Installation Insights from Gen Conveyor Belt Review
Gen conveyor belt is known for its durability and efficiency, catering to various industrial applications such as manufacturing, mining, and material handling. This review aims to provide a comprehensive evaluation of the gen conveyor belt, covering its key features, performance, and suitability for different operational environments. By exploring the benefits and potential drawbacks of the gen conveyor belt, this review seeks to offer valuable insights for businesses looking to optimize their conveyor systems for enhanced productivity and safety.
Key Features of Gen Conveyor Belt Review
The Gen conveyor belt stands out in the industrial sector due to its advanced features and robust design, tailored to meet the diverse needs of various applications. This section will detail the essential features of the Gen conveyor belt, highlighting their significance and benefits in industrial environments.
Advanced Material Composition
One of the most notable features of the Gen conveyor belt is its advanced material composition. These conveyor belts are manufactured using high-quality synthetic polymers and reinforced with durable fibers, providing exceptional strength and flexibility. This material choice ensures that the Gen conveyor belt can withstand heavy loads, resist abrasion, and operate effectively in harsh conditions.
Benefits:
- Enhanced Durability: The high-quality materials used in the Gen conveyor belt make it highly resistant to wear and tear, extending its operational life and reducing maintenance costs.
- Load-Bearing Capacity: The reinforced structure allows the conveyor belt to carry heavier loads, making it suitable for a wide range of industrial applications, from mining to manufacturing.
Innovative Design Features
The Gen conveyor belt incorporates several innovative design features that enhance its performance and usability. These include:
- Modular Design: The modular design of the Gen conveyor belt allows for easy customization and scalability. Sections of the belt can be easily added or removed to accommodate changes in production requirements.
- Precision Engineering: The belts are engineered with precision to ensure smooth operation and minimal friction, which reduces energy consumption and increases efficiency.
Benefits:
- Flexibility: The modular design enables quick adjustments and repairs, minimizing downtime and improving productivity.
- Energy Efficiency: Precision engineering reduces operational resistance, leading to lower energy usage and operational costs.
Advanced Control Systems
Modern Gen conveyor belts are equipped with advanced control systems that facilitate seamless integration with other automated systems. These control systems include features like real-time monitoring, automated speed adjustment, and predictive maintenance alerts.
Benefits:
- Improved Monitoring and Control: Real-time monitoring allows operators to track the performance of the conveyor belt and make adjustments as needed, enhancing overall system efficiency.
- Reduced Downtime: Predictive maintenance alerts help identify potential issues before they become critical, reducing unexpected downtime and maintenance costs.
Safety Features
Safety is a critical concern in industrial operations, and the Gen conveyor belt addresses this with a range of safety features. These include:
- Emergency Stop Mechanisms: Easily accessible emergency stop buttons are placed at strategic points along the conveyor belt.
- Safety Guards and Shields: Protective guards and shields are installed to prevent accidental contact with moving parts.
Benefits:
- Enhanced Safety: These features protect workers from potential hazards, reducing the risk of accidents and injuries.
- Compliance with Regulations: The inclusion of robust safety mechanisms ensures that the conveyor belts comply with industry safety standards and regulations.
Performance Evaluation in the Gen Conveyor Belt Review
Evaluating the performance of the Gen conveyor belt involves assessing various metrics that determine its efficiency, reliability, and overall value in industrial applications. This section will discuss the key performance metrics and the results of these evaluations.
Load Capacity and Durability Testing
One of the primary performance metrics for conveyor belts is their load capacity and durability. The Gen conveyor belt undergoes rigorous testing to ensure it can handle the maximum load requirements of different industries without compromising on durability.
Results:
- High Load Capacity: Tests show that the Gen conveyor belt can carry significantly heavier loads compared to standard belts, making it suitable for high-demand environments.
- Long-Term Durability: Durability tests indicate that the belt maintains its integrity and performance even after prolonged use in harsh conditions, showcasing its long-term reliability.
Energy Efficiency Analysis
Energy efficiency is a critical factor in evaluating conveyor belt performance, as it directly impacts operational costs. The Gen conveyor belt is designed to operate with minimal energy consumption, and this is verified through comprehensive energy efficiency analysis.
Results:
- Lower Energy Consumption: The analysis reveals that the Gen conveyor belt consumes less energy compared to traditional belts, thanks to its precision engineering and low-friction design.
- Cost Savings: Reduced energy consumption translates to lower operational costs, providing significant savings for industrial operations over time.
Speed and Throughput Evaluation
The speed and throughput of a conveyor belt determine its efficiency in handling production processes. The Gen conveyor belt is tested for its ability to maintain consistent speed and high throughput under various conditions.
Results:
- Consistent Speed: Tests confirm that the Gen conveyor belt maintains a steady and reliable speed, ensuring smooth and continuous operation.
- High Throughput: The belt’s design allows for high throughput rates, enabling faster processing times and improved productivity.
Maintenance and Downtime Assessment
Minimizing maintenance requirements and downtime is essential for maintaining high operational efficiency. The Gen conveyor belt is evaluated for its maintenance needs and the frequency of downtime occurrences.
Results:
- Low Maintenance Requirements: The Gen conveyor belt requires minimal maintenance due to its robust design and advanced materials, which reduces the overall maintenance burden on operators.
- Reduced Downtime: Predictive maintenance features and durable construction contribute to significantly lower downtime, ensuring continuous and reliable operation.
User Feedback and Case Studies
In addition to quantitative metrics, user feedback and case studies provide valuable insights into the real-world performance of the Gen conveyor belt. Feedback from various industries highlights the practical benefits and challenges encountered during its use.
Results:
- Positive User Feedback: Users consistently report high satisfaction with the Gen conveyor belt’s performance, citing its reliability, efficiency, and ease of maintenance as key advantages.
- Successful Case Studies: Numerous case studies demonstrate successful implementations of the Gen conveyor belt in diverse industrial settings, further validating its effectiveness and versatility.
Installation and Setup Insights from Gen Conveyor Belt Review
The installation and setup process of the Gen conveyor belt is crucial for ensuring its optimal performance and longevity. This section provides detailed insights into the installation procedures, along with tips and best practices for a smooth and efficient setup.
Pre-Installation Planning
Effective installation begins with thorough pre-installation planning. This involves:
- Site Assessment: Conducting a comprehensive assessment of the installation site to identify any potential challenges and requirements.
- Resource Allocation: Ensuring that all necessary resources, including tools, equipment, and personnel, are available and ready for the installation process.
Tips:
- Detailed Site Survey: Perform a detailed survey of the installation site to identify any structural or environmental factors that may impact the installation.
- Resource Checklist: Create a checklist of all required resources and ensure they are prepared in advance to avoid delays.
Installation Process
The installation process of the Gen conveyor belt is designed to be straightforward and efficient. Key steps include:
- Foundation Preparation: Preparing the foundation and support structure to ensure stability and alignment.
- Belt Assembly: Assembling the conveyor belt sections according to the manufacturer’s instructions, ensuring proper alignment and tension.
- System Integration: Integrating the conveyor belt with other systems and components, such as motors, sensors, and control units.
Best Practices:
- Foundation Stability: Ensure that the foundation is stable and level to prevent misalignment and uneven wear on the belt.
- Correct Tensioning: Properly tension the belt to avoid slippage and ensure smooth operation.
- System Testing: Perform thorough testing of the integrated system to identify and address any issues before full-scale operation.
Post-Installation Inspection and Testing
After the installation is complete, a comprehensive inspection and testing process is essential to verify the correct setup and functionality of the Gen conveyor belt. This includes:
- Visual Inspection: Conducting a visual inspection to check for any visible defects or alignment issues.
- Operational Testing: Running the conveyor belt under various load conditions to ensure it operates smoothly and efficiently.
Tips:
- Detailed Inspection Checklist: Use a detailed checklist during the inspection to ensure all critical components are thoroughly examined.
- Load Testing: Perform load testing with different weights to verify the belt’s performance and identify any potential issues.
Maintenance Best Practices
Maintaining the Gen conveyor belt properly is crucial for maximizing its lifespan and performance. Best practices for maintenance include:
- Regular Inspections: Conducting regular inspections to identify and address any wear and tear or potential issues early on.
- Lubrication and Cleaning: Keeping the belt and its components well-lubricated and clean to prevent buildup and reduce friction.
Tips:
- Scheduled Maintenance: Establish a regular maintenance schedule to ensure timely inspections and servicing.
- Documentation: Maintain detailed records of all maintenance activities to track the belt’s condition and performance over time.
Training and Support
Providing adequate training and support for personnel involved in the installation and maintenance of the Gen conveyor belt is essential for ensuring smooth and efficient operation. This includes:
- Operator Training: Training operators on the proper use and maintenance of the conveyor belt.
- Technical Support: Ensuring access to technical support and resources from the manufacturer or supplier.
Best Practices:
- Comprehensive Training Programs: Implement comprehensive training programs that cover all aspects of the conveyor belt’s operation and maintenance.
- Access to Support: Ensure that operators and maintenance personnel have easy access to technical support and resources to address any issues promptly.
By following these detailed insights and best practices, users can ensure a smooth installation and optimal performance of the Gen conveyor belt in their industrial applications. The combination of advanced features, rigorous performance evaluation, and thorough installation procedures makes the Gen conveyor belt a reliable and efficient solution for various industries.
Maintenance Tips Highlighted in the Gen Conveyor Belt Review
Importance of Regular Maintenance
To ensure the longevity and optimal performance of Gen conveyor belts, it’s essential to implement a robust maintenance regimen. Regular maintenance helps in identifying potential issues before they escalate into significant problems, thereby avoiding unexpected downtime and costly repairs. By following the maintenance tips highlighted in the Gen conveyor belt review, you can maximize the efficiency and lifespan of your conveyor system.
Regular Inspections
Regular inspections are the cornerstone of effective conveyor belt maintenance. These inspections should be conducted at scheduled intervals, depending on the usage and environmental conditions of the conveyor system. Here are some key points to consider during inspections:
- Visual Checks:
- Inspect the conveyor belt for signs of wear and tear, such as fraying edges, cracks, or punctures.
- Check for any misalignment or uneven wear patterns that might indicate issues with the conveyor’s setup.
- Ensure that all fasteners, including screws and bolts, are secure and have not loosened due to vibration.
- Belt Tension:
- Regularly check the tension of the conveyor belt to ensure it is neither too tight nor too loose. Improper tension can lead to slippage or excessive strain on the motor and other components.
- Adjust the tension according to the manufacturer’s recommendations.
- Rollers and Pulleys:
- Inspect rollers and pulleys for any signs of damage or wear. Ensure they rotate freely and are properly aligned.
- Look for any build-up of debris or material on the rollers and pulleys that could affect their performance.
- Motor and Drive System:
- Check the motor and drive system for any unusual noises or vibrations that could indicate mechanical issues.
- Ensure the drive belt or chain is in good condition and properly tensioned.
Cleaning Methods
Keeping the Gen conveyor belt clean is vital for its efficient operation and longevity. Accumulated debris, dust, and material residues can cause various issues, including belt slippage, misalignment, and increased wear. Here are some cleaning methods to maintain your conveyor belt:
- Regular Cleaning Schedule:
- Establish a regular cleaning schedule based on the conveyor’s usage and the environment in which it operates. High-dust environments may require more frequent cleaning.
- Cleaning Tools and Techniques:
- Use appropriate cleaning tools, such as brushes, air blowers, or vacuum cleaners, to remove loose debris and dust from the belt surface and components.
- For more stubborn residues, use mild detergents and water. Avoid using harsh chemicals that could damage the belt material.
- Ensure the belt is completely dry before restarting the conveyor to prevent slippage and corrosion.
- Cleaning Specific Areas:
- Pay special attention to areas where debris is likely to accumulate, such as under the belt, around rollers and pulleys, and at transfer points.
- Regularly clean the drive system and motor housing to prevent overheating and ensure efficient operation.
Preventative Practices
In addition to regular inspections and cleaning, adopting preventative maintenance practices can significantly enhance the performance and lifespan of your Gen conveyor belt. Here are some preventative practices to consider:
- Lubrication:
- Regularly lubricate moving parts such as bearings, rollers, and chains to reduce friction and wear. Use lubricants recommended by the manufacturer to ensure compatibility with the conveyor components.
- Avoid over-lubrication, as excess lubricant can attract dust and debris, leading to further issues.
- Alignment Checks:
- Periodically check the alignment of the conveyor belt to ensure it is running straight and true. Misalignment can cause uneven wear and reduce the belt’s lifespan.
- Use alignment tools or professional services to make precise adjustments.
- Temperature Control:
- Monitor the operating temperature of the conveyor system. Excessive heat can cause the belt material to degrade and reduce its strength.
- Ensure adequate ventilation and cooling systems are in place, especially in high-temperature environments.
- Load Management:
- Avoid overloading the conveyor belt beyond its rated capacity. Overloading can cause excessive strain on the belt and other components, leading to premature failure.
- Distribute the load evenly across the belt to prevent localized stress and wear.
By following these maintenance tips highlighted in the Gen conveyor belt review, you can ensure the optimal performance and longevity of your conveyor system. Regular inspections, proper cleaning, and preventative practices are essential for maintaining the efficiency and reliability of your Gen conveyor belt.
Common Applications Covered in the Gen Conveyor Belt Review
Industrial Applications
Gen conveyor belts are renowned for their versatility and durability, making them suitable for a wide range of industrial applications. In the Gen conveyor belt review, several common applications are highlighted, showcasing the adaptability and efficiency of these conveyor systems.
- Manufacturing:
- In the manufacturing industry, Gen conveyor belts are used to transport raw materials, components, and finished products between different stages of the production process.
- These belts facilitate efficient and continuous movement, reducing manual handling and increasing productivity.
- Mining and Quarrying:
- Gen conveyor belts are widely used in the mining and quarrying industries for the transportation of bulk materials such as ores, coal, and aggregates.
- Their robust construction and resistance to abrasion and impact make them ideal for handling heavy and abrasive materials.
- Food and Beverage:
- The food and beverage industry relies on Gen conveyor belts for the hygienic and efficient transport of food products.
- These belts are designed to meet strict sanitary standards, with features such as easy-to-clean surfaces and resistance to contamination.
- Logistics and Distribution:
- In logistics and distribution centers, Gen conveyor belts are used to sort and transport packages, parcels, and other items.
- Their high-speed capabilities and reliability ensure smooth and efficient operations, even in high-volume environments.
- Automotive:
- The automotive industry utilizes Gen conveyor belts for the assembly and transport of vehicle components and parts.
- These belts support the streamlined production processes required in modern automotive manufacturing.
Specific Industry Examples
The versatility of Gen conveyor belts is further demonstrated by their application in various specific industries. Here are some examples of industries that benefit from these conveyor belts:
- Pharmaceutical:
- In the pharmaceutical industry, Gen conveyor belts are used to transport medicines, medical devices, and packaging materials.
- Their precision and cleanliness are crucial for maintaining the integrity and safety of pharmaceutical products.
- Aerospace:
- The aerospace industry uses Gen conveyor belts for the assembly and transport of aircraft components and materials.
- These belts contribute to the precise and efficient manufacturing processes required in aerospace production.
- Recycling and Waste Management:
- Gen conveyor belts play a vital role in recycling and waste management facilities, where they are used to sort and transport recyclable materials and waste.
- Their durability and resistance to wear and tear make them suitable for handling a variety of materials, including metals, plastics, and paper.
- Agriculture:
- In the agricultural industry, Gen conveyor belts are used to transport harvested crops, seeds, and fertilizers.
- These belts support the efficient and timely movement of agricultural products, contributing to increased productivity and reduced labor costs.
- Construction:
- The construction industry utilizes Gen conveyor belts for the transport of building materials such as concrete, bricks, and aggregates.
- Their robust design and ability to handle heavy loads make them essential for efficient material handling on construction sites.
By covering a wide range of industrial applications, the Gen conveyor belt review highlights the adaptability and efficiency of these conveyor systems. Whether in manufacturing, mining, food and beverage, or other industries, Gen conveyor belts provide reliable and effective solutions for material transport.
Detailed Look at Gen Conveyor Belt Parts
Key Parts of a Gen Conveyor Belt System
A Gen conveyor belt system is composed of several key parts, each playing a crucial role in the overall function and efficiency of the system. Understanding these parts and their functions is essential for effective operation and maintenance. In this detailed look at Gen conveyor belt parts, we will explore the primary components and their roles.
- Conveyor Belt:
- The conveyor belt itself is the most critical part of the system. It is a continuous loop of material that transports items from one point to another.
- The belt is typically made of durable materials such as rubber, PVC, or polyurethane, depending on the application and operating environment.
- Its design includes features like resistance to wear, flexibility, and the ability to withstand various loads and temperatures.
- Drive Pulley:
- The drive pulley is responsible for moving the conveyor belt. It is connected to the motor and transmits power to the belt, causing it to move.
- This pulley is usually made of metal and is designed to provide sufficient traction to prevent belt slippage.
- Idler Pulleys:
- Idler pulleys support the conveyor belt and help maintain proper tension. They do not provide drive power but guide and support the belt along its path.
- These pulleys are strategically placed along the conveyor system to ensure smooth and consistent movement.
- Motor:
- The motor provides the necessary power to drive the conveyor belt. It is typically an electric motor, chosen based on the required speed and load capacity of the conveyor system.
- The motor’s specifications, such as horsepower and torque, are selected to match the conveyor’s operational needs.
- Frame:
- The frame of the conveyor system provides structural support and stability. It is usually constructed from steel or aluminum, offering durability and strength.
- The frame houses and supports all other components of the conveyor system, ensuring proper alignment and operation.
- Belt Tensioning Device:
- The belt tensioning device is used to adjust the tension of the conveyor belt. Proper tension is crucial for preventing slippage and ensuring efficient operation.
- Tensioning devices can be mechanical or automatic, depending on the conveyor system’s design.
- Rollers:
- Rollers are cylindrical components that support the conveyor belt and allow it to move smoothly. They are positioned along the length of the conveyor system.
- Rollers can be made from various materials, including metal and plastic, and are designed to reduce friction and wear on the belt.
- Control System:
- The control system manages the operation of the conveyor belt, including speed, direction, and timing. It typically includes a control panel, sensors, and software.
- Advanced control systems can offer features such as automated sorting, variable speed control, and integration with other equipment.
- Belt Cleaner:
- Belt cleaners are installed to remove material residues and debris from the conveyor belt surface. They help maintain cleanliness and prevent build-up that could affect performance.
- These cleaners are typically positioned at strategic points, such as near the drive pulley, to ensure efficient cleaning.
- Safety Devices:
- Safety devices are essential components that ensure the safe operation of the conveyor system. These can include emergency stop buttons, guards, and safety sensors.
- These devices protect workers and prevent accidents by stopping the conveyor belt in case of emergencies or abnormal conditions.
Role of Each Part in the Overall Function
Each part of the Gen conveyor belt system plays a specific role in ensuring efficient and reliable operation. Here is an explanation of how these components contribute to the overall function of the conveyor belt:
- Conveyor Belt:
- The primary role of the conveyor belt is to transport materials from one location to another. Its continuous loop design allows for efficient and uninterrupted movement.
- Drive Pulley:
- The drive pulley is crucial for moving the conveyor belt. By transmitting power from the motor, it sets the belt in motion and maintains the desired speed and direction.
- Idler Pulleys:
- Idler pulleys provide support and guidance for the conveyor belt. They help maintain proper tension and alignment, ensuring smooth and consistent movement.
- Motor:
- The motor powers the conveyor system, driving the belt and enabling it to transport materials. Its specifications determine the speed and load capacity of the conveyor.
- Frame:
- The frame provides the structural foundation for the conveyor system. It ensures stability and alignment of all components, allowing for efficient operation.
- Belt Tensioning Device:
- The belt tensioning device adjusts and maintains the proper tension of the conveyor belt. Proper tension is essential for preventing slippage and ensuring efficient movement.
- Rollers:
- Rollers support the conveyor belt and reduce friction, allowing for smooth movement. They distribute the load evenly and prevent excessive wear on the belt.
- Control System:
- The control system manages the operation of the conveyor belt, including speed, direction, and timing. It ensures coordinated and efficient operation, often integrating with other systems for automation.
- Belt Cleaner:
- Belt cleaners maintain the cleanliness of the conveyor belt, preventing material build-up that could affect performance. They ensure efficient operation by removing residues and debris.
- Safety Devices:
- Safety devices protect workers and prevent accidents by stopping the conveyor belt in case of emergencies. They ensure safe operation and compliance with safety regulations.
By understanding the detailed roles of each part of the Gen conveyor belt system, operators and maintenance personnel can ensure efficient and reliable operation. Regular maintenance, proper operation, and timely replacement of worn parts are essential for maximizing the lifespan and performance of the conveyor system.
FAQs about Gen Conveyor Belt
There are three main types of conveyor belts: flat belts, modular belts, and cleated belts. Flat belts are the most common type and are used for transporting goods in a straight line. They are versatile and can handle a variety of products, making them ideal for general material handling. Modular belts are made of interlocking pieces of plastic, allowing for easy maintenance and flexibility in design. They are suitable for applications where sanitation and ease of cleaning are important, such as in the food industry. Cleated belts have raised sections or cleats that help keep products in place during transportation, making them perfect for moving items up inclines or along curves.
The world’s longest conveyor belt is located in the Western Sahara. It spans over 61 miles (98 kilometers) and is used to transport phosphate from the Bou Craa mine to the coastal town of El-Aaiun. This massive conveyor belt system is a crucial part of the mining operation, allowing for efficient and continuous movement of large quantities of phosphate rock. The belt passes through several terrains, including desert and rocky landscapes, demonstrating its robust design and engineering. The Bou Craa conveyor belt is a testament to human ingenuity and the ability to create infrastructure that can withstand harsh environmental conditions.
The strongest conveyor belt in the world is the Phoenocord St 7800, manufactured by Phoenix Conveyor Belt Systems. This belt is designed for the highest tensile strength, capable of handling demanding and heavy-duty applications. It is used in the mining industry, particularly in long-distance and high-capacity applications. The Phoenocord St 7800 has a breaking strength of up to 7,800 N/mm, making it exceptionally durable and reliable. This conveyor belt’s strength comes from its unique construction, which includes multiple layers of steel cords embedded within the rubber, providing both flexibility and extreme toughness.
Conveyor belt grade refers to the quality and characteristics of the materials used in the belt’s construction, which determine its suitability for specific applications. Different grades are assigned based on factors such as tensile strength, wear resistance, and fire resistance. For example, Grade M is designed for general use with moderate wear resistance, while Grade N is known for its superior abrasion resistance, making it suitable for handling abrasive materials. Fire-resistant grades, such as FRAS (Fire Resistant and Anti-Static), are used in environments where fire hazards are present. Understanding conveyor belt grades is essential for selecting the right belt for a particular application, ensuring both safety and efficiency.
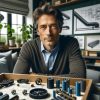
Jordan Smith, a seasoned professional with over 20 years of experience in the conveyor system industry. Jordan’s expertise lies in providing comprehensive solutions for conveyor rollers, belts, and accessories, catering to a wide range of industrial needs. From initial design and configuration to installation and meticulous troubleshooting, Jordan is adept at handling all aspects of conveyor system management. Whether you’re looking to upgrade your production line with efficient conveyor belts, require custom conveyor rollers for specific operations, or need expert advice on selecting the right conveyor accessories for your facility, Jordan is your reliable consultant. For any inquiries or assistance with conveyor system optimization, Jordan is available to share his wealth of knowledge and experience. Feel free to reach out at any time for professional guidance on all matters related to conveyor rollers, belts, and accessories.