HDPE Conveyor Idler: Widely Used
The industrial landscape has witnessed a significant evolution in conveyor systems, with conveyor idlers playing a pivotal role in enhancing operational efficiency and reducing maintenance costs. These components, crucial for supporting and guiding conveyor belts, have evolved from traditional materials to more advanced solutions. HDPE conveyor idler, made from High-Density Polyethylene, is really making waves in the industry. People are starting to notice how durable and corrosion-resistant they are, not to mention they’re lighter than the usual steel rollers. It’s pretty cool how these HDPE rollers are changing the game in conveyor technology. These rollers not only contribute to sustainability but also offer cost-saving benefits, which is always a plus. What’s truly remarkable is their ability to lessen the strain on conveyor systems while simultaneously decreasing the wear and tear on the belts. This translates to extended equipment lifespan and reduced downtime, a crucial factor in industries like mining and food processing where reliability and efficiency are paramount. It’s no wonder HDPE conveyor idlers are becoming more popular – they’re meeting the tough demands of modern industrial work like champs!
What are HDPE Conveyor Idlers?
HDPE conveyor idlers are a modern and innovative type of conveyor roller predominantly used in various material handling applications. These rollers are made from a sturdy material known as High-Density Polyethylene (HDPE), famous for its remarkable strength-to-weight ratio. Their primary role is to offer vital support to the conveyor belt, ensuring the smooth transportation of materials.
Definition and Description of HDPE Conveyor Idlers
- Material: It is made from High-Density Polyethylene, offering high impact resistance.
- Durability: Resistant to wear and tear, extending the lifespan of conveyor systems.
- Environmentally Friendly: HDPE is a recyclable material, making these idlers an eco-friendly option.
- Application: Widely used in industries like mining, agriculture, and logistics for material handling.
Comparison with Traditional Metallic and Steel Conveyor Idlers
Feature | HDPE Conveyor Idlers | Metallic and Steel Conveyor Idlers |
Weight | Lightweight, reducing the load on the conveyor system. | Heavier, increasing the load on the conveyor system. |
Corrosion Resistance | Highly resistant to corrosion and chemicals. | Susceptible to rust and corrosion in certain environments. |
Noise Level | Operate with less noise due to material properties. | Tend to be noisier during operation. |
Maintenance | Require less maintenance and are easier to handle. | Require more frequent maintenance and are heavier to handle. |
Cost | Often more cost-effective in the long run due to durability. | Initially cheaper but may incur higher maintenance costs. |
Key Components of HDPE Conveyor Idlers
- Shell: The outer part made from HDPE, providing the primary structural support.
- Bearings: Precision-engineered to facilitate smooth rotation and reduce friction.
- Sealing System: Designed to protect the bearings from dust, water, and other contaminants.
- Shaft: Typically made from steel or another durable material, connecting the idler to the conveyor framework.
HDPE conveyor idlers offer a modern, efficient, and sustainable solution for conveyor systems, outperforming traditional metallic and steel idlers in many aspects, including durability, maintenance, and environmental impact.
The Size of HDPE Conveyor Idler
The size of HDPE (High-Density Polyethylene) conveyor idlers can vary depending on the specific application and the requirements of the conveyor system. Here are some typical dimensions and considerations:
Diameter
- Common Sizes: HDPE conveyor idlers typically come in diameters ranging from 50mm to 250mm (approximately 2 inches to 10 inches).
- Selection Criteria: The diameter is selected based on the load capacity, belt width, and operational conditions. Larger diameters are used for heavier loads and wider belts to reduce the rotation speed and wear.
Length
- Standard Lengths: The length of the idler can vary widely, commonly ranging from 200mm to 2500mm (approximately 8 inches to 98 inches).
- Belt Width: The idler length should match the width of the conveyor belt. Standard widths of conveyor belts include 500mm, 650mm, 800mm, 1000mm, 1200mm, 1400mm, and up to 2400mm.
Shaft Size
- Diameter: The shaft diameter is typically between 20mm and 40mm (approximately 0.8 inches to 1.6 inches), depending on the load requirements and idler design.
- Length: The shaft length should accommodate the bearing and mounting arrangements and provide stability for the idler.
Wall Thickness
- Standard Thickness: HDPE idlers usually have a wall thickness of 4mm to 10mm (approximately 0.16 inches to 0.39 inches), ensuring durability and resistance to impact and wear.
Bearing Size
- Common Bearings: Bearings used in HDPE idlers typically range from 6204 to 6310 series, depending on the load and speed requirements.
Troughing Angle
- Standard Angles: For troughing idlers, the standard angles are usually 20°, 35°, and 45°, designed to support the conveyor belt and material load effectively.
Customization
- Tailored Sizes: HDPE conveyor idlers can be customized to meet specific needs. Custom sizes can be manufactured based on unique operational requirements, including specific lengths, diameters, and wall thicknesses.
By considering these dimensions and factors, you can select the appropriate size of HDPE conveyor idlers to ensure optimal performance and efficiency in your conveyor system.

10 Advantages of HDPE Conveyor Idlers
Incorporating HDPE conveyor rollers into different industrial conveyor setups offers a range of benefits, largely owing to the exceptional characteristics of High-Density Polyethylene (HDPE). These advantages not only boost the effectiveness and durability of conveyor systems but also play a role in promoting environmentally friendly and economically efficient operations.
High-Density Polyethylene (HDPE) conveyor idlers offer numerous advantages in various industrial applications. Here are ten notable benefits:
Lightweight:
- HDPE idlers are significantly lighter than traditional steel idlers, reducing the overall weight of the conveyor system. This makes installation and maintenance easier and less labor-intensive.
Corrosion Resistance:
- HDPE is highly resistant to corrosion caused by moisture, chemicals, and other environmental factors. This property makes HDPE idlers ideal for use in harsh and corrosive environments, such as mining and chemical processing.
Low Maintenance:
- Due to their resistance to corrosion and wear, HDPE idlers require minimal maintenance compared to steel idlers. This reduces downtime and maintenance costs.
Energy Efficiency:
- The low friction coefficient of HDPE idlers reduces the amount of energy required to move the conveyor belt. This leads to energy savings and lower operational costs.
Noise Reduction:
- HDPE idlers operate more quietly than steel idlers, contributing to a quieter working environment. This is particularly beneficial in industries where noise reduction is important, such as food processing and packaging.
Impact Resistance:
- HDPE idlers have excellent impact resistance, making them durable and capable of withstanding heavy loads and impacts without deforming or breaking.
Non-Stick Surface:
- The smooth, non-stick surface of HDPE idlers prevents the buildup of material on the rollers. This reduces the risk of belt misalignment and improves overall conveyor efficiency.
Extended Lifespan:
- The durability and resistance to wear and tear of HDPE idlers contribute to a longer lifespan compared to traditional steel idlers. This results in fewer replacements and lower long-term costs.
Environmentally Friendly:
- HDPE is a recyclable material, making HDPE idlers an environmentally friendly choice. Additionally, the longer lifespan and reduced maintenance requirements contribute to lower environmental impact over time.
Versatility:
- HDPE idlers can be used in a wide range of applications, from light to heavy-duty operations. Their adaptability makes them suitable for various industries, including mining, construction, agriculture, and food processing.
These advantages make HDPE conveyor idlers an attractive option for industries looking to improve the efficiency, durability, and sustainability of their conveyor systems.Their durability, environmental friendliness, resistance to challenging conditions, low maintenance needs, and lightweight design collectively enhance the efficiency, sustainability, and cost-effectiveness of conveyor operations.
Innovative Features of HDPE Conveyor Idler
HDPE conveyor idlers have incorporated several innovative features that significantly enhance their performance and reliability. These advancements not only improve the lifespan of the idlers but also contribute to more efficient and proactive maintenance practices.
Wear Indicator Technology for Proactive Maintenance
A standout innovation in HDPE conveyor idler is the integration of wear indicator technology. This feature allows for proactive maintenance by providing a clear indication of wear and tear. As the idler wears down, the wear indicator becomes visible, signaling the need for replacement. This technology ensures that maintenance can be scheduled before a complete failure occurs, thus preventing unexpected downtime and maintaining continuous operation efficiency.
Advanced Sealing Arrangements for Bearing Protection
The bearings in HDPE conveyor idlers are protected by advanced sealing arrangements. These seals are carefully engineered to block the entry of contaminants like dust, water, and other particles, which can lead to bearing failure. By maintaining the cleanliness of the bearings and shielding them from external elements, these sealing arrangements prolong the lifespan of the rollers and decrease the need for frequent maintenance.
Friction Welding Process for Enhanced Durability
HDPE conveyor idlers often utilize a friction welding process in their construction. In this method, heat generated through friction is employed to fuse components together, creating an exceptionally robust and long-lasting bond. Through friction welding, the idlers are designed to endure the demands of heavy-duty applications without the concern of components loosening or separating, ultimately boosting the overall durability of the idlers.
Visual Wear Indicators for Easy Maintenance Planning
Some HDPE conveyor idlers, such as PROK HDPE rollers, are equipped with visual wear indicators. These indicators provide a quick and easy way to assess the condition of the idlers without the need for complex measuring tools or equipment. By simply observing the visual indicator, maintenance teams can efficiently plan for idler replacements, ensuring that the conveyor system remains in optimal working condition.
The innovative features of HDPE conveyor idlers, including wear indicator technology, advanced sealing arrangements, friction welding for enhanced durability, and visual wear indicators, collectively contribute to their superior performance. These features enable proactive maintenance, extend the life of the idlers, and ensure that conveyor systems operate efficiently and reliably.

The Reason of HDPE Conveyor Idler Widely Used
1. High economic benefit, can reduce the comprehensive cost of belt conveyor and reduce maintenance man-hours.
2. Long service life, use time is 2-5 times longer than steel stainless steel idler idler, and can reduce belt wear, the belt can extend the life of the belt without running.
3. Corrosion resistance, acid and alkali salts are not corrosive to it.
4. An oxide film is formed on the surface, which does not contact with any substance, and no substance reacts. The grooved idler cleans the belt of contaminants, and the HDPE idler has a large feeding force on the sloped belt, low resistance, and good effect. The double-section idler can reduce the heavy pressure point of the belt on the idler. The idler hollow device can make the belt fall off by itself without sticking to the suction idler, which can extend the service life of the idler.
HDPE (High-Density Polyethylene) conveyor idlers are widely used due to their lightweight nature, corrosion resistance, and low maintenance needs. These idlers are energy-efficient, reducing operational costs through lower friction and quieter operation. Their impact resistance and non-stick surface prevent material buildup and ensure a longer lifespan. Additionally, HDPE idlers are environmentally friendly, recyclable, and versatile, making them suitable for various industries, including mining, construction, agriculture, food processing, and logistics. These benefits collectively make HDPE conveyor idlers a popular choice for efficient and sustainable material handling systems.
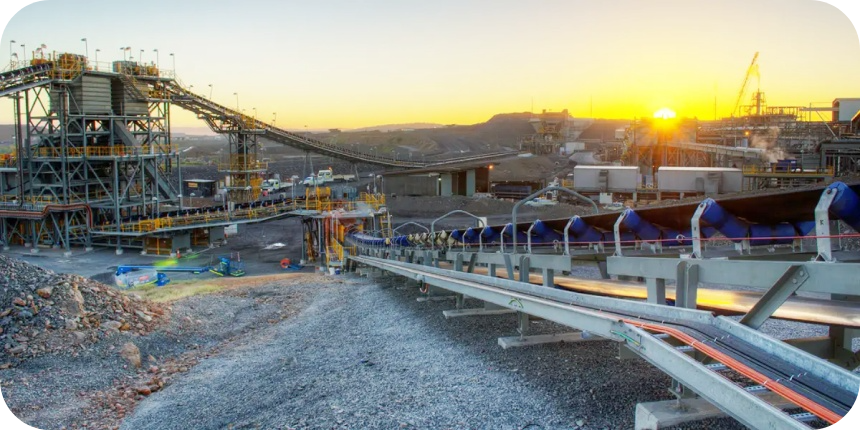
Applications of HDPE Conveyor Idlers
The versatility and robustness of HDPE conveyor idlers make them suitable for a wide range of industrial applications. Their unique properties allow them to perform exceptionally well in various sectors, environments, and specific applications within conveyor systems.
Suitability for Various Industries
- Mining: In the mining industry, HDPE conveyor idlers are highly valued for their durability and resistance to abrasive materials. They withstand the rigors of moving ores and minerals, often in harsh and demanding environments.
- Food Processing: HDPE’s resistance to corrosion and its hygienic qualities make these rollers an excellent choice for the food processing industry. They don’t introduce contaminants into food products and can be effortlessly cleaned, ensuring adherence to food safety regulations.
- Papermaking: In papermaking, HDPE conveyor idlers are used for their low maintenance requirements and resistance to moisture, which is a common challenge in this industry.
Use in Corrosive Environments and Heavy-Duty Applications
HDPE conveyor idlers excel in environments where corrosion is a major concern, such as in chemical processing or outdoor applications exposed to the elements. Their resistance to rust and corrosion extends their lifespan and reduces the need for frequent replacements. Additionally, their robust construction makes them suitable for heavy-duty applications where they need to support large loads or operate under high-stress conditions.
Specific Applications in Conveyor Systems
- Lining: HDPE idlers are used in conveyor systems as lining to provide a smooth and consistent surface for the conveyor belt to move over.
- Food Machinery: In the food industry, these idlers are used in various machinery for handling and processing food products, ensuring gentle and hygienic transport.
- Chemical Industry: HDPE’s chemical resistance makes these idlers suitable for conveyors used in the chemical industry, where they might be exposed to aggressive substances.
HDPE conveyor idlers are a versatile and essential component in various industrial sectors. Their suitability for challenging environments, such as corrosive settings and heavy-duty applications, along with their specific uses in industries like mining, food processing, and papermaking, highlight their adaptability and effectiveness in enhancing the efficiency and reliability of conveyor systems.

Installation and Maintenance Manual for HDPE Conveyor Idlers
Proper installation and maintenance are crucial for maximizing the efficiency and lifespan of HDPE conveyor idlers. This section provides a comprehensive guide on these aspects, ensuring that HDPE conveyor idlers are installed and maintained correctly for optimal performance.
Step-by-Step Guide on Installing HDPE Conveyor Idlers:
1. Preparation: Before installation, ensure that the conveyor frame is level and aligned. Gather all necessary tools and safety equipment.
2. Positioning: Place the HDPE conveyor idler in the designated position on the conveyor frame. Make sure it is oriented correctly, with the idler’s axis perpendicular to the direction of the belt travel.
3. Securing: Attach the idler to the frame using the provided mounting hardware. Tighten all bolts and nuts to the specified torque to ensure a secure fit.
4. Alignment: Check the alignment of the idler with the belt. It should be parallel to the belt path to prevent uneven wear.
5. Testing: Once installed, rotate the idler by hand to ensure it spins freely without any resistance or noise.
Maintenance Tips and Best Practices:
- Regular Inspection: Conduct periodic inspections to check for signs of wear, damage, or misalignment.
- Lubrication: Although HDPE conveyor idlers require minimal lubrication, ensure that any bearings are adequately lubricated as per the manufacturer’s recommendations.
- Cleaning: Keep the idlers clean from debris and dust that can accumulate and cause wear or operational issues.
- Replacement: Replace any idlers that show significant wear or damage immediately to prevent further issues.
Using Visual Wear Indicators and Other Innovative Features:
- Visual Inspection: Regularly check the visual wear indicators if your HDPE conveyor idlers are equipped with them. These indicators will show when the idler is nearing the end of its useful life.
- Monitoring Wear Patterns: Pay attention to the wear patterns on the idlers. Uneven wear can indicate issues with alignment or other mechanical problems.
- Utilizing Advanced Features: If your HDPE conveyor idlers come with additional features like advanced sealing or friction welding, ensure that these components are inspected and maintained as per the guidelines provided by the manufacturer.
Understanding the installation process and adhering to a regular maintenance schedule are key to ensuring the longevity and efficiency of HDPE conveyor idlers. Utilizing the innovative features such as visual wear indicators further aids in proactive maintenance, ensuring that the conveyor system remains in optimal condition.
Contact us for superior conveyor rollers and services.
HDPE Conveyor Idlers for Sale
The market for HDPE conveyor idlers offers a diverse range of models and brands, each designed to meet specific industrial needs. Understanding the available options and key features is crucial for making an informed purchase decision.
Overview of Available HDPE Conveyor Idler Models and Brands:
- Variety of Models: HDPE conveyor idlers come in various models, each suited for different conveyor sizes and load requirements. Common models include standard, impact, and return idlers.
- Brands: Several reputable brands manufacture HDPE conveyor idlers. Notable names in the industry include PROK, Rulmeca, and Conveyoroller, known for their quality and reliability.
- Customization: Many manufacturers offer customizable idlers to suit specific conveyor configurations and operational needs.
Features to Consider When Purchasing HDPE Conveyor Idlers:
- Load Capacity: Consider the maximum load the idlers need to support. Different models have varying load capacities suitable for light, medium, or heavy-duty applications.
- Durability: Look for idlers known for their durability and resistance to wear and tear, especially in harsh industrial environments.
- Maintenance Requirements: Opt for models with low maintenance needs, such as those with advanced sealing systems or self-cleaning features.
- Compatibility: Ensure the idlers are compatible with your existing conveyor system in terms of size, mounting, and operational speed.
Information on Rulmeca Idlers and Rollers, Including Catalogue References:
- Rulmeca Offerings: Rulmeca is renowned for its high-quality idlers and rollers, including HDPE models. They offer a range of idlers suitable for various applications, from mining to food processing.
- Catalogue References: Rulmeca’s catalogues provide detailed information on their product range, including technical specifications, application guides, and installation instructions. These catalogues are valuable resources for understanding the full capabilities of their HDPE idlers.
- Specialized Features: Rulmeca idlers often come with specialized features such as unique sealing systems for enhanced bearing protection and innovative designs for improved belt support and alignment.
In summary, when looking for HDPE conveyor idlers for sale, it’s important to review the range of models and brands available, consider the specific features required for your application, and consult detailed catalogues from reputable manufacturers like Rulmeca. This approach ensures that you select the most suitable HDPE conveyor idlers for your conveyor system’s needs.

Manufacturers and Suppliers
In the realm of conveyor systems, several manufacturers stand out for their quality and innovation, especially in the production of HDPE conveyor idlers. Among these, PROK and Rulmeca are notable for their extensive experience and comprehensive product ranges.
Overview of Leading Manufacturers like PROK and Rulmeca:
- PROK: Known for its pioneering advancements in conveyor technology, PROK has established itself as a leader in the industry. They specialize in producing a wide range of conveyor components, including HDPE conveyor idlers renowned for their durability and efficiency. PROK’s commitment to quality and innovation has made them a go-to choice for many industries.
- Rulmeca: Rulmeca is another key player in the conveyor component market, recognized for its high-quality rollers and idlers. Their products, including HDPE conveyor idlers, are designed to meet the demands of various industrial applications, offering reliability and performance. Rulmeca’s global presence and expertise make them a trusted supplier in the conveyor system sector.
Insights into Their Product Ranges, Including HDPE Rollers and Conveyor Belt Rollers:
- Both PROK and Rulmeca offer a diverse range of conveyor components. Their product lines include HDPE rollers that are lightweight, corrosion-resistant, and suitable for a variety of industrial applications. These rollers are designed to reduce operational costs and enhance the efficiency of conveyor systems.
- In addition to HDPE rollers, their product ranges also encompass a variety of conveyor belt rollers, each tailored to different operational requirements. These include standard rollers, impact rollers, and specialized rollers for specific industrial applications.
Contact Information and How to Request Catalogues or Quotes:
- To learn more about their products or to request a catalogue, interested parties can visit the PROK and Rulmeca websites. These websites offer comprehensive information on their product ranges, along with contact details for direct inquiries.
- For specific queries or to request a quote, both manufacturers provide contact forms on their websites. Customers can also reach out via email or phone, with contact details readily available online. The sales teams at PROK and Rulmeca are equipped to provide detailed information, technical specifications, and pricing to help customers make informed decisions.
In summary, when considering HDPE conveyor idlers, manufacturers like PROK and Rulmeca are excellent starting points due to their industry expertise, wide product ranges, and commitment to quality. Their websites and customer service teams are valuable resources for obtaining detailed product information, catalogues, and quotes.
The exploration of HDPE conveyor idler throughout this discussion underscores their significant benefits and the importance of their role in modern conveyor systems. HDPE conveyor idlers stand out for their exceptional durability, resistance to environmental factors like corrosion and abrasion, and their lightweight design. These attributes not only enhance the efficiency of conveyor systems but also contribute to reduced operational costs and maintenance needs. The environmental friendliness of HDPE, being a recyclable material, further elevates its appeal in industries striving for sustainable practices. The adoption of HDPE conveyor idlers represents a forward-thinking approach in material handling, aligning with the global trend towards more eco-friendly and cost-effective industrial solutions.
Looking ahead, the future of conveyor idler technology appears to be closely intertwined with advancements in materials like HDPE. As industries continue to evolve and demand more efficient, durable, and sustainable components, HDPE conveyor idlers are poised to play a pivotal role. Their adaptability to various industrial environments, coupled with innovative features such as wear indicators and advanced sealing systems, positions them at the forefront of this technological evolution. The ongoing development and refinement of HDPE conveyor idlers will likely continue, driven by the industry’s push for higher performance standards and environmental sustainability. In this dynamic landscape, HDPE conveyor idlers are not just a current solution but a key component of future advancements in conveyor technology.
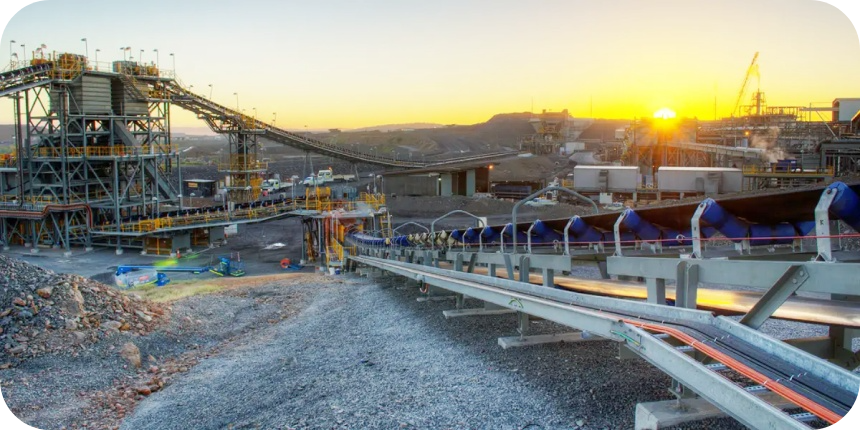
FAQs on HDPE Conveyor Idler
In conveyor systems, you’ll typically find several types of idlers. These include impact idlers, which absorb shock at loading points; return idlers that support the return side of the belt; and troughing idlers, designed to support the load-carrying side. Each type plays a specific role in ensuring smooth conveyor operation.
In a conveyor system, an idler serves as a roller with the primary purpose of providing support to the conveyor belt. These idlers are strategically positioned along the conveyor’s length to facilitate the smooth movement of the belt, minimize wear and tear, and bear the weight of the transported materials.
The dimensions of a conveyor idler can differ, depending on the specific use and the width of the conveyor belt. Typically, idler diameters fall within the range of approximately 4 inches (100mm) to 6 inches (150mm). However, it’s not unusual to come across larger idlers designed for heavy-duty tasks.
Typically, when designing an idler for a conveyor belt system, a cylindrical shape is chosen to ensure the belt moves smoothly. These idlers are affixed to a frame and can be customized to fit different belt widths and support varying load capacities. For example, HDPE idlers are meticulously engineered to provide a balance between lightweight construction and robust durability, effectively withstanding wear and resisting corrosion.
While both idlers and tensioners are found in conveyor systems, they serve different purposes. An idler is used to support the conveyor belt and guide its path. A tensioner, on the other hand, is used to apply tension to the conveyor belt. This tension is crucial for preventing slippage and ensuring the belt operates smoothly. So, while idlers support the belt, tensioners keep it taut.
Idler rollers are made from various materials tailored to specific application needs. Common materials include steel, known for its strength and durability in heavy-duty applications; rubber, which provides traction and noise reduction; HDPE (High-Density Polyethylene), favored for its lightweight, corrosion resistance, and low maintenance in moist and chemical environments; and nylon, which offers a good balance of strength, lightweight properties, and quiet operation. Each material’s unique properties ensure that idler rollers perform optimally in diverse industrial settings, from mining and manufacturing to food processing and electronics.
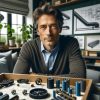
Jordan Smith, a seasoned professional with over 20 years of experience in the conveyor system industry. Jordan’s expertise lies in providing comprehensive solutions for conveyor rollers, belts, and accessories, catering to a wide range of industrial needs. From initial design and configuration to installation and meticulous troubleshooting, Jordan is adept at handling all aspects of conveyor system management. Whether you’re looking to upgrade your production line with efficient conveyor belts, require custom conveyor rollers for specific operations, or need expert advice on selecting the right conveyor accessories for your facility, Jordan is your reliable consultant. For any inquiries or assistance with conveyor system optimization, Jordan is available to share his wealth of knowledge and experience. Feel free to reach out at any time for professional guidance on all matters related to conveyor rollers, belts, and accessories.