Role of Ore Conveyor Belt in Underground Mining Operations
An ore conveyor belt is an essential component in mining operations, available in various sizes to suit different applications. The size of the ore conveyor belt is crucial as it determines the belt’s capacity to transport materials efficiently. Mining operations require belts that can handle large volumes of ore, with widths ranging from a few inches to several feet. The length of the conveyor belts can also vary significantly, from short belts used in confined spaces to extensive systems that cover long distances. Understanding the appropriate ore conveyor belt size ensures optimal performance and maximizes productivity in mining activities.
Leading Ore Conveyor Belt Manufacturers
Overview of Top Ore Conveyor Belt Manufacturers
Leading ore conveyor belt manufacturers are pivotal in providing high-quality, durable, and efficient belts essential for mining operations. These manufacturers focus on innovation, quality, and reliability, ensuring their products meet the rigorous demands of the mining industry. Below are some of the top ore conveyor belt manufacturers and their contributions to the market.
Manufacturer 1: Superior Industries
Superior Industries is a prominent name in the conveyor belt industry, known for its robust and innovative ore conveyor belts. Their belts are designed to withstand harsh mining environments, ensuring durability and long-lasting performance. Superior Industries offers a wide range of ore conveyor belts, catering to different sizes and specifications required by mining operations.
Products and Offerings:
- Customizable ore conveyor belt sizes
- High-strength materials for enhanced durability
- Advanced technology integration for improved efficiency
Market Presence:
Superior Industries has a strong global presence, with distribution networks ensuring the availability of their products in major mining regions.
Manufacturer 2: Fenner Dunlop
Fenner Dunlop is another leading manufacturer specializing in high-performance ore conveyor belts. Their belts are engineered to handle heavy loads and provide consistent performance under extreme conditions. Fenner Dunlop’s commitment to quality and innovation makes them a preferred choice for many mining companies.
Products and Offerings:
- Wide range of ore conveyor belt sizes
- Specialized belts for different mining applications
- Focus on safety and efficiency in design
Market Presence:
Fenner Dunlop’s extensive market presence and customer support services ensure that mining operations have access to reliable conveyor belt solutions.
Manufacturer 3: ContiTech
ContiTech, a subsidiary of Continental AG, is renowned for its advanced conveyor belt technologies. Their ore conveyor belts are designed for high performance and reliability, making them suitable for various mining applications. ContiTech’s emphasis on innovation and sustainability sets them apart in the industry.
Products and Offerings:
- Comprehensive range of ore conveyor belt sizes
- Eco-friendly materials and manufacturing processes
- Enhanced durability and resistance to wear
Market Presence:
ContiTech’s global reach and strong customer support infrastructure make them a leading choice for mining operations worldwide.
Manufacturer 4: Bridgestone
Bridgestone, a well-known name in the tire and rubber industry, also excels in manufacturing high-quality ore conveyor belts. Their belts are designed to offer superior performance and longevity, ensuring efficient material handling in mining operations.
Products and Offerings:
- Various ore conveyor belt sizes to meet different needs
- High resistance to abrasion and impact
- Innovative design features for improved efficiency
Market Presence:
Bridgestone’s extensive distribution network ensures the availability of their conveyor belts in key mining markets globally.
Manufacturer 5: Goodyear
Goodyear is another leading manufacturer providing robust and reliable ore conveyor belts. Known for their innovative approach, Goodyear’s belts are designed to enhance productivity and reduce downtime in mining operations.
Products and Offerings:
- Diverse range of ore conveyor belt sizes
- Focus on durability and long-lasting performance
- Custom solutions tailored to specific mining requirements
Market Presence:
Goodyear’s strong market presence and commitment to customer satisfaction make them a preferred supplier for many mining companies.
Leading ore conveyor belt manufacturers play a critical role in the mining industry by providing high-quality, efficient, and durable conveyor belts. Companies like Superior Industries, Fenner Dunlop, ContiTech, Bridgestone, and Goodyear are at the forefront of innovation, offering a wide range of products tailored to meet the specific needs of mining operations. By choosing the right manufacturer, mining companies can ensure optimal performance, enhanced productivity, and long-term reliability in their material handling processes.
Ore Conveyor Belt: Top Mining Conveyor Belt Manufacturers
The mining industry heavily relies on conveyor belts to transport materials such as ore, coal, and other minerals. Among these, the ore conveyor belt plays a crucial role in the efficient and effective movement of extracted materials from one location to another. The reliability and durability of these belts are paramount, given the harsh conditions and heavy loads they must endure. This section provides an overview of the leading manufacturers of ore conveyor belts and their significant contributions to the mining industry.
Leading Ore Conveyor Belt Manufacturers
- Continental AG
Continental AG, a German multinational company, is one of the world’s leading manufacturers of conveyor belts. With a history dating back to 1871, Continental has built a reputation for producing high-quality, durable belts that can withstand the rigorous demands of mining operations. The company offers a range of ore conveyor belts designed to handle heavy loads and resist wear and tear. Continental’s belts are known for their excellent resistance to abrasion, cutting, and gouging, making them ideal for transporting abrasive materials like ore.
- Fenner Dunlop
Fenner Dunlop, part of the Michelin Group, is another major player in the conveyor belt industry. With over 150 years of experience, Fenner Dunlop specializes in manufacturing belts that meet the specific needs of mining operations. Their ore conveyor belts are designed to provide maximum durability and performance, even in the harshest environments. Fenner Dunlop’s innovative solutions, such as their UsFlex and Fenaplast belts, offer exceptional resistance to impact and puncture, ensuring the safe and efficient transport of heavy ore.
- Bridgestone Corporation
Bridgestone Corporation, a Japanese multinational company, is renowned for its high-quality rubber products, including conveyor belts. Bridgestone’s ore conveyor belts are designed to deliver superior performance in mining applications. Their belts are known for their high tensile strength, excellent resistance to abrasion, and ability to handle heavy loads. Bridgestone’s focus on advanced materials and technology ensures that their belts can withstand the demanding conditions of mining operations.
- Goodyear Belting
Goodyear Belting, a subsidiary of Veyance Technologies, is a leading manufacturer of conveyor belts for the mining industry. Goodyear’s ore conveyor belts are designed to offer long-lasting performance and durability. Their belts are crafted from high-quality materials that provide excellent resistance to wear and tear. Goodyear Belting’s focus on innovation and customer satisfaction has made them a trusted name in the mining industry.
- Sempertrans
Sempertrans, a division of the Semperit Group, is a global leader in conveyor belt manufacturing. With a strong focus on research and development, Sempertrans produces high-performance ore conveyor belts that are tailored to the specific needs of mining operations. Their belts are designed to handle extreme loads and harsh conditions, providing excellent resistance to abrasion, impact, and other forms of wear. Sempertrans’ commitment to quality and innovation has earned them a reputation as a reliable supplier of conveyor belts for the mining industry.
- Phoenix Conveyor Belt Systems
Phoenix Conveyor Belt Kalyani Systems, a subsidiary of Continental AG, is known for its high-quality conveyor belts used in various industries, including mining. Phoenix’s ore conveyor belts are designed to meet the demanding requirements of mining operations. Their belts offer superior resistance to abrasion, cutting, and gouging, ensuring long-lasting performance. Phoenix’s focus on sustainability and innovation has led to the development of belts that are not only durable but also environmentally friendly.
Contributions to the Mining Industry
These leading manufacturers have made significant contributions to the mining industry by providing high-quality, reliable ore conveyor belts. Their innovations in materials, design, and technology have resulted in belts that offer enhanced performance, durability, and efficiency. These contributions include:
- Enhanced Durability: The use of advanced materials and innovative designs has led to the development of belts that can withstand the harsh conditions of mining operations. This includes resistance to abrasion, impact, and other forms of wear, ensuring long-lasting performance.
- Improved Efficiency: The development of belts that can handle heavier loads and operate at higher speeds has increased the efficiency of mining operations. This allows for the faster and more efficient transport of ore, reducing downtime and increasing productivity.
- Safety Innovations: Leading manufacturers have also focused on improving the safety of their belts. This includes the development of fire-resistant and anti-static belts, which help to reduce the risk of accidents and ensure the safety of workers.
- Sustainability: Many manufacturers are now focusing on sustainability, developing belts that are more environmentally friendly. This includes the use of recycled materials and the development of belts that require less energy to produce and operate.
- Customization: The ability to customize belts to meet the specific needs of mining operations has also been a significant contribution. This includes the development of belts with specific properties, such as high Conveyor Belt tensile strength, enhanced flexibility, and resistance to extreme temperatures.
By continually innovating and improving their products, these leading manufacturers have helped to drive the mining industry forward, ensuring that operations are more efficient, safe, and sustainable.
Ore Conveyor Belt: Finding Mining Conveyor Belt for Sale
Purchasing a mining conveyor belt, particularly an ore conveyor belt, involves careful consideration to ensure you select the best product for your needs. Finding the right supplier is crucial to getting a high-quality belt that meets the demands of your mining operations. This guide provides information on where to purchase mining conveyor belts, including authorized dealers and online stores, to help you make an informed decision.
Authorized Dealers
One of the best places to purchase an ore conveyor belt is through authorized dealers. Authorized dealers are certified by the manufacturers to sell their products, ensuring that you get genuine and high-quality belts. Here’s how to find authorized dealers:
- Manufacturer’s Website: Visit the websites of leading conveyor belt manufacturers like Continental AG, Fenner Dunlop, Bridgestone Corporation, and others. These websites often have a dealer locator tool that allows you to find authorized dealers in your region.
- Local Distributors: Many manufacturers have a network of local distributors who are knowledgeable about the products and can provide personalized service and support. Contacting a local distributor can help you get the conveyor belt you need quickly and efficiently.
- Industry Trade Shows: Attending industry trade shows and exhibitions can also be a great way to find authorized dealers. These events often feature booths and displays from manufacturers and their authorized dealers, allowing you to see the products in person and speak directly with representatives.
- Referral Networks: Reach out to industry peers and professional networks for recommendations on reputable dealers. Word-of-mouth referrals can often lead you to reliable sources for high-quality ore conveyor belts.
Online Stores
In addition to authorized dealers, online stores offer a convenient way to purchase mining conveyor belts. Online shopping provides the advantage of comparing different products and prices, as well as the convenience of having the product delivered to your location. Here are some options for buying conveyor belts online:
- Manufacturer’s Online Store: Many manufacturers have their own online stores where you can purchase conveyor belts directly. This ensures that you are getting a genuine product and can often provide access to exclusive deals and discounts.
- Industrial Supply Websites: Websites that specialize in industrial supplies often carry a range of conveyor belts. These sites typically offer a wide selection of products and competitive pricing. Examples of such websites include Grainger, MSC Industrial Supply, and Motion Industries.
- E-commerce Platforms: General e-commerce platforms like Amazon and eBay also carry industrial products, including mining conveyor belts. While these platforms offer convenience and a wide selection, it is important to verify the seller’s credibility to ensure that you are purchasing a genuine product.
- Specialty Online Retailers: Some online retailers specialize in conveyor belt components and accessories. These specialty retailers often have a deep knowledge of the products and can provide expert advice and support.
Tips for Purchasing an Ore Conveyor Belt
When purchasing an ore conveyor belt, consider the following tips to ensure that you make the best choice:
- Verify Authenticity: Ensure that you are purchasing from an authorized dealer or a reputable online store to avoid counterfeit products. Check for certifications and manufacturer endorsements.
- Check Reviews: Look for reviews and testimonials from other customers to gauge the quality and performance of the conveyor belt. Customer feedback can provide valuable insights into the product’s reliability and effectiveness.
- Compare Prices: Compare prices from different sources to ensure that you are getting a fair deal. While price is important, also consider the reputation of the seller and the quality of the product.
- Understand Warranty and Support: Check the warranty and support options available with the conveyor belt. Authorized dealers and reputable online stores often provide better warranty terms and customer support.
- Consult Experts: If you are unsure about which conveyor belt to purchase, consult with experts or the manufacturer’s customer service team. They can provide guidance based on your specific needs and application.
Finding the right ore conveyor belt for your mining operation involves careful consideration of various factors, including the quality of the belt, the reputation of the seller, and the specific needs of your application. By purchasing from authorized dealers or reputable online stores, you can ensure that you get a high-quality product that meets the demands of your mining operations. With the right conveyor belt, you can enhance the efficiency, safety, and productivity of your mining activities.
Ore Conveyor Belt: Role of Conveyor Belt in Underground Mining
The use of conveyor belts in underground mining operations has revolutionized the industry by enhancing efficiency, safety, and productivity. The ore conveyor belt, a critical component in these operations, facilitates the continuous transport of mined materials from the depths of the earth to the surface for further processing. This section will delve into the various roles and importance of ore conveyor belts in underground mining.
Efficient Material Transport
The primary role of an ore conveyor belt in underground mining is to transport materials efficiently. Unlike traditional methods that rely on trucks or rail systems, conveyor belts provide a continuous flow of ore, reducing the need for intermittent loading and unloading processes. This continuous transport system significantly enhances the efficiency of mining operations, allowing for the consistent movement of large volumes of material with minimal downtime.
Enhanced Safety
Safety is paramount in underground mining operations, and the use of ore conveyor belts plays a crucial role in mitigating risks associated with material transport. Conveyor belts reduce the need for heavy machinery and vehicles underground, which can be hazardous in confined spaces. By minimizing the movement of vehicles, the likelihood of accidents and collisions is significantly decreased. Moreover, conveyor belts can be equipped with advanced safety features such as emergency stop mechanisms, fire suppression systems, and automated monitoring, further enhancing the safety of mining personnel.
Cost-Effective Solution
Implementing an ore conveyor belt system in underground mining operations is a cost-effective solution compared to traditional material transport methods. Conveyor belts require less maintenance and operational costs than trucks or rail systems, which can be expensive to operate and maintain. The initial investment in conveyor belt infrastructure is offset by the long-term savings in fuel, labor, and maintenance costs. Additionally, conveyor belts can operate continuously, providing a more reliable and cost-efficient method for transporting ore.
Flexibility and Adaptability
Ore conveyor belts offer flexibility and adaptability in underground mining operations. They can be designed to navigate complex mine layouts, including inclines, declines, and curved paths. This adaptability allows conveyor belts to transport ore from remote and challenging areas of a mine, ensuring that all valuable materials are efficiently brought to the surface. Conveyor belts can also be easily extended or retracted as mining operations progress, providing a scalable solution that grows with the mine’s development.
Environmental Benefits
The use of ore conveyor belts in underground mining also has environmental benefits. Conveyor belts produce fewer emissions compared to diesel-powered trucks, reducing the overall carbon footprint of mining operations. Additionally, conveyor belts minimize dust and noise pollution, contributing to a safer and more environmentally friendly mining environment. By reducing the reliance on heavy machinery, conveyor belts help preserve the underground ecosystem and promote sustainable mining practices.
Improved Productivity
The continuous and reliable operation of ore conveyor belts directly contributes to improved productivity in underground mining. Conveyor belts can transport ore at high speeds, ensuring that mining operations can maintain a steady pace of material extraction and processing. This consistent flow of materials minimizes bottlenecks and delays, allowing mining companies to meet production targets and optimize their operations. The automation of conveyor belt systems also reduces the need for manual labor, freeing up personnel to focus on other critical tasks within the mine.
Integration with Advanced Technologies
Modern ore conveyor belts are equipped with advanced technologies that enhance their performance and efficiency. Automated control systems allow for real-time monitoring and adjustments, ensuring optimal operation and preventing potential issues before they escalate. Sensors and data analytics provide valuable insights into the condition of the conveyor belts, enabling predictive maintenance and reducing the risk of unexpected downtime. These technological advancements make ore conveyor belts an integral part of modern underground mining operations, driving innovation and continuous improvement.
Innovations by Ore Conveyor Belt Manufacturers
Ore conveyor belt manufacturers are continuously innovating to meet the evolving needs of the mining industry. These innovations focus on improving the durability, efficiency, and sustainability of conveyor belts, ensuring they can withstand the demanding conditions of underground mining. This section will explore the latest innovations and technologies introduced by ore conveyor belt manufacturers.
Advanced Materials
One of the key areas of innovation in ore conveyor belts is the development of advanced materials. Manufacturers are utilizing high-strength synthetic materials and reinforced polymers to create belts that are more durable and resistant to wear and tear. These materials offer superior tensile strength, abrasion resistance, and longevity, ensuring that conveyor belts can operate in harsh mining environments for extended periods without degradation. Additionally, the use of advanced materials reduces the overall weight of the conveyor belts, making them easier to install and maintain.
Energy-Efficient Designs
Energy efficiency is a major focus for ore conveyor belt manufacturers. Innovations in belt design and drive systems aim to reduce energy consumption and operational costs. For example, manufacturers are developing low-friction conveyor belts that require less power to operate, resulting in significant energy savings. Additionally, the use of variable frequency drives (VFDs) allows for precise control of conveyor belt speed, optimizing energy use based on the load and operational requirements. These energy-efficient designs contribute to more sustainable mining practices and lower operational costs.
Intelligent Monitoring Systems
The integration of intelligent monitoring systems is transforming the way ore conveyor belts are managed and maintained. These systems use sensors and data analytics to continuously monitor the condition of the conveyor belts, providing real-time insights into their performance. Predictive maintenance algorithms analyze data from the sensors to identify potential issues before they cause downtime, allowing for proactive maintenance and repairs. This technology not only enhances the reliability of conveyor belts but also extends their lifespan and reduces maintenance costs.
Modular and Customizable Solutions
Modularity and customization are key trends in the design of ore conveyor belts. Manufacturers are developing modular conveyor belt systems that can be easily configured and adapted to the specific needs of a mining operation. These modular designs allow for quick installation, expansion, and reconfiguration, providing mining companies with flexible and scalable solutions. Customizable conveyor belts can be tailored to meet the unique requirements of different mining applications, ensuring optimal performance and efficiency.
Sustainable and Eco-Friendly Solutions
Sustainability is a growing priority for the mining industry, and ore conveyor belt manufacturers are responding with eco-friendly solutions. Innovations in belt materials and manufacturing processes aim to reduce the environmental impact of conveyor belts. For example, some manufacturers are using recycled materials and eco-friendly adhesives in their products. Additionally, the development of energy-efficient and low-emission conveyor belt systems contributes to more sustainable mining operations. These eco-friendly innovations align with the industry’s commitment to reducing its carbon footprint and promoting environmental stewardship.
Enhanced Safety Features
Safety is a paramount concern in mining operations, and ore conveyor belt manufacturers are continuously improving safety features to protect workers and equipment. Innovations include fire-resistant conveyor belts, advanced emergency stop mechanisms, and automated safety monitoring systems. These features enhance the safety of mining operations by preventing accidents and minimizing the risk of fires and other hazards. Additionally, manufacturers are developing conveyor belts with improved ergonomic designs to reduce the physical strain on workers during installation and maintenance.
Future Trends and Developments
The future of ore conveyor belts is poised for further innovation and advancement. Emerging technologies such as artificial intelligence (AI), the Internet of Things (IoT), and blockchain are expected to play a significant role in the evolution of conveyor belt systems. AI and machine learning algorithms can optimize conveyor belt performance by predicting and adjusting to changing operational conditions. IoT connectivity enables seamless integration of conveyor belts with other mining equipment, creating a fully connected and automated mining ecosystem. Blockchain technology offers the potential for enhanced transparency and traceability in the supply chain, ensuring the authenticity and quality of conveyor belt materials.
By focusing on continuous innovation and leveraging advanced technologies, ore conveyor belt manufacturers are driving the mining industry towards greater efficiency, sustainability, and safety. These innovations ensure that conveyor belts remain a vital component of modern mining operations, capable of meeting the challenges of the future.
Maintaining Ore Conveyor Belt Size for Efficiency
Maintaining the correct size of ore conveyor belts is crucial for ensuring their optimal performance and longevity in mining operations. The size of the ore conveyor belt directly impacts its ability to transport materials efficiently and withstand the rigors of the mining environment. This section provides practical tips on maintaining the correct size of ore conveyor belts, covering aspects such as regular inspections, proper tensioning, and correct loading practices.
Importance of Correct Ore Conveyor Belt Size
- Efficiency: The right size of an ore conveyor belt ensures efficient material transport, minimizing spillage and maximizing throughput. A correctly sized belt can handle the required load capacity, reducing the likelihood of bottlenecks and delays in the mining process.
- Durability: Using the correct size of an ore conveyor belt helps prevent excessive wear and tear. An undersized belt may be overloaded, leading to premature wear, while an oversized belt may not operate efficiently. Proper sizing ensures the belt can withstand the operational demands without compromising its structural integrity.
- Safety: Ensuring the correct size of the ore conveyor belt enhances safety in mining operations. A properly sized belt reduces the risk of accidents caused by belt slippage, misalignment, or overloading. Maintaining the correct size helps keep the conveyor system stable and secure.
Regular Inspections and Monitoring
- Visual Inspections: Conduct regular visual inspections to check for signs of wear, damage, and misalignment. Look for uneven belt wear, cracks, and frayed edges that could indicate improper sizing or other issues.
- Tension Monitoring: Regularly monitor the tension of the ore conveyor belt to ensure it is within the manufacturer’s recommended range. Proper tensioning is crucial for maintaining the belt’s size and preventing slippage or excessive strain on the belt.
- Load Monitoring: Use load monitoring systems to track the amount of material being transported by the ore conveyor belt. Ensuring the belt is not overloaded helps maintain its size and prevents excessive wear and potential failure.
Proper Tensioning Practices
- Initial Tensioning: When installing a new ore conveyor belt, follow the manufacturer’s guidelines for initial tensioning. Proper initial tensioning ensures the belt is set up correctly and helps maintain its size and shape.
- Periodic Adjustments: Over time, conveyor belts may stretch or sag, affecting their size and tension. Periodically adjust the tension to compensate for any changes, ensuring the belt remains properly sized and tensioned.
- Automated Tensioning Systems: Consider using automated tensioning systems that continuously monitor and adjust the tension of the ore conveyor belt. These systems help maintain optimal tension and belt size, reducing the need for manual adjustments.
Correct Loading Practices
- Even Loading: Ensure that materials are loaded evenly onto the ore conveyor belt to prevent uneven wear and stress. Uneven loading can cause the belt to stretch or deform, affecting its size and performance.
- Proper Loading Points: Design loading points to minimize impact and distribute the load evenly across the belt. Use chutes and hoppers to control the flow of material onto the belt, reducing the risk of overloading and maintaining the belt’s size.
- Avoid Overloading: Adhere to the belt’s load capacity specifications to prevent overloading. Overloading can cause excessive strain and deformation, compromising the belt’s size and longevity.
Maintenance and Repairs
- Routine Maintenance: Implement a routine maintenance schedule to keep the ore conveyor belt in optimal condition. Regular maintenance helps identify and address issues that could affect the belt’s size and performance.
- Timely Repairs: Promptly repair any damage to the ore conveyor belt to prevent further deterioration. Use appropriate repair materials and techniques to maintain the belt’s size and structural integrity.
- Replacement of Worn Components: Regularly inspect and replace worn components such as rollers, pulleys, and idlers. Worn components can affect the belt’s size and alignment, leading to inefficient operation.
Training and Best Practices
- Employee Training: Train employees on best practices for maintaining the correct size of ore conveyor belts. Well-informed personnel can identify potential issues and perform routine maintenance effectively.
- Documentation: Keep detailed records of maintenance activities, including inspections, tension adjustments, and repairs. Documenting these activities helps track the condition of the ore conveyor belt and ensures proper maintenance practices are followed.
- Manufacturer Guidelines: Always follow the manufacturer’s guidelines for maintaining the ore conveyor belt. Manufacturer recommendations provide specific instructions for maintaining the correct belt size and ensuring optimal performance.
Technological Solutions
- Monitoring Systems: Utilize advanced monitoring systems that provide real-time data on the condition of the ore conveyor belt. These systems can detect changes in belt size and tension, allowing for timely adjustments and maintenance.
- Predictive Maintenance: Implement predictive maintenance strategies that use data analytics to anticipate potential issues with the ore conveyor belt. Predictive maintenance helps maintain the correct belt size by addressing problems before they lead to significant wear or damage.
- Smart Sensors: Install smart sensors along the conveyor system to monitor belt alignment, tension, and load. These sensors provide continuous feedback, ensuring the belt maintains its correct size and operates efficiently.
Environmental Considerations
- Temperature Control: Extreme temperatures can affect the size and performance of ore conveyor belts. Ensure the conveyor system operates within the recommended temperature range to maintain belt integrity.
- Humidity and Moisture: Excessive humidity and moisture can cause the belt to swell or shrink. Implement measures to control the environment and protect the belt from moisture-related issues.
- Dust and Debris: Regularly clean the conveyor system to remove dust and debris that can affect the belt’s size and performance. Accumulated debris can cause uneven wear and strain on the belt.
Maintaining the correct size of ore conveyor belt is essential for ensuring their efficiency, durability, and safety in mining operations. Regular inspections, proper tensioning, correct loading practices, and timely maintenance are crucial for keeping the belts in optimal condition. By following these practical tips and leveraging advanced technologies, mining companies can enhance the performance and longevity of their ore conveyor belts, contributing to more efficient and productive mining operations.
FAQs about Ore Conveyor Belt
A conveyor belt in mining is a continuous, automated system used to transport materials such as ore, coal, and overburden from one point to another. These belts are essential for efficient and cost-effective material handling in mining operations. Conveyor belts in mining are designed to withstand harsh conditions, including heavy loads, abrasive materials, and varying environmental conditions. They are often used in open-pit mines, underground mines, and processing plants to move extracted materials to different stages of the mining process, such as crushing, sorting, and loading for transport.
Mining operations utilize several types of conveyor belts, each tailored to specific requirements and conditions. The main types of belts used in mining include:
Steel Cord Belts: These belts are reinforced with steel cords, providing high tensile strength and durability. They are ideal for transporting heavy loads over long distances and are resistant to abrasion and impact.
Fabric Belts: Made from multiple layers of fabric, such as polyester or nylon, these belts offer flexibility and good resistance to abrasion. They are suitable for lighter loads and shorter distances.
Pipe Conveyor Belts: These belts form a closed pipe shape, protecting the material from external contaminants and preventing spillage. They are used in environmentally sensitive areas or where space is limited.
Chevron Belts: Featuring a chevron pattern on the surface, these belts provide extra grip, making them suitable for inclined or steeply sloped conveyor systems.
Heat Resistant Belts: Designed to handle high-temperature materials, these belts are used in applications such as transporting hot ash, clinker, or slag from mining operations.
Each type of belt is selected based on the specific needs of the mining operation, including the type of material being transported, the distance, and the environmental conditions.
A troughing belt is necessary for carrying ore because it helps to contain and center the material on the conveyor belt, reducing spillage and increasing efficiency. Troughing belts use idlers, which are sets of rollers arranged in a configuration that forms a trough shape. This design offers several advantages:
Material Containment: The trough shape helps to keep the ore centered on the belt, minimizing spillage and loss of material during transport.
Increased Capacity: The troughing design increases the carrying capacity of the conveyor belt, allowing it to transport larger volumes of ore efficiently.
Reduced Belt Wear: By keeping the material centered, troughing belts reduce uneven wear on the belt edges, extending the lifespan of the conveyor belt.
Improved Stability: The trough shape stabilizes the material load, preventing shifting and reducing the risk of belt misalignment or slippage.
These benefits make troughing belts essential for efficient and reliable material handling in mining operations, especially when transporting large quantities of ore over long distances.
Conveyor systems come in various types, each designed for specific applications and material handling needs. The three main types of conveyors are:
Belt Conveyor: This is the most common type of conveyor, consisting of a continuous belt that moves materials from one point to another. Belt conveyors are versatile and can handle a wide range of materials, from fine powders to large, heavy objects. They are used in various industries, including mining, manufacturing, and logistics.
Roller Conveyor: Roller conveyors use a series of rollers to move materials along a path. They can be powered or gravity-driven. Powered roller conveyors use motors to drive the rollers, while gravity roller conveyors rely on the force of gravity to move the materials. Roller conveyors are ideal for transporting items with a flat bottom, such as boxes and pallets.
Screw Conveyor: Also known as an auger conveyor, this type uses a helical screw blade to move materials. Screw conveyors are commonly used for handling bulk materials, such as grains, cement, and sludge. They are particularly effective for conveying semi-solid materials and can be used in both horizontal and inclined positions.
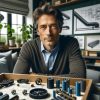
Jordan Smith, a seasoned professional with over 20 years of experience in the conveyor system industry. Jordan’s expertise lies in providing comprehensive solutions for conveyor rollers, belts, and accessories, catering to a wide range of industrial needs. From initial design and configuration to installation and meticulous troubleshooting, Jordan is adept at handling all aspects of conveyor system management. Whether you’re looking to upgrade your production line with efficient conveyor belts, require custom conveyor rollers for specific operations, or need expert advice on selecting the right conveyor accessories for your facility, Jordan is your reliable consultant. For any inquiries or assistance with conveyor system optimization, Jordan is available to share his wealth of knowledge and experience. Feel free to reach out at any time for professional guidance on all matters related to conveyor rollers, belts, and accessories.