Heavy Duty Guide Rollers: Industrial Machinery Efficiency
In the vast and intricate world of industrial applications, guide rollers stand as unsung heroes, playing a crucial role in the seamless operation of machinery. These components ensure the smooth and efficient movement of materials, products, and equipment across various sectors, including manufacturing, logistics, and construction. However, not all environments are created equal; some demand a level of durability and performance that standard solutions cannot provide. Enter heavy duty guide rollers, engineered to withstand the rigors of the most demanding environments. These robust counterparts are designed to offer unparalleled support and endurance, ensuring that even under extreme conditions, productivity remains unhindered. The focus on heavy duty guide rollers is not just about selecting a component; it’s about committing to operational excellence and reliability in scenarios where the margin for error is minimal.
What are Heavy Duty Guide Rollers
Guide rollers, pivotal components in numerous industrial applications, facilitate the movement and management of heavy loads with precision and ease. These rollers, mounted on bearings, allow for smooth linear or rotary motion of objects along a defined path. They’re extensively used across various sectors, including manufacturing, logistics, and material handling, playing a crucial role in optimizing operational efficiency and safety.
Defining Guide Rollers
Guide rollers are engineered components designed to direct, support, and position moving parts, assemblies, or materials. They’re crafted from robust materials to withstand significant wear and stress, ensuring longevity and consistent performance. The selection of materials, ranging from hardened steel to polymers, is dictated by the application’s specific needs, including load capacity, speed requirements, and environmental conditions.
Primary Functions of Guide Rollers in Industrial Settings
Guide rollers serve six primary functions in industrial environments, each vital to the seamless operation of machinery and conveyance systems:
- Load Support: They bear the weight of moving objects, reducing friction and facilitating smoother transitions across surfaces.
- Positioning Accuracy: By guiding parts along predetermined paths, they ensure precise alignment and placement, critical in automation and assembly processes.
- Speed Regulation: Guide rollers help maintain consistent movement speeds, preventing slippage and enhancing control over material handling.
- Vibration Reduction: They absorb shocks and minimize vibrations, protecting delicate components and ensuring stable operations.
- Directional Control: Rollers direct materials or components along specific routes, essential for complex machinery layouts and efficient workflow management.
- Wear Minimization: By evenly distributing loads and reducing direct contact between moving parts, they extend the lifespan of machinery components.
Standard vs. Heavy Duty Guide Rollers
While standard guide rollers are suitable for a wide range of applications, heavy-duty guide rollers are engineered for more demanding environments where higher loads, extreme temperatures, or corrosive conditions are prevalent. Heavy duty guide rollers are distinguished by their enhanced durability, greater load-bearing capacity, and resistance to wear and environmental factors. These rollers are often manufactured from superior materials such as high-grade steel or reinforced polymers, and may include specialized coatings or treatments to further increase their resilience.
Heavy duty guide rollers are integral to industries where equipment must endure harsh conditions while maintaining high performance and reliability. Their robust construction ensures they can support heavier weights, resist deformation, and offer extended service life, making them an indispensable choice for heavy machinery, mining operations, and large-scale manufacturing processes.
Guide rollers, particularly heavy-duty variants, are essential for the efficient and reliable operation of industrial machinery. Their ability to support high loads, ensure precision, and withstand harsh conditions makes them a cornerstone of modern industrial applications. Understanding the nuances between standard and heavy-duty guide rollers allows for informed decision-making, ensuring the right components are chosen for specific industrial needs.
Specialized Types of Heavy Duty Guide Rollers
In the domain of industrial applications, guide rollers play a pivotal role in ensuring the smooth and efficient operation of machinery. Among these, heavy duty guide rollers are specifically designed to handle the rigors of high-load capacities, offering robust performance in challenging environments. This segment delves into the specialized types of guide rollers, focusing on their unique features and applications.
Small Nylon Guide Wheels
Small nylon guide wheels are an integral component of the heavy duty guide rollers category. They are renowned for their lightweight yet durable properties, making them an ideal choice for applications that demand both resilience and minimal weight impact. The primary advantage of using small nylon guide wheels in heavy-duty applications lies in their size range and weight capacity. These wheels can support significantly heavy loads while maintaining a compact footprint, ensuring they can be integrated into various machinery without necessitating considerable space. Their nylon composition also offers a high resistance to wear and abrasion, which is crucial for maintaining performance in environments where durability is paramount.
Guide Roller Assembly
A guide roller assembly constitutes the comprehensive setup of heavy duty guide rollers, encompassing various components such as the rollers themselves, bearings, shafts, and mounts. The assembly is designed to ensure that each part works in harmony to provide optimal performance under heavy loads. The importance of durability in this context cannot be overstated, as each component must withstand the stresses and strains of heavy-duty operations without succumbing to failure. Additionally, the design of the guide roller assembly is crucial for achieving the desired level of precision and efficiency. Properly engineered assemblies minimize friction and wear, extend the lifespan of the machinery, and reduce the need for frequent maintenance.
Roller Guide Rails
Roller guide rails serve as the foundation upon which heavy duty guide rollers operate. Their primary function is to support and guide the roller assemblies, ensuring that movement is smooth, controlled, and aligned with the operational requirements. Roller guide rails are critical for optimal performance, as they directly influence the accuracy, speed, and overall efficiency of the machinery. They must be precisely manufactured and installed to prevent misalignment, which could otherwise lead to increased wear, energy consumption, and potential operational failures. By providing a stable and accurate guide path, roller guide rails enhance the functionality of heavy-duty guide rollers, ensuring that they can deliver their full performance potential in demanding industrial applications.
Specialized types of guide rollers, particularly those designed for heavy-duty applications, are indispensable in the industrial sector. Their ability to handle high loads with precision and durability makes them a key component in the efficient and reliable operation of machinery. Whether it’s through the use of small nylon guide wheels, the robust design of guide roller assemblies, or the precision of roller guide rails, these components collectively ensure that heavy-duty guide rollers can meet the rigorous demands of industrial use.
Components of Heavy Duty Guide Rollers Systems
The efficiency and reliability of heavy-duty guide roller systems are pivotal in industrial applications, where they bear the brunt of moving heavy loads under demanding conditions. These systems comprise various components, each playing a crucial role in ensuring smooth operation, durability, and precision. This section delves into the integral parts of heavy-duty guide roller systems, focusing on the guide roller assembly and roller guide rails, highlighting their functions, components, and some specific products used in industrial settings.
Guide Roller Assembly
The guide roller assembly is a cornerstone of heavy-duty guide roller systems, consisting of multiple components designed to work in unison to support, guide, and facilitate the movement of heavy loads.
Components
- Shaft: Acts as the core structure, providing the axis of rotation for the roller.
- Roller Body: The main contact surface that interacts with the moving load, usually made from materials like steel, nylon, or polyurethane.
- Bearings: Facilitate smooth rotation of the roller around the shaft, minimizing friction and wear.
- Seals: Protect the bearings from dust, debris, and moisture, ensuring longevity and reliability.
- End Caps/Locks: Secure the roller on the shaft and maintain the assembly’s structural integrity.
- Mounting Brackets: Allow for the secure attachment of the roller assembly to the framework or machinery.
- Lubrication System: Ensures the bearings and moving parts remain lubricated, reducing friction and wear.
Specific Products
- Heavy-Duty Gate Rollers: Designed for large industrial gates, these rollers can come in dimensions such as 4 inches in diameter by 2 inches in width, made from high-grade steel or reinforced nylon for durability.
- Track Rollers: Utilized in conveyor systems and heavy equipment, featuring diameters up to 5 inches, crafted from polyurethane for wear resistance.
- Load Rollers: Essential for material handling equipment, with dimensions like 6 inches by 3 inches, often made from rubber for shock absorption.
- Guide Wheels: For precision machinery, available in smaller sizes such as 2 inches in diameter, made from nylon or polyurethane for a balance of strength and flexibility.
- Support Rollers: Used in heavy-duty machinery and conveyors, these can be up to 8 inches in diameter, made from hardened steel for maximum load-bearing capacity.
Roller Guide Rails
Roller guide rails play an indispensable role in enhancing the functionality and performance of heavy-duty guide rollers, serving as the foundational track upon which rollers move.
Role and Functionality
- Precision Alignment: Ensure the accurate and straight movement of rollers, essential for the precise handling and positioning of loads.
- Load Distribution: Provide a stable base that supports the distribution of heavy loads across multiple rollers, reducing stress and wear.
- Reduced Friction: Minimize resistance between the rollers and the rail, facilitating smoother movement and increasing efficiency.
- Enhanced Stability: Stabilize the roller assembly against lateral and vertical forces, preventing tipping or misalignment under heavy loads.
- Increased Lifespan: By ensuring proper alignment and reducing uneven wear, guide rails extend the operational life of the entire system.
- Versatility: Accommodate various roller types and sizes, offering flexibility in system design and application.
- Customization: Can be tailored in length, material, and design to meet specific industrial requirements.
- Protective Features: Some guide rails are equipped with covers or seals to protect against dust, debris, and corrosive elements, maintaining system integrity.
The components of heavy-duty guide roller systems, from the intricately designed assemblies to the robust guide rails, ensure that industrial operations can move heavy loads efficiently, accurately, and reliably. Their integration forms the backbone of countless systems, facilitating the smooth operation of machinery and the effective management of materials across a spectrum of industrial applications.
Heavy Duty Applications of Heavy Duty Guide Rollers
Heavy duty guide rollers are integral to the operation and efficiency of various industrial systems, especially in applications requiring the movement and management of heavy loads. Their robust construction and design enable them to withstand the rigors of heavy-duty applications, from industrial castors to trolley wheels, ensuring reliability, durability, and performance. This section explores the critical role of heavy-duty guide rollers in these applications, emphasizing their load capacities and suitability for different environments and operational demands.
Heavy Duty Industrial Castors
The integration of heavy duty guide rollers in industrial castors marks a significant advancement in the mobility and flexibility of heavy machinery and equipment. These castors are designed to facilitate easy and efficient movement of large loads across factory floors, warehouses, and other industrial environments.
Integration and Load Capacity
- Load Capacity: Heavy-duty industrial castors equipped with heavy-duty guide rollers can support loads ranging from a few hundred to several thousand pounds, depending on the design and materials used.
- Environments: These castors are engineered for resilience under harsh conditions, including exposure to chemicals, high temperatures, and heavy impact. They are ideal for use in manufacturing plants, automotive assembly lines, and construction sites, where moving heavy equipment or materials is a routine requirement.
Heavy Duty Trolley Wheels
The significance of heavy-duty trolley wheels in the realms of material handling and logistics cannot be overstated. They are pivotal in ensuring the smooth, efficient, and safe transport of goods, particularly in heavy load scenarios.
Significance in Material Handling and Logistics
- Load Management: Heavy-duty trolley wheels are essential for handling and distributing heavy loads evenly, reducing the risk of overloading and ensuring stability during movement.
- Operational Efficiency: They contribute to the seamless flow of operations, minimizing downtime and enhancing productivity by enabling the quick and safe relocation of heavy items.
- Safety: By providing secure and stable movement, these wheels help to prevent accidents and damage to materials or equipment.
- Durability: Designed to withstand the wear and tear of heavy use, they ensure a longer service life and reduce maintenance costs.
- Versatility: Suitable for various applications, from industrial transportation to commercial logistics, adapting to different floor conditions and load types.
- Precision Movement: Enhanced control and maneuverability, crucial in tight spaces or when precise placement of heavy loads is required.
- Load Capacity: Similar to heavy-duty castors, these wheels are designed to support substantial weights, often exceeding thousands of pounds, catering to the demands of heavy machinery and equipment.
- Material Compatibility: Manufactured from materials like steel, nylon, and polyurethane, they offer options for different operational needs, including resistance to wear, impact, and environmental factors.
- Customization: The ability to customize wheel size, material, and bearing type allows for tailored solutions that match specific load-bearing and environmental requirements.
The heavy duty guide rollers utilized in industrial castors and trolley wheels are foundational to managing and maneuvering heavy loads across a spectrum of industrial and logistical settings. Their robust design, coupled with high load capacity and adaptability to harsh environments, ensures they play a crucial role in maintaining operational efficiency, safety, and reliability in heavy-duty applications.
Choosing the Right Heavy Duty Guide Roller
Selecting the appropriate heavy duty guide rollers is pivotal for ensuring operational efficiency, safety, and longevity in industrial applications. Given the diverse range of environments and operational demands across industries, making the right choice involves careful consideration of various factors and understanding the specific requirements of each application. Here are twelve pieces of guidance on selecting the right type of heavy-duty guide roller, followed by eight critical factors to consider during the selection process.
Guidance on Selection
- Understand Application Requirements: Begin by thoroughly assessing the operational demands, including the nature of the loads, movement patterns, and the frequency of operation.
- Identify Load Capacity Needs: Choose rollers that can support the maximum load expected, plus an additional margin for safety and unforeseen operational demands.
- Consider the Operating Environment: Evaluate environmental conditions such as exposure to chemicals, temperature extremes, and moisture, which can influence the choice of roller materials and designs.
- Evaluate Speed Requirements: High-speed applications may require rollers designed for minimal friction and high rotational speeds.
- Assess Impact and Vibration Levels: For applications subject to impacts and vibrations, select rollers with materials and designs that offer damping and shock absorption.
- Determine Material Suitability: Match the roller material with the environmental conditions and the materials of the tracks or surfaces they will interact with.
- Factor in Maintenance Needs: Consider ease of maintenance and the availability of replacement parts. Rollers with sealed bearings, for example, may offer longer service intervals.
- Review Customization Options: Some applications may benefit from custom-designed rollers to meet unique operational requirements perfectly.
- Consider Longevity and Wear Resistance: Opt for materials and designs known for durability and resistance to wear under the expected operating conditions.
- Analyze Cost-Effectiveness: While initial cost is a consideration, focus on the total cost of ownership, including maintenance, downtime, and replacement needs.
- Consult with Manufacturers: Leverage the expertise of roller manufacturers to help in selecting the best roller type for your application.
- Sample Testing: If possible, conduct tests with different roller types under actual operating conditions to directly assess performance and suitability.
Factors to Consider
- Load Capacity: Essential to ensure the roller can withstand the weight and stresses of the application without failure.
- Material: The construction material of the roller impacts its strength, durability, and compatibility with the operational environment (e.g., steel, nylon, polyurethane).
- Environmental Conditions: Exposure to harsh chemicals, extreme temperatures, and moisture can significantly affect roller performance and lifespan.
- Speed Requirements: The roller design must accommodate the operational speed of the system, affecting bearing choice and lubrication needs.
- Impact and Vibration: Rollers should be chosen for their ability to absorb shocks and dampen vibrations, maintaining stability and reducing wear.
- Maintenance and Accessibility: Consideration for ease of maintenance and replacement can prevent prolonged downtime and operational disruptions.
- Customization Needs: Custom designs may be necessary for unique applications, requiring specific roller dimensions, materials, or configurations.
- Total Cost of Ownership: Beyond the initial purchase price, consider longevity, maintenance costs, and the potential for operational downtime.
By meticulously considering these guidelines and factors, you can make an informed decision when selecting heavy duty guide rollers for your specific industrial applications. This approach ensures the chosen rollers not only meet the immediate operational requirements but also offer reliability, durability, and cost-effectiveness over the long term.
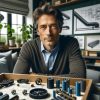
Jordan Smith, a seasoned professional with over 20 years of experience in the conveyor system industry. Jordan’s expertise lies in providing comprehensive solutions for conveyor rollers, belts, and accessories, catering to a wide range of industrial needs. From initial design and configuration to installation and meticulous troubleshooting, Jordan is adept at handling all aspects of conveyor system management. Whether you’re looking to upgrade your production line with efficient conveyor belts, require custom conveyor rollers for specific operations, or need expert advice on selecting the right conveyor accessories for your facility, Jordan is your reliable consultant. For any inquiries or assistance with conveyor system optimization, Jordan is available to share his wealth of knowledge and experience. Feel free to reach out at any time for professional guidance on all matters related to conveyor rollers, belts, and accessories.