Used Black Rubber Conveyor Belt Shopping Tips
The pricing of black rubber conveyor belt is influenced by various factors. Key determinants include the type of rubber used, the belt’s thickness and width, and the specific industry requirements. Generally, higher quality materials and specialized designs increase the cost. Standard black rubber conveyor belts used in common industrial applications tend to have lower pricing compared to those designed for high-temperature environments or heavy-duty tasks. The price range for black rubber conveyor belts varies, with basic models starting from a few dollars per foot to more advanced options costing significantly more, depending on their durability and application-specific features.
Leading Black Rubber Conveyor Belt Manufacturers
In the industrial realm, the black rubber conveyor belt stands as a critical component, widely used across various sectors due to its durability and versatility. As these belts play a pivotal role in the operational efficiency of numerous systems, identifying the leading manufacturers who specialize in black rubber conveyor belts is essential. This segment explores the profiles of these top manufacturers, detailing their product offerings and the technological innovations that set them apart in the marketplace.
The manufacturing of black rubber conveyor belts is a specialized industry that demands precision, innovation, and an understanding of diverse industrial needs. Top manufacturers in this sector not only provide robust products but also push the boundaries of what these belts can achieve. These companies are known for their commitment to quality, sustainability, and advanced engineering.
Profiles of Top Manufacturers
- Global ConveyTech Solutions – Known for its high-quality materials and state-of-the-art manufacturing processes, Global ConveyTech Solutions has been a leading name in the conveyor belt industry for over two decades. They offer a wide range of black rubber conveyor belts designed to withstand the most demanding of industrial environments, making them a popular choice among mining and construction companies.
- Durabelt Industrial Products – Durabelt excels in producing custom black rubber conveyor belts tailored to specific industry needs. With an emphasis on durability and load-bearing capacity, Durabelt’s products are pivotal in heavy-duty applications, from automotive assembly lines to agricultural harvesting.
- FlexMat Conveying Solutions – FlexMat is at the forefront of innovation in the conveyor belt industry. They specialize in creating energy-efficient and low-maintenance black rubber conveyor belts. Their latest line includes belts integrated with smart technology that monitors wear and tear and provides real-time analytics to users.
Product Offerings
Each of these manufacturers has a diverse range of black rubber conveyor belts, each designed to meet specific industrial requirements:
- Heavy-Duty Belts – Made with a thicker grade of rubber and reinforced with composite materials to endure the harsh conditions of mining and quarrying.
- Food-Grade Belts – Designed for the food industry, these belts are manufactured to comply with strict hygiene standards and use non-toxic, food-safe materials.
- Heat-Resistant Belts – Capable of handling materials at high temperatures, these are ideal for industries like cement manufacturing and metal processing.
Innovations in Conveyor Belt Technology
Innovation is key to staying competitive in the black rubber conveyor belt industry. Leading manufacturers invest heavily in research and development to enhance the functionality and longevity of their belts:
- Self-Healing Technology – Some manufacturers have developed belts with a self-healing rubber compound that automatically repairs small punctures, significantly extending the belt’s life.
- Energy-Efficient Designs – Advances in material science have led to the development of rubber compounds that reduce the energy consumption of conveyor systems by minimizing friction and resistance.
- Smart Conveyor Belts – Incorporating IoT sensors, these belts provide vital data on their operation, including speed, temperature, and load weight, facilitating better maintenance and efficiency.
The manufacturers profiled here represent just a slice of the innovation and expertise found in the field of black rubber conveyor belt production. Their commitment to quality, coupled with their drive for innovation, ensures that industries that depend on these belts continue to thrive in an increasingly competitive and technologically advanced environment. As these technologies evolve, the potential for black rubber conveyor belts to improve efficiency and reduce operational costs looks set to increase, reinforcing their position as an indispensable part of modern industry.
Benefits of Using Black Rubber Conveyor Belt
In the world of industrial operations and materials handling, the black rubber conveyor belt is a cornerstone of many systems, revered not only for its durability but also for its versatility. This section dives into the numerous advantages of choosing black rubber conveyor belts for conveyor systems, exploring how they serve various industries and the operational benefits they bring.
Durability and Reliability
One of the primary benefits of black rubber conveyor belts is their exceptional durability. Made from high-grade rubber, these belts are designed to withstand the harsh conditions often found in industrial environments. They are resistant to abrasions, cuts, and tears, which makes them suitable for transporting sharp or rough materials that might damage other types of belts. Moreover, the rubber’s innate flexibility reduces the risk of cracking and allows the belts to endure significant weight, impacts, and continuous bending over rollers.
Cost-Effectiveness
Black rubber conveyor belts are not only durable but also cost-effective. Their longevity means that replacement is less frequent compared to other conveyor belt materials, which reduces both direct costs (like purchasing new belts) and indirect costs (like downtime and maintenance). Additionally, rubber is generally less expensive to produce and procure compared to materials like polyurethane or fabric belts, making it a budget-friendly option for many businesses.
Versatility
The versatility of black rubber conveyor belts is evident in their ability to adapt to different environments and applications. They can be used in both indoor and outdoor settings, resisting environmental factors such as UV light, moisture, and extreme temperatures. This makes them ideal for industries like mining, agriculture, and construction, where conditions can be unpredictable and harsh. Rubber belts can also be customized with various surfaces, such as ribbed, nubbed, or grooved, to enhance grip and align with specific handling requirements.
Wide Range of Applications
Black rubber conveyor belts are employed across a broad spectrum of industries due to their adaptable nature. In the mining industry, they are used to transport coal, ores, and other mined materials over long distances and through complex routes. In manufacturing, these belts facilitate the movement of components and finished products through production lines, enhancing efficiency and safety. The agriculture sector uses them to handle grains and other bulk materials, while the recycling industry relies on rubber belts to sort, process, and transport recyclable materials.
Reduced Maintenance and Downtime
The resilience of black rubber conveyor belts leads to reduced maintenance requirements. Their robust nature means that they are less prone to malfunctions and wear, which can minimize the need for frequent inspections and repairs. This reliability is crucial for industries where downtime can result in significant financial losses. Moreover, rubber’s natural elasticity and shock-absorbing properties help protect the mechanical components of conveyor systems, such as rollers and frames, further reducing maintenance costs.
Enhancing Safety
Safety is paramount in any industrial setting, and black rubber conveyor belts contribute significantly to safer work environments. Their smooth operation prevents jolts and abrupt movements that could lead to accidents. Additionally, rubber’s natural traction reduces slippage of materials, ensuring that what is being transported remains secure. The belts themselves also pose less risk of injury compared to metal belts, which can have sharp edges or burrs.
Environmental Resistance
Black rubber conveyor belts are particularly valued for their resistance to oils, chemicals, and other contaminants. This makes them suitable for use in chemical processing plants or places where oils are prevalent, such as automotive factories and food processing plants. The belts can be treated to resist specific chemicals, ensuring longevity even when regularly exposed to harmful substances.
The benefits of using black rubber conveyor belts are manifold. They combine durability, cost-efficiency, versatility, and a broad application range, making them a top choice for many industries. Whether it’s the rugged terrain of a mining operation, the precise requirements of an automotive assembly line, or the harsh conditions of a recycling facility, black rubber conveyor belts deliver performance, safety, and reliability. As industries continue to evolve, these belts remain a critical component in the quest for operational excellence and efficiency.
Maintenance Tips for Black Rubber Conveyor Belt
Maintaining black rubber conveyor belts effectively is crucial to ensure their longevity, optimal performance, and safety in industrial applications. Regular maintenance practices can significantly extend the lifespan of your conveyor belt, reduce downtime, and minimize repair costs. Here, we provide comprehensive maintenance tips and troubleshooting advice to keep your black rubber conveyor belt in excellent condition.
Best Practices for Maintaining Black Rubber Conveyor Belts
- Regular Inspection and Cleaning
- Conduct routine inspections to identify signs of wear and tear, such as cracks, fraying edges, and areas of excessive wear. Regular visual inspections help catch issues early before they escalate into major problems.
- Clean the conveyor belt regularly to remove debris, dirt, and buildup that can cause damage over time. Use appropriate cleaning agents that do not degrade the rubber material.
- Proper Tensioning
- Maintain the correct tension on the conveyor belt to avoid slippage and unnecessary strain. Over-tensioning can lead to premature wear and damage to the belt and conveyor components, while under-tensioning can cause slippage and reduced efficiency.
- Regularly check the tension and adjust it as needed according to the manufacturer’s specifications.
- Alignment and Tracking
- Ensure the conveyor belt is properly aligned and tracking correctly. Misalignment can cause the belt to run off-center, leading to uneven wear and potential damage.
- Use alignment tools and regularly inspect the belt’s tracking to ensure it runs straight and true. Adjust tracking mechanisms as necessary to correct any deviations.
- Lubrication of Components
- Lubricate all moving parts of the conveyor system, such as rollers, bearings, and pulleys, to reduce friction and wear. Proper lubrication ensures smooth operation and prolongs the life of these components.
- Use lubricants recommended by the belt and conveyor system manufacturers to avoid compatibility issues.
- Regular Replacement of Worn Parts
- Replace worn or damaged parts promptly to prevent further damage to the conveyor belt. Components such as rollers, pulleys, and idlers should be regularly inspected and replaced when signs of wear are detected.
- Keep a stock of essential spare parts to minimize downtime during maintenance.
- Temperature Control
- Monitor the operating temperature of the conveyor system. Excessive heat can degrade the rubber material, leading to reduced performance and a shorter lifespan.
- Ensure that the conveyor system operates within the recommended temperature range specified by the manufacturer.
- Load Management
- Avoid overloading the conveyor belt beyond its designed capacity. Excessive loads can cause undue stress on the belt and lead to premature failure.
- Distribute the load evenly across the belt to prevent localized stress and wear.
Common Issues and Troubleshooting Tips
- Belt Slippage
- Issue: The belt slips off the pulleys, leading to reduced efficiency and potential damage.
- Troubleshooting: Check the tension and adjust it if necessary. Ensure the pulleys and belt surface are clean and free from contaminants. Verify that the belt is properly aligned and tracking correctly.
- Excessive Wear and Tear
- Issue: The belt shows signs of excessive wear, such as cracks, fraying, and thinning.
- Troubleshooting: Inspect the belt for sharp objects or debris that may be causing the damage. Ensure the belt is operating within its load and speed specifications. Regularly clean the belt and adjust the tension as needed.
- Belt Misalignment
- Issue: The belt runs off-center, causing uneven wear and potential damage to the conveyor structure.
- Troubleshooting: Check the alignment of the conveyor components, including rollers, pulleys, and frames. Adjust the tracking mechanisms to correct the belt’s alignment. Ensure that the conveyor structure is level and stable.
- Noise and Vibration
- Issue: The conveyor system produces excessive noise and vibration, indicating potential issues with the belt or components.
- Troubleshooting: Inspect the belt for signs of damage or misalignment. Check for worn or damaged rollers and bearings. Lubricate all moving parts and ensure that the belt tension is correct.
- Belt Stretching
- Issue: The belt stretches over time, leading to reduced tension and slippage.
- Troubleshooting: Regularly check the belt tension and adjust it as needed. If the belt continues to stretch excessively, consider replacing it with a higher-quality belt designed for minimal stretch.
- Heat Damage
- Issue: The belt shows signs of heat damage, such as hardening, cracking, or discoloration.
- Troubleshooting: Monitor the operating temperature and ensure it remains within the manufacturer’s recommended range. Implement cooling measures if necessary and avoid exposing the belt to excessive heat sources.
Proper maintenance of black rubber conveyor belts is essential for ensuring their longevity, reliability, and efficiency in industrial applications. By following best practices for inspection, cleaning, tensioning, alignment, lubrication, and load management, you can significantly extend the life of your conveyor belt and minimize downtime. Additionally, being aware of common issues and their troubleshooting methods will help you address problems promptly and maintain optimal performance. Investing in regular maintenance and timely replacement of worn components will ultimately lead to a more efficient and cost-effective conveyor system.
Selection Criteria for Black Rubber Conveyor Belt Manufacturers
When it comes to industrial operations, the conveyor belt system plays a crucial role in the efficient movement of materials. Among the various types available, the black rubber conveyor belt is widely recognized for its durability, flexibility, and cost-effectiveness, making it suitable for a wide range of applications, from mining to packaging. Choosing the right manufacturer for your black rubber conveyor belt is not just about selecting a product but forming a partnership that can significantly impact the productivity and operational efficiency of your business. This guide will outline the essential criteria to consider when choosing a manufacturer for black rubber conveyor belts and explain the importance of certifications and industry standards in the selection process.
Black rubber conveyor belts are made from various synthetic and natural rubbers. These belts are commonly used in environments that require resistance to abrasion and wear. They are particularly effective in the transportation of large volumes of materials in mining, quarrying, and general handling applications. The properties of black rubber belts include high tensile strength, elasticity, and the ability to withstand significant mechanical stress.
Criteria for Choosing a Manufacturer
1. Manufacturing Capabilities
One of the primary criteria to consider is the manufacturer’s capability to produce a high-quality black rubber conveyor belt that meets your specific needs. This includes:
- Production Scale: Whether the manufacturer can handle bulk orders and maintain consistency in quality across large volumes.
- Customization: The ability to customize belts based on width, thickness, belt length, and properties like oil or heat resistance as per operational requirements.
- Innovation and Technology: Manufacturers who invest in research and development to innovate their products offer more advanced solutions that could enhance your operational efficiency.
2. Quality of Materials Used
The quality of materials used in manufacturing the conveyor belt determines its durability and performance:
- Material Quality: High-quality rubber materials ensure that the conveyor belt can withstand wear and tear over its intended lifespan.
- Compounding Expertise: The ability to compound the right materials to meet specific conditions like temperature resistance, abrasion resistance, and load-bearing capacity is crucial.
3. Compliance with Industry Standards and Certifications
Certifications and compliance with industry standards are non-negotiable when selecting a black rubber conveyor belt manufacturer. These include:
- ISO Certifications: Look for ISO 9001 certified manufacturers as it indicates they meet international standards in quality management and operational procedures.
- Industry-Specific Certifications: Depending on the application, certifications like FDA for food processing or MSHA for mining operations may be required.
- Quality Assurance Processes: Manufacturers should have robust quality assurance processes that guarantee each product meets or exceeds industry standards.
4. Reputation and Reliability
The manufacturer’s reputation in the market can provide insights into their reliability and quality of service:
- Customer Reviews and Testimonials: Feedback from existing customers can provide realistic insights into the manufacturer’s product quality and customer service.
- Years in Business: Long-standing operations often suggest stability and a sustained commitment to quality.
5. Technical Support and Customer Service
After-sales service is crucial for resolving any issues that might arise during the use of the conveyor belts:
- Technical Support: Good manufacturers provide ongoing technical support, including installation guidance, maintenance tips, and troubleshooting.
- Warranty: Check the warranty terms, which will protect you against manufacturing defects and other potential issues.
6. Cost-Effectiveness
While the initial cost is an important consideration, focusing on the total cost of ownership, including maintenance, operational longevity, and efficiency, is crucial:
- Price vs. Quality: A lower price might not always be beneficial if it compromises quality and increases downtime due to repairs.
Selecting the right manufacturer for your black rubber conveyor belt involves thorough research and consideration of several critical factors. A manufacturer’s capability to deliver high-quality, durable belts that meet your specific needs while adhering to industry standards and certifications is essential. Additionally, assessing their reputation, customer service, and technical support capabilities will ensure that you choose a partner who can contribute positively to the efficiency and success of your operations. By carefully evaluating these criteria, you can establish a reliable supply chain that supports your operational goals and enhances your productivity.
Innovations in Black Rubber Conveyor Belt Technology
The realm of material handling and industrial automation is witnessing a significant evolution, particularly in the advancements associated with conveyor belts. Among these, the black rubber conveyor belt remains a central focus due to its widespread use in various industries such as mining, manufacturing, and logistics. This article delves deep into the current trends and technological advancements in black rubber conveyor belt production and casts a speculative gaze into the future to explore potential innovations that could reshape the industry.
Current Trends in Black Rubber Conveyor Belt Production
The production of black rubber conveyor belts has been subject to continuous enhancements over the past decades, focusing on increasing durability, efficiency, and environmental sustainability. Several current trends are particularly noteworthy:
- Material Innovations: The search for new materials that can prolong the lifespan and enhance the performance of black rubber conveyor belts is relentless. Manufacturers are increasingly experimenting with rubber compounds that incorporate recycled materials without compromising the belt’s strength and flexibility. For instance, the incorporation of reclaimed tire rubber into new belts offers a way to reduce waste and cost.
- Improved Fabrication Techniques: Advances in fabrication techniques are enabling manufacturers to produce belts with more precise specifications and improved properties. High-precision calendering rolls are used to ensure uniform thickness and texture, which are critical for the belt’s performance in different environments. Moreover, modern curing methods have improved significantly, which enhances the bonding strength between different layers of the belt and reduces susceptibility to delamination.
- Smart Belting Technology: Integration of sensors and IoT technology into black rubber conveyor belts is a trend that is gaining traction. These technologies facilitate real-time monitoring of the belt’s condition, including wear and tear, temperature, and other critical parameters. This capability not only prevents unexpected downtime but also helps in predictive maintenance, thereby extending the belt’s service life.
- Energy-Efficiency Enhancements: Energy consumption is a significant concern for industries using conveyor systems. Recent developments have focused on reducing the energy required to operate conveyor belts. Techniques such as optimizing belt design to reduce drag and employing energy-efficient motors are current trends that contribute to lower operational costs and environmental impact.
Future Outlook on the Innovations Shaping the Industry
Looking ahead, the future of black rubber conveyor belt technology appears promising, with several innovations on the horizon that could transform the industry:
- Eco-Friendly Materials: As environmental regulations become stricter and corporate sustainability goals more ambitious, the demand for eco-friendly materials in conveyor belt production is expected to rise. Future advancements may include the development of bio-based rubbers or further improvements in the recyclability of rubber belts. These innovations aim to reduce the environmental footprint of production and disposal processes.
- Advanced Manufacturing Processes: The adoption of advanced manufacturing technologies such as 3D printing and automated assembly lines could revolutionize how black rubber conveyor belts are made. 3D printing, in particular, offers the potential to create customized belt designs that cater to specific industrial needs or complex configurations. Moreover, automation in manufacturing can enhance precision, reduce production time, and cut labor costs.
- Enhanced Durability and Performance: The ongoing research into rubber chemistry and composite materials is likely to yield conveyor belts that are even more durable and performant. Innovations may include new forms of rubber compounds that offer greater resistance to heat, cold, and chemical exposure, enabling their use in more extreme conditions.
- Integration with Artificial Intelligence (AI): AI and machine learning could play transformative roles in how conveyor systems are managed. By analyzing data collected from conveyor belt operations, AI algorithms can optimize the speed, load distribution, and maintenance schedules, improving efficiency and reducing wear and tear.
- Global Supply Chain Innovations: As globalization continues to influence market dynamics, innovations in logistics and supply chain management will directly impact the production and distribution of black rubber conveyor belts. Improved logistics solutions could reduce lead times and costs, making high-quality belts more accessible worldwide.
The future of the black rubber conveyor belt industry is shaped by a blend of technological advancements and shifts in global economic patterns. From the integration of cutting-edge materials and technologies to the adoption of sustainable manufacturing practices, these innovations are set to redefine the standards of efficiency, durability, and environmental responsibility in the conveyor belt industry. As these trends continue to evolve, they promise to bring about more resilient, efficient, and cost-effective solutions in material handling.
FAQs about Black Rubber Conveyor Belt
The type of rubber used in conveyor belts depends on the specific application and industry requirements. Generally, conveyor belts are made from natural rubber, synthetic rubber, or a combination of both. Natural rubber is valued for its flexibility, resilience, and resistance to abrasion, making it suitable for various general-purpose applications. However, synthetic rubbers, such as Neoprene, Nitrile, and EPDM, are often used in industrial settings because of their enhanced properties.
Neoprene, for example, offers excellent resistance to oil, heat, and weather conditions, making it ideal for harsh environments. Nitrile rubber is highly resistant to oils and chemicals, which is crucial for industries dealing with these substances. EPDM rubber provides superior heat, ozone, and weather resistance, often used in high-temperature applications. Each type of rubber is selected based on the operating conditions, including temperature range, exposure to chemicals or oils, and mechanical stress. The choice ensures the conveyor belt performs efficiently, maintains durability, and requires minimal maintenance.
Conveyor belts come in a variety of colors, each serving specific purposes or indicating certain characteristics. The most common colors include black, white, green, and blue. Black conveyor belts are the most prevalent, often used in general industrial applications. They are typically made from natural or synthetic rubber and are favored for their durability and resistance to wear and tear.
White conveyor belts are frequently used in food processing and pharmaceutical industries. Their color helps in maintaining hygiene standards as they show contaminants easily and can be thoroughly cleaned. These belts are usually made from materials that meet FDA standards, ensuring they are safe for handling food products.
Green and blue conveyor belts are also used in various industries. Green belts are often employed in agricultural settings or for transporting bulk materials, while blue belts are used in environments requiring a clear differentiation from the products being conveyed, such as in food production or clean rooms. The choice of color can also help in organizing different conveyor lines within a facility, aiding in efficiency and safety management.
Rubber belts are used in a wide range of applications across various industries due to their durability, flexibility, and resistance to different environmental conditions. In the industrial sector, rubber conveyor belts are essential for transporting materials and goods efficiently. They are used in mining to move minerals, in agriculture to transport produce, and in manufacturing to handle products along the production line.
In the automotive industry, rubber belts are utilized in engines as timing belts and drive belts, ensuring the smooth operation of vehicle components. These belts must withstand high temperatures and mechanical stress, showcasing the robustness of rubber materials.
Rubber belts are also found in logistics and warehousing, where they facilitate the movement of packages and goods, enhancing operational efficiency. Additionally, in the food processing and pharmaceutical industries, specially designed rubber belts ensure hygiene and compliance with safety standards while handling sensitive products.
Overall, rubber belts are integral to modern industrial operations, contributing to efficiency, reliability, and safety in material handling and machinery applications.
Belt conveyors come in various types, each designed to suit specific applications and operational requirements. Here are some common types of belt conveyors:
Flat Belt Conveyors: These are the most common type of belt conveyors, featuring a flat belt that runs over pulleys. They are used for transporting items of various shapes and sizes in industries like manufacturing, warehousing, and logistics.
Modular Belt Conveyors: These conveyors use interlocking plastic modules, creating a belt that is flexible and easy to maintain. They are ideal for applications requiring frequent cleaning, such as in the food and beverage industry.
Cleated Belt Conveyors: These belts have vertical cleats or barriers along the belt, helping to prevent items from slipping or falling off. They are used for transporting loose or bulk materials, such as grains, sand, and chemicals.
Incline/Decline Belt Conveyors: Designed to move products between different levels, these conveyors can transport items up or down an incline. They are commonly used in packaging, manufacturing, and distribution centers.
Curved Belt Conveyors: These conveyors allow for the transportation of materials around corners or bends. They are useful in facilities with limited space or where the conveyor path needs to change direction.
Heavy-Duty Belt Conveyors: Built to handle heavy and abrasive materials, these conveyors are used in industries such as mining, construction, and metal manufacturing.
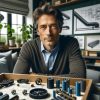
Jordan Smith, a seasoned professional with over 20 years of experience in the conveyor system industry. Jordan’s expertise lies in providing comprehensive solutions for conveyor rollers, belts, and accessories, catering to a wide range of industrial needs. From initial design and configuration to installation and meticulous troubleshooting, Jordan is adept at handling all aspects of conveyor system management. Whether you’re looking to upgrade your production line with efficient conveyor belts, require custom conveyor rollers for specific operations, or need expert advice on selecting the right conveyor accessories for your facility, Jordan is your reliable consultant. For any inquiries or assistance with conveyor system optimization, Jordan is available to share his wealth of knowledge and experience. Feel free to reach out at any time for professional guidance on all matters related to conveyor rollers, belts, and accessories.