Essential Safety Features for Safety Devices in Conveyor Belt
Safety devices in conveyor belt systems are essential components crucial for maintaining workplace safety across various industries. These devices play a pivotal role in preventing accidents and reducing unexpected downtime, which can have significant implications for operational efficiency and worker safety. By implementing the right safety devices, companies can ensure that their conveyor systems operate within the safest possible parameters. This not only protects employees but also preserves the machinery and optimizes productivity. This introduction delves into how these safety devices contribute to creating a safer working environment and highlights the importance of their widespread adoption in industry practices.
Comprehensive Guide to Safety Devices in Conveyor Belt: PDF Accessibility and Content
Accessibility and Benefits of Safety Information
The availability of PDF guides that detail safety devices in conveyor belts is invaluable for ensuring workplace safety across numerous industries. These guides provide immediate and easy access to critical safety information, which can be efficiently distributed among staff within an organization. Such accessibility is crucial for training purposes, compliance updates, and ensuring all team members are on the same page regarding safety protocols. Additionally, these PDFs serve as a constant resource for troubleshooting and quick reference during emergencies, greatly enhancing the ability to respond effectively to potential hazards.
Contents of the Safety PDF
The PDF guide on safety devices in conveyor belts covers a comprehensive range of topics essential for the safe operation of these systems. It includes:
- Device Functionality: Detailed explanations of how various safety devices function, such as emergency stop buttons, pull cord switches, and belt sway switches, and how they contribute to the safety of the conveyor system.
- Setup Guidelines: Step-by-step instructions on the correct installation of safety devices to ensure optimal performance and compliance with safety standards.
- Maintenance Protocols: Outlines regular maintenance schedules and procedures necessary to keep safety devices operational over time. This section also provides guidance on routine checks that can preempt equipment failures and potentially hazardous situations.
- Risk Management Strategies: Advice on identifying potential risks associated with conveyor belt operations and how safety devices can mitigate these risks.
- Regulatory Compliance: Information on adhering to national and international safety regulations that govern the use of conveyor belts in various sectors.
This PDF guide not only enhances the understanding of safety devices in conveyor belts but also supports ongoing education and compliance, ensuring that all safety measures are effectively implemented and maintained.
Essential Safety Devices in Conveyor Belt: Guide to Safety Switches
Types of Safety Switches
Safety switches are critical safety devices in conveyor belts, designed to prevent accidents and ensure the safe operation of conveyor systems. This section details the primary types of safety switches used:
Safety Device | Function | Placement and Use |
---|---|---|
Emergency Stop Switches | Allow operators to immediately halt the conveyor's operations in case of an emergency. | Prominently placed along the conveyor line to ensure accessibility from any point on the conveyor line. |
Pull Cord Switches | Enable operators to stop the conveyor from anywhere along its length, which is crucial for long conveyor systems. | Distributed along the length of the conveyor, providing an emergency stop option that is always within reach. |
Belt Sway Switches | Monitor the alignment of the conveyor belt and activate an alarm or stop the conveyor if the belt deviates from its intended path. | Positioned at critical points along the conveyor to detect and respond to any misalignment of the conveyor belt. |
Functions and Installations
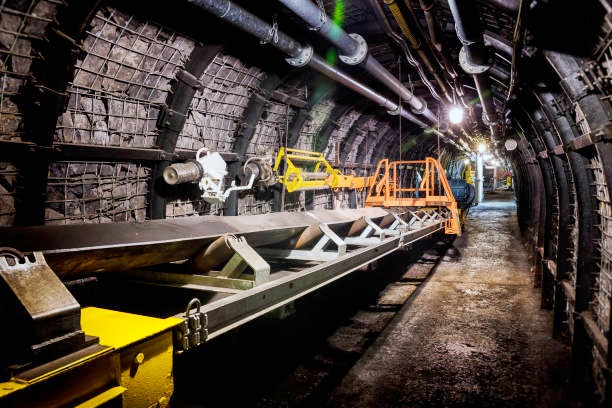
Understanding the operation and correct installation of safety switches is fundamental to enhancing conveyor belt safety:
Operating Mechanisms:
- Emergency Stop Switches: Operate on a fail-safe mechanism that ensures the conveyor stops immediately upon activation.
- Pull Cord Switches: Function by a cable system strung along the length of the conveyor, which, when pulled, triggers the stop mechanism.
- Belt Sway Switches: Detect sideways movement of the belt and trigger corrective actions to realign or stop the conveyor as necessary.
Installation Best Practices:
- Emergency Stop and Pull Cord Switches: Should be installed at regular intervals and within easy reach of personnel. The placement should consider the operator’s ability to access the switch under emergency conditions.
- Belt Sway Switches: Should be mounted on both sides of the conveyor belt at critical points where misalignment is likely to occur. Proper calibration during installation is critical to ensure responsiveness to belt misalignment without false triggers.
Implementing these safety devices in conveyor belts not only complies with occupational safety regulations but significantly contributes to a safer working environment by preventing potential accidents and reducing downtime due to mechanical failures. The guide to safety switches serves as a vital resource for conveyor system designers, safety officers, and maintenance personnel dedicated to safeguarding their operations.
Fire and Explosion Protection in Safety Devices in Conveyor Belt
Description: Safety Measures for Fire and Explosion Prevention
Conveyor systems, especially those used in industries handling combustible materials, are at risk of fire and explosion hazards. These risks can arise from frictional heat, static electricity, hot surfaces, or mechanical failures. To mitigate these dangers, implementing comprehensive fire and explosion protection measures is crucial. These measures not only protect the equipment and facility but also ensure the safety of personnel and continuity of operations.
Key Features: Heat and Smoke Detectors, Suppression Systems
Heat and Smoke Detectors
- Purpose: Heat and smoke detectors are essential for early detection of fire hazards. They monitor the environment around the conveyor system for any signs of overheating or smoke, which are indicative of a potential fire.
- Types:
- Heat Detectors: These can be either fixed temperature detectors, which activate when a specific temperature is reached, or rate-of-rise detectors, which respond to a rapid increase in temperature.
- Smoke Detectors: These come in various types, such as ionization smoke detectors, which are sensitive to smaller smoke particles, and photoelectric smoke detectors, which are better at detecting larger smoke particles typical of smoldering fires.
- Integration: These detectors can be integrated with the conveyor system’s control panel and fire alarm system to provide immediate alerts to operators and trigger automatic shutdowns.
Suppression Systems
- Purpose: Suppression systems are designed to extinguish fires quickly and effectively before they can spread and cause significant damage. They can be activated manually or automatically in response to heat or smoke detectors.
- Types:
- Water-Based Systems: These include sprinklers and water mist systems, which are effective in cooling down the fire and preventing it from spreading.
- Foam Systems: Foam systems are particularly useful for fires involving flammable liquids, as they create a barrier that cuts off the oxygen supply to the fire.
- Chemical Suppression Systems: These use dry chemicals or gaseous agents to extinguish fires. They are ideal for environments where water or foam might cause damage to the equipment or materials being conveyed.
- Placement: Suppression systems should be strategically placed along the conveyor system, particularly in high-risk areas such as transfer points, loading and unloading zones, and areas with potential ignition sources.
Maintenance Tips: Regular Inspection and Servicing of Detection and Suppression Systems
Regular Inspection
- Frequency: Inspections should be conducted at regular intervals, as recommended by the manufacturer or regulatory guidelines. This typically ranges from monthly to quarterly inspections.
- Checklist: During inspections, check for:
- Operational Status: Ensure that all detectors and suppression system components are functioning correctly.
- Physical Condition: Look for signs of wear, corrosion, or damage to the detectors and suppression system components.
- Cleanliness: Ensure that detectors are free from dust, debris, or obstructions that could impair their functionality.
- Power Supply: Verify that all power sources and backup batteries are operational and fully charged.
Servicing and Maintenance
- Professional Servicing: Engage certified professionals to service and maintain the detection and suppression systems. This should include:
- Testing: Perform functional tests to ensure detectors and suppression systems activate as intended.
- Calibration: Adjust and calibrate sensors to maintain accurate detection capabilities.
- Component Replacement: Replace any faulty or expired components, such as sensors, nozzles, or control modules.
- Documentation: Maintain detailed records of all inspections, tests, and maintenance activities. This documentation helps in tracking the system’s performance and identifying any recurring issues.
Training and Drills
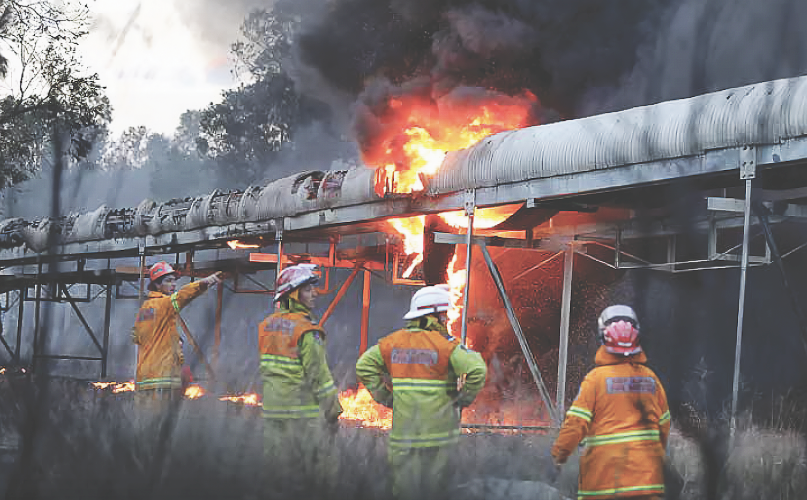
- Staff Training: Regularly train staff on the operation and maintenance of fire and explosion protection systems. Ensure they know how to respond to alarms and activate suppression systems manually if needed.
- Emergency Drills: Conduct fire drills and emergency response simulations to ensure that all personnel are familiar with evacuation routes, emergency procedures, and the location and use of fire protection equipment.
By implementing and maintaining robust fire and explosion protection measures, conveyor system operators can significantly reduce the risk of catastrophic incidents, ensuring a safe and secure working environment.
Enhancing Conveyor System Safety with Safety Devices in Conveyor Belt: Implementing a Safety Checklist
Essentials of Safety Checklists
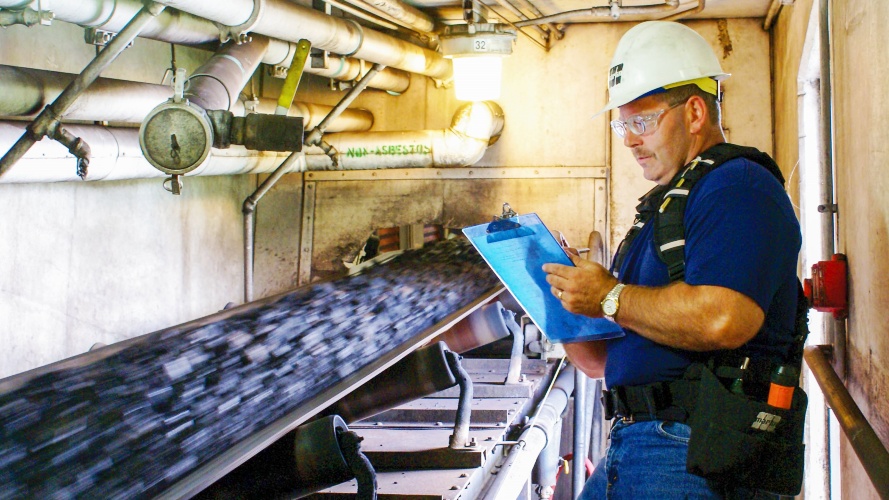
Maintaining a routine safety checklist is essential for the continuous protection of workers and adherence to regulatory safety standards. Safety checklists serve as systematic guides to ensure that all safety devices in conveyor belts are regularly checked for their operational integrity and performance. These checklists not only help in identifying potential issues before they lead to accidents or failures but also ensure that the conveyor system complies with the latest safety regulations. Regularly updating and following these checklists can significantly reduce the risk of downtime and extend the lifespan of both the safety devices and the conveyor system itself. They foster a culture of safety and diligence that permeates throughout the operations, enhancing overall workplace safety.
Checklist Components
A comprehensive safety checklist for conveyor belt systems incorporates several key components:
General Inspections:
Inspect the structural integrity of the conveyor frame to ensure it is not compromised by wear or damage.Check the alignment of the conveyor belt to prevent uneven wear and potential system malfunctions.Verify that all emergency stop mechanisms are accessible and functional.
Device-Specific Checks:
- Belt Sway Switches: Confirm these switches are properly aligned and sensitive enough to detect belt sway yet not so sensitive that they trigger false alarms.
- Speed Switches: Test these to ensure they accurately measure conveyor belt speed and initiate corrective actions when anomalies are detected.
- Emergency Stop Switches and Pull Cord Switches: Regular testing to verify they effectively stop the conveyor system immediately when activated.
- Belt Rip Switches: Ensure these are correctly calibrated to detect any tears or rips in the belt that might lead to more severe operational issues.
Safety Protocol Reviews:
Review and reinforce training protocols to ensure all personnel are aware of the proper use and responses associated with the conveyor safety devices.Update safety documentation to reflect any changes in operations or new safety standards and ensure all safety signs and instructions are clearly visible and legible.
Enhancing Safety with Safety Devices in Conveyor Belt: Protection Methods and Specifications
Protective Measures and Devices
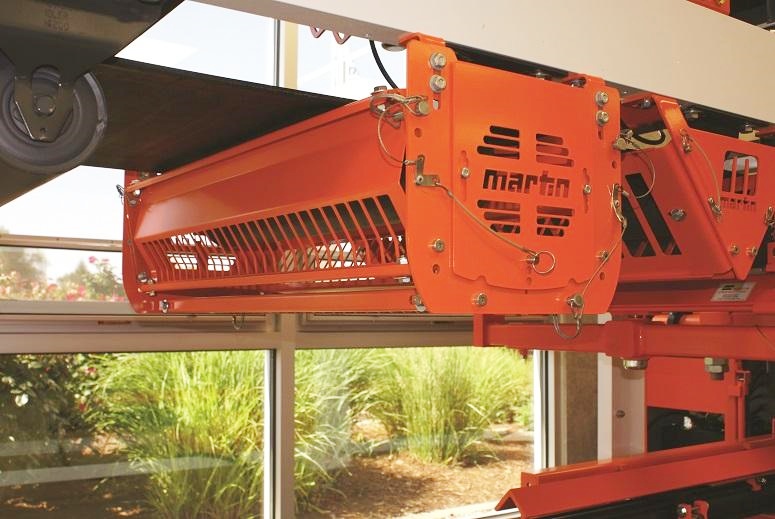
Safety devices in conveyor belts play a crucial role in maintaining workplace safety by preventing accidents and ensuring operational integrity. This section focuses on the various protective mechanisms that can be integrated into conveyor systems:
- Guards and Barriers: These are essential components designed to shield workers from moving parts of the conveyor system. Guards are typically placed around pinch points, gears, and other moving components to prevent accidental contact. Barriers serve to restrict access to areas where the conveyor operates at high speeds or where materials are in motion, thus reducing the risk of injury from flying debris or entanglement.
- Emergency Stops: Conveyor systems are equipped with easily accessible emergency stop controls along the belt’s length. These allow any worker to halt the conveyor’s operation immediately in case of an emergency, providing an essential safety measure in preventing accidents.
- Safety Interlock Switches: These devices ensure that the conveyor cannot operate when maintenance doors are open or when guards have been removed. Interlocks enforce safety procedures by integrating with the conveyor’s control system to prevent startup until all safety measures are securely in place.
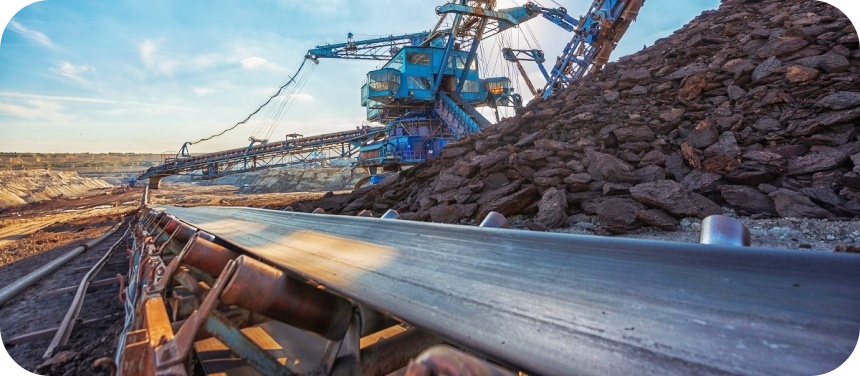
Conveyor Belt Specifications for Safety
The specifications of a conveyor belt greatly influence its safety and suitability for various operational environments:
- Material Quality: The material from which a conveyor belt is made can determine its resistance to wear, tear, and fire. High-quality materials reduce the risk of belt rupture that could lead to accidents. For instance, belts made from fire-resistant materials are crucial in environments where there is a risk of fire or explosion.
- Design Specifications: The design of the conveyor belt must suit the specific needs of the operating environment. This includes considerations like the belt’s width, thickness, and the type of cleats or ribs that can help prevent slippage of materials. Proper design ensures that the belt can handle the intended load without failure, which is vital for safety.
- Operational Suitability: Different environments require different types of conveyor belts. For example, belts used in mining operations are often designed to carry heavy loads over long distances, while belts used in packaging plants may need to accommodate smaller, more delicate items. Ensuring that the belt’s specifications match the operational requirements is essential for safe and efficient functioning.
Enhancing Safety Devices in Conveyor Belt through Interactive Quizzes
Educational Value of Safety Quizzes
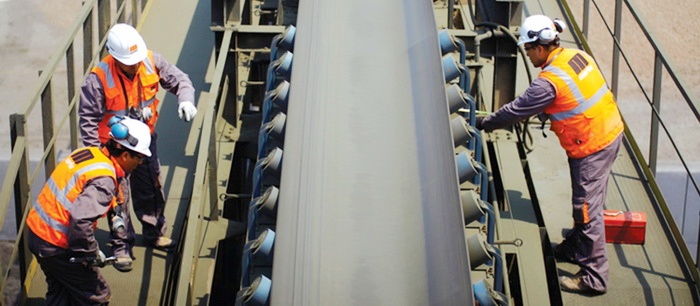
Quizzes play an invaluable role in reinforcing and deepening employees’ understanding of safety protocols associated with safety devices in conveyor belt systems. By regularly engaging with quizzes, employees are continually reminded of essential safety practices related to these devices and are motivated to apply these principles in their daily tasks. This method of learning not only solidifies safety habits but ensures that theoretical knowledge about safety devices is translated into practical, actionable behavior in the workplace. Additionally, quizzes act as a critical tool for trainers and safety officers to gauge the effectiveness of their safety training programs focused on conveyor belt safety devices, helping to pinpoint areas that need more focus and thereby fostering a proactive safety culture.
Enhancing Understanding Through Sample Quiz Content
To improve the handling of emergency situations and day-to-day operations involving conveyor belts, here are examples of typical safety scenarios that might be used in training quizzes:
- Immediate Actions for Misalignment: If a conveyor belt appears misaligned, it is crucial to halt the conveyor using the emergency stop mechanism and promptly report the situation to a supervisor or maintenance crew for further assessment and corrective action.
- Functionality of Belt Sway Switches: Belt sway switches are designed to detect any sideways movement of the conveyor belt. Detecting such movement early can prevent damage and spillage by triggering an alarm or stopping the belt to allow for corrective measures.
- Role of Pull Cord Switches: Located along the length of the conveyor, pull cord switches provide workers the ability to stop the belt instantly in emergencies, thereby offering a quick means to address potential hazards.
- Importance of Regular Checks: Conducting regular checks on the tension of safety pull cords is essential to ensure they are neither too loose nor too tight, which is critical for maintaining their effectiveness in emergency stops.
- Safety Device Inspection Frequency: Routine inspections of safety devices on conveyor belts are recommended based on the manufacturer’s guidelines and applicable safety regulations to ensure they remain in good working condition and are not compromised by wear or environmental conditions.
- Responding to Malfunctioning Safety Interlocks: If a safety interlock switch is found to be malfunctioning, the conveyor system should be deactivated immediately until the switch can be thoroughly examined and repaired by qualified personnel to avoid unintended operation.
Enhancing Conveyor System Safety with Training on Safety Devices in Conveyor Belt
Training and Compliance
Effective training is crucial for ensuring the proper use of safety devices in conveyor belts, aligning with both legal and industry standards. This training should cover all aspects of conveyor safety, from the operation of the machinery to the specific safety devices designed to protect workers. Compliance with safety standards is not just about following the law; it’s about creating an environment where safety is a priority. Training programs should therefore be comprehensive, regularly updated to reflect new standards and technologies, and mandatory for all personnel involved in conveyor operations. These programs need to address the correct responses to emergencies, the daily handling of equipment, and the importance of regular maintenance checks, ensuring that all employees are equipped to maintain a safe working environment.
Quizlet as a Training Tool
Quizlet and similar tools offer dynamic ways to enhance learning and retention of safety protocols regarding safety devices in conveyor belts. By incorporating real-life scenarios and solutions, these platforms can make learning more interactive and practical. For example, Quizlet can be used to create sets of flashcards, practice tests, and learning games that focus on different aspects of conveyor safety, such as identifying the functions of various safety devices, the steps to take in an emergency, or the regular maintenance tasks that are essential for safe operation. The ability to customize learning modules allows trainers to focus on the specific needs of their teams and the particular risks associated with their conveyor systems. Additionally, the use of such tools encourages continuous learning and assessment, which is key to maintaining high safety standards and ensuring that all personnel are consistently up to date with the best safety practices.
Enhancing Conveyor Belt Safety with Safety Devices in Conveyor Belt: Focus on Belt Sway Switches
Functionality of Belt Sway Switches
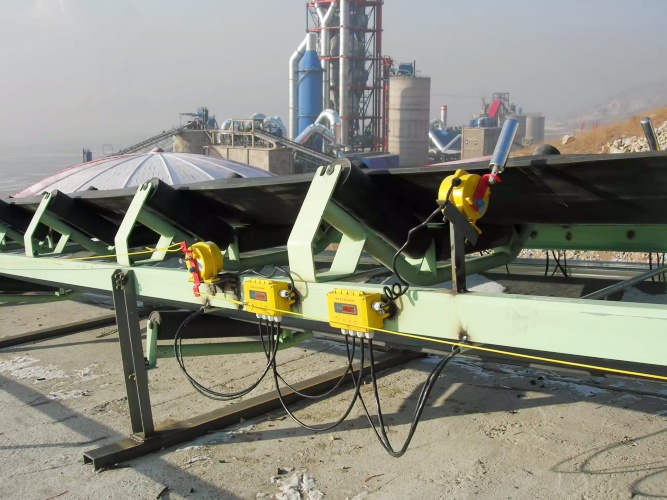
Belt sway switches are a critical type of safety device in conveyor belt systems, designed to detect and respond to any misalignments or drifts of the conveyor belt from its intended track, complementing the function of conveyor belt tracking devices. These switches are typically mounted on both sides of the conveyor frame and measure the belt’s position in relation to its central line. If the belt sways beyond a preset threshold, the belt sway switch activates an alarm or directly stops the conveyor belt, which helps in preventing further misalignment and potential damages to the belt. This immediate response is crucial for minimizing wear and tear on the conveyor system and for avoiding the spillage of materials being transported. The proper functioning of belt sway switches is vital for maintaining the efficiency and longevity of conveyor systems.
Looking for conveyor belts? Contact our experts today.
Impact on Conveyor Belt Safety
The integration of belt sway switches significantly enhances the safety of conveyor belt operations. By providing a fail-safe mechanism that responds instantly to any deviation from the belt’s intended path, these switches play a vital role in preventing accidents that could result from belt misalignment. Such misalignments can lead to severe belt damage, material spillage, or even cause the conveyor to become entangled with other machinery. Belt sway switches thus help to maintain operational continuity and reduce downtime caused by mechanical failures. Additionally, the proactive monitoring of belt alignment helps in maintaining the structural integrity of the conveyor system, ensuring that all parts function within their designed parameters and reducing the likelihood of catastrophic failures. This active safety measure is essential for any industry relying on conveyor systems, as it directly contributes to a safer working environment and more reliable equipment operation.
FAQs about Safety Devices In Conveyor Belt
Safety devices integrated into chain conveyor systems within conveyor belt setups are essential for preventing accidents and ensuring smooth operation. The primary safety devices include:
Emergency Stop Cords: These are strategically placed along the length of the conveyor and can be pulled at any time to immediately stop all operations. This is crucial in preventing accidents and allowing for quick responses to potential issues.
Safety Guards: Moving parts such as chains and sprockets are covered with guards to prevent workers from accidental contact, which can lead to severe injuries. These guards are designed according to stringent standards to ensure they can withstand the operating conditions of the conveyor.
Overload Sensors: These sensors are critical in detecting when the conveyor is overloaded, which can lead to mechanical failures. By automatically shutting down the system when excessive loads are detected, these sensors prevent damage to the conveyor and potential harm to workers nearby.
Speed Monitors: These devices monitor the operational speed of the conveyor and ensure that it does not exceed safe limits. Speeding conveyors can lead to material spillage or the breakdown of conveyor components.
Interlocks: These ensure that the conveyor cannot operate when access doors are open or when the conveyor is under maintenance, thus preventing accidental starts that could endanger maintenance personnel.
In conveyor belt systems, a key human safety device is the emergency stop system. This system is a vital component for human safety for several reasons:
Accessibility: Emergency stop buttons and pull cords are placed within easy reach along the conveyor line, ensuring that any operator, regardless of their position, can quickly halt the conveyor’s operations in case of an emergency.
Immediate Response: These devices provide an instant response to dangerous situations, allowing for the immediate shutdown of the conveyor. This can be crucial in preventing accidents and ensuring the safety of workers, especially in situations involving entanglement or when a foreign object is caught in the conveyor.
Redundancy: Multiple emergency stops and pull cords are installed to ensure that if one fails, others will still function, maintaining safety across the system.
conveyor belt systems, requires adherence to several key safety requirements:
Comprehensive Guarding: All moving parts that pose a risk of injury should be guarded. This includes tail pulleys, head pulleys, and drive mechanisms which should have physical barriers that prevent access during operation.
Regular Maintenance and Inspections: Safety devices and conveyor components should be regularly inspected to ensure they are in good working order. This includes checking for wear and tear, ensuring all safety guards are intact, and verifying that emergency stops function correctly.
Training: All personnel should receive training on the operation of the conveyor, focusing on safety procedures and the proper use of safety devices. This training should be repeated regularly and updated whenever changes are made to the system or new hazards are identified.
Safety Signage: Clear and visible safety signs should be placed along the conveyor to warn of potential hazards and instruct on emergency procedures.
For belt drives, particularly those part of safety devices in conveyor belt systems, several safety precautions must be rigorously followed:
Proper Installation and Alignment: Belt drives should be correctly installed and aligned according to the manufacturer’s specifications to prevent slippage and uneven wear.
Use of Safety Guards: Guards should be used to cover moving parts such as belts and pulleys to prevent direct contact. These guards must be secured and only removed for maintenance when the conveyor is safely locked out.
Regular Monitoring: The condition of the belts should be monitored regularly to detect signs of wear or damage. Replacement of belts should occur before they fail to avoid unexpected downtimes and potential hazards.
Lockout/Tagout Procedures: When performing maintenance, proper lockout/tagout procedures must be followed to ensure that the conveyor cannot be started accidentally. This is critical to protect maintenance personnel from injuries.
Belt conveyors are equipped with various safety devices to ensure the safety of personnel and efficient operation of the system. Some of the key safety devices include:
Emergency Stop Controls: These are strategically placed along the conveyor system to allow workers to quickly stop the conveyor in case of an emergency.
Guardrails and Barriers: These physical barriers prevent workers from coming into contact with moving parts of the conveyor system.
Safety Sensors and Alarms: Sensors detect anomalies such as belt misalignment, belt slip, or blockages and trigger alarms to alert operators.
Belt Misalignment Switches: These switches detect if the conveyor belt is running off-center and can shut down the system to prevent damage.
Pull Cord Switches: Running along the length of the conveyor, these allow workers to pull a cord to immediately stop the conveyor in an emergency.
Start-Up Warning Systems: Audible and visual warnings that alert workers when the conveyor is about to start moving.
Speed Monitors: These devices monitor the speed of the conveyor to ensure it is operating within safe limits.
Interlocking Systems: These systems ensure that certain operations are only carried out in a specific sequence to prevent accidents.
Personal Protective Equipment (PPE): While not part of the conveyor itself, ensuring workers are equipped with appropriate PPE such as helmets, gloves, and safety glasses is crucial.
Scheduled Maintenance Protocols: Regular inspections and maintenance schedules help identify and rectify potential safety hazards before they cause accidents.
Rip Detection Systems: These systems detect and alert operators to any rips or tears in the conveyor belt that could lead to larger issues.
Implementing and regularly maintaining these safety devices helps in creating a safe working environment and ensures the efficient and uninterrupted operation of belt conveyors.
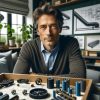
Jordan Smith, a seasoned professional with over 20 years of experience in the conveyor system industry. Jordan’s expertise lies in providing comprehensive solutions for conveyor rollers, belts, and accessories, catering to a wide range of industrial needs. From initial design and configuration to installation and meticulous troubleshooting, Jordan is adept at handling all aspects of conveyor system management. Whether you’re looking to upgrade your production line with efficient conveyor belts, require custom conveyor rollers for specific operations, or need expert advice on selecting the right conveyor accessories for your facility, Jordan is your reliable consultant. For any inquiries or assistance with conveyor system optimization, Jordan is available to share his wealth of knowledge and experience. Feel free to reach out at any time for professional guidance on all matters related to conveyor rollers, belts, and accessories.