Rubber Covered Conveyor Rollers: Industry Applications
In modern industrial operations, the importance of rubber covered conveyor rollers cannot be overstated. These rollers are crucial for the efficient movement of goods across various stages of production and packaging. By employing a rubber coating, these rollers offer enhanced grip, which is vital for transporting items securely without slippage. Additionally, the rubber covering significantly reduces wear and tear on both the rollers and the conveyed materials, extending the lifespan of the equipment. This protective layer also helps in minimizing operational noise, contributing to a safer and more pleasant working environment.
Types of Rubber Covered Conveyor Rollers
Rubber covered conveyor rollers are vital for diverse industrial applications, each type designed to meet specific operational challenges:
- Chain-Driven Rollers: These robust rollers are connected via chains, providing high torque and durability, ideal for industries like mining and heavy manufacturing where heavy loads and rough conditions are common.
- Belt-Driven Rollers: Common in automated warehouses and distribution centers, these rollers use a continuous belt to ensure smooth, steady transport of goods, minimizing jolts and vibrations.
- Rubber-Coated Drive Rollers: With a focus on traction, these rollers are essential in industries where conveyance of slippery or unevenly shaped items is common. The rubber coating increases friction, preventing items from sliding off.
- Grooved Rollers: These are specifically designed with grooves to keep conveyor belts perfectly aligned, crucial for precision tasks in industries like electronics and pharmaceuticals where precise movement and placement are required.
- Impact Rollers: Positioned at points where materials are loaded onto the belt, these rollers absorb impact and distribute loads evenly. This is vital for reducing wear and tear on both the belt and the rollers in industries such as construction and aggregate processing.
- Return Rollers: These are used on the underside of conveyor systems to support the belt and keep it clean, ensuring it runs smoothly without excessive wear or accumulation of debris, key in maintaining the longevity and efficiency of the conveyor system.
Each type serves a unique function, enhancing the conveyor system’s efficiency and adaptability to specific industrial environments. This specialization ensures that operations are not only efficient but also cost-effective by extending the life of the equipment and minimizing maintenance needs.
Materials and Manufacturing of Rubber Covered Conveyor Rollers
Rubber covered conveyor rollers are critical components in a variety of industrial settings, ensuring efficient material handling across numerous sectors. These rollers are tailored using specific materials and manufacturing processes to meet diverse operational demands. Here’s a deeper dive into the materials used and the meticulous manufacturing processes involved.
Materials Used for Rubber Coverings:
The choice of rubber material significantly impacts the performance, durability, and suitability of conveyor rollers for specific environments.
- Buna-N (Nitrile Rubber): Excellent for oil-rich environments, it resists swelling and wear under exposure to oils and fats, ensuring longevity in automotive or food processing applications.
- Neoprene: This all-rounder offers good chemical stability and flexibility over a wide temperature range, making it suitable for outdoor machinery and marine environments.
- Styrene-Butadiene Rubber (SBR): Preferred for its abrasion resistance, SBR is cost-effective for bulk handling applications where wear is a concern.
- Natural Rubber: It stands out for its ability to deform and quickly recover its shape, providing high grip and reducing slippage.
- Silicone: Best for high-temperature applications, it remains stable and flexible in environments that would degrade other rubbers.
- Polyurethane: Combines the elasticity of rubber with the toughness and durability of metal, perfect for rollers that undergo severe wear.
- Ethylene Propylene Diene Monomer (EPDM): With its excellent resistance to weather, water, and steam, EPDM is ideal for use in harsh outdoor conditions.
Manufacturing Process and Customization:
The manufacturing process of rubber covered conveyor rollers is complex and customizable to fit the unique needs of each application.
- Compounding: Custom recipes of rubber and additives are blended to achieve specific performance characteristics required by the application.
- Molding: Techniques such as injection, compression, or transfer molding are used to shape the rubber to precise dimensions.
- Machining: Rollers are machined to achieve exacting tolerances, ensuring they fit seamlessly into existing conveyor systems.
- Coating: Multiple layers of rubber might be applied to enhance performance in terms of grip and wear resistance.
- Curing: Heat and pressure are applied to set the rubber, a critical step that determines the roller’s final properties.
- Finishing: The rollers may be ground to smooth the surface or grooved to improve traction and direct liquids away.
- Quality Control: Rigorous testing ensures that each roller meets strict industrial standards and client expectations.
- Custom Solutions: Options such as variable rubber thicknesses, durometer ratings, and color coding are available to meet specific requirements.
- Rapid Prototyping: Advanced techniques allow for quick production of sample rollers, helping clients verify design specifications before full-scale manufacturing.
Through these detailed steps, manufacturers ensure that each roller not only meets the required specifications but also contributes to the efficiency and safety of the industrial operations they facilitate.
Applications in Industry of Rubber Covered Conveyor Rollers
Rubber covered conveyor rollers are integral to various industrial sectors, enhancing both efficiency and safety. Here’s how they are applied across different fields:
- Food and Beverage Processing: Rollers transport delicate items like food packages, where non-marking and hygienic rubber coatings prevent contamination and damage.
- Pharmaceuticals: In environments demanding sterility, these rollers ensure gentle handling of sensitive medical supplies and drugs.
- Automotive Manufacturing: Used for moving large car components along assembly lines, rubber rollers absorb shocks and prevent scratches.
- Mining and Quarrying: Durable rubber withstands abrasive materials and harsh conditions, reducing equipment wear.
- Printing and Publishing: These rollers help in the precise and smooth movement of paper, crucial for high-quality print results.
- Packaging Industry: Rubber rollers facilitate the efficient packaging of goods by enhancing grip and reducing slippage on conveyor belts.
- Agriculture: Employed in the processing and packing of agricultural products, ensuring that products are handled gently to preserve quality.
Each application highlights specific benefits such as reduced noise levels, increased grip that prevents slippage, resistance to abrasive materials, shock absorption capabilities, and the ability to withstand extreme environmental conditions. This specificity ensures that rubber covered conveyor rollers are not just functional but crucial for maintaining high productivity and safety standards across industries.
Purchasing Rubber Covered Conveyor Rollers
Rubber covered conveyor rollers are essential for a variety of industries, offering durability and efficiency in materials handling. Purchasing these rollers involves considering multiple sources to ensure the best fit for specific operational needs. These rollers can be sourced globally or locally, offering buyers a range of options based on quality, cost, and delivery times. Understanding the diverse channels through which these rollers can be acquired helps businesses make informed purchasing decisions.
Finding Rubber Covered Conveyor Rollers
Locating the right rubber covered conveyor rollers requires understanding the various marketplaces and suppliers available.
- Manufacturer Direct Sales: Ideal for obtaining the most current product lines with reliable after-sales support.
- Industrial Equipment Suppliers: These distributors typically have extensive catalogs and can offer quick delivery options.
- Online Industrial Marketplaces: Such platforms often provide a broad range of products from various manufacturers globally.
- Second-Hand Equipment Vendors: Useful for companies looking to reduce costs without compromising on quality.
- Industry Specific Trade Shows: These events provide opportunities to directly interact with manufacturers and view product demos.
- Local Supply Stores: They offer the convenience of immediate purchase and personal customer service.
- Factory Direct Purchases: This option might offer cost benefits, especially when ordering in bulk.
- Niche Retailers: Focus on specific segments of the industrial equipment market.
- Online Classifieds and Auctions: Can be a source for finding unusual sizes or models not commonly available.
Comparing Prices and Choosing Suppliers
Selecting the right supplier for rubber conveyor roller covers involves more than just price comparison; it requires a holistic approach considering various factors.
- Total Cost Evaluation: Factor in all associated costs, such as shipping and installation.
- Warranty and Service Agreements: Important for long-term reliability and maintenance support.
- User Testimonials and Reviews: Provide real-world insight into product performance and supplier reliability.
- Quotation Analysis: Gather multiple quotes to ensure competitive pricing and favorable terms.
- Supplier’s Reputation and Longevity: Established suppliers are likely to offer consistent product quality and better customer service.
- Customization Flexibility: Suppliers who offer customization may be preferable for unique application needs.
- Timeliness of Delivery: Essential to keep project timelines on track.
- Volume Discounts: Negotiating for larger orders can substantially lower costs.
- Certifications and Standards Compliance: Ensure the rollers meet all necessary industry standards for safety and performance.
By taking these factors into account, businesses can make strategic decisions that optimize their operations and supply chains.
Installation and Maintenance of Rubber Covered Conveyor Rollers
The effective installation and maintenance of rubber covered conveyor rollers are critical for optimizing their performance and extending their operational life. Proper installation ensures that the rollers function smoothly and efficiently, while regular maintenance prevents premature wear and unexpected failures. This section will provide detailed advice on installing rollers, specifically focusing on keyway and press-fit types, along with comprehensive maintenance tips to ensure the longevity and optimal performance of these essential industrial components.
Installation Advice for Rubber Covered Conveyor Rollers
Introduction: Proper installation of rubber covered conveyor rollers is crucial for their effective operation and longevity. Here’s how to install keyway and press-fit types:
- Assess Roller Alignment: Ensure rollers are perfectly aligned with the conveyor frame to prevent uneven wear.
- Prepare the Shaft: Clean and inspect the shaft for any irregularities that might impair installation.
- Apply Lubrication: Use appropriate lubricants on the shaft to ease the installation of press-fit rollers.
- Using Keyways: Ensure the key fits snugly within the shaft and roller keyway slot for secure installation.
- Press-fit Installation: Use a mechanical press to evenly apply pressure when installing press-fit rollers to avoid damaging the roller.
- Secure Attachments: Tighten any fasteners or set screws to prevent the roller from shifting during operation.
- Check Roller Spacing: Proper spacing between rollers ensures smooth belt movement and reduces stress.
- Test Before Full Operation: Run the conveyor at low speed to ensure the rollers are installed correctly and functioning smoothly.
- Regular Inspection Post-Installation: Monitor the rollers during the initial hours of operation to address any issues promptly.
Maintenance Tips for Rubber Covered Conveyor Rollers
Introduction: Regular maintenance of rubber covered conveyor rollers extends their service life and maintains their performance.
- Regular Cleaning: Remove debris and residues that can cause roller damage.
- Lubricate Bearings: Regularly lubricate the bearings to reduce friction and wear.
- Inspect for Wear and Tear: Regularly check rollers for signs of wear or damage and replace if necessary.
- Check for Misalignment: Realign rollers if they show signs of misalignment to prevent uneven wear.
- Monitor Load Distribution: Ensure that loads are evenly distributed across the conveyor to avoid excessive pressure on rollers.
- Temperature Checks: Monitor the temperature of the rollers, as excessive heat can indicate bearing issues.
- Replace Worn Seals: Check and replace any worn seals to prevent dust and particles from entering the bearings.
- Scheduled Downtime for Maintenance: Plan for regular maintenance checks to minimize unexpected breakdowns.
- Keep Spare Rollers: Maintain a stock of spare rollers to facilitate quick replacements when necessary.
Implementing these installation and maintenance practices will help ensure that rubber covered conveyor rollers operate efficiently and last longer, supporting uninterrupted industrial operations.
Local Suppliers and Services for Rubber Covered Conveyor Rollers
Introduction: Locating reliable local suppliers and service providers for rubber covered conveyor rollers can significantly enhance operational efficiency. This section details how to find nearby manufacturers and coating services, and discusses the benefits of local sourcing.
Finding Local Rubber Roller Manufacturers and Coating Services
Introduction: Securing a reliable local supplier for rubber covered conveyor rollers can enhance production efficiency and reduce logistical challenges. Here’s how to effectively find nearby manufacturers and coating services:
- Business Directories and Search Engines: Utilize platforms like Google My Business and Yelp to search for manufacturers and service providers in your region.
- Industry Trade Associations: Membership in industry-specific associations often gives access to a vetted directory of suppliers.
- Local Trade Shows and Industrial Expos: These events are ideal for connecting with local manufacturers and gauging their capabilities firsthand.
- Regional Business Networking Events: Participate in local chamber of commerce meetings or industry networking events.
- Online Reviews and Forums: Check platforms like Reddit or industry forums where businesses are often reviewed and discussed.
- Social Media and Professional Networks: Platforms like LinkedIn can provide insights into local manufacturers’ reputations and operations.
- Referrals from Business Contacts: Leverage the power of word-of-mouth by asking for supplier recommendations from industry peers.
- Local Industry Publications: Advertisements and articles in these publications can lead you to reputable suppliers.
- Consulting with Industry Experts: Hire or consult industry experts who possess a comprehensive understanding of local suppliers.
Importance of Local Sourcing for Quick Turnaround and Support
Introduction: Local sourcing for rubber covered conveyor rollers offers significant operational benefits, from reducing costs to improving supply chain dynamics.
- Speed of Delivery: Local suppliers can significantly shorten delivery times, which is crucial during production ramp-ups or when unexpected needs arise.
- Reduced Transportation Costs: Proximity cuts down on long-distance shipping fees and the carbon footprint associated with transport.
- Economic Impact: Supporting local businesses helps stimulate the local economy by keeping spending within the community.
- Direct Communication: Local sourcing allows for direct interactions, which can lead to better service and quicker problem resolution.
- Adaptability and Customization: Local suppliers are typically more flexible in meeting specific needs and making adjustments on short notice.
- Efficient Inventory Management: Closer suppliers mean shorter lead times, allowing for more efficient inventory management.
- Enhanced Customer Service: Local businesses often provide superior customer service to maintain their reputation within the community.
- Understanding of Local Market Conditions: Local suppliers are more attuned to the regional market conditions and can offer relevant advice.
- Networking Opportunities: Building relationships with local suppliers may lead to new business opportunities through their own networks.
These strategies not only ensure a reliable supply of rubber covered conveyor rollers but also strengthen your business’s ability to respond swiftly and effectively to market demands and operational needs.
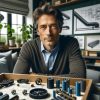
Jordan Smith, a seasoned professional with over 20 years of experience in the conveyor system industry. Jordan’s expertise lies in providing comprehensive solutions for conveyor rollers, belts, and accessories, catering to a wide range of industrial needs. From initial design and configuration to installation and meticulous troubleshooting, Jordan is adept at handling all aspects of conveyor system management. Whether you’re looking to upgrade your production line with efficient conveyor belts, require custom conveyor rollers for specific operations, or need expert advice on selecting the right conveyor accessories for your facility, Jordan is your reliable consultant. For any inquiries or assistance with conveyor system optimization, Jordan is available to share his wealth of knowledge and experience. Feel free to reach out at any time for professional guidance on all matters related to conveyor rollers, belts, and accessories.