How to Replace a Lagged Drum Pulley Efficiently
A lagged drum pulley is a crucial component in conveyor systems, featuring a layer of material, such as rubber or ceramic, applied to its surface. This layer enhances the pulley’s grip on the conveyor belt, preventing slippage and ensuring smooth, efficient operation. The lagged drum pulley is vital for maintaining proper belt tension and alignment, which significantly improves the system’s overall efficiency and durability. By reducing wear and tear on the belt and pulley, lagged drum pulleys extend the lifespan of the conveyor system, reducing maintenance costs and downtime.
Lagged Drum Pulley Replacement
Lagged Drum Pulley Replacement: Detailed Guide on When and How to Replace
Replacing a lagged drum pulley is a critical maintenance task that ensures the efficient operation and longevity of your conveyor system. Knowing when to replace a lagged drum pulley and understanding the steps involved in the replacement process can prevent unexpected downtime and costly repairs. This section provides a comprehensive guide on the signs of wear that indicate the need for replacement and a step-by-step process for replacing a lagged drum pulley.
Signs of Wear Indicating Replacement
- Excessive Wear and Tear: Over time, the lagging material on the drum pulley can wear down due to constant friction and contact with the conveyor belt. Look for visible signs of wear such as grooves, cracks, or thinning of the lagging material. If the lagging is significantly worn or damaged, it can lead to reduced traction and belt slippage.
- Material Build-Up: Accumulation of material on the drum pulley can cause uneven wear and reduce the effectiveness of the lagging. If regular cleaning does not resolve the build-up, it may be time to replace the pulley to ensure smooth operation.
- Decreased Performance: A lagged drum pulley that is no longer performing efficiently will show signs such as increased belt slippage, reduced material handling efficiency, and abnormal noises during operation. These symptoms indicate that the pulley is not providing the necessary grip and needs replacement.
- Visible Damage: Physical damage to the drum pulley, such as dents, bends, or cracks, can compromise its structural integrity and performance. Regular inspections can help identify such damage early and prevent further issues.
- Regular Maintenance Schedule: Following a regular maintenance schedule that includes periodic replacement of key components like the lagged drum pulley can prevent unexpected failures and maintain optimal conveyor performance.
Step-by-Step Replacement Instructions
- Safety Precautions: Ensure that the conveyor system is completely shut down and locked out to prevent accidental startups. Wear appropriate personal protective equipment (PPE) such as gloves, safety glasses, and hard hats to protect against injury during the replacement process.
- Remove the Conveyor Belt: Loosen the tension on the conveyor belt and carefully remove it from the drum pulley. Secure the belt in a safe position to prevent it from falling or getting damaged during the replacement process.
- Disconnect the Drum Pulley: Remove any guarding or covers around the drum pulley. Disconnect the pulley from the drive mechanism, which may include removing coupling, shaft, or mounting bolts. Make sure to keep track of all removed parts for reassembly.
- Extract the Old Pulley: Carefully extract the old drum pulley from its position. Use appropriate lifting equipment, such as hoists or cranes, to handle large or heavy pulleys. Ensure that the pulley is supported securely during removal to prevent accidents.
- Inspect the Conveyor System: Before installing the new lagged drum pulley, inspect the conveyor system for any additional wear or damage. Check the bearings, shafts, and mounting brackets for signs of wear or misalignment. Replace any damaged components as necessary.
- Install the New Pulley: Position the new lagged drum pulley in place and secure it to the drive mechanism. Ensure that all bolts and couplings are tightened to the manufacturer’s specifications. Verify that the pulley is aligned correctly with the conveyor system to prevent tracking issues.
- Reinstall the Conveyor Belt: Reinstall the conveyor belt onto the new drum pulley and adjust the tension as needed. Ensure that the belt is properly aligned to prevent tracking issues and ensure smooth operation.
- Test the Conveyor System: Perform a test run of the conveyor system to ensure that the new lagged drum pulley is functioning correctly. Check for proper alignment, tension, and performance. Address any issues that arise during the test run to ensure optimal operation.
Replacing a lagged drum pulley is an essential maintenance task that ensures the continued efficiency and reliability of conveyor systems. By recognizing the signs of wear and following a systematic replacement process, you can maintain optimal performance and prevent unexpected downtime. Regular inspections, adherence to safety precautions, and the use of appropriate tools and equipment are crucial for successful lagged drum pulley replacement. Ensuring that your conveyor system is equipped with well-maintained pulleys contributes to overall operational efficiency and productivity.
Lagged Drum Pulley for Sale
Lagged Drum Pulley for Sale: Tips on Finding and Purchasing
Finding the right lagged drum pulley for sale involves considering various factors to ensure you purchase a product that meets your operational needs and budget. This section provides tips on where to find lagged drum pulleys for sale, what to look for when evaluating options, and key considerations for selecting the right pulley for your conveyor system.
Where to Find Lagged Drum Pulleys for Sale
- Manufacturers’ Websites: Many manufacturers offer direct sales through their websites. Visiting the websites of reputable manufacturers allows you to explore their product range, specifications, and pricing. Purchasing directly from the manufacturer can also provide assurances of quality and support.
- Industrial Supply Companies: Industrial supply companies often stock a wide range of conveyor components, including lagged drum pulleys. These suppliers may offer both new and used pulleys, providing options to suit different budgets and needs.
- Online Marketplaces: Platforms such as eBay, Amazon, and specialized industrial marketplaces list various conveyor components, including lagged drum pulleys. These platforms provide the convenience of comparing multiple options, reading reviews, and making purchases from the comfort of your location.
- Local Distributors: Local distributors and dealers of industrial equipment can be a valuable resource for finding lagged drum pulleys. These distributors often have in-depth knowledge of the products they sell and can provide personalized recommendations based on your specific requirements.
- Trade Shows and Industry Events: Attending trade shows and industry events allows you to connect with manufacturers and suppliers directly. These events provide opportunities to see products firsthand, discuss your needs with experts, and negotiate pricing.
What to Look for When Evaluating Lagged Drum Pulleys
- Material Quality: The quality of the materials used in the construction of the pulley significantly impacts its durability and performance. Look for pulleys made from high-grade steel or stainless steel and high-quality lagging materials.
- Size and Specifications: Ensure that the lagged drum pulley you choose matches the size and specifications required for your conveyor system. Consider factors such as diameter, width, and lagging type to ensure compatibility and optimal performance.
- Design and Features: Evaluate the design and features of the pulley, including the type of lagging, reinforcement, and any special coatings. These features can enhance the performance and longevity of the pulley in your specific application.
- Brand Reputation: Purchasing from reputable brands and manufacturers ensures that you receive a high-quality product. Established brands have a track record of reliability and performance, reducing the risk of premature failures.
- Customization Options: Some applications may require custom-sized pulleys or specific features. Check if the supplier offers customization options to tailor the pulley to your unique requirements.
- Warranty and Support: Consider the warranty and support offered by the supplier. A comprehensive warranty and responsive customer support provide peace of mind and assistance in case of any issues with the pulley.
Key Considerations for Selecting the Right Lagged Drum Pulley
- Assess Operational Needs: Determine the specific requirements of your conveyor system, including load capacity, environmental conditions, and desired lifespan, to select the appropriate lagged drum pulley.
- Quality and Durability: Invest in high-quality pulleys made from durable materials to ensure long-term performance and reduce maintenance costs. The initial investment in quality pulleys can lead to long-term savings.
- Customization Requirements: Evaluate whether standard pulleys meet your needs or if custom-designed solutions are necessary. Custom pulleys can optimize performance but may come with higher costs.
- Supplier Reputation: Choose reputable suppliers and manufacturers known for producing reliable lagged drum pulleys. Established brands offer better warranties and customer support, ensuring peace of mind.
- Total Cost of Ownership: Consider the total cost of ownership, including initial purchase price, maintenance, and operational efficiency. Investing in durable, high-quality pulleys can result in long-term savings and improved productivity.
- Lead Time and Availability: Plan your purchases to account for lead times and ensure that pulleys are available when needed. Avoiding delays can minimize downtime and maintain productivity.
Finding the right lagged drum pulley for sale involves careful consideration of material quality, size, specifications, design features, brand reputation, customization options, warranty, and support. By leveraging various sources such as manufacturers’ websites, industrial supply companies, online marketplaces, local distributors, and trade shows, you can find a suitable pulley that meets your operational needs. Assessing operational requirements, prioritizing quality and durability, evaluating customization needs, and considering total cost of ownership and lead time are essential steps to ensure a successful purchase. Investing in high-quality lagged drum pulleys contributes to the efficiency and reliability of your conveyor system, enhancing overall productivity.
Lagged Drum Pulley: Drum Pulley for Conveyor Belt
Drum Pulley for Conveyor Belt: Role, Benefits, and Applications
The drum pulley is a vital component of conveyor belt systems, playing a key role in driving and guiding the conveyor belt. Understanding the functions, benefits, and applications of drum pulleys can help businesses optimize their conveyor systems for improved efficiency and performance. This section discusses the role of drum pulleys in conveyor belt systems, their benefits, and the various applications they are used in.
Role of Drum Pulleys in Conveyor Belt Systems
Drum pulleys serve several critical functions in conveyor belt systems:
- Driving the Conveyor Belt: The drum pulley, typically positioned at the drive end of the conveyor system, provides the necessary traction to move the conveyor belt and transport materials. The pulley is connected to a motor that drives its rotation, which in turn moves the belt.
- Guiding the Conveyor Belt: Drum pulleys help guide and support the conveyor belt, ensuring it remains aligned and tracks correctly. Proper alignment prevents belt slippage, material spillage, and unnecessary wear on the belt and pulley.
- Maintaining Tension: Drum pulleys help maintain the appropriate tension in the conveyor belt. Proper tension ensures that the belt moves smoothly and efficiently, reducing the risk of slack or excessive strain that could lead to belt damage.
Benefits of Using Drum Pulleys
- Enhanced Traction and Efficiency: Drum pulleys with lagging material, such as rubber or ceramic, provide enhanced traction, reducing slippage and improving the efficiency of material transport. The improved grip ensures that the belt moves consistently, even under heavy loads.
- Extended Belt Life: By providing proper support and maintaining tension, drum pulleys help extend the life of the conveyor belt. Reduced slippage and wear result in fewer maintenance requirements and longer operational lifespan for the belt.
- Improved Performance: High-quality drum pulleys contribute to the overall performance of the conveyor system. Efficient driving and guiding of the belt result in smooth operation, reduced downtime, and increased productivity.
- Versatility: Drum pulleys are versatile components that can be used in various conveyor systems, from light-duty to heavy-duty applications. Their adaptability makes them suitable for a wide range of industries and material handling needs.
Applications of Drum Pulleys in Conveyor Belt Systems
Drum pulleys are used in a variety of industries and applications, each with specific requirements and challenges:
- Mining and Quarrying: In the mining and quarrying industries, drum pulleys are essential for transporting bulk materials such as coal, ore, and aggregates. These pulleys are designed to handle heavy loads and operate in harsh conditions, ensuring efficient material transport.
- Manufacturing: Drum pulleys are used in manufacturing plants to move products and materials along production lines. They facilitate the efficient flow of materials, supporting processes such as assembly, packaging, and quality control.
- Agriculture: In agricultural applications, drum pulleys help transport grains, seeds, and other produce. These pulleys ensure smooth and efficient handling of bulk materials, reducing manual labor and improving productivity.
- Food Processing: The food processing industry requires conveyor systems that meet strict hygiene and safety standards. Drum pulleys used in these applications are often made from food-grade materials and designed to withstand frequent cleaning and sanitization.
- Logistics and Warehousing: In logistics and warehousing, drum pulleys facilitate the movement of packages, pallets, and other items. Efficient material handling systems help streamline operations, reduce handling times, and improve overall efficiency.
Drum pulleys are integral components of conveyor belt systems, providing essential functions such as driving the belt, guiding and supporting it, and maintaining proper tension. The benefits of using drum pulleys include enhanced traction, extended belt life, improved performance, and versatility. These pulleys are used in various industries, including mining, manufacturing, agriculture, food processing, and logistics, each with specific requirements and applications. Understanding the role and benefits of drum pulleys helps businesses optimize their conveyor systems for efficient and reliable material handling, ensuring smooth operation and increased productivity.
Lagged Drum Pulley: Tail Drum Pulley
Explanation of Tail Drum Pulley
A tail drum pulley is a critical component in conveyor systems, typically located at the tail end of the conveyor belt. Its primary function is to redirect the conveyor belt back towards the head pulley, creating a continuous loop. Unlike drive pulleys, tail drum pulleys do not provide power to move the belt. Instead, they guide the return side of the belt, ensuring it runs smoothly and maintains proper alignment and tension.
Function in a Conveyor System
The tail drum pulley plays several vital roles in a conveyor system:
- Belt Tension: By maintaining proper tension on the return side of the belt, the tail drum pulley helps to prevent sagging and ensures smooth belt movement. Proper tension is crucial for preventing belt slippage and ensuring efficient operation.
- Belt Tracking: The tail drum pulley helps to keep the conveyor belt aligned. Proper tracking is essential to avoid misalignment issues that can lead to belt damage and operational inefficiencies.
- Return Belt Support: As the belt returns to the head pulley, the tail drum pulley supports it, minimizing wear and tear on the belt and extending its lifespan.
Advantages of a Tail Drum Pulley
Using a tail drum pulley in a conveyor system offers several advantages:
- Enhanced Belt Life: By providing proper support and maintaining tension, tail drum pulleys help to reduce wear and tear on the conveyor belt, extending its operational life.
- Improved Efficiency: Properly functioning tail drum pulleys ensure smooth and efficient belt movement, reducing the risk of operational disruptions and downtime.
- Cost Savings: Extending the life of the conveyor belt and reducing maintenance needs lead to significant cost savings over the system’s lifespan.
- Versatility: Tail drum pulleys can be used in various conveyor systems, from simple, straight-line conveyors to more complex systems with multiple curves and elevation changes.
A tail drum pulley is an essential component in maintaining the efficiency and longevity of a conveyor system. By ensuring proper belt tension and alignment, it helps to prevent operational issues and extend the life of the conveyor belt. Investing in high-quality tail drum pulleys can lead to improved system performance and significant cost savings.
Drum Pulley Drawing
Importance of Accurate Drum Pulley Drawings
Accurate drum pulley drawings are crucial for the successful manufacturing and installation of conveyor pulleys. These technical drawings provide detailed specifications and dimensions, ensuring that the pulleys meet the required standards and fit seamlessly into the conveyor system.
What to Include in a Technical Drawing
An effective drum pulley drawing should include the following details:
- Dimensions: Accurate measurements of the drum’s diameter, width, and overall length are essential. These dimensions ensure that the pulley will fit properly within the conveyor system.
- Material Specifications: The drawing should specify the materials used for the drum, including any lagging material. This information is crucial for ensuring the pulley meets the required strength and durability standards.
- Mounting Details: Details about the mounting configuration, including the size and type of shaft, keyways, and mounting holes, should be included. These details ensure that the pulley can be securely attached to the conveyor system.
- Lagging Specifications: If the drum pulley is lagged, the drawing should include information about the type and thickness of the lagging material. This detail is essential for ensuring the pulley provides the required grip and friction.
- Tolerance and Finish: Specifications for manufacturing tolerances and surface finish are important for ensuring the pulley meets the required quality standards. This information helps to minimize variations and ensure consistent performance.
Benefits of Accurate Drum Pulley Drawings
Having precise and detailed drum pulley drawings offers several benefits:
- Manufacturing Accuracy: Detailed drawings ensure that manufacturers produce pulleys that meet the exact specifications, reducing the risk of errors and defects.
- Efficient Installation: Accurate drawings provide installers with the information needed to correctly fit the pulleys into the conveyor system, reducing installation time and minimizing the risk of misalignment issues.
- Quality Assurance: Clear specifications help to maintain high-quality standards, ensuring that the pulleys perform reliably and have a long operational life.
Accurate drum pulley drawings are vital for the successful manufacturing and installation of conveyor pulleys. By providing detailed specifications and dimensions, these drawings help to ensure that the pulleys meet the required standards and perform efficiently within the conveyor system. Investing in precise technical drawings can lead to improved quality, reduced installation times, and enhanced system performance.
Lagged Drum Pulley: Drum Pulley Manufacturers
Overview of Leading Drum Pulley Manufacturers
Choosing a reliable drum pulley manufacturer is crucial for ensuring the quality and performance of your conveyor system. Leading manufacturers offer a range of products and services designed to meet the needs of various industrial applications. Here, we explore some of the top drum pulley manufacturers, their product offerings, and key considerations when choosing a manufacturer.
PROK
Product Offerings
PROK is a well-known manufacturer of conveyor components, including drum pulleys. They offer a wide range of pulleys designed for different applications, from light-duty to heavy-duty industrial use. PROK’s pulleys are known for their robust construction and high-quality materials, ensuring long-lasting performance.
Key Considerations
- Quality: PROK is known for its high-quality products that meet international standards.
- Innovation: The company invests in research and development to continuously improve its product offerings.
- Support: PROK provides excellent customer support, including technical assistance and after-sales service.
Fenner Dunlop
Product Offerings
Fenner Dunlop offers a comprehensive range of conveyor pulleys, including head pulleys, tail pulleys, and bend pulleys. Their products are designed to withstand demanding industrial environments, providing reliable performance and durability.
Key Considerations
- Reputation: Fenner Dunlop is a trusted name in the conveyor industry, known for its reliable and high-performance products.
- Customization: They offer custom pulley designs to meet specific application requirements.
- Service: Fenner Dunlop provides extensive after-sales support and maintenance services.
Rulmeca
Product Offerings
Rulmeca is a global manufacturer specializing in conveyor components, including drum pulleys. Their product range includes various types of pulleys designed for different industrial applications, ensuring efficient material handling.
Key Considerations
- Global Reach: Rulmeca has a strong global presence, making it easy to source their products worldwide.
- Quality Control: The company emphasizes stringent quality control measures to ensure the reliability and durability of its products.
- Technical Expertise: Rulmeca offers technical support and expertise to help clients choose the right pulleys for their needs.
Dodge (ABB)
Product Offerings
Dodge, a brand under ABB, is renowned for its conveyor pulleys and other power transmission products. Dodge pulleys are designed for high performance and reliability, making them a preferred choice in many industrial applications.
Key Considerations
- Innovation: Dodge is known for its innovative designs and advanced manufacturing techniques.
- Reliability: Their products are built to last, offering excellent durability and performance.
- Support: Dodge provides comprehensive customer support and technical assistance.
Factors to Consider When Choosing a Manufacturer
When selecting a drum pulley manufacturer, consider the following factors:
- Product Quality: Ensure that the manufacturer’s products meet industry standards and are made from high-quality materials.
- Customization Options: Look for manufacturers that offer customization options to meet specific application requirements.
- Reputation: Choose a manufacturer with a strong reputation for reliability and customer satisfaction.
- Support Services: Consider the level of technical support and after-sales service provided by the manufacturer.
- Innovation: Opt for manufacturers that invest in research and development to provide innovative and efficient solutions.
Selecting the right lagged drum pulley manufacturer is essential for ensuring the quality and performance of your conveyor system. Leading manufacturers like PROK, Fenner Dunlop, Rulmeca, and Dodge offer a range of high-quality products designed to meet the needs of various industrial applications. By considering factors such as product quality, customization options, reputation, and support services, businesses can make informed decisions and choose manufacturers that offer the best value for their investment.
FAQs about Lagged Drum Pulley
The purpose of a lagged pulley is to increase the friction between the pulley and the conveyor belt, which helps to prevent slippage and improve the efficiency of the conveyor system. Lagged pulleys are coated with a material, such as rubber or ceramic, that enhances the grip on the belt. This increased traction ensures that the conveyor belt moves smoothly and consistently, which is crucial for maintaining the flow of materials. Additionally, lagged pulleys protect the pulley surface from wear and tear caused by the abrasive materials being transported. This not only extends the life of the pulley but also reduces maintenance costs and downtime, making the conveyor system more reliable and efficient overall.
A lagged drum, also known as a lagged pulley, is a cylindrical component used in conveyor systems that has been coated with a layer of material to improve its grip and durability. The lagging material, typically rubber or ceramic, is applied to the surface of the drum to increase friction between the drum and the conveyor belt. This enhanced friction helps prevent the belt from slipping, ensuring smooth and efficient operation of the conveyor system. Lagged drums are commonly used in both drive and non-drive positions within a conveyor setup to support the belt and maintain proper tension. By reducing slippage and wear, lagged drums contribute to the overall efficiency and longevity of the conveyor system.
Lagging a pulley involves several steps to ensure a secure and effective application. Here is a general guide on how to lag a pulley:
Preparation: Begin by cleaning the surface of the pulley thoroughly to remove any dirt, grease, or old lagging material. Use appropriate cleaning agents and tools to achieve a clean, smooth surface. Proper preparation is crucial for ensuring that the new lagging material adheres correctly.
Measurement and Cutting: Measure the circumference and width of the pulley to determine the size of the lagging material needed. Cut the lagging material to the appropriate dimensions, ensuring it fits the pulley surface accurately.
Adhesive Application: Apply a suitable adhesive to both the pulley surface and the back of the lagging material. Ensure even coverage to promote strong adhesion. The type of adhesive used will depend on the lagging material and the operating conditions of the conveyor system.
Lagging Installation: Carefully position the lagging material onto the pulley, starting at one end and working your way around. Press the material firmly onto the pulley surface, ensuring that there are no air bubbles or gaps. Use a roller or similar tool to apply even pressure and secure the lagging in place.
Seam Sealing: If the lagging material has seams, seal them with an appropriate seam sealer to prevent moisture and debris from getting underneath the lagging. This step helps to prolong the life of the lagging and the pulley.
Curing and Setting: Allow the adhesive to cure and set according to the manufacturer’s instructions. This process may take several hours, during which the pulley should not be used.
Inspection and Testing: Once the adhesive has fully cured, inspect the lagging for any defects or areas that may need additional attention. Conduct a test run of the conveyor system to ensure that the lagging is functioning correctly and providing the desired traction and protection.
The lagging of belt pulleys involves applying a layer of material to the surface of the pulleys to improve their grip and durability. This process is essential for enhancing the performance of conveyor systems. Lagging materials commonly used include rubber, ceramic, and polyurethane. These materials are chosen for their high friction coefficients and wear resistance, which help prevent belt slippage and protect the pulleys from damage caused by abrasive materials.
There are several types of pulley lagging:
Rubber Lagging: This is the most common type of lagging. It provides good friction and is relatively inexpensive. Rubber lagging can be smooth or patterned, with diamond and herringbone patterns being popular choices for increased grip.
Ceramic Lagging: Ceramic lagging offers superior wear resistance and is ideal for high-tension applications. It provides excellent traction and durability, making it suitable for harsh environments where the conveyor system is exposed to heavy loads and abrasive materials.
Polyurethane Lagging: Polyurethane is highly resistant to oils, chemicals, and abrasion. It is often used in environments where the conveyor system is exposed to harsh chemicals or extreme temperatures.
Lagging belt pulleys not only improves traction and reduces slippage but also extends the lifespan of the pulleys and conveyor belts. It ensures that the conveyor system operates efficiently and reliably, minimizing maintenance costs and downtime. Properly applied lagging can significantly enhance the overall performance and durability of conveyor systems in various industrial applications.
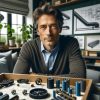
Jordan Smith, a seasoned professional with over 20 years of experience in the conveyor system industry. Jordan’s expertise lies in providing comprehensive solutions for conveyor rollers, belts, and accessories, catering to a wide range of industrial needs. From initial design and configuration to installation and meticulous troubleshooting, Jordan is adept at handling all aspects of conveyor system management. Whether you’re looking to upgrade your production line with efficient conveyor belts, require custom conveyor rollers for specific operations, or need expert advice on selecting the right conveyor accessories for your facility, Jordan is your reliable consultant. For any inquiries or assistance with conveyor system optimization, Jordan is available to share his wealth of knowledge and experience. Feel free to reach out at any time for professional guidance on all matters related to conveyor rollers, belts, and accessories.