Cost Considerations: Pricing of Impact Bed for Belt Conveyors
An impact bed for belt conveyor is an essential component in many conveyor systems, offering crucial protection against damage from heavy material impacts. By absorbing the shock and reducing the force exerted on the conveyor belt, impact beds play a vital role in prolonging the lifespan of the entire system. This protection is especially important in industries such as mining, aggregate, and cement, where heavy and abrasive materials are commonly transported. Without an impact bed for belt conveyor, these materials could cause significant wear and tear, leading to costly repairs and downtime. Hence, investing in a high-quality impact bed is a smart decision for maintaining the efficiency and durability of your conveyor system.
What is an Impact Bed for Belt Conveyors?
An impact bed for belt conveyor is a critical component designed to protect conveyor systems from the damaging effects of heavy material impacts. These impacts can occur when large, heavy, or sharp materials are dropped onto the conveyor belt, potentially causing significant wear and tear, punctures, or even complete belt failure. By absorbing and dissipating the energy from these impacts, impact beds help to maintain the integrity and longevity of both the conveyor belt and the overall conveyor system.
Definition and Purpose of an Impact Bed
An impact bed for belt conveyor is typically constructed with a series of shock-absorbing bars or blocks mounted onto a frame. These bars are made from materials such as rubber or urethane, known for their high impact resistance and durability. The primary purpose of an impact bed is to cushion the force exerted on the conveyor belt when heavy materials are loaded onto it. This cushioning effect prevents damage to the belt and reduces the risk of material spillage, which can occur when the belt is jolted by sudden impacts.
Impact beds serve multiple purposes within a conveyor system:
- Protection of the Conveyor Belt: By absorbing impact forces, impact beds prevent damage such as tears, punctures, and excessive wear on the conveyor belt, thereby extending its operational life.
- Reduction of Material Spillage: By stabilizing the belt during loading, impact beds help to maintain material on the belt, reducing spillage and the associated clean-up costs and operational disruptions.
- Minimization of Maintenance and Downtime: With less damage occurring to the belt, the need for maintenance and repairs is significantly reduced, leading to decreased downtime and increased productivity.
- Improvement of Conveyor Performance: A well-maintained conveyor system operates more efficiently, with fewer interruptions and a smoother material flow.
Explanation of Where Impact Beds are Typically Installed Within a Conveyor System
Impact beds are strategically installed at points along the conveyor system where material loading occurs, as these are the areas most susceptible to impact damage. The most common installation locations include:
Loading Zones
Loading zones are the primary areas where impact beds are installed. These zones are where materials are initially dropped onto the conveyor belt, often from considerable heights or with substantial force. By placing impact beds in these zones, the energy from the falling materials is absorbed and dissipated before it can cause damage to the belt.
Transfer Points
Transfer points are locations where materials are transferred from one conveyor belt to another or from a chute to a conveyor belt. These points are also vulnerable to impact damage due to the transfer dynamics. Installing impact beds at transfer points helps to protect the belt from the forces generated during material transfer.
Discharge Points
Although less common than loading and transfer zones, discharge points can also benefit from the installation of impact beds. At discharge points, materials are released from the belt, and the sudden unloading can cause the belt to bounce or shift, potentially leading to damage. Impact beds can help to stabilize the belt during this process, minimizing the risk of damage.
High-Impact Areas
In some conveyor systems, there may be specific areas subject to unusually high impacts due to the nature of the materials being transported or the system’s design. Identifying and reinforcing these high-impact areas with impact beds can provide additional protection and enhance the overall durability of the conveyor system.
Understanding what an impact bed for belt conveyor is and where it should be installed is crucial for optimizing the performance and longevity of conveyor systems. By providing essential protection against the damaging effects of heavy material impacts, impact beds play a vital role in maintaining the efficiency and reliability of conveyor operations. Whether installed in loading zones, transfer points, discharge points, or other high-impact areas, these components are indispensable for any system handling heavy, abrasive, or sharp materials. Investing in high-quality impact beds ensures that your conveyor system remains operational with minimal maintenance, reduced downtime, and enhanced productivity.
Types of Impact Bed for Belt Conveyor
An impact bed for belt conveyor comes in various types, each designed to meet specific needs and operational conditions. This section will explore different types of impact beds, highlighting their benefits, features, and applications.
Used Impact Bed for Belt Conveyor
Benefits of Purchasing Used Impact Beds:
- Cost Savings: Used impact beds are generally more affordable than new ones, making them an attractive option for businesses looking to save on capital expenditures.
- Immediate Availability: Often, used impact beds are readily available, reducing the lead time compared to waiting for a new unit to be manufactured.
- Environmental Impact: Purchasing used equipment can be more environmentally friendly, as it promotes recycling and reduces waste.
- Proven Performance: Used impact beds have a track record of performance, which can provide confidence in their reliability.
- Quick Installation: Used impact beds may come pre-assembled or require minimal setup, facilitating faster installation.
- Flexibility: With a variety of used options available, businesses can find impact beds that precisely match their specific requirements.
- Lower Depreciation: Used equipment typically depreciates at a slower rate than new equipment, preserving value.
- Availability of Spare Parts: Often, spare parts for used impact beds are readily available, simplifying maintenance and repairs.
Considerations When Purchasing Used Impact Beds:
- Condition: Thoroughly inspect the condition of the used impact bed to ensure it is still functional and has a reasonable lifespan remaining.
- Compatibility: Verify that the used impact bed is compatible with your existing conveyor system.
- Warranty: Check if any warranty is offered with the used impact bed, as this can provide additional peace of mind.
- History: Understanding the history of the used impact bed, including previous usage and maintenance records, can provide insights into its reliability.
- Customizations: Ensure that any customizations or modifications needed for your specific application are feasible with the used impact bed.
- Vendor Reputation: Purchase from reputable vendors to ensure quality and reliable service.
- Replacement Parts: Confirm the availability of replacement parts to support future maintenance.
- Cost-Benefit Analysis: Perform a cost-benefit analysis to determine if the savings from purchasing used outweigh the potential drawbacks.
Heavy Duty Impact Bed for Belt Conveyor
Features of Heavy Duty Impact Beds:
- Robust Construction: Built with high-strength materials to withstand heavy impacts and harsh operating conditions.
- Shock Absorption: Enhanced shock absorption capabilities to protect the conveyor belt from severe impacts.
- Durability: Designed for long-lasting performance, even in demanding environments.
- Easy Maintenance: Features that simplify maintenance tasks, such as removable bars or accessible components.
- Customizable Design: Can be tailored to fit specific conveyor system requirements and operational needs.
- High Load Capacity: Capable of handling high load capacities without compromising performance.
Applications for Heavy Duty Operations:
- Mining: Ideal for the rigorous demands of mining operations, where heavy and abrasive materials are common.
- Aggregate: Suitable for aggregate processing facilities, where impact from large rocks and materials is frequent.
- Cement: Effective in cement plants, where heavy materials are constantly loaded and transported.
- Steel: Used in steel mills to handle the impact of heavy, hot materials.
- Ports: Suitable for loading and unloading heavy materials at ports and shipping facilities.
- Quarries: Essential for quarry operations, where large stones and materials are processed.
- Recycling: Beneficial in recycling plants for handling various heavy and potentially abrasive materials.
- Construction: Used in construction sites to manage the impact of building materials and debris.
Flexco Impact Bed
Overview of Flexco’s Offerings:
Flexco is renowned for its high-quality impact beds, designed to enhance the efficiency and longevity of conveyor systems. Their impact beds are engineered with advanced technology to provide superior protection and performance.
Unique Features of Flexco Impact Beds:
- Modular Design: Flexco impact beds feature a modular design for easy installation and maintenance.
- Durable Materials: Constructed from high-quality materials that offer excellent impact resistance and durability.
- Adjustable Components: Adjustable components allow for precise alignment and fit within the conveyor system.
- Enhanced Cushioning: Advanced cushioning systems to absorb and dissipate impact energy effectively.
- Low Friction Surface: Low friction surfaces to reduce wear on the conveyor belt and enhance material flow.
- Corrosion Resistance: Components designed to resist corrosion, extending the lifespan of the impact bed.
- Versatility: Suitable for a wide range of applications across various industries.
- Comprehensive Support: Backed by Flexco’s extensive support network, ensuring reliable service and assistance.
Asgco Impact Beds
Overview of ASGCO’s Impact Beds:
ASGCO offers a range of impact beds designed to meet the diverse needs of conveyor systems across different industries. Their products are known for their innovative design and robust performance.
Benefits of ASGCO Impact Beds:
- Superior Impact Protection: ASGCO impact beds provide exceptional protection against heavy material impacts, minimizing damage to the conveyor belt.
- Reduced Maintenance Costs: With high durability and reliability, ASGCO impact beds help reduce maintenance costs and downtime.
- Enhanced Belt Stability: Improve belt stability during loading, preventing misalignment and spillage.
- Easy Installation: Designed for easy installation, with features that simplify the process and reduce setup time.
- Customizable Solutions: Can be customized to fit specific conveyor system requirements and operational conditions.
- Innovative Design: Incorporates innovative design elements that enhance performance and longevity.
- Wide Range of Applications: Suitable for use in various industries, including mining, aggregate, and recycling.
- Comprehensive Support: Supported by ASGCO’s expert team, providing assistance with selection, installation, and maintenance.
Choosing the right impact bed for belt conveyor involves understanding the different types available and their specific benefits, features, and applications. Whether opting for used impact beds, heavy-duty models, or specific brands like Flexco and ASGCO, it is crucial to consider your system’s unique needs to ensure optimal protection and performance.
Impact Bed for Belt Conveyor Price
The price of an impact bed for belt conveyor can vary widely based on several factors. Understanding these factors can help businesses make informed decisions when purchasing impact beds. This section will detail the factors influencing prices, provide a typical price range for new and used impact beds, and compare pricing across different brands.
Factors Influencing the Price of Impact Beds
- Materials Used: The type and quality of materials used in the construction of the impact bed significantly affect the price. High-end materials such as premium rubber, urethane, and reinforced steel will cost more than standard materials.
- Size of the Impact Bed: Larger impact beds, designed to accommodate wider and heavier conveyor belts, will naturally cost more due to the increased material and manufacturing requirements.
- Customization Requirements: Custom impact beds tailored to specific operational needs or unique conveyor system configurations can be more expensive due to the additional design and manufacturing efforts involved.
- Brand and Manufacturer: Reputable brands and manufacturers such as Flexco, ASGCO, and Rulmeca typically charge a premium for their products due to their proven quality and reliability.
- Load Capacity: Impact beds designed to handle higher loads and more intense impacts generally cost more due to the robust construction and enhanced shock absorption features.
- Design Complexity: More complex designs with additional features such as modular components, adjustable settings, or advanced shock-absorbing technologies will have higher prices.
- Installation Requirements: Some impact beds come with more straightforward installation processes, while others may require professional installation, adding to the overall cost.
- Shipping and Handling: The cost of shipping and handling, especially for larger or heavier impact beds, can also influence the final price.
- Warranty and After-Sales Support: Products that come with extensive warranties and after-sales support may be priced higher, reflecting the added value of customer service and assurance.
Typical Price Range for New and Used Impact Beds
New Impact Beds:
- Standard Impact Beds: $1,000 – $3,000
- Heavy-Duty Impact Beds: $3,000 – $7,000
- Customized Impact Beds: $5,000 – $10,000
Used Impact Beds:
- Standard Impact Beds: $500 – $1,500
- Heavy-Duty Impact Beds: $1,500 – $4,000
- Customized Impact Beds: $3,000 – $7,000
Comparison Between Different Brands and Their Pricing
Below is a comparison of pricing across various brands, highlighting the differences based on the types and features of impact beds offered.
Brand | Model/Type | Price Range (New) | Price Range (Used) | Key Features |
---|---|---|---|---|
Flexco | Standard Impact Bed | $1,500 - $3,500 | $700 - $1,800 | Modular design, high-quality materials, easy installation |
Flexco | Heavy-Duty Impact Bed | $4,000 - $8,000 | $2,000 - $5,000 | Enhanced shock absorption, durable construction |
ASGCO | Standard Impact Bed | $1,200 - $3,000 | $600 - $1,500 | Versatile applications, reliable performance |
ASGCO | Heavy-Duty Impact Bed | $3,500 - $7,500 | $1,800 - $4,500 | High load capacity, innovative design |
Rulmeca | Standard Impact Bed | $1,400 - $3,200 | $700 - $1,700 | Robust materials, long-lasting durability |
Rulmeca | Heavy-Duty Impact Bed | $4,200 - $8,500 | $2,200 - $5,200 | Advanced shock absorption, easy maintenance |
Martin Engineering | Standard Impact Bed | $1,600 - $3,600 | $800 - $1,900 | High-quality construction, effective impact protection |
Martin Engineering | Heavy-Duty Impact Bed | $4,500 - $9,000 | $2,300 - $5,500 | Superior durability, customizable features |
The price of an impact bed for belt conveyor varies widely based on several factors, including materials, size, customization, brand, load capacity, design complexity, installation requirements, shipping, and warranty. By understanding these factors, businesses can better assess their needs and budget for the right impact bed. The typical price range for new impact beds can be from $1,000 to $10,000, while used impact beds range from $500 to $7,000. Brands like Flexco, ASGCO, and Rulmeca offer various models with different features and price points, allowing businesses to choose based on their specific requirements and financial considerations.
Choosing the Best Impact Bed for Your Conveyor System
Selecting the best impact bed for belt conveyor systems is crucial for ensuring optimal performance and longevity. The right impact bed not only protects the conveyor belt from damage but also enhances the overall efficiency of the conveyor system. This section will discuss key considerations, the importance of compatibility with existing systems, and recommendations for various industries and use cases.
Key Considerations When Selecting an Impact Bed
- Load Requirements: Assess the weight and volume of materials that the conveyor system will handle. Heavy-duty impact beds are essential for operations involving large, heavy, or sharp materials, as they offer better shock absorption and durability.
- Environmental Conditions: Consider the operating environment of the conveyor system. Impact beds used in harsh conditions, such as mining or aggregate industries, need to be robust and resistant to abrasion, corrosion, and extreme temperatures.
- Material Type: Different materials require different impact bed features. For example, materials with high impact force need beds with superior shock absorption, while abrasive materials require impact beds with wear-resistant surfaces.
- Conveyor Belt Width: Ensure that the impact bed matches the width of the conveyor belt. An ill-fitting impact bed can cause uneven wear and potential damage to both the belt and the impact bed.
- Installation and Maintenance: Choose impact beds that are easy to install and maintain. Some designs allow for quick installation and easy access for maintenance, reducing downtime and operational costs.
- Budget: Determine your budget constraints and find a balance between cost and quality. While high-quality impact beds may have a higher upfront cost, they often result in long-term savings through reduced maintenance and longer lifespan.
- Customization Options: Depending on your specific needs, you may require customized impact beds. Look for manufacturers that offer customization to ensure the impact bed fits your conveyor system perfectly and meets all operational requirements.
- Brand and Manufacturer Reputation: Opt for impact beds from reputable brands and manufacturers known for their quality and reliability. Brands like Flexco, ASGCO, and Rulmeca have established themselves as leaders in the industry.
Importance of Compatibility with Existing Conveyor Systems
Compatibility with existing conveyor systems is a critical factor when choosing an impact bed for belt conveyor systems. Here’s why:
- Seamless Integration: An impact bed that is compatible with your existing conveyor system ensures seamless integration without the need for extensive modifications. This reduces installation time and costs.
- Operational Efficiency: Compatibility ensures that the impact bed works harmoniously with the conveyor system, maintaining smooth operation and minimizing disruptions.
- Prolonged Equipment Life: Using compatible components helps in evenly distributing the load and minimizing wear and tear on both the impact bed and the conveyor belt, thus prolonging the life of your equipment.
- Maintenance and Spare Parts: When components are compatible, sourcing spare parts and performing maintenance becomes easier and more cost-effective. It also simplifies training for maintenance personnel.
Recommendations for Various Industries and Use Cases
Different industries and use cases have unique requirements for impact beds. Here are some recommendations:
- Mining Industry: The mining industry deals with heavy and abrasive materials. Heavy-duty impact beds from brands like ASGCO are ideal due to their robust construction and superior shock absorption capabilities.
- Aggregate Industry: For operations involving stone, sand, and gravel, impact beds from Flexco are recommended. Their durable design and easy maintenance make them suitable for high-impact applications.
- Cement Industry: The cement industry requires impact beds that can withstand heavy loads and continuous operation. Rulmeca’s impact beds, known for their high durability and low maintenance, are a good fit.
- Power Plants: In power plants, where materials such as coal are transported, impact beds with flame-retardant properties are essential. Flexco’s heavy-duty impact beds are a reliable choice in this environment.
- Recycling Plants: Recycling operations often handle diverse materials, including sharp and bulky items. Impact beds that offer a combination of shock absorption and wear resistance are recommended. ASGCO’s modular impact beds are suitable for these applications.
- Food Processing: For food processing, where hygiene and cleanliness are paramount, impact beds made from food-grade materials should be used. Ensure the impact bed design facilitates easy cleaning and maintenance.
- Bulk Material Handling: For general bulk material handling, a versatile impact bed that can handle various material types and impact forces is necessary. Flexco’s range of impact beds offers solutions for different bulk material handling needs.
- Ports and Terminals: In ports and terminals, where high volumes of materials are loaded and unloaded, impact beds with high load capacity and easy installation features are beneficial. Rulmeca’s impact beds are designed to meet these demands efficiently.
By considering these factors and recommendations, you can select the best impact bed for belt conveyor systems, ensuring optimal performance, reduced maintenance costs, and prolonged equipment life.
Installation and Maintenance of Impact Bed for Belt Conveyor
Installation
Proper installation of an impact bed for belt conveyor is essential for ensuring its effectiveness in protecting the conveyor system and extending its lifespan. Here are eight detailed steps for installing an impact bed:
- Preparation: Before starting the installation, gather all necessary tools and materials, including wrenches, bolts, and alignment tools. Ensure that the conveyor system is shut down and secured to prevent any accidental movement during installation.
- Positioning the Impact Bed: Position the impact bed at the desired location, typically at the loading and transfer points where material impact is the highest. Ensure that the bed is centered over the conveyor belt and aligned with the belt’s direction of travel.
- Securing the Impact Bed: Use the provided bolts and brackets to secure the impact bed to the conveyor’s support structure. Tighten the bolts evenly to ensure the bed is firmly in place and to prevent any movement during operation.
- Aligning the Impact Bars: Check the alignment of the impact bars with the conveyor belt. The bars should be positioned perpendicular to the direction of belt travel and evenly spaced to provide uniform support.
- Adjusting the Height: Adjust the height of the impact bed to ensure it is level with the conveyor belt. The bed should be set at a height that allows the impact bars to absorb the material impact without causing undue wear on the belt.
- Securing the Skirting: Attach the conveyor skirting to the sides of the impact bed to prevent material spillage and ensure that material is directed onto the belt. The skirting should be tight enough to prevent gaps but loose enough to allow for some movement.
- Final Checks: Conduct a thorough inspection of the installation. Check all bolts and connections to ensure they are secure. Verify that the impact bed is aligned and positioned correctly and that there are no obstructions in the conveyor path.
- Test Run: After completing the installation, perform a test run of the conveyor system. Monitor the impact bed for any signs of misalignment or excessive vibration. Make any necessary adjustments to ensure smooth operation.
Maintenance
Regular maintenance is crucial for ensuring the longevity and optimal performance of an impact bed for belt conveyor systems. Here are ten maintenance tips to follow:
- Regular Inspections: Conduct regular inspections of the impact bed and surrounding components. Look for signs of wear, damage, or misalignment.
- Tighten Bolts: Check and tighten all bolts and fasteners regularly to ensure the impact bed remains securely attached to the conveyor structure.
- Replace Worn Bars: Replace any impact bars that show signs of excessive wear or damage. Worn bars can reduce the effectiveness of the impact bed and lead to conveyor belt damage.
- Check Skirting: Inspect the conveyor skirting for wear and tear. Replace any damaged sections to prevent material spillage and maintain effective material containment.
- Lubricate Moving Parts: Lubricate any moving parts of the impact bed, such as hinges or adjustable components, to prevent corrosion and ensure smooth operation.
- Monitor Belt Alignment: Regularly check the alignment of the conveyor belt. Misalignment can cause uneven wear on the impact bed and reduce its effectiveness.
- Clean the Impact Bed: Keep the impact bed clean and free of debris. Accumulated material can cause wear and reduce the impact bed’s ability to absorb shocks.
- Check for Corrosion: Inspect the impact bed for signs of corrosion, especially in environments with high humidity or exposure to corrosive materials. Treat and repair any affected areas promptly.
- Assess Impact Bed Height: Periodically check the height adjustment of the impact bed to ensure it is still aligned with the conveyor belt. Adjust as necessary to maintain optimal performance.
- Review Usage Conditions: Regularly review the operating conditions and material properties. Changes in material size, weight, or impact force may require adjustments to the impact bed or replacement with a more suitable model.
Importance of Regular Inspections and Timely Replacements
Regular inspections and timely replacements are critical for maintaining the effectiveness of an impact bed for belt conveyor systems. Here’s why:
- Preventing Downtime: Regular inspections help identify potential issues before they cause significant damage or system failure. Addressing these issues promptly can prevent costly downtime and production losses.
- Ensuring Safety: A well-maintained impact bed enhances the safety of the conveyor system by reducing the risk of belt damage and material spillage. This minimizes the risk of accidents and injuries in the workplace.
- Extending Equipment Life: Regular maintenance and timely replacement of worn components extend the life of both the impact bed and the conveyor belt. This leads to cost savings by reducing the frequency of replacements and repairs.
- Optimizing Performance: Keeping the impact bed in good condition ensures that it continues to provide effective shock absorption and protection for the conveyor belt. This optimizes the performance and efficiency of the conveyor system.
- Cost-Effective Operations: Timely replacements and proactive maintenance reduce the likelihood of major breakdowns and expensive emergency repairs. This leads to more cost-effective and predictable maintenance operations.
By following these installation and maintenance guidelines, you can ensure that your impact bed for belt conveyor systems operate efficiently, safely, and cost-effectively. Regular attention to these details will maximize the lifespan and performance of your conveyor system.
Additional Conveyor Protection Products
In addition to impact beds, several other conveyor protection products can enhance the efficiency, safety, and longevity of conveyor systems. These products work in conjunction with impact bed for belt conveyor systems to provide comprehensive protection and maintenance.
Conveyor Belt Splice Protector
Conveyor belt splice protectors are essential components that protect the integrity of the conveyor belt splice. These protectors are installed at the splice point to prevent damage and ensure the longevity of the splice. Here are some benefits and usage considerations:
- Prevents Damage: Splice protectors shield the vulnerable splice area from impact and abrasion, reducing the risk of premature wear and tear.
- Enhances Safety: By protecting the splice, these protectors help maintain the structural integrity of the conveyor belt, reducing the risk of belt failure and potential accidents.
- Works with Impact Beds: When used in conjunction with impact beds, splice protectors provide comprehensive protection for the conveyor belt, ensuring smooth and safe operation.
- Easy to Install: Most splice protectors are designed for easy installation, allowing for quick and hassle-free maintenance.
Conveyor Belt Wiper
Conveyor belt wipers play a crucial role in maintaining conveyor belt cleanliness and efficiency. These devices are installed along the conveyor belt to remove debris, moisture, and other contaminants. Here’s how they contribute to conveyor protection:
- Maintains Cleanliness: Belt wipers help remove debris and spillage from the conveyor belt, preventing buildup that can lead to belt slippage and damage.
- Enhances Efficiency: By keeping the belt clean, wipers ensure smooth and efficient operation of the conveyor system, reducing downtime and maintenance costs.
- Improves Safety: A clean conveyor belt reduces the risk of material spillage, slip hazards, and equipment damage, enhancing workplace safety.
- Different Types Available: Conveyor belt wipers come in various types, including blade wipers, brush wipers, and air knife systems, allowing for customization based on specific application requirements.
- Compatibility with Impact Beds: Like splice protectors, belt wipers can be used in conjunction with impact beds to provide comprehensive protection and maintenance for conveyor belts.
Impact bed for belt conveyor systems is essential for protecting conveyor belts from damage caused by material impact. However, to ensure optimal performance and longevity of conveyor systems, it is also crucial to consider additional protection products such as conveyor belt splice protectors and belt wipers. These products work together to enhance the efficiency, safety, and durability of conveyor systems, ultimately reducing maintenance costs and downtime.
FAQs about Impact Bed for Belt Conveyor
A conveyor impact bed is designed to support the conveyor belt optimally at the point where it receives the maximum impact of falling material. This is usually at the transfer points or the feeding point where material is dropped from a height. Impact beds are essential in absorbing the shock and dispersing the pressure, which can otherwise damage the belt and the structure. They typically consist of frames that support multiple impact bars or rollers. The design of an impact bed is crucial because it needs to maintain consistent support for the conveyor belt, manage material flow, and reduce spillage, all while withstanding the impact of heavy or abrasive materials that are being conveyed.
An impact roller, or impact idler, is installed in places along a conveyor system where the conveyor belt receives significant impacts from the falling materials. These rollers are more robust and durable than standard rollers, being specifically designed to absorb impact efficiently and protect the belt. They help in extending the lifespan of the conveyor belt by reducing the stress and wear from the loading process. The outer layer of an impact roller is typically crafted from materials such as rubber or a specialized polymer that has high shock-absorbing capabilities. They are crucial in heavy-duty applications, such as mining, quarrying, and material handling industries, where sharp, heavy materials are handled.
Impact bars are fitted at the material loading points under the conveyor belt to protect it from wear and tear caused by the contact with large, heavy, or abrasive materials. These bars are part of the conveyor’s impact bed. They combine a top layer of low friction material, often ultra-high-molecular-weight polyethylene (UHMWPE), with a cushioning layer of rubber or foam underneath. This structure helps in reducing the friction between the belt and the bars and withstands the wear while absorbing the energy of impacting materials. The use of impact bars not only prolongs the life of the conveyor belt but also stabilizes the operation, reduces maintenance costs, and minimizes product waste and spillage.
A belt bed, also known as a slider bed, is a smooth surface typically made of metal or plastic, on which the conveyor belt slides. It helps in supporting the weight and motion of the materials being transported on the belt. The belt bed includes frames which hold rollers or slider plates that facilitate the efficient movement of the conveyor belt. This part of the conveyor is pivotal as it minimizes the friction and resistance experienced as the belt moves, therefore conserving energy and reducing wear on the belt itself. Belt beds are commonly used across various industries including packaging, assembly lines, and lightweight goods manufacturing. They are particularly essential where smoother transportation of goods is required over a flat surface.
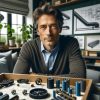
Jordan Smith, a seasoned professional with over 20 years of experience in the conveyor system industry. Jordan’s expertise lies in providing comprehensive solutions for conveyor rollers, belts, and accessories, catering to a wide range of industrial needs. From initial design and configuration to installation and meticulous troubleshooting, Jordan is adept at handling all aspects of conveyor system management. Whether you’re looking to upgrade your production line with efficient conveyor belts, require custom conveyor rollers for specific operations, or need expert advice on selecting the right conveyor accessories for your facility, Jordan is your reliable consultant. For any inquiries or assistance with conveyor system optimization, Jordan is available to share his wealth of knowledge and experience. Feel free to reach out at any time for professional guidance on all matters related to conveyor rollers, belts, and accessories.