A Deep Dive into Conveyor Belt Rubber Thickness Specifications
In this introductory section, we delve into the intricacies of conveyor belt systems, focusing particularly on the critical aspect of rubber thickness. Conveyor belts are the backbone of many industries, facilitating the efficient transport of goods and materials across various stages of production and distribution. The thickness of the rubber layer covering these belts is not a trivial detail; rather, it plays a pivotal role in determining the durability, efficiency, and safety of the conveyor system. Understanding the nuances of conveyor belt rubber thickness is essential for engineers, designers, and operations managers alike, as it directly influences the operational lifespan and performance of these belts. This knowledge is also crucial for making informed decisions regarding maintenance, procurement, and design modifications to enhance the overall productivity and reliability of conveyor belt systems.
What is Conveyor Belt Rubber Thickness
When delving into the specifics of conveyor belt systems, the topic of conveyor belt rubber thickness emerges as a critical factor that directly influences the belt’s durability, flexibility, and overall performance. The thickness of the conveyor belt rubber is not just a random measurement; it is a carefully considered specification that impacts how well the belt will perform in various operational conditions. This dimension is crucial for ensuring the conveyor belt can withstand the physical stresses of carrying materials over long distances, through different environmental conditions, and against various degrees of abrasion.
The rubber coating on a conveyor belt, which is measured in thickness, serves multiple purposes. Primarily, it provides protection to the belt’s carcass against wear and tear, thereby extending the belt’s life. Additionally, it can affect the belt’s grip on the materials it is transporting, which is essential for preventing slippage and ensuring a consistent flow of materials.
Common Thicknesses: 5 Ply and 3 Ply
Conveyor belts are often described in terms of “ply,” a term that refers to the layers of fabric or other materials that constitute the belt’s carcass. Common configurations include 5 ply and 3 ply, which indicate the number of layers embedded within the rubber coating. A 5 ply conveyor belt, with its additional layers, offers enhanced durability and is better suited for heavy-duty applications where the belt is subjected to higher impacts and more significant wear. On the other hand, a 3 ply belt might be more appropriate for lighter-duty tasks, where flexibility and cost-efficiency are prioritized over maximum durability.
The conveyor belt rubber thickness plays a pivotal role in determining the belt’s overall strength and capability. Thicker rubber coatings provide better protection for the ply layers, contribute to a higher resistance against punctures, and allow for a more substantial grip on the conveyed materials. However, it also means increased weight and, potentially, higher energy requirements for the conveyor system.
Conveyor Belt Thickness Chart

Understanding the appropriate conveyor belt rubber thickness for any given application involves consulting a conveyor belt thickness chart. These charts offer guidelines on the recommended thicknesses based on the type of materials being transported, the distance of transportation, and the operational environment of the conveyor system. By referring to a thickness chart, engineers and maintenance personnel can make informed decisions about the suitable rubber thickness needed for their specific conveyor belt applications. These decisions are critical for optimizing the belt’s lifespan, minimizing downtime due to maintenance, and ensuring efficient operation of the conveyor system.
The conveyor belt rubber thickness is a fundamental consideration in the design and selection of conveyor belts. It influences the belt’s durability, operational efficiency, and suitability for specific tasks. By understanding the importance of rubber thickness and utilizing resources like thickness charts, organizations can ensure their conveyor systems are equipped to handle their material transportation needs effectively and efficiently.
Conveyor Belt Rubber Thickness Specification Standards
Navigating through the labyrinth of “conveyor belt specification standards” is a crucial step for engineers and procurement specialists in selecting the most appropriate conveyor belt for their application. These standards are not mere suggestions; they are meticulously developed guidelines that ensure safety, efficiency, and durability in conveyor belt operations. They take into account a myriad of factors, including conveyor belt rubber thickness, to guarantee that the selected belt can withstand the intended loads and environmental conditions.
Overview of Conveyor Belt Specification Standards
Conveyor belt specification standards encompass a wide range of criteria, including material composition, tensile strength, maximum load, and, importantly, rubber thickness. These standards are developed by international and national organizations, such as the International Organization for Standardization (ISO) and the American Society for Testing and Materials (ASTM). They serve as a benchmark for quality and performance, ensuring that all conveyor belts meet a minimum set of requirements before they are deployed in operational environments.
Explanation of EP Conveyor Belt Specification
One common specification referenced in these standards is the EP conveyor belt specification. “EP” stands for “polyester nylon,” where polyester is used in the warp (lengthwise) direction and nylon in the weft (widthwise) direction. This combination provides a high level of strength, durability, and flexibility, making EP belts suitable for a wide range of applications. The specification also includes details on conveyor belt rubber thickness, as this measurement significantly affects the belt’s wear resistance and ability to absorb impact.
Importances of Choosing According to Specification Standards
- Safety: Ensuring the conveyor belt meets specified standards reduces the risk of accidents due to belt failure.
- Compatibility: Standards help in selecting a belt that is compatible with the materials being transported and the environmental conditions.
- Efficiency: A belt chosen according to specification standards is more likely to operate efficiently, without frequent breakdowns.
- Durability: Standards often dictate the minimum conveyor belt rubber thickness, directly impacting the belt’s durability.
- Cost-effectiveness: While upfront costs might be higher, selecting a belt based on standards can lead to lower total cost of ownership due to longer service life and fewer replacements.
- Regulatory Compliance: Many industries are required to comply with specific regulatory standards for safety and environmental impact.
- Predictability: Standards provide a predictable outcome for performance and lifespan of conveyor belts.
- Quality Assurance: Choosing a belt according to specification standards assures a minimum quality level.
- Innovation Encouragement: Standards evolve, promoting the development of new materials and technologies that enhance belt performance.
- Global Trade: Standards facilitate global trade by ensuring compatibility and interoperability between equipment from different manufacturers.
Adhering to “conveyor belt specification standards” is fundamental when it comes to selecting a conveyor belt. This adherence ensures the belt is suited for the intended application in terms of load capacity, speed, and environmental conditions. The conveyor belt rubber thickness plays a significant role in this selection process, as it influences the belt’s wear resistance, impact absorption, and overall durability. By prioritizing these standards, businesses can optimize their conveyor systems for safety, efficiency, and longevity.
Factors Affecting Conveyor Belt Rubber Thickness
The conveyor belt rubber thickness is a pivotal attribute that influences the operational efficacy and lifespan of a conveyor belt. It’s not a figure that is arbitrarily chosen; rather, it’s determined by a variety of factors that ensure the conveyor belt meets the specific needs of the application it’s designed for. Understanding these factors is essential for selecting a conveyor belt that can handle the intended load and environmental conditions without excessive wear or failure.
Factors Influencing Conveyor Belt Rubber Thickness
- Material Characteristics: The type of materials being transported greatly influences the required rubber thickness. Abrasive materials like gravel demand thicker rubber to withstand wear, while non-abrasive materials like packaged goods might require less thickness.
- Load Capacity: The weight and volume of material the conveyor is expected to carry directly impact the rubber thickness. Higher load capacities necessitate thicker rubber to absorb impacts and resist punctures.
- Conveying Distance and Speed: Longer conveying distances and higher speeds can increase the wear on the conveyor belt, requiring a thicker rubber coating to ensure durability and reduce maintenance needs.
- Environmental Conditions: Exposure to harsh environmental conditions such as extreme temperatures, chemicals, or UV light can degrade the conveyor belt. A thicker rubber layer can provide better protection against these elements.
- Impact at Loading Points: The point where material is loaded onto the conveyor can subject the belt to significant stress and impact. A thicker rubber layer helps in absorbing this impact and reducing damage.
- Inclination Angle: Conveyor belts operating at higher inclination angles may need thicker rubber to prevent slide back of the material and to provide additional structural support.
- Operational Lifespan Requirements: The expected operational lifespan of the conveyor belt also dictates the rubber thickness. Belts intended for long-term use will benefit from thicker rubber to endure the cumulative effects of wear and tear.
Influence of These Factors on the Selection of Conveyor Belt Thickness
The interplay of these factors necessitates a holistic approach to selecting conveyor belt rubber thickness. For instance, a conveyor system designed to transport heavy, abrasive materials over a long distance in a chemical plant will require a significantly thicker rubber coating than a belt used for short-distance transportation of agricultural produce. The selection process involves balancing the need for durability and longevity against operational costs and efficiency.
Real-World Examples Applying These Considerations
- Mining Operations: In the abrasive and heavy-load environment of mining, conveyor belts with thick rubber coatings are used to withstand the harsh conditions and heavy materials like ores and rocks.
- Agricultural Sector: Conveyors used in agriculture for transporting grains or vegetables often have moderately thick rubber to balance durability with cost-effectiveness.
- Packaging Industries: In packaging applications, where materials are generally lighter and less abrasive, conveyor belts may have thinner rubber coatings to enhance flexibility and reduce costs.
- Recycling Facilities: Conveyors in recycling plants face a variety of materials, some of which can be abrasive. Thicker rubber is essential to handle the diverse load and prolong the belt’s life.
- Chemical Plants: Conveying chemical materials requires belts with thicker rubber coatings to resist chemical degradation and protect the carcass of the belt.
- Airport Baggage Handling: While the loads are not particularly abrasive, the long operational hours and the need for reliability in airports lead to the use of conveyor belts with rubber thickness designed for durability and minimal maintenance.
These examples illustrate the critical role that conveyor belt rubber thickness plays in tailoring conveyor systems to specific operational needs. By carefully considering these factors, businesses can ensure their conveyor belts are equipped to deliver optimal performance and longevity, tailored to the unique demands of their operations.
Rubber Conveyor Belt Specifications
The realm of conveyor belt rubber thickness intertwines closely with the specifications and grades of rubber used in conveyor belts. These specifications are not just arbitrary classifications; they are indicative of the rubber’s quality, resilience, and suitability for various operational environments. Understanding the different grades of rubber and their implications is essential for selecting a conveyor belt that aligns with the specific requirements of the application, ensuring both efficiency and durability.
Different Grades of Rubber in Conveyor Belts
Rubber grades for conveyor belts are primarily distinguished by their resistance to different environmental stressors such as abrasion, temperature, chemicals, and oil. Common grades include:
- General Purpose (GP): This grade is suitable for a wide range of applications, offering moderate resistance to abrasion and environmental conditions.
- Abrasion Resistant (AR): Designed for transporting abrasive materials, this grade offers enhanced resistance to wear and tear.
- Heat Resistant (HR): HR grades are formulated to withstand high temperatures, making them ideal for applications involving hot materials or exposure to high environmental temperatures.
- Oil Resistant (OR): These belts are essential in environments where oil exposure is a concern, as they resist swelling and degradation.
- Flame Resistant (FR): FR grades are used in applications where there’s a risk of fire or explosion, as they are designed to retard flames and resist ignition.
Explanation of Rubber Grades and Environments
The selection of a specific rubber grade takes into account the conveyor belt rubber thickness and the environment in which the belt will operate. For example, an AR grade might be selected for mining applications where the conveyor belt is exposed to sharp rocks and abrasive materials, necessitating a thicker rubber to ensure longevity. Conversely, a GP grade could suffice for a warehouse conveyor transporting boxed goods, where the demands on the rubber are less severe, allowing for a thinner specification.
Uses of 5 Ply and 4 Ply Conveyor Belts
The ply of a conveyor belt refers to the number of layers of fabric that are encased in the rubber to form the belt’s carcass. The choice between a 5 ply and a 4 ply conveyor belt is influenced by the conveyor belt rubber thickness and the belt’s intended use:
- 5 Ply Conveyor Belts: These belts offer superior strength and durability, making them suitable for heavy-duty applications in industries like mining and construction. The additional ply provides extra protection for the belt’s carcass, making it better equipped to handle high impact loads and abrasive materials. The thicker rubber associated with 5 ply belts also enhances their longevity and resistance to wear.
- 4 Ply Conveyor Belts: While still providing considerable strength, 4 ply belts are more flexible and lighter than their 5 ply counterparts, making them a good choice for medium-duty applications. These belts are often used in agricultural, manufacturing, and packaging industries, where the demands on the conveyor belt involve moderate loads and less abrasive materials. The choice of rubber thickness in 4 ply belts balances durability with the need for flexibility and energy efficiency.
Understanding the specifications related to conveyor belt rubber thickness and the grades of rubber used in conveyor belts is crucial for making informed decisions about which belt to use for a specific application. By carefully considering the operational environment, material characteristics, and the conveyor belt’s intended use, businesses can select a conveyor belt that offers optimal performance, safety, and longevity.
Measurement of Conveyor Belt Rubber Thickness
Accurately measuring the conveyor belt rubber thickness is a fundamental practice in the maintenance and assessment of conveyor belt systems. This measurement is crucial not only during the initial selection and installation of the belt but also throughout its operational life. To carry out these measurements, a specialized tool known as a conveyor belt thickness gauge is employed, ensuring precision and reliability in monitoring the belt’s wear and overall condition.
Description of Conveyor Belt Thickness Gauge
A conveyor belt thickness gauge is a device specifically designed to measure the thickness of the rubber on a conveyor belt without causing damage to the belt itself. This tool can vary in complexity from simple manual calipers to more advanced electronic measuring devices. The gauge works by applying a consistent pressure to the belt surface, allowing for a measurement that factors out any surface irregularities or deformations, providing a true reading of the rubber’s thickness. Regular use of this gauge is essential for effective conveyor belt management, as it directly influences maintenance decisions and operational adjustments.
Importances of Regular Measurements and Inspections
- Wear and Tear Detection: Regular measurement of conveyor belt rubber thickness helps in detecting wear and tear before it becomes severe, allowing for timely maintenance or replacement actions.
- Performance Optimization: Monitoring thickness variations enables adjustments to be made to conveyor speed, load distribution, and other operational parameters to maintain optimal performance levels.
- Spillage Prevention: Thinning of the belt can lead to increased spillage due to reduced troughability. Early detection and correction can prevent material loss and environmental contamination.
- Safety Improvements: A conveyor belt that is wearing unevenly or has become too thin can pose safety risks, such as the potential for sudden failures. Regular inspections ensure that these risks are mitigated.
- Cost Management: By preventing catastrophic failures and optimizing belt life, regular thickness measurements can significantly reduce operational costs associated with unplanned downtime and extensive repairs.
- Lifecycle Extension: Understanding wear patterns and thickness reduction over time allows for more accurate lifecycle planning, extending the useful life of the conveyor belt through better management and maintenance.
- Quality Assurance: Regular inspections and measurements ensure that the conveyor belt continues to meet the required specifications for its intended use, maintaining the quality and consistency of the transported material.
- Regulatory Compliance: In some industries, maintaining certain standards for conveyor belt conditions is not just best practice but a regulatory requirement. Regular measurements ensure compliance with these standards, avoiding potential legal and financial penalties.
The measurement of conveyor belt rubber thickness is a critical aspect of conveyor belt management. Utilizing a conveyor belt thickness gauge for regular inspections ensures that the belt remains in optimal condition, enhancing safety, performance, and cost-efficiency. These practices are integral to the successful operation of any conveyor belt system, highlighting the importance of precision and regularity in maintenance routines.
Conveyor Belt Rubber Thickness In The Industry
The conveyor belt rubber thickness is a paramount consideration across a wide array of industries, playing a vital role in determining the functionality, safety, and longevity of conveyor systems. Each industry presents unique demands on conveyor belts, necessitating specific thicknesses to handle the operational requirements efficiently and safely. Here, we explore ten different applications of conveyor belt thickness across various industries, alongside specific scenarios that underscore the importance of selecting the proper thickness for both function and safety.
Different Applications of Conveyor Belt Thickness in Industries
- Mining and Quarrying: Heavy-duty conveyor belts with thick rubber coatings are essential for transporting abrasive materials such as ores and rocks. The thickness ensures resistance to cuts, abrasions, and punctures, prolonging the belt’s life under extreme conditions.
- Agriculture: Belts with moderate thickness are used for transporting grain, vegetables, and other agricultural products. The thickness is optimized for durability while ensuring flexibility for various loads and speeds.
- Manufacturing: In the manufacturing sector, conveyor belt thickness varies widely depending on the product being handled. For example, automotive parts require thicker belts for weight and durability, whereas electronics components might be transported on thinner, more precise belts.
- Food Processing: Food-grade conveyor belts with specific thicknesses are designed for direct food contact, balancing ease of cleaning with the need for durability against cutting, abrasion, and the harsh cleaning chemicals used in food sanitation.
- Pharmaceuticals: Conveyors in the pharmaceutical industry often use thinner, highly durable belts designed for cleanliness and precision, accommodating the delicate nature of pharmaceutical products.
- Recycling: Thick, durable conveyor belts are crucial in recycling facilities to withstand the impact of varied and unpredictable materials, from metals and plastics to glass and paper.
- Construction: The construction industry utilizes belts of varying thicknesses for different phases of projects, from thick, heavy-duty belts for transporting building materials to thinner belts for removing debris.
- Packaging: Packaging lines use belts with tailored thickness to match the product weight and packaging type, ensuring efficient and safe transport through the packaging process.
- Logistics and Distribution: Conveyor systems in logistics centers require belts with specific thicknesses that can handle the weight and volume of goods being moved, often incorporating thicker belts for heavy or bulky items.
- Airports: Baggage handling systems use durable, moderately thick belts designed to withstand constant use, variable loads, and the need for secure transport of luggage.
Specific Scenarios Illustrating the Importance of Proper Thickness
- Mining Scenario: In a copper mine, the conveyor belt used for transporting extracted ore must have a thickness that can withstand sharp edges and abrasive materials. An inadequately thick belt could lead to premature wear, risking belt failure and potentially hazardous work conditions.
- Food Processing Scenario: A poultry processing plant requires a conveyor belt that balances thickness with hygienic surface properties. Too thick, and the belt may be challenging to clean effectively; too thin, and it may not withstand the processing environment’s demands.
- Airport Baggage Handling Scenario: The chosen conveyor belt must be thick enough to handle the rough handling of baggage over long distances without wear and tear but flexible enough to navigate through tight corners and various elevations within the airport’s baggage handling system.
In each of these scenarios, the conveyor belt rubber thickness is selected based on a comprehensive understanding of the industry’s demands, ensuring that the conveyor belt performs its intended function effectively and safely. Proper selection and application of conveyor belt thickness are critical for operational efficiency, safety, and the economic lifespan of the conveyor system, underscoring the tailored approach needed across different industries.
FAQs about Conveyor Belt Rubber Thickness
The thickness of a conveyor belt can vary significantly depending on its intended use, the materials it will carry, and the conditions under which it will operate. Generally, conveyor belts are designed with a range of thicknesses to accommodate different levels of wear resistance, load capacity, and environmental factors. For instance, lightweight belts used in packaging or food processing industries may have a thickness of around 3 mm to 5 mm, while heavy-duty belts used in mining or construction can be over 15 mm thick. The “conveyor belt rubber thickness” is a critical specification that influences the belt’s durability, performance, and overall ability to fulfill its role in material handling processes. Selecting the appropriate thickness is crucial for ensuring operational efficiency and longevity of the conveyor system.
Conveyor belts are manufactured using various types of rubber, each chosen for its specific properties and suitability for different applications. The most common types of rubber used include:
Natural Rubber (NR): Valued for its elasticity and resistance to tears and abrasions, making it suitable for general-purpose belts.
Styrene-Butadiene Rubber (SBR): Offers good abrasion resistance and is often used in combination with NR for cost-effectiveness.
Nitrile Rubber (NBR): Known for its resistance to oil, fats, and other chemicals, making it ideal for belts used in the chemical and food processing industries.
Ethylene Propylene Diene Monomer (EPDM): Exhibits excellent resistance to weathering, heat, and ozone, suitable for outdoor or high-temperature applications.
Butadiene Rubber (BR): Provides superior cold resistance, beneficial for conveyor belts used in cold environments.
The selection of rubber material is based on the conveyor belt’s intended application, considering factors such as the type of materials being transported, operating temperature range, and exposure to chemicals or oils.
A 2 ply conveyor belt typically refers to a belt with two layers of fabric, textile, or other material embedded in the rubber. The thickness of a 2 ply conveyor belt can range from approximately 3 mm to 6 mm. This variation depends on the specific materials used for the plies and the rubber, the belt’s intended use, and the need for flexibility versus durability. 2 ply belts are generally used in applications requiring a balance of flexibility and strength, such as light to medium load material handling, packaging, and assembly lines. The specific thickness chosen often reflects the operational demands and the need to optimize the belt’s performance and lifespan.
A 4 ply conveyor belt consists of four layers of fabric or material encased in rubber, designed to offer higher strength and durability than 2 or 3 ply belts. The thickness of a 4 ply conveyor belt typically ranges from about 5 mm to 10 mm. This range can vary based on the type of material used for the plies, the rubber’s quality and thickness, and the belt’s intended application. 4 ply belts are often used in more demanding environments where the conveyor will carry heavier loads or be subject to greater wear and tear, such as in mining, construction, and heavy industrial applications. The increased thickness and additional plies provide enhanced protection for the belt’s carcass and improved resistance to impacts, punctures, and abrasions, ensuring a longer operational life under tough conditions.
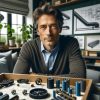
Jordan Smith, a seasoned professional with over 20 years of experience in the conveyor system industry. Jordan’s expertise lies in providing comprehensive solutions for conveyor rollers, belts, and accessories, catering to a wide range of industrial needs. From initial design and configuration to installation and meticulous troubleshooting, Jordan is adept at handling all aspects of conveyor system management. Whether you’re looking to upgrade your production line with efficient conveyor belts, require custom conveyor rollers for specific operations, or need expert advice on selecting the right conveyor accessories for your facility, Jordan is your reliable consultant. For any inquiries or assistance with conveyor system optimization, Jordan is available to share his wealth of knowledge and experience. Feel free to reach out at any time for professional guidance on all matters related to conveyor rollers, belts, and accessories.