Unveiling the Longest Conveyor Belt in South Africa
Conveyor belts play a pivotal role in the industrial sector by enhancing the efficiency of transportation and logistics within facilities. They are particularly indispensable in the mining industry, where they are used to move large volumes of materials across considerable distances. This brings us to the topic of the longest conveyor belt in South Africa, a remarkable example of engineering and industrial advancement. The Impumelelo conveyor belt project stands as one of the longest in South Africa. It significantly contributes to the mining sector by improving the transportation of coal from mines to power stations. This not only boosts production capacities but also underscores the critical role of such technologies in supporting the infrastructure and economy of the region.
Historical Development and Significance of the Longest Conveyor Belt in South Africa
Conveyor belts have been integral to the mining industry for over a century, evolving significantly with technological advancements. Initially used for simple tasks, these systems have grown in complexity and importance, mirroring the technological and industrial revolutions occurring globally. Here’s how conveyor belts have transformed the mining industry over time:
- Early Developments: The genesis of conveyor belts dates back to the late 19th century when they were first used in the grain industry. Their adaptation to the mining sector for coal and ore transportation marked the beginning of a transformative era in industrial operations.
- Introduction of Steel: The introduction of steel belts in the early 20th century revolutionized conveyor systems, allowing for longer distances and heavier loads, which was a boon for the burgeoning mining industry.
- Impact of World War II: The war effort required increased production of raw materials, propelling advancements in conveyor technology to meet the heightened demands.
- Technological Advancements: Post-war, the mining industry benefited from innovations such as synthetic belt materials that increased durability and reduced maintenance costs.
- Advent of Automation: The 1970s saw the mining conveyor systems begin to incorporate automation, significantly enhancing operational efficiency and safety.
- Safety Measures: Subsequent decades focused heavily on improving safety around conveyor belts, introducing emergency controls, automatic guards, and rigorous training protocols.
- Environmental Considerations: By the 1990s, environmental sustainability became crucial, leading to designs that minimized conveyor systems’ energy consumption and emissions.
- Long-distance Conveying: The development of long-distance conveyor belts helped reduce the need for truck transport, cutting operational costs and enhancing environmental sustainability.
- Current Trends: The contemporary focus is on digitalization and IoT to optimize maintenance and operations, ensuring high efficiency and safety standards.
South Africa’s Mining Industry
South Africa’s mining sector is a cornerstone of its economy, necessitating the most efficient and advanced conveyor systems available. The evolution of these systems in South Africa reflects both the global technological trends and the unique challenges of the country’s mining industry. Here’s a closer look:
- Rich Mining Heritage: South Africa’s mining history is deeply rooted, with significant mineral deposits driving the need for robust mining operations.
- Scale of Operations: The extensive mining activities require equally extensive conveyor systems that can handle large volumes efficiently.
- Advancements in Belt Technology: The harsh mining conditions in South Africa have led to the development of highly durable and efficient conveyor belts.
- Integration of Sophisticated Controls: Automation in conveyor systems allows for precise control over material handling, enhancing throughput and reducing waste.
- Energy Efficiency: Energy-efficient conveyor designs are critical in reducing operational costs and supporting sustainability initiatives.
- Safety Standards: High safety standards are crucial, and modern conveyor systems in South Africa are equipped with cutting-edge safety features.
- Economic Impact: Efficient conveyor systems are vital for maintaining profitability in the mining sector by lowering transportation costs.
- Environmental Initiatives: Contemporary conveyor designs also focus on reducing environmental impacts, such as dust emissions and energy usage.
- The Longest Conveyor Belt in South Africa: This prestigious title highlights not only the scale but also the sophistication of South Africa’s conveyor systems, particularly the Impumelelo project, which plays a critical role in the energy sector by ensuring coal delivery from mines to power stations.
These details underscore the significant reliance on and the innovative advancements in conveyor belt systems within South Africa’s mining industry.
The Impumelelo Conveyor Belt Project
The Impumelelo conveyor belt, known as the longest conveyor belt in South Africa, represents a significant engineering achievement in the region. This conveyor belt system was designed to enhance the transportation of coal directly from the Impumelelo mine to the SASOL Brandspruit coal-to-liquids processing plant, ensuring a consistent and reliable supply of coal necessary for energy production.
- Description of the Impumelelo Conveyor Belt: The Impumelelo conveyor belt is a state-of-the-art facility that incorporates advanced materials and technologies to withstand the harsh mining environment. It is built to carry large volumes of coal over long distances with minimal maintenance requirements. The belt itself is composed of a multi-layered rubber compound that provides durability and reduces wear and tear, which is crucial given the abrasive nature of coal.
- Location: This extensive conveyor system is situated near Secunda, in the northeastern part of South Africa. The region is known for its extensive coal reserves and is a critical area for South Africa’s energy sector. The strategic placement of the conveyor belt optimizes the transport process by significantly reducing the distance coal needs to travel from the mine to the processing plant.
- Length: Stretching approximately 26.8 kilometers (about 16.7 miles), this conveyor belt is not just the longest in South Africa but also one of the longest of its kind in the world. The length of the conveyor is a testament to the ambitious scale of the project and the significant investment in infrastructure that supports the mining and energy industries in South Africa.
- Connection: The primary purpose of the Impumelelo conveyor belt is to connect the Impumelelo coal mine directly to SASOL’s Brandspruit plant. This direct connection allows for continuous and efficient transport of coal, reducing the reliance on truck haulage, which is more costly and environmentally detrimental. By using this conveyor belt system, SASOL can ensure that its processing plant has a steady and reliable input of coal, which is essential for the production of synthetic fuels and other chemical products.
The Impumelelo conveyor belt project underscores the innovative approach to mining and material handling in South Africa. It highlights the country’s commitment to improving industrial efficiency and sustainability, which is crucial for maintaining its competitive edge in the global energy market.
Design and Engineering of the Longest Conveyor Belt in South Africa
The engineering prowess behind the longest conveyor belt in South Africa showcases a remarkable blend of durability, sophisticated design, and technological integration. This section delves into the technical specifications, outlining the crucial components and methodologies employed to optimize its performance and longevity. These specifications reflect a deep understanding of the operational challenges and environmental conditions specific to South Africa’s mining sector. Now, let’s explore the meticulous details and innovative features that define this monumental project.
Technical Specifications
The design and engineering of the longest conveyor belt in South Africa, the Impumelelo conveyor belt, showcase a blend of traditional mechanics and modern innovations. Here are some of the critical aspects:
- Width and Speed: The conveyor belt is designed with a width of approximately 1200 mm to accommodate a substantial amount of coal. It operates at a speed that allows the transport of thousands of tonnes per hour, optimizing coal delivery to the processing plant.
- Tensile Strength: High tensile strength materials are used to withstand the immense operational load. The belt can handle significant stress without elongation, ensuring operational integrity and reducing downtime.
- Belt Composition: Multiple layers of specially engineered rubber and reinforced fabric ensure durability against the abrasive nature of coal and the environmental elements of the South African landscape.
- Drive System: Multiple drive stations are installed along the conveyor’s length to maintain consistent belt tension and propulsion, which are critical for the efficiency and longevity of such a long conveyor system.
- Idlers: Engineered with high-grade steel and designed for high-load capacities, the idlers reduce the belt’s operational wear and enhance its lifespan.
- Pulleys: The conveyor uses specially designed pulleys that are wider and larger than standard sizes to support the belt’s weight and the load it carries. These pulleys are critical in maintaining the belt’s path and tension.
- Impact Beds: Strategically placed along the loading zones, impact beds absorb the shock and stress of loading coal onto the conveyor, protecting the belt from damage and reducing spillage.
- Advanced Design Technologies: Utilizing software like BeltStat for dynamic analysis and BeltFlex for stress simulation, engineers optimized the conveyor’s design to ensure maximum efficiency and safety under varying load conditions and environmental impacts.
Materials and Construction
The construction of the Impumelelo conveyor belt involved selecting materials that offer durability, efficiency, and environmental sustainability:
- Rubber Compounds: The belt is made from high-quality, abrasion-resistant rubber compounds that withstand the harsh mining conditions and the abrasive nature of coal.
- Reinforcing Materials: Layers of strong fabric and steel cords within the belt provide necessary tensile strength and resistance to tearing and stretching.
- Steel Structures: The framework of the conveyor system, including trusses and support beams, is constructed from steel, chosen for its strength and durability under significant loads.
- Weather-resistant Materials: Materials capable of withstanding South Africa’s varied climate conditions, from intense sun to heavy rains, are used to prevent environmental degradation and maintain structural integrity.
- Eco-friendly Technologies: Components of the conveyor system are selected based on their low environmental impact, such as energy-efficient motors and reduced-noise rollers, contributing to a smaller ecological footprint.
- Structural Adaptations: Considering the geographical undulations and environmental conditions, the conveyor’s route and structural supports were meticulously planned to ensure stability and adaptability across different terrains.
- Modular Design: Portions of the conveyor are designed modularly to facilitate easier maintenance and replacement, which is particularly crucial given the system’s length and the remote locations of some of its parts.
- Safety Features: Incorporation of advanced safety features, such as automatic shutdown sensors and emergency stop systems, protect the workforce and the system itself from unexpected failures or accidents.
These detailed technical specifications and careful material choices underline the complexity and innovative nature of the longest conveyor belt in South Africa, ensuring it meets the high demands of the mining industry while supporting sustainable operational practices.
Operational Efficiency of the Longest Conveyor Belt in South Africa
The operational efficiency of the longest conveyor belt in South Africa, integral to the logistics of the mining industry, emphasizes both throughput and sustainability. This section delves deeper into the performance metrics, examining not only the capacity and speed of the conveyor but also its uptime and reliability. Additionally, we explore comprehensive energy efficiency strategies that have been integrated into the system.
Performance Metrics
To gauge the performance of the longest conveyor belt in South Africa, several key metrics are considered:
- Capacity: The conveyor is engineered to transport up to 2,400 tonnes of coal per hour, making it a backbone of coal supply management for the SASOL Brandspruit plant.
- Speed: Operating at a calculated speed of 5 meters per second, the conveyor belt strikes an optimal balance between rapid material transport and minimizing wear on mechanical components.
- Uptime: High reliability is crucial for continuous operations. This conveyor system is designed for a high uptime percentage, with robust maintenance strategies in place to prevent prolonged downtimes.
- Reliability: Advanced monitoring systems are implemented to predict and prevent potential failures. These systems help maintain consistent operation and alert maintenance teams about necessary repairs before critical failures occur.
Energy Efficiency
In an era where energy conservation is paramount, the longest conveyor belt in South Africa incorporates several features to reduce energy consumption:
- Energy-Efficient Motors: The motors used in the conveyor system are selected for their high efficiency and capability to reduce electrical consumption, particularly during periods of variable load demands.
- Variable Speed Drives (VSDs): These devices adjust the speed of the conveyor belt based on the immediate processing needs, thereby conserving energy when full capacity is not required.
- Low Rolling Resistance Technology: Rollers designed with low rolling resistance reduce the energy required to move the conveyor, even under heavy loads, thus significantly lowering operational costs.
- Optimized Conveyor Path: The route of the conveyor is strategically designed to minimize elevational changes, reducing the energy required to lift the materials, which contributes further to energy efficiency.
These carefully considered design choices and technological implementations not only boost the performance of the conveyor belt but also underscore a commitment to environmental sustainability and operational cost reduction. By focusing on both performance metrics and energy efficiency, the longest conveyor belt in South Africa sets a standard for future industrial conveyor systems worldwide.
Economic Impact of the Longest Conveyor Belt in South Africa
The longest conveyor belt in South Africa, a key component in the mining sector, significantly impacts the economic landscape both locally and industry-wide. This section will explore its influence on the regional economy through job creation and broader economic benefits, as well as its implications for the mining industry in terms of enhanced operational capacities and global competitiveness.
Local Economy
The introduction and operation of the longest conveyor belt in South Africa have had profound effects on the local economy:
- Boost to the Regional Economy: The operation of the conveyor belt has significantly increased the efficiency of coal transportation, which in turn boosts the productivity of the mining and processing plants it serves. This efficiency enhancement translates into higher outputs and better economic returns, contributing to the economic stability of the regions involved.
- Job Creation: The construction and ongoing operation of this extensive conveyor system have created numerous job opportunities. Positions range from construction workers during the initial phase to engineers, technicians, and operational staff needed to maintain and run the conveyor system continuously.
- Economic Benefits for Local Communities: Beyond job creation, the conveyor belt project stimulates local economies by increasing demand for ancillary services such as accommodation, food services, and transportation. This kind of infrastructure project also often leads to improvements in local infrastructure, including roads and utilities.
- Sustainable Development Initiatives: Part of the economic impact includes investments in community development and environmental sustainability initiatives as part of corporate social responsibility. These programs aim to improve living conditions and education within local communities and ensure that economic benefits are somewhat long-lasting.
Industry Implications
On a broader scale, the longest conveyor belt in South Africa has implications for the mining industry that extend beyond the local context:
- Enhancements in Capacity and Operational Efficiency: This conveyor belt significantly increases the mining operation’s capacity and efficiency. By reducing the time and cost associated with transportation, it allows for a quicker turnaround in coal supply and helps manage market demand more effectively.
- Contribution to South Africa’s Position in the Global Mining Industry: The operational successes of such an advanced conveyor system not only bolster South Africa’s reputation as a leader in mining technology but also enhance its competitive edge in the global market. The efficiency and innovation demonstrated by projects like this conveyor belt attract foreign investment and set a benchmark for mining operations worldwide.
- Technological Leadership: The adoption of advanced technologies and practices through this conveyor belt project reflects and promotes South Africa’s capabilities in mining engineering and technology. This leadership can extend to other sectors, driving broader industrial growth and innovation.
- Global Market Dynamics: By optimizing the logistics of coal production, the conveyor belt directly affects global market dynamics for this commodity. It enables South Africa to maintain a reliable supply chain, which is crucial in the global energy markets, particularly in times of fluctuating fuel prices and market demands.
The economic impact of the longest conveyor belt in South Africa is thus multifaceted, influencing both the immediate regional economies and the broader industrial landscape, marking a significant stride in mining and industrial efficiency on a global scale.
Challenges and Solutions for the Longest Conveyor Belt in South Africa
Operating and maintaining the longest conveyor belt in South Africa comes with its set of challenges. This section examines the operational difficulties encountered during both the construction and operational phases of the conveyor belt, along with the solutions implemented to overcome them. It also explores the maintenance strategies crucial for ensuring the system’s longevity and efficiency.
Operational Challenges
The construction and operation of the longest conveyor belt in South Africa present unique challenges that require innovative solutions:
- Geographical and Environmental Challenges: The conveyor’s route through varying terrains and environmental conditions posed significant engineering challenges. Solutions included advanced geological surveys and the use of construction materials suited to different environmental conditions to ensure stability and durability.
- Technical and Mechanical Issues: Common issues such as belt alignment, wear and tear on rollers, and efficient power transmission needed addressing to avoid operational disruptions. Engineers implemented cutting-edge alignment technologies, wear-resistant materials for rollers, and energy-efficient motors.
- Logistical Hurdles: Coordinating the delivery and assembly of parts along the 26.8 kilometers of conveyor was daunting. This was managed through meticulous planning and staging, ensuring that parts and labor were available as needed throughout the construction phase.
- Regulatory and Safety Compliance: Meeting stringent safety and environmental regulations required comprehensive compliance strategies, including regular safety drills and the installation of numerous safety features along the conveyor.
Maintenance Strategies
Maintaining such an extensive system necessitates detailed and proactive maintenance strategies:
- Regular Inspection and Monitoring: Scheduled inspections are carried out to assess the integrity of the conveyor belt, with sensors installed along the length of the belt to provide real-time monitoring and data analysis.
- Preventative Maintenance Protocols: This involves routine checks and the replacement of parts before they fail. Such protocols help in avoiding unscheduled downtimes and prolong the life of the conveyor system.
- Use of High-Quality Replacement Parts: Parts from reliable suppliers like YB Components are used to ensure compatibility and reliability. High-quality parts reduce the risk of malfunctions and extend the intervals between maintenance activities.
- Advanced Lubrication Systems: Automated lubrication systems are used to ensure that all moving parts are consistently lubricated, reducing wear and tear and increasing efficiency.
- Training and Development: Continuous training programs for maintenance staff ensure that the team is up-to-date with the latest techniques and technologies in conveyor maintenance.
- Data-Driven Maintenance: Utilizing data collected from monitoring systems to predict potential failures and plan maintenance activities accordingly.
- Strategic Partnerships with Suppliers: Collaborations with suppliers like YB Components ensure a steady supply of essential parts and support services, which is critical given the unique requirements of such a large-scale system.
- Emergency Response Procedures: Established procedures for quick response in case of a critical system failure help minimize downtime and potential damage.
- Sustainability Practices: Incorporating environmentally friendly maintenance practices and materials to align with global sustainability standards and local regulations.
Through these detailed operational solutions and comprehensive maintenance strategies, the longest conveyor belt in South Africa is able to meet the high demands of the mining industry, maintaining efficiency and reliability in challenging operational conditions.
FAQs about Longest Conveyor Belt in South Africa
The title of the longest conveyor belt in the world is held by the conveyor belt system located in the Western Sahara. This extensive system stretches over 98 kilometers (61 miles) and is used primarily to transport phosphate rocks from the mines in Bou Craa to the port city of Laayoune on the Atlantic coast. This conveyor belt stands out not only for its impressive length but also for its ability to operate in one of the harshest environments on Earth. The conveyor traverses a barren, desert landscape, overcoming extreme temperatures, sand, and wind, which presents significant operational challenges. The design and maintenance strategies are therefore tailored to endure these severe conditions, ensuring continuous and efficient operations.
The longest overland conveyor in South Africa is the Impumelelo conveyor belt, which stretches approximately 26.8 kilometers (about 16.7 miles). This conveyor system, one of the most advanced in the country, facilitates the efficient transportation of coal from the Impumelelo mine in Mpumalanga to Sasol’s Brandspruit coal-to-liquids conversion plant. This system is crucial for the energy sector in South Africa, providing a reliable and continuous flow of coal necessary for the production of synthetic fuels and chemicals. Its construction has not only enhanced the operational capabilities of the mining sector but also significantly contributed to the local and national economy through job creation and infrastructural development.
The world’s largest conveyor belt system is found in the Western Sahara, specifically from the phosphate mines of Bou Craa to Laayoune, on the coast. This belt extends for over 98 kilometers and serves as the primary mode of transporting phosphate ore across the desert to the export port. The environment poses unique challenges for the conveyor system, including high winds and sand, which necessitate robust engineering and maintenance solutions. The system’s scale and its operation in such an extreme setting highlight its importance not only as a logistical solution but also as an engineering marvel, showcasing the capacity to adapt industrial operations to challenging environments.
The longest conveyor belt in the Southern Hemisphere is located in Western Australia. This conveyor, part of the Boddington Bauxite Mine’s operations, stretches approximately 31 kilometers (19 miles). It is used to transport bauxite—the primary ore used in the production of aluminum—from the mine to a processing plant, and then to a port for export. This conveyor system is critical to the mining operation, enhancing both its efficiency and environmental sustainability by reducing the reliance on truck haulage, which is both costlier and more environmentally damaging. The system’s length and capacity are tailored to meet the immense scale of production and demand associated with bauxite mining in the region.
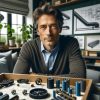
Jordan Smith, a seasoned professional with over 20 years of experience in the conveyor system industry. Jordan’s expertise lies in providing comprehensive solutions for conveyor rollers, belts, and accessories, catering to a wide range of industrial needs. From initial design and configuration to installation and meticulous troubleshooting, Jordan is adept at handling all aspects of conveyor system management. Whether you’re looking to upgrade your production line with efficient conveyor belts, require custom conveyor rollers for specific operations, or need expert advice on selecting the right conveyor accessories for your facility, Jordan is your reliable consultant. For any inquiries or assistance with conveyor system optimization, Jordan is available to share his wealth of knowledge and experience. Feel free to reach out at any time for professional guidance on all matters related to conveyor rollers, belts, and accessories.