The Ultimate Guide to Stainless Steel Gravity Rollers
In the realm of material handling and logistics, stainless steel gravity rollers stand as a cornerstone for efficient, reliable, and durable conveyor systems across a myriad of industries. These rollers, crafted from high-grade stainless steel, offer unparalleled resistance to corrosion, hygiene maintenance, and strength, making them an ideal choice for sectors demanding stringent cleanliness and durability, such as food processing, pharmaceuticals, and manufacturing. Gravity rollers, by design, leverage the force of gravity to facilitate the movement of goods across a declining path or to assist manual pushing along a flat surface. This simplicity in function belies their critical role in streamlining operations, reducing manual labor, and enhancing workflow efficiency. The utility of stainless steel gravity rollers extends beyond just transportation of goods; they are pivotal in optimizing the overall productivity and operational flow within a facility, underscoring their indispensable nature in modern industrial applications.
The Basics of Stainless Steel Gravity Rollers
Stainless steel gravity rollers are integral components of modern conveyor systems, designed to facilitate the movement of goods across various distances and terrains without the need for external power sources. These rollers are crafted from high-quality stainless steel, a material chosen for its strength, durability, and resistance to environmental factors. Here are some key points that define and describe stainless steel gravity rollers:
- Material Composition: Made primarily from stainless steel, known for its corrosion resistance and strength.
- Mechanism of Action: Utilizes the force of gravity to move goods, requiring either a slight incline or manual force to initiate movement.
- Structure: Consists of a series of cylindrical tubes mounted on a frame, allowing for the smooth and efficient transport of items.
- Application Flexibility: Can be used in a wide range of industries, including food processing, pharmaceuticals, manufacturing, and more.
- Design Variability: Available in various sizes and diameters to accommodate different load requirements and conveyor widths.
- Installation: Designed for easy installation and integration into existing conveyor systems.
- Maintenance: Requires minimal maintenance due to the high durability and resistance to wear and tear of the materials used.
Advantages of Using Stainless Steel in Gravity Rollers
Before exploring the myriad benefits, it’s crucial to understand that the choice of stainless steel as the material for gravity rollers is not arbitrary. Its inherent properties significantly contribute to the functionality, durability, and overall performance of conveyor systems. Here are the key advantages:
- Durability: Stainless steel gravity rollers are highly durable, capable of withstanding significant wear and tear over time, which reduces the need for frequent replacements.
- Hygiene: The non-porous surface of stainless steel is easy to clean and sanitize, making it ideal for industries where hygiene is a critical concern, such as food and pharmaceuticals.
- Corrosion Resistance: Stainless steel’s resistance to corrosion ensures that these rollers can be used in harsh environments, including those with high moisture or chemical exposure, without deteriorating.
- Load Capacity: The strength of stainless steel allows these rollers to support heavier loads compared to those made from other materials, enhancing the versatility of the conveyor system.
- Low Maintenance: The resilience of stainless steel gravity rollers to various forms of damage results in lower maintenance costs and less downtime for repairs.
- Temperature Resistance: These rollers can operate efficiently across a broad temperature range, making them suitable for environments with extreme heat or cold.
- Aesthetic Quality: Stainless steel offers a sleek, professional appearance that can contribute to the overall aesthetic of the facility.
- Environmental Impact: Stainless steel is 100% recyclable, reducing the environmental footprint of the manufacturing and disposal processes.
- Cost Efficiency: While the initial investment in stainless steel gravity rollers may be higher than other materials, their longevity and reduced maintenance requirements offer significant cost savings over time.
Incorporating stainless steel gravity rollers into conveyor systems not only elevates the efficiency and reliability of material handling but also underscores a commitment to quality, sustainability, and operational excellence. Their wide-ranging benefits make them a cornerstone in the infrastructure of industries looking to optimize productivity and maintain high standards of operation.
Types of Stainless Steel Gravity Rollers
Stainless steel gravity rollers are essential components in the material handling industry, offering a durable and efficient solution for moving goods across various environments. These rollers are crafted from stainless steel, providing a robust, corrosion-resistant surface ideal for numerous applications. Below, we explore the diverse types of stainless steel gravity rollers available in the market, highlighting their unique features and applications.
Different Types of Stainless Steel Gravity Rollers
- Standard Stainless Steel Rollers: Standard stainless steel rollers are the backbone of many conveyor systems, prized for their balance of strength, durability, and corrosion resistance. These rollers are versatile enough to handle a variety of materials across different industries, from lightweight packaging to more substantial manufacturing goods. Their smooth surface ensures that materials can glide over them with minimal resistance, making them a staple in environments where both cleanliness and efficiency are paramount.
- Stainless Steel Rollers with Bearings: Incorporating precision bearings, these stainless steel rollers are engineered to minimize friction, facilitating a smoother and more efficient material flow. The bearings significantly enhance the rollers’ performance, particularly in systems where long tracks or high-speed operations are common. They are especially beneficial in automated sorting systems, assembly lines, and other applications where reducing the physical effort to move goods can lead to increased productivity and reduced wear on the system.
- Grooved Stainless Steel Rollers: Grooved stainless steel rollers are designed with specific tracks that accommodate conveyor belts, ensuring that the belt remains centered and stable during operation. These rollers are crucial in belt-driven conveyor systems, preventing slippage and misalignment that could disrupt the conveyor’s functionality. Their application is widespread in industries where precise movement and positioning of goods are required, such as in packaging or bulk material handling.
- Spring-Loaded Stainless Steel Rollers: Featuring ends that are spring-loaded, these rollers offer unparalleled ease of installation and removal. This design allows for quick adjustments, replacements, or maintenance without significant downtime, enhancing the conveyor system’s overall efficiency. Spring-loaded rollers are particularly valued in environments where conveyor setups change frequently or where rapid maintenance is crucial to operational continuity.
- Tapered Stainless Steel Rollers: Tapered rollers are uniquely shaped to facilitate the movement of goods around curves and corners within the conveyor system, ensuring that items remain securely on the track without derailing. Their design is critical in complex conveyor layouts where directional changes are necessary. These rollers are often used in distribution centers, airports, and packaging facilities, where space constraints require flexible conveyor paths.
- Heavy-Duty Stainless Steel Rollers: Engineered for the most demanding applications, heavy-duty stainless steel rollers are built to carry significantly heavier loads and withstand abrasive conditions. These rollers are thicker and more robust, designed to endure the rigors of heavy manufacturing, mining, and other industrial environments where standard rollers might fail. Their enhanced durability and load-bearing capacity make them ideal for moving heavy machinery, metal parts, and other high-density materials.
Each type of stainless steel gravity roller offers unique benefits tailored to specific operational needs, ensuring that conveyor systems can be optimized for maximum efficiency, durability, and reliability across a wide range of industrial applications.
Highlight on Stainless Steel Rollers with Bearings
Stainless steel rollers with bearings offer several advantages, enhancing the functionality and efficiency of conveyor systems:
- Reduced Friction: Bearings significantly lower the friction between the roller and the material, facilitating smoother movement.
- Increased Load Capacity: The inclusion of bearings allows these rollers to handle heavier loads without compromising performance.
- Enhanced Durability: Bearings protect the roller from wear, extending its lifespan even in high-use scenarios.
- Improved Efficiency: The smooth operation provided by bearings can lead to increased conveyor speeds and improved throughput.
- Noise Reduction: Bearings can decrease operational noise, contributing to a quieter working environment.
- Ease of Maintenance: Rollers with bearings are often easier to maintain and replace, minimizing downtime.
- Versatility: Suitable for a wide range of applications, from light to heavy-duty material handling.
- Cost-Effectiveness: Despite the initial investment, the long-term savings in maintenance and replacement costs make these rollers a cost-effective choice.
Discussion on Heavy-Duty Steel Rollers for Industrial Applications
Heavy-duty stainless steel gravity rollers are designed for the toughest applications, offering unparalleled strength and durability:
- Superior Load Handling: These rollers are engineered to support significantly heavier loads, making them suitable for moving large items or bulk materials.
- Enhanced Resistance to Wear: The construction of heavy-duty rollers ensures they can withstand abrasive materials and harsh environments without significant wear.
- Longevity in Harsh Conditions: Designed to resist corrosion and damage from chemicals, these rollers maintain functionality in challenging conditions.
- Optimal for High-Impact Use: The robust design absorbs impacts more effectively, reducing the risk of damage during operation.
- Suitable for High-Speed Applications: Heavy-duty rollers can handle higher speeds without degradation, ideal for efficient production lines.
- Minimal Maintenance Required: The durability and design of these rollers result in lower maintenance needs and costs.
- Versatile Design Options: Available in various sizes and configurations to meet specific industrial requirements.
- Improved Safety: The stability and reliability of heavy-duty rollers contribute to safer operation and material handling.
- Economic Efficiency Over Time: Although the initial cost may be higher, the extended service life and reduced maintenance needs provide economic benefits.
- Environmental Resistance: Capable of operating in extreme temperatures and resistant to water and dust, making them suitable for outdoor or exposed applications.
The variety of stainless steel gravity rollers available ensures that there is an option suited to virtually any material handling need. From standard applications to the most demanding industrial environments, these rollers provide the performance, durability, and efficiency required to optimize operations.
Applications of Stainless Steel Gravity Rollers
Stainless steel gravity rollers are integral to the efficiency and productivity of various industries, offering a durable and hygienic solution for material handling and conveyor systems. Their corrosion-resistant properties and ease of cleaning make them particularly suitable for industries requiring stringent hygiene standards and robust material handling solutions. Here, we delve into the applications of stainless steel gravity rollers across six key industries, showcasing their versatility and critical role in operational workflows.
Food Processing
In the food processing sector, the utmost importance is placed on hygiene and efficiency. Stainless steel gravity rollers are integral to the conveyor systems that move raw materials through to finished products, offering a clean, durable, and efficient solution.
- Hygienic Material Handling: Stainless steel’s non-porous surface prevents bacterial growth and contamination.
- Resistance to Water and Easy Cleaning: Can be easily washed down, supporting frequent cleaning without rusting.
- Durability in Wet Environments: Specifically designed to resist corrosion, even in high-moisture areas.
- Temperature Resistance: Capable of withstanding extreme temperatures, from cold storage to baking ovens.
- Food Safety Compliance: Meets stringent food safety standards, crucial for regulatory compliance.
- Efficient Product Flow: Ensures smooth and consistent movement of goods, reducing bottlenecks in processing and packaging.
Pharmaceuticals
The pharmaceutical industry demands equipment that upholds the highest standards of cleanliness and contamination control. Stainless steel gravity rollers are key in achieving these standards, providing a sterile conveyance medium for sensitive materials.
- Non-reactive Surfaces: Eliminates the risk of chemical reactions that could contaminate pharmaceutical products.
- Ease of Sanitization: Allows for thorough cleaning and sterilization to maintain a sterile environment.
- Contamination Control: Minimizes the risk of product contamination, a critical concern in pharmaceutical manufacturing.
- Durability and Longevity: Offers a long service life even in rigorous cleaning regimes.
- Smooth Operation: Facilitates the gentle handling of delicate pharmaceutical products.
- Regulatory Compliance: Helps in meeting the strict regulatory requirements of the pharmaceutical industry.
Manufacturing
Manufacturing industries, ranging from automotive to electronics, rely on stainless steel gravity rollers for their robustness and ability to handle a variety of materials and components.
- Heavy Load Capacity: Designed to support the weight of heavy manufacturing components and finished products.
- Abrasion Resistance: Resists wear and tear from rough or sharp materials.
- Versatility: Adaptable to various segments of the manufacturing process, from assembly to shipping.
- Low Maintenance: Requires minimal upkeep, even in high-use scenarios.
- Operational Efficiency: Enhances the flow of materials, contributing to lean manufacturing practices.
- Safety: Reduces the need for manual handling, lowering the risk of workplace injuries.
Logistics & Distribution
In logistics and distribution centers, the rapid and accurate movement of goods is essential. Stainless steel gravity rollers facilitate these operations with their durability and efficiency, ensuring smooth transitions and handling.
- Rapid Sorting and Distribution: Enables quick and efficient sorting of packages for distribution.
- High Throughput Capacity: Accommodates a high volume of goods, crucial for peak operational times.
- Minimal Downtime: Durable construction reduces the need for repairs, keeping systems operational.
- Adaptability: Easily integrated into various parts of the distribution center, from unloading to loading areas.
- Energy Efficiency: Utilizes gravity, reducing the need for powered conveyance and saving on energy costs.
- Ergonomic Handling: Minimizes the physical strain on workers by facilitating easier movement of goods.
Agriculture
Agriculture processing plants benefit from the use of stainless steel gravity rollers in handling produce from the field through to packaging, offering a solution that minimizes damage and maintains product quality.
- Gentle Handling of Produce: Designed to transport delicate agricultural products without causing damage.
- Resistance to Contaminants: Stainless steel does not harbor bacteria, pesticides, or other contaminants.
- Ease of Cleaning: Can be quickly and thoroughly cleaned to prevent cross-contamination between batches.
- Weather and Rust Resistance: Suitable for use in environments exposed to the elements.
- Efficient Workflow: Streamlines the process from sorting to packaging, improving overall efficiency.
- Durability in Demanding Conditions: Withstands the abrasive nature of some agricultural products.
Retail
In the retail sector, backroom operations and stock management are streamlined with stainless steel gravity rollers, enhancing efficiency from the stockroom to the sales floor.
- Inventory Management: Facilitates the movement of stock for efficient inventory management.
- Space Optimization: Configurable to fit within limited backroom spaces, maximizing storage and workflow.
- Product Safety: Ensures products are moved safely, reducing the risk of damage.
- Versatile Use: Suitable for a wide range of retail goods, from clothing to electronics.
- Quick Unloading and Stocking: Speeds up the process of unloading delivery trucks and stocking shelves.
- Retail Efficiency: Improves the overall efficiency of retail operations, contributing to a better shopping experience.
Recycling & Waste Management
In recycling and waste management facilities, stainless steel gravity rollers play a vital role in sorting and processing recyclables, supporting environmental sustainability efforts.
- Sorting Efficiency: Enhances the sorting process, allowing for efficient separation of materials.
- Resistance to Corrosion: Withstands exposure to potentially corrosive substances found in recyclables.
- Heavy-Duty Performance: Capable of handling the weight and abrasiveness of recycled materials.
- Low Maintenance: Resists wear and tear, reducing the need for frequent replacements.
- Sustainability: Supports recycling processes, contributing to environmental sustainability.
- Adaptability: Can be customized to fit specific sorting and processing needs.
Automotive
The automotive industry relies on stainless steel gravity rollers for the efficient movement of parts through assembly lines and distribution centers, ensuring timely production and distribution.
- Component Handling: Facilitates the movement of automotive parts through various stages of assembly.
- Durability Under Load: Supports the weight of heavy automotive components and assemblies.
- Efficiency in Production: Streamlines the production process, reducing assembly time.
- Resistance to Automotive Fluids: Materials resist degradation from oils and other automotive fluids.
- Customizable Solutions: Can be tailored to specific automotive production line requirements.
- Supply Chain Optimization: Enhances the efficiency of the automotive supply chain from manufacturer to distributor.
The widespread use of stainless steel gravity rollers across these industries underscores their importance in modern material handling and manufacturing processes. Their durability, hygiene, and efficiency-enhancing properties make them a preferred choice for businesses looking to optimize their operations.
How to Choose the Best Stainless Steel Gravity Rollers
Selecting the right stainless steel gravity rollers is crucial for optimizing the efficiency and reliability of your conveyor system. The choice of rollers impacts everything from the smooth operation of the conveyor to the longevity of the system itself. Understanding the key factors and considerations that go into selecting the best stainless steel gravity rollers will ensure that your conveyor system meets your operational needs while maintaining high standards of durability and performance.
Factors to Consider When Selecting Stainless Steel Gravity Rollers
When choosing stainless steel gravity rollers, several critical factors must be considered to ensure they are well-suited to your specific application needs:
- Load Capacity: It’s crucial to evaluate the maximum weight the rollers will need to support. Selecting rollers that can handle the anticipated load without deformation ensures the system’s longevity and prevents breakdowns, enhancing overall productivity.
- Roller Diameter: The diameter directly influences the types of items the conveyor can efficiently transport. Larger diameters are typically more suitable for heavier loads, providing better distribution of weight and reducing the risk of roller and item damage.
- Material Quality: Opt for high-grade stainless steel to ensure superior corrosion resistance and durability. The quality of the material directly affects the roller’s ability to withstand harsh environments, including those with moisture, chemicals, or extreme temperatures.
- Roller Length: Matching the roller length to the width of the conveyed items ensures stability and efficient handling. Incorrect roller length can lead to material handling issues, including items tipping over or getting stuck during transit.
- Bearing Type: Bearings play a critical role in load capacity, noise levels, and maintenance needs. Selecting the appropriate bearing type based on application requirements can significantly enhance the conveyor’s performance and longevity.
- Surface Finish: A smoother roller surface reduces resistance against materials, facilitating more efficient movement. This is particularly important for applications involving delicate or lightweight items that could be affected by surface irregularities.
- Environmental Conditions: The operating environment can greatly influence the choice of roller material and construction. Factors such as exposure to corrosive substances, moisture, or extreme temperatures should guide the selection process to ensure optimal performance and durability.
- Maintenance Requirements: Consider rollers designed for ease of maintenance to minimize operational downtime and costs. Rollers that are easy to clean, lubricate, and replace parts can significantly reduce maintenance time and improve system reliability.
Tips on Selecting Rollers with Bearings for Specific Applications
Rollers with bearings are essential for applications requiring smooth and efficient movement. Here are nine tips for selecting the right ones:
- Assess Application Needs: Clearly understanding the speed, precision, and load requirements of your application is essential. This initial assessment will guide you in choosing rollers with bearings that meet or exceed these specifications, ensuring efficient operation.
- Choose the Right Bearing Type: The selection between ball bearings and roller bearings should be based on the application’s specific needs. Ball bearings are ideal for high-speed, low-load applications, while roller bearings are better suited for higher load capacities.
- Consider Sealed Bearings: In environments where dust, debris, or moisture is present, sealed bearings can offer enhanced protection. This prevents contaminants from entering the bearing, prolonging its life and maintaining smooth operation.
- Evaluate Bearing Material: The material of the bearings should be chosen based on the environment in which they will operate. Stainless steel bearings are excellent for corrosion resistance, while other materials may be selected for less demanding conditions or specific performance requirements.
- Check for Bearing Load Ratings: Ensuring that the bearings can comfortably support the expected loads is vital to prevent premature failure. Overloading bearings can lead to increased wear and tear, reducing the efficiency and lifespan of the rollers.
- Noise Considerations: In environments where noise reduction is important, selecting bearings that operate quietly can make a significant difference. This can enhance the work environment and is particularly crucial in settings such as hospitals or offices.
- Maintenance Accessibility: Rollers designed with easily accessible bearings simplify the maintenance process, allowing for quick inspections, lubrication, and replacements as needed, thereby reducing downtime and maintenance costs.
- Lubrication Requirements: Understanding the lubrication needs of the bearings is crucial for maintaining their performance and longevity. Some bearings require regular lubrication, while others are designed to be maintenance-free.
- Compatibility with Existing Systems: Ensuring that the selected rollers with bearings are compatible with your existing conveyor system is crucial for seamless integration. This includes considerations of size, load capacity, and the type of materials being conveyed.
By thoroughly considering these detailed factors and tips, you can make an informed decision when selecting stainless steel gravity rollers and rollers with bearings, ensuring that your conveyor system operates efficiently, reliably, and meets your specific operational requirements.
Stainless Steel Gravity Rollers Near Me
Finding the right stainless steel gravity rollers for your conveyor system is crucial for ensuring operational efficiency, durability, and reliability. Whether you’re setting up a new system or upgrading an existing one, knowing how to locate reputable suppliers and manufacturers of stainless steel gravity rollers is essential. This section will guide you through the process of finding the best suppliers near you and underline the importance of selecting a reliable supplier.
How to Find Suppliers and Manufacturers of Stainless Steel Gravity Rollers
Locating suppliers and manufacturers of stainless steel gravity rollers involves a strategic approach to ensure you partner with a provider that meets your specific needs. Here are seven points to guide you in your search:
- Online Directories and Search Engines: Utilize industrial and business directories, as well as search engines, to compile a list of suppliers. Keywords like “stainless steel gravity rollers near me” can yield targeted results.
- Industry Associations and Trade Shows: Industry associations often have directories of suppliers and manufacturers. Additionally, trade shows are excellent venues to meet suppliers and see their products firsthand.
- Referrals and Recommendations: Ask for referrals from industry peers or contacts within your network who have experience with conveyor systems. Personal recommendations can lead to finding trusted suppliers.
- Social Media and Forums: Platforms like LinkedIn and industry-specific forums can be valuable resources for finding suppliers and getting feedback from current customers.
- Supplier Reviews and Testimonials: Look for reviews and testimonials to gauge the reliability and quality of potential suppliers. Websites, forums, and social media can be good sources of feedback.
- Product Catalogs and Technical Specifications: Reviewing detailed product catalogs and technical specifications on suppliers’ websites can help you assess if they have the right type of stainless steel gravity rollers for your application.
- Customer Service and Support: Contact potential suppliers to inquire about their products and services. A supplier’s responsiveness and willingness to provide information can be indicative of their customer service quality.
Importance of Choosing a Reliable Supplier for Quality and Durability
Selecting a reliable supplier for stainless steel gravity rollers is not just about finding a source for your components; it’s about ensuring the long-term success and efficiency of your conveyor system. Here are several points highlighting the importance of this choice:
- Consistent Quality: A reliable supplier guarantees high-quality rollers that meet industry standards, ensuring your conveyor system operates smoothly and efficiently.
- Durability: Quality stainless steel gravity rollers are designed to last, reducing the need for frequent replacements and lowering long-term operational costs.
- Technical Support: A reputable supplier offers excellent technical support, assisting with selection, installation, and maintenance queries.
- Product Range: Reliable suppliers have a wide product range, allowing you to find the exact specifications you need for your system.
- Customization Options: In many cases, conveyor systems require customized solutions. A dependable supplier can provide custom rollers tailored to your specific requirements.
- Warranty and After-sales Service: Good suppliers stand behind their products with warranties and offer after-sales service, ensuring peace of mind and support throughout the product’s lifecycle.
- Compliance with Standards: Reliable suppliers ensure their products comply with relevant industry standards and regulations, which is crucial for safety and efficiency.
Taking the time to find and choose a reliable supplier for stainless steel gravity rollers near you is a critical step that impacts the effectiveness, reliability, and cost-efficiency of your conveyor system. By following the outlined steps and understanding the importance of this decision, you can establish a beneficial partnership that supports your operational goals.
Pricing and Purchasing Options for Stainless Steel Gravity Rollers
When it comes to integrating or upgrading your conveyor system with stainless steel gravity rollers, understanding the pricing landscape and knowing where to find the best purchasing options are key to making an informed decision. This section will delve into the pricing range for stainless steel gravity rollers, offer tips on securing the best deals, and provide insights on how to ensure you’re getting the best value for your investment.
Overview of the Pricing Range for Stainless Steel Gravity Rollers
The cost of stainless steel gravity rollers can vary widely based on several factors. Here are six points that outline the pricing range:
- Roller Diameter and Length: Larger and longer rollers typically cost more due to the increased amount of material and manufacturing effort required.
- Material Quality: High-grade stainless steel, known for its durability and corrosion resistance, may command a higher price.
- Load Capacity: Rollers designed to support heavier loads often come at a premium due to the need for stronger materials and more robust construction.
- Customization: Custom-made rollers to fit specific conveyor systems or applications can increase the price.
- Quantity: Purchasing in bulk often results in lower per-unit costs due to economies of scale.
- Supplier: Prices can vary significantly between suppliers based on their manufacturing processes, material sources, and overhead costs.
Some Tips on Finding the Best Deals for Stainless Steel Gravity Rollers
Securing the best deals requires a combination of research, negotiation, and timing. Consider these six tips:
- Compare Suppliers: Don’t settle for the first price you find. Compare offerings from multiple suppliers to ensure competitive pricing.
- Look for Bulk Discounts: If your project allows, purchasing in bulk can significantly reduce the cost per unit.
- Consider Used Options: For less critical applications, high-quality used rollers can provide substantial savings.
- Negotiate: Especially for large orders, there’s often room to negotiate on price. Don’t hesitate to ask for a better deal.
- Check for Overstock Sales: Suppliers may offer discounts on overstock items. These can be a great option for standard sizes.
- Seasonal Offers: Some suppliers may have sales during off-peak seasons. Keeping an eye out for these can lead to savings.
Information on Purchasing Stainless Steel Gravity Rollers for Sale and How to Get the Best Value
Getting the best value extends beyond just finding the lowest price. Consider these points to ensure you’re making a wise investment:
- Assess Quality: Ensure the rollers meet your required standards for durability and performance. Lower prices shouldn’t mean compromised quality.
- Warranty and Support: Check if the rollers come with a warranty and what kind of after-sales support the supplier offers.
- Delivery Costs: Factor in shipping or delivery costs, as these can add significantly to the overall price.
- Installation Services: Some suppliers offer installation services. While this may increase initial costs, it could save money in the long run by ensuring proper setup.
- Longevity and Maintenance: Consider the expected lifespan of the rollers and any maintenance they require. Lower upfront costs might lead to higher long-term expenses.
- Supplier Reputation: Work with reputable suppliers known for quality products and good customer service to ensure you’re getting value for your money.
By carefully considering these aspects of pricing and purchasing options for stainless steel gravity rollers, you can make an informed decision that balances cost with quality, durability, and service, ensuring your conveyor system operates efficiently for years to come.
Installation and Maintenance of Stainless Steel Gravity Rollers
Ensuring the proper installation and regular maintenance of stainless steel gravity rollers is crucial for the longevity and optimal performance of your conveyor system. This section provides a basic guide on how to correctly install these rollers and offers nine maintenance tips to keep them operating at their best.
Basic Guide on Installing Stainless Steel Gravity Rollers
Installing stainless steel gravity rollers correctly is essential for the smooth operation of your conveyor system. Follow these steps for a successful installation:
- Preparation: Before installation, ensure that the conveyor frame is level and stable. This will prevent uneven wear on the rollers and ensure smooth operation.
- Spacing: Properly space the rollers according to the manufacturer’s recommendations to support the load evenly and prevent material sagging between rollers.
- Alignment: Align the rollers so that they are parallel to each other and perpendicular to the direction of travel to ensure smooth and straight movement of materials.
- Securing: Secure the rollers in place using the provided mounting brackets or hardware. Ensure they are tightly fastened to prevent shifting during operation.
- Testing: Once installed, test the rollers with a few items to ensure they move smoothly and the system operates as expected.
Maintenance Tips to Ensure Longevity and Optimal Performance of the Rollers
Regular maintenance is key to extending the life of your stainless steel gravity rollers and maintaining the efficiency of your conveyor system. Here are nine maintenance tips:
- Regular Cleaning: Keep the rollers clean from dust, debris, and any materials that could cause build-up, which might hinder their movement or cause damage over time.
- Lubrication: If your rollers have bearings that require lubrication, ensure they are lubricated regularly with the appropriate type of lubricant as specified by the manufacturer.
- Inspection: Conduct regular inspections to check for signs of wear, damage, or misalignment. Early detection of issues can prevent more significant problems down the line.
- Adjustment: Adjust the tension and alignment of the rollers as needed to ensure they continue to operate smoothly and efficiently.
- Replacement of Worn Parts: Replace any rollers that show significant signs of wear or damage. Operating with damaged rollers can affect the performance of the entire system.
- Check for Corrosion: Even though stainless steel is corrosion-resistant, it’s important to check for any signs of corrosion, especially in harsh environments, and take corrective action if needed.
- Load Distribution: Regularly monitor load distribution to ensure that the system is not being overloaded, which can lead to premature wear and failure of the rollers.
- Training: Ensure that personnel are trained on the proper use and maintenance of the conveyor system to prevent misuse that could lead to damage.
- Professional Maintenance: Consider scheduling periodic maintenance checks by professionals who can conduct a thorough inspection and maintenance of the system.
By following these installation and maintenance guidelines for stainless steel gravity rollers, you can ensure that your conveyor system remains reliable, efficient, and productive over its lifespan. Proper care and regular maintenance not only extend the life of the rollers but also help in maintaining the overall efficiency of your material handling operations.
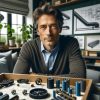
Jordan Smith, a seasoned professional with over 20 years of experience in the conveyor system industry. Jordan’s expertise lies in providing comprehensive solutions for conveyor rollers, belts, and accessories, catering to a wide range of industrial needs. From initial design and configuration to installation and meticulous troubleshooting, Jordan is adept at handling all aspects of conveyor system management. Whether you’re looking to upgrade your production line with efficient conveyor belts, require custom conveyor rollers for specific operations, or need expert advice on selecting the right conveyor accessories for your facility, Jordan is your reliable consultant. For any inquiries or assistance with conveyor system optimization, Jordan is available to share his wealth of knowledge and experience. Feel free to reach out at any time for professional guidance on all matters related to conveyor rollers, belts, and accessories.