High-Quality Materials in MOR Conveyor Belt Construction
A MOR conveyor belt, which stands for “Moderate Oil Resistance,” is a specialized type of conveyor belt designed to handle materials with moderate oil content. These belts are essential in industries where materials such as grains, wood chips, and certain minerals are processed, as they provide durability and resistance to oil-related degradation. The MOR conveyor belt is crafted from high-quality materials that ensure longevity and efficiency, even in challenging conditions. Its design minimizes maintenance requirements and downtime, making it a cost-effective solution for businesses aiming to maintain consistent and reliable operations in environments where moderate oil resistance is necessary.
Applications of MOR Conveyor Belt
The MOR conveyor belt, known for its superior oil and abrasion resistance, has become an essential component in various industrial applications. Its unique composition and characteristics make it suitable for a broad range of uses, particularly in industries where the transportation of materials can involve contact with oils or similar substances. Here, we explore the diverse MOR conveyor belt applications across different sectors.
Food Processing Industry
One of the primary MOR conveyor belt applications is in the food processing industry. These belts are ideal for transporting food items that may contain oils, such as meat, poultry, and baked goods. The oil-resistant properties ensure that the belt maintains its integrity and performance even when exposed to fats and oils. This reduces maintenance costs and extends the lifespan of the conveyor system, making it a cost-effective solution for food processing plants.
Chemical Industry
In the chemical industry, materials often contain oils or other lubricants that can degrade standard conveyor belts. The MOR conveyor belt’s resistance to these substances makes it an excellent choice for transporting chemicals and chemical products. Whether it’s raw materials, intermediates, or finished products, these belts can handle the challenges posed by oily substances without compromising on durability or efficiency.
Recycling Industry
Recycling facilities often deal with materials that have been contaminated with oils and other substances. The MOR conveyor belt is particularly useful in these settings, as it can withstand the harsh conditions and abrasive materials typically found in recycling operations. This durability ensures that the conveyor belts remain functional over longer periods, reducing the need for frequent replacements and downtime.
Automotive Industry
In the automotive industry, the manufacturing process involves the use of various oils and lubricants. The MOR conveyor belt is ideal for moving parts and components within this sector, as its oil-resistant properties prevent degradation caused by exposure to these substances. This application helps in maintaining a clean and efficient production line, contributing to overall productivity and cost savings.
Mining Industry
The mining industry presents one of the most challenging environments for conveyor belts. The presence of oil and abrasive materials demands a robust solution, and the MOR conveyor belt fits this requirement perfectly. Its durability and resistance to oil make it suitable for transporting minerals and other extracted materials, ensuring smooth operations and minimal downtime.
Timber Industry
In the timber industry, conveyor belts are used to transport logs, lumber, and other wood products. These materials can often be coated with oil or resin, making the MOR conveyor belt an ideal choice. Its resistance to these substances ensures that the belts remain functional and efficient, facilitating smooth operations and reducing the need for frequent maintenance.
Pharmaceuticals Industry
The pharmaceutical industry requires conveyor belts that can handle delicate materials often mixed with oils or lubricants. The MOR conveyor belt is perfect for this application, ensuring the safe and efficient transport of pharmaceutical products. Its oil-resistant properties help in maintaining the integrity of the conveyor system, ensuring that it meets the stringent standards of the industry.
Airports and Logistics
Airports and logistics centers rely on conveyor belts to handle a vast array of packages, many of which contain items that may leak oils or lubricants. The MOR conveyor belt is ideal for these settings, as it can handle the diverse range of materials and ensure that operations run smoothly without interruptions caused by belt degradation.
Agriculture
In the agricultural sector, conveyor belts are used to transport a variety of products, including grains, seeds, and other produce that can contain oils. The MOR conveyor belt is suitable for these applications, providing a durable and efficient solution that withstands the challenges posed by oil-containing materials.
Waste Management
Waste management facilities handle a wide range of materials, some of which can be oily or abrasive. The MOR conveyor belt is an excellent choice for these applications, offering resistance to oils and durability in harsh conditions. This ensures that the conveyor systems remain functional and efficient, reducing the need for frequent repairs or replacements.
Packaging Industry
In the packaging industry, conveyor belts are essential for moving products through various stages of the packaging process. Products often contain oils or lubricants, making the MOR conveyor belt a suitable choice. Its resistance to these substances ensures that the packaging process remains smooth and efficient, contributing to overall productivity and cost-effectiveness.
The MOR conveyor belt applications are vast and varied, spanning multiple industries that require a durable, oil-resistant solution for material handling. Its versatility and robustness make it an indispensable component in modern industrial operations, ensuring efficiency, longevity, and cost savings.
Key Features of MOR Conveyor Belt
Understanding the key features of the MOR conveyor belt is crucial for selecting the right belt for specific industrial applications. The MOR conveyor belt features a range of attributes that make it suitable for handling materials containing oils and other challenging substances. Here, we delve into the distinctive characteristics that set the MOR conveyor belt apart.
Oil Resistance
The most significant feature of the MOR conveyor belt is its resistance to oils. This characteristic is vital for industries where the belt is exposed to oils, fats, and lubricants. The oil-resistant compound used in the belt’s construction prevents it from swelling or deteriorating when in contact with these substances, ensuring a longer service life and consistent performance.
Abrasion Resistance
Another notable feature of the MOR conveyor belt is its abrasion resistance. The belt is designed to withstand the wear and tear that comes from transporting abrasive materials. This durability is crucial in industries like mining, recycling, and timber, where the belt is subjected to harsh conditions and rough materials.
Heat Resistance
Some applications involve high temperatures, and the MOR conveyor belt is equipped to handle these conditions. Its heat-resistant properties allow it to function efficiently in environments where temperatures can fluctuate significantly. This feature is particularly beneficial in industries such as food processing and chemicals, where heat is often a factor.
Flexibility
The MOR conveyor belt is designed to be flexible, enabling it to navigate complex conveyor systems with ease. This flexibility ensures that the belt can handle sharp turns and inclines without compromising its structural integrity or performance. It is an essential feature for industries with intricate conveyor setups.
High Tensile Strength
Tensile strength is a critical factor in conveyor belt performance, and the MOR conveyor belt boasts high tensile strength. This feature ensures that the belt can carry heavy loads without stretching or breaking, making it suitable for demanding applications in industries such as mining, automotive, and logistics.
Chemical Resistance
In addition to oil resistance, the MOR conveyor belt is also resistant to a variety of chemicals. This chemical resistance makes it suitable for use in environments where the belt may come into contact with corrosive substances, such as in the chemical and pharmaceutical industries.
Anti-Static Properties
Static electricity can be a concern in certain applications, and the MOR conveyor belt is designed with anti-static properties to mitigate this issue. This feature is particularly important in industries like electronics and packaging, where static discharge can damage products or pose safety risks.
Hygienic Design
For industries like food processing and pharmaceuticals, hygiene is paramount. The MOR conveyor belt is designed to meet stringent hygiene standards, with surfaces that are easy to clean and materials that do not harbor bacteria or other contaminants. This feature ensures that the belt contributes to a clean and safe production environment.
Customizability
The MOR conveyor belt can be customized to meet specific requirements of different industries. Whether it’s the size, thickness, or specific material composition, the belt can be tailored to ensure optimal performance for a particular application. This customizability makes it a versatile choice for a wide range of industrial needs.
Durability
Durability is a cornerstone of the MOR conveyor belt’s design. Its robust construction ensures that it can withstand the rigors of continuous use in demanding environments. This long-lasting durability reduces the frequency of belt replacements, resulting in lower operational costs and less downtime.
Smooth Surface
The smooth surface of the MOR conveyor belt facilitates the easy movement of materials. This feature is crucial for ensuring that products are transported efficiently and without damage. It also aids in the easy cleaning and maintenance of the belt, contributing to overall operational efficiency.
Energy Efficiency
The design of the MOR conveyor belt contributes to energy efficiency in conveyor systems. Its low friction surface and lightweight construction reduce the energy required to move materials, leading to cost savings and a smaller carbon footprint.
The MOR conveyor belt features a combination of oil resistance, abrasion resistance, heat resistance, flexibility, high tensile strength, chemical resistance, anti-static properties, hygienic design, customizability, durability, smooth surface, and energy efficiency. These features make it an excellent choice for a wide range of industrial applications, ensuring reliable and efficient material handling.
Benefits of Using MOR Conveyor Belt
Using the MOR conveyor belt in industrial applications offers numerous advantages that enhance operational efficiency, reduce costs, and improve overall productivity. Here, we explore the key MOR conveyor belt benefits that make it a preferred choice across various industries.
Extended Lifespan
One of the most significant benefits of the MOR conveyor belt is its extended lifespan. The belt’s resistance to oils, abrasion, and chemicals ensures that it remains functional and durable even in harsh conditions. This longevity reduces the need for frequent replacements, resulting in cost savings and less downtime for maintenance.
Cost-Effectiveness
The extended lifespan of the MOR conveyor belt translates directly into cost savings. Fewer replacements mean lower maintenance costs and less expenditure on new belts. Additionally, the belt’s durability ensures that it can handle high loads and challenging materials without frequent wear and tear, further enhancing its cost-effectiveness.
Enhanced Efficiency
The MOR conveyor belt is designed to provide smooth and efficient material handling. Its oil-resistant and abrasion-resistant properties ensure that it maintains optimal performance even when transporting challenging substances. This enhanced efficiency contributes to higher productivity and smoother operations in industrial settings.
Reduced Downtime
Frequent conveyor belt failures can lead to significant downtime, disrupting operations and reducing productivity. The MOR conveyor belt’s durability and resistance to oils and abrasives minimize the risk of unexpected breakdowns, ensuring continuous operation and reducing the impact of downtime on overall production.
Versatility
The versatility of the MOR conveyor belt is another major benefit. Its ability to handle a wide range of materials, including those containing oils and chemicals, makes it suitable for various industries. This adaptability means that businesses can use the same type of belt for different applications, simplifying inventory management and reducing the need for multiple belt types.
Improved Safety
Safety is a critical concern in industrial operations, and the MOR conveyor belt contributes to a safer working environment. Its anti-static properties reduce the risk of static discharge, which can be hazardous in certain settings. Additionally, its resistance to oils and chemicals ensures that the belt does not degrade or pose risks of contamination, enhancing overall safety.
Better Product Quality
Using the MOR conveyor belt can lead to better product quality. Its smooth surface and efficient material handling reduce the risk of product damage during transport. In industries like food processing and pharmaceuticals, where product integrity is paramount, the belt’s hygienic design and resistance to contamination ensure that products remain safe and of high quality.
Environmental Benefits
The energy efficiency of the MOR conveyor belt contributes to environmental sustainability. Its low friction surface and lightweight construction reduce the energy required for operation, leading to lower energy consumption and a smaller carbon footprint. Additionally, its long lifespan means fewer belts need to be produced and disposed of, reducing environmental impact.
Customizability
The MOR conveyor belt can be customized to meet specific industrial requirements, providing tailored solutions that enhance operational efficiency. Whether it’s adjusting the size, thickness, or material composition, customization ensures that the belt performs optimally in its intended application. This customizability is a significant benefit for industries with unique material handling needs.
Reliability
Reliability is a key benefit of the MOR conveyor belt. Its robust design and resistance to challenging conditions ensure that it performs consistently over time. This reliability is crucial for maintaining continuous operations and meeting production targets, especially in high-demand industries like mining, automotive, and logistics.
Easy Maintenance
Maintaining the MOR conveyor belt is straightforward due to its durable and resistant properties. The belt’s design minimizes the buildup of oils and other substances, making it easier to clean and maintain. This ease of maintenance reduces the time and effort required for upkeep, allowing for more focus on core operational activities.
Compliance with Standards
The MOR conveyor belt is designed to comply with industry standards, ensuring that it meets the necessary safety and performance criteria. This compliance is particularly important in regulated industries such as food processing, pharmaceuticals, and chemicals, where adherence to standards is essential for legal and safety reasons.
The MOR conveyor belt benefits include an extended lifespan, cost-effectiveness, enhanced efficiency, reduced downtime, versatility, improved safety, better product quality, environmental benefits, customizability, reliability, easy maintenance, and compliance with standards. These advantages make it an excellent choice for a wide range of industrial applications, contributing to smoother operations, cost savings, and overall productivity improvements.
Materials Used in MOR Conveyor Belt
Overview of MOR Conveyor Belt Materials
The MOR conveyor belt, which stands for Moderate Oil Resistance, is designed to endure environments where the conveyor belt will be exposed to substances containing moderate levels of oil. These environments often include industries such as recycling, wood processing, grain handling, and more. To effectively resist oil degradation, the MOR conveyor belt is constructed from specific materials that offer both durability and resistance to oil and other chemical contaminants.
Core Materials
- Rubber Compounds:
The primary material used in MOR conveyor belts is a specially formulated rubber compound. This rubber is engineered to provide moderate oil resistance, ensuring that the belt maintains its integrity and performance even when exposed to oily substances. The rubber compound typically includes additives and fillers that enhance its oil-resistant properties. - Fabric Layers:
Beneath the rubber surface, MOR conveyor belts often incorporate multiple layers of fabric. These fabrics are usually made from polyester, nylon, or a blend of both. The fabric layers provide the belt with additional strength and flexibility, allowing it to handle varying loads and stresses during operation. The type and quality of the fabric used can significantly impact the overall performance and durability of the belt. - Adhesives:
High-quality adhesives are used to bond the rubber and fabric layers together. These adhesives must also be resistant to oil and other chemicals to ensure a strong and lasting bond. The choice of adhesive is crucial, as it affects the belt’s ability to withstand the operational conditions without delaminating.
Special Additives and Coatings
- Oil-Resistant Additives:
To enhance the oil resistance of the rubber compound, various additives are included during the manufacturing process. These additives can include specific types of plasticizers, fillers, and stabilizers that help the rubber maintain its properties when exposed to oils and other chemicals. - Protective Coatings:
Some MOR conveyor belts are equipped with additional protective coatings on the surface. These coatings provide an extra layer of protection against oil and other contaminants, further extending the life of the belt. The coatings can be applied during the manufacturing process or as part of routine maintenance. - Heat and Abrasion Resistance:
In addition to oil resistance, MOR conveyor belts often need to withstand heat and abrasion. Materials and additives that provide these properties are included to ensure the belt performs well in a variety of challenging conditions.
Installation Process for MOR Conveyor Belt
Pre-Installation Preparation
- Site Inspection:
Before the installation of a MOR conveyor belt, a thorough site inspection is essential. This involves checking the conveyor system for any potential issues such as misalignment, worn-out components, or debris. Ensuring the conveyor structure is in good condition will help prevent problems during and after installation. - Measurement and Verification:
Accurate measurement of the conveyor system is critical. This includes verifying the dimensions of the conveyor frame, pulleys, and other components. Correct measurements ensure that the MOR conveyor belt fits properly and functions as intended. - Selection of the Right Belt:
Choosing the appropriate MOR conveyor belt for the specific application is crucial. Factors such as the type of material being transported, the operating environment, and the load capacity should be considered. Consulting with the belt manufacturer or supplier can help in selecting the right belt.
Installation Steps
- Preparation of Tools and Equipment:
Gather all necessary tools and equipment before starting the installation. This may include wrenches, clamps, alignment tools, and safety gear. Having everything ready will streamline the installation process and reduce downtime. - Removing the Old Belt:
If replacing an existing belt, carefully remove the old belt from the conveyor system. This may involve loosening tensioners, removing fasteners, and sliding the belt off the pulleys. Proper disposal of the old belt should be done in accordance with environmental regulations. - Positioning the New Belt:
Carefully position the new MOR conveyor belt on the conveyor frame. Ensure that the belt is aligned with the pulleys and other components. Proper alignment is crucial to prevent tracking issues and ensure smooth operation. - Joining the Belt Ends:
The ends of the MOR conveyor belt need to be joined together to form a continuous loop. This can be done using various methods such as mechanical fasteners, vulcanization, or adhesives. The chosen method should be compatible with the belt material and the operating conditions. - Tensioning the Belt:
Once the belt ends are joined, the next step is to properly tension the belt. Incorrect tension can lead to slippage, excessive wear, and reduced performance. Follow the manufacturer’s guidelines for tensioning to achieve the optimal balance between tension and flexibility. - Final Alignment and Testing:
After tensioning, check the alignment of the belt again. Run the conveyor system to test the belt’s performance. Observe for any tracking issues, unusual noises, or other problems. Make necessary adjustments to ensure smooth and efficient operation.
Post-Installation Checks
- Inspection and Adjustment:
Conduct a thorough inspection of the installed MOR conveyor belt. Check for proper alignment, tension, and any signs of damage or wear. Make any necessary adjustments to ensure optimal performance. - Lubrication and Maintenance:
Lubricate any moving parts of the conveyor system as needed. Establish a regular maintenance schedule to keep the system in good working condition. Proper maintenance will extend the life of the MOR conveyor belt and reduce downtime. - Training and Documentation:
Ensure that personnel operating the conveyor system are trained on proper usage and maintenance of the MOR conveyor belt. Keep documentation of the installation process, including any adjustments or modifications made. This information can be valuable for future reference and troubleshooting.
Maintenance Tips for MOR Conveyor Belt
Regular Inspections
- Visual Inspections:
Conduct regular visual inspections of the MOR conveyor belt to check for any signs of wear, damage, or misalignment. Look for cracks, cuts, or fraying on the belt surface, as well as any issues with the belt edges or splices. - Monitoring Belt Tension:
Proper belt tension is crucial for efficient operation. Regularly check the tension of the MOR conveyor belt and adjust it as needed. Over-tensioned or under-tensioned belts can lead to premature wear and reduced performance. - Checking Belt Tracking:
Ensure that the belt is running straight and true along the conveyor system. Misalignment can cause uneven wear and potential damage to the belt and conveyor components. Adjust the tracking as necessary to maintain proper alignment.
Cleaning and Lubrication
- Cleaning the Belt:
Regular cleaning of the MOR conveyor belt is essential to remove any buildup of oil, dirt, or debris. Use appropriate cleaning agents that do not damage the belt material. Keeping the belt clean will help maintain its oil-resistant properties and prevent slippage. - Lubricating Moving Parts:
Lubricate the moving parts of the conveyor system, such as bearings, pulleys, and rollers. Proper lubrication reduces friction and wear, ensuring smooth operation and extending the life of the MOR conveyor belt.
Preventive Maintenance
- Scheduled Maintenance:
Establish a preventive maintenance schedule for the MOR conveyor belt. This should include regular inspections, cleaning, lubrication, and any necessary adjustments. Following a maintenance schedule helps prevent unexpected breakdowns and extends the life of the belt. - Replacing Worn Components:
Monitor the condition of conveyor components such as pulleys, rollers, and bearings. Replace any worn or damaged parts promptly to prevent further damage to the MOR conveyor belt and ensure efficient operation. - Splicing and Repair:
If the MOR conveyor belt develops any damage, such as cuts or tears, address the issue promptly. Perform proper splicing and repair techniques to restore the belt’s integrity and prevent further damage.
Record Keeping
- Maintenance Logs:
Keep detailed records of all maintenance activities performed on the MOR conveyor belt. Include information such as inspection dates, findings, repairs made, and any adjustments. Maintenance logs provide valuable information for troubleshooting and future reference. - Performance Tracking:
Monitor the performance of the MOR conveyor belt over time. Track metrics such as belt wear, downtime, and maintenance costs. Analyzing performance data helps identify trends and areas for improvement, allowing for proactive maintenance and optimization.
Training and Safety
- Operator Training:
Ensure that all personnel operating and maintaining the conveyor system are properly trained on the correct procedures for working with MOR conveyor belts. Training should include safe operating practices, maintenance techniques, and emergency procedures. - Safety Precautions:
Emphasize the importance of safety when working with MOR conveyor belts. Implement safety measures such as emergency stop buttons, guards, and proper signage. Regularly review and update safety protocols to ensure a safe working environment.
Proper maintenance of the MOR conveyor belt is essential for maximizing its performance and longevity. By conducting regular inspections, cleaning, lubrication, and preventive maintenance, businesses can ensure that their conveyor systems operate efficiently and reliably. Keeping detailed maintenance logs and tracking performance metrics further aids in optimizing the maintenance process. Additionally, providing comprehensive training and emphasizing safety precautions help create a safe and productive work environment. Following these maintenance tips will help businesses get the most out of their MOR conveyor belts and minimize downtime, ultimately contributing to overall operational success.
FAQs about MOR Conveyor Belt
Conveyor belts come in various types, each suited for different applications and industries. The three primary types are flat belts, modular belts, and cleated belts. Flat belts are the most common and versatile, used in numerous industries for straightforward material handling tasks. They are typically made from durable materials like rubber or fabric composites. Modular belts are made from interlocking plastic pieces, offering flexibility and easy maintenance, often used in food processing and packaging industries. Cleated belts have raised sections (cleats) that help transport materials up steep inclines and prevent them from sliding backward, commonly used in agricultural and construction applications.
The term “M 24” refers to the grade of the conveyor belt, indicating its material composition and intended use. M 24 conveyor belts are made from high-quality, wear-resistant rubber that can withstand abrasive and heavy-duty applications. This grade is typically used in industries where the belt will be exposed to harsh conditions, such as mining, cement, and coal handling. The “M” stands for “mining,” and the “24” indicates the strength and durability level, ensuring that the belt can endure demanding operational environments while maintaining its integrity and performance.
The biggest conveyor belt in the world is the Boddington Bauxite Mine belt, located in Western Australia. This impressive conveyor system spans over 31 kilometers (approximately 19 miles) and plays a crucial role in transporting bauxite ore from the mine to the refinery. The belt’s extensive length and robust design enable it to handle the massive volume of ore required for processing, demonstrating the scale and efficiency of modern conveyor belt technology. The Boddington belt stands as a testament to engineering innovation, showcasing the ability to move large quantities of materials over long distances efficiently.
A belt roller, also known as a conveyor roller, is a cylindrical component used in conveyor systems to support and guide the belt. These rollers are essential for ensuring smooth and efficient operation, helping to reduce friction and wear on the belt. Belt rollers come in various sizes and materials, depending on the specific requirements of the conveyor system. They are strategically placed along the conveyor’s length to maintain proper tension and alignment of the belt. High-quality rollers are crucial for minimizing downtime and maintenance costs, ensuring the conveyor system operates effectively and reliably.
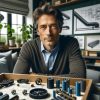
Jordan Smith, a seasoned professional with over 20 years of experience in the conveyor system industry. Jordan’s expertise lies in providing comprehensive solutions for conveyor rollers, belts, and accessories, catering to a wide range of industrial needs. From initial design and configuration to installation and meticulous troubleshooting, Jordan is adept at handling all aspects of conveyor system management. Whether you’re looking to upgrade your production line with efficient conveyor belts, require custom conveyor rollers for specific operations, or need expert advice on selecting the right conveyor accessories for your facility, Jordan is your reliable consultant. For any inquiries or assistance with conveyor system optimization, Jordan is available to share his wealth of knowledge and experience. Feel free to reach out at any time for professional guidance on all matters related to conveyor rollers, belts, and accessories.