What is a Snub Pulley? Key Functions Explained
A snub pulley is a critical component in belt conveyor systems, designed to increase the wrap angle of the conveyor belt around the drive pulley. By enhancing the contact between the belt and the drive pulley, the snub pulley improves belt traction and reduces slippage, ensuring efficient power transmission. This increased friction is crucial for maintaining consistent belt movement and preventing operational disruptions. The snub pulley is typically positioned close to the drive pulley and helps maintain the proper tension and alignment of the belt, thereby extending the life of the conveyor system. Implementing a snub pulley is essential for optimizing the performance and reliability of conveyor systems in various industrial applications.
Deflector Pulley in Conveyor Operations
In conveyor systems, various components work in harmony to ensure efficient and reliable material handling. Among these components, the deflector pulley plays a crucial role in directing the belt path and ensuring smooth operation. Its interaction with the snub pulley is essential for optimal belt management, enhancing the overall performance and longevity of the conveyor system. This section explores the role of the deflector pulley in directing the belt path and its interaction with the snub pulley.
Role of Deflector Pulley in Directing Belt Path
The deflector pulley, also known as a bend pulley, is a pivotal component in conveyor systems, primarily responsible for changing the direction of the conveyor belt. This ability to redirect the belt path is essential for various reasons:
Directional Control: The primary function of the deflector pulley is to provide directional control of the conveyor belt. By changing the belt’s direction, the deflector pulley allows the conveyor system to navigate around obstacles, optimize space, and create more efficient material handling routes. This capability is particularly important in complex conveyor systems where the belt needs to traverse different levels or bypass structural elements.
Tension Management: Proper tension management is critical for the smooth operation of a conveyor belt. The deflector pulley helps maintain the correct tension in the belt by redirecting its path and ensuring even distribution of tension across the belt’s length. This uniform tension distribution prevents slack and reduces the risk of belt slippage, which can lead to operational inefficiencies and increased wear and tear.
Minimizing Wear and Tear: By providing smooth directional changes, the deflector pulley minimizes the stress and strain on the conveyor belt. This reduction in stress helps prevent premature wear and tear, extending the lifespan of the belt and reducing maintenance costs. The deflector pulley’s ability to guide the belt smoothly around bends and turns is crucial for maintaining the belt’s integrity and ensuring long-term reliability.
Space Optimization: In many industrial settings, space is a valuable asset. The deflector pulley enables conveyor systems to be designed in a more compact and efficient manner by allowing the belt to navigate tight spaces and sharp turns. This space optimization is essential for maximizing the use of available floor space and creating more streamlined material handling processes.
Interaction with Snub Pulley for Optimal Belt Management
The interaction between the deflector pulley and the snub pulley is vital for achieving optimal belt management in conveyor systems. While the deflector pulley is responsible for changing the belt’s direction, the snub pulley plays a complementary role in enhancing belt traction and alignment.
Enhanced Belt Traction: The snub pulley is strategically positioned to increase the wrap angle of the conveyor belt around the drive pulley. By increasing this wrap angle, the snub pulley enhances the friction between the belt and the drive pulley, providing better traction. This improved traction is essential for preventing belt slippage, particularly in high-tension applications or when handling heavy loads. The combined action of the deflector pulley directing the belt and the snub pulley increasing traction ensures smooth and efficient belt movement.
Improved Belt Alignment: Belt alignment is crucial for the efficient operation of conveyor systems. Misalignment can lead to uneven wear, increased maintenance, and potential system failures. The snub pulley helps to maintain proper belt alignment by keeping the belt centered on the pulleys and ensuring it follows the intended path. When used in conjunction with the deflector pulley, the snub pulley provides additional control over the belt’s position, reducing the risk of misalignment and enhancing overall system reliability.
Tension Control and Distribution: Both the deflector pulley and the snub pulley contribute to effective tension control and distribution across the conveyor belt. The deflector pulley helps manage tension by directing the belt’s path, while the snub pulley ensures even tension distribution by increasing the wrap angle around the drive pulley. This combined action helps maintain consistent tension throughout the belt, reducing the likelihood of slack or excessive tension that could lead to operational issues.
Reduced Belt Wear: The coordinated interaction between the deflector pulley and the snub pulley helps to minimize belt wear by ensuring smooth transitions and optimal tension management. The deflector pulley reduces stress on the belt during directional changes, while the snub pulley enhances traction and alignment. This synergy reduces the overall wear and tear on the belt, leading to longer belt life and lower maintenance costs.
Operational Efficiency: The combined use of deflector and snub pulleys contributes to the overall operational efficiency of conveyor systems. By providing precise directional control, enhanced traction, and improved alignment, these pulleys ensure that the conveyor belt operates smoothly and reliably. This efficiency translates to increased productivity, reduced downtime, and lower operational costs, making the interaction between deflector and snub pulleys a critical aspect of conveyor system design and operation.
Versatility in Applications: The versatility of deflector and snub pulleys allows them to be used in a wide range of conveyor applications. Whether in mining, manufacturing, logistics, or food processing, these pulleys can be adapted to meet the specific needs of different industries. Their ability to handle various belt types, load capacities, and operational conditions makes them indispensable components in modern conveyor systems.
Installation and Maintenance Considerations: Proper installation and maintenance of deflector and snub pulleys are essential for ensuring their optimal performance. During installation, it is important to position the pulleys correctly to achieve the desired belt path and wrap angle. Regular inspections and maintenance are necessary to check for signs of wear, misalignment, or tension issues. Timely replacement of worn or damaged pulleys helps prevent potential system failures and ensures continuous, efficient operation.
What is Snub Pulley
How Snub Pulley Supports Tail Pulley Functions
In conveyor systems, the efficient and reliable operation of the belt relies on various components working in harmony. One critical component is the snub pulley, which plays a vital role in supporting the functions of the tail pulley. The snub pulley enhances the performance and longevity of the conveyor system by improving belt tension, alignment, and tracking.
Snub Pulley Functionality:
The snub pulley is typically located close to the drive pulley and tail pulley in a conveyor system. Its primary function is to increase the angle of contact between the conveyor belt and the pulleys, thereby improving the grip and traction of the belt on the drive pulley. This enhanced contact helps in transferring the driving force more efficiently, reducing slippage and ensuring smooth belt movement.
Supporting Tail Pulley Functions:
- Improving Belt Tension: The snub pulley helps maintain proper belt tension, which is crucial for the smooth operation of the conveyor system. By increasing the wrap angle around the drive and tail pulleys, the snub pulley ensures that the belt remains taut, preventing sagging and reducing the risk of belt misalignment. Proper tension also minimizes wear and tear on the belt and other conveyor components, extending their lifespan.
- Enhancing Belt Tracking: Belt tracking refers to the alignment of the conveyor belt as it moves along the pulleys. Misalignment can cause the belt to run off track, leading to spillage, damage, and increased maintenance costs. The snub pulley plays a crucial role in guiding the belt and keeping it centered on the pulleys. By adjusting the position and angle of the snub pulley, operators can fine-tune the belt tracking, ensuring optimal alignment and reducing the risk of operational disruptions.
- Reducing Belt Slippage: Slippage occurs when the conveyor belt loses traction with the drive pulley, leading to inefficient material handling and increased wear on the belt. The snub pulley enhances the grip of the belt on the drive pulley by increasing the wrap angle, thereby reducing slippage. This improved traction ensures that the conveyor system operates efficiently, with minimal downtime and maintenance requirements.
- Supporting Load Distribution: The snub pulley helps distribute the load more evenly across the conveyor belt, reducing the strain on specific sections and preventing localized wear. This balanced load distribution enhances the overall durability and performance of the conveyor system, ensuring consistent material handling and minimizing the risk of belt failure.
Bend Pulley Function in Conveyor Systems
Definition and Application of Bend Pulley
A bend pulley is another essential component in conveyor systems, primarily used to change the direction of the conveyor belt. Unlike the snub pulley, which enhances belt tension and tracking, the bend pulley serves a different purpose by altering the belt’s pathway to fit the layout of the conveyor system.
Definition:
The bend pulley is typically installed at points where the conveyor belt needs to change direction or navigate around obstacles. It can be placed at the tail end, take-up, or any other point along the conveyor system where a directional change is necessary. The bend pulley does not contribute to driving the belt but instead guides it through the desired pathway.
Application:
Bend pulleys are commonly used in complex conveyor systems where space constraints or design requirements necessitate changes in the belt’s direction. They help the conveyor belt navigate turns, inclines, and declines, ensuring that the material is transported efficiently and safely through the system. Bend pulleys are also used in tandem with other pulleys, such as snub pulleys and take-up pulleys, to create a comprehensive and efficient conveyor system layout.
How Bend Pulley Differs from Snub Pulley
While both bend pulleys and snub pulleys are crucial for the proper functioning of conveyor systems, they serve different purposes and have distinct characteristics.
Primary Function:
- Snub Pulley: The main function of the snub pulley is to increase the wrap angle of the conveyor belt around the drive and tail pulleys, enhancing traction, tension, and tracking. It supports the efficient transfer of driving force and minimizes slippage.
- Bend Pulley: The bend pulley primarily changes the direction of the conveyor belt, guiding it through turns and around obstacles. It does not contribute to driving the belt but ensures the smooth navigation of the belt through the system layout.
Location in Conveyor System:
- Snub Pulley: Snub pulleys are typically located close to the drive pulley and tail pulley. They are strategically positioned to increase the wrap angle and improve belt traction.
- Bend Pulley: Bend pulleys can be placed at various points along the conveyor system where directional changes are required. They are not limited to a specific location and can be installed wherever needed to guide the belt.
Impact on Belt Tension and Tracking:
- Snub Pulley: By increasing the wrap angle, snub pulleys play a significant role in maintaining proper belt tension and improving belt tracking. They help ensure that the belt remains aligned and operates efficiently.
- Bend Pulley: Bend pulleys do not directly impact belt tension or tracking. Their primary role is to guide the belt through directional changes, ensuring that the belt follows the desired pathway without disruption.
How about Tail Pulley and Snub Pulley Interaction
In conveyor systems, each component plays a crucial role in ensuring smooth and efficient operation. Two key components, the tail pulley and the snub pulley, work together to optimize belt performance and longevity. This section explores the role of the tail pulley in conveyor systems and how the snub pulley supports its functions.
Role of Tail Pulley in Conveyor Systems
The tail pulley is a fundamental component located at the end of the conveyor system, opposite the drive pulley. Its primary functions are crucial for the overall efficiency and reliability of the conveyor system:
Belt Tensioning: One of the primary roles of the tail pulley is to provide the necessary tension to the conveyor belt. Proper tensioning is essential to prevent slippage, ensure smooth belt movement, and maintain the alignment of the belt. The tail pulley, often adjustable, allows operators to fine-tune the tension to match the specific requirements of the conveyor system and the materials being transported.
Direction Reversal: The tail pulley serves as the return point for the conveyor belt, reversing its direction and guiding it back towards the drive pulley. This function is essential for creating a continuous loop that enables the conveyor to transport materials from one point to another efficiently. By ensuring smooth direction reversal, the tail pulley minimizes stress on the belt and reduces the risk of wear and tear.
Support and Stability: The tail pulley provides support and stability to the conveyor belt, particularly in areas where the belt transitions from the carrying side to the return side. This support is crucial for maintaining the belt’s alignment and preventing sagging, which can lead to operational inefficiencies and increased maintenance needs. The tail pulley’s robust construction helps withstand the forces exerted by the moving belt and the materials being transported.
Belt Cleaning and Maintenance: The location of the tail pulley makes it an ideal point for installing belt cleaning devices, such as scrapers and brushes. These devices remove residual material from the belt, preventing build-up and reducing wear. By maintaining a clean belt, the tail pulley helps improve the overall efficiency and lifespan of the conveyor system.
How Snub Pulley Supports Tail Pulley Functions
The snub pulley plays a complementary role to the tail pulley, enhancing its functions and contributing to the optimal performance of the conveyor system. The interaction between the snub pulley and the tail pulley is essential for several reasons:
Enhanced Belt Traction: The snub pulley increases the wrap angle of the conveyor belt around the tail pulley. This increased wrap angle enhances the friction between the belt and the pulley, providing better traction and reducing the risk of slippage. Improved traction ensures that the belt remains in contact with the tail pulley, maintaining consistent tension and preventing operational disruptions.
Improved Belt Alignment: The snub pulley helps maintain proper belt alignment by guiding the belt as it transitions from the tail pulley to the return side of the conveyor. This guidance is essential for preventing misalignment, which can cause uneven wear, increased maintenance, and potential system failures. By keeping the belt centered and aligned, the snub pulley ensures smooth and efficient operation.
Tension Distribution: Both the tail pulley and the snub pulley contribute to effective tension distribution across the conveyor belt. The tail pulley provides the primary tensioning, while the snub pulley ensures even distribution by increasing the belt’s wrap angle. This combined action prevents localized stress points and reduces the likelihood of belt damage, extending the belt’s lifespan and reducing maintenance costs.
Minimized Belt Wear: The interaction between the tail pulley and the snub pulley helps minimize belt wear by providing smooth transitions and optimal tension management. The snub pulley reduces stress on the belt during direction changes, while the tail pulley ensures proper support and stability. This synergy reduces the overall wear and tear on the belt, leading to longer belt life and lower maintenance costs.
Operational Efficiency: The combined use of tail and snub pulleys contributes to the overall operational efficiency of conveyor systems. By providing precise tensioning, enhanced traction, and improved alignment, these pulleys ensure that the conveyor belt operates smoothly and reliably. This efficiency translates to increased productivity, reduced downtime, and lower operational costs, making the interaction between the tail and snub pulleys a critical aspect of conveyor system design and operation.
Versatility in Applications: The versatility of tail and snub pulleys allows them to be used in a wide range of conveyor applications. Whether in mining, manufacturing, logistics, or food processing, these pulleys can be adapted to meet the specific needs of different industries. Their ability to handle various belt types, load capacities, and operational conditions makes them indispensable components in modern conveyor systems.
Installation and Maintenance Considerations: Proper installation and maintenance of tail and snub pulleys are essential for ensuring their optimal performance. During installation, it is important to position the pulleys correctly to achieve the desired belt tension and alignment. Regular inspections and maintenance are necessary to check for signs of wear, misalignment, or tension issues. Timely replacement of worn or damaged pulleys helps prevent potential system failures and ensures continuous, efficient operation.
The Keys of Snub Pulley
Specific Functions and Placement in Conveyor Systems
In conveyor systems, snub pulleys play a crucial role in enhancing the efficiency and reliability of material handling operations. By increasing the wrap angle of the belt around the drive pulley, snub pulleys improve traction and reduce slippage, ensuring smooth and efficient belt movement. This section explores the specific functions and optimal placement of snub pulleys in conveyor systems.
Functions of Snub Pulley
1. Increasing Wrap Angle:
The primary function of a snub pulley is to increase the wrap angle of the conveyor belt around the drive pulley. By doing so, it enhances the contact between the belt and the pulley, improving traction and reducing the likelihood of slippage. This increased contact ensures that the drive pulley can efficiently transfer the driving force to the belt, enabling smooth and continuous movement.
2. Enhancing Belt Tension:
Snub pulleys help maintain proper belt tension, which is crucial for the effective operation of the conveyor system. By positioning the snub pulley strategically, operators can ensure that the belt remains taut, preventing sagging and reducing the risk of belt misalignment. Proper tension also minimizes wear and tear on the belt and other conveyor components, extending their lifespan and reducing maintenance costs.
3. Improving Belt Tracking:
Belt tracking refers to the alignment of the conveyor belt as it moves along the pulleys. Misalignment can cause the belt to run off track, leading to spillage, damage, and increased maintenance costs. Snub pulleys play a crucial role in guiding the belt and keeping it centered on the pulleys. By adjusting the position and angle of the snub pulley, operators can fine-tune the belt tracking, ensuring optimal alignment and reducing the risk of operational disruptions.
4. Reducing Belt Slippage:
Slippage occurs when the conveyor belt loses traction with the drive pulley, leading to inefficient material handling and increased wear on the belt. The snub pulley enhances the grip of the belt on the drive pulley by increasing the wrap angle, thereby reducing slippage. This improved traction ensures that the conveyor system operates efficiently, with minimal downtime and maintenance requirements.
5. Supporting Load Distribution:
The snub pulley helps distribute the load more evenly across the conveyor belt, reducing the strain on specific sections and preventing localized wear. This balanced load distribution enhances the overall durability and performance of the conveyor system, ensuring consistent material handling and minimizing the risk of belt failure.
Placement of Snub Pulley
The optimal placement of snub pulleys in a conveyor system depends on various factors, including the type of conveyor, the material being transported, and the specific operational requirements. Generally, snub pulleys are positioned near the drive pulley and tail pulley to maximize their effectiveness.
1. Near the Drive Pulley:
Placing a snub pulley near the drive pulley increases the wrap angle of the belt around the drive pulley, enhancing traction and reducing slippage. This placement is particularly beneficial in systems where high torque is required to move heavy loads or where the drive pulley needs additional support to maintain efficient operation.
2. Near the Tail Pulley:
A snub pulley placed near the tail pulley can help maintain proper belt tension and alignment. By increasing the wrap angle of the belt around the tail pulley, the snub pulley ensures that the belt remains taut and centered, preventing sagging and misalignment. This placement is especially useful in long conveyor systems where maintaining consistent belt tension is challenging.
3. Intermediate Positions:
In some conveyor systems, snub pulleys may be placed at intermediate positions along the conveyor to provide additional support and enhance belt tracking. These intermediate snub pulleys can help guide the belt through complex system layouts, ensuring smooth and efficient material handling.
Pressure Pulley vs. Snub Pulley
Understanding the Role of Pressure Pulley
A pressure pulley, also known as a tension pulley or take-up pulley, is used in conveyor systems to maintain consistent belt tension. Unlike snub pulleys, pressure pulleys do not increase the wrap angle of the belt around the drive or tail pulleys. Instead, they apply a constant force to the belt, ensuring that it remains taut and properly tensioned throughout its operation.
1. Function:
The primary function of a pressure pulley is to maintain the proper tension of the conveyor belt. This is achieved by applying a constant force to the belt, which compensates for any slack or elongation that occurs during operation. Proper tension is crucial for preventing belt slippage, ensuring smooth material transport, and reducing wear and tear on the belt and other conveyor components.
2. Placement:
Pressure pulleys are typically placed at the tail end or take-up section of the conveyor system. They are connected to a tensioning mechanism, such as a spring or hydraulic system, which provides the necessary force to maintain belt tension. In some cases, pressure pulleys may also be used in combination with other tensioning devices to achieve optimal belt tension.
Key Differences and Complementary Functions with Snub Pulley
While both pressure pulleys and snub pulleys are essential for the proper functioning of conveyor systems, they serve different purposes and have distinct characteristics. Understanding these differences and how they complement each other is crucial for optimizing conveyor performance.
Primary Function:
- Snub Pulley: The main function of the snub pulley is to increase the wrap angle of the conveyor belt around the drive and tail pulleys, enhancing traction, tension, and tracking. It supports the efficient transfer of driving force and minimizes slippage.
- Pressure Pulley: The primary function of the pressure pulley is to maintain consistent belt tension by applying a constant force to the belt. This ensures that the belt remains taut and properly tensioned throughout its operation, preventing slack and reducing wear.
Impact on Belt Tension and Tracking:
- Snub Pulley: By increasing the wrap angle, snub pulleys play a significant role in maintaining proper belt tension and improving belt tracking. They help ensure that the belt remains aligned and operates efficiently.
- Pressure Pulley: Pressure pulleys do not directly impact belt tracking or wrap angle. Instead, they maintain consistent belt tension, ensuring smooth material transport and reducing the risk of belt slippage.
Location in Conveyor System:
- Snub Pulley: Snub pulleys are typically located close to the drive pulley and tail pulley. They are strategically positioned to increase the wrap angle and improve belt traction.
- Pressure Pulley: Pressure pulleys are usually placed at the tail end or take-up section of the conveyor system. They are connected to a tensioning mechanism to maintain proper belt tension.
Complementary Functions:
- Synergy: Snub pulleys and pressure pulleys work together to ensure the efficient operation of conveyor systems. While the snub pulley enhances traction and tracking by increasing the wrap angle, the pressure pulley maintains consistent belt tension, preventing slack and ensuring smooth material transport.
- Optimization: By combining the functions of snub pulleys and pressure pulleys, conveyor systems can achieve optimal performance, with reduced maintenance costs, increased efficiency, and extended equipment lifespan.
Comparing Snub Pulley and Head Pulley
In conveyor systems, various pulleys play distinct and crucial roles to ensure efficient and reliable material transport. Among these, the snub pulley and the head pulley are essential components, each serving unique purposes. This section will explore the differences between the snub pulley and the head pulley and discuss their specific functions and placement within conveyor systems.
Differences Between Snub Pulley and Head Pulley
The snub pulley and the head pulley, while both integral to the operation of a conveyor system, differ significantly in their design, function, and placement.
Design and Construction:
- The snub pulley is typically smaller in diameter compared to the head pulley and is positioned close to the drive pulley. It is designed to increase the wrap angle of the conveyor belt around the drive pulley, enhancing friction and grip.
- The head pulley, on the other hand, is larger and usually located at the discharge end of the conveyor system. It is designed to drive the conveyor belt, facilitating the movement of materials along the conveyor path.
Functionality:
- The primary function of the bend pulley and snub pulley is to improve the belt’s traction on the drive pulley by increasing the belt’s contact surface area. This enhanced traction helps prevent slippage, ensuring efficient power transmission from the drive pulley to the conveyor belt.
- The head pulley serves as the main driving force behind the conveyor belt. It is powered by an electric motor and is responsible for pulling the belt along the conveyor path. The head pulley also assists in the discharge of materials from the conveyor belt, guiding them to their next destination.
Placement in the Conveyor System:
- The snub pulley is strategically placed on the return side of the conveyor belt, near the drive pulley. Its position allows it to redirect the belt, increasing the wrap angle and enhancing the grip between the belt and the drive pulley.
- The head pulley is located at the discharge end of the conveyor system, where the conveyor belt completes its travel and releases the transported materials. It is positioned to effectively drive the belt and facilitate the unloading process.
Specific Functions and Placement in Conveyor Systems
Understanding the specific functions and ideal placement of both the snub pulley and the head pulley is crucial for optimizing conveyor system performance.
Snub Pulley Functions:
- Enhancing Belt Traction: The snub pulley increases the wrap angle of the conveyor belt around the drive pulley. This additional wrap enhances the friction between the belt and the drive pulley, providing better traction and preventing slippage. Improved traction is vital for maintaining efficient power transmission and ensuring that the belt moves smoothly without interruptions.
- Tension Distribution: By increasing the wrap angle, the bend pulley helps distribute tension more evenly across the belt. This even distribution reduces localized stress points, minimizing wear and tear on the belt and extending its lifespan.
- Supporting Belt Alignment: The snub pulley aids in maintaining proper belt alignment by ensuring that the belt follows a precise path. Proper alignment is essential for preventing belt drift and reducing uneven wear, contributing to the overall reliability and efficiency of the conveyor system.
Head Pulley Functions:
- Driving the Conveyor Belt: The head pulley is the primary driving force behind the conveyor belt. Powered by an electric motor, it pulls the belt along the conveyor path, enabling the transport of materials from the loading point to the discharge end.
- Material Discharge: Positioned at the end of the conveyor system, the head pulley facilitates the discharge of materials. As the belt passes over the head pulley, materials are guided off the belt and into the next phase of processing or handling.
- Maintaining Belt Tension: The head pulley also plays a role in maintaining the overall tension of the conveyor belt. Proper tension is necessary to prevent slippage, ensure smooth operation, and reduce wear on both the belt and the pulley itself.
Placement in Conveyor Systems:
- The snub pulley is typically installed on the return side of the conveyor belt, near the drive pulley. This placement allows it to effectively increase the wrap angle and enhance traction. Its position can vary depending on the specific design and requirements of the conveyor system, but it is generally placed to maximize contact between the belt and the drive pulley.
- The head pulley is always located at the discharge end of the conveyor system. Its placement is critical for driving the belt and facilitating the discharge of materials. The head pulley is usually positioned to allow for easy access for maintenance and to ensure efficient unloading of transported materials.
Snub Pulley
Enhancing Belt Wrap with Snub Pulley
In conveyor systems, maintaining optimal belt tension and alignment is crucial for efficient operation. One critical component that plays a significant role in achieving this is the snub pulley. The snub pulley is designed to enhance the belt wrap around the drive pulley, thereby improving belt traction and reducing slippage. This section explores how the snub pulley increases the wrap angle on the drive pulley and the benefits of improved belt traction and reduced slippage.
How Snub Pulley Increases Wrap Angle on Drive Pulley
The primary function of a snub pulley is to increase the wrap angle of the conveyor belt around the drive pulley. The wrap angle refers to the portion of the drive pulley circumference that is in contact with the conveyor belt. By increasing this contact area, the snub pulley enhances the grip of the belt on the drive pulley, which is essential for efficient power transmission and belt movement.
Positioning of Snub Pulley:
The snub pulley is typically positioned close to the drive pulley, either before or after it, depending on the design and operational requirements of the conveyor system. By strategically placing the snub pulley, the conveyor belt is directed to wrap more around the drive pulley, increasing the contact surface area. This increased wrap angle improves the frictional grip between the belt and the drive pulley, reducing the likelihood of belt slippage.
Mechanics of Wrap Angle Enhancement:
When the conveyor belt passes over the snub pulley, it is redirected to create a larger arc of contact with the drive pulley. This redirection alters the belt’s pathway, ensuring that more of the belt’s surface area comes into contact with the drive pulley. The increased wrap angle means that the drive pulley can exert more force on the belt without causing slippage, as the frictional forces are distributed over a larger area. This enhanced contact allows for more efficient transmission of power from the drive motor to the conveyor belt.
Benefits of Improved Belt Traction and Reduced Slippage
The benefits of using a snub pulley to increase the wrap angle on the drive pulley are numerous, contributing to the overall efficiency and reliability of the conveyor system.
1. Enhanced Belt Traction:
Improved traction is one of the most significant benefits of increasing the wrap angle. With a larger contact area, the drive pulley can grip the belt more effectively, ensuring that the belt moves smoothly and consistently. Enhanced traction prevents the belt from slipping, which is crucial for maintaining a steady flow of materials on the conveyor. This consistency is particularly important in applications where precise material handling is required, such as in manufacturing or packaging processes.
2. Reduced Belt Slippage:
Belt slippage occurs when the frictional forces between the drive pulley and the conveyor belt are insufficient to move the belt, causing it to slip. Slippage can lead to several issues, including uneven material flow, increased wear on the belt and pulleys, and potential damage to the conveyor system. By increasing the wrap angle, the snub pulley significantly reduces the risk of slippage. The improved grip ensures that the belt moves synchronously with the drive pulley, maintaining consistent speed and direction.
3. Increased Conveyor Efficiency:
With enhanced traction and reduced slippage, the overall efficiency of the conveyor system is improved. The drive motor can transmit power more effectively to the belt, reducing energy losses and ensuring that the system operates at optimal performance levels. This increased efficiency can lead to lower operational costs, as the system requires less energy to achieve the same output. Additionally, a more efficient conveyor system can handle higher loads and operate at faster speeds, increasing productivity.
4. Extended Component Lifespan:
Reducing belt slippage also contributes to the longevity of the conveyor components. Slippage can cause excessive wear on the belt and pulleys, leading to premature failure and the need for frequent replacements. By enhancing the grip between the belt and the drive pulley, the snub pulley helps distribute the forces more evenly, reducing localized wear. This balanced distribution of forces extends the lifespan of the belt and pulleys, reducing maintenance costs and downtime.
5. Improved Material Handling:
Consistent belt movement is crucial for effective material handling. Uneven belt speed or direction changes caused by slippage can lead to material spillage, blockages, or uneven distribution of materials on the belt. By ensuring that the belt moves smoothly and predictably, the snub pulley improves the reliability of the conveyor system. This reliability is essential in industries where precise material handling is critical, such as food processing, pharmaceuticals, and automotive manufacturing.
6. Enhanced Safety:
A well-functioning conveyor system is also a safer system. Belt slippage and misalignment can create hazardous conditions, including the risk of material spillage, equipment damage, and even worker injuries. By improving belt traction and ensuring smooth operation, the snub pulley helps mitigate these risks, contributing to a safer working environment. Enhanced safety not only protects workers but also reduces the likelihood of costly accidents and downtime.
7. Flexibility in Conveyor Design:
The use of snub pulleys provides greater flexibility in conveyor system design. By adjusting the position and angle of the snub pulley, operators can fine-tune the wrap angle and tension of the conveyor belt. This flexibility allows for customization of the conveyor system to meet specific operational requirements and constraints. It also enables the system to adapt to changes in load conditions, material types, and other variables, ensuring consistent performance across a range of applications.
FAQS about Snub Pulley
A bent pulley, often referred to as a bend pulley, is used in conveyor systems to change the direction of the conveyor belt. Positioned at points where the conveyor path changes, bend pulleys are critical in redirecting the belt while maintaining proper tension and alignment. They are typically used in systems with multiple directional changes or in applications where space constraints require the conveyor to follow a specific path. Bend pulleys are designed to withstand the lateral forces exerted by the changing direction of the belt, ensuring smooth and continuous operation. By effectively guiding the belt through turns and bends, bend pulleys help in optimizing the layout and functionality of conveyor systems, making them essential components in complex material handling setups.
The head pulley and tail pulley serve distinct functions in a conveyor system. The head pulley is located at the discharge end of the conveyor and is responsible for driving the belt. It is connected to the drive motor and transmits the motion required to move the belt and the materials on it. The head pulley is typically larger in diameter to provide better traction and control over the belt’s movement. On the other hand, the tail pulley is situated at the loading end of the conveyor. Its primary function is to provide tension and alignment for the conveyor belt as it returns from the discharge end back to the loading point. Unlike the head pulley, the tail pulley is not powered but helps maintain the belt’s proper path and tension. Together, the head and tail pulleys ensure the smooth and efficient operation of the conveyor system.
The snub roller, much like the snub pulley, is designed to increase the belt’s wrap angle around a pulley, usually the drive pulley, to improve the friction and grip between the belt and the pulley. This additional contact surface helps in reducing slippage and ensures smoother transmission of power from the drive pulley to the conveyor belt. Snub rollers are placed on the return side of the conveyor belt near the head or drive pulley. They play a crucial role in maintaining belt tension and alignment, contributing to the overall efficiency and reliability of the conveyor system. By providing additional support and guidance to the belt, snub rollers help in minimizing wear and tear, thereby extending the lifespan of the conveyor belt and reducing maintenance costs.
A snub pulley is a component used in conveyor systems to increase the contact angle between the conveyor belt and the drive pulley, thereby improving the grip and tension of the belt on the drive pulley. Positioned close to the drive pulley, the snub pulley redirects the belt back onto the drive pulley, ensuring that it wraps around a larger portion of the drive pulley’s circumference. This increased contact helps prevent belt slippage, especially in high-tension applications. Snub pulleys are essential in enhancing the efficiency and reliability of conveyor systems by ensuring that the drive pulley can transmit the necessary force to move the belt and the materials being transported. They are typically made of durable materials like steel to withstand the constant friction and load.
Last Updated on June 11, 2024 by Jordan Smith
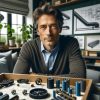
Jordan Smith, a seasoned professional with over 20 years of experience in the conveyor system industry. Jordan’s expertise lies in providing comprehensive solutions for conveyor rollers, belts, and accessories, catering to a wide range of industrial needs. From initial design and configuration to installation and meticulous troubleshooting, Jordan is adept at handling all aspects of conveyor system management. Whether you’re looking to upgrade your production line with efficient conveyor belts, require custom conveyor rollers for specific operations, or need expert advice on selecting the right conveyor accessories for your facility, Jordan is your reliable consultant. For any inquiries or assistance with conveyor system optimization, Jordan is available to share his wealth of knowledge and experience. Feel free to reach out at any time for professional guidance on all matters related to conveyor rollers, belts, and accessories.