Utilizing a Lagged Pulley Calculator for Precision
Conveyor pulley systems are integral components of conveyor belts, essential for material handling processes across various industries. A lagged pulley, in particular, plays a critical role by providing increased friction between the belt and the pulley surface, preventing slippage and ensuring smooth operation. Pulleys are crucial for maintaining the tension and direction of the conveyor belt, which is vital for efficient and reliable material transport. By optimizing the performance of conveyor systems, pulleys contribute significantly to productivity and reduce downtime in industrial operations. Understanding the function and benefits of lagged pulleys is essential for maintaining efficient conveyor systems.
Importance of Lagged Pulley in Conveyor Systems
The concept of a lagged pulley is fundamental in the realm of conveyor systems. A lagged pulley refers to a conveyor pulley that has been coated with a layer of material, typically rubber or ceramic, known as lagging. This layer is applied to enhance the performance and lifespan of both the pulley and the conveyor belt. The significance of a lagged pulley in conveyor systems can be understood through its various benefits and applications.
How Lagging Improves Traction
One of the primary advantages of a lagged pulley is its ability to improve traction between the pulley and the conveyor belt. In conveyor systems, slippage between the pulley and the belt can lead to inefficiencies, such as reduced material transport speed and increased wear on the belt. Lagging, with its high-friction surface, mitigates this slippage by providing better grip. The material used in lagging, whether rubber or ceramic, has a textured surface that increases the coefficient of friction. This enhanced grip ensures that the conveyor belt moves smoothly and consistently over the pulley, maintaining optimal operational efficiency.
Reducing Slippage with Lagged Pulley
Slippage is a common issue in conveyor systems, particularly in conditions where moisture, dust, or other contaminants are present. A lagged pulley effectively reduces slippage by offering a surface that resists these conditions. Rubber lagging, for example, provides excellent grip even in wet conditions, making it ideal for environments where water or other liquids might cause the belt to slip. Ceramic lagging, with its hard and abrasive-resistant properties, is suitable for heavy-duty applications where high levels of slippage could otherwise occur. By reducing slippage, lagged pulleys help maintain the correct tension and alignment of the conveyor belt, preventing disruptions in the material handling process.
Extending Lifespan of Pulley and Conveyor Belt
The application of lagging on a pulley significantly extends the lifespan of both the pulley and the conveyor belt. The lagging material acts as a protective barrier, absorbing the wear and tear that would otherwise affect the metal surface of the pulley. This protective layer reduces the direct contact between the metal pulley and the belt, minimizing the risk of damage due to abrasion. Additionally, the lagging material helps to distribute the load more evenly across the pulley surface, reducing the stress on specific points and preventing premature wear. As a result, both the pulley and the belt experience less wear and tear, leading to longer service life and reduced maintenance costs.
Additional Benefits of Lagged Pulley
Beyond traction improvement, slippage reduction, and lifespan extension, lagged pulleys offer several other benefits. They can help in noise reduction, as the softer lagging material absorbs some of the sound generated by the conveyor system. This can be particularly advantageous in settings where noise levels need to be minimized for safety or comfort reasons. Moreover, lagged pulleys can improve the overall energy efficiency of a conveyor system. By reducing slippage and ensuring smooth operation, the system requires less power to operate, leading to lower energy consumption and operational costs.
The importance of a lagged pulley in conveyor systems cannot be overstated. Its ability to improve traction, reduce slippage, extend the lifespan of both the pulley and the belt, and provide additional benefits like noise reduction and energy efficiency make it an essential component in maintaining effective and reliable conveyor operations.
Exploring Lagged Pulley Sizes
Lagged pulleys come in a variety of sizes to meet the diverse needs of different conveyor systems. The size of a lagged pulley is determined by several factors, including the diameter, face width, and the specific requirements of the conveyor application. Understanding the different sizes of lagged pulleys and their appropriate uses is crucial for selecting the right pulley for a given system.
Diameter of Lagged Pulley
The diameter of a lagged pulley is a critical dimension that influences the overall performance of the conveyor system. Larger diameter pulleys are typically used in heavy-duty applications where greater torque and load capacity are required. These pulleys provide a larger contact area with the conveyor belt, which helps in distributing the load more evenly and reducing wear on both the pulley and the belt. Conversely, smaller diameter pulleys are suitable for lighter-duty applications where space constraints and lower load capacities are considerations. Selecting the correct diameter is essential to ensure that the pulley can handle the operational demands without causing excessive wear or slippage.
Face Width of Lagged Pulley
The face width of a lagged pulley refers to the width of the pulley surface that comes into contact with the conveyor belt. This dimension is important for ensuring that the pulley can accommodate the width of the belt and provide adequate support. Wider face widths are used in applications where the conveyor belt is wider, offering more surface area for grip and reducing the likelihood of belt misalignment. Narrower face widths are appropriate for smaller belts or in applications where space is limited. Ensuring the correct face width is crucial for maintaining belt alignment and preventing edge wear, which can lead to premature belt failure.
Standard and Custom Sizes
Lagged pulleys are available in standard sizes that are commonly used in many conveyor systems. These standard sizes provide a good starting point for many applications and are readily available from manufacturers. However, there are instances where standard sizes may not meet the specific needs of a particular conveyor system. In such cases, custom-sized lagged pulleys can be designed and manufactured to meet the exact specifications required. Custom sizes allow for precise matching of the pulley to the conveyor system, ensuring optimal performance and longevity.
Factors Influencing Pulley Size Selection
Selecting the appropriate size of a lagged pulley involves considering several factors. The type of material being transported, the speed of the conveyor belt, the environmental conditions, and the load capacity are all critical factors that influence the choice of pulley size. For instance, in environments with high levels of moisture or contaminants, larger pulleys with robust lagging materials may be necessary to prevent slippage and wear. Similarly, in high-speed applications, the pulley size must be chosen to ensure stability and prevent excessive vibration. Consulting with engineers and using tools like a lagged pulley calculator can help in making informed decisions about pulley size selection.
Importance of Proper Size Selection
Proper selection of lagged pulley sizes is vital for the efficient and reliable operation of a conveyor system. Incorrectly sized pulleys can lead to a range of issues, including increased wear on the conveyor belt, reduced traction, slippage, and potential system failure. By choosing the right size, operators can ensure that the pulley provides adequate support and grip, maintains proper belt tension, and distributes the load evenly. This not only enhances the performance of the conveyor system but also extends the lifespan of its components, leading to reduced maintenance costs and downtime.
Exploring and selecting the correct sizes of lagged pulleys is a critical step in the design and maintenance of conveyor systems. Understanding the factors that influence pulley size, the importance of diameter and face width, and the availability of standard and custom sizes can help in making the right choices for specific applications.
Utilizing a Lagged Pulley Calculator
A lagged pulley calculator is an invaluable tool for engineers and technicians involved in the design and maintenance of conveyor systems. This tool simplifies the process of determining the appropriate size and lagging requirements for a pulley based on specific operational parameters. Utilizing a lagged pulley calculator can lead to more accurate and efficient conveyor system designs.
Lagged Pulley Calculator
The lagged pulley calculator is designed to assist in calculating the dimensions and lagging requirements of a pulley. By inputting various parameters, such as the diameter, face width, material, and load conditions, the calculator provides precise recommendations for the pulley size and lagging type needed for optimal performance. This tool is particularly useful for customizing pulley designs to meet specific operational needs.
Key Input Parameters
When using a lagged pulley calculator, several key input parameters must be considered:
- Diameter: The diameter of the pulley is a primary input that affects the overall performance and load capacity. The calculator uses this dimension to determine the appropriate size and lagging requirements.
- Face Width: The face width is another crucial dimension that influences the contact area between the pulley and the conveyor belt. Inputting the correct face width ensures that the pulley provides adequate support and grip for the belt.
- Material: The material of the pulley and lagging must be specified, as different materials have varying densities and friction properties. Common materials include rubber and ceramic, each offering distinct advantages for different applications.
- Load Conditions: The load conditions, including the weight and type of material being transported, are important factors. The calculator uses this information to recommend the appropriate lagging type and thickness to handle the load efficiently.
- Environmental Factors: Environmental conditions, such as temperature, moisture, and the presence of contaminants, are also considered. These factors influence the choice of lagging material and design to ensure reliable performance under specific conditions.
Benefits of Using a Lagged Pulley Calculator
The lagged pulley calculator offers several significant benefits:
- Accuracy: The calculator provides precise calculations based on standardized formulas and up-to-date material properties. This accuracy ensures that the selected pulley and lagging meet the operational requirements.
- Time-Saving: Manually calculating the dimensions and lagging requirements of a pulley can be time-consuming. The calculator streamlines this process, providing quick and reliable results, allowing engineers to focus on other critical tasks.
- Customization: The calculator allows for the customization of pulley designs to meet specific needs. By inputting unique operational parameters, users can obtain recommendations for custom-sized pulleys and lagging.
- Cost Efficiency: Accurate calculations help in selecting the right pulley size and lagging, reducing the risk of over-engineering or under-engineering. This balance leads to cost savings in materials and maintenance.
- Improved System Performance: By using the calculator to select the appropriate pulley size and lagging, conveyor systems can achieve optimal performance. Properly sized and lagged pulleys reduce wear, prevent slippage, and maintain consistent operation.
Steps to Use a Lagged Pulley Calculator
Using a lagged pulley calculator involves several straightforward steps:
- Gather Input Data: Collect all necessary input data, including pulley dimensions, material properties, load conditions, and environmental factors.
- Input Data into Calculator: Enter the collected data into the lagged pulley calculator. Ensure that all parameters are accurately specified to obtain reliable results.
- Review Recommendations: After inputting the data, review the recommendations provided by the calculator. These may include the suggested pulley diameter, face width, lagging type, and thickness.
- Consult with Engineers: If needed, consult with engineers or technical experts to validate the recommendations and ensure that they meet the specific requirements of the conveyor system.
- Implement Recommendations: Use the recommended pulley size and lagging specifications in the design and installation of the conveyor system. Regularly review and update the input parameters to maintain accuracy as operational conditions change.
A lagged pulley calculator is an essential tool for optimizing the design and performance of conveyor systems. By providing accurate and efficient calculations, the calculator helps in selecting the appropriate pulley size and lagging, ensuring reliable and cost-effective operation.
Lagged Pulley: Overview of Conveyor Pulley Types
Conveyor pulleys are essential components in conveyor systems, playing a pivotal role in the movement and control of conveyor belts. Among the various types of conveyor pulleys, the lagged pulley stands out due to its enhanced friction and wear resistance. However, it is crucial to understand the different types of pulleys available to appreciate the specific advantages and applications of lagged pulleys.
Lagged Pulleys
Lagged pulleys are characterized by the application of a lagging material, such as rubber or ceramic, to their surface. This lagging increases the friction between the pulley and the conveyor belt, reducing slippage and improving belt tracking. Lagged pulleys are particularly beneficial in high-tension and heavy-duty applications where maintaining consistent belt movement is crucial. They also help extend the life of both the pulley and the belt by providing a cushioning effect that reduces wear and tear.
Drum Pulleys
Drum pulleys, also known as cylindrical pulleys, are the most common type of conveyor pulley. They consist of a cylindrical shell with a straight face and a crowned surface, which helps in centering the belt. Drum pulleys are used at the head and tail of the conveyor system, where they provide the driving force and tension necessary for belt movement. While they are effective in many applications, they may not offer the same level of grip as lagged pulleys, making them less suitable for high-tension scenarios without additional lagging.
Wing Pulleys
Wing pulleys, also known as self-cleaning pulleys, are designed with a series of individual wings or fins extending from the center hub. These wings help to deflect and dislodge material that might otherwise build up on the pulley surface. Wing pulleys are commonly used in applications where the conveyor system handles bulk materials that are prone to sticking, such as in mining or agricultural operations. The self-cleaning action helps maintain efficiency and reduces the risk of belt damage.
Other Common Types
In addition to lagged, drum, and wing pulleys, several other types are used in conveyor systems, each with specific benefits:
- Snub Pulleys: These pulleys are placed close to the drive pulley to increase the belt’s wrap angle around the drive pulley, enhancing traction and reducing slippage.
- Take-Up Pulleys: These are used in the take-up assembly of the conveyor to maintain proper belt tension, which is critical for efficient operation.
- Bend Pulleys: These pulleys are used to change the direction of the belt, often found in conveyor systems with complex routing.
Understanding the various types of conveyor pulleys allows for better system design and optimization. Each pulley type offers unique benefits, and selecting the appropriate pulley for specific applications ensures efficient and reliable conveyor operation.
Lagged Pulley: Types of Pulley Lagging
Pulley lagging is essential for enhancing the performance and longevity of conveyor systems. Various types of lagging materials are available, each offering distinct benefits and suited to different applications. Here, we explore the primary types of pulley lagging: rubber lagging, ceramic lagging, and weld-on lagging.
Rubber Lagging
Rubber lagging is the most common type of pulley lagging. It involves covering the pulley surface with a layer of rubber, which can be applied in various patterns such as plain, diamond, or herringbone. Each pattern is designed to provide optimal grip and water dispersion, depending on the specific requirements of the conveyor system.
- Benefits: Rubber lagging increases the friction between the pulley and the belt, reducing slippage and improving belt tracking. It also provides a cushioning effect that minimizes wear and tear on both the pulley and the belt.
- Applications: Rubber lagging is suitable for a wide range of applications, including light to medium-duty conveyor systems, and is often used in industries such as manufacturing, packaging, and food processing.
Ceramic Lagging
Ceramic lagging involves the use of ceramic tiles embedded in a rubber base, providing superior wear resistance and increased friction. Ceramic lagging is particularly effective in high-tension and heavy-duty applications where traditional rubber lagging might wear out too quickly.
- Benefits: Ceramic lagging offers excellent abrasion resistance and a high coefficient of friction, making it ideal for extreme conditions. It also has a longer service life compared to rubber lagging, reducing the need for frequent maintenance.
- Applications: This type of lagging is commonly used in mining, bulk material handling, and other heavy-duty industrial applications where high wear resistance and increased grip are essential.
Weld-On Lagging
Weld-on lagging is a more permanent solution that involves welding metal bars or strips directly onto the pulley surface. This type of lagging is often used in applications where extreme durability and reliability are required.
- Benefits: Weld-on lagging provides a robust and long-lasting solution, capable of withstanding the harshest operating conditions. It is highly resistant to abrasion and impact, making it ideal for severe environments.
- Applications: Weld-on lagging is typically used in heavy-duty mining and quarrying operations, where the conveyor system must handle abrasive materials and operate continuously under high stress.
By understanding the different types of pulley lagging and their respective benefits, users can make informed decisions to optimize their conveyor systems for specific applications. Selecting the appropriate lagging material ensures improved performance, reduced maintenance, and longer service life.
Lagged Pulley: Pulley Lagging Procedure PDF
Proper installation and maintenance of lagged pulleys are crucial for ensuring their optimal performance and longevity. To aid in this process, many manufacturers and industry experts provide pulley lagging procedure PDFs. These documents offer detailed, step-by-step instructions for the correct application and maintenance of lagging materials on conveyor pulleys.
Importance of Pulley Lagging Procedure PDFs
Pulley lagging procedure PDFs are invaluable resources for anyone involved in the installation and maintenance of conveyor systems. They provide comprehensive guidelines that help ensure the lagging is applied correctly, maximizing the benefits and extending the life of the pulleys and belts.
Contents of Pulley Lagging Procedure PDFs
These procedure documents typically include:
- Preparation Steps: Detailed instructions on how to prepare the pulley surface for lagging, including cleaning, degreasing, and roughening the surface to ensure a strong bond.
- Adhesive Application: Guidelines on selecting and applying the appropriate adhesive for the specific type of lagging material being used.
- Lagging Material Application: Step-by-step directions on how to apply the lagging material, whether it is rubber, ceramic, or weld-on. This section includes tips on aligning the material, applying consistent pressure, and avoiding air bubbles.
- Curing Process: Information on the curing time required for the adhesive to set properly, ensuring a durable and long-lasting bond.
- Maintenance Tips: Recommendations for regular inspection and maintenance of the lagged pulleys to detect and address any signs of wear or damage early.
Benefits of Using Pulley Lagging Procedure PDFs
Following the guidelines provided in pulley lagging procedure PDFs helps prevent common issues such as improper adhesion, uneven lagging application, and premature wear. By adhering to these procedures, users can achieve the following benefits:
- Enhanced Performance: Correctly applied lagging ensures optimal friction and grip, improving the overall efficiency and reliability of the conveyor system.
- Extended Lifespan: Proper installation and maintenance extend the service life of both the pulley and the belt, reducing the need for frequent replacements and repairs.
- Cost Savings: By minimizing downtime and maintenance costs, users can achieve significant savings over the lifespan of the conveyor system.
Pulley lagging procedure PDFs are essential tools for ensuring the successful application and maintenance of lagged pulleys. By providing clear and detailed instructions, these documents help users achieve optimal performance, longevity, and cost-efficiency in their conveyor systems.
Advantages of Rubber Lagging Pulley
A lagged pulley, particularly one with rubber lagging, offers numerous benefits that enhance the performance and longevity of conveyor systems. Rubber lagging is one of the most common and effective types of lagging, providing several key advantages that make it a preferred choice in various industrial applications. Here, we delve into the benefits of rubber lagging pulleys, highlighting their increased grip, reduced wear, noise reduction, and discussing common applications where rubber lagging is especially advantageous.
Increased Grip
One of the primary advantages of a rubber lagged pulley is the significant increase in grip between the pulley and the conveyor belt. The rubber material used in lagging has a high coefficient of friction, which ensures that the belt remains securely in place as it moves over the pulley. This enhanced grip is crucial for preventing belt slippage, which can lead to operational inefficiencies and potential damage to the conveyor system.
The improved grip provided by rubber lagging is particularly beneficial in high-tension applications where the conveyor system is subjected to heavy loads. In such scenarios, the risk of slippage is higher due to the increased force exerted on the belt. Rubber lagging effectively mitigates this risk, ensuring smooth and reliable belt movement. Additionally, the increased grip helps maintain proper belt alignment, reducing the likelihood of misalignment issues that can cause wear and tear on the belt edges.
Reduced Wear
Another significant benefit of rubber lagged pulleys is the reduction in wear and tear on both the pulley and the conveyor belt. The rubber layer acts as a protective cushion, absorbing impact and reducing the abrasive forces that can cause premature wear. This cushioning effect is especially important in applications where the conveyor system handles heavy or abrasive materials that can exert significant pressure on the pulley and belt surfaces.
By minimizing direct contact between the metal pulley and the conveyor belt, rubber lagging helps extend the lifespan of both components. The reduced wear on the belt means fewer replacements and lower maintenance costs, while the extended life of the pulley itself contributes to overall cost savings for the conveyor system. In industries where downtime can result in substantial financial losses, the durability provided by rubber lagging is a critical advantage.
Noise Reduction
In addition to improving grip and reducing wear, rubber lagged pulleys also contribute to noise reduction in conveyor systems. The rubber material dampens vibrations and minimizes the noise generated as the belt moves over the pulley. This is particularly beneficial in environments where noise levels need to be controlled, such as in manufacturing plants or facilities located near residential areas.
Reduced noise levels not only create a more comfortable working environment for employees but also help comply with occupational health and safety regulations that limit permissible noise exposure levels. By minimizing the noise produced by conveyor systems, rubber lagging pulleys contribute to a safer and more productive workplace.
Common Applications of Rubber Lagging Pulleys
Rubber lagging pulleys are widely used in various industries due to their versatility and the multiple benefits they offer. Some common applications include:
Manufacturing
In manufacturing plants, conveyor systems are often required to handle diverse materials ranging from lightweight components to heavy machinery parts. Rubber lagging pulleys provide the necessary grip and durability to ensure efficient material handling and reduce the risk of production interruptions due to belt slippage or wear.
Mining
The mining industry involves the transportation of heavy, abrasive materials such as ore and minerals. Rubber lagged pulleys are ideal for this harsh environment, offering the durability and wear resistance needed to withstand the demanding conditions. The enhanced grip provided by rubber lagging also ensures that the conveyor belts can handle the heavy loads without slipping, maintaining consistent throughput.
Food Processing
In food processing facilities, conveyor systems must operate smoothly and hygienically to avoid contamination and ensure the efficient movement of products. Rubber lagging pulleys contribute to this by providing a clean, non-slip surface that reduces wear on the conveyor belts and minimizes the risk of product contamination.
Packaging
Packaging operations often involve rapid, continuous movement of goods. Rubber lagged pulleys help maintain the necessary belt tension and alignment to ensure that packaging processes run smoothly and efficiently. The noise reduction properties of rubber lagging are also beneficial in maintaining a quieter work environment in packaging facilities.
Scenarios Where Rubber Lagging Is Particularly Advantageous
High Moisture Environments
Rubber lagging pulleys are particularly advantageous in high moisture environments where water or other liquids can reduce the friction between the belt and the pulley. The rubber material maintains its grip even in wet conditions, preventing slippage and ensuring continuous operation. This makes rubber lagged pulleys ideal for industries such as food processing and agriculture, where moisture levels can vary significantly.
High Temperature Applications
Rubber lagging can also be formulated to withstand high temperatures, making it suitable for applications where the conveyor system is exposed to elevated temperatures. In such environments, maintaining the integrity and performance of the pulley and belt is crucial, and rubber lagging provides the necessary heat resistance and durability.
Heavy Load Handling
In applications where the conveyor system is required to handle heavy loads, the additional grip and wear resistance provided by rubber lagging pulleys are essential. The rubber material helps distribute the load evenly across the pulley surface, reducing stress on individual components and enhancing the overall stability and efficiency of the system.
Rubber lagging pulleys offer numerous advantages that enhance the performance and longevity of conveyor systems. By providing increased grip, reduced wear, and noise reduction, they contribute to more efficient and reliable operations across various industries. Common applications such as manufacturing, mining, food processing, and packaging benefit significantly from the use of rubber lagged pulley.
FAQs about Lagged Pulley
A lagged pulley is a type of conveyor pulley that has a layer of material, typically rubber or ceramic, applied to its surface. This layer, known as lagging, is designed to increase the friction between the pulley and the conveyor belt. This enhanced grip helps prevent slippage, improves belt tracking, and extends the lifespan of both the pulley and the belt. Lagged pulleys are essential in high-tension and heavy-duty applications where the conveyor system needs additional traction to handle the load efficiently. By providing a more consistent and reliable grip, lagged pulleys contribute to the overall efficiency and safety of the conveyor system.
Applying pulley lagging involves several steps to ensure a secure and durable attachment of the lagging material to the pulley. First, the pulley surface is cleaned and prepped, often involving degreasing and sandblasting to remove contaminants and roughen the surface. Next, an adhesive is applied to both the pulley and the lagging material. The lagging material, typically rubber or ceramic strips, is then carefully aligned and pressed onto the pulley surface. It is crucial to apply consistent pressure to avoid air bubbles and ensure a uniform bond. Finally, the lagged pulley is allowed to cure for a specified period, ensuring the adhesive fully sets. Proper application of pulley lagging requires precision and attention to detail to maximize performance and durability.
Rubber lagging refers to the application of rubber material onto the surface of a conveyor pulley. This rubber layer enhances the friction between the pulley and the conveyor belt, reducing slippage and improving belt tracking. Rubber lagging is available in various patterns, such as plain, diamond, and herringbone, each designed to optimize grip and water dispersion. The choice of pattern depends on the specific requirements of the conveyor system, including the type of material being transported and the environmental conditions. Rubber lagging not only increases the traction but also provides a cushioning effect, reducing wear and tear on both the pulley and the belt.
The thickness of the lagging material on a pulley can vary depending on the application and the type of lagging used. Standard rubber lagging typically ranges from 6 mm (0.24 inches) to 12 mm (0.47 inches) in thickness. For heavy-duty applications, thicker lagging may be used to provide additional durability and grip. Ceramic lagging, which offers higher wear resistance, can also vary in thickness, generally ranging from 10 mm (0.39 inches) to 20 mm (0.79 inches). The appropriate thickness is chosen based on factors such as the conveyor system’s load capacity, operating conditions, and the specific performance requirements of the application. Proper selection of lagging thickness ensures optimal performance and longevity of the conveyor system.
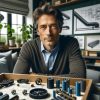
Jordan Smith, a seasoned professional with over 20 years of experience in the conveyor system industry. Jordan’s expertise lies in providing comprehensive solutions for conveyor rollers, belts, and accessories, catering to a wide range of industrial needs. From initial design and configuration to installation and meticulous troubleshooting, Jordan is adept at handling all aspects of conveyor system management. Whether you’re looking to upgrade your production line with efficient conveyor belts, require custom conveyor rollers for specific operations, or need expert advice on selecting the right conveyor accessories for your facility, Jordan is your reliable consultant. For any inquiries or assistance with conveyor system optimization, Jordan is available to share his wealth of knowledge and experience. Feel free to reach out at any time for professional guidance on all matters related to conveyor rollers, belts, and accessories.