Key Types of Idler in Belt Conveyor Applications
Idlers are a crucial component in belt conveyors, playing a significant role in the overall efficiency and longevity of the system. By supporting the conveyor belt and ensuring its smooth operation, different types of idler in belt conveyor systems help in maintaining alignment and minimizing wear and tear. The types of idler in belt conveyor applications, such as carrying idlers, return idlers, and impact idlers, are designed to address specific operational needs, contributing to reduced maintenance costs and enhanced performance. Understanding these types of idler in belt conveyor systems is essential for optimizing the functionality and durability of conveyor systems across various industries.
The Role of Types of Idler in Belt Conveyor
Idlers are an essential component of belt conveyor systems, playing a pivotal role in their operation and effectiveness. They serve multiple functions that contribute to the overall efficiency and longevity of the conveyor system. This section delves into the basic functions of idlers and explains how they support the belt and control its alignment and motion.
The Basic Functions of Idlers
In belt conveyor systems, idlers are designed to support the conveyor belt and the material being transported along the belt. The types of idlers in belt conveyor systems are varied, each tailored to specific functions and operational needs. Generally, idlers perform the following basic functions:
- Support: Idlers provide the necessary support to the conveyor belt, ensuring it can carry the load without sagging or becoming misaligned. This support is crucial for maintaining the belt’s integrity and preventing damage.
- Alignment: Proper alignment of the conveyor belt is essential for smooth operation. Misalignment can cause the belt to drift off course, leading to material spillage, increased wear and tear, and potential system failures. Idlers help keep the belt centered and aligned, reducing the risk of such issues.
- Motion Control: Idlers facilitate the smooth movement of the conveyor belt, ensuring it runs efficiently and with minimal resistance. This smooth motion is vital for reducing energy consumption and minimizing operational costs.
How Idlers Support the Belt and Control Its Alignment and Motion
The effectiveness of a conveyor system largely depends on how well the idlers support the belt and control its alignment and motion. Different types of idler in belt conveyor systems are designed to address specific challenges and operational requirements. Here’s how idlers achieve this:
Carrying Idlers
Carrying idlers are positioned on the carrying side of the belt, supporting the load being transported. They are typically arranged in sets of three or more rollers, forming a trough shape that cradles the material. This troughing effect helps to keep the load stable and centered on the belt. The angle of the trough can vary, with common angles being 20°, 35°, and 45°, depending on the type of material and the required capacity.
By providing stable support, carrying idlers prevent the belt from sagging under the weight of the load, which can lead to misalignment and increased wear. Properly functioning carrying idlers ensure the load is evenly distributed across the belt, enhancing the system’s efficiency and longevity.
Return Idlers
Return idlers are located on the return side of the belt, supporting the empty belt on its return journey. There are several types of return idlers, including flat return idlers, V-return idlers, rubber disc return idlers, and spiral return idlers. Each type is designed to address specific issues such as belt tracking, debris removal, and minimizing belt wear.
For instance, flat return idlers provide a flat surface for the belt to travel over, while V-return idlers help in centering the belt. Rubber disc return idlers are effective in shedding sticky materials, and spiral return idlers help clean the belt and prevent material buildup. These idlers play a crucial role in maintaining the belt’s alignment and preventing it from wandering off course, which can cause damage and reduce efficiency.
Impact Idlers
Impact idlers are placed at loading and transfer points where the material first lands on the belt. These idlers are designed to absorb the shock and impact of the material being loaded, protecting the belt from damage. They typically feature a series of rollers with a resilient surface, such as rubber, to cushion the impact.
By reducing the force of the impact, these idlers help prevent tears and punctures in the belt, extending its lifespan. Additionally, impact idlers aid in maintaining the belt’s alignment by preventing sudden shifts and movements caused by the loading process.
The Importance of Selecting the Right Types of Idler in Belt Conveyor Systems
Choosing the appropriate types of idler in belt conveyor systems is crucial for ensuring optimal performance and longevity. Factors such as the nature of the material being transported, the conveyor’s operational conditions, and the specific requirements of the application must be considered when selecting idlers.
High-quality idlers are manufactured to meet stringent industry standards, such as those set by DIN, CEMA, JIS, AS, SANS-SABS, GOST, and AFNOR. These standards ensure that idlers are built to withstand the demands of heavy-duty operations and provide reliable performance.
Idlers are integral to the functionality of belt conveyor systems. By understanding the different types of idler in belt conveyor systems and their specific roles, operators can ensure their conveyors run smoothly, efficiently, and with minimal downtime. Properly selected and maintained idlers contribute significantly to the overall success of material handling operations, enhancing productivity and reducing operational costs.
Types of Idler in Belt Conveyor and Their Applications
In belt conveyor systems, various types of idler in belt conveyor applications are utilized to ensure the efficient and effective movement of materials. Each type of idler serves a specific purpose and is chosen based on the operational requirements of the conveyor system. This section explores the different types of idlers, their roles, and their applications in various industries.
Carrying Idlers
Description of Carrying Idlers and Their Role
Carrying idlers are essential components positioned on the carrying side of the conveyor belt. Their primary function is to support the load being transported by the belt, ensuring the material is carried efficiently and safely. These idlers are typically arranged in sets of three or more rollers, forming a trough shape that stabilizes the material on the belt.
Examples of Carrying Idlers
- Standard Troughing Idlers: These idlers consist of three rollers arranged in a V-shape to form a trough that supports the load.
- Garland Idlers: These idlers have multiple rollers linked together, providing flexible support and better load distribution.
- Training Idlers: Designed to help correct the belt’s alignment, ensuring it runs centrally.
- Offset Idlers: These idlers are staggered to prevent the material from spilling off the belt.
- Transition Idlers: Used at the transition points of the conveyor, providing support as the belt changes angles.
Detailing Trough Angles and Their Applications
The trough angle of carrying idlers can significantly impact the conveyor’s capacity and stability. Common trough angles include 20°, 35°, and 45°, each suited to different applications.
- 20° Trough Angle: Ideal for light to medium-duty applications where material stability is less of a concern.
- 35° Trough Angle: Commonly used in standard conveyor systems, providing a good balance between load capacity and stability.
- 45° Trough Angle: Suitable for heavy-duty applications, ensuring maximum load support and stability.
- 10° Trough Angle: Used for low-volume, precise applications where material control is crucial.
- 60° Trough Angle: Employed in specialized applications requiring extreme load stability.
Industries Served by Carrying Idlers
Carrying idlers are widely used across various industries, including:
- Mining: For transporting extracted minerals and ores.
- Cement: To move raw materials and finished products.
- Power Plants: Handling coal and other fuels.
- Agriculture: Transporting grains and other agricultural products.
- Construction: Moving construction materials such as sand and gravel.
Return Idlers
Explanation of Return Idlers
Return idlers are positioned on the return side of the conveyor belt and support the empty belt as it returns to the loading point. Several types of return idlers are used to address specific operational needs, including:
- Flat Return Idlers: Provide a flat surface for the belt, suitable for standard applications.
- Rubber Disc Return Idlers: Feature rubber discs to prevent material buildup and ensure a clean return path.
- Spiral Return Idlers: Designed to remove sticky materials from the belt, reducing buildup and maintaining belt cleanliness.
- V-Return Idlers: Help to center the belt and maintain alignment, particularly useful for longer conveyors.
- Self-aligning Return Idlers: Automatically adjust to correct belt misalignment, reducing the risk of belt damage.
Functions, Structures, and Benefits of Return Idlers
Return idlers play a crucial role in maintaining the belt’s alignment and preventing issues such as stretching, sagging, and failure. Here are five key examples of their benefits:
- Flat Return Idlers: Simple structure, preventing sagging and supporting the belt uniformly.
- Rubber Disc Return Idlers: The rubber discs help shed material buildup, ensuring a smooth return path and reducing maintenance.
- Spiral Return Idlers: The spiral design effectively removes sticky materials, keeping the belt clean and functional.
- V-Return Idlers: The V-shape aids in centering the belt, reducing misalignment and potential damage.
- Self-aligning Return Idlers: These idlers adjust automatically to maintain proper belt alignment, enhancing the conveyor’s efficiency and lifespan.
Impact Idlers
Brief Introduction to Impact Idlers
Impact idlers are installed at loading and transfer points where the material first contacts the belt. These idlers are designed to absorb the impact of the material being loaded, protecting the conveyor belt from damage and extending its service life.
Examples of Impact Idlers
- Heavy-duty Impact Idlers: Used in high-impact areas to absorb significant shock loads.
- Rubber Cushion Impact Idlers: Feature rubber cushioning to reduce impact force and protect the belt.
- Suspension Impact Idlers: Provide additional shock absorption through a suspended design.
- Impact Bar Idlers: Combine rollers with impact bars to distribute the load and minimize belt wear.
- Composite Impact Idlers: Made from composite materials to provide lightweight yet effective shock absorption.
Impact idlers play a crucial role in maintaining the integrity of the conveyor belt, ensuring smooth operation and reducing maintenance costs by preventing damage at critical points.
Understanding the various types of idler in belt conveyor systems and their specific applications is essential for optimizing the performance and longevity of conveyor systems. By selecting the appropriate idlers for each application, operators can enhance the efficiency, reliability, and durability of their material handling operations.
Selecting the Right Types of Idler in Belt Conveyor
Choosing the appropriate types of idler in belt conveyor systems is critical for ensuring optimal performance, efficiency, and longevity of the conveyor system. The selection process involves considering various factors such as the specific operational requirements of the conveyor, the nature of the materials being transported, and the environmental conditions in which the conveyor operates. This section provides a detailed guide on how to select the right type of idler for different conveyor applications.
Conveyor Operation Requirements
The first step in selecting the right types of idler in belt conveyor systems is to understand the specific requirements of the conveyor operation.
- Load Capacity: The weight and volume of the material being transported will determine the type and size of idlers required. Heavy loads necessitate robust idlers with higher load-bearing capacities.
- Conveyor Speed: The speed at which the conveyor operates can impact the choice of idlers. High-speed conveyors require idlers that can handle increased rotational speeds without compromising stability and alignment.
- Belt Width and Length: The width and length of the conveyor belt will influence the type and arrangement of idlers needed to provide adequate support and prevent sagging.
- Material Characteristics: The physical properties of the material, such as abrasiveness, lump size, and moisture content, will affect the selection of idlers. For example, abrasive materials require idlers with wear-resistant surfaces, while sticky materials may necessitate self-cleaning idlers.
Evaluating Environmental Conditions
Environmental conditions play a significant role in the selection of the right types of idler in belt conveyor systems.
- Temperature Extremes: Extreme temperatures, whether hot or cold, can affect the performance of idlers. High temperatures may require idlers with heat-resistant properties, while cold environments may need idlers designed to withstand freezing conditions.
- Moisture and Humidity: Wet and humid conditions can lead to corrosion and rusting of idlers. In such environments, selecting idlers made from corrosion-resistant materials, such as stainless steel or galvanized components, is essential.
- Dust and Debris: Dusty environments, common in mining and quarrying operations, can cause idlers to clog and wear prematurely. Sealed or shielded idlers can help mitigate these issues by preventing dust ingress.
- Chemical Exposure: In industries where idlers are exposed to chemicals, such as in chemical processing plants, choosing idlers made from chemical-resistant materials is crucial to prevent degradation and ensure longevity.
Matching Idler Types to Applications
Different types of idler in belt conveyor systems are designed to meet specific operational needs. Here’s how to match the appropriate idler type to various applications:
Carrying Idlers
Carrying idlers are used to support the load on the carrying side of the belt. When selecting carrying idlers, consider the following:
- Standard Troughing Idlers: Suitable for general material handling applications. Choose the appropriate trough angle (e.g., 20°, 35°, 45°) based on the material’s stability and the desired capacity.
- Training Idlers: Ideal for correcting belt misalignment. These idlers are beneficial in applications where maintaining belt alignment is challenging.
- Offset Idlers: Useful for preventing material spillage in applications with loose or fine materials.
- Transition Idlers: Required at points where the belt transitions from a flat to a trough shape. Essential for minimizing stress and wear at transition points.
- Garland Idlers: Flexible and suitable for curved or uneven conveyor paths, providing better load distribution.
Return Idlers
Return idlers support the empty belt on its return journey. Key considerations include:
- Flat Return Idlers: Basic support for the return side of the belt. Suitable for standard applications.
- V-Return Idlers: Help in centering the belt, ideal for long conveyors to maintain alignment.
- Rubber Disc Return Idlers: Prevent material buildup and are suitable for applications involving sticky or wet materials.
- Spiral Return Idlers: Provide a self-cleaning action, perfect for environments with high levels of debris.
- Self-aligning Return Idlers: Automatically adjust to correct belt misalignment, reducing maintenance requirements and prolonging belt life.
Impact Idlers
Impact idlers are crucial at loading and transfer points where the belt is subjected to shock loads. Selection criteria include:
- Heavy-duty Impact Idlers: Required for high-impact applications, such as in mining or quarrying operations.
- Rubber Cushion Impact Idlers: Provide additional cushioning to absorb shock and protect the belt.
- Suspension Impact Idlers: Offer enhanced shock absorption through a suspended design, ideal for extremely heavy or abrasive materials.
- Impact Bar Idlers: Combine rollers with impact bars to distribute the load and minimize wear, suitable for high-impact zones.
- Composite Impact Idlers: Made from lightweight composite materials, these idlers provide effective shock absorption and are resistant to corrosion.
Selecting the right types of idler in belt conveyor systems requires a thorough understanding of the conveyor’s operational requirements and the environmental conditions it will face. By carefully evaluating these factors and matching the appropriate idler types to the specific application, operators can enhance the efficiency, reliability, and longevity of their conveyor systems. Properly selected idlers reduce maintenance costs, minimize downtime, and ensure smooth, trouble-free operation, ultimately contributing to the overall success of material handling processes.
Specifications and Standards for Types of Idler in Belt Conveyor
Selecting the appropriate belt conveyor idler types systems requires an understanding of the specific specifications and standards that these components must meet. Ensuring that idlers adhere to recognized standards is crucial for guaranteeing their quality, reliability, and compatibility with different conveyor systems. This section provides an overview of the specifications for various idler types and the standards adhered to in their manufacturing.
Overview of Specifications for Different Idler Types
Idlers come in various types, each with specific design and operational specifications tailored to their particular functions within a belt conveyor system. The primary specifications include dimensions, load capacity, and material properties, which are critical for ensuring optimal performance and longevity.
Carrying Idlers
Carrying idlers are available in various configurations to accommodate different belt widths and trough angles. Standard belt widths range from 450 mm to 2400 mm, with idlers designed to match these widths. The trough angles typically include 20°, 35°, and 45°, with some specialized idlers offering angles such as 10° or 60° for specific applications.
The load capacity of carrying idlers must match the conveyor’s operational requirements. This capacity is influenced by the material density, belt speed, and the idler’s design. High-capacity idlers are essential for heavy-duty applications, such as mining or bulk material handling.
Carrying idlers are typically made from high-quality steel, with rollers featuring sealed bearings to prevent contamination and ensure smooth rotation. Some idlers may also have rubber or polyurethane coatings to reduce wear and noise.
Return Idlers
Return idlers also come in various sizes to match the belt widths, typically ranging from 450 mm to 2400 mm. They are designed to provide stable support for the returning belt, preventing sagging and misalignment.
Similar to carrying idlers, return idlers must support the weight of the belt and any residual material. The load capacity will vary depending on the belt width and the specific type of return idler, such as flat, V-return, or rubber disc return idlers.
Return idlers are constructed from durable materials such as galvanized steel or stainless steel to withstand harsh environmental conditions. Rubber disc and spiral return idlers include additional materials to prevent buildup and ensure smooth operation.
Impact Idlers
Impact idlers are designed to match the belt widths and are typically placed at loading points where the material first impacts the belt. These idlers must be robust to absorb the shock and prevent damage to the belt. Standard widths range from 450 mm to 2400 mm.
Impact idlers must withstand the high impact forces generated by loading materials. They are constructed with reinforced frames and resilient rollers, often featuring rubber or composite materials to cushion the impact.
Heavy-duty materials such as reinforced steel and high-impact rubber are used to construct impact idlers. The rollers are designed to absorb shock and minimize damage to the belt, extending its lifespan.
Standards Adhered to in Manufacturing Idlers
To ensure the quality and reliability of idlers, manufacturers adhere to several international standards. These standards specify the design, dimensions, materials, and performance criteria for idlers used in belt conveyor systems.
- DIN (Deutsches Institut für Normung): The German Institute for Standardization provides comprehensive guidelines for conveyor idlers, including dimensions, load capacities, and material specifications. DIN standards ensure that idlers meet rigorous quality and performance criteria.
- CEMA (Conveyor Equipment Manufacturers Association): CEMA standards are widely recognized in the conveyor industry, particularly in North America. These standards cover the design, construction, and testing of conveyor idlers, ensuring they meet the necessary performance requirements.
- JIS (Japanese Industrial Standards): JIS standards provide specifications for conveyor idlers used in Japan, focusing on dimensions, materials, and performance. Adhering to JIS standards ensures that idlers are compatible with conveyor systems in the Japanese market.
- AS (Australian Standards): Australian Standards specify the requirements for conveyor idlers used in Australia, including design, construction, and performance criteria. These standards ensure that idlers can withstand the demanding conditions of Australian mining and industrial applications.
- SANS-SABS (South African National Standards – South African Bureau of Standards): These standards provide guidelines for the design and construction of conveyor idlers used in South Africa, ensuring they meet the necessary quality and performance requirements.
- GOST (Russian National Standards): GOST standards specify the design, dimensions, and materials for conveyor idlers used in Russia and other CIS countries. Adhering to GOST standards ensures that idlers meet the required performance criteria in these regions.
- AFNOR (Association Française de Normalisation): AFNOR standards provide specifications for conveyor idlers used in France, focusing on dimensions, materials, and performance. Compliance with AFNOR standards ensures that idlers meet the quality and reliability expectations of the French market.
Understanding the specifications and standards for the various types of idler in belt conveyor systems is essential for selecting the right components for your conveyor operation. By adhering to recognized international standards, manufacturers ensure that their idlers meet the necessary quality and performance criteria, providing reliable and efficient support for conveyor belts in various industrial applications. Selecting idlers that comply with these standards guarantees optimal performance, longevity, and safety for your conveyor system, ultimately contributing to the success of your material handling operations.
Manufacturing and Quality Assurance for Types of Idler in Belt Conveyor
The manufacturing and quality assurance processes for the types of idler in belt conveyor systems are crucial for ensuring the reliability, efficiency, and longevity of conveyor operations. High-quality idlers contribute to reduced maintenance costs, improved operational efficiency, and extended conveyor belt life. This section provides insight into the manufacturing process and the importance of selecting high-quality idlers.
Insight into the Manufacturing Process
Factory Size and Infrastructure
Manufacturing high-quality idlers requires advanced facilities with adequate space for large-scale production. A typical idler manufacturing factory spans several thousand square meters, equipped with state-of-the-art machinery and technology. These facilities include automated production lines, precision machining centers, and advanced testing equipment to ensure each idler meets stringent quality standards.
Workforce and Expertise
A skilled and experienced workforce is essential for producing high-quality idlers. Factories employ a diverse team of professionals, including mechanical engineers, machinists, and quality control specialists. These experts work together to oversee the entire production process, from raw material selection to final assembly and testing.
R&D Engineers
Research and development (R&D) engineers play a vital role in the continuous improvement of idler designs and manufacturing processes. These engineers conduct extensive research to develop innovative solutions that enhance the performance and durability of idlers. They work on improving materials, optimizing designs, and incorporating new technologies to meet the evolving demands of conveyor systems.
Certification and Standards Compliance
Ensuring that idlers comply with international standards is a critical aspect of the manufacturing process. Factories typically adhere to certifications such as ISO 9001 (Quality Management System), ISO 14001 (Environmental Management System), and OHSAS 18001 (Occupational Health and Safety Management System). Compliance with these certifications ensures that the manufacturing processes are consistent, environmentally friendly, and safe for workers.
Importance of Selecting High-Quality Idlers
Choosing high-quality idlers is essential for optimal performance and durability in conveyor systems.
- Enhanced Load Capacity
High-quality idlers are designed to support heavy loads without deformation or failure. For instance, in mining operations where large volumes of ore are transported, robust idlers made from high-grade steel can withstand significant weight and impact, ensuring smooth and uninterrupted operation.
- Improved Belt Alignment
Precision-engineered idlers maintain the alignment of the conveyor belt, preventing misalignment issues that can cause material spillage and increased wear. Self-aligning idlers, for example, automatically adjust to correct belt misalignment, reducing maintenance needs and prolonging the belt’s life.
- Reduced Wear and Tear
Idlers made from high-quality materials, such as wear-resistant rubber or polyurethane coatings, reduce friction between the belt and the rollers. This minimizes wear and tear on both the belt and the idlers, leading to longer service life and lower replacement costs. Rubber disc return idlers are an example, as they effectively prevent material buildup and reduce belt wear.
- Shock Absorption
Impact idlers with advanced shock-absorbing materials protect the conveyor belt from damage at loading and transfer points. Heavy-duty impact idlers, equipped with reinforced rubber cushions, absorb the shock of falling material, preventing belt tears and extending its operational life.
- Environmental Resilience
High-quality idlers are designed to operate reliably in harsh environmental conditions, such as extreme temperatures, humidity, or corrosive environments. For example, galvanized steel or stainless steel idler rollers resist corrosion, making them suitable for use in coastal or chemical processing plants where exposure to corrosive elements is common.
The manufacturing and quality assurance processes for the types of idler in belt conveyor systems are critical for ensuring that these components meet the high standards required for reliable and efficient operation. A well-equipped factory with a skilled workforce, supported by rigorous R&D efforts and adherence to international certifications, ensures the production of high-quality idlers.
Selecting high-quality idlers is essential for optimal performance and durability in conveyor systems. Enhanced load capacity, improved belt alignment, reduced wear and tear, effective shock absorption, and resilience to harsh environmental conditions are just some of the benefits of using top-tier idlers. By investing in high-quality idlers, operators can achieve smoother operations, lower maintenance costs, and prolonged conveyor system lifespans, ultimately contributing to the overall success of material handling operations.
FAQs About Types of Idler in Belt Conveyor
Conveyor idlers are crucial components in belt conveyor systems, designed to support and guide the conveyor belt as it transports materials. There are several types of conveyor idlers, each serving a specific function:
Carrying Idlers: Positioned on the carrying side of the belt, these idlers support the load. They come in various configurations, such as standard troughing idlers, which create a trough shape to cradle the material, and garland idlers, which provide flexible support.
Return Idlers: These idlers support the empty belt on its return journey. Types include flat return idlers for basic support, V-return idlers for better belt alignment, and rubber disc return idlers to prevent material buildup.
Impact Idlers: Located at loading points, impact idlers absorb the shock of material falling onto the belt. They feature reinforced rollers with resilient surfaces to protect the belt from damage.
Training Idlers: These idlers help to correct belt misalignment. They automatically adjust to keep the belt centered and prevent it from drifting off course.
Transition Idlers: Used at points where the belt transitions from a flat to a trough shape, ensuring smooth changes in belt profile and reducing stress.
Belt idlers are essential for maintaining the stability and efficiency of a conveyor belt system. Different types of belt idlers include:
Flat Idlers: Used primarily on the return side of the belt, flat idlers provide basic support and are simple in design.
Troughing Idlers: These idlers are used on the carrying side of the belt and come in various trough angles, such as 20°, 35°, and 45°. They create a trough shape that helps to support and stabilize the load.
Self-aligning Idlers: These idlers are designed to automatically correct any misalignment of the belt. They can be used on both the carrying and return sides and help in maintaining the belt’s alignment, thus reducing wear and tear.
Rubber Disc Idlers: Typically used on the return side, rubber disc idlers help to clean the belt and prevent material buildup. The rubber discs also provide some shock absorption.
Spiral Idlers: These idlers have a spiral shape and are used to remove sticky materials from the belt, keeping it clean and functional.
An idler in a belt conveyor is a cylindrical component that supports and guides the conveyor belt as it moves materials from one point to another. Idlers are installed at regular intervals along the conveyor frame and play a critical role in ensuring the belt runs smoothly and efficiently. There are several types of idlers, each designed for specific functions:
Support: Idlers support the weight of the conveyor belt and the materials being transported, preventing the belt from sagging and maintaining its shape.
Alignment: Idlers help keep the conveyor belt aligned, preventing it from drifting off track, which can cause spillage and increased wear.
Motion Control: By providing a smooth surface for the belt to travel over, idlers reduce friction and ensure efficient motion, which helps in minimizing energy consumption and operational costs.
Idlers are essential for the efficient operation of belt conveyor systems, contributing to the system’s overall reliability and longevity.
Idler frames are the structures that support and hold idlers in place on a conveyor system. Different types of idler frames include:
Fixed Frames: These are the most common type of idler frames and are securely mounted to the conveyor structure. They provide stable support for the idlers and are suitable for most conveyor applications.
Suspended Frames: Suspended idler frames hang from the conveyor structure, allowing for more flexibility and movement. They are often used in applications where the conveyor needs to navigate curves or uneven terrain.
Garland Frames: These frames support garland idlers, which consist of multiple rollers linked together. Garland frames provide flexible support and are ideal for conveyors that handle heavy loads or operate in harsh conditions.
Retractable Frames: Designed for ease of maintenance, retractable frames can be pulled out or moved to provide access to the idlers for inspection and replacement without stopping the conveyor.
Training Frames: These frames support training idlers, which are used to correct belt misalignment. Training frames allow the idlers to pivot and adjust, helping to keep the belt centered and running smoothly.
Each type of idler frame is designed to meet specific operational needs, ensuring the conveyor system operates efficiently and reliably.
Last Updated on July 25, 2024 by Jordan Smith
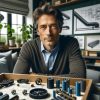
Jordan Smith, a seasoned professional with over 20 years of experience in the conveyor system industry. Jordan’s expertise lies in providing comprehensive solutions for conveyor rollers, belts, and accessories, catering to a wide range of industrial needs. From initial design and configuration to installation and meticulous troubleshooting, Jordan is adept at handling all aspects of conveyor system management. Whether you’re looking to upgrade your production line with efficient conveyor belts, require custom conveyor rollers for specific operations, or need expert advice on selecting the right conveyor accessories for your facility, Jordan is your reliable consultant. For any inquiries or assistance with conveyor system optimization, Jordan is available to share his wealth of knowledge and experience. Feel free to reach out at any time for professional guidance on all matters related to conveyor rollers, belts, and accessories.