Sustainability Through the Longest Conveyor Belt in India
The longest conveyor belt in India isn’t just a remarkable feat of engineering; it is a crucial component in enhancing operational efficiencies across several key sectors. Conveyor belts play an essential role in industrial operations by facilitating the fast, reliable, and cost-effective movement of goods and materials. This is especially true in the mining, manufacturing, and utility industries where the ability to move large quantities of materials efficiently directly impacts productivity and profitability. The longest conveyor belt in India exemplifies how advanced material handling technology can lead to more streamlined operations and substantial economic benefits. By reducing the reliance on truck transport, it significantly lowers fuel costs and decreases road congestion, leading to a smoother flow of operations and reduced environmental impact.
The Longest Conveyor Belt in India
The longest conveyor belt in India, a landmark achievement in industrial engineering, serves as a vital artery for the efficient transportation of materials in one of the country’s burgeoning industrial sectors. Located in Odisha, this marvel of modern technology extends over 7 kilometers, making it not only the longest in India but also a critical component in the nation’s infrastructure landscape.
Overview of India’s Longest Conveyor Belt
The significance of the longest conveyor belt in India transcends its mere length. Strategically situated in an area rich in minerals, this mine conveyor belt system plays a pivotal role in the mining sector. It connects the iron ore beneficiation plants to the shipping docks, thereby streamlining the entire transportation process. The belt’s location and functionality are crucial for minimizing the cost and time involved in moving raw materials to production sites and ultimately to markets.
The belt’s design and operation reflect a deep understanding of the geographic and economic context of the region. It passes through a landscape that includes arid regions, underdeveloped areas, and zones of ecological sensitivity. Accordingly, the design incorporates advanced technology to reduce environmental impact, such as systems that minimize dust emissions and noise, ensuring compliance with India’s stringent environmental regulations.
Technical Specifications and Role of Jindal’s Conveyor Belt
The heart of this logistical phenomenon is Jindal’s 7km pipe conveyor belt, which claims the title of the longest conveyor belt in India. This conveyor belt stands out not only for its length but also for its sophisticated construction and high capacity. Designed primarily for the transportation of coal, this conveyor system helps in conveying approximately 20 million tonnes of coal annually.
The technical specifications of Jindal’s conveyor belt include a pipe design that encloses the conveyor material, offering an eco-friendly solution by protecting the transported material from wind and preventing spillage and dust emissions. This is particularly important in regions where environmental conservation is a priority. The belt operates at a speed that maximizes throughput without compromising safety, typically around 5 meters per second, and incorporates features like automatic monitoring systems to ensure operational safety and efficiency.
The belt’s construction uses high-grade, wear-resistant materials to withstand the harsh conditions of heavy industrial use and the abrasive nature of raw materials like coal. The design also includes features for easy maintenance and longevity, reducing downtime and keeping the belt operational for longer periods without significant overhauls.
Economic and Environmental Impact
The operational efficiencies brought about by the longest conveyor belt in India are manifold. Economically, it reduces the reliance on truck transport, which is significantly more expensive and less reliable. The reduced road traffic also means fewer emissions and a smaller carbon footprint, aligning with global environmental goals and local sustainability targets.
Environmentally, the enclosed design of the pipe conveyor significantly mitigates the potential for pollution. By preventing materials from being exposed to the environment, it protects local wildlife and habitats from the potentially damaging effects of mining operations. This is especially critical in India, where the balance between industrial growth and environmental conservation is a key policy consideration.
Future Prospects
The success of the longest conveyor belt in India sets a benchmark for similar projects across the country and potentially in other developing nations with similar geographic and industrial profiles. It showcases the potential of advanced material handling technologies to transform industrial operations, not just in terms of efficiency and economics, but also in sustainability.
The continued evolution of conveyor technology promises even greater advancements, with potential developments including more energy-efficient motors, smarter control systems that adapt to changing loads and conditions, and materials that offer even greater durability and environmental protection.

Longest Conveyor Belt in India:Coal Mine’s 21 km Conveyor Belt
The longest conveyor belt in India spans approximately 21 kilometers (13 miles) and plays a crucial role in the country’s coal mining and power generation industries. Below is a detailed exploration of this impressive engineering structure, including its purpose, specifications, and significance.
Location and Ownership
This conveyor belt is situated in the Jharsuguda district of Odisha, a region known for its abundant mineral resources in eastern India. It connects a coal mine to an industrial plant or power station, facilitating efficient coal transportation. It is likely operated by key stakeholders in India’s mining and power sector, such as Mahanadi Coalfields Limited (MCL) or private companies like Adani Power or Vedanta.
Specifications of the Conveyor Belt
- Length: 21 kilometers (13 miles), making it the longest conveyor belt in India.
- Material: Constructed from highly durable rubber capable of withstanding the abrasive nature of coal dust and continuous heavy loads.
- Capacity: The belt transports thousands of tons of coal per hour, ensuring a continuous and reliable supply.
- Speed: It operates at a regulated speed, balancing efficiency and safety.
- Structure: The conveyor runs across a series of rollers and pulleys, supported by elevated steel platforms. Some sections are enclosed to reduce dust emissions and protect the belt from weather conditions.
Purpose and Function
This conveyor belt system is designed to streamline the transportation of coal from mining sites to power plants or processing facilities, eliminating the need for road transport by trucks. This setup ensures an uninterrupted flow of coal, critical for power plants relying on thermal energy, and reduces the dependency on rail transport, making operations more cost-efficient.
Advantages of the Conveyor System
- Cost-Efficiency: In the long run, conveyor systems are more economical than road or rail transport.
- Environmental Impact: By reducing truck usage, it cuts down on fuel consumption, emissions, and road congestion.
- Reduced Transit Time: The conveyor belt enables faster delivery compared to other methods of coal transport.
- Operational Safety: With less manual handling and fewer trucks in operation, the system reduces accident risks.
Challenges
- Maintenance: Regular inspections and maintenance are necessary to avoid breakdowns due to the system’s extended length.
- Weather Sensitivity: Heavy rainfall or storms can affect exposed sections, though weatherproofing measures mitigate these risks.
- Energy Consumption: The conveyor belt requires a significant amount of power, though it remains more energy-efficient than alternatives like trucking.
Impact on Industry and Economy
The 21 km conveyor belt plays a vital role in India’s energy sector, where coal-based thermal power plants contribute a substantial share of electricity. It also promotes sustainable mining practices by reducing the carbon footprint of coal transport. With this system in place, coal demand is met promptly, supporting the uninterrupted operation of power stations and industrial facilities, ultimately boosting India’s economy and energy security.
This conveyor belt represents a major step forward in engineering, resource management, and industrial efficiency. It showcases how advanced infrastructure can streamline operations while reducing environmental impact, making it a key component of India’s industrial future.
Longest Conveyor Belt in India:Utkal Alumina Project
The Utkal Alumina Project in Odisha, India, operates India’s longest conveyor belt system, which spans over 21 kilometers. This conveyor is a vital part of the alumina production process, ensuring the seamless transportation of bauxite (the primary raw material for aluminum production) from mines to the refinery. Here is a detailed exploration of the project and its significance.
Location and Project Overview
- Location: The conveyor belt system operates in the Rayagada and Kalahandi districts of Odisha, a mineral-rich region known for its bauxite deposits.
- Operator: Hindalco Industries, part of the Aditya Birla Group, owns the Utkal Alumina project, which focuses on the production of alumina for use in aluminum manufacturing.
- Purpose: The conveyor belt transports bauxite from the mines at Baphlimali hills to the alumina refinery located 21 kilometers away, reducing transportation costs and environmental impact.
Specifications of the Conveyor Belt
- Length: 21 kilometers (13 miles), making it India’s longest single-belt conveyor system.
- Material: The belt is designed to be highly durable to handle rough and heavy bauxite ore.
- Capacity: It can move tons of bauxite per hour to meet the refinery’s requirements for continuous production.
- Structure: The conveyor belt passes through difficult terrain, including hilly and forested areas, supported by steel structures, pulleys, and rollers. Some parts are enclosed to prevent dust emissions and weather damage.
- Automation: The system is automated to monitor operations and prevent interruptions, with sensors to detect load and track maintenance needs.
Purpose and Function
The Utkal Alumina Project’s conveyor system addresses the logistical challenges of transporting large quantities of bauxite from remote mines to the refinery. Traditional transportation methods like trucks were costly, slow, and caused environmental degradation. The conveyor ensures a steady flow of raw materials to the refinery, maintaining production efficiency and minimizing downtime.
Advantages of the Conveyor System
- Cost-Efficiency: A conveyor belt reduces long-term transportation costs compared to trucks or railways.
- Environmental Impact: The belt minimizes carbon emissions by reducing the need for truck fleets, helping promote green mining practices.
- Continuous Operation: It allows for uninterrupted delivery of bauxite to the refinery, essential for maintaining production schedules.
- Operational Safety: The automated system reduces manual handling and eliminates the risks associated with road transportation.
- Lower Maintenance: With fewer moving parts than a fleet of trucks, the system is easier to maintain, though regular inspections are still required.
Challenges
- Maintenance and Repairs: The belt requires regular maintenance to prevent breakdowns, given the rough terrain and heavy loads it handles.
- Weather Conditions: Rain, storms, and other weather events can pose challenges, though weatherproofing solutions have been implemented.
- Energy Consumption: Running a 21 km conveyor system demands significant power, though it remains more efficient than trucking over the same distance.
Impact on Industry and Economy
The Utkal Alumina conveyor belt plays a crucial role in India’s aluminum supply chain, ensuring the timely delivery of raw materials for processing. This contributes to economic growth, as aluminum is essential for industries like automotive, construction, and packaging. The conveyor belt also supports sustainable mining practices, aligning with India’s goals to reduce the environmental impact of industrial activities.
The Utkal Alumina Project sets an example of how large-scale conveyor systems can replace conventional transport methods, enhancing operational efficiency while lowering environmental costs. This state-of-the-art infrastructure is a key enabler of the alumina refinery’s success, ensuring the consistent and reliable production of alumina to meet both domestic and international demands.

Longest Conveyor Belt in India:84 km Pipe Conveyor Transportation System
India is home to one of the longest pipe conveyor transportation systems in the world, spanning a remarkable 84 kilometers (52 miles). This massive infrastructure is part of an advanced logistics solution used to transport coal and other bulk materials efficiently and sustainably. Below is a detailed description of this impressive system and its impact on industry and the environment.
Location and Project Overview
- Location: The 84 km pipe conveyor system is part of a coal transportation project in Odisha, India, linking coal mines to industrial plants and thermal power stations.
- Operator: The system has been developed by companies such as Essar Steel and NTPC to supply raw materials like coal and iron ore to power plants or steel manufacturing units.
- Objective: The primary purpose of this conveyor is to transport coal seamlessly over long distances, reducing reliance on traditional truck and rail transport.
What is a Pipe Conveyor System?
- Design: A pipe conveyor differs from conventional conveyor belts by enclosing the material within a circular pipe formed by the belt itself. The belt is flat at loading points and gradually curves into a pipe shape, holding the material securely inside.
- Benefits: This enclosed design minimizes material loss, dust emissions, and contamination while protecting the material from wind and rain, ensuring safe and efficient transport across long distances.
Specifications of the Conveyor System
- Length: 84 kilometers (52 miles), making it India’s longest conveyor system and one of the longest in the world.
- Capacity: It transports thousands of tons per hour of coal or other bulk materials, ensuring the steady operation of power plants.
- Speed: The system runs at a regulated speed to balance load handling and power consumption efficiently.
- Structure: It crosses rivers, forests, and hilly terrain, utilizing a network of rollers, pulleys, and steel platforms. Some sections are fully enclosed to minimize dust pollution.
Purpose and Function
The 84 km conveyor belt addresses the logistics challenges of transporting coal and other materials from remote mines to power stations or manufacturing plants. This system eliminates the need for truck convoys and minimizes the use of rail transport, providing a cost-effective and eco-friendly alternative for long-distance material handling.
Advantages of the 84 km Pipe Conveyor System
- Environmental Impact: By replacing trucks and reducing rail dependency, the conveyor minimizes carbon emissions and lowers the environmental footprint of coal transportation.
- Material Safety: The enclosed pipe design prevents material loss and contamination, ensuring high-quality delivery to the destination.
- Continuous Operation: The conveyor enables round-the-clock transport without interruptions, ensuring uninterrupted power plant operations.
- Reduced Costs: Long-term savings are achieved by reducing fuel consumption, labor costs, and road maintenance.
- Operational Safety: With fewer manual operations involved, the risk of accidents and injuries is significantly reduced.
Challenges
- High Installation and Maintenance Costs: Initial setup of such an extensive system requires significant investment. Regular maintenance is also essential to prevent breakdowns.
- Terrain Difficulties: Traversing challenging landscapes like rivers, hills, and forests can complicate installation and maintenance operations.
- Energy Requirements: Operating an 84 km conveyor demands substantial energy, though it remains more efficient than trucking over the same distance.
Impact on Industry and Economy
The 84 km pipe conveyor system is vital for India’s energy and steel sectors, ensuring the steady supply of raw materials like coal and iron ore. This contributes to energy security by facilitating uninterrupted power generation and enhances industrial productivity by reducing logistical delays.
Additionally, the conveyor system promotes sustainable industrial practices by reducing the environmental impact of material transport. It aligns with India’s green energy goals, supporting efforts to reduce emissions while improving operational efficiency.
The 84 km pipe conveyor system is a technological marvel that exemplifies the potential of modern infrastructure to address logistical challenges in a sustainable and cost-effective manner. It ensures faster, safer, and more reliable transportation, boosting both industrial output and environmental sustainability.
Technical Specifications and Operational Highlights of the Longest Conveyor Belt in India
The longest conveyor belt in India not only epitomizes impressive engineering prowess but also serves as a benchmark for operational efficiency in the conveyor technology sector. This section delves into the sophisticated technical specifications, the variety of materials transported, and the cutting-edge technology that underpins this monumental infrastructure.
Detailed Technical Specifications
India’s longest conveyor belt, measuring approximately 7 kilometers in length, is a testament to modern engineering and design capabilities. Constructed primarily from high-grade, durable materials, the belt is designed to withstand the abrasive nature of the heavy loads it carries. It features a multi-layered fabric core covered with a protective layer of rubber, which is both wear-resistant and designed to reduce slippage and heat build-up during operation.
The conveyor belt’s width and thickness are optimized to handle a significant capacity — capable of transporting thousands of tons of material per hour. This capability is critical in maintaining a steady supply chain and operational flow in industries such as mining and manufacturing. The conveyor operates at a speed designed to maximize efficiency while preserving the integrity of the materials transported, typically maintaining a speed of about 5 meters per second.
Materials Transported
The longest conveyor belt in India is predominantly used to transport coal and iron ore from deep within mining fields to processing plants and transportation hubs. The belt’s robust construction allows it to carry other abrasive materials like limestone and aggregates, which are essential components in construction and manufacturing sectors. The versatility in handling different materials is crucial for industries that rely on a diversified raw material base for their production processes.
Technology Used
The technology embedded in the longest conveyor belt in India includes advanced monitoring systems that ensure safety and efficiency. Real-time sensors along the belt monitor for signs of malfunctions, such as alignment issues or tears in the belt, which can be preemptively addressed to avoid operational downtime. Automated tensioning systems help maintain the correct pressure to avoid slippage or excessive wear.
Moreover, the conveyor is equipped with energy-efficient motors and variable speed drives that adjust the belt’s speed based on the load, which significantly reduces energy consumption. This not only lowers operational costs but also aligns with sustainable operational practices by reducing the carbon footprint of heavy industries.
Operational Efficiency
The operational efficiency of world’s longest conveyor belt india is evident in its impact on production timelines and cost reduction. By automating the transport of raw materials over significant distances, the conveyor eliminates the need for multiple handling processes, thereby reducing labor costs and minimizing material loss during transport.
Furthermore, the conveyor’s design minimizes environmental impact. Its enclosed structure prevents fine particles and dust from escaping into the atmosphere, a crucial factor in maintaining air quality and reducing the environmental degradation commonly associated with mining operations. This design also contributes to operational efficiency by ensuring that materials are not lost or contaminated during transport.

Environmental and Economic Impact of the Longest Conveyor Belt in India
The longest conveyor belt in India is not just a marvel of engineering; it is a cornerstone in the nexus of environmental sustainability and economic efficiency. This infrastructure has far-reaching impacts on the industries it serves, significantly altering their environmental footprint and economic landscape.
Environmental Sustainability Contributions
The environmental impact of the longest conveyor belt in India is profound, primarily due to its ability to significantly reduce the carbon emissions associated with traditional transport methods. In industries like mining and manufacturing, where raw materials need to be transported over large distances, the default transport methods often involve large fleets of trucks or railcars. These methods are not only fuel-intensive but also contribute to significant emissions of CO2 and other pollutants.
By replacing hundreds of truck journeys, the longest conveyor belt in India cuts down on diesel consumption, leading to a substantial reduction in greenhouse gas emissions. This is crucial for India, a country striving to meet ambitious climate targets and reduce its carbon footprint. Moreover, the enclosed design of the conveyor minimizes the scattering of dust and particulates, which are a common byproduct of transporting raw materials like coal or iron ore. This feature is particularly important in densely populated or ecologically sensitive areas, where dust from transportation can contribute to air pollution and have adverse health impacts on communities.
Economic Benefits
Economically, the longest conveyor belt in India offers several benefits that directly influence the bottom line of the industries it supports. One of the most significant benefits is the reduction in transportation costs. Traditional truck transport is not only fuel-intensive but also requires significant labor costs and maintenance. Conveyors, on the other hand, automate the transport process, significantly reducing the need for manual labor and lowering operational costs over time.
Furthermore, the reliability of conveyor systems like India’s longest belt enhances production efficiency. Materials can be moved continuously and at a predictable rate, allowing for smoother production schedules with less downtime. This reliability also reduces the risk of supply chain disruptions, which can be costly and damage customer relationships.
Safety is another critical area where the longest conveyor belt in India adds economic value. Transport by conveyor belt is far safer than by truck, which is prone to accidents and human error. A safer work environment not only reduces the potential for costly accidents and associated liabilities but also improves the overall working conditions for employees. This can lead to better workforce retention and lower insurance costs.
Increased Safety and Its Economic Implications
The safety enhancements provided by conveyor belts also extend to the durability and maintenance aspects of the operation. The longest conveyor belt in India is designed to handle massive loads and to operate under challenging environmental conditions with minimal maintenance. This durability reduces unexpected downtime, which can lead to significant losses in large-scale operations. Regular maintenance schedules and predictive maintenance enabled by modern sensor technology keep the belt running efficiently and prevent costly breakdowns.
Challenges and Innovations in Managing the Longest Conveyor Belt in India
Managing and maintaining the longest conveyor belt in India presents a unique set of challenges. From the harsh environmental conditions to the sheer scale of the operation, each aspect demands innovative solutions to ensure efficiency and longevity. This section explores the various hurdles encountered during the installation and ongoing maintenance of this extensive system and highlights the innovative technologies and practices that have been adopted to overcome these challenges.
Installation Challenges
The installation of the longest conveyor belt in India was a formidable engineering feat, considering the geographic and environmental complexities involved. One of the primary challenges was the terrain over which the conveyor had to be installed. Spanning several kilometers, the conveyor belt passes through varied landscapes, including rocky terrains and ecologically sensitive zones. Ensuring minimal environmental impact while navigating these areas required precise planning and execution.
Another significant challenge was the logistical aspect of transporting and assembling vast quantities of heavy materials and equipment in remote or difficult-to-access locations. The sheer size of the components used in the conveyor system also posed challenges in handling and assembly, necessitating the use of specialized machinery and techniques.
Maintenance Challenges
Once installed, the longest conveyor belt in India faces ongoing maintenance challenges. The extreme weather conditions prevalent in many parts of India, including intense heat, dust, and monsoon rains, can wear down the mechanical and structural components of the conveyor system. Preventing corrosion, abrasion, and other forms of wear and tear is crucial for maintaining the integrity and functionality of the conveyor belt.
Moreover, the length of the conveyor makes monitoring and timely maintenance a complex task. Identifying problem areas quickly and addressing them before they escalate into more significant issues is essential to avoid prolonged downtimes and ensure continuous operation.
Innovations in Material Handling and Automation
To address these challenges, several innovations have been integrated into the longest conveyor belt in India. Advanced material handling technologies have been employed to enhance the durability and efficiency of the conveyor system. For example, the belt itself is made from specially engineered rubber compounds that provide superior resistance to abrasion and tearing. This material choice not only extends the life of the conveyor belt but also reduces maintenance needs.
Automated systems play a pivotal role in the operational efficiency of the conveyor. State-of-the-art sensors and monitoring systems are installed along the length of the conveyor belt. These systems provide real-time data on the condition of the belt and alert maintenance teams to potential issues before they develop into serious problems. This predictive maintenance approach helps in planning and conducting repairs without major disruptions to operations.
In addition to physical technologies, software innovations, such as advanced analytics platforms, are used to analyze data collected from the conveyor system. These platforms help in understanding wear patterns and operational inefficiencies, allowing for more informed decision-making regarding maintenance and adjustments.
Energy Efficiency and Sustainability
Innovations aren’t limited to maintenance and material technologies. Energy efficiency and sustainability have also been significant focuses in the operation of the longest conveyor belt in India. The conveyor is equipped with energy-efficient motors and variable speed drives that adjust the conveyor’s operation to the load being carried. This not only reduces energy consumption but also decreases the wear on the belt, contributing to longer service life and reduced environmental impact.
FAQs about Longest Conveyor Belt in India
The longest belt conveyor system in the world is the Western Sahara conveyor belt. This extensive system spans over 98 kilometers (about 61 miles) and is used primarily to transport phosphate ores from the mines in Bou Craa to the port city of El-Aaiun in Western Sahara. This conveyor system is particularly notable not just for its length but also for its role in facilitating the movement of one of the main exports of the region. The harsh desert environment poses unique challenges, yet this conveyor system operates efficiently, moving thousands of tons of phosphate each day. This engineering feat demonstrates the capability of conveyor technology to adapt to extreme conditions and significantly streamline industrial operations.
The world’s largest conveyor belt is considered to be the Western Sahara conveyor, as mentioned above. However, in terms of the largest ‘single’ conveyor belt, it is the Phoenix Conveyor Belt Systems GmbH’s production, which spans over 20 kilometers from the lignite mines in Germany. This conveyor belt was specifically designed to handle the high demands of transporting materials over long distances without intermediate transfer stations, thus reducing operational costs and enhancing efficiency. Its construction utilizes a special type of belting material that offers durability against wear and tear, making it suitable for continuous operation under varying environmental conditions.
The longest conveyor belt in Odisha, India, is operated by Paradip Port. It is used to transport coal and other materials such as iron ore and limestone from the ships to the port’s storage facilities or directly to the industries further inland. This conveyor system is crucial for the port’s operations, enabling efficient handling of vast amounts of materials. The belt stretches approximately 9 kilometers, making it one of the longest in the region. The system is equipped with modern technology to monitor and maintain the flow and speed of the conveyor, ensuring safety and efficiency in operations.
The length of a conveyor belt in industrial applications can vary widely and is primarily determined by the specific requirements of the production or transportation process it is designed to support. Factors that influence the length of a conveyor belt include the distance between the start and end points of the material transfer, the layout of the production facility, and the nature of the material being transported. Conveyor belts can be custom-designed to fit specific paths, with lengths ranging from a few meters within small manufacturing units to several kilometers for large mining operations or inter-facility material transportation. Engineers must consider the optimal balance between conveyor length, speed, and the load capacity to ensure efficiency while minimizing wear and operational costs.
The longest conveyor belt in India is operated by Lafarge Umiam Mining Ltd. This belt stretches approximately 17 kilometers, transporting limestone from the mines located in Meghalaya to the cement plant in Chhatak, Bangladesh. It plays a crucial role in cross-border trade by supplying raw materials efficiently. The belt crosses challenging terrains, including hills, forests, and rivers, demonstrating impressive engineering capabilities. This conveyor system reduces the need for trucks, which helps minimize environmental pollution and transport costs. Operated continuously, it handles several tons of limestone every day, supporting the cement production process. With advanced technology, it ensures a seamless flow of materials with minimal manual intervention. This system is a model of long-distance material transport, contributing to sustainable operations in the cement industry. It is not only India’s longest but also one of the longest single conveyor belts in the world.
The Jharia coalfield, located in the Dhanbad district of Jharkhand, is the largest and most prominent coal belt in India. Covering an area of around 450 square kilometers, Jharia is known for its high-quality coking coal, essential for the steel industry. The coalfield has a long history of mining dating back to colonial times. However, it is also infamous for underground fires that have been burning for over a century, causing environmental and health issues. Despite these challenges, Jharia remains a key player in India’s energy sector, producing millions of tons of coal annually. Several major coal companies, including Coal India Limited (CIL), operate in the region. Jharia is strategically important as India depends heavily on its domestic coal supply for thermal power generation and steel production, making it a cornerstone of the country’s industrial economy.
The longest underground conveyor belt in the world operates at the Baodian Coal Mine in Shandong Province, China. It spans 31 kilometers, transporting coal from underground mining sites to surface facilities. The system plays a vital role in moving materials without the need for traditional trucks, ensuring energy-efficient and continuous operations. The belt is designed to withstand the harsh underground environment, including high temperatures and dust, with minimal maintenance requirements. It operates on advanced automation systems, ensuring uninterrupted transport of coal, reducing operational downtime, and improving overall productivity. These long underground conveyor belts are crucial in mining because they allow for efficient material movement without disturbing the surface environment. Such belts help mines operate more sustainably, with reduced environmental impact, lower costs, and increased safety.
There is no single standard length for a conveyor belt as it varies significantly based on the application and industry. Conveyor belts used in warehouses or manufacturing plants might only be a few meters long, typically ranging from 1 meter to 30 meters. In contrast, mining operations require much longer conveyor belts, often exceeding several kilometers. For example, overland conveyors can stretch more than 10 kilometers, while specialized belts like the Lafarge system in India extend 17 kilometers. Conveyor belts used in airports or logistics hubs typically run between 20 to 50 meters. The belt length depends on the distance between loading and unloading points, operational requirements, and terrain. Additionally, belts can be customized by joining smaller sections, enabling modular setups. While standard lengths exist for common industrial uses, longer belts are custom-built to meet specific project needs, especially in sectors like mining and construction.
Last Updated on October 18, 2024 by Jordan Smith
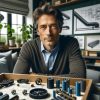
Jordan Smith, a seasoned professional with over 20 years of experience in the conveyor system industry. Jordan’s expertise lies in providing comprehensive solutions for conveyor rollers, belts, and accessories, catering to a wide range of industrial needs. From initial design and configuration to installation and meticulous troubleshooting, Jordan is adept at handling all aspects of conveyor system management. Whether you’re looking to upgrade your production line with efficient conveyor belts, require custom conveyor rollers for specific operations, or need expert advice on selecting the right conveyor accessories for your facility, Jordan is your reliable consultant. For any inquiries or assistance with conveyor system optimization, Jordan is available to share his wealth of knowledge and experience. Feel free to reach out at any time for professional guidance on all matters related to conveyor rollers, belts, and accessories.