PPI Guide Rollers: Ensuring Conveyor Reliability
Precision Pulley & Idler (PPI) stands as a pivotal manufacturer in the conveyor system industry, renowned for its high-quality components that enhance the efficiency and longevity of conveyor systems. Among its wide range of products, PPI guide rollers are particularly noteworthy for their critical role in maintaining the alignment and performance of conveyor belts. These guide rollers are engineered to prevent the belt from drifting off its intended path, thereby reducing wear and tear on both the belt and the conveyor structure. The importance of guide rollers in conveyor systems cannot be overstated; they are essential in ensuring smooth, uninterrupted operations across various industries, from mining and aggregate production to food processing and distribution. By incorporating PPI guide rollers into their systems, businesses can significantly improve the reliability and productivity of their conveyor operations.
The Role of PPI Guide Rollers
Precision Pulley & Idler (PPI) guide rollers play an indispensable role in the operational efficiency of conveyor systems. These components are not just accessories but are fundamental in maintaining the conveyor belt’s alignment and functionality. The significance of PPI guide rollers extends across various dimensions of conveyor system performance, emphasizing their critical role in industrial operations.
Primary Functions of PPI Guide Rollers
At the heart of conveyor system efficiency and longevity are the PPI guide rollers, engineered with precision to fulfill several critical functions. These rollers are more than just parts; they are the backbone of conveyor belt reliability and performance. Here, we delve into the primary functions that set PPI guide rollers apart, highlighting their indispensable role in the seamless operation of conveyor systems.
- Alignment Correction: Central to their design, PPI guide rollers correct misalignments of the conveyor belt, ensuring it travels along the intended path. This correction is vital for the smooth operation of the system and helps prevent material spillage.
- Protection of Conveyor Framework: By maintaining belt alignment, PPI guide rollers safeguard the conveyor framework against wear and damage, which can occur from the belt rubbing against the structure.
- Reduced Maintenance Costs: With the belt alignment kept in check by PPI guide rollers, the frequency of maintenance and repairs is significantly reduced, leading to lower operational costs.
- Enhanced Belt Lifespan: The lifespan of conveyor belts is extended thanks to PPI guide rollers, which prevent edge fraying and reduce stress on the belt fabric.
- Improved Safety: The risk of accidents and material spillage is minimized with the use of PPI guide rollers, contributing to a safer working environment.
- Versatility: Designed for adaptability, PPI guide rollers can accommodate a variety of conveyor belt sizes and types, making them suitable for a broad range of applications.
- Efficiency in Operation: The efficiency of material transport along the conveyor system is ensured by the smooth operation of conveyor belts, supported by PPI guide rollers.
- Prevention of Material Loss: Proper belt alignment, maintained by PPI guide rollers, is crucial in preventing the loss of materials during conveyance, which is essential for operational efficiency and profitability.
Importance in Preventing Belt Misalignment and Damage
The role of PPI guide rollers extends beyond mere functionality; they are pivotal in preventing belt misalignment and the subsequent damage that can ensue. Misalignment is not just a minor inconvenience; it can lead to significant operational challenges and safety issues. Below, we explore the critical importance of PPI guide rollers in maintaining conveyor belt alignment and preventing damage, underscoring their value in industrial applications.
- Minimized Operational Downtime: By preventing belt misalignment, PPI guide rollers significantly reduce downtime, which can otherwise lead to operational disruptions and financial losses.
- Reduced Wear on Components: Misaligned belts can cause excessive wear on conveyor components. PPI guide rollers mitigate this wear, prolonging the lifespan of these components.
- Energy Efficiency: Aligned belts facilitated by PPI guide rollers require less energy to operate, contributing to the energy efficiency of the conveyor system.
- Consistent Product Quality: Smooth and consistent belt movement, ensured by PPI guide rollers, plays a crucial role in maintaining the quality of the conveyed product.
- Prevention of Belt Slippage: Belt slippage, a common issue with misaligned belts, is effectively prevented by PPI guide rollers, ensuring the belt remains in its proper path.
- Optimized Material Handling: The smooth and reliable transport of materials is significantly enhanced by the use of PPI guide rollers, optimizing the material handling process.
- Environmental Protection: PPI guide rollers contribute to environmental protection by reducing material spillage and thus minimizing waste and contamination.
- Compliance with Regulations: In many sectors, regulations mandate the use of mechanisms like PPI guide rollers to ensure the safe and efficient operation of conveyor systems, highlighting their critical role in compliance and safety efforts.
Through these functions and benefits, PPI guide rollers prove to be essential components in the design and operation of effective conveyor systems, ensuring not only the longevity and efficiency of the conveyor itself but also the safety and productivity of the entire operation.
Key Features of PPI Guide Rollers
Precision Pulley & Idler (PPI) guide rollers are distinguished by their innovative design and engineering, which cater to the demanding needs of conveyor systems across various industries. The key features of PPI guide rollers underscore their superiority and adaptability, making them indispensable components for enhancing conveyor performance and reliability. Here, we delve into at least nine key features that set PPI guide rollers apart from the competition.
- Prevention of Belt Damage: A fundamental feature of PPI guide rollers is their ability to prevent belt damage by ensuring that the conveyor belt remains centered, thus avoiding contact with the conveyor framework. This significantly reduces wear and tear on the belt, extending its service life.
- Ease of Installation: PPI guide rollers are designed with slotted foot pads, which not only facilitate easy installation but also allow for quick adjustments to be made on-site, ensuring optimal alignment and performance with minimal downtime.
- Compatibility with Legacy Products: Understanding the diverse nature of conveyor systems, PPI guide rollers are engineered to be compatible with existing legacy products in the marketplace. This ensures seamless integration and upgrades, providing flexibility and cost-effectiveness for system operators.
- Robust Construction: Crafted from high-quality materials, PPI guide rollers boast a robust construction that can withstand harsh operating conditions, including extreme temperatures, heavy loads, and abrasive materials, ensuring long-term reliability and performance.
- Precision Engineering: Each PPI guide roller is precision-engineered to provide the utmost in performance and durability. The meticulous design ensures that rollers operate with minimal friction and wear, contributing to the overall efficiency of the conveyor system.
- Adjustable Tensioning: To accommodate varying operational needs, PPI guide rollers feature adjustable tensioning systems. This allows for precise control over the belt’s alignment, ensuring optimal performance under different load conditions and belt speeds.
- Low Maintenance Requirements: The design and materials used in PPI guide rollers result in low maintenance requirements, reducing the need for frequent replacements and repairs. This contributes to lower operational costs and less downtime.
- High Load Capacity: PPI guide rollers are designed to handle high load capacities, making them suitable for a wide range of industrial applications, from light-duty packaging lines to heavy-duty mining operations.
- Versatile Application: Whether for troughing, return, or flat belt conveyors, PPI guide rollers are available in various sizes and configurations to meet the specific requirements of different conveyor types and applications. This versatility ensures that there is a PPI guide roller suitable for every conveyor design.
These key features of PPI guide rollers highlight their essential role in maintaining the efficiency, safety, and longevity of conveyor systems. By incorporating these advanced rollers into their operations, businesses can achieve improved conveyor performance, reduced maintenance costs, and enhanced operational reliability.
Types of PPI Guide Rollers
Precision Pulley & Idler (PPI) offers a comprehensive range of guide rollers designed to meet the diverse needs of conveyor systems across various industries. Each type of PPI guide roller is engineered with specific features to enhance conveyor belt performance and longevity. Here, we explore at least seven distinct types of PPI guide rollers, showcasing the versatility and innovation that PPI brings to conveyor system solutions.
- Conveyor Side Guide Rollers: Essential for maintaining the conveyor belt’s alignment, these rollers prevent lateral movements that could lead to belt damage or operational disruptions. PPI’s conveyor side guide rollers are engineered for durability and can be adjusted to accommodate various belt widths, ensuring the belt remains centered under all load conditions.
- Belt Guide Rollers: Tailored to engage directly with the belt, PPI’s belt guide rollers offer a precise guidance solution that minimizes friction and wear. Their design focuses on reducing belt misalignment, which is crucial for prolonging belt life and maintaining efficient conveyor operations. These rollers are versatile, suitable for both heavy-duty applications and environments where precision is key.
- Guide Roller Wheels: As integral components of the guide roller assembly, these wheels are designed for direct contact with the conveyor belt. Made from high-quality materials resistant to wear and abrasion, PPI guide roller wheels ensure consistent performance and durability. Their smooth surface and robust construction help in reducing belt wear, making them ideal for continuous operation.
- Guide Roller Assembly: Offering a complete solution for belt guidance, the guide roller assembly includes all necessary parts for immediate installation. PPI designs these assemblies with ease of maintenance in mind, allowing for quick adjustments and replacements without significant downtime. This comprehensive approach ensures that conveyor systems remain operational and efficient, with minimal intervention required.
- Troughing Guide Rollers: Specifically designed to support the belt in a troughed configuration, these rollers enhance the conveyor’s carrying capacity. PPI’s troughing guide rollers are critical for bulk material handling applications, ensuring that the belt forms the correct shape to carry large volumes of material efficiently. Their robust design helps in stabilizing the belt, reducing spillage and optimizing material flow.
- Return Guide Rollers: Positioned along the return path of the belt, these rollers play a vital role in maintaining belt alignment and cleanliness. By ensuring that the belt travels back in a centered and clean state, PPI’s return guide rollers extend the lifespan of the conveyor system. They are particularly important in environments where debris and material spillage can lead to operational issues.
- Impact Guide Rollers: These rollers are strategically placed at loading points where material is transferred onto the conveyor belt. PPI’s impact guide rollers are designed to absorb and distribute the energy from material impact, protecting both the belt and the conveyor structure from damage. Their presence is crucial in heavy-duty applications where the force of dropping materials could otherwise compromise the integrity of the conveyor system.
Each type of PPI guide roller is a reflection of the company’s commitment to providing high-quality, durable solutions for conveyor systems. By offering a wide selection of guide rollers, PPI ensures that businesses can find the perfect match for their specific conveyor needs, enhancing both performance and reliability.
PPI Guide Rollers Parts and Assembly
Precision Pulley & Idler (PPI) guide rollers are integral components of conveyor systems, designed to ensure optimal performance and longevity of conveyor belts. The assembly of PPI guide rollers and the selection of their parts are critical processes that require attention to detail to meet specific conveyor needs. Here, we delve deeper into the components that constitute PPI guide rollers, the assembly process, the pivotal role of guide roller wheels, and guidelines for selecting the right parts.
Guide Roller Assembly Process
The assembly process of PPI guide rollers is a detailed procedure that ensures each component functions cohesively to provide optimal support and guidance to conveyor belts. This process is critical for maintaining the efficiency and longevity of the conveyor system. Here’s a deeper look into the nuanced steps involved in the guide roller assembly process, highlighting its complexity and importance.
- Component Inspection: Before assembly begins, each component of the guide roller, including the wheels, bearings, shafts, and housing, undergoes a thorough inspection. This step ensures that all parts meet PPI’s stringent quality standards to guarantee performance and durability.
- Precision Engineering: The guide roller components are engineered with precision to ensure a perfect fit. This precision is crucial for the assembly process, as it affects the roller’s functionality and its ability to maintain the conveyor belt’s alignment.
- Bearing Installation: Bearings are carefully installed into the roller housing. This step requires precision to ensure that the bearings are seated correctly, allowing the roller to rotate smoothly without excessive play or friction that could affect the conveyor belt’s operation.
- Shaft Alignment: The shaft is aligned and inserted through the bearings. Proper alignment is crucial to prevent undue wear on the bearings and ensure smooth rotation of the roller. This step often involves specialized tools and equipment to achieve the required precision.
- Wheel Mounting: Guide roller wheels are mounted onto the shaft, positioned to interact effectively with the conveyor belt. The wheels’ placement is determined based on the specific application and operational requirements of the conveyor system.
- Securing Components: Once all parts are correctly positioned, they are securely fastened. This may involve tightening bolts and nuts, applying locking compounds, or using other fastening methods to ensure that the assembly remains intact under operational stresses.
- Final Inspection and Testing: The assembled guide roller undergoes a final inspection and testing phase. This includes rotational tests to check for smooth operation and alignment tests to ensure the roller will effectively guide the conveyor belt as intended.
This comprehensive assembly process of PPI guide rollers underscores the meticulous attention to detail required to produce a component that meets the high standards of durability, reliability, and performance expected in industrial conveyor systems. Through this process, PPI ensures that each guide roller is capable of providing the essential guidance and support needed for conveyor belts to operate efficiently and effectively.
Significance of Guide Roller Wheels in Overall Functionality
- Durability: Guide roller wheels are made from materials that offer high resistance to wear and abrasion, ensuring long-term durability even in harsh operating conditions.
- Reduced Friction: These wheels are designed to minimize friction between the roller and the conveyor belt, which is crucial for extending the life of the belt and reducing energy consumption.
- Load Distribution: Properly designed guide roller wheels help distribute the load evenly across the belt, preventing excessive wear in any one area and maintaining belt integrity.
- Alignment Correction: The wheels play a critical role in correcting misalignment of the conveyor belt, ensuring it runs smoothly and efficiently.
- Versatility: They come in various sizes and materials to match different conveyor belt types and operational requirements, offering versatility in application.
- Noise Reduction: High-quality guide roller wheels are engineered to operate quietly, reducing noise levels in the workplace.
- Maintenance Ease: The design of these wheels allows for easy maintenance and replacement, minimizing downtime and operational disruptions.
- Operational Efficiency: By ensuring the smooth operation of the conveyor belt, guide roller wheels contribute significantly to the overall efficiency of the conveyor system.
Selecting the Right Parts for Specific Conveyor Needs
- Belt Width and Speed: Choose parts that are compatible with the width and speed of your conveyor belt to ensure optimal performance and safety.
- Load Capacity: Consider the maximum load the conveyor will carry to select guide rollers that can withstand the operational demands.
- Material Compatibility: Ensure that the materials of the guide rollers and wheels are compatible with the type of products being conveyed to avoid contamination or damage.
- Environmental Conditions: Select materials that are suitable for the operating environment, including temperature extremes, moisture levels, and exposure to chemicals.
- Operational Requirements: Consider the specific operational requirements, such as the need for noise reduction or impact resistance, when selecting guide roller parts.
- Maintenance and Replacement: Opt for parts that offer ease of maintenance and replacement to reduce downtime and maintenance costs.
- Manufacturer Reputation: Choose PPI guide rollers and parts known for quality and reliability to ensure long-term performance and value.
- Technical Support: Ensure that the manufacturer provides comprehensive technical support for the selection, installation, and maintenance of guide rollers and parts.
By understanding the components and assembly process of PPI guide rollers, as well as the critical role of guide roller wheels and the criteria for selecting the right parts, operators can enhance the functionality and longevity of their conveyor systems. PPI’s commitment to quality and innovation ensures that their guide rollers meet the highest standards of performance and reliability.
Applications of PPI Guide Rollers
PPI guide rollers are pivotal components in a wide array of industrial applications, where their role in maintaining conveyor belt alignment directly impacts productivity, safety, and operational efficiency. These rollers are designed to meet the rigorous demands of various sectors, demonstrating the versatility and reliability of PPI’s engineering. Here, we explore at least eight critical applications of PPI guide rollers across different industries.
- Aggregate and Sand Production: In the harsh environments of aggregate and sand production, PPI guide rollers ensure the conveyor belts transport materials efficiently without misalignment, which could lead to significant downtime and maintenance issues.
- Parcel/Warehousing/Distribution/Baggage: The logistics and warehousing sector relies on PPI guide rollers to keep conveyor belts aligned, ensuring smooth and uninterrupted flow of parcels, baggage, and goods. This is crucial for maintaining tight delivery schedules and operational efficiency.
- Mining and Mineral Processing: The mining industry demands robust and reliable conveyor solutions. PPI guide rollers play a critical role in mineral processing and mining operations, where they withstand heavy loads and abrasive materials, ensuring continuous operation and minimizing belt wear.
- Food Processing: In food processing, cleanliness and precision are paramount. PPI guide rollers are designed to meet these requirements, providing reliable belt guidance while adhering to strict hygiene standards.
- Forestry and Lumber: Conveying wood products and lumber requires rollers that can handle heavy loads and resist wear. PPI guide rollers are engineered to operate in these challenging conditions, ensuring the efficient transport of forestry products.
- Recycling and Waste Management: In recycling plants, conveyor systems are essential for sorting and processing materials. PPI guide rollers ensure these belts run smoothly, reducing the risk of jams and disruptions in waste management operations.
- Manufacturing and Assembly Lines: Manufacturing facilities utilize conveyor systems extensively for assembly lines. PPI guide rollers contribute to the precision and efficiency of these systems, ensuring products move seamlessly through various stages of assembly and inspection.
- Chemical Processing: The chemical industry requires conveyor systems that can withstand corrosive substances and extreme conditions. PPI guide rollers are built to endure these environments, providing reliable service and maintaining belt alignment in the process.
- Agriculture and Grain Handling: In the agriculture sector, especially in grain handling, conveyors play a vital role in moving bulk materials. PPI guide rollers ensure these materials are transported efficiently from storage to processing facilities, maintaining the integrity of the conveyor system.
- Construction Materials Handling: Conveying construction materials such as cement, bricks, and tiles requires durable and efficient conveyor systems. PPI guide rollers are integral to these operations, ensuring that materials are moved safely and effectively to their destinations.
These applications highlight the broad adaptability and reliability of PPI guide rollers across various industries. By ensuring conveyor belt alignment, reducing maintenance needs, and enhancing operational efficiency, PPI guide rollers are essential for businesses looking to optimize their conveyor systems and maintain a competitive edge in their respective markets.
How to Choose the Right PPI Guide Rollers
Selecting the appropriate PPI guide roller for your conveyor system is crucial for ensuring optimal performance, longevity, and safety. The right guide roller not only maintains the conveyor belt’s alignment but also contributes to the system’s overall efficiency and reliability. Here are key considerations to guide you in choosing the right PPI guide roller, incorporating various conveyor belt roller types and addressing specific needs of the conveyor system.
Conveyor Belt Roller Types
The selection of the right type of conveyor belt roller is pivotal in designing an efficient, reliable, and long-lasting conveyor system. Each roller type serves a specific function and is crucial in maintaining the conveyor belt’s alignment, reducing wear, and optimizing material handling. PPI guide rollers, known for their quality and durability, are designed to work seamlessly with various conveyor belt roller types. Understanding the different roller types and their applications is the first step in ensuring your conveyor system operates at peak efficiency.
- Troughing Rollers: Ideal for bulk material handling, troughing rollers help form the belt into a trough shape, increasing its carrying capacity. Select PPI guide rollers that complement these rollers by ensuring the belt remains centered in the trough.
- impact rollers: Placed at loading points, impact rollers absorb the shock and impact of material falling onto the belt. Choose PPI guide rollers that can withstand adjacent vibrations and help keep the belt aligned under dynamic loads.
- Return Rollers: These rollers support the return side of the belt. Opt for PPI guide rollers that ensure the return path is as aligned and efficient as the carrying side, preventing belt sag and misalignment.
- Flat Belt Rollers: For systems utilizing flat belts, select PPI guide rollers designed to maintain flat belt alignment, especially in longer conveyor systems where lateral movement is more likely.
- Self-Aligning Rollers: These rollers automatically adjust the belt’s position to keep it aligned. Pairing them with PPI guide rollers designed for self-aligning action can enhance the conveyor’s efficiency and reduce maintenance needs.
- Specialty Rollers: For conveyors with specific applications (e.g., high-temperature environments, corrosive materials handling), choose PPI guide rollers that are designed to work in tandem with specialty rollers, ensuring compatibility and performance under unique conditions.
Specific Needs of the Conveyor
Choosing the appropriate PPI guide roller requires a thorough understanding of the specific needs of your conveyor system. Factors such as the conveyor belt’s width, load capacity, operational speed, and the nature of the materials being conveyed all play a significant role in selecting the right guide roller. Additionally, environmental conditions, operational requirements, and maintenance considerations must be taken into account to ensure the conveyor system is not only efficient but also safe and cost-effective over its lifespan. By addressing these specific needs, you can select PPI guide rollers that enhance the performance and reliability of your conveyor system.
- Belt Width and Thickness: Ensure the PPI guide rollers are compatible with the belt’s width and thickness, providing adequate support and guidance without causing undue wear.
- Load Capacity: Consider the maximum load the conveyor will handle. The selected PPI guide rollers must be robust enough to support the load without compromising the belt’s alignment.
- Speed of the Conveyor: High-speed conveyors require guide rollers with bearings that can handle the increased operational demands, ensuring smooth and efficient belt movement.
- Material Being Conveyed: The nature of the materials (e.g., abrasive, corrosive, sticky) can significantly affect roller choice. PPI offers guide rollers with materials and coatings suited to different conveying materials.
- Environmental Conditions: For conveyors operating in harsh environments (e.g., extreme temperatures, wet conditions), select PPI guide rollers designed to withstand these conditions without degradation.
- Operational Requirements: Consider any specific operational requirements, such as the need for noise reduction or vibration damping. PPI provides guide rollers that address these needs, enhancing workplace safety and comfort.
- Maintenance and Accessibility: Choose guide rollers that facilitate easy maintenance and replacement, considering the conveyor system’s accessibility and operational downtime constraints.
- Regulatory and Safety Standards: Ensure the selected PPI guide rollers meet industry-specific regulatory and safety standards, contributing to a safer and compliant operation.
- Cost-Effectiveness: While initial cost is a consideration, focus on the total cost of ownership, including maintenance, replacement, and operational efficiency. PPI guide rollers, known for their durability and reliability, can offer long-term cost savings.
By carefully considering these points and selecting the appropriate PPI guide rollers, you can ensure that your conveyor system operates smoothly, efficiently, and safely, meeting the specific demands of your application.
PPI Idlers and Guide Rollers Catalog
Accessing the PPI Idlers and Guide Rollers Catalog is a critical step for professionals seeking to enhance their conveyor systems with high-quality components. This catalog is a comprehensive resource, offering detailed information on a wide range of guide rollers and idler products designed to meet various operational needs. Here’s how to access and utilize the PPI Idlers Catalog effectively, ensuring you find the best conveyor solutions for your specific requirements.
Accessing the PPI Idlers Catalog
Navigating through the extensive range of conveyor solutions begins with accessing the PPI Idlers and Guide Rollers Catalog. This essential resource is your gateway to understanding and selecting from the premium range of PPI products, each designed to enhance conveyor system performance. Whether you’re upgrading an existing system or designing a new one, the catalog offers detailed insights into the comprehensive lineup of PPI guide rollers and idlers. Here’s how to access this invaluable tool, ensuring you have the latest information at your fingertips to make informed decisions about your conveyor system components.
- Visit the Official PPI Website: The PPI Idlers and Guide Rollers Catalog is readily available on the Precision Pulley & Idler (PPI) official website. This digital catalog is updated regularly with the latest products and specifications.
- Contact PPI Directly: For those who prefer personalized assistance, contacting PPI directly via phone or email can provide access to the catalog and additional support from their customer service team.
- Download the PDF Version: Often, the catalog is available for download in PDF format, allowing for easy access and reference offline.
- Request a Printed Copy: For users who prefer a tangible reference, requesting a printed copy of the catalog can be beneficial. This option is particularly useful for workshops and on-site consultations.
- Subscribe to PPI Updates: Subscribing to PPI’s newsletter or update service can provide immediate notifications when the new catalog editions are released or when new products are added.
- Attend PPI Webinars and Training Sessions: PPI often showcases their idlers and guide rollers during webinars and training sessions, providing a practical overview of their catalog offerings.
- Use the PPI Mobile App: If available, using the PPI mobile app can offer an interactive way to browse the catalog and access product information on the go.
Tips on Using the Catalog to Find the Best Conveyor Solutions
Once you have the PPI Idlers and Guide Rollers Catalog in hand, the next step is to navigate its contents effectively to find the best solutions for your conveyor system. This catalog is not just a list of products; it’s a comprehensive guide designed to assist you in selecting the most suitable components that meet your specific operational needs. With a variety of options available, it’s important to approach the catalog with a strategic mindset. Here are some tips to help you utilize the catalog efficiently, ensuring you find the ideal PPI guide rollers and idlers that will contribute to the optimal performance and longevity of your conveyor system.
- Identify Your Conveyor’s Specifications: Before diving into the catalog, clearly understand your conveyor system’s specifications, including belt width, speed, load capacity, and operational environment.
- Utilize the Search and Filter Functions: Make use of any search and filter functions within the digital catalog to narrow down the product listings to those that match your specific needs.
- Compare Products: The catalog typically provides detailed comparisons between different guide rollers and idlers, helping you understand the advantages of each option.
- Check for Compatibility: Ensure that the guide rollers or idlers you’re interested in are compatible with your existing conveyor system to avoid costly modifications.
- Review Technical Specifications: Pay close attention to the technical specifications of each product, including material composition, load capacity, and recommended applications.
- Consider Environmental Conditions: Select products that are designed to withstand the environmental conditions of your operation, whether it involves exposure to chemicals, extreme temperatures, or moisture.
- Look for Customization Options: Some conveyor applications may require customized solutions. Check the catalog for information on how PPI can tailor their products to meet unique requirements.
- Contact PPI for Advice: If you’re unsure about the best solution for your conveyor system, don’t hesitate to contact PPI for expert advice. Their team can help you navigate the catalog and make informed decisions based on your specific needs.
By following these guidelines and utilizing the PPI Idlers and Guide Rollers Catalog, you can ensure that you select the most appropriate and effective components for your conveyor system, enhancing its efficiency, reliability, and longevity.
FAQs about PPI Guide Rollers
A guide roller is an essential component of conveyor systems, designed to ensure the conveyor belt remains centered and aligned during operation. These rollers prevent the belt from drifting off its intended path, which could lead to uneven wear, damage to the belt, and potential operational disruptions. Guide rollers come in various designs and sizes, tailored to specific types of conveyor systems and operational requirements. They are strategically placed along the conveyor frame and can be adjusted to maintain optimal belt tension and alignment. The effectiveness of guide rollers in maintaining belt alignment is crucial for the longevity of the conveyor belt and the efficiency of the conveyor system as a whole. By minimizing belt misalignment, guide rollers play a key role in reducing maintenance needs, enhancing operational efficiency, and preventing downtime.
The standard size of conveyor rollers can vary widely depending on the application, the type of material being conveyed, and the specific requirements of the conveyor system. However, common diameters for conveyor rollers range from about 1.5 inches (38 mm) to 8 inches (203 mm), with lengths that can extend up to several feet to accommodate the width of the conveyor belt. The size selection is based on the load the roller must support, the speed of the conveyor, and the environmental conditions in which the system operates. Manufacturers often provide a range of standard sizes but can also customize rollers to meet specific operational needs. It’s important to consult with roller manufacturers or refer to their catalogs to select the appropriate size for your conveyor system, ensuring optimal performance and longevity.
Conveyor idlers, which support the conveyor belt and the material being transported along the belt, come in various standard sizes designed to fit different conveyor widths and load requirements. The standard diameters for conveyor idlers typically range from 3 inches (76 mm) to 6 inches (152 mm), with the length varying according to the width of the conveyor belt they are supporting. These sizes are often categorized according to the Conveyor Equipment Manufacturers Association (CEMA) standards, with CEMA B, C, D, and E being common designations that indicate both the diameter and the load capacity of the idlers. The choice of idler size is critical for ensuring the conveyor operates efficiently, with minimal wear and tear on the belt and the idlers themselves. Selecting the correct idler size involves considering the belt width, the amount and type of material being conveyed, and the operational speed of the conveyor.
The diameter of idler rollers can vary significantly based on the application, the load they are designed to support, and the specific requirements of the conveyor system. Standard diameters for idler rollers typically fall within the range of 3 inches (76 mm) to 6 inches (152 mm), aligning with the sizes set forth by CEMA standards for conveyor idlers. These diameters are selected to provide the best combination of support for the conveyor belt and the materials being transported, while also ensuring durability and efficiency of the conveyor system. Larger diameters are generally used for heavier loads or higher impact applications, as they distribute the weight more evenly and reduce the wear on the conveyor belt. When selecting idler rollers, it’s important to consider the operational conditions, including the belt speed, load type, and environmental factors, to choose the appropriate diameter that ensures reliable operation and minimizes maintenance requirements.
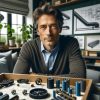
Jordan Smith, a seasoned professional with over 20 years of experience in the conveyor system industry. Jordan’s expertise lies in providing comprehensive solutions for conveyor rollers, belts, and accessories, catering to a wide range of industrial needs. From initial design and configuration to installation and meticulous troubleshooting, Jordan is adept at handling all aspects of conveyor system management. Whether you’re looking to upgrade your production line with efficient conveyor belts, require custom conveyor rollers for specific operations, or need expert advice on selecting the right conveyor accessories for your facility, Jordan is your reliable consultant. For any inquiries or assistance with conveyor system optimization, Jordan is available to share his wealth of knowledge and experience. Feel free to reach out at any time for professional guidance on all matters related to conveyor rollers, belts, and accessories.