Benefits of Using a 3 Ply Rubber Conveyor Belt
Conveyor belts are essential components in various industries, facilitating the efficient movement of materials and products. Among the different types of conveyor belts, the 3 ply rubber conveyor belt stands out for its durability and versatility. This type of belt is constructed with three layers of fabric, making it suitable for heavy-duty applications in industries such as mining, manufacturing, and food processing. In this blog, we will explore the key aspects of the 3 ply rubber conveyor belt, including its prices, dimensions, availability, and benefits. By understanding these features, you can make informed decisions when selecting the right conveyor belt for your needs.
What is a 3 Ply Rubber Conveyor Belt?
Definition and Explanation of “Ply” in Conveyor Belts
In the context of conveyor belts, the term “ply” refers to the layers of fabric that are embedded within the rubber belt. Each ply is typically a woven fabric that contributes to the overall strength and durability of the belt. The number of plies in a conveyor belt indicates the number of fabric layers present, which in turn affects the belt’s capacity to handle heavy loads, resist wear, and endure various industrial stresses.
A single-ply conveyor belt consists of one layer of fabric, while a 3 ply rubber conveyor belt consists of three layers. The more plies a belt has, the more robust and resistant it becomes to mechanical damage, making it suitable for more demanding applications.
Detailed Description of a 3 Ply Rubber Conveyor Belt
The 3 ply rubber conveyor belt is specifically designed to offer enhanced strength and durability. It is composed of three layers of fabric, each separated by a layer of rubber. These layers work together to provide a belt that is both flexible and resilient, capable of withstanding the rigors of heavy-duty industrial use.
Construction
The construction of a 3 ply rubber conveyor belt involves the integration of three distinct layers of fabric, which are usually made from materials such as polyester, nylon, or cotton. These fabric layers are embedded within layers of rubber, providing the belt with its necessary durability and flexibility. The rubber covers on both the top and bottom of the belt serve to protect the fabric layers from external wear and damage.
- Top Cover: The top rubber cover is designed to endure the abrasive nature of the materials being transported. It can vary in thickness, typically ranging from 1/16 inch to 1/4 inch, depending on the specific requirements of the application.
- Middle Layer: This is the core strength layer, consisting of the three plies of fabric. These plies are bonded together with layers of rubber, providing structural integrity and the ability to handle significant loads.
- Bottom Cover: The bottom rubber cover is usually slightly thinner than the top cover and is designed to protect the belt from the impact and wear that occur from contact with conveyor rollers and idlers.
Durability and Strength for Heavy-Duty Applications
The 3 ply rubber conveyor belt is particularly well-suited for heavy-duty applications where high strength and durability are essential. The three layers of fabric reinforcement ensure that the belt can handle substantial weight and resist stretching under load. This makes it ideal for industries such as mining, quarrying, and bulk material handling, where the belt needs to transport large, heavy, and abrasive materials continuously.
- Load Capacity: The multiple fabric layers allow the 3 ply rubber conveyor belt to support significant loads without compromising on flexibility. This is crucial in industries that require the transport of heavy goods over long distances.
- Wear Resistance: The thick rubber covers provide excellent resistance to wear and tear, ensuring a longer lifespan even in harsh operating conditions. The top cover’s thickness can be customized to suit the specific abrasiveness of the transported material.
- Flexibility: Despite its strength, the 3 ply rubber conveyor belt maintains a degree of flexibility that allows it to operate efficiently around conveyor pulleys and troughing idlers. This flexibility helps to prevent cracking and splitting, which can occur in less robust belts under similar conditions.
Benefits of a 3 Ply Rubber Conveyor Belt
- Enhanced Durability: The multi-layer construction provides superior resistance to physical damage and wear, extending the belt’s operational life.
- High Load Capacity: Capable of handling heavy and abrasive materials, making it suitable for demanding industrial environments.
- Versatility: The belt’s design allows it to be used in a wide range of applications, from mining to manufacturing and food processing.
- Cost-Effectiveness: Although it may have a higher initial cost compared to single-ply belts, the extended lifespan and reduced maintenance needs of a 3 ply rubber conveyor belt can lead to significant cost savings over time.
- Customization: The ability to customize the thickness of the top and bottom covers, as well as the materials used in the fabric plies, allows for tailored solutions to specific industrial needs.
The 3 ply rubber conveyor belt is a robust and versatile solution for heavy-duty conveyor systems. Its multi-layered construction provides the strength, durability, and flexibility needed to handle demanding industrial applications effectively. By understanding the features and benefits of the 3 ply rubber conveyor belt, industries can make informed decisions that enhance their operational efficiency and longevity of their conveyor systems.
Key Features and Benefits of the 3 Ply Rubber Conveyor Belt
The 3 ply rubber conveyor belt is renowned for its robustness and versatility, making it a preferred choice for numerous industrial applications. Its design incorporates several key features that collectively offer significant benefits, ensuring optimal performance in demanding environments.
Thick Top Cover
One of the standout features of the 3 ply rubber conveyor belt is its thick top cover. This cover plays a crucial role in protecting the belt’s fabric layers from the abrasive and damaging effects of the materials being transported.
- Enhanced Protection: The thick top cover provides an additional layer of defense against wear and tear. This is particularly important in industries where the belt is exposed to sharp, heavy, or abrasive materials that can quickly degrade thinner covers.
- Customizable Thickness: The thickness of the top cover can be customized based on the specific requirements of the application. Typically, it ranges from 1/16 inch to 1/4 inch, allowing for tailored solutions that maximize the belt’s lifespan and efficiency.
- Extended Service Life: By reducing the rate of wear and tear, the thick top cover extends the overall service life of the 3 ply rubber conveyor belt, leading to lower maintenance costs and less frequent belt replacements.
Durability
Durability is a hallmark of the 3 ply rubber conveyor belt, making it suitable for heavy-duty use in various industrial settings.
- Heavy-Duty Applications: The belt’s construction, featuring three layers of fabric reinforcement, ensures it can withstand the rigors of heavy-duty applications. This makes it ideal for industries such as mining, quarrying, and bulk material handling, where the belt must support substantial loads and endure continuous use.
- Strength and Stability: The multiple plies provide added strength and stability, preventing the belt from stretching or deforming under heavy loads. This structural integrity is crucial for maintaining consistent performance and preventing operational disruptions.
- Long-Term Reliability: The durability of the 3 ply rubber conveyor belt translates into long-term reliability, reducing downtime and enhancing productivity in industrial operations.
Flexibility
Despite its robust construction, the 3 ply rubber conveyor belt maintains a degree of flexibility that is essential for efficient operation.
- Handling Varying Loads: The belt’s flexibility allows it to accommodate varying loads and materials, making it versatile enough to be used in different industrial processes. Whether transporting light or heavy materials, the belt can adapt without compromising performance.
- Smooth Operation: Flexibility ensures that the belt can navigate around conveyor pulleys and troughing idlers smoothly, minimizing the risk of cracking or splitting. This smooth operation is vital for maintaining the integrity of the conveyor system and ensuring continuous material flow.
- Adaptability: The belt’s ability to flex and bend as needed makes it suitable for complex conveyor layouts, including those with curves or inclines. This adaptability enhances the overall efficiency of the conveyor system.
Resistance
The 3 ply rubber conveyor belt is designed to offer high resistance to various environmental and operational challenges, ensuring it can perform reliably in harsh conditions.
- Abrasion Resistance: The belt’s top cover is formulated to resist abrasion, which is crucial for maintaining its structural integrity when exposed to abrasive materials. This resistance helps prevent surface damage and prolongs the belt’s service life.
- Heat Resistance: In environments where high temperatures are a concern, such as in industrial processing or manufacturing, the belt’s heat-resistant properties ensure it can withstand elevated temperatures without degrading. This capability is essential for maintaining safe and efficient operations.
- Chemical Resistance: The 3 ply rubber conveyor belt is also resistant to chemicals, making it suitable for industries where exposure to various chemicals is common. This resistance protects the belt from chemical damage, ensuring it remains functional and safe to use.
- Overall Durability: The combination of abrasion, heat, and chemical resistance makes the 3 ply rubber conveyor belt exceptionally durable, capable of performing in a wide range of challenging environments.
Summary of Benefits
The 3 ply rubber conveyor belt’s features collectively offer numerous benefits that enhance its performance and reliability in industrial applications:
- Enhanced Protection: The thick top cover provides superior protection against wear and tear, extending the belt’s service life.
- Suitability for Heavy-Duty Use: The belt’s durability ensures it can handle heavy loads and continuous use in demanding environments.
- Operational Flexibility: Its flexibility allows it to adapt to varying loads and complex conveyor layouts, ensuring smooth and efficient operation.
- Resistance to Environmental Challenges: High resistance to abrasion, heat, and chemicals ensures the belt can perform reliably in harsh conditions.
The 3 ply rubber conveyor belt is a robust and versatile solution designed to meet the demands of heavy-duty industrial applications. Its thick top cover, durability, flexibility, and resistance properties make it an invaluable asset for industries requiring reliable and long-lasting conveyor belts.
Dimensions and Specifications of 3 Ply Rubber Conveyor Belt
Understanding the dimensions and specifications of the 3 ply rubber conveyor belt is crucial for selecting the right belt for your specific industrial needs. This section delves into the typical thickness range, standard dimensions, and example specifications to help you make informed decisions.
3 Ply Conveyor Belt Thickness
Typical Thickness Range: 5 – 10 mm
The thickness of the 3 ply rubber conveyor belt generally ranges from 5 mm to 10 mm. This range is designed to provide a balance between flexibility and strength, ensuring the belt can handle various loads and applications effectively.
- 5 mm Thickness: At the lower end of the range, a 5 mm thick belt offers greater flexibility and is suitable for lighter loads or applications where the belt needs to navigate tight curves and inclines. This thickness is often used in industries where precision and light material handling are paramount.
- 10 mm Thickness: At the higher end of the range, a 10 mm thick belt provides enhanced strength and durability, making it ideal for heavy-duty applications. This thickness can support substantial weights and resist significant wear and tear, which is essential in industries like mining and bulk material handling.
Importance of Choosing the Right Thickness
Selecting the appropriate thickness for a 3 ply rubber conveyor belt is critical for ensuring optimal performance and longevity. The right thickness will depend on several factors, including the nature of the materials being transported, the load capacity required, and the operational environment.
- Material Handling: For abrasive or heavy materials, a thicker belt is preferable as it provides additional protection and durability.
- Load Capacity: Heavier loads require a thicker belt to prevent stretching and deformation, ensuring the belt maintains its integrity and efficiency over time.
- Operational Conditions: In environments with harsh conditions, such as extreme temperatures or exposure to chemicals, a thicker belt with specialized cover compounds may be necessary to withstand these challenges.
3 Ply Rubber Conveyor Belt Dimensions
Standard Widths and Lengths Available
The 3 ply rubber conveyor belt comes in various standard widths and lengths to cater to a wide range of industrial applications. Standard widths typically range from 300 mm to 2400 mm, while lengths can be customized based on specific requirements.
- Standard Widths: Common widths include 300 mm, 600 mm, 900 mm, 1200 mm, 1500 mm, 1800 mm, and 2400 mm. These widths are designed to fit standard conveyor systems, making them a versatile choice for many industries.
- Standard Lengths: Lengths can vary significantly, with options ranging from short lengths of a few meters to long rolls that span hundreds of meters. The length chosen will depend on the conveyor system’s design and the distance materials need to be transported.
Custom Dimensions for Unique Industrial Needs
While standard dimensions are suitable for many applications, some industries require custom dimensions to meet unique operational needs. Customization options include specific widths, lengths, and even tailored cover thicknesses to address particular challenges or enhance performance.
- Customized Widths and Lengths: For specialized conveyor systems, custom widths and lengths ensure a perfect fit and optimal performance. This customization allows industries to maximize efficiency and reduce waste.
- Tailored Cover Thicknesses: Customizing the top and bottom cover thicknesses can provide additional protection and durability, especially in environments with extreme wear or exposure to harsh chemicals.
Example Specifications
Top Cover Thickness: 1/4 inch
The top cover of the 3 ply rubber conveyor belt typically features a thickness of 1/4 inch. This substantial thickness provides excellent protection against abrasion and impacts, ensuring the belt can handle heavy and abrasive materials without premature wear.
- Abrasion Resistance: The 1/4 inch top cover enhances the belt’s resistance to abrasion, making it ideal for industries where the belt is exposed to sharp or coarse materials.
- Impact Protection: The thicker top cover also provides better impact protection, reducing the risk of damage from heavy or falling objects.
Bottom Cover Thickness: Customizable
The bottom cover thickness of the 3 ply rubber conveyor belt can be customized to suit specific operational requirements. While the bottom cover is generally thinner than the top cover, customization allows for enhanced protection and durability based on the conveyor system’s design and the materials being handled.
- Standard Bottom Cover: A standard bottom cover thickness might range from 1.5 mm to 3 mm, providing adequate protection against wear from conveyor rollers and idlers.
- Enhanced Bottom Cover: In applications where the belt is exposed to significant wear or harsh conditions, a thicker bottom cover can be specified to improve durability and extend the belt’s service life.
The 3 ply rubber conveyor belt’s dimensions and specifications are tailored to meet a wide range of industrial needs. The typical thickness range of 5 to 10 mm ensures a balance between flexibility and strength, while standard and custom widths and lengths provide versatility for various conveyor systems. The example specifications, including a 1/4 inch top cover and customizable bottom cover, highlight the belt’s ability to handle demanding applications with enhanced durability and protection. By understanding these key dimensions and specifications, industries can select the right 3 ply rubber conveyor belt to optimize their operational efficiency and longevity.
Pricing and Cost Considerations for a 3 Ply Rubber Conveyor Belt
Understanding the pricing and cost considerations of a 3 ply rubber conveyor belt is essential for making informed purchasing decisions. This section explores the factors that influence the price, the availability and benefits of used conveyor belts, and offers tips for finding cost-effective solutions.
3 Ply Rubber Conveyor Belt Price
Factors Influencing Price
Several factors affect the price of a 3 ply rubber conveyor belt. These include:
- Material Quality: Higher quality materials, such as premium rubber compounds and durable fabrics, increase the cost but offer better performance and longer lifespan.
- Dimensions: The width, length, and thickness of the belt directly impact the price. Larger dimensions require more material and thus cost more.
- Supplier: Prices can vary significantly between suppliers based on their production processes, overhead costs, and markup rates.
- Customization: Custom dimensions, special cover compounds, and tailored specifications can add to the cost.
- Market Demand: Fluctuations in market demand for raw materials and finished products can influence pricing.
- Geographic Location: Transportation costs and local economic conditions affect pricing.
- Brand Reputation: Well-known brands with a reputation for quality and reliability may charge a premium.
- Additional Features: Features such as enhanced resistance to heat, chemicals, or abrasion can increase the price.
Average Price Range and Cost Examples
The price of a 3 ply rubber conveyor belt typically ranges from $15 to $40 per linear foot, depending on the factors mentioned above. For instance, a standard 3 ply rubber conveyor belt measuring 36 inches wide and 10 feet long might cost between $150 and $400.
Used Conveyor Belt Rubber for Sale
Availability of Second-Hand Options
Used conveyor belts are available from various sources, including industrial surplus stores, online marketplaces, and specialized suppliers. These belts can offer significant cost savings compared to new belts.
Benefits of Purchasing Used Belts
- Cost Savings: Used belts are typically much cheaper than new ones.
- Immediate Availability: Used belts can often be sourced quickly, reducing downtime.
- Sustainability: Reusing belts reduces waste and supports environmental sustainability.
- Proven Performance: If well-maintained, used belts can still offer good performance.
- Variety: A wide range of used belts is available, catering to different needs.
- Negotiable Prices: Prices for used belts are often negotiable, providing room for bargains.
- Short-Term Solutions: Ideal for short-term projects or temporary setups.
- Reduced Depreciation: Used belts have already undergone most of their depreciation, offering better value.
Risks of Purchasing Used Belts
- Unknown History: The previous usage history may not be fully known, leading to potential issues.
- Wear and Tear: Used belts may have existing wear and tear that reduces their lifespan.
- Limited Warranty: Typically, used belts come with limited or no warranty.
- Compatibility Issues: Ensuring that a used belt is compatible with existing equipment can be challenging.
- Hidden Damage: Potential for hidden damage that might not be immediately visible.
- Reduced Performance: Used belts may not perform as well as new ones in demanding applications.
3 Ply Rubber Conveyor Belt Cost
Cost Comparison Between New and Used Belts
Aspect | New Belt Cost | Used Belt Cost |
---|---|---|
Initial Price | Higher | Lower |
Longevity | Longer | Shorter |
Warranty | Standard Warranty | Limited/No Warranty |
Performance | Optimal | Variable |
Customization | Available | Limited |
Availability | May require lead time | Immediate |
Tips for Finding Cost-Effective Solutions
- Compare Multiple Suppliers: Get quotes from several suppliers to find the best deal.
- Consider Used Options: Evaluate the condition of used belts for potential savings.
- Bulk Purchases: Buying in bulk can often result in discounts.
- Off-Peak Purchasing: Prices may be lower during off-peak times.
- Negotiate Prices: Don’t hesitate to negotiate with suppliers for better terms.
- Look for Promotions: Watch for sales and promotions from suppliers.
- Evaluate Total Cost of Ownership: Consider long-term costs, including maintenance and replacement.
- Seek Local Suppliers: Reduce shipping costs by purchasing from local suppliers.
- Check for Compatibility: Ensure the belt meets your specifications to avoid costly replacements.
- Read Reviews and Testimonials: Learn from other customers’ experiences to identify reliable suppliers and products.
By understanding these pricing and cost considerations, you can make more informed decisions when purchasing a 3 ply rubber conveyor belt, ensuring you balance quality, performance, and cost-effectiveness to meet your specific industrial needs.
Availability and Where to Buy 3 Ply Rubber Conveyor Belt
3 Ply Rubber Conveyor Belt Near Me
When searching for a “3 ply rubber conveyor belt near me,” it’s essential to consider local suppliers and distributors. Local sourcing not only supports the regional economy but also ensures faster delivery times and easier access to customer support. Here are eight key importance of sourcing from reputable local suppliers:
- Quality Assurance: Reputable suppliers often adhere to strict quality standards, ensuring you receive durable and reliable products.
- Expertise: Local suppliers are familiar with regional industry requirements and can provide tailored advice and solutions.
- Quick Turnaround: Proximity means quicker delivery times, reducing downtime and increasing productivity.
- Customer Service: Easier access to customer support for troubleshooting, maintenance, and after-sales service.
- Cost Savings: Reduced shipping costs and potential bulk purchasing discounts.
- Support Local Economy: Purchasing from local suppliers helps sustain the local economy and community.
- Customization: Local suppliers can offer customized solutions to meet specific needs and requirements.
- Sustainable Practices: Reduced transportation distances contribute to lower carbon footprints, supporting environmental sustainability.
Online Marketplaces
In today’s digital age, online marketplaces have become a popular avenue for purchasing conveyor belts. These platforms offer a wide range of products, including the “3 ply rubber conveyor belt,” catering to various industrial needs.
Popular Online Platforms
- Amazon: Known for its extensive range of products and reliable delivery services.
- Alibaba: A global platform that connects buyers with manufacturers, often at competitive prices.
- eBay: Offers both new and used conveyor belts, allowing for more cost-effective solutions.
- Direct Industry: A specialized platform for industrial products, ensuring quality and reliability.
- IndiaMART: Popular in Asia, providing a variety of conveyor belt options and direct supplier contact.
Pros and Cons of Buying Online vs. In-Store
Pros of Buying Online:
- Convenience: Shop from the comfort of your office or home, 24/7.
- Variety: Access to a broader range of products from global suppliers.
- Price Comparison: Easy to compare prices and features across different sellers.
- Reviews and Ratings: Customer reviews provide insights into product performance and supplier reliability.
Cons of Buying Online:
- Lack of Physical Inspection: Inability to physically inspect the product before purchase.
- Shipping Costs: Potential high shipping costs for bulky items.
- Delayed Delivery: Shipping times can vary, sometimes causing delays in receiving the product.
- Return Issues: Returning defective or unsuitable products can be cumbersome and time-consuming.
3 Ply Rubber Conveyor Belt for Sale
When looking for a “3 ply rubber conveyor belt for sale,” identifying top suppliers and manufacturers is crucial. These entities ensure the product’s quality, performance, and longevity, meeting the rigorous demands of various industries.
Highlighting Top Suppliers and Manufacturers
- Fenner Dunlop: Renowned for their high-quality conveyor belts, Fenner Dunlop offers robust solutions for heavy-duty applications.
- Continental AG: A leading manufacturer known for innovative conveyor belt technology and comprehensive service offerings.
- Bridgestone: Specializes in producing durable and efficient conveyor belts tailored for industrial use.
- Goodyear: Offers a range of conveyor belts designed for different industrial environments, known for their durability and performance.
- Phoenix Conveyor Belt Systems: Provides customized conveyor belt solutions with a focus on innovation and reliability.
Case Studies and Success Stories
- Continental AG: Known for their innovative solutions, Continental AG supplied a 3 ply rubber conveyor belt to a major mining operation in Australia. The belt’s durability and performance significantly improved the efficiency of the mining process, leading to increased productivity and reduced downtime.
- Fenner Dunlop: Fenner Dunlop’s conveyor belts were used in a large-scale manufacturing plant in the United States. The 3 ply rubber conveyor belt provided excellent resistance to wear and tear, ensuring a smooth and continuous operation for the assembly line, ultimately resulting in higher output and lower maintenance costs.
- Goodyear Belting: Goodyear Belting’s products have been utilized in various industries, including automotive and food processing. A notable success story includes their collaboration with a major car manufacturer, where the 3 ply rubber conveyor belt helped streamline the production process, enhancing overall efficiency and product quality.
Whether you choose to purchase a 3 ply rubber conveyor belt from local suppliers or through online marketplaces, it is crucial to consider the reputation and reliability of the supplier. By selecting top manufacturers and leveraging the success stories of reputable brands, you can ensure that your investment in a conveyor belt will yield long-term benefits for your operations.
Applications and Industries of 3 Ply Rubber Conveyor Belt
Common Industries Using 3 Ply Rubber Conveyor Belts
The “3 ply rubber conveyor belt” is a versatile and durable solution that finds applications across a wide range of industries. Its robust construction and flexibility make it ideal for handling various materials and processes efficiently. Below are some of the common industries utilizing this type of conveyor belt:
Mining, Quarrying, and Material Handling
In the mining and quarrying sectors, the “3 ply rubber conveyor belt” is essential for transporting heavy materials such as ore, coal, and aggregates. Companies like Fenner Dunlop and Continental AG supply these belts to ensure durability and reliability under harsh conditions. The belts must withstand abrasion, impact, and heavy loads, making the 3 ply construction perfect for these demanding applications.
Manufacturing and Production Lines
Manufacturing industries, ranging from automotive to electronics, rely on “3 ply rubber conveyor belts” for efficient and seamless production processes. Goodyear and Bridgestone provide conveyor belts that cater to specific manufacturing needs, including assembly line operations, material transport, and automated production systems. The belts’ durability and flexibility help minimize downtime and enhance productivity.
Food Processing and Packaging
In the food processing and packaging industry, hygiene and cleanliness are paramount. Phoenix Conveyor Belt Systems offers specialized 3 ply rubber conveyor belts designed to meet stringent food safety standards. These belts are used in processing plants to transport raw materials, handle packaged goods, and maintain clean, efficient operations. The belts’ smooth surface and easy-to-clean properties ensure compliance with food safety regulations.
Specific Use Cases and Examples of Successful Implementations
The versatility of the 3 ply rubber conveyor belt is evident through various successful implementations across different industries. Here are six examples:
- Rio Tinto – Mining Operations:
Rio Tinto, a leading global mining group, utilizes Fenner Dunlop’s 3 ply rubber conveyor belts in their mining operations. These belts have significantly improved material handling efficiency and reduced maintenance costs, thanks to their robustness and durability. - Ford Motor Company – Automotive Manufacturing:
Ford Motor Company uses Goodyear’s 3 ply rubber conveyor belts in their assembly lines. The belts’ flexibility and strength have enhanced the production process by ensuring smooth and continuous movement of parts and components, thereby increasing overall productivity. - Nestlé – Food Processing:
Nestlé, a global food and beverage leader, implemented Phoenix Conveyor Belt Systems’ 3 ply rubber conveyor belts in their chocolate processing plants. The belts’ compliance with food safety standards and ease of cleaning have optimized their production lines, ensuring high hygiene levels and efficient operations. - Coca-Cola – Beverage Packaging:
Coca-Cola employs Bridgestone’s 3 ply rubber conveyor belts in their bottling and packaging facilities. These belts have improved the handling of bottles and cans, reducing downtime and increasing throughput. The belts’ reliability has been crucial in maintaining continuous production flows. - Bosch – Electronics Manufacturing:
Bosch, a global supplier of technology and services, uses Continental AG’s 3 ply rubber conveyor belts in their electronics manufacturing plants. The belts have facilitated the smooth transport of delicate electronic components, minimizing damage and enhancing production efficiency. - Procter & Gamble – Consumer Goods Production:
Procter & Gamble, a multinational consumer goods corporation, integrates Fenner Dunlop’s 3 ply rubber conveyor belts in their production lines. The belts’ durability and adaptability have allowed for efficient handling of various products, from packaging materials to finished goods, ensuring consistent production outputs.
The 3 ply rubber conveyor belt is a critical component across multiple industries, offering durability, flexibility, and efficiency. Its successful implementations in companies like Rio Tinto, Ford Motor Company, Nestlé, Coca-Cola, Bosch, and Procter & Gamble demonstrate its versatility and reliability in meeting diverse industrial needs.
Maintenance and Care of 3 Ply Rubber Conveyor Belt
Proper maintenance and care are crucial to prolonging the life and ensuring the optimal performance of a 3 ply rubber conveyor belt. Implementing a comprehensive maintenance strategy can prevent costly downtime and extend the belt’s lifespan, ultimately enhancing operational efficiency and productivity.
Tips for Prolonging the Life of a 3 Ply Rubber Conveyor Belt
- Regular Cleaning: Keep the belt clean by regularly removing debris and spilled materials. This prevents excessive wear and tear caused by abrasive particles.
- Proper Tensioning: Ensure the belt is correctly tensioned to avoid slippage and excessive stretching. Over-tensioning can damage the belt, while under-tensioning can cause misalignment.
- Alignment Checks: Frequently check and adjust the belt alignment to prevent tracking issues. Misaligned belts can lead to uneven wear and reduced efficiency.
- Lubrication of Bearings: Regularly lubricate bearings to reduce friction and prevent overheating, which can damage the belt and other components.
- Inspection for Wear and Damage: Conduct regular inspections to identify signs of wear, such as fraying edges, cracks, or splits. Early detection allows for timely repairs and prevents further damage.
- Load Management: Avoid overloading the belt to prevent excessive strain and potential damage. Distribute loads evenly to maintain balance and stability.
- Avoid Contaminants: Keep the belt free from contaminants such as oil, grease, and chemicals that can degrade the rubber material and shorten the belt’s life.
- Use Proper Cleaning Agents: When cleaning the belt, use appropriate cleaning agents that do not harm the rubber material. Avoid harsh chemicals that can cause deterioration.
- Monitor Temperature: Ensure the operating temperature is within the belt’s specified range. Excessive heat can weaken the belt material, while extreme cold can make it brittle.
- Training and Education: Train employees on proper handling and maintenance procedures. Educated personnel are more likely to follow best practices, reducing the risk of damage.
- Scheduled Downtime: Plan regular downtime for thorough inspections and maintenance tasks. Preventive maintenance during scheduled downtimes can avoid unexpected failures.
- Record Keeping: Maintain detailed records of maintenance activities, inspections, and repairs. This helps track the belt’s condition over time and plan future maintenance effectively.
Importance of Regular Inspections and Timely Repairs
- Prevent Catastrophic Failures: Regular inspections can identify minor issues before they escalate into major problems, preventing catastrophic failures that could halt operations.
- Extend Belt Lifespan: Timely repairs address wear and tear promptly, significantly extending the belt’s useful life and reducing replacement costs.
- Maintain Safety Standards: Regular checks ensure the conveyor system operates safely, minimizing the risk of accidents and injuries caused by faulty belts.
- Improve Operational Efficiency: Well-maintained belts operate smoothly, enhancing overall system efficiency and reducing energy consumption.
- Cost Savings: Preventive maintenance reduces the need for expensive emergency repairs and minimizes costly downtime.
- Compliance with Regulations: Regular maintenance ensures compliance with industry regulations and standards, avoiding potential fines and legal issues.
- Enhanced Performance: Properly maintained belts perform at their optimal level, ensuring reliable and consistent operation.
Maintenance Practices to Ensure Optimal Performance
- Visual Inspections: Conduct daily visual inspections to identify visible signs of wear, damage, or misalignment. This quick check helps catch issues early.
- Scheduled Maintenance Checks: Implement a schedule for more thorough inspections and maintenance tasks, such as checking tension, alignment, and lubrication.
- Vibration Analysis: Use vibration analysis tools to detect unusual vibrations that could indicate underlying issues with the belt or other components.
- Thermal Imaging: Employ thermal imaging cameras to monitor the belt’s temperature, identifying hot spots that could signify potential problems.
- Ultrasonic Testing: Utilize ultrasonic testing to detect internal flaws or weaknesses in the belt material that are not visible to the naked eye.
- Load Testing: Periodically perform load testing to ensure the belt can handle the required capacity without issues, ensuring it operates within its design limits.
By following these maintenance and care guidelines, businesses can ensure that their 3 ply rubber conveyor belt remains in excellent condition, providing reliable and efficient service for an extended period. Regular inspections, timely repairs, and proactive maintenance practices are key to maximizing the belt’s performance and longevity.
FAQs about 3 Ply Rubber Conveyor Belt
A 3 ply conveyor belt typically has a thickness ranging from 7 to 8 millimeters (0.28 to 0.31 inches). The actual thickness can vary depending on the materials used and the specific construction of the belt. Each “ply” is a layer of fabric or other material that provides strength and flexibility. In a 3 ply belt, there are three such layers sandwiched between the top and bottom cover materials. This construction gives the belt added durability and strength, making it suitable for heavy-duty applications where higher tensile strength is required. The cover materials, often made from rubber or PVC, also contribute to the overall thickness and protection against wear and tear.
The primary difference between 2 ply and 3 ply conveyor belts lies in the number of fabric layers and their resulting strength and durability. A 2 ply belt has two layers of fabric, while a 3 ply belt has three. The additional ply in a 3 ply belt increases its tensile strength, making it better suited for handling heavier loads and more demanding applications. This extra layer also enhances the belt’s resistance to stretching and wear. As a result, 3 ply belts are typically used in more rigorous environments, whereas 2 ply belts might be sufficient for lighter duty tasks. The choice between the two depends on the specific requirements of the conveyor system, including load capacity, operational conditions, and budget considerations.
In a conveyor belt, “ply” refers to the layers of fabric or material that provide structural support and strength. Each ply is a sheet of fabric, usually made from materials such as polyester, nylon, or cotton, which is impregnated with a rubber or PVC compound. The number of plies in a belt directly influences its tensile strength, durability, and flexibility. For example, a belt with more plies can handle higher tension and heavier loads. The plies are sandwiched between the top and bottom cover materials, which protect the internal layers from abrasion, chemicals, and environmental factors. Understanding the ply construction is crucial when selecting a conveyor belt for specific applications, as it affects performance and longevity.
A 4 ply conveyor belt typically has a thickness ranging from 10 to 12 millimeters (0.39 to 0.47 inches). The exact thickness can vary based on the materials used in the construction of both the plies and the cover layers. The four layers of fabric within the belt provide enhanced strength and resistance to stretching, making these belts suitable for very heavy-duty applications. The additional plies contribute to the belt’s overall durability and ability to withstand higher tension and more abrasive conditions. As with other ply configurations, the outer cover materials also play a significant role in determining the total thickness and the belt’s resistance to wear and environmental damage.
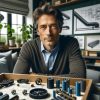
Jordan Smith, a seasoned professional with over 20 years of experience in the conveyor system industry. Jordan’s expertise lies in providing comprehensive solutions for conveyor rollers, belts, and accessories, catering to a wide range of industrial needs. From initial design and configuration to installation and meticulous troubleshooting, Jordan is adept at handling all aspects of conveyor system management. Whether you’re looking to upgrade your production line with efficient conveyor belts, require custom conveyor rollers for specific operations, or need expert advice on selecting the right conveyor accessories for your facility, Jordan is your reliable consultant. For any inquiries or assistance with conveyor system optimization, Jordan is available to share his wealth of knowledge and experience. Feel free to reach out at any time for professional guidance on all matters related to conveyor rollers, belts, and accessories.