High-Quality Plain Flat Rubber Conveyor Belt for Sale
A plain flat rubber conveyor belt is a versatile and durable conveyor solution used across various industries. It consists of a smooth, flat rubber surface that transports materials efficiently. Commonly used in manufacturing, logistics, and agriculture, plain flat rubber conveyor belts handle light to medium loads, including boxes, packages, and bulk materials. Their simplicity and ease of maintenance make them an ideal choice for facilities requiring reliable material handling solutions.
Plain Flat Rubber Conveyor Belt Price
Understanding the factors that influence the pricing of a plain flat rubber conveyor belt is crucial for businesses looking to optimize their material handling systems while managing costs effectively. The price of these conveyor belts can vary significantly based on several key elements, including material quality, belt dimensions, manufacturing processes, market demand, and supplier factors. This section provides an in-depth analysis of these factors to help you make informed purchasing decisions.
Material Quality
The type and quality of materials used in manufacturing a plain flat rubber conveyor belt are primary determinants of its price. Here’s how different materials impact cost:
- Natural Rubber: Natural rubber is prized for its excellent flexibility, tensile strength, and resistance to wear and tear. However, natural rubber can be more expensive due to its reliance on agricultural production, which can be subject to price fluctuations based on supply and demand in the market.
- Synthetic Rubber: Synthetic rubbers, such as neoprene, nitrile, and EPDM, are engineered to provide specific properties like resistance to oil, chemicals, and extreme temperatures. These materials can be more costly to produce due to complex manufacturing processes but offer enhanced performance characteristics that justify their higher price.
- Blended Materials: Some conveyor belts use a blend of natural and synthetic rubbers to balance cost and performance. These belts can provide a middle ground, offering good durability and resistance properties at a moderate price point.
Belt Dimensions
The dimensions of a plain flat rubber conveyor belt, including its length, width, and thickness, directly influence its price:
- Length: Longer conveyor belts require more material and thus are more expensive. Custom lengths can also incur additional costs due to non-standard production runs.
- Width: The width of the belt affects both the amount of rubber used and the complexity of the manufacturing process. Wider belts are generally more expensive than narrower ones due to the increased material usage and potential for higher production costs.
- Thickness: Thicker conveyor belts provide greater durability and resistance to wear and tear, making them suitable for heavy-duty applications. However, they also use more material, which increases the cost. The specific thickness needed depends on the application and the type of materials being transported.
Manufacturing Processes
The techniques and technologies used in the manufacturing of plain flat rubber conveyor belts also play a significant role in their pricing:
- Vulcanization: Vulcanization is a chemical process that enhances the durability and elasticity of rubber. Conveyor belts that undergo vulcanization typically have a higher price due to the improved performance characteristics and longer lifespan they offer.
- Reinforcement Layers: The incorporation of reinforcement layers, such as fabric or steel cords, can significantly enhance the strength and durability of the conveyor belt. However, these additional layers add to the manufacturing complexity and material costs, resulting in a higher overall price.
- Surface Treatments: Special surface treatments or coatings can be applied to conveyor belts to improve their resistance to specific conditions, such as extreme temperatures, oils, or chemicals. These treatments increase the belt’s durability and suitability for particular applications but also raise the cost.
Market Demand and Supply
Market dynamics, including demand and supply, can cause fluctuations in the price of plain flat rubber conveyor belts:
- Economic Conditions: During periods of economic growth, the demand for industrial products, including conveyor belts, tends to rise, which can drive up prices. Conversely, during economic downturns, demand may decrease, leading to lower prices.
- Industry-Specific Demand: Certain industries may experience seasonal or cyclical demand changes, affecting the pricing of conveyor belts. For example, increased construction activity in warmer months can lead to higher demand for conveyor belts in the construction industry.
- Raw Material Availability: The availability and cost of raw materials, such as rubber and reinforcement fabrics, can influence the price of conveyor belts. Supply chain disruptions or shortages can lead to increased raw material costs, which are often passed on to the consumer.
Supplier Factors
The choice of supplier and their business practices can also impact the price of plain flat rubber conveyor belts:
- Brand and Reputation: Established brands with a reputation for quality and reliability may charge higher prices for their conveyor belts. However, these brands often provide added value through superior product performance and customer support.
- Geographic Location: The geographic location of the supplier can affect pricing due to differences in labor costs, regulatory environments, and shipping expenses. Local suppliers might offer lower prices due to reduced shipping costs, while international suppliers might provide competitive pricing due to lower production costs in their regions.
- Volume Discounts: Many suppliers offer discounts for bulk purchases, which can significantly reduce the unit price of conveyor belts. Businesses with large-scale operations can take advantage of these discounts to lower their overall procurement costs.
The price of a plain flat rubber conveyor belt is influenced by various factors, including the quality and type of materials used, the dimensions and thickness of the belt, the manufacturing processes involved, market demand and supply dynamics, and supplier-specific factors. By understanding these elements, businesses can make informed decisions when purchasing conveyor belts, ensuring they select the right product that offers the best balance of cost, performance, and durability for their specific needs. Whether opting for natural or synthetic rubber, considering reinforcement layers, or negotiating with suppliers for bulk discounts, each decision impacts the overall cost and effectiveness of the conveyor system.
Used Plain Flat Rubber Conveyor Belt
Advantages of Purchasing Used Plain Flat Rubber Conveyor Belts
Purchasing a used plain flat rubber conveyor belt offers several benefits, particularly for businesses looking to manage costs without compromising on operational efficiency. Here are some key advantages:
- Cost Savings: The most significant advantage of buying used conveyor belts is the cost savings. Used belts are often available at a fraction of the price of new ones. This can free up capital for other critical investments within the business.
- Environmental Benefits: Opting for used conveyor belts is an environmentally friendly choice. Reusing belts reduces waste and the demand for raw materials, contributing to more sustainable industrial practices.
- Immediate Availability: Used belts are typically available for immediate purchase and use, unlike new belts which might have lead times for manufacturing and delivery. This can be crucial for operations needing quick replacements to minimize downtime.
- Proven Performance: Used belts have been operationally tested, and their performance is known. This can provide some assurance of their reliability and suitability for specific tasks.
- Customization Potential: Often, used belts can be easily modified or cut to fit specific conveyor systems, providing a level of flexibility that can be advantageous for certain applications.
Tips for Assessing the Quality and Lifespan of Used Belts
When purchasing a used plain flat rubber conveyor belt, it’s essential to assess its quality and remaining lifespan to ensure it meets your operational needs. Here are some tips to guide you:
- Visual Inspection: Conduct a thorough visual inspection of the belt. Look for signs of wear such as cracks, fraying edges, or significant surface wear. Check both sides of the belt to ensure there are no hidden damages.
- Check for Consistent Thickness: Measure the belt thickness at multiple points. Consistent thickness indicates even wear and better remaining lifespan, while significant variations could signal potential weak points.
- Assess Flexibility: Bend the belt to check its flexibility. A good-quality belt should flex without cracking. If the belt feels brittle or shows signs of cracking when bent, it might be nearing the end of its useful life.
- Inspect the Splices: Splices are often the weakest points of a conveyor belt. Check the condition of any splices for wear or separation. Well-maintained splices indicate a belt that has been properly used and maintained.
- Test for Hardness: Use a durometer to measure the hardness of the rubber. A belt that is too hard or too soft compared to its original specifications might not perform optimally in your application.
- Request Usage History: If possible, obtain information about the belt’s previous use. Knowing the type of material it transported and the conditions it operated under can give insights into its remaining lifespan.
Where to Find Reliable Sources for Used Plain Flat Rubber Conveyor Belts
Finding reliable sources for used plain flat rubber conveyor belts is crucial to ensuring you get a product that meets your needs. Here are some recommended sources:
- Industrial Equipment Resellers: Many companies specialize in reselling industrial equipment, including used conveyor belts. These resellers often inspect and refurbish belts before selling them, providing some assurance of quality.
- Online Marketplaces: Websites like eBay, Alibaba, and specialized industrial equipment platforms often list used conveyor belts. These platforms allow you to compare different products and prices easily.
- Auctions and Liquidation Sales: Companies going out of business or undergoing restructuring often sell their equipment through auctions. Attending these sales can offer opportunities to purchase high-quality used belts at significantly reduced prices.
- Local Suppliers and Distributors: Contacting local suppliers and distributors can be beneficial. They might have used belts in stock or know of other businesses looking to sell used equipment.
- Networking with Industry Contacts: Leveraging industry contacts and networks can help locate used conveyor belts. Businesses often update their equipment and might be willing to sell their old belts directly.
- Recycling Centers: Some recycling centers focus on industrial materials and might have used conveyor belts available for resale. These centers aim to repurpose materials, offering an environmentally friendly option.
Detailed Explanation of Plain Flat Rubber Conveyor Belt and Its Applications
Rubber conveyor belting is a vital component in many industrial and commercial operations, providing an efficient means of transporting materials. Rubber belts are made from durable materials that can withstand the rigors of various industrial environments. They consist of multiple layers, including a rubber cover and a reinforcing fabric or steel cord layer that adds strength and flexibility.
Applications of Rubber Conveyor Belting
- Manufacturing: In manufacturing plants, rubber conveyor belts transport raw materials, components, and finished products between different stages of production. They are used in assembly lines, packaging stations, and shipping areas.
- Mining: The mining industry relies heavily on rubber conveyor belts to move large quantities of ore, coal, and other mined materials. These belts need to be exceptionally durable to handle the abrasive nature of the materials and the harsh working conditions.
- Agriculture: In agriculture, rubber conveyor belts are used to transport grains, seeds, and other agricultural products. They are also employed in processing plants to move produce through various stages of cleaning, sorting, and packaging.
- Food Processing: Rubber belts used in food processing must meet strict hygiene standards. They transport ingredients and finished food products through different processing stages, ensuring they reach the packaging stage without contamination.
- Logistics and Warehousing: Conveyor belts streamline the movement of goods within warehouses and distribution centers, making the process of sorting, storing, and shipping products more efficient.
- Recycling: The recycling industry uses rubber conveyor belts to move materials through sorting, shredding, and processing stages. These belts need to be tough to handle a variety of materials, including metals, plastics, and glass.
Key Features and Benefits of Using Rubber Conveyor Belting
Rubber conveyor belting offers several features and benefits that make it ideal for a wide range of applications:
- Durability: Rubber belts are known for their durability and ability to withstand heavy loads, high impact, and abrasive materials. This makes them suitable for demanding industrial environments.
- Flexibility: Rubber belts can bend and flex around pulleys and curves, allowing for more complex conveyor system designs. This flexibility helps in optimizing space and improving the efficiency of material handling.
- Resistance to Chemicals and Oils: Certain types of rubber, such as nitrile, are resistant to oils, chemicals, and other harsh substances. This resistance makes them ideal for industries like food processing and chemical manufacturing, where exposure to such materials is common.
- Temperature Resistance: Rubber conveyor belts can operate in a wide range of temperatures, from freezing conditions to high heat. This versatility allows them to be used in various environments, from cold storage facilities to hot foundries.
- Noise Reduction: Rubber belts operate more quietly compared to other types of conveyor belts, such as metal belts. This noise reduction can create a more pleasant working environment and reduce noise pollution.
- Customizability: Rubber belts can be customized in terms of thickness, width, length, and surface texture to meet specific operational needs. This customizability ensures that the belt performs optimally for the intended application.
- Cost-Effectiveness: Despite their durability and high performance, rubber conveyor belts are often cost-effective. They offer a good balance between initial investment and long-term operational costs due to their longevity and low maintenance requirements.
Rubber conveyor belting plays a crucial role in various industries by providing a reliable, durable, and efficient means of material transport. Understanding the applications, key features, and benefits of rubber conveyor belts can help businesses select the right type of belt for their specific needs, ensuring optimal performance and cost-effectiveness.
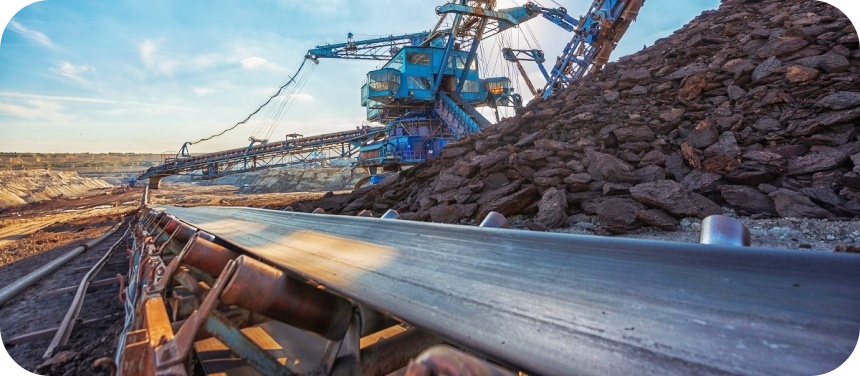
Plain Flat Rubber Conveyor Belt for Sale
Overview of the Market for New Plain Flat Rubber Conveyor Belts
The market for new plain flat rubber conveyor belts is diverse and robust, driven by the extensive applications of these belts across various industries such as manufacturing, logistics, agriculture, and mining. Plain flat rubber conveyor belts are essential components in material handling systems, providing efficient, reliable, and durable solutions for transporting a wide range of goods and materials. The demand for these belts continues to grow as industries expand and seek to optimize their operational efficiencies.
The market is segmented into several key areas based on the type of rubber used, the dimensions and specifications of the belts, and the specific applications they are designed for. Natural rubber and synthetic rubbers like neoprene, nitrile, and EPDM are commonly used, each offering distinct advantages in terms of flexibility, durability, and resistance to various environmental factors.
Manufacturers are constantly innovating to improve the performance and lifespan of plain flat rubber conveyor belts. This includes advancements in rubber compounds, the incorporation of reinforcing materials such as fabric or steel cords, and the development of specialized surface treatments that enhance resistance to abrasion, chemicals, and extreme temperatures.
Pricing in the market can vary widely depending on factors such as material quality, belt dimensions, and the presence of any additional features or customizations. While higher-end belts offer superior performance and durability, budget-friendly options are also available, catering to smaller businesses or less demanding applications.
Trusted Suppliers and Manufacturers Offering Plain Flat Rubber Conveyor Belts for Sale
Selecting a reliable supplier or manufacturer is crucial when purchasing a plain flat rubber conveyor belt. Here are some of the trusted names in the industry, known for their quality products and excellent customer service:
- Dunlop Conveyor Belting: Dunlop is a well-established name in the conveyor belt industry, offering a wide range of rubber belts tailored for different applications. Their belts are known for their durability, quality, and resistance to harsh working conditions.
- Continental AG: As one of the leading manufacturers in the world, Continental provides a comprehensive range of conveyor belts, including plain flat rubber options. Their belts are engineered for high performance and reliability, making them suitable for various industrial applications.
- Fenner Dunlop: Fenner Dunlop specializes in conveyor belting solutions that combine innovative technology with high-quality materials. They offer custom solutions to meet specific operational requirements, ensuring maximum efficiency and longevity.
- Bridgestone Corporation: Bridgestone is renowned for its high-quality rubber products, including conveyor belts. Their plain flat rubber conveyor belts are designed to withstand heavy loads and harsh environments, providing reliable performance over long periods.
- Goodyear Rubber Products, Inc.: Goodyear offers a diverse range of conveyor belts known for their robustness and versatility. Their belts are suitable for various applications, from light-duty to heavy-duty operations, ensuring optimal material handling solutions.
- Bando Chemical Industries, Ltd.: Bando is a global leader in conveyor belt manufacturing, providing innovative and high-performance belts for different industries. Their commitment to quality and customer satisfaction makes them a trusted supplier worldwide.
These manufacturers not only supply high-quality plain flat rubber conveyor belts but also offer comprehensive customer support, including technical advice, installation services, and maintenance tips. This ensures that customers receive the best possible solution for their specific needs.
Considerations When Buying a New Plain Flat Rubber Conveyor Belt
When purchasing a new plain flat rubber conveyor belt, several factors must be considered to ensure the belt meets your specific requirements and provides long-term value. Here are some key considerations:
- Material and Construction: Evaluate the type of rubber used in the belt. Natural rubber offers excellent flexibility and tensile strength, while synthetic rubbers like neoprene and nitrile provide specific resistance to oils, chemicals, and extreme temperatures. Additionally, consider the construction of the belt, including the number of ply layers and the type of reinforcement used.
- Dimensions and Specifications: Ensure the belt dimensions (length, width, and thickness) match your conveyor system’s requirements. The thickness of the belt should be appropriate for the load it will carry and the operational conditions it will face. Custom dimensions might be necessary for specialized applications.
- Load Capacity: Determine the load capacity of the belt, which should align with the weight and type of materials being transported. Overloading a belt can lead to premature wear and potential failure, so it’s crucial to select a belt with adequate strength and durability.
- Environmental Resistance: Consider the environmental conditions the belt will operate in. If the belt will be exposed to oils, chemicals, extreme temperatures, or abrasive materials, choose a belt with appropriate resistance properties to ensure longevity and performance.
- Surface Characteristics: Depending on the application, the surface texture of the belt might be important. Smooth surfaces are ideal for general-purpose use, while textured surfaces can provide additional grip for inclined conveying or handling slippery materials.
- Brand and Supplier Reputation: Purchase from reputable brands and suppliers known for their quality products and reliable customer service. Established manufacturers often offer warranties and support services that can provide peace of mind and ensure long-term satisfaction.
- Cost vs. Performance: While cost is an important factor, it should not be the sole consideration. A higher-priced belt may offer better performance, durability, and lower maintenance costs over its lifespan, providing better overall value.
- Installation and Maintenance: Consider the ease of installation and maintenance of the belt. Some belts come with features that simplify these processes, reducing downtime and associated costs. Additionally, ensure that you have access to necessary maintenance tools and support.
The market for plain flat rubber conveyor belt offers a wide range of options to meet various industrial needs. By understanding the factors that influence pricing, identifying trusted suppliers, and carefully considering the specific requirements of your application, you can select the best belt for your needs. Investing in a high-quality conveyor belt can enhance your operational efficiency, reduce downtime, and provide long-term cost savings, making it a critical component of your material handling system.
Plain Flat Rubber Conveyor Belt: Used Conveyor Belt Rubber for Sale
Benefits and Drawbacks of Buying Used Conveyor Belt Rubber
When considering the purchase of used conveyor belt rubber, it’s essential to weigh the benefits against the potential drawbacks to make an informed decision.
Benefits
- Cost Savings: One of the most significant advantages of buying used conveyor belt rubber is the cost savings. Used belts are often available at a fraction of the cost of new ones, making them an attractive option for businesses looking to minimize expenses.
- Environmental Impact: Purchasing used conveyor belts contributes to environmental sustainability by reducing waste. It gives the belts a second life and decreases the demand for new materials, thus lowering the overall environmental footprint.
- Immediate Availability: Used conveyor belts are typically readily available, allowing for quick acquisition and installation. This can be particularly beneficial for businesses that need to replace belts urgently without waiting for new ones to be manufactured and delivered.
- Tested Performance: Used belts have already been in operation, which can provide some assurance of their performance capabilities. You can often find belts that have been well-maintained and still have a considerable lifespan left.
Drawbacks
- Limited Lifespan: The primary drawback of used conveyor belts is their potentially reduced lifespan compared to new belts. They may already have significant wear and tear, which could lead to earlier failure and the need for more frequent replacements.
- Quality Variability: The quality of used belts can vary widely. Without proper inspection and assessment, you might end up with a belt that has hidden defects or is not suitable for your specific application.
- Lack of Warranty: Used belts often come with little to no warranty, meaning any repairs or replacements will need to be covered out of pocket. This can increase the overall cost of ownership if issues arise.
- Compatibility Issues: There might be challenges in finding used belts that perfectly match your conveyor system’s specifications, leading to potential compatibility issues that could affect performance.
How to Determine the Best Used Conveyor Belt Rubber for Your Needs
Selecting the best used conveyor belt rubber requires careful evaluation to ensure it meets your operational requirements and offers good value for money.
- Assess Your Needs: Determine the specific requirements of your application, including the type of materials to be transported, the load capacity, and the operating environment. This will help you identify the necessary properties of the belt, such as flexibility, abrasion resistance, and chemical resistance.
- Inspect the Belt Thoroughly: Conduct a detailed visual inspection of the belt for signs of wear and tear, such as cracks, fraying, and surface abrasions. Check both sides of the belt and pay particular attention to the edges and splices, as these are common points of failure.
- Measure Thickness and Uniformity: Use a micrometer to measure the thickness of the belt at various points. Consistent thickness indicates even wear and better durability. Significant variations in thickness could signal potential weak spots.
- Check for Flexibility: Bend the belt to test its flexibility. A high-quality belt should flex without cracking. Brittle or stiff belts may be near the end of their useful life and are more prone to breakage.
- Review the Usage History: If possible, obtain information about the belt’s previous usage, including the types of materials it transported and the conditions it operated under. This can provide valuable insights into its remaining lifespan and suitability for your application.
Best Practices for Purchasing Used Conveyor Belt Rubber to Ensure Quality and Reliability
Following best practices when purchasing used conveyor belt rubber can help ensure you acquire a quality product that meets your needs and offers good value.
- Buy from Reputable Sources: Purchase used conveyor belts from reputable suppliers who specialize in industrial equipment. These suppliers often inspect and refurbish belts before selling them, providing some assurance of quality.
- Request Detailed Information: Ask for detailed information about the belt, including its age, previous usage, and maintenance history. This information can help you assess the belt’s condition and expected lifespan.
- Test the Belt: If possible, conduct a performance test on the belt to ensure it operates correctly under load and meets your application requirements. This can help identify any hidden defects or issues that might not be apparent during a visual inspection.
- Seek Expert Advice: Consult with experts or engineers who have experience with conveyor systems and used belts. They can provide valuable insights and help you evaluate the belt’s suitability for your specific needs.
- Negotiate Warranty and Return Terms: While used belts often come with limited warranties, it’s worth negotiating terms with the supplier. Ensure there are clear return policies in place if the belt does not meet your expectations or fails prematurely.
- Consider Refurbished Options: Look for refurbished conveyor belts that have undergone maintenance or repairs to extend their lifespan. Refurbished belts can offer a good balance between cost savings and reliability.
By following these best practices, you can mitigate the risks associated with purchasing used conveyor belt rubber and ensure you select a product that provides reliable performance for your operations.
Plain Flat Rubber Conveyor Belt Material
Various Materials Used in the Manufacture of Rubber Conveyor Belts
Rubber conveyor belts are manufactured from a variety of materials, each chosen for its specific properties that make it suitable for different applications. Understanding these materials can help you select the best belt for your needs.
- Natural Rubber: Known for its excellent elasticity, tensile strength, and resistance to wear, natural rubber is commonly used in general-purpose conveyor belts. It performs well in environments where flexibility and durability are essential.
- Styrene-Butadiene Rubber (SBR): SBR is a synthetic rubber that offers good abrasion resistance and aging stability. It is widely used in industrial applications where the belt is exposed to harsh conditions, such as in mining and construction.
- Nitrile Rubber (NBR): NBR is resistant to oils, fats, and various chemicals, making it ideal for use in the food processing, chemical, and petrochemical industries. It maintains its properties in a wide range of temperatures and environments.
- Ethylene Propylene Diene Monomer (EPDM): EPDM rubber is known for its excellent resistance to heat, ozone, and weathering. It is used in applications where the belt needs to withstand high temperatures and harsh environmental conditions.
- Neoprene: Neoprene rubber offers good chemical stability and maintains its flexibility over a wide temperature range. It is used in conveyor belts that require resistance to oils, chemicals, and heat.
- Polyurethane (PU): PU belts are known for their high resistance to abrasion and their ability to handle sharp and heavy objects. They are commonly used in applications that involve handling abrasive materials.
How to Choose the Best Rubber Material for Your Specific Conveyor Belt Needs
Selecting the best rubber material for your conveyor belt involves evaluating the specific requirements of your application and the operating environment. Here are some key considerations:
- Load and Impact Resistance: Determine the weight and type of materials that the belt will transport. For heavy loads and high-impact applications, choose materials like natural rubber or polyurethane that offer high tensile strength and durability.
- Environmental Conditions: Consider the environmental conditions where the belt will operate. If the belt will be exposed to oils, chemicals, or extreme temperatures, select materials like nitrile rubber, neoprene, or EPDM that offer resistance to these conditions.
- Abrasion and Wear Resistance: For applications involving abrasive materials, choose a rubber material with high abrasion resistance, such as polyurethane or SBR. This will ensure the belt has a longer lifespan and requires less frequent replacement.
- Flexibility and Flex Cracking Resistance: If the belt needs to bend around pulleys and curves frequently, select a material with good flexibility and resistance to flex cracking. Natural rubber and neoprene are suitable choices for such applications.
- Chemical and Oil Resistance: In environments where the belt will come into contact with oils, fats, or chemicals, choose a material like nitrile rubber or neoprene that can withstand these substances without degrading.
- Temperature Resistance: For high-temperature applications, select a rubber material that can maintain its properties under heat, such as EPDM or neoprene. Conversely, for low-temperature environments, ensure the material remains flexible and does not become brittle.
- Cost Considerations: While high-performance materials may come at a higher cost, they can offer better durability and lower maintenance costs in the long run. Balance the initial investment with the total cost of ownership to make an informed decision.
By carefully evaluating these factors and understanding the properties of different rubber materials, you can select the best plain flat rubber conveyor belt material that meets your operational needs and ensures efficient, reliable performance.
Ready to enhance your operations with our Rubber Conveyor Belts? Submit your inquiry, and we’ll provide you with the best solutions.
FAQs about Plain Flat Rubber Conveyor Belt
Flat belt conveyors are a type of conveyor system that uses a continuous, flat belt to transport materials or products from one point to another. These belts are typically made of durable materials like rubber, PVC, or other synthetic compounds, and are supported by rollers or a flat pan along their length. Flat belt conveyors are widely used in various industries, including manufacturing, packaging, warehousing, and logistics, due to their versatility and efficiency. They are ideal for transporting light to medium-weight items such as boxes, packages, and components. The simplicity of their design makes them easy to maintain, and they can be customized to fit specific operational needs, including different belt materials, widths, and lengths.
Conveyor belts are made from various types of rubber, each chosen based on the specific requirements of the application. Common types include natural rubber, styrene-butadiene rubber (SBR), and nitrile rubber (NBR). Natural rubber is known for its excellent flexibility and tensile strength, making it suitable for general-purpose belts. SBR is favored for its good abrasion resistance and ability to withstand harsh conditions, making it ideal for transporting materials like gravel, sand, and coal. NBR is used in environments where resistance to oils, fats, and other hydrocarbons is essential, such as in the food processing or chemical industries. The choice of rubber type is critical to ensure the belt performs optimally under the operating conditions it will face.
Designing a flat belt conveyor involves several key steps to ensure it meets the specific needs of the application while operating efficiently and safely. First, determine the load characteristics, including weight, size, and shape of the materials to be transported. Next, choose the appropriate belt material and thickness based on the load and environmental conditions, such as temperature and exposure to chemicals. The conveyor’s length and speed must be calculated to match the required throughput. Select suitable drive components, including motors and gearboxes, to provide adequate power. Additionally, consider safety features like emergency stop buttons and guards. Ensure the design allows for easy maintenance and includes adjustable tensioning and tracking mechanisms to keep the belt aligned. Finally, consult with engineers or experienced conveyor designers to validate the design and ensure all factors are thoroughly addressed.
There are several types of conveyor belts, each designed for specific applications and operating environments. The most common types include:
Flat Belt Conveyors: These are the most widely used type, featuring a continuous flat belt that transports materials. They are suitable for light to medium loads and are commonly found in manufacturing, packaging, and distribution industries.
Modular Belt Conveyors: Made from interlocking plastic modules, these belts are highly durable and easy to clean. They are ideal for applications in the food and beverage industry, where hygiene is critical.
Cleated Belt Conveyors: These belts have raised sections (cleats) that help in transporting materials at inclines or preventing them from slipping. They are used in industries like agriculture and mining.
Incline/Decline Belt Conveyors: These are designed to move materials up or down a slope. They are used in various industries to move products between different levels of a facility.
Curved Belt Conveyors: These belts are used to navigate turns and curves within a facility, providing flexibility in layout and design.
Steel Belt Conveyors: Made of steel, these belts are used for heavy-duty applications and are resistant to high temperatures and harsh environments, making them ideal for industrial applications like metal stamping and recycling.
Each type of conveyor belt is engineered to meet the demands of specific applications, providing efficient and reliable material handling solutions across different industries.
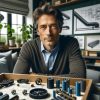
Jordan Smith, a seasoned professional with over 20 years of experience in the conveyor system industry. Jordan’s expertise lies in providing comprehensive solutions for conveyor rollers, belts, and accessories, catering to a wide range of industrial needs. From initial design and configuration to installation and meticulous troubleshooting, Jordan is adept at handling all aspects of conveyor system management. Whether you’re looking to upgrade your production line with efficient conveyor belts, require custom conveyor rollers for specific operations, or need expert advice on selecting the right conveyor accessories for your facility, Jordan is your reliable consultant. For any inquiries or assistance with conveyor system optimization, Jordan is available to share his wealth of knowledge and experience. Feel free to reach out at any time for professional guidance on all matters related to conveyor rollers, belts, and accessories.