Essential Types of Conveyor Belts Used in Mining
Conveyor belts are integral to mining operations, providing an efficient method for transporting materials across various stages of the mining process. Understanding the different types of mining conveyor belts is essential for optimizing productivity and ensuring safety. These belts streamline the movement of ore, coal, and other materials, reducing manual labor and enhancing operational efficiency. Selecting the right type of conveyor belt is crucial, as it can significantly impact the overall performance and safety of mining activities. By choosing appropriate types of conveyor belts used in mining, companies can ensure smoother operations, minimize downtime, and promote a safer working environment for their employees.
Types of Conveyor Belts Used in Mining
Understanding the specific types of idlers in belt conveyor is essential for selecting the right system for particular applications. There are two primary types of conveyor belts used in mining: surface conveyor belts and underground mining conveyor belts.
Surface Conveyor Belts
Surface conveyor belts are used in open-pit mining operations, where the extraction occurs at the surface. These belts are designed to withstand the harsh conditions of open-pit mining, such as exposure to the elements and the heavy loads of transported materials.
- Steel Cord Conveyor Belts: These belts are reinforced with steel cords, providing exceptional strength and durability for transporting heavy materials over long distances in open-pit mines.
- Fabric Conveyor Belts: Made from multiple layers of fabric, these belts are flexible and suitable for transporting a variety of materials, including ore and overburden.
- Chevron Conveyor Belts: Equipped with a chevron pattern, these belts prevent material rollback on steep inclines, making them ideal for transporting materials up and out of the pit.
- Heat-Resistant Conveyor Belts: These belts are designed to withstand high temperatures, which is essential when transporting materials that are hot from the mining process.
- Ripstop Conveyor Belts: Reinforced with a special ripstop layer, these belts are resistant to tears and punctures, providing reliability in rugged mining environments.
Underground Mining Conveyor Belts
Underground mining conveyor belts are used in subterranean mining operations, where the mining activities occur below the surface. These belts are designed with safety and efficiency in mind, given the confined and often hazardous conditions of underground mines.
- Fire-Resistant Conveyor Belts: Safety is paramount in underground mining, and these belts are designed to resist ignition and prevent the spread of fire, protecting workers and equipment.
- Antistatic Conveyor Belts: These belts are made from materials that dissipate static electricity, reducing the risk of sparks that could ignite flammable gases or dust in the mine.
- Low-Smoke, Zero-Halogen (LSZH) Belts: In the event of a fire, these belts produce minimal smoke and no halogen gases, ensuring better visibility and less toxic exposure for workers.
- Heavy-Duty Conveyor Belts: Designed to handle the high loads and abrasive materials typical of underground mining, these belts are built for durability and long service life.
- Impact-Resistant Conveyor Belts: Equipped with special layers to absorb the shock of heavy loads, these belts reduce the risk of damage and downtime caused by falling rocks or other materials.
Understanding the various types of conveyor belts used in mining and their specific applications is crucial for optimizing mining operations. By selecting the appropriate conveyor belt system, mining companies can enhance efficiency, improve safety, and ensure the smooth transport of materials from extraction to processing.
Key Components of Types of Conveyor Belts Used in Mining Systems
Understanding the key components of mining conveyor belt systems is essential for selecting the right belt conveyor idler types. These components work together to ensure the efficient, safe, and reliable transport of materials in mining operations. Here, we explore the primary elements that make up these systems, including pulleys, motors, and the belt material itself.
Pulleys
Pulleys are critical components in any conveyor belt system. They provide the driving force and direction for the belt, ensuring smooth and continuous operation. There are several types of pulleys used in mining conveyor belt systems, each serving a specific purpose:
- Drive Pulleys: These pulleys are connected to the motor and provide the necessary force to move the belt. They are typically covered with a rubber or ceramic surface to increase friction and prevent belt slippage.
- Tail Pulleys: Located at the opposite end of the drive pulley, the tail pulley provides tension and helps guide the belt. It ensures that the belt remains aligned and runs smoothly.
- Snub Pulleys: Positioned near the drive pulley, snub pulleys increase the angle of contact between the belt and the drive pulley, enhancing grip and power transmission.
- Bend Pulleys: These pulleys are used to change the direction of the belt, allowing it to navigate complex paths within the mining site. They are crucial for systems with multiple transfer points.
- Take-Up Pulleys: Located along the return side of the belt, take-up pulleys help maintain proper belt tension, compensating for any stretch or slack in the belt over time.
Motors
Motors are the power source for mining conveyor belt systems. They convert electrical energy into mechanical energy, driving the pulleys and, consequently, the belt. Different types of motors are used based on the specific requirements of the mining operation:
- AC Motors: Alternating current (AC) motors are commonly used in conveyor systems due to their reliability and efficiency. They are available in various power ratings to match the demands of the conveyor belt system.
- DC Motors: Direct current (DC) motors are less common but can be used in applications where precise speed control is required. They are typically used in variable speed conveyor systems.
- Gear Motors: These motors are equipped with an integrated gearbox, providing high torque and efficient power transmission. They are ideal for heavy-duty mining applications where large loads need to be moved.
- Servo Motors: Used in applications requiring precise control, servo motors are ideal for automated mining operations. They offer accurate positioning and speed control, essential for complex conveyor systems.
- Hydraulic Motors: In some mining operations, hydraulic motors are used to drive conveyor belts. They are particularly useful in environments where electrical power is not readily available or where explosion-proof equipment is required.
Belt Material
The belt material is a critical component that directly affects the performance and durability of the conveyor system. The types of conveyor belts used in mining vary based on the specific needs of the operation. Key considerations include the type of material being transported, environmental conditions, and the belt’s resistance to wear and tear.
- Rubber Belts: These are the most common type of belts used in mining. Rubber belts offer flexibility, durability, and resistance to abrasion. They are suitable for transporting a wide range of materials, including ore and coal.
- PVC Belts: Polyvinyl chloride (PVC) belts are used in mining operations where chemical resistance is essential. They are ideal for transporting materials that may contain chemicals or oils.
- Steel Cord Belts: These belts are reinforced with steel cords, providing exceptional strength and durability. They are used in applications requiring the transport of heavy loads over long distances.
- Fabric Belts: Made from multiple layers of fabric, these belts offer flexibility and tensile strength. They are used in lighter-duty applications where flexibility and ease of installation are important.
- Flame-Resistant Belts: In underground mining operations, flame-resistant belts are essential for safety. These belts are designed to resist ignition and prevent the spread of fire, protecting workers and equipment.
Additional Components
In addition to pulleys, motors, and belt materials, several other components are crucial for the effective operation of mining conveyor belt systems:
- Idlers: Idlers are rollers that support the belt and help it maintain its shape. They are essential for reducing friction and ensuring smooth movement of the belt.
- Belt Cleaners: These devices are used to remove material that sticks to the belt, preventing buildup and ensuring efficient operation. They are particularly important in mining operations where sticky materials are transported.
- Transfer Points: These are locations where materials are transferred from one conveyor belt to another. Proper design and maintenance of transfer points are essential to prevent spillage and material loss.
- Skirting and Sealing Systems: These systems are used to contain material on the belt, preventing spillage and reducing dust. They are essential for maintaining a clean and safe working environment.
- Controls and Sensors: Modern conveyor belt systems are equipped with various controls and sensors to monitor performance, detect issues, and automate operations. These components enhance safety, efficiency, and reliability.
By understanding the key components of mining conveyor belt systems, mining operations can select the appropriate types of conveyor belts used in mining to optimize performance, enhance safety, and ensure reliable material transport.
Types of Types of Conveyor Belts Used in Mining Material
The choice of conveyor belt material is critical in mining operations, as it directly impacts the durability, flexibility, and safety of the conveyor system. Understanding the different types of conveyor belts used in mining, particularly the materials they are made from, helps in selecting the right belt for specific applications. Here, we discuss various materials used in manufacturing conveyor belts, focusing on their key properties and suitability for mining environments.
Rubber Conveyor Belts
Rubber is one of the most common materials used in the manufacturing of conveyor belts for mining. Rubber belts offer several advantages, making them suitable for various mining applications:
- Durability: Rubber belts are highly durable, capable of withstanding the harsh conditions of mining operations. They are resistant to abrasion, cuts, and impacts, which is essential for handling rough and heavy materials like ore and coal.
- Flexibility: These belts are flexible, allowing them to bend and move around pulleys and other components without cracking or breaking. This flexibility makes rubber belts ideal for systems with complex routing and tight spaces.
- Fire Resistance: In underground mining operations, fire resistance is a critical safety feature. Rubber belts can be manufactured with flame-resistant properties, reducing the risk of fire and enhancing the safety of workers.
- Temperature Resistance: Rubber belts can also be designed to withstand high temperatures, making them suitable for transporting materials that are hot or subjected to high-temperature processes.
- Chemical Resistance: Specially formulated rubber belts can resist chemical degradation, making them suitable for environments where exposure to oils, acids, and other chemicals is common.
PVC Conveyor Belts
Polyvinyl chloride (PVC) is another widely used material in the manufacturing of conveyor belts for mining. PVC belts are known for their versatility and specific advantages:
- Chemical Resistance: PVC belts offer excellent resistance to a wide range of chemicals, including acids, alkalis, and oils. This makes them suitable for mining operations where chemical exposure is a concern.
- Low Maintenance: PVC belts require minimal maintenance, reducing downtime and operational costs. Their smooth surface prevents material buildup, ensuring efficient operation.
- Flexibility: Like rubber belts, PVC belts are flexible and can adapt to complex routing and varying belt lengths. This flexibility is essential for accommodating the dynamic nature of mining operations.
- Lightweight: PVC belts are lightweight compared to rubber belts, which can reduce the overall load on the conveyor system and improve energy efficiency.
- Cost-Effective: PVC belts are generally more cost-effective than rubber belts, making them an attractive option for mining operations with budget constraints.
Steel Cord Conveyor Belts
Steel cord belts are designed for heavy-duty mining applications where high strength and long-distance transport are required. These belts consist of steel cords embedded in a rubber matrix, offering exceptional performance:
- High Strength: Steel cord belts provide superior tensile strength, allowing them to transport heavy loads over long distances without stretching or breaking.
- Durability: The steel cords offer excellent resistance to impact and abrasion, making these belts suitable for harsh mining environments with rough and sharp materials.
- Low Elongation: Steel cord belts exhibit minimal elongation under load, maintaining consistent tension and reducing the need for frequent adjustments.
- Fire Resistance: Similar to rubber belts, steel cord belts can be manufactured with flame-resistant properties, enhancing safety in underground mining operations.
- Fatigue Resistance: The steel cords provide high resistance to fatigue, ensuring a long service life even under continuous and demanding mining conditions.
Fabric Conveyor Belts
Fabric conveyor belts, also known as textile belts, are made from multiple layers of synthetic fibers such as polyester, nylon, or cotton. These belts offer several benefits for mining applications:
- Flexibility: Fabric belts are highly flexible, making them suitable for applications with complex routing and frequent direction changes.
- Lightweight: The lightweight nature of fabric belts reduces the overall load on the conveyor system, improving energy efficiency and reducing wear on components.
- Cost-Effective: Fabric belts are generally more affordable than steel cord or rubber belts, making them a cost-effective solution for many mining operations.
- Tear Resistance: High-quality fabric belts offer excellent resistance to tearing and punctures, ensuring durability in demanding mining environments.
- Customizability: Fabric belts can be tailored to specific mining requirements, with options for different fabric types, thicknesses, and coatings to enhance performance.
Composite Conveyor Belts
Composite conveyor belts combine multiple materials to leverage the advantages of each. These belts are designed for specialized mining applications requiring specific performance characteristics:
- Durability: Composite belts can be engineered to offer superior durability, combining the abrasion resistance of rubber with the strength of steel or fabric reinforcements.
- Flexibility: By incorporating flexible materials such as fabric, composite belts can adapt to complex conveyor routing while maintaining high strength.
- Fire Resistance: Composite belts can be manufactured with advanced flame-resistant properties, making them suitable for high-risk underground mining operations.
- Chemical Resistance: By integrating chemically resistant materials, composite belts can withstand exposure to harsh chemicals, ensuring long-term performance.
- Custom Performance: Composite belts can be tailored to meet specific mining requirements, offering a combination of properties such as high strength, flexibility, and resistance to extreme conditions.
The choice of conveyor belt material is crucial for optimizing the performance and safety of mining operations. By understanding the different types of conveyor belts used in mining and their specific material properties, mining companies can select the most suitable belts for their needs, ensuring efficient and reliable material transport.
Types of Conveyor Belts Used in Mining Maintenance
Maintenance is a critical aspect of managing conveyor belt systems in mining operations. Understanding the types of conveyor belts used in mining and implementing effective maintenance strategies can significantly enhance operational efficiency and safety. Here, we discuss the importance of regular maintenance, provide examples, and outline preventive maintenance strategies and common maintenance tasks.
Importance of Regular Maintenance
Regular maintenance of mining conveyor belts is essential for several reasons:
- Operational Efficiency: Regular maintenance ensures that conveyor belts run smoothly, minimizing downtime and maximizing productivity. For example, by routinely checking and adjusting belt tension, operators can prevent slippage and ensure consistent material flow.
- Safety: Proper maintenance reduces the risk of accidents and injuries. For instance, regularly inspecting and replacing worn-out or damaged belts can prevent belt breakage, which could otherwise lead to hazardous situations.
- Cost Savings: Proactive maintenance helps in identifying and addressing issues before they become major problems, reducing repair costs and extending the lifespan of conveyor belts. For example, detecting and repairing minor tears in the belt early on can prevent the need for costly belt replacements.
- Environmental Compliance: Regular maintenance helps in managing spillage and dust control, which is crucial for adhering to environmental regulations. For example, maintaining belt cleaners and skirting systems can minimize material spillage and dust emissions.
- Reliability: Consistent maintenance ensures that conveyor systems operate reliably, reducing unexpected breakdowns and production delays. For example, routine lubrication of bearings and pulleys can prevent premature wear and failure.
Preventive Maintenance Strategies and Common Maintenance Tasks
Preventive maintenance is a proactive approach aimed at preventing failures and extending the life of conveyor belt systems. Here are some key strategies and common tasks involved in preventive maintenance for the types of conveyor belts used in mining:
Visual Inspections
Regular visual inspections are crucial for identifying potential issues early on. Operators should inspect the belts for signs of wear, damage, and misalignment. Key points to check include:
- Belt Surface: Look for cracks, cuts, and frayed edges. Addressing these issues promptly can prevent further deterioration.
- Joints and Splices: Check the condition of joints and splices to ensure they are secure and intact. Weak or damaged splices can lead to belt failure.
- Pulleys and Idlers: Inspect pulleys and idlers for signs of wear and ensure they are properly aligned and rotating smoothly.
Belt Tension and Alignment
Proper belt tension and alignment are essential for efficient operation. Misaligned or improperly tensioned belts can cause excessive wear and reduce the lifespan of the belt. Maintenance tasks include:
- Tension Adjustment: Regularly check and adjust belt tension to prevent slippage and ensure smooth operation.
- Alignment Correction: Use alignment tools to ensure the belt runs straight and true on the conveyor frame, reducing uneven wear and potential damage.
Lubrication
Lubrication is vital for the smooth operation of conveyor components. Key lubrication tasks include:
- Bearings and Pulleys: Apply the appropriate lubricant to bearings and pulleys to minimize friction and wear.
- Gearboxes and Motors: Regularly lubricate gearboxes and motors to ensure efficient power transmission and prevent overheating.
Belt Cleaning
Keeping the belt clean is essential for maintaining performance and preventing material buildup. Common cleaning tasks include:
- Belt Cleaners: Regularly inspect and maintain belt cleaners to ensure they effectively remove material from the belt surface.
- Scrapers and Brushes: Use scrapers and brushes to clean the belt and remove any adhered material, reducing the risk of carryback and spillage.
Component Replacement
Timely replacement of worn or damaged components is crucial for maintaining system integrity. Key replacement tasks include:
- Belt Sections: Replace sections of the belt that are excessively worn or damaged to prevent unexpected failures.
- Rollers and Idlers: Replace worn or damaged rollers and idlers to ensure smooth belt movement and prevent misalignment.
- Pulleys and Bearings: Replace pulleys and bearings that show signs of wear or damage to maintain optimal performance.
Maintaining the types of conveyor belts used in mining through regular and preventive maintenance is essential for ensuring operational efficiency, safety, and reliability. By implementing comprehensive maintenance strategies, mining operations can minimize downtime, reduce costs, and extend the lifespan of their conveyor belt systems. Regular inspections, proper tensioning and alignment, lubrication, cleaning, and timely component replacement are key aspects of an effective maintenance program. Investing in these maintenance activities not only enhances productivity but also contributes to a safer and more sustainable mining operation.
Selected Types of Conveyor Belts Used in Mining Manufacturers
When selecting the right types of conveyor belts used in mining, it is crucial to consider the manufacturer’s reputation, product quality, and the range of services they offer. Leading manufacturers in the industry provide durable and efficient conveyor belts tailored to meet the demanding requirements of mining operations. Here, we present an overview of prominent manufacturers and outline key factors to consider when choosing a mining conveyor belt manufacturer.
Leading Manufacturers
- Fenner Dunlop: Fenner Dunlop is renowned for its high-quality conveyor belts that cater to various mining applications. With over 150 years of experience, the company offers a wide range of belts, including steel cord, fabric, and solid woven belts. Their products are known for their durability, flexibility, and resistance to harsh mining environments. Fenner Dunlop also provides extensive after-sales service and technical support, ensuring optimal performance and longevity of their conveyor systems.
- ContiTech (Continental AG): ContiTech, a division of Continental AG, is a leading manufacturer of conveyor belts for mining. Their products are designed to withstand extreme conditions, offering excellent resistance to wear, impact, and fire. ContiTech’s portfolio includes steel cord belts, textile belts, and specialty belts tailored for specific mining applications. The company emphasizes innovation, providing advanced solutions such as digital monitoring systems to enhance the efficiency and safety of conveyor operations.
- Bridgestone Corporation: Bridgestone is a global leader in the production of conveyor belts for mining and industrial applications. Known for their high-quality rubber compounds, Bridgestone belts are designed to deliver superior performance in demanding mining environments. The company offers a comprehensive range of products, including steel cord, fabric, and heat-resistant belts. Bridgestone also focuses on sustainability, developing eco-friendly conveyor belt solutions that reduce environmental impact.
- Phoenix Conveyor Belt Systems (a subsidiary of Continental AG): Phoenix Conveyor Belt Systems is recognized for its innovative and durable conveyor belt solutions. Their products are widely used in mining operations around the world, providing excellent resistance to abrasion, fire, and chemicals. Phoenix offers a diverse range of belts, including heavy-duty steel cord belts, fabric belts, and specialty belts designed for specific mining applications. The company also provides extensive technical support and maintenance services to ensure the reliability and efficiency of their conveyor systems.
- Yokohama Rubber Co., Ltd.: Yokohama Rubber is a leading manufacturer of conveyor belts for mining and industrial applications. Their belts are known for their exceptional durability, flexibility, and resistance to wear and impact. Yokohama offers a wide range of products, including steel cord, fabric, and flame-resistant belts. The company also focuses on innovation, developing advanced belt monitoring systems and environmentally friendly solutions to enhance the performance and sustainability of their conveyor systems.
Factors to Consider When Selecting a Mining Conveyor Belt Manufacturer
When choosing a manufacturer for the types of conveyor belts used in mining, several factors should be taken into account to ensure you select the best supplier for your needs:
- Product Range: It is important to choose a manufacturer that offers a comprehensive range of conveyor belts suited for various mining applications. This includes steel cord belts, fabric belts, flame-resistant belts, and specialty belts designed for specific operational requirements. A diverse product range ensures that you can find the right belt for your specific mining conditions.
- Quality and Durability: The quality and durability of the conveyor belts are crucial for reliable and efficient operation in harsh mining environments. Look for manufacturers with a proven track record of producing high-quality belts that can withstand abrasion, impact, and extreme conditions. Certifications and industry standards can also indicate the quality of the products.
- After-Sales Service: After-sales service is a critical factor in ensuring the long-term performance of your conveyor belt systems. Choose manufacturers that offer comprehensive after-sales support, including installation, maintenance, and repair services. Prompt and reliable after-sales service can minimize downtime and extend the lifespan of your conveyor belts.
- Technical Support: Technical support is essential for addressing any operational issues and optimizing the performance of your conveyor belt systems. Select manufacturers that provide extensive technical support, including troubleshooting, training, and on-site assistance. Advanced monitoring and diagnostic tools can also enhance the efficiency and safety of your operations.
- Innovation and Sustainability: Consider manufacturers that prioritize innovation and sustainability in their products and services. Innovative solutions such as digital monitoring systems, eco-friendly materials, and energy-efficient designs can improve the performance and environmental impact of your conveyor belt systems. Manufacturers committed to sustainability can also help you meet regulatory requirements and achieve your environmental goals.
Selecting the right manufacturer for the types of conveyor belts used in mining is crucial for optimizing operational efficiency, safety, and longevity. By considering factors such as product range, quality, after-sales service, technical support, and innovation, mining operations can ensure they choose a reliable and reputable supplier to meet their specific needs.
Innovative Types of Conveyor Belts Used in Mining for Sale
The mining industry continually evolves, driven by advancements in technology and materials that enhance efficiency, safety, and productivity. Selecting the right types of conveyor belts used in mining is crucial to achieving these goals. Here, we highlight some of the most innovative conveyor belts available on the market, designed specifically for mining applications, and discuss the key features to consider when purchasing a mining conveyor belt.
Advanced Conveyor Belts on the Market
- Steel Cord Conveyor Belts: These belts are renowned for their exceptional tensile strength and durability, making them ideal for heavy-duty mining applications. Steel cord belts consist of steel cables embedded in a rubber matrix, providing superior resistance to impact, abrasion, and stretching. These belts are particularly suited for long-distance transport and high-load capacities, ensuring reliability in the most demanding environments.
- Chevron Conveyor Belts: Chevron belts feature a unique V-shaped pattern on their surface, designed to prevent material rollback on steep inclines. This innovation is especially useful in open-pit mining where materials need to be transported up steep slopes. The chevron pattern enhances grip and stability, ensuring efficient material handling and reducing spillage.
- Fire-Resistant Conveyor Belts: Safety is a paramount concern in mining, especially in underground operations where fire hazards are significant. Fire-resistant conveyor belts are made from specially formulated rubber compounds that resist ignition and flame spread. These belts are essential for ensuring the safety of workers and equipment, and they comply with stringent industry safety standards.
- Pipe Conveyor Belts: Pipe conveyor belts are designed to form a closed tube shape during transport, preventing material spillage and protecting the environment. This design is particularly advantageous in areas where contamination and environmental impact need to be minimized. Pipe conveyor belts are versatile and can navigate complex routes with ease, making them suitable for various mining applications.
- Impact-Resistant Conveyor Belts: Mining operations often involve the transport of heavy and abrasive materials that can damage standard conveyor belts. Impact-resistant belts are reinforced with special layers that absorb and dissipate the energy from impacts, preventing damage and extending the belt’s lifespan. These belts are ideal for use in loading zones and areas where materials are dropped from significant heights.
Features to Look for When Purchasing a Mining Conveyor Belt
When selecting the right types of conveyor belts used in mining, several key features should be considered to ensure optimal performance and longevity:
- Wear Resistance: Mining conveyor belts are subjected to continuous abrasion from the materials they transport. High wear resistance is essential to minimize maintenance and replacement costs. Look for belts made from durable materials such as steel cords or high-quality rubber compounds that offer excellent resistance to wear and tear.
- Load Capacity: The load capacity of a conveyor belt determines how much material it can transport without experiencing excessive strain or damage. It is crucial to select a belt that can handle the expected load volumes of your mining operation. Steel cord belts, for example, offer high load capacities suitable for heavy-duty applications.
- Environmental Adaptability: Mining operations often occur in harsh environments with extreme temperatures, moisture, and chemical exposure. Conveyor belts must be able to withstand these conditions without compromising performance. Fire-resistant, heat-resistant, and chemically resistant belts are available for environments with specific challenges.
- Flexibility and Adaptability: Conveyor belts need to be flexible enough to navigate complex routes and varying terrains within mining sites. Pipe conveyor belts, with their ability to form a closed tube shape, offer excellent adaptability for complex transport routes. Similarly, fabric belts provide the necessary flexibility for intricate conveyor systems.
- Safety Features: Safety is a critical consideration in mining operations. Belts with fire-resistant properties, antistatic materials, and low-smoke, zero-halogen (LSZH) compositions enhance the safety of the work environment. These features reduce the risk of fires, explosions, and toxic smoke emissions, ensuring the protection of workers and equipment.
- Maintenance Requirements: The ease of maintenance and availability of spare parts are important factors to consider when selecting a conveyor belt. Belts that require minimal maintenance and have readily available replacement parts reduce downtime and operational costs. Manufacturers offering comprehensive after-sales support and maintenance services add value to the investment.
Innovative types of conveyor belts used in mining offer significant advancements in durability, safety, and efficiency. By highlighting advanced conveyor belts on the market, such as steel cord belts, chevron belts, fire-resistant belts, pipe belts, and impact-resistant belts, mining operations can make informed decisions to enhance their material handling processes. Key features to look for when purchasing a mining conveyor belt include wear resistance, load capacity, environmental adaptability, flexibility, safety features, and maintenance requirements. Selecting the right conveyor belt ensures optimal performance, safety, and cost-efficiency in mining operations, contributing to the overall success and sustainability of the industry.
Safety and Environmental Considerations for Types of Conveyor Belts Used in Mining
In the mining industry, safety and environmental considerations are paramount when selecting and operating conveyor belt systems. The types of conveyor belts used in mining must be designed and managed with stringent safety standards to protect workers and the environment. Here, we discuss the importance of adhering to safety standards, provide examples, and examine the environmental impact of conveyor belt systems, highlighting how modern designs are mitigating these effects.
Importance of Adhering to Safety Standards
Adhering to safety standards in the design and operation of conveyor belts in mining is crucial to prevent accidents, protect workers, and ensure efficient operations. Here are five key examples:
- Fire Resistance: Conveyor belts in mining, especially in underground operations, must be fire-resistant to prevent the risk of ignition and the spread of fire. Using fire-resistant materials in the construction of conveyor belts is essential. For example, flame-retardant rubber compounds reduce the risk of fires and enhance safety.
- Anti-Static Properties: Static electricity can accumulate on conveyor belts, posing a risk of sparks that could ignite flammable materials or gases. Anti-static conveyor belts dissipate static electricity, minimizing this risk. For instance, belts with conductive properties safely discharge static buildup, preventing hazardous situations.
- Emergency Stop Mechanisms: Conveyor belt systems must be equipped with emergency stop mechanisms to halt operations instantly in case of an emergency. These systems allow workers to stop the conveyor belt quickly, preventing accidents and injuries. Emergency pull cords or push buttons placed at regular intervals along the conveyor belt provide immediate access for emergency stops.
- Guarding and Safety Shields: To protect workers from moving parts, conveyor belts should be fitted with appropriate guarding and safety shields. These barriers prevent accidental contact with the belt, pulleys, and other moving components. For example, guards and shields around drive pulleys and return rollers reduce the risk of entanglement and injuries.
- Regular Inspections and Maintenance: Routine inspections and maintenance are critical for identifying and addressing potential safety hazards before they result in accidents. Regular checks of the belt condition, tension, alignment, and components such as pulleys and idlers help maintain safe and efficient operations. Implementing a preventive maintenance program ensures that safety standards are consistently met.
Environmental Impact of Conveyor Belt Systems
Conveyor belt systems in mining can have significant environmental impacts, including habitat disruption, dust generation, and energy consumption. However, modern designs are increasingly focused on minimizing these effects:
- Energy Efficiency: Modern conveyor belt systems are designed to be more energy-efficient, reducing their overall environmental footprint. Energy-efficient motors, variable frequency drives (VFDs), and optimized belt designs help lower energy consumption. For example, using lightweight materials and reducing friction can significantly decrease the power required to operate the belts.
- Dust Suppression: Mining operations often generate dust, which can impact air quality and surrounding ecosystems. Advanced conveyor belt designs incorporate dust suppression systems such as enclosed conveyor belts, dust covers, and integrated misting systems. These features minimize dust generation and reduce the environmental impact on nearby communities and ecosystems.
- Material Spillage Control: Spillage of materials from conveyor belts can lead to environmental contamination. Modern conveyor belts are equipped with features to control and reduce spillage, such as side skirts, belt cleaners, and properly designed transfer points. For instance, using skirting systems and belt sealing mechanisms prevents material from escaping the conveyor, ensuring cleaner operations.
- Recyclable and Sustainable Materials: The use of recyclable and sustainable materials in conveyor belt manufacturing is becoming more common. Manufacturers are increasingly adopting eco-friendly materials and production processes. For example, belts made from recycled rubber or bio-based materials contribute to reducing the environmental impact of mining operations.
- Noise Reduction: Conveyor belt systems can generate significant noise, affecting both workers and the surrounding environment. Modern designs incorporate noise reduction features such as quieter idlers, vibration dampening, and soundproofing enclosures. These measures help create a more comfortable working environment and reduce noise pollution in nearby areas.
Safety and environmental considerations are critical when selecting and operating the types of conveyor belts used in mining. Adhering to safety standards, such as using fire-resistant and anti-static belts, implementing emergency stop mechanisms, and ensuring proper guarding, is essential for protecting workers and maintaining efficient operations. Additionally, modern conveyor belt designs focus on minimizing environmental impacts through energy-efficient systems, dust suppression, spillage control, sustainable materials, and noise reduction. By prioritizing safety and environmental sustainability, mining operations can achieve greater efficiency, reduce their environmental footprint, and ensure the well-being of their workforce and surrounding communities.
Choosing the Right Types of Conveyor Belts Used in Mining
Selecting the appropriate types of conveyor belts used in mining is critical for ensuring efficiency, safety, and durability in mining operations. The right conveyor belt can significantly impact productivity and operational costs. Here, we delve into the critical factors to consider when choosing a mining conveyor belt, including the type of materials being transported, the mining environment, and the length of transport routes.
Type of Materials Being Transported
Understanding the type of materials that will be transported is essential for choosing the right conveyor belt. Different materials have varying properties that affect the belt’s performance and longevity.
- Abrasion-Resistant Belts: For transporting abrasive materials like ore, sand, or gravel, belts made from abrasion-resistant materials are ideal. These belts are designed to withstand the wear and tear caused by sharp and coarse materials. For example, belts reinforced with rubber compounds or steel cords offer superior resistance to abrasion, ensuring a longer service life.
- Heat-Resistant Belts: When transporting hot materials, such as those exiting a kiln or furnace, it’s crucial to use heat-resistant conveyor belts. These belts are manufactured from materials that can withstand high temperatures without degrading. For instance, belts made from specially formulated rubber or PVC can handle temperatures up to several hundred degrees Celsius.
- Fire-Resistant Belts: In underground mining operations, fire safety is a top priority. Fire-resistant belts are essential to prevent the spread of flames in the event of a fire. These belts are designed with flame-retardant properties and comply with industry safety standards. Using fire-resistant conveyor belts in coal mines or other underground operations helps protect workers and equipment.
- Oil-Resistant Belts: In environments where materials may contain oils or chemicals, oil-resistant conveyor belts are necessary. These belts are resistant to the degrading effects of oils, ensuring they maintain their structural integrity and performance. Belts made from nitrile or other oil-resistant compounds are suitable for transporting materials like ore mixed with oil or chemicals.
- Cleated Belts: For transporting loose or bulk materials up steep inclines, cleated conveyor belts are ideal. These belts feature raised sections (cleats) that help prevent materials from sliding back. Cleated belts are commonly used in mining operations to move materials from lower to higher elevations efficiently.
Mining Environment
The mining environment plays a significant role in determining the appropriate conveyor belt. Factors such as temperature, humidity, and exposure to chemicals can impact belt performance.
- Temperature Range: The temperature of the mining environment, both ambient and of the transported materials, must be considered. High-temperature environments require heat-resistant belts, while cold environments may require belts with enhanced flexibility to prevent cracking.
- Humidity and Moisture: In humid or wet environments, belts with moisture-resistant properties are essential to prevent degradation and slippage. For example, using belts with waterproof coatings or made from materials that do not absorb water can enhance performance in wet conditions.
- Chemical Exposure: If the mining environment involves exposure to chemicals, selecting chemically resistant belts is crucial. Belts made from materials like PVC or specific rubber compounds can withstand harsh chemical conditions, ensuring longevity and reliability.
Length of Transport Routes
The length of the transport route impacts the choice of conveyor belt, particularly in terms of durability and energy efficiency.
- Long-Distance Transport: For long-distance transport, belts with high tensile strength and low elongation are preferred. Steel cord belts, known for their strength and minimal stretching, are ideal for transporting materials over long distances with minimal maintenance.
- Incline and Decline Routes: When the transport route involves significant inclines or declines, belts with specialized surface patterns, like chevron belts, provide better grip and prevent material rollback. This ensures efficient and safe transport of materials on steep slopes.
- Load Capacity: The load capacity of the belt must match the volume and weight of the materials being transported. Heavy-duty belts designed for high load capacities are necessary for transporting large volumes of materials efficiently.
- Flexibility: For routes with multiple curves and turns, flexible belts are essential to navigate the conveyor path smoothly. Fabric belts, known for their flexibility, are suitable for complex routes with numerous bends.
- Energy Efficiency: Energy-efficient belts reduce operational costs by minimizing the power required to transport materials. Belts designed with low rolling resistance and optimized for energy savings are beneficial for long and heavily loaded transport routes.
Choosing the right types of conveyor belts used in mining involves a careful evaluation of the materials being transported, the mining environment, and the length of transport routes. By considering factors such as abrasion resistance, heat resistance, fire resistance, oil resistance, and the need for cleated belts, mining operations can ensure optimal performance and safety. Additionally, understanding the impact of environmental conditions and the specific requirements of transport routes helps in selecting conveyor belts that enhance efficiency and durability. Investing in the right conveyor belt not only boosts productivity but also ensures the long-term sustainability and safety of mining operations.
FAQs About Types of Conveyor Belts Used in Mining
In mining, several types of conveyor belts are used depending on the specific needs of the operation. The primary types include steel cord conveyor belts, fabric conveyor belts, fire-resistant belts, and heat-resistant belts. Steel cord belts are favored for their high tensile strength and durability, making them suitable for long-distance and heavy-duty applications. Fabric belts, often made from materials like polyester or nylon, are flexible and can handle various loads and environmental conditions. Fire-resistant belts are crucial in underground mining to prevent the spread of flames and ensure worker safety. Heat-resistant belts are used to transport materials at high temperatures without degrading. Each type of belt is designed to handle the specific challenges of different mining environments, ensuring efficient and safe material transport.
The most commonly used type of conveyor belt in mines is the steel cord conveyor belt. These belts are highly valued for their exceptional tensile strength, durability, and ability to handle heavy loads over long distances. Steel cord belts consist of multiple steel cords embedded in a rubber matrix, providing superior resistance to impact, abrasion, and stretching. This makes them ideal for the demanding conditions of mining operations, where belts must transport large volumes of heavy materials reliably and efficiently. Additionally, steel cord belts have minimal elongation, ensuring consistent tension and reducing the need for frequent adjustments. Their robustness and longevity make them the preferred choice in many mining applications, from transporting ore and coal to moving aggregate materials.
There are several types of belt conveyors used in various industries, including mining. Some of the primary types include flat belt conveyors, modular belt conveyors, cleated belt conveyors, and incline/decline belt conveyors. Flat belt conveyors are the most common type and are used for general material handling applications. They consist of a continuous loop of material, typically rubber or fabric, and are suitable for transporting goods over flat or slightly inclined surfaces. Modular belt conveyors use interlocking plastic segments to create a flexible and durable belt, ideal for transporting items that require frequent cleaning or exposure to water. Cleated belt conveyors have raised sections (cleats) that prevent materials from slipping, making them suitable for steep inclines and transporting loose or bulk materials. Incline/decline belt conveyors are designed to move materials between different heights, with the belt configured to travel up or down an incline. Each type of belt conveyor is tailored to specific operational needs, ensuring efficient and reliable material handling.
The thickness of a mining conveyor belt varies depending on its design and intended use. Typically, mining conveyor belts range from 1/4 inch (6 millimeters) to 1 inch (25 millimeters) in thickness. Thicker belts are generally used for heavy-duty applications where durability and strength are crucial, such as transporting large volumes of ore, coal, or other abrasive materials. For instance, steel cord belts used in long-distance and high-capacity mining operations are usually thicker to provide the necessary strength and longevity. On the other hand, fabric belts used in less demanding applications may be thinner but still offer the flexibility and durability required for efficient material transport. The specific thickness required for a mining conveyor belt depends on factors such as the type of material being transported, the distance and elevation changes in the conveyor system, and the environmental conditions of the mining site.
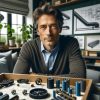
Jordan Smith, a seasoned professional with over 20 years of experience in the conveyor system industry. Jordan’s expertise lies in providing comprehensive solutions for conveyor rollers, belts, and accessories, catering to a wide range of industrial needs. From initial design and configuration to installation and meticulous troubleshooting, Jordan is adept at handling all aspects of conveyor system management. Whether you’re looking to upgrade your production line with efficient conveyor belts, require custom conveyor rollers for specific operations, or need expert advice on selecting the right conveyor accessories for your facility, Jordan is your reliable consultant. For any inquiries or assistance with conveyor system optimization, Jordan is available to share his wealth of knowledge and experience. Feel free to reach out at any time for professional guidance on all matters related to conveyor rollers, belts, and accessories.