Key Components in Conveyor Idler Traduction Systems
Conveyor idler traduction is a crucial aspect of material handling systems, ensuring smooth and efficient operation. Understanding the translation and interpretation of technical terms related to conveyor idlers helps in maintaining, troubleshooting, and optimizing conveyor systems. Conveyor idlers, which support and guide the belt, play a vital role in reducing wear and tear, minimizing energy consumption, and ensuring the longevity of the conveyor system. Proper traduction of these terms ensures clear communication among engineers, operators, and maintenance personnel, leading to improved productivity and reduced downtime in various industrial applications.
Conveyor Idler Traduction: Safety Considerations
When working with conveyor idlers, safety is paramount to ensure the well-being of personnel and the efficient operation of the system. The following are crucial safety measures to follow during handling, installation, and regular inspections of conveyor idlers.
Proper Handling
Handling conveyor idlers requires meticulous attention to safety protocols to prevent injuries and damage to the equipment. Here are some essential tips for proper handling:
- Use Appropriate Personal Protective Equipment (PPE): Ensure that all personnel involved in handling conveyor idlers wear appropriate PPE, including gloves, safety glasses, steel-toed boots, and high-visibility clothing.
- Manual Handling Techniques: When manually lifting or moving idlers, use correct lifting techniques to avoid back injuries. Always lift with the legs, not the back, and get assistance for heavy or awkward loads.
- Mechanical Aids: Utilize mechanical lifting aids such as hoists, cranes, or forklifts for moving heavy or bulky idlers. Ensure that the equipment is suitable for the weight and size of the idlers being handled.
- Secure Storage: Store idlers in a secure, designated area to prevent them from rolling or falling. Use racks or stands to keep them organized and off the ground.
Installation Safety
The installation of conveyor idlers involves various steps where safety must be prioritized to prevent accidents and ensure the proper functioning of the conveyor system.
- Pre-Installation Inspection: Before installation, conduct a thorough inspection of the idlers to check for any signs of damage or defects. Damaged idlers should not be installed as they can cause operational issues and pose safety hazards.
- Proper Tools and Equipment: Use the appropriate tools and equipment for installing conveyor idlers. Ensure that all tools are in good condition and suitable for the task.
- Secure Mounting: Properly secure idlers to their frames or brackets to prevent them from dislodging during operation. Follow the manufacturer’s guidelines and use the recommended mounting hardware.
- Alignment: Ensure that the idlers are correctly aligned with the conveyor belt. Misalignment can cause uneven wear, increased friction, and potential belt damage.
- Lockout/Tagout (LOTO): Implement lockout/tagout procedures to ensure that the conveyor system is de-energized and cannot be accidentally started during installation.
Regular Inspections
Regular inspections are critical for maintaining the safety and efficiency of conveyor idlers. These inspections help identify and address potential issues before they lead to failures or accidents.
- Visual Inspections: Conduct routine visual inspections to check for signs of wear, misalignment, or damage. Look for indications such as excessive noise, unusual vibrations, or belt tracking issues.
- Wear and Tear: Monitor the wear patterns on the idlers and the conveyor belt. Excessive wear can indicate misalignment or improper loading conditions.
- Lubrication: Ensure that idlers with bearings are properly lubricated according to the manufacturer’s recommendations. Insufficient lubrication can lead to bearing failure and increased friction.
- Cleaning: Keep the idlers and the surrounding area clean from debris and material buildup. Accumulated material can cause blockages and interfere with the smooth operation of the conveyor system.
- Documentation: Maintain detailed records of all inspections, maintenance activities, and any issues identified. This documentation helps track the performance and condition of the idlers over time.
Innovations in Conveyor Idler Traduction Technology
The field of conveyor idler traduction has seen significant advancements in recent years, driven by the need for improved efficiency, reliability, and sustainability in material handling systems. The following are some of the key innovations that are transforming conveyor idler technology.
Advanced Materials
The development of new materials has significantly enhanced the performance and durability of conveyor idlers.
- High-Density Polyethylene (HDPE): HDPE idlers are gaining popularity due to their lightweight, corrosion resistance, and low friction properties. These idlers reduce energy consumption and extend the lifespan of the conveyor belt.
- Composite Materials: Composite idlers combine different materials to achieve a balance of strength, weight, and durability. They are designed to withstand harsh environments and heavy loads while reducing maintenance requirements.
- Ceramic Coatings: Ceramic-coated idlers offer superior wear resistance and low friction. They are particularly useful in abrasive applications where traditional idlers would wear out quickly.
Smart Idlers
The integration of smart technology into conveyor idlers has opened up new possibilities for monitoring and optimizing conveyor systems.
- Sensors and IoT: Smart idlers equipped with sensors can monitor various parameters such as temperature, vibration, and rotational speed. These sensors transmit real-time data to a central control system, enabling predictive maintenance and early detection of issues.
- Remote Monitoring: The Internet of Things (IoT) allows for remote monitoring and control of conveyor idlers. Operators can access real-time information and make adjustments from anywhere, improving responsiveness and reducing downtime.
- Data Analytics: Advanced data analytics can process the vast amount of data collected from smart idlers to identify trends, predict failures, and optimize maintenance schedules.
Energy Efficiency
Innovations aimed at reducing energy consumption are becoming increasingly important in conveyor idler traduction.
- Low-Friction Bearings: The development of low-friction bearings reduces the amount of energy required to rotate the idlers. This results in lower operational costs and decreased environmental impact.
- Optimized Design: Modern idlers are designed with aerodynamic and structural efficiency in mind. This includes streamlined shapes and materials that reduce rolling resistance and energy consumption.
- Regenerative Braking: Some advanced conveyor systems incorporate regenerative braking technology, which captures and reuses the energy generated during braking. This can significantly improve the overall energy efficiency of the system.
Noise Reduction
Reducing noise levels is a key focus area in the development of new conveyor idlers.
- Acoustic Insulation: Idlers with built-in acoustic insulation materials help dampen noise generated by the conveyor system. This is particularly important in noise-sensitive environments such as residential areas or workplaces.
- Vibration Dampening: Innovations in vibration dampening materials and designs help minimize the transmission of vibrations, further reducing noise levels.
- Quiet Bearings: Bearings designed specifically for low-noise operation contribute to a quieter overall system.
Request a quote for the best conveyor rollers here!
Common Challenges in Conveyor Idler Traduction
Despite the advancements in technology, there are still several common challenges that can affect the performance and reliability of conveyor idlers. Understanding these challenges and knowing how to address them is essential for maintaining efficient and trouble-free operations.
Misalignment
Misalignment of conveyor idlers is a frequent issue that can lead to various problems, including uneven wear, increased friction, and belt damage.
- Causes: Misalignment can be caused by improper installation, structural movement, or wear and tear of the conveyor frame.
- Solutions: Regularly inspect and adjust the alignment of the idlers. Use laser alignment tools for precise measurements and corrections. Ensure that the conveyor frame is properly maintained and free from damage.
Excessive Wear
Excessive wear on conveyor idlers can shorten their lifespan and lead to frequent replacements.
- Causes: Wear can be caused by abrasive materials, improper loading, or inadequate lubrication.
- Solutions: Use idlers made from wear-resistant materials such as HDPE or ceramic coatings. Ensure proper loading practices to distribute the weight evenly. Regularly lubricate bearings and monitor wear patterns to address issues early.
Material Buildup
Material buildup on idlers can cause blockages, increased friction, and operational inefficiencies.
- Causes: Buildup occurs when material adheres to the idlers due to moisture, static electricity, or sticky substances.
- Solutions: Implement regular cleaning routines to remove accumulated material. Use anti-stick coatings or materials that repel buildup. Ensure that the conveyor system is designed to minimize material spillage.
Bearing Failure
Bearing failure is a critical issue that can halt conveyor operations and cause significant downtime.
- Causes: Bearing failure can result from insufficient lubrication, contamination, or overloading.
- Solutions: Use high-quality, sealed bearings that are resistant to contamination. Implement a regular lubrication schedule and monitor bearing temperatures and vibrations. Avoid overloading the conveyor system and ensure that it operates within its design capacity.
Belt Tracking Issues
Improper belt tracking can lead to belt damage, increased wear on idlers, and operational disruptions.
- Causes: Belt tracking issues can arise from misaligned idlers, uneven loading, or a damaged conveyor belt.
- Solutions: Regularly inspect and adjust belt tracking. Use tracking devices and sensors to monitor the belt’s position. Ensure that the conveyor belt is in good condition and free from damage.
Noise and Vibration
Excessive noise and vibration can indicate underlying issues and affect the working environment.
- Causes: Noise and vibration can result from misalignment, bearing wear, or structural problems.
- Solutions: Use vibration dampening materials and noise-reducing designs for idlers. Regularly inspect and maintain the conveyor system to identify and address the root causes of noise and vibration.
Environmental Factors
Environmental conditions such as temperature, humidity, and corrosive substances can impact the performance of conveyor idlers.
- Causes: Extreme temperatures, moisture, and corrosive environments can cause material degradation and operational issues.
- Solutions: Choose idlers made from materials that are suitable for the specific environmental conditions. Implement protective measures such as coatings or enclosures to shield idlers from harsh environments. Regularly inspect and maintain the idlers to ensure they are in good condition.
Troubleshooting Tips
Effective troubleshooting can help address these common challenges and ensure the smooth operation of conveyor idlers.
- Systematic Approach: Use a systematic approach to identify and diagnose issues. Start with visual inspections and follow up with more detailed checks as needed.
- Documentation: Keep detailed records of all maintenance activities, inspections, and issues encountered. This documentation can help identify recurring problems and inform future maintenance strategies.
- Training: Ensure that all personnel involved in the operation and maintenance of conveyor idlers are properly trained. This includes understanding the common challenges and knowing how to address them effectively.
- Preventive Maintenance: Implement a preventive maintenance program that includes regular inspections, lubrication, and cleaning. Address potential issues before they lead to failures or operational disruptions.
By understanding and addressing the safety considerations, innovations, and common challenges associated with conveyor idler traduction, companies can improve the efficiency, reliability, and longevity of their material handling systems. This proactive approach not only enhances productivity but also ensures a safer working environment for all personnel involved.
Conveyor Idler Traduction: Key Components
Conveyor idlers play a crucial role in the smooth and efficient operation of conveyor systems. Understanding the key components of conveyor idler traduction is essential for optimizing performance and ensuring the longevity of the system. This section provides an in-depth look at the essential components of conveyor idlers, including rolls, shafts, bearings, and frames, and how they contribute to the overall system.
Rolls
Description and Function
Rolls are the primary component of conveyor idlers. They support the conveyor belt and the material being transported, reducing friction and wear. Rolls are typically cylindrical and rotate around their axes, allowing the belt to move smoothly over them.
Types of Rolls
- Carrying Rolls: Positioned on the carrying side of the conveyor, these rolls support the loaded belt and the material. They are designed to withstand heavy loads and provide stable support.
- Return Rolls: Located on the return side, these rolls support the empty belt as it returns to the loading point. Return rolls are generally lighter and less robust than carrying rolls.
- Impact Rolls: Positioned at loading points, impact rolls are reinforced to absorb the impact of falling material, protecting the belt from damage.
- Troughing Rolls: These rolls are arranged in sets to form a trough shape, supporting the belt in a concave configuration, which helps contain the material.
Materials and Construction
Rolls are made from various materials, including steel, rubber, and composite materials. The choice of material depends on the application and the type of material being transported. High-quality construction ensures durability and reduces the risk of premature failure.
Shafts
Description and Function
Shafts are the central components of rolls, providing the axis around which the rolls rotate. They are critical for maintaining the structural integrity and alignment of the idler rolls.
Materials and Construction
Shafts are typically made from high-strength steel to withstand the stresses and loads imposed during operation. Precision machining ensures proper alignment and smooth rotation, reducing wear on the bearings and rolls.
Bearings
Description and Function
Bearings facilitate the smooth rotation of the rolls around the shafts. They are designed to reduce friction and support the radial and axial loads imposed on the rolls.
Types of Bearings
- Ball Bearings: Commonly used in light to medium-duty applications, ball bearings provide low friction and smooth operation.
- Roller Bearings: Suitable for heavy-duty applications, roller bearings can support higher loads and provide greater durability.
- Sealed Bearings: These bearings are protected from contaminants such as dust and moisture, extending their service life and reducing maintenance requirements.
Maintenance and Lubrication
Proper lubrication is essential for the longevity and performance of bearings. Regular maintenance ensures that the bearings operate smoothly and prevents premature failure.
Frames
Description and Function
Frames provide the structural support for the idler rolls and maintain the alignment of the conveyor system. They are designed to withstand the mechanical stresses imposed by the load and the operating environment.
Types of Frames
- Fixed Frames: These frames are stationary and provide a stable support structure for the idler rolls.
- Adjustable Frames: Designed for applications where the angle or position of the rolls needs to be adjusted, adjustable frames offer flexibility and ease of maintenance.
- Impact Frames: Reinforced to withstand the impact of falling material, impact frames are used at loading points to protect the conveyor belt and rolls.
Materials and Construction
Frames are typically made from steel or aluminum, providing strength and durability. Corrosion-resistant coatings or materials are used in environments with high moisture or corrosive substances to extend the service life of the frames.
Integration of Components
Alignment and Assembly
Proper alignment and assembly of the conveyor idler components are crucial for optimal performance. Misalignment can lead to increased friction, wear, and potential failure of the idler system. Precision assembly ensures that all components work together seamlessly.
Balancing Load Distribution
Balancing the load distribution across the idler rolls is essential for efficient operation. Uneven load distribution can cause excessive wear on certain rolls and bearings, reducing the system’s overall lifespan. Regular inspection and adjustment help maintain balanced load distribution.
Understanding the key components of conveyor idler traduction, including rolls, shafts, bearings, and frames, is essential for optimizing the performance and longevity of conveyor systems. Each component plays a critical role in supporting the belt and material, reducing friction, and maintaining alignment. Proper selection, maintenance, and integration of these components ensure efficient and reliable operation, contributing to the overall productivity of the conveyor system.
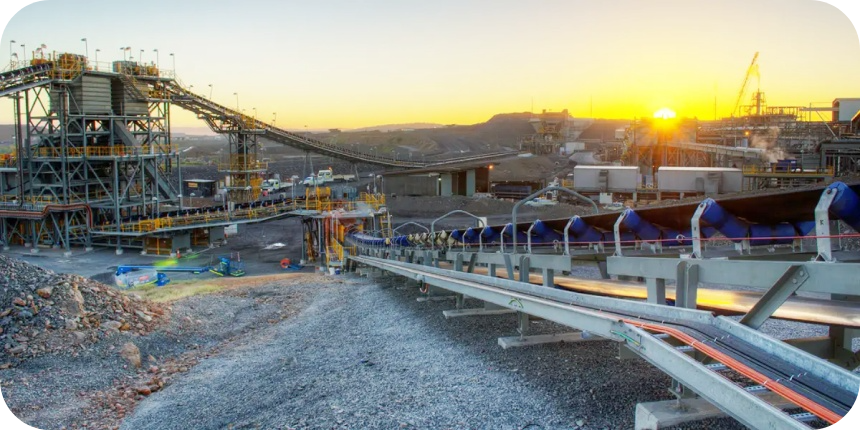
Installation Process for Conveyor Idler Traduction
Proper installation of conveyor idlers is critical for ensuring optimal performance and longevity of the conveyor system. This section provides a step-by-step guide on how to install conveyor idlers in a traduction system, emphasizing the importance of accuracy, alignment, and safety.
Pre-Installation Preparations
1. Gather Tools and Materials
Before beginning the installation process, gather all necessary tools and materials. These may include wrenches, screwdrivers, measuring tape, alignment tools, level, and the idler components (rolls, shafts, bearings, and frames).
2. Inspect Components
Inspect all idler components for any signs of damage or defects. Ensure that the rolls, shafts, bearings, and frames are in good condition and meet the specifications required for the application.
3. Prepare the Installation Site
Clear the installation site of any debris or obstructions. Ensure that the conveyor structure is stable and capable of supporting the idler components. Check the alignment of the conveyor frame to ensure proper installation.
Step-by-Step Installation Guide
1. Position the Frames
Begin by positioning the idler frames at the designated locations along the conveyor structure. Ensure that the frames are spaced according to the manufacturer’s recommendations and the specific requirements of the conveyor system.
2. Secure the Frames
Secure the frames to the conveyor structure using bolts or other appropriate fasteners. Ensure that the frames are level and properly aligned with the conveyor structure. Use a level and alignment tools to check for accuracy.
3. Install the Shafts
Insert the shafts into the frames, ensuring that they are properly seated and aligned. The shafts should be securely fastened to the frames to prevent movement during operation.
4. Mount the Rolls
Mount the rolls onto the shafts, ensuring that they rotate freely. Check for proper alignment and spacing of the rolls to ensure even load distribution and smooth operation. Use alignment tools to verify that the rolls are parallel to the conveyor belt.
5. Install the Bearings
Install the bearings onto the shafts, ensuring that they are properly seated and lubricated. Secure the bearings in place using the appropriate fasteners and ensure that they are aligned with the rolls and frames.
6. Adjust the Tension
Adjust the tension of the conveyor belt to ensure that it is properly seated on the idler rolls. The belt should be tight enough to prevent slippage but not so tight as to cause excessive wear on the rolls and bearings.
Post-Installation Checks
1. Verify Alignment
After installation, verify the alignment of all idler components. Use alignment tools to ensure that the rolls, shafts, bearings, and frames are properly aligned with the conveyor structure and belt. Correct any misalignments to prevent operational issues.
2. Test the System
Run the conveyor system to test the installation. Observe the operation of the idler rolls and listen for any unusual noises that may indicate misalignment or other issues. Check for smooth and efficient movement of the conveyor belt over the idlers.
3. Inspect for Wear and Damage
Inspect the idler components for any signs of wear or damage during the initial test run. Ensure that the bearings are operating smoothly and that the rolls are rotating freely. Address any issues immediately to prevent further damage.
Safety Considerations
1. Follow Manufacturer’s Guidelines
Always follow the manufacturer’s guidelines and recommendations for the installation of conveyor idlers. Adhering to these guidelines ensures that the idlers are installed correctly and safely.
2. Use Personal Protective Equipment (PPE)
Wear appropriate personal protective equipment (PPE) during the installation process. This may include safety glasses, gloves, hard hats, and steel-toed boots to protect against potential hazards.
3. Lockout/Tagout Procedures
Implement lockout/tagout procedures to ensure that the conveyor system is safely de-energized during installation. This prevents accidental startup and reduces the risk of injury.
Common Installation Challenges
1. Misalignment
Misalignment of idler components can lead to increased wear, operational inefficiency, and potential system failure. Regularly check and adjust the alignment to ensure optimal performance.
2. Incorrect Spacing
Incorrect spacing of idler frames and rolls can cause uneven load distribution and increased wear on certain components. Follow the manufacturer’s recommendations for spacing to ensure even load distribution.
3. Inadequate Tension
Inadequate tension on the conveyor belt can lead to slippage and reduced efficiency. Ensure that the belt is properly tensioned during installation and adjust as necessary.
Proper installation of conveyor idlers is essential for ensuring the optimal performance and longevity of the conveyor system. By following a step-by-step installation guide, verifying alignment, and addressing common challenges, operators can ensure that the idlers function efficiently and reliably. Adhering to safety considerations and manufacturer’s guidelines further enhances the success of the installation process, contributing to the overall productivity and efficiency of the conveyor system.
Find custom conveyor roller solutions. Inquire for more info!
Maintenance Tips for Conveyor Idler Traduction
Regular maintenance of conveyor idlers is crucial for preventing breakdowns and extending the service life of the conveyor system. Proper maintenance practices ensure that the idler components operate efficiently and reduce the risk of unexpected failures. This section provides practical advice and best practices for maintaining conveyor idlers in a traduction system.
Routine Inspection
1. Visual Inspection
Conduct regular visual inspections of the conveyor idlers to identify any signs of wear, damage, or misalignment. Look for worn or cracked rolls, loose fasteners, and signs of corrosion on the frames and bearings.
2. Listening for Unusual Noises
Listen for any unusual noises during conveyor operation, such as squeaking, grinding, or rattling. These noises may indicate issues with the bearings, rolls, or alignment and should be addressed promptly.
3. Checking Alignment
Regularly check the alignment of the idler rolls, shafts, and frames. Misalignment can cause uneven wear and reduce the efficiency of the conveyor system. Use alignment tools to ensure that all components are properly aligned.
Lubrication
1. Importance of Proper Lubrication
Proper lubrication is essential for the smooth operation of the bearings and rolls. It reduces friction, prevents wear, and extends the service life of the components.
2. Lubrication Schedule
Establish a regular lubrication schedule based on the manufacturer’s recommendations and the operating conditions of the conveyor system. Lubricate the bearings and other moving parts at regular intervals to ensure optimal performance.
3. Choosing the Right Lubricant
Select the appropriate lubricant for the bearings and other components based on the manufacturer’s recommendations. Consider factors such as operating temperature, load, and environmental conditions when choosing the lubricant.
Cleaning
1. Regular Cleaning
Regularly clean the idler components to remove dust, dirt, and debris that can cause wear and reduce efficiency. Use appropriate cleaning methods and materials to avoid damaging the components.
2. Preventing Material Build-Up
Prevent material build-up on the idler rolls and frames by implementing proper cleaning and maintenance practices. Material build-up can cause misalignment, increased friction, and reduced efficiency.
3. Environmental Considerations
Consider the environmental conditions when cleaning the idler components. For example, in wet or corrosive environments, use corrosion-resistant cleaning agents and methods to protect the components.
Replacement of Worn Components
1. Identifying Worn Components
Identify worn or damaged components through regular inspections. Look for signs of wear, such as grooves, cracks, or flat spots on the rolls, and excessive play or noise in the bearings.
2. Timely Replacement
Replace worn or damaged components promptly to prevent further damage and reduce the risk of unexpected failures. Timely replacement of worn parts ensures the continued efficient operation of the conveyor system.
3. Keeping Spare Parts
Keep a stock of spare parts, such as rolls, bearings, and fasteners, to facilitate quick and easy replacement of worn components. This reduces downtime and ensures that the conveyor system can be quickly returned to operation.
Monitoring and Predictive Maintenance
1. Condition Monitoring
Implement condition monitoring techniques to continuously assess the health and performance of the idler components. Use sensors and monitoring equipment to track parameters such as temperature, vibration, and noise.
2. Predictive Maintenance
Use predictive maintenance strategies to identify potential issues before they lead to failures. Analyze data from condition monitoring equipment to predict when components are likely to fail and schedule maintenance activities accordingly.
3. Data Analysis
Regularly analyze the data collected from condition monitoring equipment to identify trends and patterns. Use this information to optimize maintenance schedules and improve the overall reliability of the conveyor system.
Best Practices for Maintenance
1. Training and Education
Provide training and education for maintenance personnel to ensure they are knowledgeable about the maintenance requirements and best practices for conveyor idlers. Regular training ensures that maintenance activities are performed correctly and efficiently.
2. Documentation
Maintain detailed records of maintenance activities, including inspections, lubrication, cleaning, and component replacements. Documentation helps track the performance and condition of the idler components and informs future maintenance decisions.
3. Continuous Improvement
Continuously evaluate and improve maintenance practices based on feedback and performance data. Implementing continuous improvement strategies helps optimize maintenance activities and enhances the overall efficiency of the conveyor system.
Regular maintenance of conveyor idler traduction is essential for preventing breakdowns and extending the service life of the conveyor system. By conducting routine inspections, ensuring proper lubrication, cleaning the components, and replacing worn parts promptly, operators can maintain the efficiency and reliability of the idler components. Implementing condition monitoring and predictive maintenance strategies further enhances the effectiveness of maintenance activities. Following best practices for maintenance, including training, documentation, and continuous improvement, ensures the long-term success and productivity of the conveyor system.
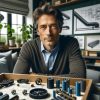
Jordan Smith, a seasoned professional with over 20 years of experience in the conveyor system industry. Jordan’s expertise lies in providing comprehensive solutions for conveyor rollers, belts, and accessories, catering to a wide range of industrial needs. From initial design and configuration to installation and meticulous troubleshooting, Jordan is adept at handling all aspects of conveyor system management. Whether you’re looking to upgrade your production line with efficient conveyor belts, require custom conveyor rollers for specific operations, or need expert advice on selecting the right conveyor accessories for your facility, Jordan is your reliable consultant. For any inquiries or assistance with conveyor system optimization, Jordan is available to share his wealth of knowledge and experience. Feel free to reach out at any time for professional guidance on all matters related to conveyor rollers, belts, and accessories.