Longest Conveyor Belt in Australia: Location and Impact
When exploring the longest conveyor belt in Australia, one discovers a remarkable feat of engineering that significantly impacts the mining industry. This conveyor belt is located in Western Australia and is primarily used to transport iron ore from mines to ports. The longest conveyor belt in Australia spans hundreds of kilometers, efficiently moving vast quantities of materials to support the country’s mining operations. Its purpose is to streamline the transportation process, reducing the reliance on trucks and minimizing environmental impact. Understanding the significance of the longest conveyor belt in Australia reveals its critical role in enhancing productivity and sustainability within the mining sector.
Longest Conveyor Belt in Australia
The Role of Conveyor Belts in Global Mining Operations
Conveyor belts have revolutionized the mining industry by significantly enhancing efficiency and productivity. Among these engineering marvels, the longest conveyor belt in Australia stands out as a testament to the advancements in mining technology. Located in Western Australia, this conveyor belt is a crucial component of the mining operations at the BHP Billiton Iron Ore mining area in the Pilbara region. Stretching approximately 20 kilometers, it plays a vital role in the transportation of iron ore, contributing immensely to the mining industry’s efficiency and productivity.
Enhancing Efficiency in Mining Operations
The primary advantage of long conveyor belts, such as the longest conveyor belt in Australia, is their ability to transport large quantities of materials over long distances efficiently. In the mining industry, where large volumes of raw materials need to be moved from extraction sites to processing plants, conveyor belts offer a cost-effective and time-saving solution. The longest conveyor belt in Australia, for instance, reduces the reliance on trucks and rail transport, which are not only more expensive but also less environmentally friendly.
Conveyor belts minimize the need for manual handling of materials, thereby reducing labor costs and the risk of workplace injuries. By automating the transportation process, conveyor belts ensure a continuous flow of materials, leading to uninterrupted mining operations. This continuous operation is critical in maximizing the output of mining sites, as any delay or disruption can lead to significant financial losses.
Productivity and Capacity
The capacity of a conveyor belt to move vast quantities of material is a significant factor in boosting productivity. The longest conveyor belt in Australia is designed to transport thousands of tons of iron ore per hour, ensuring that the mining operations can meet their production targets. This high capacity reduces the time required to transport materials from the mines to the processing plants, allowing for quicker turnaround times and increased overall productivity.
In addition to high capacity, the efficiency of conveyor belts in handling materials contributes to the optimization of the mining process. Conveyor belts can be customized to suit the specific needs of a mining operation, including the type of material being transported and the distance it needs to cover. This customization ensures that the conveyor belt operates at optimal efficiency, reducing energy consumption and operational costs.
Technological Advancements
Technological advancements have played a crucial role in the development of long conveyor belts, including the longest conveyor belt in Australia. Modern conveyor belts are equipped with advanced monitoring and control systems that ensure smooth and efficient operation. These systems include sensors that monitor the belt’s speed, tension, and alignment, as well as automated control systems that adjust the belt’s operation in real-time to maintain optimal performance.
Predictive maintenance technologies are also integrated into modern conveyor belts, allowing for early detection of potential issues and timely maintenance. This proactive approach minimizes downtime and extends the lifespan of the conveyor belt, ensuring that it continues to operate efficiently over the long term. The integration of these advanced technologies has made conveyor belts more reliable and cost-effective, further enhancing their role in global mining operations.
Environmental Impact
The environmental benefits of conveyor belts cannot be overlooked, especially in the context of mining operations. By reducing the reliance on trucks and rail transport, conveyor belts help to lower greenhouse gas emissions and minimize the environmental footprint of mining activities. The longest conveyor belt in Australia, for example, contributes to a reduction in fuel consumption and emissions, making the mining operations more sustainable.
In addition to reducing emissions, conveyor belts also help to minimize land disturbance and habitat destruction. Traditional transportation methods such as trucks and railways require extensive infrastructure and can have significant impacts on the surrounding environment. Conveyor belts, on the other hand, can be designed to follow the natural contours of the landscape, reducing the need for extensive earthworks and preserving the natural environment.
Economic Benefits
The economic benefits of long conveyor belts extend beyond the mining operations themselves. By enhancing the efficiency and productivity of mining activities, conveyor belts contribute to the overall economic growth of mining regions. The increased output and reduced operational costs associated with conveyor belts lead to higher profitability for mining companies, which in turn drives investment and development in the mining sector.
The longest conveyor belt in Australia, for instance, has had a positive impact on the economy of Western Australia. The mining industry is a major contributor to the region’s economy, and the efficiency gains achieved through the use of conveyor belts have helped to sustain and grow this vital industry. The economic benefits also extend to local communities, with increased employment opportunities and improved infrastructure resulting from the success of mining operations.
Future Prospects
The future of conveyor belts in the mining industry looks promising, with ongoing advancements in technology set to further enhance their efficiency and sustainability. Innovations in materials science, such as the development of more durable and lightweight materials, are expected to improve the performance and lifespan of conveyor belts. Advances in automation and control systems will continue to optimize the operation of conveyor belts, reducing energy consumption and operational costs.
The integration of renewable energy sources, such as solar and wind power, into the operation of conveyor belts is another exciting prospect. By harnessing clean energy, conveyor belts can further reduce their environmental impact and contribute to the sustainability of mining operations. The future of conveyor belts in the mining industry will be shaped by these technological and environmental advancements, ensuring that they continue to play a crucial role in global mining operations.
What is Longest Conveyor Belt in Australia
Economic and Environmental Benefits of Long Conveyor Belts
The longest conveyor belt in Australia, found at the Boddington Bauxite Mine in Western Australia, stands as a testament to the innovative engineering solutions that drive the mining industry. This conveyor belt, stretching approximately 31 kilometers (19 miles), plays a crucial role in the efficient transportation of materials from the mine to the processing facilities. Its implementation has brought about significant economic advantages and environmental benefits, making it a model for the mining and materials transportation industries.
Economic Advantages
The economic advantages of using long conveyor belts, such as the longest conveyor belt in Australia, are substantial. One of the most significant benefits is the reduction in transportation costs. Traditional methods of transporting mined materials, such as trucks or trains, can be expensive due to fuel costs, maintenance, and labor. In contrast, conveyor belts provide a continuous, automated means of transport, significantly reducing operational costs.
The use of conveyor belts also enhances productivity and efficiency. With the ability to transport large quantities of materials continuously, conveyor belts ensure a steady supply to processing plants, minimizing downtime and bottlenecks. This continuous flow of materials is crucial in maintaining the pace of operations, especially in large-scale mining projects. By reducing the reliance on intermittent and labor-intensive transport methods, conveyor belts streamline operations and contribute to higher output levels.
Furthermore, the initial investment in a long conveyor belt system, while substantial, often results in long-term cost savings. The maintenance and operational costs of conveyor belts are generally lower than those of heavy transport vehicles. Conveyor belts also have a longer lifespan, reducing the need for frequent replacements and the associated costs. The return on investment for a long conveyor belt system can be realized relatively quickly, making it a financially sound choice for mining companies.
Environmental Benefits
In addition to the economic advantages, the longest conveyor belt in Australia also brings significant environmental benefits. One of the primary environmental benefits is the reduction in greenhouse gas emissions. Traditional transportation methods, such as trucks and trains, rely heavily on fossil fuels, contributing to carbon emissions and air pollution. Conveyor belts, powered by electricity, produce significantly lower emissions, helping to reduce the environmental footprint of mining operations.
The use of conveyor belts also minimizes habitat disruption and land degradation. Traditional transport methods often require the construction of extensive road networks, which can disrupt local ecosystems and lead to soil erosion. Conveyor belts, on the other hand, require a narrower footprint and can be designed to follow the natural contours of the land, reducing the impact on the environment. This is particularly important in ecologically sensitive areas where preserving biodiversity is a priority.
Moreover, conveyor belts help to reduce noise pollution. The continuous operation of heavy transport vehicles can generate significant noise, affecting both wildlife and local communities. Conveyor belts operate more quietly, contributing to a reduction in noise pollution and improving the overall quality of life for nearby residents.
Operational Efficiency
The operational efficiency of long conveyor belts, such as the longest conveyor belt in Australia, is another critical factor contributing to their economic and environmental benefits. Conveyor belts provide a reliable and consistent means of transporting materials, reducing the risk of delays and interruptions that can occur with traditional transport methods. This consistency is essential for maintaining production schedules and meeting market demands.
Advanced monitoring and maintenance technologies further enhance the efficiency of conveyor belt systems. Sensors and automated systems can detect potential issues, such as belt misalignment or wear, before they lead to significant problems. This proactive approach to maintenance helps to minimize downtime and ensures the continuous operation of the conveyor belt system. The ability to quickly address and resolve issues also contributes to the longevity of the conveyor belt, providing further economic benefits.
Case Study: Boddington Bauxite Mine
The Boddington Bauxite Mine, home to the longest conveyor belt in Australia, provides a compelling case study of the economic and environmental benefits of long conveyor belts. The mine, located in Western Australia, is one of the largest bauxite mines in the world, producing millions of tons of bauxite each year. The conveyor belt system at Boddington is a critical component of the mine’s operations, enabling the efficient transport of bauxite from the mine to the processing plant.
The implementation of the conveyor belt system at Boddington has resulted in significant cost savings. The reduction in fuel and maintenance costs associated with traditional transport methods has contributed to lower operational expenses. Additionally, the continuous operation of the conveyor belt has enhanced productivity, allowing the mine to meet its production targets consistently.
From an environmental perspective, the conveyor belt system at Boddington has reduced greenhouse gas emissions and minimized the impact on local ecosystems. The narrow footprint of the conveyor belt has limited habitat disruption, and the reduced reliance on fossil fuels has helped to lower carbon emissions. The quieter operation of the conveyor belt has also reduced noise pollution, benefiting local wildlife and communities.
Future Prospects
The success of the longest conveyor belt in Australia highlights the potential for expanding the use of long conveyor belts in the mining and materials transportation industries. As technology advances, the efficiency and reliability of conveyor belt systems continue to improve, making them an increasingly attractive option for mining companies.
Future prospects for long conveyor belts include the integration of renewable energy sources, such as solar or wind power, to further reduce environmental impacts. Advances in materials science could also lead to the development of more durable and sustainable conveyor belts, extending their lifespan and reducing maintenance requirements.
Additionally, the use of smart technologies, such as the Internet of Things (IoT) and artificial intelligence (AI), can enhance the monitoring and management of conveyor belt systems. These technologies can provide real-time data on the condition and performance of the conveyor belt, enabling more efficient maintenance and operational decisions.
The Key of Longest Conveyor Belt in Australia
Technological Advancements in Conveyor Belt Systems
When exploring the technological marvels in the mining industry, the longest conveyor belt in Australia is a prime example of how advancements in engineering and technology have revolutionized material transport. Located in the Pilbara region of Western Australia, this belt is a crucial component of the mining operations at the BHP Billiton Iron Ore mining area. Stretching approximately 20 kilometers, it exemplifies the significant strides made in conveyor belt technology.
Advanced Materials and Durability
One of the key technological advancements in conveyor belt systems is the development of advanced materials that enhance durability and performance. The longest conveyor belt in Australia is constructed from high-strength, reinforced rubber and fabric materials designed to withstand the harsh conditions of the mining environment. These materials provide the necessary strength to handle the immense weight and continuous movement of large volumes of iron ore.
In addition to their strength, these materials are resistant to abrasion, reducing wear and tear over time. Special coatings are also applied to minimize friction and heat buildup, ensuring smooth and efficient operation. These innovations extend the lifespan of the conveyor belt, reducing the frequency of replacements and maintenance.
Automation and Control Systems
The integration of automation and control systems has significantly improved the efficiency and reliability of conveyor belt operations. The longest conveyor belt in Australia is equipped with sophisticated control systems that monitor its performance in real-time. Sensors embedded along the belt track various parameters such as speed, tension, alignment, and temperature.
These sensors provide continuous feedback to a central control system, which can adjust the belt’s operation to maintain optimal performance. For instance, if the belt becomes misaligned or if there is a sudden change in load, the control system can automatically make the necessary adjustments to prevent disruptions. This level of automation reduces the need for manual intervention, ensuring a more consistent and efficient operation.
Predictive Maintenance Technologies
Predictive maintenance technologies have also played a crucial role in enhancing the reliability of conveyor belt systems. By analyzing data collected from sensors, predictive maintenance algorithms can identify patterns and detect early signs of potential issues. This proactive approach allows for timely maintenance and repairs, minimizing downtime and preventing costly breakdowns.
The longest conveyor belt in Australia benefits from these technologies, which help maintain its continuous operation. Regular maintenance activities, guided by predictive insights, ensure that the belt remains in optimal condition, supporting the high productivity demands of the mining operations.
Environmental Considerations
Technological advancements in conveyor belt systems have also focused on reducing their environmental impact. Conveyor belts offer a more sustainable alternative to traditional transportation methods such as trucks and railways, which are associated with higher emissions and environmental disruption. The longest conveyor belt in Australia contributes to lower greenhouse gas emissions by minimizing the reliance on fuel-intensive transport options.
Furthermore, the design and construction of conveyor belts can be tailored to minimize their ecological footprint. For example, the belt can be routed to follow the natural contours of the landscape, reducing the need for extensive earthworks and preserving the natural environment. Dust suppression systems and noise reduction technologies are also employed to mitigate the impact on surrounding areas.
Global Applications and Innovations
The advancements seen in the longest conveyor belt in Australia are mirrored in other parts of the world, such as Africa and the United States. In Western Sahara, the world’s longest conveyor belt stretches 98 kilometers, transporting phosphate across the desert. This belt incorporates similar technological innovations, including advanced materials, automation, and predictive maintenance systems.
In the United States, conveyor belts are widely used in various industries, from mining to manufacturing. The integration of renewable energy sources, such as solar and wind power, is an emerging trend that enhances the sustainability of conveyor belt operations. By harnessing clean energy, these systems can further reduce their environmental impact and contribute to the goal of sustainable development.
Future Prospects
Looking ahead, the future of conveyor belt systems promises further advancements and innovations. Continued research and development in materials science will likely lead to the creation of even more durable and lightweight materials. Improvements in automation and artificial intelligence will enhance the efficiency and reliability of conveyor belt operations.
The integration of smart technologies, such as the Internet of Things (IoT), will enable more sophisticated monitoring and control systems. These technologies will provide deeper insights into the performance of conveyor belts, allowing for more precise adjustments and maintenance. Additionally, the focus on sustainability will drive the adoption of eco-friendly materials and renewable energy sources in conveyor belt design and operation.
How about Longest Conveyor Belt in Australia
Future Prospects for Conveyor Belt Technology
The longest conveyor belt in Australia, stretching across vast distances to connect mining operations with processing facilities, exemplifies the pinnacle of current conveyor belt technology. Located at the Boddington Bauxite Mine in Western Australia, this conveyor belt has revolutionized material transportation, demonstrating significant economic and environmental benefits. As we look to the future, it is essential to speculate on potential advancements in conveyor belt technology that could further enhance their efficiency and sustainability.
Innovations in Material Science
One of the most promising areas for future development in conveyor belt technology lies in material science. The traditional rubber belts, while durable, face challenges such as wear and tear, especially in harsh environments like those found in mining operations. Future conveyor belts might utilize advanced composite materials, offering superior resistance to abrasion, extreme temperatures, and chemical exposure.
Innovative materials such as high-performance polymers, carbon fiber composites, and even graphene could be integrated into conveyor belt designs. These materials not only offer enhanced durability but also reduce the overall weight of the belts, leading to lower energy consumption and increased operational efficiency. By reducing the frequency of maintenance and replacements, these advanced materials can significantly extend the lifespan of conveyor belts, providing both economic and environmental benefits.
Energy Efficiency and Renewable Integration
The energy consumption of conveyor belt systems is a critical consideration, especially for long-distance belts like the longest conveyor belt in Australia. Future developments are likely to focus on improving the energy efficiency of these systems. One potential advancement is the integration of energy-efficient motors and drive systems, which can reduce power consumption while maintaining high performance.
Moreover, the incorporation of renewable energy sources into conveyor belt operations presents a significant opportunity for sustainability. Solar panels and wind turbines could be installed along the length of conveyor belts to harness natural energy sources, providing a green and sustainable power supply. This approach not only reduces the carbon footprint of mining operations but also offers a reliable and cost-effective energy solution, particularly in remote areas where traditional power infrastructure may be limited.
Automation and Smart Technologies
The advent of automation and smart technologies is poised to revolutionize conveyor belt operations. Sensors and IoT (Internet of Things) devices can be embedded within conveyor belts to monitor their condition in real-time. These sensors can track various parameters such as temperature, tension, alignment, and wear, providing valuable data to predict maintenance needs and prevent unexpected breakdowns.
Artificial intelligence (AI) and machine learning algorithms can analyze this data to optimize conveyor belt performance. Predictive maintenance, enabled by AI, allows for timely interventions before minor issues escalate into major problems. This proactive approach minimizes downtime, enhances operational efficiency, and extends the lifespan of the conveyor belt system.
Environmental Impact Reduction
As environmental concerns become increasingly paramount, future conveyor belt technologies will likely emphasize reducing their ecological footprint. In addition to using renewable energy sources, conveyor belts can be designed to minimize land disruption and habitat fragmentation. Elevated conveyor belt structures, for instance, can allow wildlife to move freely underneath, preserving natural habitats and reducing the impact on local ecosystems.
Moreover, advancements in dust control technologies will play a crucial role in mitigating the environmental impact of conveyor belts. Dust suppression systems that use water sprays, foam, or chemical additives can significantly reduce the amount of dust generated during material transportation. These systems not only improve air quality but also enhance the health and safety of workers and nearby communities.
Enhanced Safety Features
Future developments in conveyor belt technology will also focus on enhancing safety features. Conveyor belts used in mining and industrial operations pose various safety risks, including belt misalignment, overloading, and fire hazards. Integrating advanced safety features can mitigate these risks and ensure the well-being of workers.
Emergency stop systems, automatic shut-off mechanisms, and fire detection and suppression systems can be incorporated into conveyor belt designs. Additionally, the use of augmented reality (AR) and virtual reality (VR) technologies can provide immersive training for workers, allowing them to understand and respond to potential hazards effectively.
Modular and Flexible Designs
The future of conveyor belt technology will likely see the development of more modular and flexible designs. Traditional conveyor belts are often custom-built for specific applications, which can be time-consuming and costly. Modular conveyor belt systems, on the other hand, offer greater flexibility and ease of installation.
Modular designs allow for the quick assembly and disassembly of conveyor belts, enabling mining operations to adapt to changing needs and conditions. This flexibility is particularly beneficial in environments where mining sites may shift or expand over time. By using standardized components, modular conveyor belts can reduce installation times, lower costs, and improve operational efficiency.
Sustainability and Circular Economy
Embracing the principles of sustainability and the circular economy will be crucial for the future of conveyor belt technology. Manufacturers will increasingly focus on designing conveyor belts that are recyclable and made from sustainable materials. End-of-life management strategies, such as recycling programs and the repurposing of old conveyor belts, will become more prevalent.
Additionally, the concept of the circular economy can be applied to the entire lifecycle of conveyor belts. This approach involves designing products with a focus on longevity, reparability, and recyclability. By extending the lifespan of conveyor belts and minimizing waste, the mining industry can contribute to a more sustainable and environmentally friendly future.
Integration with Advanced Transportation Systems
The integration of conveyor belt systems with advanced transportation technologies, such as autonomous vehicles and drones, presents an exciting frontier for future developments. Autonomous vehicles can be used to transport materials to and from conveyor belts, streamlining logistics and reducing the need for manual labor.
Drones equipped with cameras and sensors can provide aerial surveillance and inspection of conveyor belts, identifying potential issues and ensuring optimal performance. These advanced transportation systems can enhance the overall efficiency and effectiveness of conveyor belt operations, particularly in large-scale mining projects.
The Types of Longest Conveyor Belt in Australia
Maintenance and Operational Challenges of Long Conveyor Belts
When discussing the marvels of modern engineering in the mining industry, the longest conveyor belt in Australia stands out as a significant achievement. Located in Western Australia’s Pilbara region, this belt spans approximately 20 kilometers and plays a crucial role in the efficient transport of iron ore. However, maintaining and operating such an extensive conveyor belt system presents unique challenges that must be addressed to ensure its reliability and longevity.
Maintenance Practices
Maintenance is a critical aspect of ensuring the optimal performance of long conveyor belts. The longest conveyor belt in Australia is subjected to continuous use, transporting large quantities of iron ore across vast distances. To maintain its functionality, a comprehensive maintenance strategy is essential.
Routine inspections are a cornerstone of effective maintenance. These inspections involve checking the belt for signs of wear and tear, such as fraying edges, cracking, and surface damage. Regularly scheduled inspections help identify potential issues before they become major problems, allowing for timely repairs and replacements.
Lubrication of moving parts, such as rollers and pulleys, is another vital maintenance practice. Proper lubrication reduces friction, which in turn minimizes wear and extends the lifespan of these components. The maintenance team must ensure that the correct type of lubricant is used and that it is applied at appropriate intervals.
Operational Challenges
Operating the longest conveyor belt in Australia involves overcoming several challenges. One of the primary challenges is dealing with the harsh environmental conditions of the Pilbara region. Extreme temperatures, dust, and heavy rains can all impact the performance of the conveyor belt.
Dust is a significant issue in mining environments. It can accumulate on the belt and its components, leading to increased friction and wear. Dust suppression systems, such as water sprays and dust collectors, are employed to mitigate this problem. These systems must be regularly maintained to ensure their effectiveness.
Temperature fluctuations pose another challenge. The intense heat of the Australian summer can cause the belt to expand, while cooler temperatures at night can lead to contraction. This thermal expansion and contraction can cause misalignment and increased tension, potentially leading to belt damage. To address this, the conveyor belt system is equipped with tensioning devices that automatically adjust the belt tension to compensate for temperature changes.
Advanced Monitoring Technologies
To manage the maintenance and operational challenges of long conveyor belts, advanced monitoring technologies are increasingly being utilized. These technologies provide real-time data on the condition and performance of the belt, enabling proactive maintenance and timely interventions.
For example, sensors installed along the length of the conveyor belt monitor various parameters such as speed, tension, and temperature. These sensors detect anomalies and alert the maintenance team to potential issues. By analyzing this data, the team can predict when maintenance is needed, reducing the risk of unexpected breakdowns.
Predictive Maintenance
Predictive maintenance is a forward-thinking approach that leverages data analytics and machine learning to forecast maintenance needs. By analyzing historical data and identifying patterns, predictive maintenance systems can predict when a component is likely to fail and schedule maintenance accordingly.
The longest conveyor belt in Australia benefits from predictive maintenance, which helps minimize downtime and extend the lifespan of the belt. This approach not only enhances the reliability of the conveyor belt but also reduces maintenance costs by preventing major failures and optimizing the use of resources.
Environmental Considerations
Operating and maintaining long conveyor belts also involves addressing environmental considerations. The Pilbara region’s delicate ecosystem requires careful management to minimize the environmental impact of mining operations.
One of the ways this is achieved is through the use of eco-friendly lubricants and dust suppression systems. These products are designed to have minimal environmental impact while effectively maintaining the conveyor belt. Additionally, the conveyor belt’s route is planned to avoid sensitive areas and reduce habitat disruption.
Regular environmental monitoring is conducted to ensure that the mining operations, including the conveyor belt, comply with environmental regulations and standards. This monitoring includes assessing the impact on local wildlife, vegetation, and water sources.
Safety Measures
Safety is a paramount concern in the operation and maintenance of long conveyor belts. The longest conveyor belt in Australia is equipped with multiple safety features to protect workers and ensure safe operations.
Emergency stop systems are installed at regular intervals along the belt, allowing workers to halt the belt in case of an emergency. Guards and barriers are in place to prevent accidental contact with moving parts. Additionally, workers receive comprehensive training on safe operating procedures and emergency response protocols.
Future Developments
The future of long conveyor belts, including the longest conveyor belt in Australia, lies in continuous improvement and innovation. Research and development efforts are focused on developing new materials that offer greater durability and resistance to environmental factors. Advances in automation and artificial intelligence will further enhance the efficiency and reliability of conveyor belt systems.
As technology continues to evolve, the integration of smart systems and the Internet of Things (IoT) will provide even greater control and monitoring capabilities. These advancements will help address the maintenance and operational challenges of long conveyor belts, ensuring they remain a vital component of the mining industry for years to come.
FAQS about Longest Conveyor Belt in Australia
The longest conveyor in Australia is the Curragh overland conveyor, which extends over 20 kilometers (12.4 miles). Located in Queensland, this conveyor system is an integral part of the Curragh coal mine operations. It efficiently transports coal from the mine to the processing plant, significantly enhancing the mine’s productivity and operational efficiency. The Curragh conveyor system is a remarkable engineering achievement, showcasing advanced technology in material handling and transportation. The conveyor’s design includes robust components to ensure reliable performance and minimal maintenance, even under the demanding conditions of a large-scale mining operation. This system exemplifies how long-distance conveyor belts can improve the logistics and overall efficiency of resource extraction and processing industries.
The world’s longest conveyor belt is located in the Western Sahara, stretching over 61 miles (98 kilometers) from the phosphate mines of Bou Craa to the coast south of El-Aaiun. This conveyor belt system, built in the early 1980s, was designed to transport vast quantities of phosphate rock from the mines to the port for export. The belt’s remarkable length and capacity allow it to move up to 2,000 tons of phosphate rock per hour, making it a critical component in the global phosphate supply chain. Its construction involved overcoming significant engineering challenges, including traversing harsh desert terrain and ensuring the system’s durability and reliability in an extreme environment. The Bou Craa conveyor belt is an impressive testament to human ingenuity and the capability to create infrastructure that supports large-scale industrial operations.
The world’s largest conveyor belt is also located in the Western Sahara, specifically from the Bou Craa phosphate mines to the coastal port near Laayoune. This conveyor system holds the record for being the longest single belt conveyor, spanning an impressive 61 miles (98 kilometers). The conveyor belt plays a crucial role in the transportation of phosphate rock, a key ingredient in agricultural fertilizers, from the mines to the port for shipping to various parts of the world. The belt’s visibility from space highlights its massive scale and the significant impact it has on the region’s economy. The system’s ability to handle the transportation of large quantities of phosphate rock efficiently makes it an essential infrastructure component for the mining and agricultural industries globally.
The Australian standard for conveyors is outlined in the AS 1755-2000 standard, which provides comprehensive guidelines for the design, installation, and operation of conveyor systems to ensure safety and efficiency. This standard covers various aspects of conveyor systems, including belt conveyors, chain conveyors, and roller conveyors. It includes requirements for guarding, emergency stop controls, and maintenance procedures to minimize the risk of accidents and ensure the safe operation of conveyor equipment. The AS 1755-2000 standard emphasizes the importance of regular inspections, proper training for operators, and adherence to safety protocols to prevent workplace injuries. Compliance with these standards is essential for companies operating conveyor systems in Australia, ensuring they meet regulatory requirements and maintain high safety and operational standards.
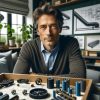
Jordan Smith, a seasoned professional with over 20 years of experience in the conveyor system industry. Jordan’s expertise lies in providing comprehensive solutions for conveyor rollers, belts, and accessories, catering to a wide range of industrial needs. From initial design and configuration to installation and meticulous troubleshooting, Jordan is adept at handling all aspects of conveyor system management. Whether you’re looking to upgrade your production line with efficient conveyor belts, require custom conveyor rollers for specific operations, or need expert advice on selecting the right conveyor accessories for your facility, Jordan is your reliable consultant. For any inquiries or assistance with conveyor system optimization, Jordan is available to share his wealth of knowledge and experience. Feel free to reach out at any time for professional guidance on all matters related to conveyor rollers, belts, and accessories.