Specialized Rubber Conveyor Belt Types for Unique Needs
Rubber conveyor belts are essential components in a wide range of industries, facilitating the efficient movement of materials. These belts are prized for their durability, flexibility, and ability to handle diverse operational demands. The different types of rubber conveyor belt cater to various applications, from mining and manufacturing to logistics and agriculture. Each type of rubber conveyor belt is designed to meet specific needs, ensuring optimal performance in distinct environments. Understanding the various rubber conveyor belt types and their unique applications is crucial for selecting the right belt for your industry’s requirements.
Types of Rubber Conveyor Belt Types
Understanding the different rubber conveyor belt types is essential for selecting the right belt to ensure efficient and effective material handling in various industrial applications. Below is an overview of six distinct types of rubber conveyor belts, along with insights into their construction and the materials used.
General Purpose Rubber Conveyor Belts
General purpose rubber conveyor belts are the most commonly used belts in various industries. These belts are designed for transporting materials with minimal abrasive properties. They are made from high-quality rubber compounds that offer excellent resistance to wear and tear. The construction typically includes a durable rubber cover on both sides of the belt, with a strong fabric or steel reinforcement in the middle to provide added strength and flexibility. General purpose belts are suitable for use in industries such as manufacturing, packaging, and logistics.
Heat-Resistant Rubber Conveyor Belts
Heat-resistant rubber conveyor belts are specifically designed to withstand high temperatures. These belts are constructed using heat-resistant materials and special rubber compounds that can endure temperatures up to 200°C (392°F) without degrading. The core of the belt is reinforced with heat-resistant fabrics or steel cords to maintain structural integrity under extreme heat conditions. Heat-resistant rubber conveyor belts are commonly used in industries such as cement manufacturing, steel production, and foundries, where materials are transported at elevated temperatures.
Oil-Resistant Rubber Conveyor Belts
Oil-resistant rubber conveyor belts are engineered to handle materials that contain oil or grease. The rubber compounds used in these belts are formulated to resist swelling, softening, or cracking when exposed to oils and fats. The belt construction includes a specialized oil-resistant cover and a robust fabric or steel reinforcement layer. These belts are ideal for applications in the food processing industry, recycling plants, and chemical manufacturing, where contact with oil and grease is frequent.
Flame-Resistant Rubber Conveyor Belts
Flame-resistant rubber conveyor belts are designed to reduce the risk of fire hazards in industries where combustible materials are transported. These belts are constructed using flame-retardant rubber compounds and materials that meet stringent safety standards. The inner structure typically includes a fire-resistant fabric or steel reinforcement layer to provide additional protection and strength. Flame-resistant rubber conveyor belts are essential in industries such as mining, underground transportation, and grain processing, where safety against fire is a critical concern.
Abrasion-Resistant Rubber Conveyor Belts
Abrasion-resistant rubber conveyor belts are built to handle the most demanding applications involving sharp, abrasive materials. These belts feature a thick, high-durability rubber cover that provides exceptional resistance to cuts, gouges, and wear. The inner construction includes heavy-duty fabric or steel reinforcement to ensure longevity and reliability under harsh conditions. Abrasion-resistant rubber conveyor belts are widely used in industries such as mining, quarrying, and construction, where materials like rocks, sand, and gravel are transported.
Cold-Resistant Rubber Conveyor Belts
Cold-resistant rubber conveyor belts are specially designed to perform effectively in low-temperature environments. These belts are made from rubber compounds that remain flexible and durable even at sub-zero temperatures. The belt construction includes cold-resistant fabric or steel cords for reinforcement, ensuring the belt maintains its structural integrity in freezing conditions. Cold-resistant rubber conveyor belts are suitable for applications in industries such as food storage, outdoor material handling, and arctic mining operations, where temperatures can drop significantly.
Construction and Materials
The construction of rubber conveyor belts involves several key components that determine their performance and suitability for specific applications. The primary materials used in the construction include:
- Rubber Compounds: The type of rubber used in the belt cover is crucial for determining its resistance to heat, oil, flames, abrasion, and cold. High-quality synthetic and natural rubber compounds are selected based on the specific requirements of the belt type.
- Reinforcement Layers: Rubber conveyor belts are reinforced with layers of fabric or steel cords to enhance their strength and durability. Common reinforcement materials include polyester, nylon, and aramid fabrics, as well as steel cables.
- Cover Material: The outer cover of the belt provides protection against environmental factors and mechanical wear. Depending on the application, the cover material can be designed to resist heat, oil, flames, abrasion, or cold temperatures.
Understanding the different rubber conveyor belt types and their construction materials helps in selecting the right belt for specific industrial needs, ensuring optimal performance and longevity.
Rubber Conveyor Belt Specifications: Understanding Rubber Conveyor Belt Types
When selecting the appropriate rubber conveyor belt for a specific application, understanding the various specifications is crucial. These specifications help classify the different rubber conveyor belt types and ensure that the chosen belt meets the operational demands of the intended application.
Specifications of Rubber Conveyor Belt Types
Tensile Strength
Tensile strength refers to the maximum load a rubber conveyor belt can withstand before breaking. It is a critical specification that determines the belt’s ability to handle heavy loads. The tensile strength is usually measured in Newtons per millimeter (N/mm) or pounds per square inch (psi). High tensile strength is essential for belts used in heavy-duty applications such as mining and construction.
Belt Width
The width of the rubber conveyor belt is a fundamental specification that influences the volume of material the belt can transport. Belt widths typically range from 300 mm (12 inches) to 2400 mm (94 inches), depending on the application. Wider belts are used for high-capacity applications, while narrower belts are suitable for lighter loads and confined spaces.
Belt Thickness
Belt thickness affects the belt’s durability and load-carrying capacity. Thicker belts offer better resistance to wear and tear, making them suitable for abrasive materials. The thickness of rubber conveyor belts can vary from a few millimeters to over 25 mm (1 inch), depending on the type of belt and its intended use.
Ply Rating
The ply rating indicates the number of fabric layers (plies) within the belt. Each ply adds strength and durability to the belt. Common ply ratings range from 2-ply to 6-ply, with higher ply ratings indicating stronger belts. Belts with higher ply ratings are used in heavy-duty applications where additional strength is required.
Cover Grade
The cover grade refers to the type of rubber compound used for the outer layer of the belt. Different cover grades offer various levels of resistance to heat, oil, abrasion, and flame. For example, an abrasion-resistant cover grade is suitable for handling sharp and abrasive materials, while a heat-resistant cover grade is essential for high-temperature applications.
Operating Temperature Range
The operating temperature range specifies the minimum and maximum temperatures the rubber conveyor belt can withstand while maintaining its performance. Belts designed for extreme temperatures have specialized rubber compounds that prevent degradation and ensure longevity. Understanding the temperature range is crucial for applications in environments with significant temperature variations.
Elongation at Break
Elongation at break measures the belt’s ability to stretch under load before breaking. It is expressed as a percentage of the original length. A higher elongation at break indicates a more flexible belt, which is beneficial in applications requiring belt flexibility and shock absorption.
Flexibility
Flexibility is the belt’s ability to bend without cracking or losing integrity. Flexible rubber conveyor belts are necessary for applications involving curved or complex conveyor systems. The flexibility is influenced by the type of rubber compound and the reinforcement materials used in the belt construction.
Adhesion
Adhesion measures the bond strength between the rubber layers and the reinforcement materials. High adhesion values are essential to prevent delamination and ensure the belt remains intact under various operational conditions. Adhesion is particularly important for belts used in high-impact and heavy-load applications.
Weight
The weight of the rubber conveyor belt affects the ease of installation and the energy required for its operation. Lighter belts are easier to handle and require less power to operate, making them suitable for applications with lower load requirements. Conversely, heavier belts are used in demanding applications where durability and load capacity are paramount.
Importance of Matching Belt Specifications to Application Requirements
Selecting the appropriate types of rubber conveyor belt and matching their specifications to the application requirements is vital for several reasons:
- Optimal Performance: Ensuring the belt’s specifications align with the operational demands results in efficient material handling and prolonged belt life.
- Safety: Properly specified belts reduce the risk of failures, which can lead to accidents and safety hazards in the workplace.
- Cost Efficiency: Using the right belt specifications minimizes maintenance costs and downtime, leading to cost savings over time.
- Durability: Belts that meet the application requirements are more durable and resistant to wear and tear, reducing the frequency of replacements.
- Energy Efficiency: Matching the belt specifications to the application ensures that the conveyor system operates efficiently, consuming less energy and reducing operational costs.
- Material Compatibility: Specific belt specifications, such as cover grade and tensile strength, ensure compatibility with the materials being transported, preventing damage to both the belt and the materials.
- Environmental Conditions: Belts designed for specific environmental conditions, such as extreme temperatures or exposure to oils, ensure reliable performance and longevity.
- Compliance with Standards: Properly specified belts comply with industry standards and regulations, ensuring safe and legal operation.
- Load Capacity: Selecting a belt with the appropriate tensile strength and ply rating ensures it can handle the expected load without compromising performance.
- System Compatibility: Ensuring the belt fits the conveyor system’s design and requirements prevents operational issues and enhances the overall system efficiency.
Understanding and applying the correct specifications for different rubber conveyor belt types ensures optimal performance, safety, and cost efficiency in various industrial applications.
Common Types of Rubber Conveyor Belt Types
When selecting a conveyor belt for specific industrial applications, understanding the various rubber conveyor belt types is essential. This section provides an in-depth look at one of the common types: Cold Resistant Rubber Textile Conveyor Belts, focusing on their features, specifications, material construction, and key attributes.
Cold Resistant Rubber Textile Conveyor Belts
Cold resistant rubber textile conveyor belts are specifically designed for use in extremely cold environments where standard belts would become brittle and fail. These belts maintain their flexibility and durability in sub-zero temperatures, ensuring reliable performance in challenging conditions.
Product Offer: Overview of Features and Benefits
Cold resistant rubber conveyor belts offer several distinct features and benefits that make them suitable for low-temperature applications:
- Temperature Tolerance: These belts can operate efficiently in temperatures as low as -50°C (-58°F), making them ideal for arctic and refrigerated environments.
- Flexibility: Even at low temperatures, these belts remain flexible, preventing cracking and breaking, which is common in standard rubber belts exposed to extreme cold.
- Durability: The belts are designed to withstand the wear and tear of continuous use, providing a long service life even in harsh conditions.
- Reduced Downtime: By maintaining performance in low temperatures, these belts reduce the risk of unexpected failures and the associated downtime.
- Versatility: Cold resistant belts are suitable for various industries, including food processing, outdoor material handling, and cold storage.
Specifications: Details on Rubber Cover Grades for Cold Resistance
The rubber cover grades for cold resistant conveyor belts are formulated to provide maximum performance in low-temperature environments. Key specifications include:
- Cold Resistance: The cover grade is engineered to resist the effects of freezing temperatures, ensuring the belt remains pliable and effective.
- Abrasion Resistance: Despite being cold-resistant, the rubber compound is also designed to resist abrasion, extending the belt’s lifespan in abrasive conditions.
- Oil and Fat Resistance: Some cold resistant belts are also resistant to oils and fats, making them suitable for food processing and other industries where these substances are present.
- Flame Resistance: In certain applications, cold resistant belts are also required to have flame-resistant properties to meet safety standards.
- Thickness: The rubber cover thickness can range from 1.5 mm to 8 mm, depending on the application requirements and the desired balance between flexibility and durability.
Material Construction: Description of Carcass Materials Used
The carcass of cold resistant rubber textile conveyor belts is constructed using high-quality materials that enhance the belt’s overall performance:
- Textile Fabrics: The primary reinforcement layer in these belts consists of textile fabrics such as polyester, nylon, or aramid. These materials provide the necessary strength and flexibility to the belt.
- Layered Construction: The belts typically feature a multi-ply construction, with each ply contributing to the overall tensile strength and durability.
- Bonding Layers: Special bonding layers are used to ensure a strong adhesion between the rubber covers and the textile carcass, preventing delamination and maintaining belt integrity.
- Cold-Resistant Compounds: The rubber compounds used in the construction are specifically formulated to maintain their properties at low temperatures, ensuring the belt remains flexible and durable.
- Additional Reinforcements: In some cases, additional reinforcements such as steel cords may be used to enhance the belt’s load-bearing capacity and resistance to impact.
Key Features: Highlights of the Rubber Layers for Lower Temperature Resistance
The rubber layers in cold resistant conveyor belts are designed to provide optimal performance in low-temperature environments. Key features include:
- Enhanced Pliability: The rubber layers are formulated to remain pliable at low temperatures, preventing the belt from becoming brittle and cracking.
- Impact Resistance: The rubber compounds offer excellent impact resistance, protecting the belt from damage caused by heavy loads and sharp materials.
- Thermal Stability: These rubber layers maintain their stability and performance across a wide temperature range, ensuring consistent operation.
- Chemical Resistance: In addition to cold resistance, the rubber layers may also be resistant to chemicals, oils, and other substances commonly encountered in industrial applications.
- Extended Service Life: By resisting the detrimental effects of cold temperatures, these rubber layers contribute to an extended service life for the conveyor belt, reducing the frequency of replacements and maintenance.
Understanding the specifications, construction, and key features of cold resistant rubber textile conveyor belts helps in selecting the right rubber conveyor belt types for low-temperature applications. These belts provide the necessary durability, flexibility, and resistance required to operate efficiently in harsh, cold environments, ensuring continuous and reliable material handling.
Specialized Rubber Conveyor Belt Types
Specialized rubber conveyor belts are designed to meet unique operational needs across various industries. These belts cater to specific requirements such as eliminating static electricity, minimizing vibrations, enhancing strength, and more. Understanding the different rubber conveyor belt types and their specialized applications helps in selecting the right belt for specific operational challenges.
Anti-static Belts
Anti-static rubber conveyor belts are designed to eliminate the risk of static electricity, which can cause sparks and lead to fires or explosions in sensitive environments.
Features and Benefits:
- Static Dissipation: Made with conductive materials that dissipate static electricity, ensuring safe operation in explosive or flammable environments.
- Safety Compliance: Meet stringent safety standards for use in industries such as electronics manufacturing, chemical processing, and grain handling.
- Durability: Resistant to wear and tear, maintaining their anti-static properties over time.
Anti-vibration Belts
Anti-vibration rubber conveyor belts are engineered to minimize vibrations in conveyor systems, ensuring smoother operation and protecting sensitive materials.
Features and Benefits:
- Vibration Dampening: Incorporate materials that absorb and dampen vibrations, reducing noise and preventing damage to transported goods.
- Enhanced Stability: Provide a stable conveying surface, improving the accuracy and reliability of material handling.
- Long-lasting Performance: Maintain their anti-vibration properties even under continuous use, extending the lifespan of the conveyor system.
Armored Belts
Armored rubber conveyor belts feature steel inserts to prevent tears and damage from sharp objects, making them ideal for heavy-duty applications.
Features and Benefits:
- Steel Reinforcement: Embedded with steel cables or plates that protect the belt from cuts, tears, and punctures.
- High Strength: Capable of handling heavy loads and abrasive materials without compromising on durability.
- Versatility: Suitable for use in mining, recycling, and construction industries where materials with sharp edges are common.
Cable Belts
Cable belts are reinforced with cables to provide enhanced strength and support for long-distance material transportation.
Features and Benefits:
- Cable Reinforcement: Utilize steel or synthetic cables for increased tensile strength and reduced elongation.
- Long-distance Transport: Ideal for applications requiring the movement of materials over long distances, such as in mining and bulk material handling.
- Reduced Maintenance: Durable construction minimizes the need for frequent maintenance and repairs.
Endless Round Belts
Endless round rubber conveyor belts are single-piece belts designed for applications requiring stretching and flexibility.
Features and Benefits:
- Seamless Design: Manufactured as a continuous loop, eliminating the risk of joint failure.
- High Flexibility: Capable of stretching and bending to accommodate complex conveyor layouts.
- Smooth Operation: Provide a smooth and consistent conveying surface, reducing the risk of material jamming or slipping.
Fin Belts
Fin belts are equipped with fin-like protrusions that provide additional grip and support for specific applications.
Features and Benefits:
- Enhanced Grip: Fin-like protrusions improve the belt’s grip on materials, preventing slippage and ensuring accurate positioning.
- Specialized Applications: Ideal for applications requiring precise material handling, such as packaging, sorting, and assembly lines.
- Customizable Design: Fins can be tailored to specific requirements, enhancing the belt’s versatility.
Multi-speed Belts
Multi-speed rubber conveyor belts are suitable for applications that require variable speed operation, allowing for flexible material handling.
Features and Benefits:
- Variable Speed Compatibility: Designed to operate efficiently at different speeds, accommodating varying production demands.
- Consistent Performance: Maintain consistent conveying performance even when speed changes occur.
- Energy Efficiency: Optimized for energy-efficient operation, reducing power consumption and operational costs.
Twisted Belts
Twisted rubber conveyor belts are designed as replacements for endless round belts, providing flexibility and ease of installation.
Features and Benefits:
- Easy Installation: Can be easily installed without the need for extensive splicing or joining processes.
- High Flexibility: Offer the same flexibility and stretch as endless round belts, suitable for complex conveyor systems.
- Durable Construction: Built to withstand continuous use and maintain their integrity over time.
V-belts
V-belts are characterized by their v-shaped profile, providing a secure grip and efficient power transmission in conveyor systems.
Features and Benefits:
- Secure Grip: The v-shaped profile ensures a secure grip on pulleys, preventing slippage and maintaining efficient power transmission.
- High Efficiency: Designed for efficient power transfer, reducing energy loss and improving overall system performance.
- Versatile Applications: Suitable for a wide range of industrial applications, including automotive, manufacturing, and agricultural machinery.
Understanding these specialized rubber conveyor belt types allows for the selection of the most suitable belt for specific operational needs, ensuring optimal performance, safety, and efficiency in various industrial applications. Each type of belt offers unique features and benefits that address specific challenges, making them essential components in modern material handling systems.
FAQs about Rubber Conveyor Belt Types
Rubber belts are essential components in various industrial applications, each designed to fulfill specific operational needs. The main types include:
V-belts: Recognized for their trapezoidal cross-section, these belts are ideal for high-speed, high-torque drives on light or heavy industrial equipment.
Timing belts: These have teeth that fit into a matching toothed pulley, ensuring positive grip and exact alignment, crucial for timing and precision.
Flat belts: Used primarily for power transmission from one drive to another, these belts enjoy a simple construction and alignment versatility.
Conveyor belts: Specifically designed for transporting materials from one point to another, usually made from robust rubber materials to withstand various environmental factors.
Multi-rib belts: Similar to flat belts but with multiple V-shaped grooves which increase surface contact area, improving transmission efficiency.
Wrapped belts: These are cased in a protective wrap for extra durability and resilience against external elements.
Each type of belt is crafted to address specific mechanical requirements and operational stresses, making them indispensable in their respective fields.
Conveyor belts are generally made from rubber due to its durability, flexibility, and resistance to abrasion. The type of rubber used can vary depending on the application requirements:
Natural Rubber: Excellent for high tensile strength and resilience, used in mining or quarrying conveyor belts.
SBR (Styrene Butadiene Rubber): Commonly used for general-purpose belts because of its good wear resistance and low cost.
NBR (Nitrile Rubber): Preferred in applications involving oils, fats, and greases due to its excellent oil resistance.
EPDM (Ethylene Propylene Diene Monomer): Used in environments with high exposure to weather elements and temperatures due to its outstanding ozone, UV, and heat resistance.
Each rubber type provides unique characteristics that tailor a conveyor belt to specific environmental conditions and materials handled.
Belt conveyors are versatile systems used to transport a broad range of materials in industries. They include several types based on construction and application:
Flat Belt Conveyors: Most common, used for moving items between departments, assembly lines, etc.
Modular Belt Conveyors: Built with segments that can be easily replaced, suitable for sharp or irregular shaped products.
Cleated Belt Conveyors: Equipped with vertical cleats to prevent product slippage in inclined or vertical applications.
Curved Belt Conveyors: Can navigate corners and obstructions, maintaining continuous flow.
Incline/Decline Belt Conveyors: Ideal for moving products between different heights or levels.
Each type optimizes different aspects of material handling, from simple linear movement to complex layouts and product orientations.
The grading of conveyor belts, such as grade 1 and grade 2, often refers to the rubber’s resistance to wear and tear — important for determining the belt’s operational lifespan and efficacy:
Grade 1: Higher quality rubber with superior resistance to abrasion, making it suitable for more demanding conditions where the material conveyed causes significant wear.
Grade 2: Offers less abrasion resistance compared to Grade 1 and is typically used in applications where materials are not as harsh.
The choice between Grade 1 and Grade 2 will depend on the specific requirements of the application, including budget constraints and expected conveyor belt life under normal operating conditions.
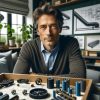
Jordan Smith, a seasoned professional with over 20 years of experience in the conveyor system industry. Jordan’s expertise lies in providing comprehensive solutions for conveyor rollers, belts, and accessories, catering to a wide range of industrial needs. From initial design and configuration to installation and meticulous troubleshooting, Jordan is adept at handling all aspects of conveyor system management. Whether you’re looking to upgrade your production line with efficient conveyor belts, require custom conveyor rollers for specific operations, or need expert advice on selecting the right conveyor accessories for your facility, Jordan is your reliable consultant. For any inquiries or assistance with conveyor system optimization, Jordan is available to share his wealth of knowledge and experience. Feel free to reach out at any time for professional guidance on all matters related to conveyor rollers, belts, and accessories.