General Conveyor Belt Industries Used
General conveyor belt is an essential component in numerous industries, facilitating the efficient movement of materials and products. These belts are versatile and can be tailored to meet specific operational needs, making them indispensable in manufacturing, logistics, and mining. Key considerations when selecting a general conveyor belt include the price, which can vary based on material and dimensions, the frequency of replacement needed to maintain optimal performance, and the availability of parts for maintenance and repair. Understanding these factors helps businesses choose the right conveyor belt for their operations, ensuring longevity and reliability.
Factors Influencing General Conveyor Belt Price
When considering the acquisition of a general conveyor belt, understanding the various factors that influence its price is crucial for making an informed decision. The price of a general conveyor belt is determined by a combination of material quality, dimensions, and additional features. This section delves into these factors in detail.
Material Quality
The material used in the construction of a general conveyor belt significantly impacts its price. Conveyor belts can be made from various materials, each with different properties and cost implications.
- Rubber Belts: These are commonly used due to their durability and flexibility. They are ideal for handling a wide range of materials, including abrasive and heavy items. Rubber belts are generally affordable but can vary in price based on the quality and thickness of the rubber.
- PVC and PU Belts: These belts are known for their chemical resistance and ease of cleaning, making them suitable for food processing and pharmaceutical applications. PVC and PU belts tend to be more expensive than rubber belts due to their specialized properties.
- Metal Belts: Used in high-temperature applications or environments requiring a high degree of sanitation, metal belts are made from stainless steel or other alloys. These belts are typically the most expensive due to their robustness and specialized manufacturing processes.
Dimensions: Length and Width
The length and width of a general conveyor belt directly affect its price. Larger belts require more material and, consequently, have higher costs.
- Length: The longer the belt, the more material is needed, which increases the overall price. Long conveyor belts are often used in large-scale industrial operations and can be customized to fit specific needs.
- Width: Wider belts are necessary for transporting bulkier items or handling higher volumes of material. The width of the belt must be chosen based on the size and type of items being conveyed, with wider belts generally costing more.
Special Features
Special features and customizations can also drive up the price of a general conveyor belt.
- Cleats and Sidewalls: Adding cleats or sidewalls to a conveyor belt helps to prevent material from falling off and improves handling on inclines. These features add to the manufacturing complexity and cost of the belt.
- Heat Resistance: For applications involving high temperatures, heat-resistant belts are required. These belts are made from specialized materials that can withstand extreme heat, which increases their cost.
- Oil and Chemical Resistance: In industries dealing with oils, chemicals, or corrosive substances, belts with special resistance properties are necessary. These belts are more expensive due to the advanced materials and treatments used in their production.
- Antistatic Properties: In environments where static electricity could pose a hazard, antistatic conveyor belts are essential. These belts prevent static build-up and are typically priced higher than standard belts.
Manufacturing and Supply Chain Factors
The manufacturing process and supply chain logistics also play a role in the pricing of general conveyor belts.
- Production Costs: The cost of raw materials, labor, and manufacturing technology affects the final price of the conveyor belt. Advances in production technology can reduce costs, but high-quality materials and skilled labor will always be reflected in the price.
- Shipping and Logistics: The cost of transporting large and heavy conveyor belts can add significantly to the overall price, especially for international shipments. Proper packaging and handling to prevent damage during transit are also factors that influence costs.
Market Demand and Supply
The market dynamics of supply and demand can affect the price of general conveyor belts. High demand for certain types of belts or shortages of specific materials can lead to price increases. Conversely, technological advancements and increased competition can drive prices down.
Industries Where General Conveyor Belts Can Be Used
Manufacturing
- Applications: Moving parts and materials through assembly lines, transporting finished products to packaging areas.
- Benefits: Increases efficiency, reduces manual labor, and ensures consistent production flow.
Food and Beverage
- Applications: Transporting ingredients, finished food products, packaging, and sorting.
- Benefits: Maintains hygiene standards, reduces contamination risk, and speeds up production processes.
Pharmaceutical
- Applications: Conveying tablets, capsules, bottles, and packaging materials through various stages of production and packaging.
- Benefits: Ensures precise handling of delicate products, maintains cleanliness, and complies with strict industry regulations.
Mining
- Applications: Moving extracted minerals, ores, and rocks from mines to processing plants.
- Benefits: Handles heavy loads, operates in harsh conditions, and improves efficiency in transporting bulk materials.
Automotive
- Applications: Transporting car parts through assembly lines, handling finished vehicles, and moving components to different production areas.
- Benefits: Streamlines assembly processes, reduces manual handling, and enhances production speed.
Agriculture
- Applications: Conveying crops, seeds, fertilizers, and other agricultural products.
- Benefits: Increases efficiency in handling bulk agricultural products, reduces labor costs, and improves safety.
Logistics and Warehousing
- Applications: Sorting packages, transporting goods within warehouses, loading and unloading trucks.
- Benefits: Enhances order fulfillment speed, improves inventory management, and reduces manual labor.
Packaging
- Applications: Moving products through different packaging stages, from filling to sealing to labeling.
- Benefits: Automates packaging processes, ensures consistency, and increases throughput.
Retail
- Applications: Transporting goods within distribution centers, moving products from storage to shipping areas.
- Benefits: Enhances supply chain efficiency, reduces handling time, and supports large-scale operations.
General conveyor belts play a crucial role in various industries by improving efficiency, reducing manual labor, enhancing safety, and supporting large-scale operations. By understanding the specific needs of each industry, businesses can select the appropriate conveyor belts to optimize their processes and achieve better productivity.

Choose The Right General Conveyor Belts For Your Equipment
Choosing the right general conveyor belt for your equipment involves a detailed understanding of your operational requirements and the specific features of different belt types. Here is a comprehensive guide to help you make the right choice:
Step-by-Step Guide to Choosing the Right Conveyor Belt
1. Identify Your Conveyor System Requirements
- Type of Material: Determine the type of material to be conveyed (e.g., bulk, unit loads, abrasive, corrosive).
- Load Capacity: Know the maximum load that the belt will carry.
- Conveyor Speed: Define the operating speed of the conveyor system.
- Inclination: Consider if the conveyor will operate at an incline or decline.
- Environmental Conditions: Assess the operating environment (temperature, humidity, exposure to chemicals).
2. Select the Belt Material
- Rubber: Durable, flexible, suitable for heavy-duty applications.
- PVC: Lightweight, resistant to chemicals, suitable for light to medium-duty applications.
- Polyurethane: High resistance to abrasion, cuts, and chemicals, ideal for food processing.
- Metal: Suitable for high-temperature applications and heavy-duty industries.
3. Consider Belt Properties
- Abrasion Resistance: Required for handling abrasive materials like minerals and sand.
- Heat Resistance: Necessary for high-temperature applications like baking or foundries.
- Oil and Chemical Resistance: Important for conveying oily, greasy, or chemically aggressive materials.
- Food Grade: Essential for food processing to ensure hygiene and safety.
4. Choose the Appropriate Belt Type
- Flat Belts: Common for general-purpose use, ideal for moving small and medium-sized objects.
- Modular Belts: Made of interlocking pieces, suitable for handling complex loads and easy to maintain.
- Cleated Belts: Have raised sections (cleats) for moving materials at an incline or preventing roll-back.
- Roller Belts: Use rollers to support and convey materials, suitable for heavy loads.
- Wire Mesh Belts: Made of metal wire, perfect for high-temperature and food processing applications.
5. Determine Belt Thickness and Width
- Thickness: Choose based on the weight of materials and the required durability.
- Width: Should be wide enough to handle the load without spillage but fit within the conveyor system’s frame.
6. Assess Drive and Tension Requirements
- Drive Type: Match the belt with the conveyor drive system (e.g., friction drive, positive drive).
- Tension: Ensure the belt can be properly tensioned to prevent slippage and ensure smooth operation.
7. Evaluate Installation and Maintenance Needs
- Ease of Installation: Consider belts that are easy to install and require minimal downtime.
- Maintenance: Opt for belts that are easy to clean and maintain to reduce operational disruptions.
By following these steps, you can ensure that you select the most suitable conveyor belt for your equipment, enhancing efficiency, reducing downtime, and maintaining smooth operations.
Importance of Timely General Conveyor Belt Replacement
Maintaining the efficiency and longevity of conveyor systems hinges on the timely replacement of general conveyor belts. Delaying replacement can lead to a host of issues, from operational inefficiencies to safety hazards. This section underscores the importance of timely general conveyor belt replacement and highlights key indicators that signal the need for replacement.
Maintaining Efficiency and Productivity
A worn or damaged conveyor belt can significantly reduce the efficiency of an entire production line. Over time, belts can develop cracks, tears, or become misaligned, leading to slower operation speeds and increased energy consumption. Timely replacement ensures that the conveyor system operates at optimal efficiency, maintaining high productivity levels and minimizing energy costs.
Preventing Downtime
Unexpected conveyor belt failures can result in costly downtime, halting production and causing delays in order fulfillment. By proactively replacing general conveyor belts before they fail, companies can avoid unscheduled downtime and the associated costs. Planned maintenance and scheduled replacements allow for better resource allocation and less disruption to operations.
Ensuring Safety
Worn conveyor belts can pose serious safety risks to workers. A belt that is frayed or has lost its structural integrity may snap or malfunction, potentially causing injuries. Regular inspections and timely replacements are essential to maintaining a safe working environment. Safety features such as emergency stop mechanisms and guards should also be checked and maintained during the replacement process.
Protecting Equipment
A damaged conveyor belt can affect other components of the conveyor system, such as pulleys, rollers, and motors. Prolonged use of a compromised belt can lead to increased wear and tear on these components, resulting in more extensive and costly repairs. Timely replacement of the belt helps protect the entire conveyor system, extending its overall lifespan and reducing maintenance costs.
Indicators for Replacement
Knowing when to replace a general conveyor belt is crucial for maintaining smooth operations. Here are key indicators that signal the need for replacement:
- Visible Damage: Cracks, tears, or frayed edges on the belt surface are clear signs that the belt needs to be replaced.
- Unusual Noise: Excessive noise during operation, such as squeaking or grinding, can indicate belt misalignment or wear.
- Slippage: If the belt is slipping or not maintaining proper tension, it may be stretched or worn out.
- Reduced Performance: A noticeable decline in the conveyor’s speed or efficiency often points to belt degradation.
- Regular Inspections: Scheduled inspections should reveal any early signs of wear, allowing for proactive replacement.
By addressing these indicators and prioritizing timely replacement, companies can ensure the continuous, safe, and efficient operation of their general conveyor belt systems.

Step-by-Step Guide to General Conveyor Belt Replacement
Replacing a general conveyor belt is a detailed process that requires careful planning and execution to ensure safety and efficiency. This section provides a comprehensive, step-by-step guide to replacing a general conveyor belt, along with essential safety tips and best practices.
Step 1: Preparation and Safety Measures
Before beginning the replacement process, it is crucial to prepare and take necessary safety measures.
- Shut Down the System: Ensure that the conveyor system is completely shut down and locked out to prevent accidental startup during the replacement process.
- Gather Tools and Equipment: Prepare all necessary tools and equipment, including wrenches, screwdrivers, safety gear, and the new conveyor belt.
- Safety Gear: Equip all personnel involved with appropriate safety gear, such as gloves, safety glasses, and hard hats.
Step 2: Remove the Old Conveyor Belt
Removing the old belt involves several steps to ensure it is done safely and efficiently.
- Release Belt Tension: Use the tensioning mechanism to release the tension on the old belt. This will make it easier to remove.
- Disconnect Belt Fasteners: If the belt is joined with mechanical fasteners, disconnect them carefully. For belts that are spliced, cut the belt using a suitable cutting tool.
- Remove the Belt: Carefully pull the old belt off the conveyor system, ensuring that it does not get tangled or cause injury during removal.
Step 3: Prepare the Conveyor System
Before installing the new belt, the conveyor system needs to be prepared.
- Clean the Conveyor: Thoroughly clean the conveyor frame, pulleys, and other components to remove any debris or buildup that could affect the new belt.
- Inspect Components: Check all components, such as rollers and pulleys, for wear and damage. Replace any worn or damaged parts to ensure smooth operation.
Step 4: Install the New Conveyor Belt
Installing the new belt requires careful handling and precise alignment.
- Position the Belt: Lay the new conveyor belt in position, making sure it is properly aligned with the pulleys and rollers.
- Join the Belt Ends: Depending on the belt type, join the ends using mechanical fasteners or by splicing. Follow the manufacturer’s instructions for the specific joining method.
- Tension the Belt: Adjust the tensioning mechanism to apply the correct tension to the new belt. Proper tensioning is crucial for preventing slippage and ensuring smooth operation.
Step 5: Final Adjustments and Testing
After installing the new belt, make final adjustments and test the system.
- Align the Belt: Ensure the belt is properly aligned on the pulleys and rollers to prevent tracking issues.
- Test the System: Run the conveyor system at low speed to check for any issues, such as misalignment or unusual noise. Make necessary adjustments to ensure smooth operation.
- Secure Fasteners: Once the belt is running smoothly, secure all fasteners and components to prevent loosening during operation.
Safety Tips and Best Practices
- Follow Manufacturer’s Instructions: Always follow the manufacturer’s instructions for installing and tensioning the belt.
- Regular Maintenance: Perform regular maintenance and inspections to identify and address issues early.
- Training: Ensure all personnel involved in the replacement process are trained and aware of safety procedures.
- Emergency Procedures: Have emergency procedures in place in case of accidents or unexpected issues during the replacement process.
By following this step-by-step guide and adhering to safety tips and best practices, companies can ensure a successful and safe general conveyor belt replacement process. This proactive approach helps maintain the efficiency and longevity of the conveyor system, reducing downtime and operational costs.
Key General Conveyor Belt Parts and Their Functions
A general conveyor belt system is a complex assembly of various components, each playing a crucial role in ensuring smooth operation and efficiency. Understanding these parts and their functions is essential for maintenance, troubleshooting, and optimizing performance. This section provides an overview of the essential parts of a general conveyor belt system and a detailed description of the role each part plays in the overall system.
Belt
The belt is the most visible and central component of a general conveyor belt system. It serves as the surface on which materials are transported from one point to another. Belts can be made from various materials, including rubber, PVC, fabric, and metal, depending on the application and the type of materials being conveyed.
Function:
- Transportation: The primary function of the belt is to move materials along the conveyor system efficiently and reliably.
- Support and Containment: The belt provides support for the materials being conveyed, ensuring they stay in place and are transported without spillage.
Pulleys
Pulleys are critical components that drive and support the belt. There are typically two main types of pulleys in a general conveyor belt system: the drive pulley and the idler pulley.
Drive Pulley:
- Function: The drive pulley is connected to a motor and provides the necessary force to move the belt. It is usually located at the end of the conveyor where the motor is installed.
- Power Transmission: It transmits power from the motor to the belt, enabling the belt to move continuously.
- Function: The idler pulley supports the belt and helps maintain tension, ensuring the belt runs smoothly and efficiently.
- Alignment: It helps keep the belt aligned and prevents it from slipping off the track.
Rollers
Rollers are cylindrical components that support the belt and the materials being conveyed. They are placed along the length of the conveyor and can be classified into carrying rollers and return rollers.
Carrying Rollers:
- Function: Carrying rollers support the loaded side of the belt, ensuring it remains flat and stable while transporting materials.
- Load Distribution: They help distribute the weight of the materials evenly across the belt.
- Function: Return rollers support the empty side of the belt as it returns to the loading point.
- Belt Tracking: They help maintain proper belt tracking and alignment.
Motor
The motor is the power source of the general conveyor belt system. It converts electrical energy into mechanical energy to drive the conveyor.
Function:
- Power Generation: The motor generates the necessary torque to move the belt and the materials on it.
- Speed Control: Motors often come with speed control mechanisms to adjust the conveyor speed based on operational requirements.
Frame
The frame is the structural backbone of the conveyor system. It supports all other components, providing stability and alignment.
Function:
- Support: The frame holds the belt, pulleys, rollers, and motor in place, ensuring they remain aligned and function properly.
- Structure: It provides the necessary structural integrity to withstand the weight and movement of the conveyor system.
Belt Tensioner
The belt tensioner is a device used to adjust and maintain the tension of the conveyor belt. Proper tension is crucial for preventing slippage and ensuring smooth operation.
Function:
- Tension Adjustment: The tensioner allows operators to adjust the belt tension to the optimal level for efficient operation.
- Belt Longevity: Proper tensioning helps prevent excessive wear and tear on the belt, extending its lifespan.
Sensors and Control Systems
Modern conveyor systems often incorporate sensors and control systems to enhance automation and efficiency.
Function:
- Monitoring: Sensors monitor various parameters, such as belt speed, load weight, and alignment, providing real-time data for system control.
- Automation: Control systems automate the operation of the conveyor, adjusting speed, starting, and stopping the belt as needed.

Maintenance Tips for General Conveyor Belt Parts
Proper maintenance of the different parts of a general conveyor belt system is essential for ensuring longevity, efficiency, and safety. This section provides comprehensive advice on maintaining various conveyor belt parts, including cleaning, lubrication, and regular inspections.
Belt Maintenance
Cleaning:
- Regular Cleaning: Keep the belt clean by removing debris, dirt, and any accumulated materials. Use appropriate cleaning agents and tools based on the belt material.
- Preventive Measures: Install scrapers and brushes to continuously clean the belt during operation, reducing the need for manual cleaning.
Inspection:
- Visual Inspection: Regularly inspect the belt for signs of wear, tears, cracks, and fraying. Address any issues promptly to prevent further damage.
- Thickness Check: Measure the belt thickness periodically to monitor wear and determine when replacement is needed.
Pulley Maintenance
Cleaning:
- Remove Build-Up: Clean the pulleys regularly to remove any material build-up that can cause belt slippage or misalignment.
- Surface Inspection: Check for signs of wear or damage on the pulley surface and address them promptly.
Lubrication:
- Bearings: Lubricate the pulley bearings as per the manufacturer’s recommendations to ensure smooth operation and prevent overheating.
Roller Maintenance
Cleaning:
- Debris Removal: Clean the rollers regularly to remove any debris that may affect their rotation and cause belt misalignment.
- Inspection: Inspect rollers for signs of wear, dents, or damage. Replace any damaged rollers to maintain proper belt tracking.
Lubrication:
- Regular Lubrication: Lubricate roller bearings to ensure they rotate smoothly and reduce friction.
Motor Maintenance
Inspection:
- Regular Checks: Inspect the motor for signs of overheating, unusual noise, or vibration. Address any issues immediately to prevent motor failure.
- Electrical Connections: Ensure all electrical connections are secure and free from corrosion.
Lubrication:
- Bearings: Lubricate motor bearings as specified by the manufacturer to ensure efficient operation.
Frame Maintenance
Cleaning:
- Dust and Debris: Keep the frame clean from dust and debris to prevent corrosion and maintain structural integrity.
- Rust Prevention: Apply anti-rust treatments if the frame is made of metal and exposed to corrosive environments.
Inspection:
- Structural Integrity: Regularly inspect the frame for signs of damage or wear. Ensure all bolts and fasteners are tight and secure.
Belt Tensioner Maintenance
Adjustment:
- Regular Adjustment: Check and adjust the belt tension regularly to ensure it remains at the optimal level for efficient operation.
- Alignment: Ensure the tensioner is properly aligned to prevent belt misalignment and uneven wear.
Lubrication:
- Moving Parts: Lubricate moving parts of the tensioner to ensure smooth operation and ease of adjustment.
Sensors and Control Systems Maintenance
Inspection:
- Sensor Functionality: Regularly test sensors to ensure they are functioning correctly and providing accurate data.
- Control Systems: Check the control systems for any software updates or calibration needs.
Cleaning:
- Sensor Cleaning: Keep sensors clean from dust and debris to maintain accurate readings.
- Control Panel: Clean the control panel regularly to prevent dust accumulation and ensure all buttons and displays are visible.
Common Issues with General Conveyor Belt Parts and How to Fix Them
Despite regular maintenance, issues can still arise with general conveyor belt parts. This section identifies common problems and provides solutions and preventative measures to address these issues.
Belt Issues
Problem: Belt Slippage
- Cause: Belt slippage can occur due to insufficient tension, worn pulleys, or excessive load.
- Solution: Adjust the belt tension using the tensioner. Inspect and replace worn pulleys. Ensure the load is within the conveyor’s capacity.
Problem: Belt Misalignment
- Cause: Misalignment can be caused by uneven load distribution, improper installation, or worn rollers.
- Solution: Realign the belt by adjusting the rollers and pulleys. Ensure even load distribution and inspect rollers for wear.
Pulley Issues
Problem: Pulley Wear
- Cause: Pulleys can wear out due to constant friction with the belt, debris build-up, or improper alignment.
- Solution: Regularly clean pulleys and remove debris. Replace worn pulleys and ensure proper alignment during installation.
Problem: Pulley Slippage
- Cause: Slippage can occur if the pulley surface is smooth or the belt is not properly tensioned.
- Solution: Increase belt tension and ensure the pulley surface has adequate grip. Replace smooth or worn pulleys.
Roller Issues
Problem: Roller Jamming
- Cause: Rollers can jam due to debris build-up, bearing failure, or misalignment.
- Solution: Clean rollers regularly and remove debris. Lubricate and replace bearings as needed. Ensure rollers are aligned correctly.
Problem: Roller Wear
- Cause: Rollers wear out due to constant use and friction with the belt.
- Solution: Inspect rollers regularly and replace worn or damaged rollers promptly to maintain smooth operation.
Motor Issues
Problem: Overheating
- Cause: Motors can overheat due to overloading, poor ventilation, or electrical faults.
- Solution: Ensure proper ventilation around the motor. Avoid overloading the conveyor system. Check and maintain electrical connections.
Problem: Unusual Noise
- Cause: Unusual noise can indicate bearing failure, loose components, or electrical issues.
- Solution: Inspect and lubricate motor bearings. Tighten any loose components. Address electrical issues promptly.
Frame Issues
Problem: Structural Damage
- Cause: Structural damage can occur due to heavy loads, impacts, or corrosion.
- Solution: Inspect the frame regularly for signs of damage. Repair or replace damaged sections. Apply anti-rust treatments as needed.
Problem: Loose Fasteners
- Cause: Fasteners can become loose due to vibration and regular use.
- Solution: Regularly check and tighten all fasteners to maintain structural integrity.
Belt Tensioner Issues
Problem: Incorrect Tension
- Cause: Incorrect belt tension can result from improper adjustment or worn tensioner components.
- Solution: Adjust the belt tension to the optimal level. Inspect and replace worn tensioner parts.
Sensor and Control Systems Issues
Problem: Inaccurate Readings
- Cause: Sensors can provide inaccurate readings due to dirt accumulation, misalignment, or malfunction.
- Solution: Clean sensors regularly and ensure they are properly aligned. Replace malfunctioning sensors.
Problem: Control System Errors
- Cause: Errors in the control system can arise from software glitches or hardware malfunctions.
- Solution: Update control system software regularly. Inspect and replace faulty hardware components.
By understanding the key parts of a general conveyor belt system, maintaining them properly, and addressing common issues promptly, companies can ensure the efficiency, safety, and longevity of their conveyor systems. This proactive approach minimizes downtime, reduces maintenance costs, and optimizes operational performance.

FAQs about General Conveyor Belt
A general purpose conveyor belt is designed for use in a variety of industries and applications where the conveying of bulk materials or packaged goods is required. These belts are typically made from materials that provide a good balance of durability, flexibility, and cost-effectiveness. They are suitable for a wide range of operating conditions, including light to moderate loads, normal operating temperatures, and standard environmental conditions. General purpose conveyor belts are commonly used in industries such as manufacturing, logistics, packaging, and distribution centers. They are ideal for transporting items such as boxes, bags, and other goods across short to medium distances within a facility.
There are several types of conveyor belts used in industrial applications, but three common types include:
Flat Belt Conveyors: These are the most widely used type of conveyor belts. They consist of a flat, continuous belt made from materials like fabric, rubber, or plastic. Flat belt conveyors are ideal for transporting small to medium-sized items, including boxes, bags, and loose products, in various industries such as manufacturing and distribution.
Modular Belt Conveyors: These belts are made from interlocking plastic modules, creating a highly flexible and durable conveyor system. Modular belt conveyors are excellent for applications that require frequent cleaning and maintenance, as they are easy to disassemble and reassemble. They are commonly used in the food and beverage industry, as well as in packaging and pharmaceuticals.
Cleated Belt Conveyors: Featuring raised sections or cleats, these belts are designed to prevent materials from sliding backward on inclines. Cleated belt conveyors are particularly useful for moving bulk materials, such as grains, sand, or gravel, up steep inclines. They are often found in agricultural, mining, and construction industries where transporting materials on an incline is necessary.
The basic concept of a conveyor belt involves a continuous loop of material, usually made of rubber, fabric, or metal, that is driven by pulleys or motors. The belt moves items from one point to another, facilitating the transportation of goods and materials within a facility. Key components of a conveyor belt system include:
Belt: The continuous loop that carries the items.
Pulleys: The wheels that drive and support the belt, typically including a drive pulley and an idler pulley.
Frame: The structure that supports the belt and pulleys.
Motor: The power source that drives the belt, often using electric or hydraulic power.
Conveyor belts can vary in length, width, and capacity, depending on the application. They are designed to handle specific types of loads and environmental conditions, making them a versatile and essential component in many industrial processes.
The most common conveyor belt system is the flat belt conveyor system. This type of conveyor belt is widely used across various industries due to its simplicity, versatility, and cost-effectiveness. Flat belt conveyors consist of a continuous loop of material, typically made from fabric, rubber, or plastic, that moves over a series of pulleys. They are ideal for transporting a wide range of items, including boxes, packages, and bulk materials, over short to medium distances.
Flat belt conveyors are popular in industries such as manufacturing, logistics, warehousing, and packaging. They are used to move products through different stages of production, assembly, or distribution processes. The ease of installation, maintenance, and customization makes flat belt conveyor systems a preferred choice for many businesses looking to improve their material handling efficiency. Additionally, these systems can be equipped with various accessories, such as side guards, cleats, and sensors, to enhance their functionality and adapt to specific operational needs.
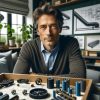
Jordan Smith, a seasoned professional with over 20 years of experience in the conveyor system industry. Jordan’s expertise lies in providing comprehensive solutions for conveyor rollers, belts, and accessories, catering to a wide range of industrial needs. From initial design and configuration to installation and meticulous troubleshooting, Jordan is adept at handling all aspects of conveyor system management. Whether you’re looking to upgrade your production line with efficient conveyor belts, require custom conveyor rollers for specific operations, or need expert advice on selecting the right conveyor accessories for your facility, Jordan is your reliable consultant. For any inquiries or assistance with conveyor system optimization, Jordan is available to share his wealth of knowledge and experience. Feel free to reach out at any time for professional guidance on all matters related to conveyor rollers, belts, and accessories.