The Impact of 4 Conveyor Roller on Industry Efficiency
Conveyor rollers play a crucial role in the seamless operation of numerous industrial applications, facilitating the efficient movement of goods and materials across factory floors and assembly lines. The 4 conveyor roller, in particular, stands out for its versatility and is widely adopted across several sectors including manufacturing, packaging, and distribution. This specific size is favored due to its optimal balance of strength and flexibility, making it suitable for a broad range of materials and weights. Its common uses span various industries where precision and reliability are paramount, enhancing productivity and operational efficacy in complex industrial environments.
What Is 4 Conveyor Roller
The 4 conveyor roller is a pivotal component in numerous automated systems, designed to facilitate smooth and efficient transport of materials across various industrial settings. Its popularity stems from its optimal size, which perfectly suits a range of operational needs from light to moderate duty tasks. Here’s a closer look at why these rollers are such a popular choice in the industry:
- Size Advantage: The 4″ diameter is compact enough to fit into various systems while providing adequate surface to support diverse materials.
- Versatile Use: These rollers are commonly employed across numerous sectors, such as automotive assembly, food processing, and more, showcasing their flexibility.
- Balance of Properties: They offer an excellent balance between lightweight design and robust capacity to handle substantial weights, essential for dynamic industrial environments.
- Industry Standard: Their adoption as a standard size facilitates compatibility and interchangeability across different conveyor systems.
- Integration Ease: The 4″ rollers are designed to be easily integrated into existing setups, minimizing the need for extensive modifications.
- Precision in Operation: They are engineered for precision, crucial in applications where accurate material placement is key.
- Durability: Constructed to withstand extensive use, these rollers are built to last, reducing downtime and maintenance costs.
- Low Maintenance: These rollers are designed with simplicity in mind, requiring less frequent upkeep to maintain optimal functionality.
- Cost-Effective: Due to their standardized production, 4″ rollers are typically more affordable than custom-sized options, making them a cost-efficient choice.
Key Features of 4 Conveyor Roller
The 4 conveyor roller offers specific features that enhance its utility and performance in industrial applications. From material options to structural design, these features are tailored to meet diverse operational demands. Here’s what makes 4 conveyor rollers a fundamental element in material handling systems:
- Diameter: The 4-inch diameter of these rollers is ideal for ensuring the necessary contact area with conveyed items, supporting efficient movement.
- Material Varieties: Available in steel, stainless steel, or plastic, each material provides unique benefits, such as durability or corrosion resistance.
- Load Capacity: These rollers are capable of supporting varying loads, making them suitable for different industrial applications.
- Axle Options: Offered with several axle configurations to cater to different assembly requirements and load types.
- Bearing Choices: Equipped with a range of bearing options, from non-precision to precision, affecting both load capacity and operational speed.
- Surface Treatments: Options like galvanized, rubber-coated, or polyurethane-coated surfaces help handle various environmental conditions.
- Environmental Suitability: They are designed to perform under diverse environmental conditions including dusty, wet, or corrosive settings.
- Operational Quietness: Engineered for reduced noise levels, making them suitable for environments where noise reduction is crucial.
- Customization Capability: These rollers can be customized in terms of length and feature additions like grooves or sprockets to fulfill specific operational needs.
Each feature of the 4 conveyor roller is meticulously designed to optimize performance and enhance durability, ensuring they meet the rigorous demands of industrial applications.
Types of Conveyor Rollers
In the world of material handling, conveyor rollers are indispensable for their ability to facilitate smooth, efficient product movement. Each type of conveyor roller is designed with specific features to meet varied industrial demands. Here, we explore the variety of conveyor roller types, including gravity rollers, heavy-duty rollers, and custom designs, and examine how the 4 conveyor roller fits within these categories.
Overview of Different Conveyor Roller Types
Conveyor rollers are fundamental components in various material handling systems, designed to facilitate the movement of goods across industrial environments. Each type of conveyor roller is engineered to meet specific operational demands, enhancing productivity and reducing labor requirements. Here’s an exploration of the most common types of conveyor rollers used in industry today:
- Gravity Rollers: These are the simplest and most cost-effective type. They rely on gravity to move products along a decline or manual force on a horizontal setup.
- Heavy-Duty Rollers: Built to handle higher loads and more strenuous conditions, heavy-duty rollers are often made from stronger materials like thick steel.
- Custom Conveyor Rollers: Tailored to specific needs, these can include variations in size, material, bearing types, and surface treatments to handle unique applications.
- Grooved Rollers: Designed with grooves that are compatible with specific drive belts or chains, these rollers are essential for precise motion control.
- Polyurethane-Coated Rollers: These offer enhanced grip and noise reduction, ideal for environments where noise is a concern or where delicate handling is necessary.
- Stainless Steel Rollers: Best suited for environments prone to rust or where cleanliness is crucial, such as food processing or pharmaceutical industries.
Detailed Look at How 4 Conveyor Rollers Fit Within These Categories
The 4 conveyor roller is a versatile component that adapts well to various types of conveyor systems. Here’s how this specific size fits into and enhances each roller category:
- Versatility in Gravity Systems: The 4 conveyor roller is commonly used in gravity roller systems due to its ability to handle sufficient loads with minimal effort, making it a versatile choice.
- Adaptability in Heavy-Duty Applications: Thanks to its robust build, the 4 conveyor roller can be adapted for heavy-duty applications by using thicker tubing and stronger axle materials.
- Customization Capabilities: The 4 conveyor roller offers extensive customization options, including length variations and different axle types, to meet specific industrial requirements.
- Integration with Grooved Systems: 4 rollers can be easily integrated into grooved systems, with custom grooving to fit belts or chains for improved drive compatibility.
- Enhanced Functionality with Polyurethane Coating: Applying a polyurethane coat can enhance the functionality of a 4 conveyor roller, increasing grip and reducing operational noise.
- Durability in Corrosive Environments: When made from stainless steel, the 4″ roller excels in corrosive environments, maintaining functionality without succumbing to rust or decay.
- Precision Handling: Its optimal diameter allows for precise handling in automated systems, crucial for industries requiring exact material placement.
- Ease of Maintenance: Due to its standard size, the 4 conveyor roller is easier to maintain and replace, offering a practical solution for continuous operations.
- Economic Efficiency: Being a common size, the 4 conveyor roller is often more economically efficient due to mass production benefits, reducing costs for businesses.
The 4 conveyor roller, with its myriad of features and adaptabilities, exemplifies how one component can meet diverse industrial needs through careful selection and customization.
Applications of 4 Conveyor Rollers in Industry
The 4 conveyor roller is a vital component in various industrial sectors, offering tailored solutions to improve operational efficiencies and handle diverse material loads. This section explores specific real-world applications of the 4 conveyor roller across different industries and discusses the benefits that these rollers bring to each application.
Examples of Industrial Applications
The 4 conveyor roller is indispensable in various sectors due to its efficiency and versatility. It’s particularly beneficial in environments where reliability and durability are paramount. This segment outlines specific industries where the 4 conveyor roller is integral, illustrating its wide-ranging applicability and key roles in facilitating complex industrial processes.
- Automotive Assembly Lines: 4 conveyor rollers are used to transport parts and sub-assemblies across different stages of the assembly process, helping to streamline production and reduce manual handling.
- Food and Beverage Manufacturing: In this sector, 4 rollers are used in processing lines and packaging areas to move products through filling, sealing, and packing processes, ensuring gentle handling of delicate items.
- Pharmaceutical Packaging: These rollers are employed in the clean rooms of pharmaceutical plants to transport drugs and other sensitive materials, supporting strict hygiene and precision handling requirements.
- Logistics and Distribution Centers: 4″ rollers facilitate the movement of goods in warehouses, from sorting to packaging and dispatch, enhancing the speed and accuracy of order fulfillment.
- Electronics Manufacturing: Used in the assembly lines for electronic goods where precision and anti-static properties are critical, 4 conveyor rollers help in the safe handling of sensitive components.
- Agricultural Equipment Manufacturing: These rollers support the heavy-duty handling required in the manufacturing and assembly of large agricultural machines, providing durability and strength.
Benefits of Using 4″ Rollers in These Applications
The adoption of 4 conveyor rollers brings numerous advantages to industrial operations, enhancing not just productivity but also operational dynamics. Below are key benefits that underscore the value of incorporating these rollers in various industry applications.
- Improved Load Handling: The 4″ diameter offers optimal balance, enabling it to handle a variety of loads efficiently, which is essential for industries like automotive and agricultural equipment manufacturing.
- Enhanced Efficiency: By facilitating quicker movement of materials, these rollers significantly reduce cycle times and increase throughput in high-volume environments such as logistics centers.
- Versatility: The 4 conveyor roller can be adapted for use in different environments, whether it’s the high sanitation requirements of food processing or the ruggedness needed in industrial manufacturing.
- Reduced Operational Costs: Efficient movement means less wear on the system and lower energy costs, contributing to overall reduced operational expenses.
- Increased Safety: Their stable and reliable transport of goods reduces the risk of accidents and damage, enhancing workplace safety.
- Easy Integration: Due to their standard size, 4″ rollers are easily integrated into existing systems without the need for significant modifications, facilitating upgrades and expansions.
- Customizability: These rollers can be customized with different materials and coatings to meet specific industry needs, such as non-marking rubber for delicate surfaces in electronics manufacturing.
- Low Maintenance Requirements: The design and materials used for 4 conveyor roller often require less maintenance, thus minimizing downtime and maintenance costs.
- Improved Product Quality: Consistent and gentle handling of products reduces damages and improves the quality of the final goods, particularly important in industries like pharmaceuticals and food processing.
The 4 conveyor roller exemplifies a versatile and efficient solution that enhances productivity and operational capabilities across a broad spectrum of industrial applications. Its adaptability and the numerous benefits it offers make it a fundamental component in any material handling setup.
How to Choose the Right 4 Conveyor Roller
Choosing the right 4 conveyor roller is pivotal for maximizing the performance and efficiency of your conveyor system. The selection process should take into account a variety of factors that influence the functionality and longevity of the roller in specific operational contexts. Understanding these factors will help ensure that the roller you choose not only fits within your system but also enhances its overall reliability and effectiveness. Here are the essential considerations to guide you in selecting the ideal conveyor roller for your needs.
Factors to Consider When Selecting a Conveyor Roller
Understanding these factors will help ensure that the roller you choose not only fits within your system but also enhances its overall reliability and effectiveness. Here are the essential considerations to guide you in selecting the ideal conveyor roller for your needs.
- Load Capacity: Consider the maximum weight the rollers need to support. The chosen roller must be able to handle the load without deforming or failing.
- Operational Speed: The speed at which the conveyor will operate often determines the type of roller needed. High-speed operations may require rollers with better bearings and balance to operate smoothly.
- Work Environment: Rollers must be suitable for the environment in which they will operate. Factors like temperature, moisture, and exposure to chemicals should influence the material and design of the roller.
- Product Type: The nature of the products being conveyed (e.g., their size, shape, and material) can affect roller choice. For delicate or irregular-shaped products, softer materials or rollers with a non-marking surface might be necessary.
- Conveyor Length and Width: The dimensions of the conveyor system influence the size and spacing of the rollers. Longer conveyors might need more robust rollers to prevent sagging.
- Durability Requirements: Depending on the expected usage and the quality of the conveyor, the durability of the rollers can be a critical factor. More durable rollers reduce the frequency of replacements.
- Maintenance Needs: Some rollers are easier to maintain than others. Consider how easy it is to access and replace the rollers and what kind of regular maintenance they require.
- Cost: Initial cost vs. long-term cost should be evaluated. Cheaper rollers might save money upfront but could lead to higher maintenance and replacement costs down the line.
- Availability: Consider the lead time for receiving new rollers or replacements. Rollers that are readily available can reduce downtime significantly.
Comparison Between Standard and Custom 4 Conveyor Roller
Here’s a table to help compare the features and benefits of standard versus custom 4 conveyor rollers:
Feature | Standard 4" Conveyor Roller | Custom 4" Conveyor Roller |
---|---|---|
Material Options | Limited to commonly used materials | Can be tailored to specific materials for unique needs |
Load Capacity | Generally predefined based on industry standards | Can be designed to handle specific, often heavier loads |
Cost | Typically lower initial cost | Higher initial cost, potentially lower long-term cost |
Lead Time | Shorter, as they are often stock items | Longer, due to custom manufacturing processes |
Design Flexibility | Standard designs with limited flexibility | High flexibility to meet precise application needs |
Environmental Suitability | May not suit all environments perfectly | Can be customized for specific environmental challenges |
Maintenance Requirements | Generally standard and straightforward | Can be designed for easier maintenance based on setup |
Durability | Fixed, based on standard materials and designs | Enhanced, as materials and designs can be optimized |
Operational Speed | Suitable for general use | Optimized for specific operational speeds |
Choosing between standard and custom 4 conveyor rollers largely depends on the specific needs of the application, including operational demands and budget constraints. Custom rollers offer tailored solutions but come at a higher cost and with longer lead times, whereas standard rollers provide a quick, cost-effective solution that suits general needs.
Installation and Maintenance of 4 Conveyor Roller
Ensuring the proper installation and regular maintenance of 4 conveyor roller is crucial for the smooth operation and longevity of any conveyor system. This section provides a detailed guide on how to install 4 conveyor rollers correctly and outlines best practices for their maintenance. Following these guidelines will help maximize the operational efficiency and extend the lifespan of the rollers.
Guide on How to Install 4 Conveyor Roller
This guide provides step-by-step instructions tailored to installing 4 conveyor rollers, focusing on ensuring accuracy and safety throughout the process.
- Preparation: Before installation, verify that all components, such as the 4 conveyor roller itself and the mounting hardware, are correct and complete according to the specifications.
- Align Frames: Ensure the conveyor frame is properly aligned. Misalignment can lead to excessive wear and tear on rollers.
- Position Rollers: Place the 4 conveyor rollers in the frame mounts. Make sure they are evenly spaced and parallel to each other to ensure smooth operation.
- Secure Axles: Insert and securely fasten the axles through the rollers and frame. Axle retention must be checked to prevent the roller from dislodging during operation.
- Check Level: Use a level to ensure that all rollers are perfectly horizontal. This prevents uneven wear and assists in smooth material flow.
- Test Spin: Manually spin the 4 conveyor rollers to ensure they rotate freely without any obstructions or noise which could indicate incorrect installation.
- Load Testing: Conduct a light load test to observe the behavior of the conveyor. Look for any unusual vibrations or sounds.
- Safety Inspection: Perform a thorough inspection to ensure all safety guards and features are in place and functional before full operation commences.
Best Practices for Maintaining 4 Conveyor Roller
Maintaining your 4 conveyor rollers is crucial to prevent breakdowns and extend the equipment’s life. Regular and effective maintenance ensures continuous and efficient operation, reduces downtime, and saves costs. The following best practices should be incorporated into your regular maintenance routines to keep your conveyor system running smoothly.
- Regular Cleaning: Keep the rollers and the surrounding area clean from debris and dust that can accumulate and cause wear or operational interference.
- Lubrication: Regularly lubricate the bearings according to the manufacturer’s recommendations. Over-lubrication can attract dirt and under-lubrication can cause premature failure.
- Inspection Schedule: Establish a routine inspection schedule to check for wear and tear, misalignment, or any signs of damage that could impair functionality.
- Replace Worn Rollers: Promptly replace any rollers that show signs of significant wear or damage to prevent further issues along the conveyor line.
- Monitor Load Capacities: Ensure that the conveyor is not overloaded beyond the specified capacity of the 4″ rollers, as this can accelerate wear and lead to failure.
- Align and Tension: Regularly check and adjust the alignment and tension of the conveyor belt, as misalignment can cause uneven roller wear and operational issues.
- Record Keeping: Keep detailed records of maintenance activities, replacements, and observations from inspections to track the performance and condition over time.
Following these installation guidelines and maintenance best practices will help ensure that your 4 conveyor rollers perform efficiently and last as long as possible, reducing downtime and maintenance costs in your operations.
Where to Buy 4 Conveyor Roller
Selecting the right manufacturer and supplier for 4 conveyor roller is crucial for ensuring you receive high-quality components that meet your specific operational needs. A reliable supplier not only provides a product that fits your system but also supports your ongoing requirements with excellent service and expertise. Here’s how to evaluate manufacturers and what critical aspects to consider when choosing where to purchase your 4 conveyor roller.
Advice on Choosing a Conveyor Roller Manufacturer
This section offers detailed advice on key factors to consider when choosing a conveyor roller manufacturer, helping you identify a reliable partner that can meet both your operational needs and quality expectations.
- Reputation and Reliability: Look for suppliers with a strong reputation in the industry, evidenced by positive reviews and testimonials from other businesses.
- Quality Certifications: Choose manufacturers that adhere to recognized quality standards and hold relevant certifications such as ISO certifications, which indicate a commitment to quality and consistency.
- Product Range: Ensure the supplier offers a wide range of conveyor rollers, including the specific 4 conveyor rollers you need, and can cater to various customizations you might require.
- Technical Support: Check that the supplier offers comprehensive technical support, including assistance with installation, troubleshooting, and maintenance.
- Lead Times: Consider the lead times for delivery of rollers. A good supplier should have efficient logistics in place to ensure timely delivery.
- Pricing and Value: Compare pricing between suppliers but consider overall value too, which includes after-sales service, warranty terms, and the durability of the rollers.
- Customer Service: Good customer service is essential. The supplier should be easy to communicate with and responsive to your queries and needs.
- Industry Expertise: Look for a supplier with expertise in your specific industry, as they will better understand the challenges and requirements unique to your environment.
Options for Purchasing Replacement 4 Conveyor Rollers and New Installations
Once you’ve identified what to look for in a manufacturer, the next step is understanding where to purchase your 4 conveyor roller. This segment details various purchasing options, ranging from direct manufacturer sales to online marketplaces, providing a comprehensive guide to finding the right source for both replacement rollers and new installations.
- Direct from Manufacturer: Buying directly from the manufacturer can often ensure you get the best price and access to expert advice and support.
- Distributors and Resellers: These entities often carry stock from various manufacturers, which can be advantageous if you need a quick replacement.
- Online Industrial Marketplaces: Platforms like McMaster-Carr, Grainger, and others offer a wide range of conveyor components with detailed product specifications and user reviews.
- Custom Roller Manufacturers: For specific needs, custom roller manufacturers can design and produce 4 conveyor rollers tailored to your exact requirements.
- Refurbished and Used Rollers: Some suppliers offer refurbished or used rollers at a reduced cost, which can be a cost-effective option for non-critical applications.
- International Suppliers: If local options are limited, consider looking at suppliers from overseas who can offer competitive pricing and unique products.
- Trade Shows and Industrial Expos: These events provide opportunities to meet directly with manufacturers and distributors, see product demos, and negotiate purchase terms face-to-face.
By considering these options and criteria when choosing where to buy your 4 conveyor roller, you can ensure that you select a supplier that will provide high-quality products and reliable service, supporting the efficiency and longevity of your conveyor system.
Innovations and Trends in Conveyor Roller Technology
The technology surrounding 4 conveyor roller is continuously evolving, driven by the need for more efficient, durable, and environmentally friendly solutions in material handling. This section highlights some of the most significant recent advancements in the design and materials of 4 conveyor rollers, reflecting the industry’s response to the increasing demands of modern production environments.
Recent Advancements in Conveyor Roller Design and Materials
- High-Performance Materials: New composite materials are being used to make 4 conveyor rollers lighter, more durable, and less prone to wear. These materials also offer reduced friction, which improves energy efficiency.
- Precision Bearings: The integration of advanced bearing systems has significantly increased the efficiency and load capacity of 4 conveyor roller, allowing them to operate more smoothly and with less maintenance.
- Sealing Technology: Enhanced sealing techniques are being employed to protect the internal components of conveyor rollers from dirt, dust, and moisture, which extends their operational life, particularly in harsh environments.
- Smart Monitoring: Rollers equipped with sensors that monitor performance parameters such as speed, temperature, and vibration levels, enabling predictive maintenance and reducing downtime.
- Eco-friendly Solutions: There is a growing focus on sustainability, with the development of recyclable and energy-efficient 4 conveyor rollers that minimize environmental impact.
- Modular Design: Rollers are being designed with modularity in mind, allowing for quick and easy replacement of parts and enabling systems to be more easily customized and scaled.
Future Trends in Conveyor Roller Technology
As industries continue to advance, so too does the technology behind conveyor systems. This section delves into the future trends expected to shape the industry, focusing on how automation and smart technologies are integrating with traditional conveyor systems to create more dynamic and efficient processes.
- Integration of IoT: The Internet of Things (IoT) is set to revolutionize the way 4 conveyor rollers are monitored and controlled, with real-time data collection and analysis improving efficiency and predictive maintenance.
- Advanced Automation: Greater automation in conveyor systems will allow for more precise control and timing of movements, reducing waste and improving productivity.
- Increased Customization: The demand for tailor-made conveyor solutions will drive further innovations in roller design, allowing for more specific and varied applications.
- Artificial Intelligence: AI will enhance the decision-making processes in conveyor systems, optimizing routes and loads automatically based on workflow demands.
- Energy Efficiency: Future designs will emphasize energy conservation, with more efficient motors and the use of energy-harvesting systems to power sensors and other small components.
- Safety and Ergonomics: Enhanced safety features, such as emergency stop systems and better ergonomic designs, will improve the working conditions around conveyor systems.
- Collaborative Systems: There will be a move towards systems that can communicate and operate in sync with other machinery and systems within a warehouse or production line, creating a more interconnected and efficient workflow.
By staying ahead of these trends and innovations, manufacturers and users of 4 conveyor roller can ensure their operations remain efficient, cost-effective, and aligned with the latest technological advances. This proactive approach not only improves productivity but also positions businesses to lead in competitive markets.
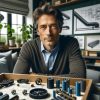
Jordan Smith, a seasoned professional with over 20 years of experience in the conveyor system industry. Jordan’s expertise lies in providing comprehensive solutions for conveyor rollers, belts, and accessories, catering to a wide range of industrial needs. From initial design and configuration to installation and meticulous troubleshooting, Jordan is adept at handling all aspects of conveyor system management. Whether you’re looking to upgrade your production line with efficient conveyor belts, require custom conveyor rollers for specific operations, or need expert advice on selecting the right conveyor accessories for your facility, Jordan is your reliable consultant. For any inquiries or assistance with conveyor system optimization, Jordan is available to share his wealth of knowledge and experience. Feel free to reach out at any time for professional guidance on all matters related to conveyor rollers, belts, and accessories.