Industrial Uses of Conveyor Belt Rubber Matting
Conveyor belt rubber matting is an essential component widely utilized across various industries due to its durability and versatility. This type of matting is crucial in sectors such as mining, agriculture, and manufacturing, where it serves not only as a component in machinery but also plays a significant role in safety and operational efficiency. The uses of conveyor belt rubber matting include floor protection, reducing slip hazards, noise dampening, and providing comfortable standing grounds, particularly in assembly lines.Choosing the right type of conveyor belt rubber matting can significantly impact the efficiency and safety of industrial operations. The appropriate matting helps in protecting conveyor systems from wear and tear, extends the life of the equipment, and can also reduce maintenance costs. It is vital to select matting that is specifically designed for the environment it will be used in, considering factors such as exposure to oils, chemicals, and UV light, which necessitates the selection of a suitable rubber material and thickness. This careful selection helps ensure that the matting performs optimally under varying industrial conditions.
What is Conveyor Belt Rubber Matting
Conveyor belt rubber matting refers to thick, industrial-grade sheets of rubber used primarily on conveyor systems to facilitate, protect, and cushion the items being conveyed. This matting typically enhances grip, reduces item slippage, decreases noise levels, and extends the life of the conveyor belt system. Below are some defining characteristics and examples that further elucidate the utility and diversity of conveyor belt rubber matting:
Characteristics of Conveyor Belt Rubber Matting:
- Durability: Highly durable and capable of withstanding extreme environmental conditions, heavy impacts, and continuous wear and tear.
- Resilience: Possesses a high level of elasticity, which allows it to absorb shocks and resist punctures and tears effectively.
- Anti-Slip Surface: The textured surface provides excellent grip, which helps in preventing accidents by reducing slippage of items.
- Noise Reduction: Acts as a sound barrier by dampening the noise produced by the movement of items on the conveyor.
- Chemical Resistance: Often resistant to chemicals, making it suitable for industries where oils, greases, and other substances are prevalent.
Common Types and Their Properties:
Natural Rubber Matting:
- Properties: Highly flexible and tear-resistant, natural rubber matting is best suited for industries where a supple yet durable matting solution is crucial. It’s not suitable for environments exposed to oils and chemicals.
- Uses: Ideal for agricultural conveyors and general manufacturing plants where chemical exposure is minimal.
Nitrile Rubber Matting (NBR):
- Properties: Excellent resistance to oils, fats, and petroleum-based products; it is also highly durable and maintains flexibility over a wide temperature range.
- Uses: Predominantly used in the automotive industry and recycling plants where oil resistance is essential for the conveyor belt rubber matting.
EPDM Rubber Matting:
- Properties: Outstanding resistance to weathering, UV, and ozone exposure; EPDM maintains its integrity over wide climatic variations.
- Uses: Suitable for outdoor applications such as in construction and roofing conveyors where environmental resistance is needed.
Silicone Rubber Matting:
- Properties: Excellent high and low-temperature resistance, this type of matting is also inert and does not react with most chemicals and solvents.
- Uses: Best used in the pharmaceutical and food processing industries where high-temperature processes are common.
Polyurethane Matting:
- Properties: Extremely abrasion-resistant and capable of handling higher loads; polyurethane also offers good resistance to oils and chemicals.
- Uses: Commonly used in mining and mineral processing industries where abrasive materials are conveyed.
Each type of conveyor belt rubber matting offers unique properties that make it suitable for specific industrial applications and environments. Selecting the right type of matting not only optimizes the functionality of the conveyor system but also contributes significantly to the safety and efficiency of industrial operations. By understanding these types and their properties, industries can better match their specific needs with the most appropriate conveyor belt rubber matting, enhancing overall productivity and safety.
Key Considerations When Selecting Conveyor Belt Rubber Matting
Selecting the right conveyor belt rubber matting is crucial for ensuring operational efficiency, safety, and longevity of your conveyor system. Below are detailed factors and considerations that should guide your selection process:
Critical Factors to Consider:
Durability:
- Importance: The matting must withstand the operational demands without excessive wear and tear.
- Consideration: Look for high tensile strength and good abrasion resistance. Durability will be influenced by the rubber composition and thickness of the matting.
Application Environment:
- Importance: The environment where the matting will be used can greatly affect its performance.
- Consideration: Assess factors such as exposure to chemicals, temperature extremes, and mechanical wear. For example, Nitrile rubber is preferred in oil-exposed environments, whereas EPDM is suitable for outdoor use.
Material Properties:
- Importance: Different materials offer different benefits, such as chemical resistance or thermal stability.
- Consideration: Choose a material that best suits the specific conditions it will face. Silicone rubber, for instance, excels in high-temperature environments.
Thickness and Density:
- Importance: These factors affect the cushioning ability and impact resistance of the matting.
- Consideration: Thicker matting can absorb more impact and is ideal for heavier use, but may not be necessary for lighter applications.
Surface Texture:
- Importance: The texture impacts the grip and safety the matting provides.
- Consideration: Patterns such as ribbed, diamond, or corrugated enhance grip and reduce slip hazards, crucial in wet or high-traffic areas.
Assessing Your Needs Against Market Offerings:
To effectively match your needs with the best conveyor belt rubber matting available, follow these steps:
Identify Operational Requirements:
- Determine the primary function of the matting in your setup—whether for vibration reduction, decreasing slippage, or protecting goods.
Evaluate the Environment:
- Consider the environmental factors such as chemical exposure, temperature range, and physical wear. Each factor can significantly dictate the type of matting required.
Consider Regulatory and Safety Requirements:
- Some industries have strict regulatory standards that dictate specific types of matting. Ensure compliance with OSHA, FDA, or other relevant bodies depending on your industry.
Review Material Options:
- Analyze the properties of different materials. For instance, polyurethane might be preferred for abrasive conditions while silicone might be chosen for temperature extremes.
Test Samples:
- Whenever possible, obtain samples of conveyor belt rubber matting to test under your specific conditions. This can help verify the matting’s performance before making a large investment.
Consult with Experts:
- Speak with manufacturers or specialists who can provide insights and recommendations based on their experience with different materials and applications.
By carefully considering these aspects and assessing your specific needs against what is available on the market, you can select the most appropriate conveyor belt rubber matting. This process not only ensures that you invest in a product that will meet your needs but also optimizes your conveyor system’s efficiency and safety.
Pricing Insights for Conveyor Belt Rubber Matting
Understanding the pricing of conveyor belt rubber matting is crucial for budgeting and cost management in any project involving its use. Below we explore the general pricing trends and the factors that typically influence the costs associated with this versatile material.
General Pricing Trends:
The cost of conveyor belt rubber matting can vary significantly depending on several factors but typically ranges from $5 to $50 per square foot. Prices vary mainly due to the type of rubber, the complexity of the designs, and the specific properties required for the application. The following are insights into how pricing for conveyor belt rubber matting is structured:
- Standard Matting: Basic designs without specialized properties usually cost on the lower end of the spectrum.
- Specialized Matting: Designs that include anti-static properties, food-grade materials, or oil resistance features tend to be priced higher.
Factors Influencing Pricing:
Several key factors affect the pricing of conveyor belt rubber matting; the most impactful are material type, thickness, and overall size. Below, we break down these factors:
- Material Type:
- Different materials are priced differently based on their availability and the production process required to manufacture them. For example, synthetic rubbers like Nitrile are typically more expensive than natural rubber due to their superior oil and chemical resistance.
- Thickness:
- Thicker mats are generally more expensive due to the increased amount of material used. Thickness is often directly correlated with durability and the type of use-cases the matting can handle.
- Size:
- Larger pieces require more material and thus cost more. However, bulk purchasing can often reduce the cost per unit area.
The table below illustrates how these factors might influence the price per square foot of conveyor belt rubber matting:
Material | Thickness (inches) | Size (square feet) | Price per Sq Ft |
---|---|---|---|
Natural Rubber | 0.5 | 10 | $10 |
Nitrile Rubber | 0.5 | 10 | $15 |
EPDM Rubber | 0.75 | 10 | $20 |
Silicone Rubber | 0.5 | 10 | $25 |
Polyurethane | 1 | 10 | $30 |
Evaluating Cost Efficiency:
To ensure cost-effectiveness when purchasing conveyor belt rubber matting, consider the following tips:
- Assess the Total Cost of Ownership: Include considerations for maintenance, durability, and potential downtime due to matting failures.
- Bulk Purchases: Consider larger orders to leverage bulk pricing.
- Custom Orders: Custom sizes might be more expensive per unit area but can reduce waste and the need for additional modifications.
By understanding these pricing insights and considering the total ownership costs, you can make more informed decisions that align with your operational needs and budget constraints when selecting conveyor belt rubber matting. This strategic approach will help optimize both the performance and cost-effectiveness of your conveyor system.
Availability and Sourcing of Conveyor Belt Rubber Matting
When it comes to acquiring conveyor belt rubber matting, understanding the best practices for sourcing can significantly simplify the process. Whether you’re looking for new or used matting, various strategies can ensure you find high-quality materials at a reasonable cost near you.
How to Find Conveyor Belt Rubber Matting Near You:
Local Industrial Suppliers:
- Start by checking with local suppliers who specialize in industrial rubber products. These suppliers often have a variety of conveyor belt rubber matting options and can provide valuable advice based on your specific requirements.
Online Industrial Marketplaces:
- Websites like Grainger, McMaster-Carr, and even Amazon offer extensive listings for conveyor belt rubber matting. These platforms often feature user reviews which can help in assessing the quality and suitability of the matting.
Manufacturer Direct Purchases:
- Consider purchasing directly from manufacturers. Many manufacturers offer customized solutions and may provide a broader range of materials, sizes, and thicknesses than retail suppliers.
Industrial Trade Shows:
- Trade shows are great places to connect with multiple suppliers and manufacturers. These events also often showcase new technologies and materials that might be ideal for your specific conveyor belt needs.
Local Classifieds and Forums:
- Platforms like Craigslist, eBay, or industry-specific forums can be excellent resources for finding both new and used conveyor belt rubber matting in your area.
Tips for Sourcing New and Used Conveyor Belt Rubber Matting:
Verify Quality:
- Always check the quality of the matting, especially if purchasing used items. For new matting, ensure it meets all industry standards and specifications.
Consider Lifespan and Durability:
- Understand the expected lifespan and durability of the rubber matting. Used matting might be less expensive but consider whether it will adequately meet your needs over time.
Assess Compatibility:
- Make sure the matting is compatible with your conveyor system, especially in terms of size, thickness, and material type. This is crucial for maintaining the efficiency and safety of the system.
Look for Warranties or Guarantees:
- When possible, purchase matting that comes with a manufacturer’s warranty or guarantee. This can provide peace of mind and protection against potential defects.
Negotiate Bulk Deals:
- If you require a large amount of matting, try to negotiate bulk pricing with suppliers. Bulk deals can significantly reduce the overall cost.
Environmental Considerations:
- If sustainability is a concern, look for suppliers that offer recycled or eco-friendly rubber matting options. This can help in reducing your environmental impact while still meeting your needs.
Sample Products:
- Request samples from suppliers to physically assess the quality and suitability of the matting before making a large purchase. This can prevent any mismatch between expected and received products.
By following these strategies for finding and sourcing conveyor belt rubber matting, you can ensure that you receive high-quality materials tailored to your specific needs, whether the matting is new or used. Additionally, considering environmental options and negotiating on pricing can further enhance the value and sustainability of your purchase.
Used Conveyor Belt Rubber Matting
Opting for used conveyor belt rubber matting can be a cost-effective and environmentally friendly choice for many businesses. Understanding the benefits and considerations involved will help ensure that you make an informed decision that aligns with your operational needs and sustainability goals.
Benefits of Using Used Conveyor Belt Rubber Matting
Cost Efficiency:
- Primary Benefit: Purchasing used conveyor belt rubber matting typically costs significantly less than buying new materials—often up to 50% cheaper.
- Consideration: The lower cost allows for a reduced initial investment, making it easier to fit into tight budgets without compromising on quality.
Environmental Impact:
- Primary Benefit: Reusing conveyor belt materials helps reduce waste and promotes recycling efforts, which is crucial for sustainability practices.
- Consideration: By opting for used materials, companies contribute to a circular economy, lessening their environmental footprint.
Tested Durability:
- Primary Benefit: Since the matting has already been in use, it has proven its durability and functionality under actual working conditions.
- Consideration: Ensure the used matting still meets your operational requirements; check for any signs of wear that might affect performance.
Quick Availability:
- Primary Benefit: Used conveyor belt rubber matting is often available for immediate purchase and can be easier to source than new, custom-ordered materials.
- Consideration: This is particularly beneficial for urgent needs where waiting for new products could lead to downtime.
Variety of Applications:
- Primary Benefit: Used matting can be repurposed for various uses beyond original conveyor applications, such as floor matting, anti-slip surfaces, or insulation layers.
- Consideration: Inspect the matting to ensure it is appropriate for the new usage, particularly if it will be used in sensitive or high-stress environments.
Considerations When Opting for Used Conveyor Belt Rubber Matting
- Physical Condition: Check for excessive wear, tears, and compatibility with your conveyor system. Matting that has minor wear might still be suitable for less demanding applications.
- Cleanliness: Used matting might need cleaning or treatment before installation to meet hygiene standards, especially in food processing or pharmaceuticals.
- Size Specifications: Verify that the dimensions of the used matting meet your system’s requirements. Custom fitting used matting can be challenging if the sizes are not a close match.
- Supplier Reliability: Source from reputable suppliers who provide quality assurance for their used products to avoid potential issues with poor quality materials.
- Legal and Compliance Issues: Ensure that the used matting complies with all relevant safety and industry standards to avoid legal troubles.
Where to Find Reliable Sources for Used Conveyor Belt Rubber Matting
Industrial Surplus Stores:
- These stores typically stock a wide range of used industrial materials, including conveyor belt rubber matting. They are a good starting point due to their broad selection and ability to inspect materials in person.
Online Marketplaces:
- Websites like eBay, Alibaba, and even specific forums and marketplaces for industrial materials can be excellent sources for finding used matting. These platforms allow you to compare different options and often provide buyer protections.
Local Auctions and Liquidation Sales:
- Businesses undergoing upgrades or closures often sell their equipment through auctions. These events are ideal for finding high-quality industrial materials at reduced prices.
Directly From Facilities:
- Contacting local manufacturing or processing facilities directly can lead to deals on used matting. Facilities looking to upgrade or replace their conveyor systems often sell their old equipment at a discount.
Recycling Centers:
- Some recycling centers specialize in industrial materials and can be a source for used conveyor belt rubber matting. They typically offer materials that have been cleaned and inspected, ensuring they are safe for reuse.
By considering these benefits and careful evaluations, businesses can effectively utilize used conveyor belt rubber matting, achieving cost savings and environmental benefits while maintaining high operational standards. The key is to assess each piece’s condition and suitability for the intended application, ensuring that it aligns with both practical requirements and sustainability objectives.
Heavy Duty Options for Conveyor Belt Rubber Matting
Heavy duty conveyor belt rubber matting is designed to withstand the most demanding of industrial conditions, providing enhanced durability and performance where lesser materials might fail. Below, we explore the applications of heavy duty matting and discuss why some industries are particularly inclined towards these robust options.
Applications of Heavy Duty Conveyor Belt Rubber Matting
Mining and Quarrying:
- Application: In the mining industry, conveyor belts face extreme loads when carrying heavy minerals and rocks.
- Benefit: Heavy duty matting is crucial here to resist cuts, abrasions, and tears while managing sharp, heavy materials that could easily damage standard conveyor belts.
Metal Processing Facilities:
- Application: Facilities dealing with metal smelting or casting use conveyors to move raw materials and finished products.
- Benefit: Heavy duty matting can withstand high temperatures and abrasive materials, making it ideal for environments with hot, sharp, or otherwise challenging loads.
Construction and Demolition:
- Application: Conveyors are used on demolition sites to remove heavy rubble and on construction sites to transport building materials.
- Benefit: The rugged nature of heavy duty matting protects belts from jagged rubble and prolonged exposure to harsh environmental conditions.
Recycling Plants:
- Application: Conveyors in recycling plants sort and transport bulk materials like metals, plastics, and paper.
- Benefit: Heavy duty matting resists the wear and tear from rough recycled materials and exposure to chemicals and moisture.
Agriculture:
- Application: Used for handling large quantities of agricultural products such as grains, feeds, and in some cases, manure.
- Benefit: It supports the weight and bulk of such materials while resisting the corrosive effects of natural elements and organic acids.
Why Industries Prefer Heavy Duty Options
Durability:
- Heavy duty conveyor belt rubber matting is made from materials that are thicker and more resilient than standard matting. This makes them more durable over time, reducing the frequency and costs of replacement.
Cost-Effectiveness:
- Although heavy duty matting may be more expensive upfront, its longevity and lower maintenance requirements provide a better return on investment in the long run, particularly in high-demand environments.
Safety:
- Using appropriate matting reduces the risk of malfunctions and accidents, which is critical in industries where safety is paramount. Heavy duty options ensure that conveyors operate smoothly even under tough conditions.
Efficiency:
- These mats are designed to maintain their structural integrity under high load, which helps in keeping the conveyor systems efficient and reduces downtime caused by material-caused damage or slippages.
Where to Find Heavy Duty Conveyor Belt Rubber Matting
Specialized Industrial Suppliers:
- Companies that specialize in industrial-grade materials often stock heavy duty options tailored for specific conditions like high temperature and abrasion resistance.
Manufacturer Direct Sales:
- Purchasing directly from manufacturers can often allow for customization of matting to exact specifications needed for heavy duty applications.
Online B2B Marketplaces:
- Platforms such as Thomasnet, Alibaba, and others offer listings from multiple suppliers, providing a variety of heavy duty matting options and the ability to compare specifications and prices.
Trade Shows and Expositions:
- Industrial and manufacturing expos often feature the latest advancements in conveyor technology, including heavy duty matting options, and provide direct access to experts.
Consultants and Industry Specialists:
- Consulting with industry specialists can provide insights into the best materials and suppliers for heavy duty needs tailored to specific industry requirements.
Choosing the right heavy duty conveyor belt rubber matting involves understanding the specific demands of your industry and selecting a product that not only withstands those conditions but also improves the efficiency and safety of your operations. By exploring these robust options and knowing where to source them, industries can significantly enhance the operational lifespan and effectiveness of their conveyor systems.
Material Specifications for Conveyor Belt Rubber Matting
Conveyor belt rubber matting is manufactured from various rubber materials, each chosen for its unique properties and suitability for different industrial environments. Below, we provide a detailed look at the common rubber materials used in the production of conveyor belt rubber matting, focusing on SBR (Styrene-Butadiene Rubber), Nitrile Rubber, and other significant materials.
Overview of Rubber Materials Used in Conveyor Belt Rubber Matting
- Styrene-Butadiene Rubber (SBR):
- Properties: SBR is known for its good abrasion resistance and aging stability. It is resistant to many chemicals and temperature changes.
- Applications: Commonly used in general-purpose applications such as in public utilities and standard conveyors not exposed to oil, fats, or greasy materials.
- Nitrile Rubber (NBR):
- Properties: Excellent resistance to oil, solvents, and fats. Nitrile rubber is more durable against such substances compared to other rubbers.
- Applications: Ideal for applications involving oils or solvents, such as in automotive assembly lines or chemical processing plants.
- Natural Rubber (NR):
- Properties: High tensile strength and tear resistance. It is also highly stretchable, making it effective in high-stress applications.
- Applications: Best for abrasive materials or applications requiring a high degree of flexibility and strength, like heavy-duty mining.
- Ethylene Propylene Diene Monomer (EPDM):
- Properties: Excellent resistance to weathering, ozone, UV, and aging. It also performs well in hot and cold temperatures.
- Applications: Suitable for outdoor applications and in the chemical and automotive industries where temperature fluctuations are common.
- Silicone Rubber:
- Properties: Maintains flexibility and mechanical properties over a wide temperature range. It is also resistant to many chemicals and excellent for high and low-temperature applications.
- Applications: Used in food processing, pharmaceuticals, and other health-sensitive environments due to its inert properties.
Comparative Analysis of Rubber Materials
The table below highlights the key properties and common applications of these rubber materials in conveyor belt rubber matting:
Material | Abrasion Resistance | Chemical Resistance | Temperature Range | Typical Applications |
---|---|---|---|---|
SBR | Good | Moderate | -50°C to 100°C | Utilities, light conveying |
Nitrile (NBR) | Excellent | Excellent | -30°C to 120°C | Oil exposure environments, automotive, chemical plants |
Natural Rubber | Excellent | Poor | -60°C to 80°C | Mining, construction, heavy-duty conveying |
EPDM | Fair | Excellent | -50°C to 150°C | Outdoor, automotive, high/low-temperature environments |
Silicone | Fair | Excellent | -55°C to 230°C | Food processing, pharmaceuticals, high-temperature areas |
Selecting the Right Material
When selecting conveyor belt rubber matting, consider the following aspects based on the material specifications:
- Environment Compatibility: Choose a rubber material that can handle the environmental conditions of the application area, such as exposure to chemicals, oils, or extreme temperatures.
- Load and Usage Requirements: Consider the strength and durability needs of the conveyor system. Heavier loads and more abrasive materials will require tougher rubber like natural rubber or NBR.
- Regulatory Compliance: Ensure that the rubber matting complies with all relevant safety and health regulations, especially in food processing or pharmaceutical applications where silicone rubber might be necessary.
- Cost-Effectiveness: While NBR and silicone provide superior performance in their respective recommended areas, they are also more expensive. SBR and natural rubber offer cost-effective solutions for less demanding conditions.
By understanding these material properties and how they compare, industries can make informed decisions on the best type of conveyor belt rubber matting to use, balancing performance requirements with cost considerations. This detailed analysis ensures that the selected matting not only meets the operational demands but also optimizes safety and efficiency across various applications.
Conveyor Belt Rubber Matting Manufacturers
Selecting the right manufacturer for conveyor belt rubber matting is crucial as it impacts the quality, durability, and effectiveness of the matting used in industrial applications. Below, we profile five top manufacturers known for their high-quality products in the conveyor belting industry and provide guidance on choosing the best manufacturer based on specific needs.
Top Manufacturers of Conveyor Belt Rubber Matting
Bridgestone Corporation:
- Distinctive Features: Bridgestone is renowned for its high-performance rubber products and innovation in rubber technology. Their conveyor belts are praised for their durability and high load capacity.
- Specializations: Offers a wide range of rubber matting products, including custom solutions tailored to meet specific industrial needs.
ContiTech AG:
- Distinctive Features: A segment of Continental AG, ContiTech is a leader in technical rubber products and rubber technology. They excel in providing eco-friendly rubber conveyor belts with a focus on durability and environment sustainability.
- Specializations: Known for their high-strength and low-maintenance rubber matting, which is ideal for demanding industrial applications.
Goodyear Rubber Products Inc.:
- Distinctive Features: Goodyear Rubber Products specializes in providing both standard and custom-made conveyor belt solutions that offer superior performance in various applications.
- Specializations: Their products are particularly noted for their resistance to abrasion and the ability to handle extreme temperatures, making them suitable for a wide range of industries.
Fenner Dunlop Conveyor Belting:
- Distinctive Features: Fenner Dunlop specializes in conveyor belting for mining and heavy-duty industrial applications. They are well-known for their engineered conveyor solutions tailored to maximally extend belt life.
- Specializations: Their conveyor belts are designed to offer superior resistance to wear and tear, particularly in high-impact loading conditions.
Intralox:
- Distinctive Features: Intralox provides comprehensive conveying solutions including modular plastic belting, which offers unique solutions beyond traditional rubber matting.
- Specializations: Known for their innovative use of modular plastic in conveyor belts, Intralox products are aimed at industries looking for sanitary, easy-to-clean options that reduce maintenance needs.
How to Choose a Manufacturer Based on Your Needs
When selecting a manufacturer for conveyor belt rubber matting, consider the following factors:
Industry Expertise:
- Choose a manufacturer with proven expertise in your specific industry. Manufacturers that specialize in your field will understand the unique challenges and requirements of your applications.
Product Quality:
- Assess the quality of the products by looking at the specifications like tensile strength, abrasion resistance, and temperature tolerance. High-quality materials will ensure longer lifespan and better performance.
Customization Capabilities:
- Depending on your needs, you may require custom solutions. Look for manufacturers that offer customization options that can tailor products to your exact requirements.
Environmental Compliance:
- If sustainability is a concern, select a manufacturer that adheres to environmental regulations and offers eco-friendly products. This is particularly important in industries regulated for environmental impact.
Support Services:
- Comprehensive customer and technical support can significantly enhance the value offered by a manufacturer. Good support services include installation guidance, troubleshooting, and timely response to queries.
Cost:
- While not the only factor, cost is always a consideration. Compare pricing among manufacturers for similar products and services, but ensure you are not compromising quality for price.
Reputation and Reliability:
- Research the manufacturer’s reputation in the market. Reviews, testimonials, and case studies can provide insights into the reliability and integrity of the manufacturer.
By carefully considering these aspects and evaluating the distinctive features and specializations of potential manufacturers, you can choose the right conveyor belt rubber matting manufacturer that not only meets your specific needs but also enhances the efficiency and safety of your operations. This strategic approach ensures a cost-effective and high-performance outcome for your industrial conveying needs.
FAQs About Conveyor Belt Rubber Matting
Conveyor belts are manufactured using several types of rubber, each chosen based on the specific requirements of the application and environment where the belt will be used. The most common types of rubber used include:
Natural Rubber (NR): Known for its excellent tensile strength and elasticity, natural rubber is used in conveyor belts where high levels of durability and flexibility are required. It is particularly effective in handling bulk materials like aggregates and large volumes of goods.
Styrene-Butadiene Rubber (SBR): This synthetic rubber is valued for its abrasion resistance and ability to withstand multiple environmental conditions. It is commonly used in general-purpose belts and in industries where resistance to wear and tear is critical.
Nitrile Rubber (NBR): Excellent for applications involving oils, fats, and other hydrocarbons, Nitrile rubber is used in conveyor belts in the automotive and food processing industries where oil resistance is essential.
Ethylene Propylene Diene Monomer (EPDM): Known for its outstanding resistance to heat, weathering, and ozone, EPDM is used in outdoor conveyor applications or those exposed to harsh weather conditions.
These materials are chosen to ensure optimal performance, durability, and efficiency of conveyor systems across various industries.
Skirt rubber in belt conveyors is used to enhance the sealing between the conveyor belt and the skirt board. This rubber strip plays a crucial role in preventing spillage of materials being transported along the conveyor. Here’s why it’s important:
Prevention of Material Spillage: Skirt rubber helps keep the material on the conveyor belt, especially at transfer points where materials are loaded. This reduces wastage and keeps the surrounding area clean, which is crucial in industries handling bulk materials like mining, agriculture, and recycling.
Reduction of Dust and Particles: By creating a tight seal, skirt rubber minimizes the escape of dust and small particles, important for maintaining air quality and reducing contamination in sensitive environments such as food processing or pharmaceuticals.
Extends Belt Life: By keeping the materials contained, skirt rubber reduces the risk of damage to the edges of the conveyor belt from spillage or rubbing against structural components, thereby extending the belt’s operational life.
Skirt rubber is made from durable, flexible materials such as natural rubber or a blend of synthetic rubbers to ensure it can withstand the abrasion and pressure from the material load.
Conveyor belts can be made from a wide range of materials, each selected for its specific properties and the demands of the application. The most commonly used materials include:
Rubber: Including natural and synthetic varieties like SBR, NBR, and EPDM, rubber is favored for its flexibility, strength, and ability to handle different environmental conditions.
PVC: Polyvinyl chloride is used in light to medium-duty applications where chemical resistance and fire resistance are important. It’s commonly used in food processing, electronics, and other industries where the belt might be exposed to oils or acidic substances.
Metal: Steel or stainless steel belts are used in applications that require high strength, thermal conductivity, and resistance to tears and abrasions, such as in metalworking or foundries.
Fabric: Materials like nylon, polyester, or aramid are used for their lightweight properties and high tensile strength, suitable for various applications across different sectors.
Each material offers specific benefits and is chosen based on factors like load type, environmental conditions, and the desired lifespan of the belt.
Making a rubber conveyor belt involves several key steps that ensure its durability and functionality. The manufacturing process typically includes:
Material Selection: Depending on the application, suitable rubber materials are chosen for the top and bottom covers of the belt. Common choices include natural rubber, SBR, or specialized rubbers like NBR for oil resistance.
Calendaring: The rubber is calendared or pressed into sheets. These sheets form the covers and are later combined with other materials like fabric or metal, which will serve as the reinforcing layer.
Building: The reinforcing layers (fabric or metal) are assembled, and the rubber sheets are placed on top and below these layers. This assembly is carefully arranged to ensure proper alignment and distribution of materials.
Vulcanizing: The assembled belt is then subjected to vulcanization, a curing process that involves heat and pressure. Vulcanization solidifies the structure, enhancing the belt’s strength and elasticity.
Finishing: Finally, the edges of the belt are trimmed, and any finishes such as coatings or textures are applied to enhance performance in specific applications.
This manufacturing process can vary slightly depending on the specific requirements of the conveyor belt to be produced, including its strength
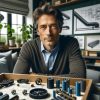
Jordan Smith, a seasoned professional with over 20 years of experience in the conveyor system industry. Jordan’s expertise lies in providing comprehensive solutions for conveyor rollers, belts, and accessories, catering to a wide range of industrial needs. From initial design and configuration to installation and meticulous troubleshooting, Jordan is adept at handling all aspects of conveyor system management. Whether you’re looking to upgrade your production line with efficient conveyor belts, require custom conveyor rollers for specific operations, or need expert advice on selecting the right conveyor accessories for your facility, Jordan is your reliable consultant. For any inquiries or assistance with conveyor system optimization, Jordan is available to share his wealth of knowledge and experience. Feel free to reach out at any time for professional guidance on all matters related to conveyor rollers, belts, and accessories.