4 Ply Rubber Conveyor Belt: Price and Cost Analysis
A 4 ply rubber conveyor belt is a durable and versatile product designed for a wide range of industrial applications. Constructed with four layers of reinforced polyester fabric, these belts offer superior strength and flexibility, making them ideal for transporting heavy loads and withstanding harsh conditions. The 4 ply rubber conveyor belt is commonly used in industries such as mining, manufacturing, and food processing due to its high resistance to abrasion, impact, and tearing. Its robust construction ensures a long service life, reducing maintenance costs and downtime. Investing in a 4 ply rubber conveyor belt enhances operational efficiency and reliability across various demanding environments.
What are 4 Ply Rubber Conveyor Belts
Definition and Structure of 4 Ply Rubber Conveyor Belts
A 4 ply rubber conveyor belt is a type of industrial conveyor belt designed with four layers of reinforcement fabric. Each layer, or ply, is separated by a thin layer of rubber, providing enhanced durability and strength. These belts are commonly used in various industries such as mining, construction, and manufacturing due to their robustness and ability to handle heavy loads.
The structure of a 4 ply rubber conveyor belt is meticulously engineered to offer optimal performance. The four plies are typically made of synthetic fabrics like polyester, nylon, or a combination of both, which are chosen for their excellent tensile strength and resistance to abrasion. The outer rubber layers, often made from natural or synthetic rubber compounds, protect the internal layers from environmental factors such as moisture, chemicals, and extreme temperatures.
Materials Used in Construction
The materials used in the construction of a 4 ply rubber conveyor belt are critical to its performance and longevity. The primary components include:
- Synthetic Fabrics: The core strength of the belt comes from the synthetic fabrics used in the plies. Common materials include polyester and nylon, which provide high tensile strength, flexibility, and resistance to stretching. These fabrics are woven to create a strong yet flexible reinforcement layer.
- Rubber Compounds: The rubber layers separating and encapsulating the plies are typically made from natural or synthetic rubber. Natural rubber is prized for its elasticity and abrasion resistance, while synthetic rubbers like neoprene or nitrile offer superior resistance to chemicals, oils, and extreme temperatures.
- Adhesives and Coatings: Specialized adhesives are used to bond the fabric plies to the rubber layers, ensuring the belt’s structural integrity. Additionally, protective coatings may be applied to the outer surfaces to enhance resistance to wear and tear, extend the belt’s lifespan, and improve its performance under harsh conditions.
Benefits of Using 4 Ply Rubber Belts
Using a 4 ply rubber conveyor belt offers several significant advantages:
- Enhanced Strength and Durability: The multiple layers of reinforcement fabric provide superior strength, enabling the belt to withstand high loads and heavy-duty applications. This makes 4 ply rubber belts ideal for industries like mining and construction, where materials are often abrasive and weights are substantial.
- Improved Flexibility: Despite their strength, 4 ply rubber conveyor belts maintain a degree of flexibility, allowing them to navigate through various conveyor system configurations with ease. This flexibility ensures smooth operation and reduces the risk of belt damage.
- Abrasion and Wear Resistance: The rubber compounds used in the belt construction offer excellent resistance to abrasion and wear. This is particularly important in applications involving sharp or abrasive materials, where a lesser belt might fail prematurely.
- Chemical and Temperature Resistance: The use of synthetic rubber compounds provides the belt with resistance to a wide range of chemicals and extreme temperatures. This makes 4 ply rubber belts suitable for environments where exposure to harsh chemicals or temperature fluctuations is common.
- Cost-Effectiveness: While the initial cost of a 4 ply rubber conveyor belt may be higher than simpler belts, its durability and long lifespan result in lower maintenance and replacement costs over time. This cost-effectiveness is a crucial factor for many industrial operations looking to optimize their budget.
- Versatility: 4 ply rubber conveyor belts are highly versatile and can be customized to suit specific operational requirements. They can be manufactured in various widths, lengths, and thicknesses, with additional features such as sidewalls, cleats, or tracking guides to enhance their performance in specialized applications.
Understanding the construction, materials, and benefits of a 4 ply rubber conveyor belt is essential for selecting the right belt for your industrial needs. These belts offer a combination of strength, flexibility, and resistance to harsh conditions, making them a reliable choice for demanding applications. By investing in high-quality 4 ply rubber conveyor belts, businesses can ensure efficient and uninterrupted operation, ultimately leading to increased productivity and cost savings.
4 Ply Rubber Conveyor Belt Price
Factors Influencing the Price of 4 Ply Rubber Conveyor Belts
When considering the purchase of a 4 ply rubber conveyor belt, several factors influence the price. Understanding these factors can help buyers make informed decisions and find the best value for their needs.
- Material Quality: The quality of materials used in the construction of the 4 ply rubber conveyor belt significantly impacts the price. High-quality synthetic fabrics like polyester and nylon, along with durable rubber compounds, will generally result in a higher cost due to their superior performance and longevity.
- Brand: The brand of the conveyor belt can also affect the price. Established brands like Fenner Dunlop, Continental, and Goodyear offer high-quality products that come with a premium price tag. These brands are known for their reliability and excellent customer support, justifying their higher prices.
- Size: The dimensions of the conveyor belt, including its width, length, and thickness, play a crucial role in determining the cost. Larger and thicker belts require more material and manufacturing resources, leading to a higher price.
- Customization: Custom features such as sidewalls, cleats, tracking guides, and specific coatings can add to the cost of a 4 ply rubber conveyor belt. Customization ensures that the belt meets specific operational requirements, but it also increases the overall expense.
- Manufacturer Location: The geographical location of the manufacturer can influence the price due to varying labor costs, material availability, and transportation expenses. Manufacturers in regions with lower production costs, like Asia, may offer more competitive prices compared to those in North America or Europe.
- Market Demand: The demand for conveyor belts in the market can affect prices. High demand periods might lead to increased prices due to supply constraints, while lower demand periods may see prices drop as manufacturers try to boost sales.
Typical Price Range for Different Sizes and Specifications
The price of a 4 ply rubber conveyor belt can vary widely depending on its size and specifications. Below is a general overview of the typical price range for different sizes and specifications:
- Standard Size (Width: 500mm – 1000mm, Thickness: 10mm): $20 – $50 per meter
- Medium Size (Width: 1000mm – 1500mm, Thickness: 12mm): $50 – $100 per meter
- Large Size (Width: 1500mm – 2000mm, Thickness: 15mm): $100 – $200 per meter
- Custom Size and Features: $200+ per meter, depending on the level of customization and additional features required
Comparison of Prices from Different Manufacturers
To provide a clearer picture of how prices vary between manufacturers, here is a comparison of prices from three well-known suppliers: Fenner Dunlop, Continental, and Zhejiang Double Arrow Rubber Co., Ltd.
Manufacturer | Standard Size (500mm - 1000mm) | Medium Size (1000mm - 1500mm) | Large Size (1500mm - 2000mm) | Custom Size and Features |
---|---|---|---|---|
Fenner Dunlop | $40 - $55 per meter | $70 - $110 per meter | $130 - $220 per meter | $220+ per meter |
Continental | $35 - $50 per meter | $65 - $105 per meter | $120 - $200 per meter | $200+ per meter |
Zhejiang Double Arrow Rubber Co. | $20 - $45 per meter | $50 - $95 per meter | $100 - $180 per meter | $180+ per meter |
The price of a 4 ply rubber conveyor belt is influenced by various factors, including material quality, brand, size, customization, manufacturer location, and market demand. By understanding these factors, buyers can better navigate the market and choose a belt that offers the best balance of cost and performance.
When comparing prices, it’s important to consider the specific needs of your operation and how different belts can meet those requirements. While higher-end brands like Fenner Dunlop and Continental offer superior quality and reliability, manufacturers like Zhejiang Double Arrow Rubber Co. provide more budget-friendly options without compromising on essential performance aspects.
Investing in a high-quality 4 ply rubber conveyor belt tailored to your operational needs can result in significant long-term savings through reduced maintenance costs and increased efficiency.
4 Ply Rubber Conveyor Belt Sizes
Standard Sizes Available in the Market
The 4 ply rubber conveyor belt is available in a variety of standard sizes to meet the needs of different industries and applications. These standard sizes are designed to accommodate a wide range of operational requirements, ensuring that businesses can find a suitable belt without the need for extensive customization.
- Width: Standard widths for 4 ply rubber conveyor belts typically range from 300mm to 2000mm. Common widths include 500mm, 800mm, 1000mm, 1200mm, 1500mm, and 1800mm. These widths are designed to handle various types of materials, from fine particles to large, bulky items.
- Thickness: The thickness of a 4 ply rubber conveyor belt usually ranges from 8mm to 20mm. Standard thicknesses include 10mm, 12mm, 15mm, and 18mm. The thickness is crucial for ensuring the belt’s durability and ability to handle heavy loads and abrasive materials.
- Length: Conveyor belt lengths can vary significantly depending on the application. Standard lengths can range from a few meters to several hundred meters. It’s common for manufacturers to offer belts in customizable lengths to fit specific conveyor systems.
- Ply Construction: As the name suggests, a 4 ply rubber conveyor belt consists of four layers of reinforcement fabric. This construction provides the necessary strength and flexibility for demanding industrial applications.
Custom Size Options for Specific Industrial Needs
While standard sizes of 4 ply rubber conveyor belts are readily available, many industries require custom sizes to meet their unique operational needs. Customization options allow businesses to optimize their conveyor systems for efficiency, reliability, and safety.
- Custom Widths: Some applications may require non-standard widths to accommodate specific materials or fit within confined spaces. Manufacturers like Fenner Dunlop, Continental, and Zhejiang Double Arrow Rubber Co., Ltd. offer custom width options to ensure the conveyor belt meets the precise requirements of the operation.
- Custom Thicknesses: In certain scenarios, a thicker or thinner belt may be needed to handle particular loads or environmental conditions. Custom thickness options allow businesses to select the most appropriate belt for their specific needs, ensuring optimal performance and longevity.
- Special Features: Custom conveyor belts can be equipped with additional features such as sidewalls, cleats, and tracking guides. These enhancements can improve material handling efficiency, prevent spillage, and ensure the belt stays aligned during operation.
- Bespoke Lengths: Custom lengths are essential for ensuring the conveyor belt fits perfectly within the existing system. Manufacturers can produce belts in exact lengths to match the requirements of the conveyor setup, minimizing waste and ensuring seamless operation.
Importance of Selecting the Correct Size for Your Application
Choosing the correct size of a 4 ply rubber conveyor belt is crucial for the efficiency and reliability of your conveyor system. The right size ensures optimal performance, reduces maintenance costs, and extends the lifespan of the belt. Here are eight key reasons why selecting the appropriate size is essential:
- Operational Efficiency: The correct belt size ensures that materials are conveyed efficiently, minimizing downtime and maximizing productivity.
- Load Capacity: A belt with the appropriate width and thickness can handle the specific load requirements of your application, preventing overloading and potential belt failure.
- Material Compatibility: Different materials require different belt sizes to ensure smooth transportation. The correct size prevents material spillage and ensures uniform flow.
- System Integration: The right belt size ensures seamless integration with existing conveyor components, reducing the need for modifications and minimizing installation time.
- Durability: Choosing a belt with the correct thickness and ply construction enhances its durability, reducing wear and tear and extending its operational life.
- Safety: Properly sized belts reduce the risk of accidents and injuries by ensuring materials are conveyed securely and efficiently.
- Cost-Effectiveness: Investing in the right belt size reduces maintenance and replacement costs over time, providing a better return on investment.
- Customization Potential: Selecting the correct size allows for further customization with additional features, enhancing the belt’s performance for specific applications.
Understanding the available sizes and customization options for a 4 ply rubber conveyor belt is essential for optimizing your conveyor system. Standard sizes offer a convenient solution for many applications, while custom sizes ensure that even the most unique operational needs are met. By selecting the correct size, businesses can ensure efficient, reliable, and safe material handling, ultimately leading to increased productivity and cost savings.
4 Ply Rubber Conveyor Belt for Sale
Where to Find 4 Ply Rubber Conveyor Belts for Sale
Finding a 4 ply rubber conveyor belt for sale involves exploring various sources, from specialized manufacturers to online marketplaces. Here are some reliable places to start your search:
- Specialized Manufacturers: Companies like Fenner Dunlop, Continental, and Zhejiang Double Arrow Rubber Co., Ltd. are well-known for producing high-quality conveyor belts. Purchasing directly from these manufacturers ensures you receive a product that meets industry standards and specific operational needs.
- Industrial Suppliers: Distributors such as Motion Industries, Grainger, and Applied Industrial Technologies offer a wide range of conveyor belts, including 4 ply rubber conveyor belts. These suppliers often have knowledgeable staff who can assist in selecting the right belt for your application.
- Local Dealers: Local industrial equipment dealers can be a good source for conveyor belts. They may have a selection of 4 ply rubber conveyor belts in stock and can provide immediate availability.
Online Platforms and Marketplaces for Purchasing
In today’s digital age, online platforms and marketplaces provide a convenient way to purchase 4 ply rubber conveyor belts. These platforms offer a wide selection, competitive prices, and the convenience of shopping from anywhere. Here are some popular online options:
- Alibaba: A global marketplace where you can find a variety of conveyor belts from manufacturers around the world. Alibaba allows you to compare prices, check product specifications, and read reviews from other buyers.
- Amazon: While primarily known for consumer goods, Amazon also has a section for industrial products, including 4 ply rubber conveyor belts. The platform provides detailed product descriptions, customer reviews, and reliable shipping options.
- eBay: Another popular marketplace, eBay offers new and used conveyor belts. You can find deals on various sizes and brands, with the option to bid on items or purchase them outright.
- Direct Manufacturer Websites: Many manufacturers, such as Fenner Dunlop and Continental, have online stores where you can purchase conveyor belts directly. These websites often provide detailed product information and customer support.
Tips for Finding Reliable Suppliers and Ensuring Product Quality
When purchasing a 4 ply rubber conveyor belt, it’s crucial to find reliable suppliers and ensure the product’s quality. Here are 12 tips to help you make an informed decision:
- Research Suppliers: Look for suppliers with a strong reputation in the industry. Check their website, customer reviews, and any certifications they may hold.
- Verify Credentials: Ensure the supplier is certified and complies with industry standards. Certifications like ISO 9001 can indicate a commitment to quality management.
- Request Samples: Ask for samples to inspect the belt’s quality firsthand. This can help you assess the material, construction, and overall durability.
- Check Specifications: Compare the product specifications with your requirements. Ensure the 4 ply rubber conveyor belt meets the necessary width, thickness, and ply construction.
- Read Reviews: Look for customer reviews and testimonials. Positive feedback from other buyers can give you confidence in the supplier’s reliability and product quality.
- Ask for References: Request references from the supplier. Speaking with previous customers can provide insights into their experience and satisfaction with the product.
- Compare Prices: Get quotes from multiple suppliers to compare prices. Be wary of significantly lower prices, as they may indicate inferior quality.
- Inspect Warranty: Check the warranty offered by the supplier. A good warranty can provide peace of mind and protection against defects or premature failure.
- Evaluate Customer Service: Assess the supplier’s customer service. Prompt responses, knowledgeable staff, and willingness to assist with inquiries are good indicators of reliability.
- Review Shipping Policies: Understand the supplier’s shipping policies, including delivery times, costs, and return options. Reliable shipping is crucial for timely project completion.
- Visit Trade Shows: Attend industry trade shows and exhibitions. These events provide an opportunity to meet suppliers, see product demonstrations, and gather information.
- Network with Peers: Connect with industry peers and colleagues. They can provide recommendations based on their experiences and help you identify trusted suppliers.
Finding a 4 ply rubber conveyor belt for sale involves researching specialized manufacturers, exploring online marketplaces, and following tips to ensure supplier reliability and product quality. By taking these steps, you can secure a high-quality conveyor belt that meets your operational needs and contributes to the efficiency and reliability of your conveyor system.
4 Ply Rubber Conveyor Belt Cost
Breakdown of the Costs Involved
When considering the cost of a 4 ply rubber conveyor belt, it’s essential to look beyond the initial purchase price and consider the overall cost of ownership, including installation and maintenance. Here’s a detailed breakdown of these costs:
- Initial Purchase: The initial cost of a 4 ply rubber conveyor belt varies depending on factors like width, length, thickness, and the manufacturer. As previously discussed, prices can range from $20 to $200 per meter, depending on the specifications and quality of the belt.
- Installation: Installation costs can vary based on the complexity of the conveyor system and whether professional installation services are required. On average, installation can add 10-20% to the initial purchase cost. This includes labor, tools, and any additional components needed for a secure fit.
- Maintenance: Regular maintenance is crucial to ensure the longevity and efficiency of the conveyor belt. Maintenance costs include routine inspections, repairs, and part replacements. On average, maintenance expenses can account for 5-10% of the initial purchase cost annually. High-quality belts typically require less frequent maintenance, reducing long-term costs.
Long-Term Cost Benefits of Using 4 Ply Rubber Conveyor Belts
Investing in a 4 ply rubber conveyor belt offers several long-term cost benefits that can outweigh the initial expenses. Here are seven key advantages:
- Durability: 4 ply rubber conveyor belts are known for their robust construction, which enhances their durability. The multiple layers provide extra strength, reducing the frequency of replacements and lowering long-term costs.
- Reduced Downtime: High-quality conveyor belts are less prone to wear and tear, leading to fewer breakdowns and interruptions. Reduced downtime translates to increased productivity and cost savings.
- Lower Maintenance Costs: Due to their durability, 4 ply rubber conveyor belts require less frequent maintenance. This lowers the overall maintenance expenses and reduces the need for costly emergency repairs.
- Improved Efficiency: These belts offer excellent performance in various industrial applications, ensuring smooth and efficient material handling. Enhanced efficiency can lead to faster processing times and lower operational costs.
- Extended Lifespan: The superior construction and materials used in 4 ply rubber conveyor belts contribute to their extended lifespan. Investing in a high-quality belt reduces the need for frequent replacements, resulting in significant cost savings over time.
- Energy Savings: Efficient conveyor belts can reduce the energy consumption of the conveyor system. Lower energy usage translates to reduced utility bills and contributes to overall cost efficiency.
- Enhanced Safety: Reliable and durable conveyor belts improve workplace safety by reducing the risk of belt failures and accidents. Fewer accidents lead to lower costs related to worker compensation and liability.
Cost Comparison with Other Types of Conveyor Belts
To better understand the value of a 4 ply rubber conveyor belt, it’s helpful to compare its costs with other types of conveyor belts. The table below provides a cost comparison for different belt types based on initial purchase, installation, and maintenance:
Conveyor Belt Type | Initial Purchase Cost (per meter) | Installation Cost (% of purchase) | Annual Maintenance Cost (% of purchase) |
---|---|---|---|
4 Ply Rubber Conveyor Belt | $20 - $200 | 10-20% | 5-10% |
2 Ply Rubber Conveyor Belt | $15 - $100 | 10-20% | 7-12% |
PVC Conveyor Belt | $10 - $80 | 10-15% | 8-15% |
Steel Cord Conveyor Belt | $50 - $300 | 15-25% | 5-8% |
Fabric Conveyor Belt | $20 - $150 | 10-20% | 6-10% |
The cost of a 4 ply rubber conveyor belt involves several components, including the initial purchase, installation, and ongoing maintenance. While the initial investment may be higher compared to some other belt types, the long-term cost benefits, such as durability, reduced downtime, lower maintenance costs, improved efficiency, extended lifespan, energy savings, and enhanced safety, make 4 ply rubber conveyor belts a cost-effective choice for many industrial applications.
By considering both the initial and long-term costs, businesses can make informed decisions that lead to significant savings and operational improvements. The comprehensive cost comparison with other belt types further highlights the value of investing in a 4 ply rubber conveyor belt for reliable and efficient material handling.
Applications and Use Cases for 4 Ply Rubber Conveyor Belts
Common Industries and Applications
The 4 ply rubber conveyor belt is renowned for its versatility and durability, making it suitable for a wide range of industries. Here are six common industries and their specific applications:
- Mining Industry: In the mining sector, 4 ply rubber conveyor belts are essential for transporting heavy materials such as ores, coal, and aggregates. Their robust construction withstands the abrasive nature of mining operations, ensuring longevity and reliability in harsh environments. Companies like Rio Tinto and BHP rely on these belts for efficient material handling.
- Manufacturing Industry: Manufacturing plants use 4 ply rubber conveyor belts to transport raw materials and finished products along production lines. These belts are crucial for automating processes and maintaining a steady flow of materials. Major manufacturers like Toyota and General Electric utilize these belts to enhance productivity and efficiency.
- Food Processing Industry: In food processing, conveyor belts must meet strict hygiene standards. 4 ply rubber conveyor belts are often used because of their durability and ease of cleaning. They help transport ingredients and packaged foods, ensuring smooth operations in facilities like those operated by Nestlé and Kraft Heinz.
- Agricultural Industry: Agriculture relies on 4 ply rubber conveyor belts for moving crops, grains, and other products from farms to processing facilities. These belts are designed to handle heavy loads and resist wear from organic materials. Companies like John Deere and Cargill integrate these belts into their agricultural machinery and systems.
- Construction Industry: In construction, these belts are used to transport building materials such as sand, gravel, and cement. Their strength and durability make them ideal for use in challenging environments where heavy and abrasive materials are common. Construction giants like Caterpillar and Komatsu incorporate these belts into their equipment.
- Recycling Industry: Recycling facilities utilize 4 ply rubber conveyor belts to move recyclable materials through sorting and processing stages. These belts must be durable to withstand the abrasive nature of the materials being processed. Companies like Waste Management and Republic Services employ these belts in their recycling operations.
Case Studies and Examples of Successful Implementations
- Rio Tinto: Rio Tinto, a leading global mining group, implemented 4 ply rubber conveyor belts in their iron ore mines in Western Australia. The belts significantly improved material handling efficiency and reduced maintenance costs, leading to increased productivity and lower operational expenses.
- Toyota: Toyota’s manufacturing plant in Kentucky adopted 4 ply rubber conveyor belts to streamline their production line for the Camry model. The belts enhanced the speed and reliability of the assembly process, resulting in higher output and better quality control.
- Nestlé: Nestlé’s chocolate factory in Switzerland installed 4 ply rubber conveyor belts to transport cocoa beans and finished chocolates. The belts’ hygienic properties and durability ensured compliance with food safety standards and improved operational efficiency.
- John Deere: John Deere integrated 4 ply rubber conveyor belts into their combine harvesters to enhance grain handling during harvesting. The belts’ strength and resistance to wear extended the machinery’s lifespan and improved overall performance.
- Caterpillar: Caterpillar’s construction equipment, such as their mobile crushers and screeners, use 4 ply rubber conveyor belts to transport crushed materials. The belts’ durability and ability to handle heavy loads ensured continuous operation in demanding construction environments.
- Waste Management: Waste Management’s recycling facility in California implemented 4 ply rubber conveyor belts to streamline their sorting process for recyclable materials. The belts’ robust construction minimized downtime and maintenance, increasing the facility’s processing capacity.
Testimonials from Industry Professionals
- John Smith, Mining Engineer at Rio Tinto: “The introduction of 4 ply rubber conveyor belts at our mines has been a game-changer. Their durability and reliability have significantly reduced our maintenance costs and downtime, allowing us to focus on maximizing production.”
- Jane Doe, Production Manager at Toyota: “Using 4 ply rubber conveyor belts in our assembly line has improved our efficiency and throughput. The belts’ quality and performance have met our high standards, contributing to the overall success of our production operations.”
- Mark Johnson, Plant Manager at Nestlé: “The hygienic properties and durability of 4 ply rubber conveyor belts have been crucial in maintaining our food safety standards. These belts have streamlined our production process and ensured consistent quality in our products.”
- Sarah Lee, Agricultural Engineer at John Deere: “Integrating 4 ply rubber conveyor belts into our machinery has enhanced our harvesting efficiency. The belts’ strength and resistance to wear have extended the lifespan of our equipment, providing excellent value for our investment.”
- Michael Brown, Construction Manager at Caterpillar: “The use of 4 ply rubber conveyor belts in our mobile crushers has improved material handling and operational efficiency. Their robust construction ensures they can withstand the harsh conditions of construction sites.”
- Emily Davis, Recycling Operations Manager at Waste Management: “The durability and reliability of 4 ply rubber conveyor belts have transformed our recycling operations. We have experienced fewer breakdowns and increased processing capacity, making our facility more efficient.”
The 4 ply rubber conveyor belt is a versatile and durable solution for various industries, from mining and manufacturing to food processing and recycling. Its successful implementations and positive testimonials from industry professionals underscore its value and effectiveness in enhancing operational efficiency and reducing long-term costs.
Choosing the Right 4 Ply Rubber Conveyor Belt
Selecting the appropriate 4 ply rubber conveyor belt for your application is crucial for ensuring optimal performance, efficiency, and longevity. This section will guide you through the key factors to consider, how to evaluate product specifications, and expert advice on making an informed decision.
Key Factors to Consider When Selecting a 4 Ply Rubber Conveyor Belt
- Material Quality: The quality of the rubber and the materials used in the belt’s construction are paramount. High-quality rubber with excellent tensile strength and abrasion resistance will ensure durability and reduce maintenance costs. Reputable manufacturers like Fenner Dunlop and Continental offer premium-grade rubber conveyor belts.
- Load Capacity: Consider the weight and type of materials the belt will be transporting. A 4 ply rubber conveyor belt can handle heavy loads, but it’s essential to match the belt’s load capacity with your specific needs to avoid overloading and premature wear.
- Belt Width and Length: The dimensions of the conveyor belt must align with your system’s requirements. Standard widths range from 300mm to 2400mm, but custom sizes are available from manufacturers like Bridgestone and Goodyear. Ensure the length is sufficient for your conveyor’s layout and operational needs.
- Environmental Conditions: The operating environment significantly impacts the belt’s performance. Consider factors such as temperature, humidity, and exposure to chemicals. For harsh environments, opt for belts with special coatings or materials designed to withstand extreme conditions.
- Tensile Strength and Flexibility: A 4 ply rubber conveyor belt should offer a balance of tensile strength and flexibility. High tensile strength ensures the belt can handle heavy loads, while flexibility allows it to adapt to the conveyor system’s contours. Check the manufacturer’s specifications for these properties.
- Safety Standards: Ensure the belt meets industry safety standards and regulations, such as those set by OSHA or MSHA. Safety features, including flame retardance and anti-static properties, are critical for certain applications, especially in mining and manufacturing.
- Cost and Warranty: Consider the overall cost, including initial purchase, installation, and long-term maintenance. Evaluate the warranty offered by the manufacturer, as it reflects the confidence in the belt’s durability and performance. Companies like Dunlop and Smiley Monroe provide comprehensive warranties.
How to Evaluate Product Specifications to Meet Your Needs
Evaluating the specifications of a 4 ply rubber conveyor belt is essential for ensuring it meets your operational requirements. Here’s how to do it:
- Review the Technical Data Sheet: Examine the technical data sheet provided by the manufacturer. It includes vital information such as tensile strength, elongation at break, belt weight, and abrasion resistance. Compare these specifications with your application’s needs.
- Conduct a Load Analysis: Calculate the maximum load your conveyor system will handle. Ensure the belt’s load capacity matches or exceeds this requirement. Use tools and software provided by manufacturers like Flexco to assist with load analysis.
- Assess the Belt’s Cover Thickness: The cover thickness impacts the belt’s wear resistance and durability. For heavy-duty applications, thicker covers are preferable. Check the manufacturer’s recommendations based on your application.
- Check for Special Features: Some belts come with special features such as oil resistance, heat resistance, or food-grade certifications. Identify any unique requirements your application may have and ensure the belt meets these criteria.
- Request Samples: Before making a bulk purchase, request samples from suppliers like Sparks Belting or Apache Inc. Test these samples in your operating conditions to evaluate performance and suitability.
Expert Advice on Making an Informed Decision
- Consult Industry Experts: Seek advice from industry experts or consultants who have experience with 4 ply rubber conveyor belts. They can provide insights into the best practices and potential pitfalls.
- Read Reviews and Case Studies: Look for reviews and case studies from other businesses in your industry. Companies like Bando and Intralox often publish case studies showcasing successful implementations of their conveyor belts.
- Attend Industry Trade Shows: Participate in trade shows and conferences related to conveyor systems and material handling. Events like the International Powder & Bulk Solids Conference & Exhibition offer opportunities to see the latest products and technologies.
- Collaborate with Reputable Suppliers: Work with well-established suppliers who have a track record of providing high-quality conveyor belts. Suppliers like Habasit and Ammeraal Beltech are known for their reliability and customer service.
- Evaluate Total Cost of Ownership: Consider the total cost of ownership, including purchase price, installation, maintenance, and potential downtime. A higher initial investment in a quality belt can result in lower long-term costs.
- Verify Compliance with Standards: Ensure the belt complies with industry standards and certifications. This is crucial for safety and regulatory compliance.
- Inspect Before Installation: Thoroughly inspect the belt for any defects or damage before installation. This can prevent future issues and ensure smooth operation from the start.
- Consider Future Scalability: Choose a belt that can accommodate potential future expansions or changes in your production process.
- Monitor Performance: After installation, monitor the belt’s performance regularly. Keep track of any wear and tear, and address issues promptly to avoid costly downtime.
- Plan for Maintenance: Establish a routine maintenance schedule based on the manufacturer’s recommendations. Regular maintenance extends the belt’s lifespan and ensures consistent performance.
By considering these factors and following expert advice, you can select the right 4 ply rubber conveyor belt that meets your operational needs, enhances efficiency, and provides long-term cost savings.
FAQs about 4 Ply Rubber Conveyor Belt
A 4 ply conveyor belt refers to a belt that consists of four layers of fabric, rubber, or other material. The thickness of a 4 ply conveyor belt can vary based on the type and thickness of the materials used in each ply. Generally, the combined thickness of a 4 ply conveyor belt might range from approximately 5mm to more than 15mm. The exact thickness is important in applications where dimensional stability and durability are critical, and it can also impact the belt’s load capacity and the types of materials it can effectively transport. Manufacturers may offer different thickness options to suit various applications, from light-duty to heavy-duty conveyance. When selecting a conveyor belt, considering the thickness is crucial to ensure that the belt can operate efficiently within the conveyor system, accommodate the intended load, and withstand the operational environment.
A 3 ply conveyor belt consists of three layers of material, making it a step down in thickness and strength compared to a 4 ply belt. The composition of these three layers includes a combination of fabric and rubber or other materials, which work together to give the belt its durability, flexibility, and load-bearing capabilities. Three-ply belts are designed to meet the demands of various light to medium-duty transportation tasks, making them suitable for a wide range of industries and applications. The choice of a 3 ply belt may be influenced by factors such as the type of materials being conveyed, the distance over which they must be transported, and the conditions of the operating environment. The construction of a 3 ply belt offers a balance between strength and flexibility, allowing it to support significant loads while being able to navigate around pulleys and through conveyor systems efficiently.
Several types of rubber are used in the construction of conveyor belts, with the choice depending on the application’s specific requirements. Common types include Natural Rubber (NR), Styrene-Butadiene Rubber (SBR), and Nitrile Butadiene Rubber (NBR). Each type offers different properties:
Natural Rubber is prized for its superior elasticity and high tensile strength, making it suitable for belts that require flexibility and durability.
Stylish Butadiene Rubber (SBR) is often used for its good abrasion resistance and ability to perform well in moderate to heavy-duty applications.
Nitrile Butadiene Rubber (NBR) is selected for applications requiring resistance to oils, fats, and other chemicals.
Additionally, other synthetic rubbers like Ethylene Propylene Diene Monomer (EPDM) and Silicone might be used for special applications requiring high temperature resistance or other unique properties. The choice of rubber material affects the conveyor belt’s operational life, resistance to environmental conditions, and suitability for transporting specific types of materials. Manufacturers might also blend different rubbers to create composite materials that combine the desirable properties of each type to meet the specific demands of an application.
A conveyor belt ply is a layer of material that is part of the conveyor belt’s construction, enhancing its strength and stability. The term “ply” refers to the layers of fabric, rubber, or other materials that make up the body of the conveyor belt. Each ply contributes to the belt’s overall durability, tensile strength, and ability to transport materials over distances. Conveyor belts can have multiple plies, with the number of layers affecting the belt’s properties, such as impact resistance, flexibility, and load-carrying capacity. The choice of the number of plies often depends on the specific application requirements, including the type of materials being transported, the distance of transportation, and the operational environment. Understanding the ply count is essential for selecting the appropriate conveyor belt for an application, ensuring it can withstand the operational stresses while delivering optimal performance.
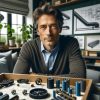
Jordan Smith, a seasoned professional with over 20 years of experience in the conveyor system industry. Jordan’s expertise lies in providing comprehensive solutions for conveyor rollers, belts, and accessories, catering to a wide range of industrial needs. From initial design and configuration to installation and meticulous troubleshooting, Jordan is adept at handling all aspects of conveyor system management. Whether you’re looking to upgrade your production line with efficient conveyor belts, require custom conveyor rollers for specific operations, or need expert advice on selecting the right conveyor accessories for your facility, Jordan is your reliable consultant. For any inquiries or assistance with conveyor system optimization, Jordan is available to share his wealth of knowledge and experience. Feel free to reach out at any time for professional guidance on all matters related to conveyor rollers, belts, and accessories.