Choosing Your Rubber Coated Conveyor Drive Rollers Wisely
In the world of material handling and production, rubber coated conveyor drive rollers stand as pivotal components, ensuring smooth, efficient, and quiet operation across a myriad of industries. From the intricate conveyance systems in packaging and printing facilities to the rugged lines in manufacturing plants, these rollers offer unmatched durability and grip, thanks to their rubber coating. This guide delves into the essential aspects of rubber coated conveyor drive rollers, shedding light on their significance, diverse applications, and how they contribute to the optimization of conveyor systems. Moreover, readers will navigate through the nuances of pricing, identifying quality manufacturers, and finding reliable suppliers nearby. Whether you’re in the market to purchase, seeking maintenance tips, or simply wish to understand their role in your industry, this guide promises comprehensive insights into everything related to these indispensable components.
What are Rubber Coated Conveyor Drive Rollers
Definition and Description
Rubber coated conveyor drive rollers are integral components of conveyor systems, designed to move materials efficiently across a designated area. These rollers are cylindrical rods, covered with a rubber coating, that are positioned at critical points along a conveyor belt to drive the belt, control its tension, and support the materials being transported. The rubber coating on these rollers is not just a superficial layer; it’s a meticulously engineered solution designed to enhance the performance and longevity of the conveyor system.
The primary function of rubber coated conveyor drive rollers is to provide a smooth, controlled motion of the conveyor belt that carries various materials or products from one point to another within a facility. This function is critical in ensuring efficiency and productivity in operations across various industries, including manufacturing, logistics, packaging, and more.
Benefits of Using Rubber Coated Drive Rollers
- Durability: One of the standout benefits of rubber coated conveyor drive rollers is their exceptional durability. The rubber coating provides a protective layer that resists wear and tear from the constant movement of materials. This durability ensures that the rollers maintain their integrity and functionality over time, reducing the need for frequent replacements and maintenance.
- Traction: The rubber coating on these rollers offers superior traction compared to uncoated rollers. This enhanced grip ensures that the conveyor belt does not slip or misalign, which could disrupt the smooth flow of operations. Traction is particularly important in applications where precise movement and positioning of materials are critical.
- Noise Reduction: Rubber coated conveyor drive rollers significantly reduce operational noise, contributing to a more pleasant and safer work environment. The rubber material absorbs vibrations and sound, making the conveyor system quieter during operation. This benefit is particularly valued in facilities where noise levels are a concern for worker comfort and safety.
- Shock Absorption: The elasticity of rubber allows these rollers to absorb shocks and impacts that may occur during material handling. This shock absorption capability protects not only the conveyor system itself but also the materials being transported, minimizing the risk of damage during transit.
- Chemical Resistance: Rubber coatings can be formulated to resist a variety of chemicals, making rubber coated conveyor drive rollers suitable for use in environments where exposure to corrosive substances is a concern. This chemical resistance ensures that the rollers can maintain their performance and longevity even in harsh conditions.
- Versatility: The versatility of rubber coated conveyor drive rollers is unmatched. They can be customized in terms of size, rubber type, and coating thickness to meet specific operational requirements. Whether the application involves high temperatures, abrasive materials, or specific chemical exposures, there is a rubber coating solution to meet those needs.
- Improved Product Handling: The soft, yielding nature of rubber minimizes the risk of damage to sensitive or fragile materials during handling. This makes rubber coated conveyor drive rollers an excellent choice for industries where product integrity is paramount.
The benefits of using rubber coated conveyor drive rollers extend far beyond their basic function of moving materials. Their durability, traction, noise reduction, shock absorption, chemical resistance, versatility, and improved product handling capabilities make them an indispensable component of any efficient and reliable conveyor system.
Types and Features of Rubber Coated Conveyor Drive Rollers
Rubber coated conveyor drive rollers are essential components in various conveyor systems, offering durability, flexibility, and enhanced grip to handle materials across different industries. This section delves into the types of rubber coatings and innovative design features that set these rollers apart, ensuring optimal performance and longevity.
Materials and Coatings
Rubber coatings for conveyor drive rollers are chosen based on the application’s specific needs, including resistance to wear, temperature, chemicals, and the ability to provide friction. Here, we explore five types of rubber coatings and their industrial applications, demonstrating the versatility of rubber coated conveyor drive rollers:
Type of Rubber Coating | Properties | Industrial Applications |
---|---|---|
Natural Rubber | High elasticity and tensile strength | General-purpose conveyors, packaging |
Nitrile Rubber | Oil and chemical resistance | Oil refineries, chemical processing |
Silicone Rubber | High-temperature resistance, low compressibility | High-temperature applications, food processing |
EPDM Rubber | Weather, ozone, and age resistance | Outdoor applications, automotive manufacturing |
Polyurethane Rubber | Abrasion resistance, flexibility | Precision equipment, paper handling |
These rubber coatings are applied to the rollers to meet the demanding conditions of various environments, enhancing the rubber coated conveyor drive rollers’ functionality and service life.
Innovative Designs
The innovative design features of rubber coated conveyor drive rollers not only contribute to the efficiency of conveyor systems but also extend their operational life. Below are 10 notable features and advantages:
- Integrated Bearings: Bearings are embedded within the rollers to ensure smooth rotation, reducing friction and wear.
- Anti-Static Properties: Some rollers are designed with materials that dissipate static electricity, crucial in sensitive electronic component manufacturing.
- High Load Capacity: Enhanced structural design allows these rollers to support heavier loads without deformation.
- Temperature Resistance: Special rubber materials can withstand extreme temperatures, from freezing cold to scorching heat.
- Chemical Resistance: Coatings resistant to chemicals prevent degradation in harsh chemical environments.
- Noise Reduction: The rubber coating significantly reduces operational noise, creating a more pleasant workplace.
- Impact Absorption: Rubber has natural shock-absorbing properties, protecting the conveyor system and the materials being transported.
- Customizability: Rollers can be customized in size, coating type, and hardness to fit specific applications.
- Water and Moisture Resistance: Certain rubber coatings are impermeable to water, suitable for wet or humid conditions.
- Easy Maintenance: The durability and resistance properties of rubber coated conveyor drive rollers ensure they require less frequent maintenance.
Each of these features contributes to the overall effectiveness and reliability of rubber coated conveyor drive rollers, making them indispensable in modern industrial operations. The adaptability and customizability of these rollers allow them to meet the specific needs of any conveyor system, ensuring efficient and uninterrupted production processes.
Industrial Applications of Rubber Coated Conveyor Drive Rollers
Rubber coated conveyor drive rollers are versatile components that play a crucial role in the efficiency and functionality of conveyor systems across a broad range of industries. Their ability to provide traction, reduce noise, and withstand various environmental conditions makes them invaluable in many industrial applications.
Versatility Across Industries
The adaptability of rubber coated conveyor drive rollers to different environments and requirements underscores their importance in numerous sectors. Here are eight industries where these rollers are particularly crucial:
- Packaging: Ensures smooth movement of packages, reducing damage and improving packaging line speed.
- Printing: Offers precise control and pressure for transferring ink, crucial for high-quality printing results.
- Manufacturing: Facilitates the assembly line movement of parts and finished goods, accommodating various weights and sizes.
- Food Processing: Complies with hygiene standards while handling food products gently and efficiently.
- Pharmaceuticals: Supports clean room environments with rollers that can be easily cleaned and sterilized.
- Agriculture: Moves bulk materials like grains and feeds without degrading product quality.
- Mining and Quarrying: Withstands abrasive and heavy loads, essential for the transport of raw materials.
- Recycling: Sorts and moves recyclable materials, contributing to efficient recycling processes.
These industries benefit from the specific properties of rubber coated conveyor drive rollers, such as resistance to abrasion, chemicals, and impacts, ensuring longevity and reliability of the conveyor systems.
Case Studies
To illustrate the effectiveness and value of rubber coated conveyor drive rollers, here are four brief case studies showcasing successful implementations:
- A Beverage Bottling Plant: Faced with frequent breakdowns due to the harsh, wet environment, the plant upgraded to rubber coated conveyor drive rollers with superior water resistance and durability. The result was a significant reduction in downtime and maintenance costs.
- A High-Speed Printing Facility: The facility struggled with ink transfer issues, affecting print quality. Switching to precision-engineered rubber coated conveyor drive rollers improved ink application, leading to sharper images and faster production times.
- An Automotive Assembly Line: The introduction of rubber coated conveyor drive rollers with integrated bearings and high load capacity allowed for smoother operation and handling of heavy automotive components, enhancing productivity and worker safety.
- A Pharmaceutical Packaging Line: To meet strict hygiene standards, a pharmaceutical company implemented specially coated rollers that could be easily cleaned and sterilized, ensuring contamination-free packaging of sensitive products.
These case studies demonstrate how rubber coated conveyor drive rollers can be tailored to meet the specific needs of different industries, leading to improved efficiency, reduced operational costs, and higher product quality. The adaptability and effectiveness of these rollers make them a key component in the success of various industrial operations.
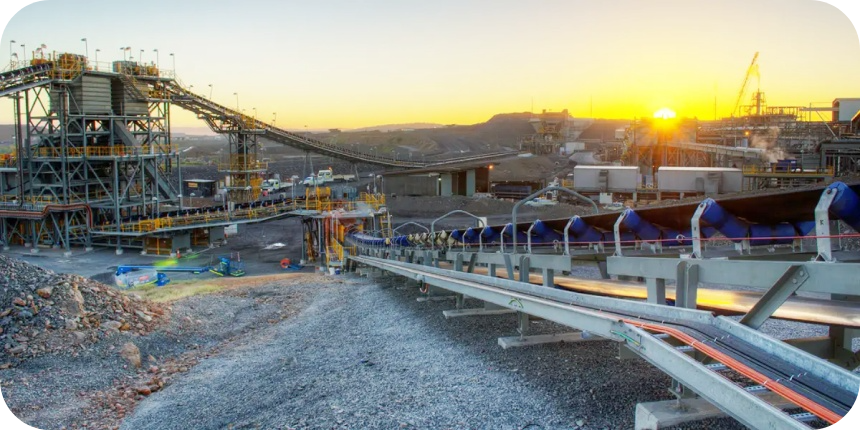
Choosing the Right Rubber Coated Conveyor Drive Rollers
Selecting the right rubber coated conveyor drive rollers is paramount to achieving optimal performance and longevity of conveyor systems. Various factors come into play, influencing the efficiency and suitability of the rollers for specific applications. Moreover, partnering with the right manufacturer ensures access to high-quality materials, customization options, and expert advice.
Factors to Consider
When it comes to choosing the ideal rubber coated conveyor drive rollers for your operations, several key factors should be taken into account:
- Size: Proper sizing is critical for compatibility with the conveyor system and for handling the intended load efficiently.
- Load Capacity: The rollers must be capable of supporting the weight of the materials being conveyed without deforming or breaking.
- Environment: Consideration of the operational environment (temperature, exposure to chemicals, moisture) is crucial for selecting the right rubber material and coating.
- Rubber Material: Different rubber compounds offer varying levels of resistance to abrasion, chemicals, temperature, and impact, influencing performance and durability.
- Speed Requirements: The rollers need to sustain the conveyor speed without degradation or excessive noise.
- Maintenance Needs: Ease of maintenance and cleaning may affect the choice of rollers, especially in industries with stringent hygiene standards.
- Lifespan: Estimating the expected service life helps in assessing the cost-effectiveness of different roller options.
- Compliance and Certifications: Ensure the rollers meet industry standards and regulatory requirements, especially in food and pharmaceutical sectors.
- Customization Options: The ability to customize dimensions, coatings, and other specifications can be crucial for unique applications.
- Supplier Reliability: Considering the supplier’s track record for reliability and service can prevent future disruptions.
Finding the Right Manufacturer
Selecting a manufacturer for rubber coated conveyor drive rollers involves more than comparing prices; it requires a thorough assessment of their capabilities, quality assurance, and customer service. Here are 10 tips to help identify a reputable and capable manufacturer:
- Experience: Look for manufacturers with a proven track record in producing high-quality rubber coated conveyor drive rollers.
- Quality of Materials: Ensure they use premium materials that offer the durability and performance you need.
- Customization Capabilities: The best manufacturers can tailor rollers to your specific requirements.
- Technical Support: Access to expert advice and support can help you choose the right rollers and maintain them properly.
- Production Capacity: Ensure they can meet your demand, whether you need a few specialized rollers or large volumes.
- Lead Times: Short lead times can be crucial for maintaining your operation’s efficiency.
- Warranty and After-sales Support: Look for strong warranties and responsive customer service to safeguard your investment.
- Compliance and Certifications: Verify that the manufacturer complies with relevant industry standards and certifications.
- References and Reviews: Seek feedback from current and past customers to gauge the manufacturer’s reliability and quality.
- Innovation and Continuous Improvement: Partners who invest in research and development can offer the latest advancements in rubber technology and roller design.
Choosing the right rubber coated conveyor drive rollers and a reliable manufacturer is a strategic decision that impacts the productivity, efficiency, and cost-effectiveness of your operations. Careful consideration of the mentioned factors and tips can guide you in making an informed choice, ensuring your conveyor system operates at its best.
Pricing and Purchasing Guide for Rubber Coated Conveyor Drive Rollers
Understanding the pricing and purchasing landscape for rubber coated conveyor drive rollers is crucial for making informed decisions that align with your budgetary and operational needs. This guide aims to demystify the factors affecting the cost of these essential components and offers insights on how to navigate the market to find the best products and deals.
Understanding Pricing
The price of rubber coated conveyor drive rollers can vary significantly based on several factors. Being aware of these can help you anticipate the investment required and identify areas where you might save costs or need to allocate more budget. Here are eight key factors influencing pricing:
- Material Quality: High-grade rubber materials and coatings command a higher price due to their superior durability and performance.
- Size and Dimensions: Larger rollers or those with custom dimensions typically cost more due to increased material usage and manufacturing complexity.
- Load Capacity: Rollers designed to handle heavier loads require more robust construction, affecting the price.
- Environmental Resistance: Specialized coatings and materials designed to withstand harsh environments, chemicals, or extreme temperatures can increase costs.
- Customization: Any customization beyond standard specifications, such as unique coatings or integrated technologies, will likely incur additional charges.
- Quantity: Ordering in bulk can often reduce the cost per unit, thanks to economies of scale.
- Manufacturer Reputation: Established manufacturers with a proven track record may charge more for their expertise and reliability.
- Additional Features: Features like anti-static properties, integrated bearings, or noise-reducing designs can add to the cost.
Where to Buy
Finding the right source for purchasing rubber coated conveyor drive rollers can be as crucial as selecting the rollers themselves. Here are ten guidelines to help you navigate the market:
- Manufacturer Direct: Purchasing directly from manufacturers often allows for customization and direct technical support.
- Industrial Supply Distributors: Distributors may offer a broader selection of brands and immediate availability for standard products.
- Online Marketplaces: Platforms like Alibaba or Amazon Business can connect you with suppliers worldwide and offer competitive pricing.
- Trade Shows: Industry-specific trade shows are excellent opportunities to meet manufacturers, view products firsthand, and negotiate deals.
- Referrals: Recommendations from industry peers can lead you to trusted suppliers.
- Local Suppliers: Searching for “rubber coated conveyor drive rollers near me” can yield local vendors for quicker delivery and potential cost savings on shipping.
- Bulk Purchasers: Consider joining a buying group to leverage collective bargaining power for better pricing.
- Second-Hand or Refurbished: For budget constraints, consider reputable sources for used or refurbished rollers.
- Technical Forums: Online forums and industry communities can offer insights and recommendations based on real-world experiences.
- Custom Fabricators: If your needs are highly specific, custom fabricators can provide tailored solutions, though this may come at a premium.
Investing in rubber coated conveyor drive rollers involves balancing cost against performance, longevity, and operational efficiency. By understanding the factors that influence pricing and knowing where to look for suppliers, you can make choices that support your business’s needs while managing expenses effectively.
Request a quote for our premium conveyor rollers today.
Maintenance and Care for Rubber Coated Conveyor Drive Rollers
Maintaining rubber coated conveyor drive rollers is vital for ensuring their longevity and optimal performance within conveyor systems. Proper care and routine maintenance can significantly extend the life of these rollers, reducing the need for frequent replacements and, consequently, lowering operational costs. Here are practical tips and advice on maintaining these components and finding reliable recoating services.
Longevity of Rollers
To maximize the service life of rubber coated conveyor drive rollers, consider the following maintenance tips:
- Regular Cleaning: Keep rollers clean from debris and dust that can cause abrasion and degrade the rubber coating.
- Lubrication: Ensure bearings and any movable parts are adequately lubricated to prevent wear and tear.
- Inspection Routine: Regularly inspect rollers for signs of wear, cracking, or brittleness, especially in harsh environments.
- Proper Alignment: Misaligned rollers can cause uneven wear and tear, reducing their lifespan.
- Environmental Controls: If possible, control environmental factors such as temperature and humidity to prevent premature degradation of the rubber.
- Avoid Overloading: Adhere to the recommended load capacities to prevent excessive stress and deformation.
- Use of Softeners: Certain rubber types may benefit from conditioners or softeners that prevent drying and cracking.
- Replacement of Worn Parts: Promptly replace rollers or parts that are beyond repair to maintain the system’s efficiency.
- Professional Assessments: Periodically have a professional evaluate the condition of your rollers, offering an expert perspective on maintenance needs.
Adhering to these maintenance tips can significantly extend the lifespan of your rubber coated conveyor drive rollers, ensuring they continue to perform effectively and efficiently.
Rubber Roller Coating Services Near Me
When the time comes for recoating or maintaining your rubber coated conveyor drive rollers, finding a reputable service provider is crucial. Here’s how to locate and select the best service:
- Online Search: A simple online search for “rubber roller coating services near me” can yield a list of potential providers. Look for companies with good reviews and a robust online presence.
- Industry Recommendations: Consult with peers in your industry for recommendations. Often, the best services are found through word-of-mouth from those with firsthand experience.
- Trade Associations: Industry trade associations can provide directories of service providers specializing in rubber coating and maintenance.
- Manufacturer Referrals: Contact the manufacturer of your rollers for recommended service providers or inquire if they offer recoating services themselves.
- Qualifications and Experience: Once you have a list of potential services, evaluate their qualifications, experience, and portfolio of work. Ensure they have experience with rubber coated conveyor drive rollers specifically.
- Quotes and Estimates: Obtain quotes or estimates from several services to compare pricing, but also consider the quality and scope of the service offered.
- Warranty and Guarantee: Prefer services that offer a warranty or guarantee on their work, providing assurance of the quality and longevity of the recoating.
- Turnaround Time: Consider the provider’s turnaround time for recoating services, as prolonged downtime can affect your operations.
- After-service Support: Opt for services that offer after-service support, indicating they stand by the quality of their work and are available for any follow-up needs.
Selecting the right service for recoating and maintaining your rubber coated conveyor drive rollers is essential for ensuring their continued performance and longevity. With careful selection and regular maintenance, your conveyor system can operate smoothly, efficiently, and cost-effectively for years to come.
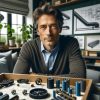
Jordan Smith, a seasoned professional with over 20 years of experience in the conveyor system industry. Jordan’s expertise lies in providing comprehensive solutions for conveyor rollers, belts, and accessories, catering to a wide range of industrial needs. From initial design and configuration to installation and meticulous troubleshooting, Jordan is adept at handling all aspects of conveyor system management. Whether you’re looking to upgrade your production line with efficient conveyor belts, require custom conveyor rollers for specific operations, or need expert advice on selecting the right conveyor accessories for your facility, Jordan is your reliable consultant. For any inquiries or assistance with conveyor system optimization, Jordan is available to share his wealth of knowledge and experience. Feel free to reach out at any time for professional guidance on all matters related to conveyor rollers, belts, and accessories.