of rubber discs or rings that cushion the load, reducing the impact on both the materials being conveyed and the conveyor system itself. The use of impact rollers helps to extend the life of the conveyor belt, prevent damage to the rollers, and reduce the noise and vibration that can occur when materials are dropped onto the conveyor system. By mitigating the force of impact, these rollers play a critical role in maintaining the structural health of the conveyor and ensuring smooth operation.
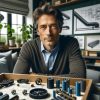
Jordan Smith, a seasoned professional with over 20 years of experience in the conveyor system industry. Jordan’s expertise lies in providing comprehensive solutions for conveyor rollers, belts, and accessories, catering to a wide range of industrial needs. From initial design and configuration to installation and meticulous troubleshooting, Jordan is adept at handling all aspects of conveyor system management. Whether you’re looking to upgrade your production line with efficient conveyor belts, require custom conveyor rollers for specific operations, or need expert advice on selecting the right conveyor accessories for your facility, Jordan is your reliable consultant. For any inquiries or assistance with conveyor system optimization, Jordan is available to share his wealth of knowledge and experience. Feel free to reach out at any time for professional guidance on all matters related to conveyor rollers, belts, and accessories.