Conveyor Belt Design Parameters: Optimal System Performance
Conveyor belt design parameters encompass the essential variables and considerations crucial for the efficient functioning of conveyor systems. These parameters dictate the structural integrity, operational efficiency, and overall performance of conveyor belts in various industries. Understanding and optimizing conveyor belt design parameters are fundamental in ensuring smooth material handling processes, minimizing downtime, and enhancing productivity. By comprehensively evaluating and implementing these parameters, organizations can achieve cost-effective conveyor systems tailored to their specific operational needs.Several key factors influence conveyor belt design parameters, including material characteristics, operational environment, throughput requirements, and safety regulations. Material properties such as size, shape, weight, and abrasiveness impact the selection of belt material, width, and strength. Environmental conditions such as temperature, humidity, and dust levels determine the choice of conveyor components and maintenance schedules. Throughput requirements dictate conveyor speed, capacity, and layout design. Safety regulations mandate the inclusion of emergency stop systems, guarding, and other safety features. Balancing these factors is essential in optimizing conveyor belt design parameters for maximum efficiency and reliability.
Exploring Conveyor Belt Design Parameters through Calculations
Significance of Calculations in Conveyor Belt Design Parameters
Calculations play a pivotal role in the design process of conveyor belts, as they provide essential insights into various parameters influencing system performance. By conducting thorough calculations, engineers can determine critical factors such as belt tension, motor power requirements, conveyor capacity, and load distribution. These calculations ensure that conveyor belt design parameters are optimized for efficient operation, minimal wear and tear, and maximum throughput. Additionally, calculations enable engineers to anticipate potential challenges, such as belt slippage or excessive material spillage, and devise appropriate solutions to mitigate these issues.
Overview of Common Calculations and Their Relevance
Common calculations in conveyor belt design parameters include those related to belt tension, horsepower requirements, conveyor capacity, and material trajectory. Belt tension calculations determine the required tension for proper belt operation and prevent excessive sagging or stretching. Horsepower calculations help determine the motor power necessary to drive the conveyor belt system design efficiently. Conveyor capacity calculations establish the maximum volume of material that the conveyor can handle within a given time frame. Material trajectory calculations predict the trajectory of materials on the conveyor belt, aiding in chute design and material transfer optimization.
Resources for Conveyor Belt Calculations
Various resources are available for conducting conveyor belt calculations, including handbooks, software applications, and online calculators. Conveyor belt design handbooks provide comprehensive guidelines and formulas for performing calculations related to belt tension, horsepower requirements, and conveyor capacity. Additionally, PDF documents and online resources offer valuable insights and tools for engineers to streamline the calculation process and ensure accurate results. These resources serve as invaluable aids in optimizing conveyor belt design parameters and facilitating efficient material handling operations.
Exploring Conveyor Belt Systems for Design Parameters Optimization
Types and Configurations of Conveyor Belt Systems
Conveyor belt systems come in various types and configurations, each tailored to specific applications and operational requirements. Common types include flat belt conveyors, roller conveyors, belt over roller conveyors, and inclined belt conveyors. Flat belt conveyors are suitable for transporting goods on flat surfaces, while roller conveyors utilize rollers to facilitate material movement. Belt over roller conveyors combine the benefits of both belt and roller conveyors, offering versatility and efficiency. Inclined belt conveyors are designed to transport materials at an angle, allowing for elevation changes in material handling processes. Configurations may vary based on factors such as layout constraints, material characteristics, and throughput requirements, with options for straight, curved, or spiral conveyor configurations.
Application-Specific Considerations in Conveyor Belt System Design
When designing conveyor belt systems, it is crucial to consider the specific requirements and challenges of the intended application. Factors such as material type, size, and weight, as well as environmental conditions and space constraints, must be taken into account. For example, in food processing facilities, conveyor belts must meet stringent hygiene standards and regulations to ensure product safety. In manufacturing plants, conveyor systems may need to accommodate rapid production cycles and high throughput rates. By understanding the unique requirements of each application, engineers can tailor conveyor belt systems to optimize performance, reliability, and efficiency while minimizing maintenance and operational costs.
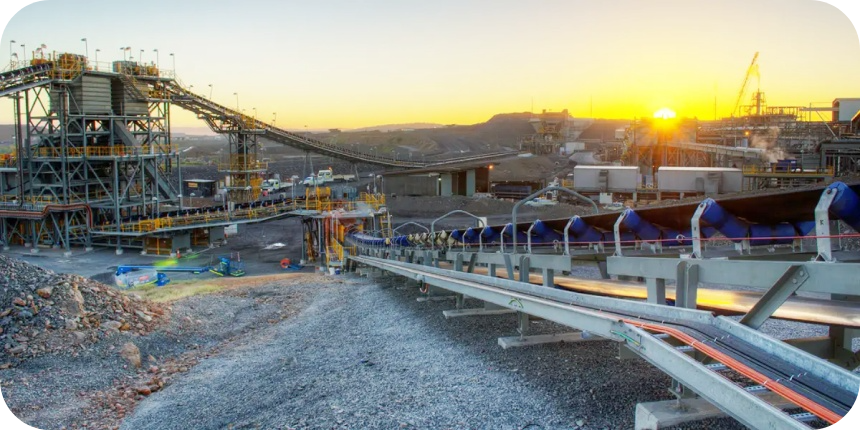
Advantages and Limitations of Different System Setups
Each type of conveyor belt system offers distinct advantages and limitations, depending on the application and operational requirements:
Conveyor Type | Advantages | Limitations |
---|---|---|
Flat Belt Conveyors | Versatile, easy to maintain | Struggles with inclines or declines |
Roller Conveyors | Efficient for heavy-duty applications | May require frequent roller replacement |
Belt Over Roller Conveyors | Combines benefits of flat and roller systems | More complex to install and maintain |
Inclined Belt Conveyors | Ideal for transporting materials up/down inclines | Requires additional safety features to prevent spillage |
Utilizing Conveyor Belt Design Handbook for Conveyor Belt Design Parameters Optimization
Overview of Available Resources and Their Contents
Conveyor belt design handbooks are invaluable resources that provide comprehensive guidance and information on designing conveyor belt systems. These handbooks typically cover a wide range of topics related to conveyor belt design parameters, including belt selection, conveyor system layout, material handling considerations, safety guidelines, and maintenance procedures. They often include detailed diagrams, formulas, tables, and case studies to illustrate key concepts and principles. Additionally, conveyor belt design handbooks may contain information on industry standards, regulations, and best practices, ensuring that engineers have access to the most up-to-date and relevant information when designing conveyor systems.
How to Effectively Use Conveyor Belt Design Handbooks for Optimal Results?
To effectively utilize conveyor belt design handbooks, engineers should follow a systematic approach that encompasses several key steps. Firstly, it is essential to familiarize oneself with the contents of the handbook, including the table of contents, index, and chapter summaries, to identify relevant sections related to the specific design parameters of interest. Next, engineers should carefully study the provided information, paying close attention to explanations, examples, and calculations to gain a thorough understanding of the underlying principles and concepts. Additionally, engineers should utilize the provided formulas, tables, and charts to perform calculations and make informed decisions regarding belt selection, system layout, and operational parameters. Lastly, engineers should continuously reference the handbook throughout the design process to ensure compliance with industry standards, regulations, and best practices, ultimately optimizing conveyor belt design parameters for maximum efficiency, reliability, and safety.
Conveyor Belt Calculator: A Practical Tool for Optimizing Conveyor Belt Design Parameters
Introduction to Conveyor Belt Calculators
Conveyor belt calculators are valuable tools used in the design and optimization of conveyor belt systems. These calculators are software applications or online tools that facilitate the calculation of various parameters essential for conveyor belt design parameters optimization. They provide engineers with quick and accurate solutions for determining factors such as belt tension, horsepower requirements, conveyor capacity, and material trajectory. By inputting relevant data such as belt length, material characteristics, conveyor incline, and operational conditions, engineers can obtain crucial insights into the performance and efficiency of conveyor belt systems.
Benefits of Using Calculators in the Design Process
The utilization of conveyor belt calculators greatly enhances the design process of conveyor systems by offering multiple benefits that streamline and optimize the engineering workflow. Here’s a more detailed discussion, along with a comparative table to illustrate the specific advantages of using calculators compared to traditional manual calculations:
- Efficiency and Time-Saving: Conveyor belt calculators significantly reduce the time required to perform complex calculations. By automating these processes, engineers can focus more on design optimization and less on the arithmetic, leading to faster project turnaround.
- Accuracy and Precision: Manual calculations are prone to human error, which can result in costly mistakes in the design and operation of conveyor systems. Calculators, being programmed with exact formulas, minimize these risks by providing precise and reliable results.
- Instantaneous Results: In dynamic design environments where multiple iterations are common, the ability to quickly evaluate different scenarios is invaluable. Calculators provide instant feedback on changes to design parameters, allowing for rapid assessment and adjustment.
- Comprehensive Analysis: Modern conveyor belt calculators are capable of simulating various real-world conditions and their impact on conveyor performance. This helps in predicting potential operational challenges and in designing systems that are robust under varied conditions.
- Informed Decision-Making: By enabling detailed sensitivity analysis—assessing how changes in one aspect of design affect others—calculators facilitate deeper insights into system behaviors. This supports more informed decision-making, enhancing both the efficiency and the reliability of the conveyor system.
Examples of Calculations for Different Parameters
Conveyor belt calculators can perform calculations for a wide range of parameters relevant to conveyor belt design parameters optimization. For example, engineers can use calculators to determine the required belt tension based on factors such as conveyor length, material weight, and pulley diameter. Similarly, calculators can help calculate the horsepower requirements for driving the conveyor system efficiently, taking into account factors such as conveyor speed, material density, and incline angle. Furthermore, calculators can be used to estimate the conveyor capacity, indicating the maximum volume of material that the conveyor can handle within a given time frame. By utilizing conveyor belt calculators, engineers can efficiently analyze and optimize conveyor belt design parameters to meet specific application requirements and operational goals.
Have questions about our conveyor rollers? Reach out today!
Exploring Conveyor Belt Components for Optimal Conveyor Belt Design Parameters
Overview of Essential Components in Conveyor Belt Systems
Conveyor belt systems consist of various essential components that work together to facilitate the efficient movement of materials. These components include the conveyor belt itself, pulleys, idlers, drives, and support structures. Each component plays a crucial role in ensuring the smooth operation and longevity of the conveyor system. Understanding the functions and importance of these components is essential for optimizing conveyor belt design parameters and achieving optimal performance.
Functions and Importance of Each Component
- Conveyor Belt: The conveyor belt is the primary component responsible for carrying materials from one point to another. It must be durable, flexible, and capable of withstanding the load and environmental conditions.
- Pulleys: Pulleys provide the driving force for the conveyor belt and help maintain its tension. They come in various sizes and designs, including head pulleys, tail pulleys, and bend pulleys.
- Idlers: Idlers support the conveyor belt and help maintain its alignment and tension. They reduce friction and ensure smooth material movement. Various types of idlers, such as troughing idlers, impact idlers, and return idlers, serve specific functions.
- Drives: Drives power the conveyor belt and control its speed and direction. They include motors, gearboxes, and drive pulleys, which must be selected based on the conveyor’s load and operational requirements.
- Support Structures: Support structures provide the framework for the conveyor system, ensuring stability and proper alignment. They include frames, stands, and brackets, which must be robust and adequately designed to withstand the conveyor’s load and environmental conditions.
Considerations in Selecting Components for Specific Applications
When selecting components for conveyor belt systems, engineers must consider various factors to ensure compatibility and optimal performance. These factors include the type and characteristics of the materials being transported, the operational environment (e.g., temperature, humidity, and dust levels), throughput requirements, and safety regulations. Additionally, factors such as maintenance requirements, cost-effectiveness, and ease of installation should also be taken into account. By carefully evaluating these considerations, engineers can select the most suitable components for specific applications, optimizing conveyor belt design parameters and ensuring efficient and reliable material handling operations.
FANQs about Conveyor Belt Design Parameters
When designing a conveyor system, several parameters must be carefully considered to ensure optimal performance. These parameters include:
Material characteristics: Size, shape, weight, and abrasiveness of the materials being transported.
Throughput requirements: Desired rate of material transfer per unit of time.
Operational environment: Factors such as temperature, humidity, and presence of dust or contaminants.
Conveyor layout: Configuration of the conveyor system, including straight runs, curves, inclines, and declines.
Safety regulations: Compliance with industry standards and regulations regarding conveyor system design and operation.
Conveyor belt design involves several key considerations to ensure efficient and reliable operation. These considerations include:
Belt material: Selection of the appropriate material based on factors such as material characteristics, operating conditions, and desired lifespan.
Belt width and thickness: Determination of the optimal belt width and thickness to accommodate the material being transported and prevent belt sagging or stretching.
Belt tension: Proper adjustment of belt tension to prevent slippage and ensure smooth operation.
Pulley and idler selection: Selection of pulleys and idlers based on belt width, load capacity, and alignment requirements.
Splicing and joining methods: Selection of appropriate splicing and joining methods to ensure seamless belt operation and minimize downtime.
Conveyor belts must meet specific requirements to ensure efficient and reliable operation in various applications. These requirements include:
Strength and durability: Ability to withstand the load and stress of material transport without stretching, tearing, or deforming.
Flexibility: Ability to bend and conform to pulley and idler configurations without compromising performance.
Resistance to abrasion and wear: Ability to withstand abrasive materials and environments without significant degradation.
Chemical resistance: Resistance to chemicals, oils, and other substances that may come into contact with the belt during operation.
Temperature tolerance: Ability to operate within a wide range of temperatures without deterioration or loss of performance.
The specification of a conveyor belt includes various parameters that define its characteristics and performance capabilities. These specifications may include:
Belt material: Composition of the belt material, such as rubber, PVC, or fabric.
Belt width and thickness: Dimensions of the belt, typically measured in inches or millimeters.
Tensile strength: Maximum load the belt can withstand without breaking or stretching.
Operating temperature range: Range of temperatures at which the belt can safely and effectively operate.
Surface texture: Texture of the belt surface, such as smooth, textured, or cleated, to facilitate material grip and transport.
Other features: Additional features such as flame resistance, anti-static properties, and special coatings for specific applications.
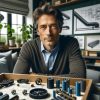
Jordan Smith, a seasoned professional with over 20 years of experience in the conveyor system industry. Jordan’s expertise lies in providing comprehensive solutions for conveyor rollers, belts, and accessories, catering to a wide range of industrial needs. From initial design and configuration to installation and meticulous troubleshooting, Jordan is adept at handling all aspects of conveyor system management. Whether you’re looking to upgrade your production line with efficient conveyor belts, require custom conveyor rollers for specific operations, or need expert advice on selecting the right conveyor accessories for your facility, Jordan is your reliable consultant. For any inquiries or assistance with conveyor system optimization, Jordan is available to share his wealth of knowledge and experience. Feel free to reach out at any time for professional guidance on all matters related to conveyor rollers, belts, and accessories.