Detailed Overview of ST Conveyor Belt Specification
An ST conveyor belt, or steel cord conveyor belt, is designed for high-strength applications. Composed of steel cords embedded within the belt, the ST conveyor belt offers exceptional tensile strength and durability, making it ideal for heavy-duty tasks such as transporting coal, ore, and bulk materials in mining operations. The steel cords provide excellent resistance to impact, tearing, and abrasion, ensuring a long service life even in harsh environments. Additionally, the low elongation properties of an ST conveyor belt help maintain consistent tension, reducing maintenance needs and improving overall efficiency in material handling operations.
ST Conveyor Belt: Comprehensive Guide to Steel Cord Conveyor Belt Specification PDF
Steel cord conveyor belts, commonly referred to as ST conveyor belts, are designed to handle the most demanding conditions and transport heavy loads over long distances. These belts are reinforced with steel cords, providing exceptional strength, durability, and resistance to wear and tear. This section provides a comprehensive guide to the specifications of steel cord conveyor belts, highlighting key parameters and performance characteristics. Understanding these specifications is crucial for selecting the right belt for your application and ensuring optimal functionality and longevity.
Key Specifications of ST Conveyor Belts
- Tensile Strength
The tensile strength of an ST conveyor belt is a critical specification that indicates the belt’s ability to withstand tension and carry heavy loads. Measured in Newtons per millimeter (N/mm), tensile strength is determined by the number and quality of steel cords embedded within the belt. High tensile strength ensures that the belt can handle substantial weight and resist stretching under heavy loads, making it suitable for mining, quarrying, and other heavy-duty applications.
- Belt Width
The width of the ST conveyor belt is another important specification, affecting the volume of material the belt can transport. Belt widths typically range from 500 mm to 2400 mm, depending on the application requirements. Wider belts are used for high-capacity operations, allowing for the efficient movement of large volumes of material. Selecting the appropriate belt width ensures that the conveyor system can handle the desired load without compromising performance.
- Belt Thickness
Belt thickness is determined by the combined thickness of the cover and the steel cord reinforcement. This specification is crucial for determining the belt’s durability and resistance to wear. Thicker belts offer enhanced protection against abrasion, impact, and punctures, extending the belt’s lifespan. The cover thickness, typically measured in millimeters, can vary based on the material being transported and the environmental conditions.
- Steel Cord Diameter and Spacing
The diameter and spacing of the steel cords within the belt are key factors influencing its strength and flexibility. Steel cord diameters usually range from 2.5 mm to 12 mm, with closer spacing providing greater conveyor belt tensile strength and load-bearing capacity. Proper spacing ensures even load distribution across the belt, minimizing the risk of failure and enhancing overall performance.
- Cover Grade and Material
The cover grade and material of an ST conveyor belt determine its resistance to abrasion, chemicals, heat, and other environmental factors. Common cover materials include natural rubber, synthetic rubber, and PVC. Each material offers specific benefits, such as heat resistance, oil resistance, and flame retardancy. Selecting the right cover grade ensures that the belt can withstand the operational environment and maintain its performance over time.
- Elongation at Break
Elongation at break is a specification that measures the belt’s ability to stretch before breaking. This characteristic is crucial for determining the belt’s flexibility and resistance to sudden impacts. Lower elongation values indicate a more rigid belt, while higher values suggest greater flexibility. Understanding the elongation at break helps in selecting a belt that can handle dynamic loads and varying operational conditions.
- Operating Temperature Range
The operating temperature range of an ST conveyor belt specifies the minimum and maximum temperatures the belt can withstand without degrading. This specification is essential for applications involving extreme temperatures, such as in steel mills or chemical plants. Ensuring that the belt can operate within the required temperature range prevents premature failure and maintains the belt’s integrity.
Importance of ST Conveyor Belt Specifications
- Performance and Efficiency
Understanding the specifications of an ST conveyor belt is crucial for ensuring optimal performance and efficiency. Selecting a belt with the appropriate tensile strength, width, and thickness ensures that it can handle the required load and operate smoothly without frequent maintenance or downtime.
- Durability and Longevity
Properly specified ST conveyor belts offer enhanced durability and longevity, reducing the need for frequent replacements. Key specifications such as steel cord diameter, cover grade, and elongation at break contribute to the belt’s resistance to wear, impact, and environmental factors, ensuring long-term reliability.
- Safety
Adhering to the correct specifications also enhances safety in industrial operations. Belts with adequate tensile strength and appropriate cover materials minimize the risk of belt failure and accidents, protecting both personnel and equipment.
- Cost-Effectiveness
While higher-specification belts may come with a higher initial cost, their durability and reduced maintenance requirements lead to cost savings over time. Investing in a properly specified ST conveyor belt ensures that the system operates efficiently and economically.
The specifications of steel cord conveyor belts play a crucial role in determining their performance, durability, and suitability for various industrial applications. By understanding key parameters such as tensile strength, belt width, thickness, steel cord diameter, cover grade, elongation at break, and operating temperature range, businesses can select the right ST conveyor belt for their needs. Properly specified belts ensure efficient material handling, enhanced safety, and long-term cost savings, making them an invaluable asset in heavy-duty operations.
Essential ST Conveyor Belt Parts
An ST conveyor belt system comprises various essential components that work together to ensure efficient material handling and transport. Each part plays a critical role in the overall operation, contributing to the belt’s functionality, durability, and performance. This section focuses on the various components that make up an ST conveyor belt, describing each part’s role and how it contributes to the overall operation of the conveyor belt system.
Key Components of an ST Conveyor Belt
- Steel Cords
The steel cords are the backbone of an ST conveyor belt, providing the primary reinforcement and tensile strength. These cords are made from high-strength steel and are embedded within the belt to support heavy loads and resist stretching. The diameter and spacing of the steel cords are crucial factors that influence the belt’s strength and flexibility. Properly designed steel cords ensure even load distribution and enhance the belt’s durability.
- Cover Layer
The cover layer of an ST conveyor belt is the outermost layer that comes into direct contact with the transported material. This layer is typically made from rubber, PVC, or other synthetic materials, providing protection against abrasion, impact, and environmental factors. The cover layer’s thickness and material composition are selected based on the specific requirements of the application, ensuring optimal performance and longevity.
- Skim Coating
Skim coating is the layer of rubber or other material that surrounds the steel cords, bonding them to the cover layers. This coating plays a vital role in enhancing the adhesion between the cords and the covers, preventing delamination and ensuring the belt’s structural integrity. Skim coating also provides additional protection against moisture and chemicals, extending the belt’s lifespan.
- Bottom Cover
The bottom cover is the layer of material on the underside of the ST conveyor belt, providing additional protection and support. Like the top cover, the bottom cover is made from durable materials that resist wear and environmental factors. The bottom cover helps maintain the belt’s shape and stability, ensuring smooth operation on the conveyor system’s rollers and pulleys.
- Edge Reinforcement
Edge reinforcement is a critical component that protects the edges of the ST conveyor belt from damage and wear. This reinforcement typically consists of extra layers of material or specialized coatings that provide additional strength and durability. Edge reinforcement prevents fraying and tearing, ensuring that the belt remains intact and functional even under heavy use.
- Splicing Materials
Splicing materials are used to join the ends of the ST conveyor belt, creating a continuous loop. These materials include adhesives, vulcanizing agents, and mechanical fasteners, each selected based on the belt’s specifications and the application requirements. Proper splicing ensures a strong, seamless connection that maintains the belt’s strength and performance.
- Pulley Lagging
Pulley lagging is the covering applied to the conveyor system’s pulleys to increase friction and reduce belt slippage. This lagging is typically made from rubber or ceramic materials and provides additional grip and traction. Pulley lagging enhances the efficiency of the conveyor system, ensuring smooth operation and reducing wear on the belt.
The Role of Each Component
- Steel Cords
The steel cords provide the primary reinforcement for the ST conveyor belt, enabling it to carry heavy loads and resist stretching. These cords ensure that the belt maintains its shape and structural integrity, even under demanding conditions. The steel cords’ strength and flexibility are crucial for the belt’s performance and durability.
- Cover Layer
The cover layer protects the ST conveyor belt from abrasion, impact, and environmental factors. This layer ensures that the belt can withstand the rigors of the application, maintaining its performance and longevity. The cover layer also provides the necessary traction for transporting materials efficiently.
- Skim Coating
Skim coating enhances the adhesion between the steel cords and the cover layers, preventing delamination and ensuring the belt’s structural integrity. This coating also provides additional protection against moisture and chemicals, extending the belt’s lifespan and maintaining its performance.
- Bottom Cover
The bottom cover provides additional support and protection for the ST conveyor belt, ensuring smooth operation on the conveyor system’s rollers and pulleys. This layer helps maintain the belt’s shape and stability, reducing wear and extending the belt’s lifespan.
- Edge Reinforcement
Edge reinforcement protects the edges of the ST conveyor belt from damage and wear, preventing fraying and tearing. This reinforcement ensures that the belt remains intact and functional, even under heavy use. Edge reinforcement is crucial for maintaining the belt’s overall durability and performance.
- Splicing Materials
Splicing materials create a strong, seamless connection between the ends of the ST conveyor belt, ensuring continuous operation. Proper splicing maintains the belt’s strength and performance, preventing weak points that could lead to failure. Splicing materials are essential for creating a reliable, durable conveyor belt system.
- Pulley Lagging
Pulley lagging increases friction and reduces belt slippage, enhancing the efficiency of the conveyor system. This covering provides additional grip and traction, ensuring smooth operation and reducing wear on the belt. Pulley lagging is crucial for maintaining the conveyor system’s performance and longevity.
An ST conveyor belt is composed of various essential components, each playing a critical role in the belt’s functionality, durability, and performance. Understanding the role of each part, from steel cords and cover layers to skim coating, bottom cover, edge reinforcement, splicing materials, and pulley lagging, is crucial for maintaining and optimizing the conveyor belt system. Proper selection, installation, and maintenance of these components ensure that the ST conveyor belt can handle the demands of various industrial applications, providing reliable and efficient material handling solutions.
ST Conveyor Belt: Factors Influencing Steel Cord Conveyor Belt Price
When considering the purchase of an ST conveyor belt, several factors influence the overall cost. Understanding these factors can help businesses make informed decisions and budget appropriately for their material handling needs. This section will discuss the key elements that affect the pricing of steel cord conveyor belts, including materials, manufacturing processes, and market demand.
Materials
- Steel Cords: The primary cost driver for ST conveyor belts is the steel cords themselves. The quality and grade of steel used can significantly impact the price. High-tensile steel cords, designed to provide superior strength and durability, are more expensive than lower-grade steel options. The number of steel cords embedded in the belt also affects the cost, with more cords typically translating to higher prices.
- Rubber Compounds: The type and quality of rubber used in the conveyor belt’s construction also play a crucial role in pricing. Rubber compounds with enhanced properties, such as increased abrasion resistance, heat resistance, and flexibility, are generally more costly. The thickness of the rubber covers on the top and bottom of the belt can further influence the price, with thicker covers offering greater protection and longevity.
- Additional Materials: Other materials, such as adhesion agents and anti-corrosive coatings, may be used to enhance the performance and lifespan of the ST conveyor belt. These additional materials can add to the overall cost but are often necessary for specific applications that require extra durability and protection.
Manufacturing Processes
- Production Techniques: The manufacturing process for ST conveyor belts is complex and requires advanced techniques to ensure the proper embedding of steel cords within the rubber matrix. Techniques such as hot vulcanization and cold bonding are used to achieve the desired properties of the conveyor belt. The precision and expertise required for these processes contribute to the overall cost.
- Quality Control: Ensuring the quality and consistency of ST conveyor belts involves rigorous testing and inspection throughout the manufacturing process. Quality control measures, such as X-ray inspection of steel cord alignment and tensile strength testing, are essential to maintain high standards. These quality assurance steps add to the production costs but are crucial for delivering reliable and safe conveyor belts.
- Customization: Customizing ST conveyor belts to meet specific application requirements can also influence the price. Customizations may include varying the belt width, length, cover thickness, and the number of plies. Tailoring the belt to fit unique operational needs often involves additional design and production steps, resulting in higher costs.
Market Demand
- Industry Demand: The demand for ST conveyor belts can vary across different industries, such as mining, construction, and manufacturing. High demand in specific sectors can drive up prices due to increased competition for available products. Conversely, periods of low demand may result in more competitive pricing as manufacturers seek to attract buyers.
- Economic Conditions: Economic factors, such as inflation, currency exchange rates, and raw material costs, can impact the pricing of ST conveyor belts. Fluctuations in the global economy can lead to changes in production costs and market prices, influencing the overall cost of conveyor belts.
- Technological Advancements: Innovations in conveyor belt technology can affect pricing. New materials, improved manufacturing processes, and enhanced performance features can lead to higher initial costs but may offer long-term savings through increased efficiency and reduced maintenance requirements.
Additional Considerations
- Transportation and Logistics: The cost of transporting and delivering ST conveyor belts to the installation site can also influence the overall price. Factors such as distance, shipping method, and handling requirements play a role in determining transportation costs.
- Installation and Maintenance: The expenses associated with installing and maintaining ST conveyor belts should also be considered. Proper installation ensures optimal performance and longevity, while regular maintenance helps prevent costly repairs and downtime. These costs, though not directly related to the purchase price, are important factors in the total cost of ownership.
- Supplier and Brand Reputation: The reputation and reliability of the conveyor belt supplier can impact pricing. Established brands with a track record of quality and performance may charge premium prices for their products. However, the assurance of receiving a high-quality, reliable ST conveyor belt often justifies the higher cost.
The price of an ST conveyor belt is influenced by various factors, including the materials used, manufacturing processes, market demand, and additional considerations such as transportation and maintenance. By understanding these factors, businesses can make informed decisions when budgeting for their conveyor belt needs. Investing in a high-quality ST conveyor belt may involve higher initial costs, but the benefits of durability, efficiency, and reduced maintenance can lead to long-term savings and improved operational performance.
ST Conveyor Belt: Detailed Overview of Steel Cord Belt Specification
Understanding the technical specifications of an ST conveyor belt is crucial for selecting the right belt for specific industrial applications. This section provides a comprehensive overview of the key specifications that define the performance and capabilities of steel cord conveyor belts, including their construction, tensile strength, and other critical features.
Construction
- Steel Cords: The backbone of an ST conveyor belt is the steel cords embedded within the rubber matrix. These cords are made from high-tensile steel and are designed to provide exceptional strength and durability. The number and arrangement of steel cords can vary based on the belt’s intended use, with more cords providing greater load-carrying capacity.
- Rubber Covers: The steel cords are encased in rubber covers on both the top and bottom of the belt. These covers protect the steel cords from damage and environmental factors, such as abrasion, impact, and chemicals. The thickness of the rubber covers is a key specification, with thicker covers offering enhanced protection and longevity.
- Adhesion Layers: Adhesion layers are used to bond the steel cords to the rubber matrix. These layers ensure that the steel cords remain securely embedded within the rubber, providing a cohesive and durable conveyor belt. High-quality adhesion layers contribute to the overall strength and performance of the belt.
Tensile Strength
- Nominal Tensile Strength: The nominal tensile strength of an ST conveyor belt is a critical specification that indicates the maximum load the belt can handle before breaking. This value is typically measured in newtons per millimeter (N/mm) and reflects the combined strength of the steel cords and rubber matrix. High tensile strength ensures the belt can transport heavy loads over long distances without stretching or breaking.
- Working Tension: The working tension is the maximum load the belt can handle during normal operation without experiencing significant elongation or damage. This value is usually expressed as a percentage of the nominal tensile strength and helps determine the belt’s suitability for specific applications.
- Elongation at Break: Elongation at break indicates the belt’s ability to stretch under tension before breaking. This specification is expressed as a percentage and provides insight into the belt’s flexibility and resilience. Low elongation values are desirable for maintaining consistent tension and reducing maintenance needs.
Abrasion and Impact Resistance
- Abrasion Resistance: The ability of an ST conveyor belt to resist wear and abrasion is crucial for its longevity and performance. Abrasion resistance is typically measured using standardized tests, such as the DIN 22102 standard, which quantifies the material loss in cubic millimeters. High abrasion resistance ensures the belt can withstand continuous contact with abrasive materials, reducing wear and extending the belt’s service life.
- Impact Resistance: Impact resistance refers to the belt’s ability to absorb and withstand impacts from heavy or sharp materials. This specification is important for applications where the belt is exposed to frequent impacts, such as in mining operations. High impact resistance prevents damage to the belt and ensures reliable performance under challenging conditions.
Fire and Chemical Resistance
- Fire Resistance: In industries such as mining and chemical processing, fire resistance is a critical safety feature for conveyor belts. Fire-resistant ST conveyor belts are designed to withstand high temperatures and resist ignition, preventing the spread of fire along the belt. Compliance with fire safety standards, such as ISO 340 and EN 12882, is essential for ensuring the belt’s safety and suitability for hazardous environments.
- Chemical Resistance: Chemical resistance is another important specification for ST conveyor belts used in environments where they are exposed to oils, acids, solvents, and other chemicals. Chemical-resistant belts are made from specialized rubber compounds that prevent degradation and maintain performance in harsh chemical environments. This resistance extends the belt’s lifespan and reduces the need for frequent replacements.
Dimensional Specifications
- Belt Width and Length: The width and length of an ST conveyor belt are critical dimensions that must match the requirements of the conveyor system. Standard belt widths range from 500 mm to 2400 mm, while custom widths can be manufactured to meet specific needs. The length of the belt is determined by the distance it needs to cover and the configuration of the conveyor system.
- Cover Thickness: The thickness of the rubber covers on the top and bottom of the belt is an important specification that affects the belt’s durability and protection. Standard cover thicknesses range from 3 mm to 15 mm, with thicker covers providing greater resistance to wear and impact.
- Carcass Thickness: The overall thickness of the conveyor belt, including the steel cords and rubber covers, is referred to as the carcass thickness. This specification influences the belt’s flexibility, load-carrying capacity, and resistance to damage.
The detailed specifications of an ST conveyor belt encompass various aspects, including its construction, tensile strength, abrasion and impact resistance, fire and chemical resistance, and dimensional attributes. Understanding these specifications is essential for selecting the right conveyor belt for specific industrial applications. By considering factors such as material quality, manufacturing processes, and operational requirements, businesses can choose an ST conveyor belt that delivers optimal performance, durability, and safety. Investing in a high-quality steel cord conveyor belt ensures efficient material handling,
ST Conveyor Belt: Applications and Benefits of Rubber Conveyor Belt
Rubber conveyor belts are widely used in various industries due to their versatility, durability, and efficiency. These belts are made from a combination of rubber and other materials, providing the necessary strength and flexibility for a range of applications. This section highlights the uses of rubber conveyor belts in different industries, discusses their advantages, and explains why they are a popular choice for many conveyor systems.
Applications of Rubber Conveyor Belts
- Mining Industry
Rubber conveyor belts are extensively used in the mining industry for transporting bulk materials such as coal, ore, and gravel. These belts are designed to withstand harsh conditions, including abrasive materials, heavy loads, and extreme temperatures. Their durability and resistance to wear and tear make them ideal for mining operations, ensuring efficient and continuous material handling.
- Construction Industry
In the construction industry, rubber conveyor belts are used to transport construction materials such as sand, cement, gravel, and bricks. These belts facilitate the efficient movement of materials on construction sites, reducing the need for manual labor and improving productivity. Rubber conveyor belts are also used in the demolition industry for handling debris and waste materials.
- Agricultural Sector
Rubber conveyor belts play a crucial role in the agricultural sector by transporting harvested crops, seeds, and fertilizers. They are used in various agricultural machines, such as combine harvesters and grain conveyors, to streamline the processing and handling of agricultural products. The flexibility and durability of rubber conveyor belts ensure smooth and efficient operation in agricultural applications.
- Food Processing Industry
In the food processing industry, rubber conveyor belts are used to transport raw materials and finished products through different stages of production. These belts are designed to meet strict hygiene and safety standards, ensuring that food products are handled safely and efficiently. Rubber conveyor belts are also resistant to oils, fats, and chemicals, making them suitable for food processing environments.
- Recycling and Waste Management
Rubber conveyor belts are used in recycling and waste management facilities to transport recyclable materials such as plastics, metals, and paper. These belts are designed to handle various types of waste materials, providing an efficient solution for sorting and processing recyclables. The durability and resistance to wear and tear of rubber conveyor belts ensure reliable performance in recycling operations.
- Manufacturing Industry
In the manufacturing industry, rubber conveyor belts are used to transport raw materials, components, and finished products through different stages of production. These belts are essential for automating material handling processes, improving efficiency, and reducing labor costs. Rubber conveyor belts are also used in assembly lines and packaging systems to streamline manufacturing operations.
Benefits of Rubber Conveyor Belts
- Durability
One of the primary benefits of rubber conveyor belts is their durability. These belts are designed to withstand harsh conditions and heavy loads, ensuring long-lasting performance. The high resistance to wear and tear makes rubber conveyor belts suitable for demanding industrial applications, reducing the need for frequent replacements and maintenance.
- Flexibility
Rubber conveyor belts offer excellent flexibility, allowing them to adapt to various conveyor configurations and applications. This flexibility ensures smooth and efficient operation, even in complex conveyor systems with multiple bends and inclines. The ability to handle different materials and conditions makes rubber conveyor belts a versatile solution for various industries.
- Cost-Effectiveness
Rubber conveyor belts are a cost-effective solution for material handling due to their durability and low maintenance requirements. The long lifespan of rubber conveyor belts reduces the need for frequent replacements, resulting in lower operational costs. Additionally, the efficiency and reliability of rubber conveyor belts improve productivity, contributing to cost savings.
- Resistance to Chemicals and Oils
Rubber conveyor belts are resistant to various chemicals, oils, and fats, making them suitable for use in industries where exposure to these substances is common. This resistance ensures that the belts maintain their performance and integrity, even in challenging environments. The ability to handle chemicals and oils makes rubber conveyor belts ideal for food processing, manufacturing, and recycling applications.
- High Load Capacity
Rubber conveyor belts are designed to handle heavy loads, making them suitable for transporting bulk materials in industries such as mining, construction, and agriculture. The high tensile strength of rubber conveyor belts ensures that they can carry substantial weight without stretching or breaking. This load-bearing capacity enhances the efficiency and reliability of material handling processes.
- Hygiene and Safety
In industries such as food processing and pharmaceuticals, hygiene and safety are critical considerations. Rubber conveyor belts are designed to meet strict hygiene standards, ensuring that products are handled safely and without contamination. The smooth surface of rubber conveyor belts also prevents the buildup of debris and bacteria, maintaining a clean and safe conveyor system.
- Noise Reduction
Rubber conveyor belts operate quietly, reducing noise levels in industrial environments. This noise reduction is particularly beneficial in facilities where loud machinery can create an uncomfortable or hazardous working environment. The quiet operation of rubber conveyor belts contributes to a safer and more pleasant workplace.
Rubber conveyor belts are an essential component of many industrial operations, offering numerous benefits such as durability, flexibility, cost-effectiveness, and high load capacity. Their versatility allows them to be used in a wide range of applications, from mining and construction to food processing and recycling. By choosing rubber conveyor belts, businesses can ensure efficient, reliable, and safe material handling solutions that enhance productivity and reduce operational costs.
ST Conveyor Belt: Features and Advantages of Steel Conveyor Belt
Steel conveyor belts, often referred to as ST conveyor belts, are renowned for their high tensile strength, durability, and resistance to extreme conditions. These belts are designed to handle heavy loads and are commonly used in industries that require robust and reliable material handling solutions. This section explores the unique features of steel conveyor belts and discusses the benefits they offer in demanding industrial environments.
Key Features of ST Conveyor Belts
- High Tensile Strength
One of the most significant features of ST conveyor belts is their high tensile strength. The steel cords embedded within the belt provide exceptional reinforcement, allowing the belt to handle heavy loads without stretching or breaking. This high tensile strength makes ST conveyor belts ideal for applications that involve the transport of large volumes of materials over long distances.
- Durability
ST conveyor belts are known for their durability and resistance to wear and tear. The steel cords and robust cover materials used in these belts ensure that they can withstand harsh conditions, including abrasive materials, high impact, and extreme temperatures. This durability extends the lifespan of the belt, reducing the need for frequent replacements and maintenance.
- Low Elongation
Steel conveyor belts exhibit low elongation, meaning they do not stretch significantly under tension. This characteristic ensures that the belt maintains its shape and structural integrity, even under heavy loads. Low elongation is crucial for maintaining consistent performance and preventing issues such as belt slippage and misalignment.
- Resistance to Impact and Puncture
The steel cords in ST conveyor belts provide excellent resistance to impact and puncture. This resistance is essential for applications where the belt is exposed to sharp or heavy objects that could cause damage. The robust construction of steel conveyor belts ensures that they can handle such conditions without compromising performance.
- Heat and Chemical Resistance
ST conveyor belts are designed to withstand high temperatures and exposure to chemicals, making them suitable for use in challenging industrial environments. The materials used in the construction of these belts are selected for their ability to resist degradation from heat and chemical exposure, ensuring long-term performance and reliability.
- Flexible Design
Despite their robust construction, ST conveyor belts are designed to be flexible, allowing them to adapt to various conveyor configurations. This flexibility ensures smooth operation and easy installation, making them suitable for a wide range of industrial applications.
Advantages of ST Conveyor Belts
- Enhanced Load-Bearing Capacity
The high tensile strength and low elongation of ST conveyor belts allow them to handle heavy loads efficiently. This enhanced load-bearing capacity makes them ideal for industries such as mining, construction, and manufacturing, where the transport of large volumes of materials is required.
- Increased Lifespan
The durability and resistance to wear and tear of ST conveyor belts result in an extended lifespan. This increased lifespan reduces the need for frequent replacements, leading to cost savings and improved operational efficiency. The long-term reliability of ST conveyor belts makes them a cost-effective solution for material handling.
- Improved Safety
ST conveyor belts provide improved safety in industrial operations due to their resistance to impact, puncture, and extreme conditions. The robust construction of these belts minimizes the risk of belt failure and accidents, protecting both personnel and equipment. Enhanced safety features contribute to a safer working environment.
- Consistent Performance
The low elongation and high tensile strength of ST conveyor belts ensure consistent performance, even under demanding conditions. This consistency is crucial for maintaining efficient material handling processes and minimizing downtime. Reliable performance enhances productivity and ensures smooth operation.
- Versatile Applications
The unique features of ST conveyor belts make them suitable for a wide range of applications. They can be used in industries such as mining, construction, manufacturing, and logistics, providing a versatile solution for various material handling needs. The ability to handle different materials and conditions enhances the flexibility of ST conveyor belts.
- Cost Savings
The durability, reliability, and long lifespan of ST conveyor belt lead to significant cost savings. Reduced maintenance and replacement requirements lower operational costs, while the efficiency and performance of the belts improve productivity. Investing in ST conveyor belts provides a high return on investment.
FAQs about ST Conveyor Belt
An ST conveyor belt, also known as a steel cord conveyor belt, is a type of conveyor belt that uses steel cords as the tension element. These steel cords are embedded in the rubber cover of the belt, providing exceptional tensile strength and durability. ST conveyor belts are designed to handle very high loads and are commonly used in industries such as mining, where they transport heavy materials like coal, ore, and other bulk materials over long distances. The steel cords offer excellent resistance to impact, tearing, and abrasion, ensuring long-lasting performance even in the harshest conditions. These belts also have low elongation properties, which help maintain consistent tension and reduce maintenance needs.
Conveyor belts come in various types, but three of the most common types are:
Flat Belt Conveyors: These are the most widely used type of conveyor belt, ideal for transporting items in a straight line. They consist of a continuous loop of material, usually rubber or fabric, driven by pulleys. Flat belt conveyors are commonly used in manufacturing, warehousing, and assembly lines due to their simplicity and versatility.
Modular Belt Conveyors: Modular belts are made up of interlocking plastic modules, which allow for easy replacement and maintenance. These belts are highly durable and can handle heavy loads, making them suitable for applications in the food and beverage industry, automotive sector, and other heavy-duty environments. The modular design also allows for customization in terms of width and length.
Cleated Belt Conveyors: Cleated belts feature raised sections or cleats that help in carrying materials up inclined planes or preventing them from rolling back. They are particularly useful in industries where items need to be transported uphill or downhill, such as agriculture, construction, and recycling. Cleated belt conveyors ensure that materials stay in place during transport, increasing efficiency and safety.
The primary difference between belt and slat conveyors lies in their design and the materials they are best suited to transport:
Belt Conveyors: Belt conveyors use a continuous belt made of rubber, fabric, or other materials to transport items. They are ideal for moving lightweight to medium-weight materials and are commonly used in industries such as manufacturing, warehousing, and food processing. Belt conveyors are versatile and can handle a variety of items, including bulk materials and packaged goods.
Slat Conveyors: Slat conveyors consist of a series of slats or plates, usually made of metal or plastic, connected to a chain. The slats provide a stable surface for transporting heavy or bulky items that would be difficult to move on a belt conveyor. Slat conveyors are often used in applications requiring the transportation of large, heavy, or awkwardly shaped items, such as automotive parts, appliances, and machinery. They offer greater strength and durability compared to belt conveyors and can handle higher loads.
A V belt conveyor refers to a type of conveyor system that uses V-belts, which are belts with a V-shaped cross-section. These belts run in matching V-shaped grooves in the pulleys, ensuring a secure grip and preventing slippage. V belt conveyors are known for their high efficiency and ability to transmit significant power over long distances. They are commonly used in applications requiring high torque and speed, such as in industrial machinery, agricultural equipment, and automotive systems. The V shape of the belt provides better traction, reducing the risk of belt slippage and improving the overall performance and longevity of the conveyor system.
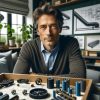
Jordan Smith, a seasoned professional with over 20 years of experience in the conveyor system industry. Jordan’s expertise lies in providing comprehensive solutions for conveyor rollers, belts, and accessories, catering to a wide range of industrial needs. From initial design and configuration to installation and meticulous troubleshooting, Jordan is adept at handling all aspects of conveyor system management. Whether you’re looking to upgrade your production line with efficient conveyor belts, require custom conveyor rollers for specific operations, or need expert advice on selecting the right conveyor accessories for your facility, Jordan is your reliable consultant. For any inquiries or assistance with conveyor system optimization, Jordan is available to share his wealth of knowledge and experience. Feel free to reach out at any time for professional guidance on all matters related to conveyor rollers, belts, and accessories.