Maximizing Efficiency with Idler Roller Assembly Solutions
In the realm of conveyor systems, the idler roller assembly plays a pivotal role, ensuring the seamless operation and longevity of the conveyor belt. These assemblies are more than just components; they are the backbone of material handling systems, facilitating the smooth and efficient transport of goods across various industries, including manufacturing, packaging, and logistics. An idler roller assembly typically comprises a series of rollers mounted on a common frame, designed to support the conveyor belt and the materials it carries. Its critical role extends beyond mere support, as it significantly reduces the wear and tear on the conveyor belt, thereby minimizing downtime and maintenance costs. By maintaining optimal belt tension and alignment, idler roller assemblies enhance the operational efficiency of conveyor systems, making them indispensable in the material handling and packaging industries. Their importance cannot be overstated, as they directly impact productivity, efficiency, and the overall success of industrial operations.
The Basics of Idler Roller Assembly
The idler roller assembly is a fundamental component in the design and operation of conveyor systems, serving multiple critical functions that ensure the efficiency and longevity of conveyor operations. Understanding the basics of idler roller assemblies involves exploring their definition, functions, and the significant roles they play in the operation of conveyor belts.
Definition and Function of Idler Rollers in Conveyor Belts
An idler roller assembly consists of a series of rollers that are strategically positioned along the length of a conveyor belt to support and guide the belt as it moves materials from one point to another. These rollers are mounted on a frame and can vary in size, material, and design based on the application.
- Supporting the Conveyor Belt: The primary function of an idler roller assembly is to provide a stable and consistent support surface for the conveyor belt, ensuring it remains in a continuous, flat position as it transports materials.
- Reducing Belt Wear: By supporting the belt, idler rollers minimize the friction and wear on the belt surface, extending its lifespan.
- Facilitating Material Transport: The smooth rotation of idler rollers allows for the effortless movement of materials along the belt, enhancing efficiency.
- Maintaining Belt Tension: Properly spaced idler roller assemblies help maintain the correct tension in the conveyor belt, preventing slippage or sagging.
- Improving Belt Tracking: Idler rollers are crucial in keeping the conveyor belt aligned and on track, preventing drift and potential operational issues.
- Absorbing Impact: In loading zones, specialized impact idler rollers absorb the shock and stress of materials being loaded onto the belt, protecting both the belt and the structure of the conveyor system.
The Significance of Idler Rollers in Supporting the Weight, Impact of Materials, and Maintaining Belt Tracking
The significance of the idler roller assembly in a conveyor system cannot be overstated, as it directly impacts the system’s efficiency, safety, and operational costs.
- Weight Distribution: Idler rollers evenly distribute the weight of materials across the width of the belt, preventing undue stress and strain on the conveyor structure.
- Impact Resistance: Specially designed impact idler rollers in loading areas help dissipate the force of falling materials, reducing damage to the belt and supporting structure.
- Preventing Material Spillage: By maintaining proper belt alignment, idler rollers help prevent material spillage at the edges of the belt, reducing waste and cleanup costs.
- Enhancing Operational Safety: A well-supported and aligned belt, thanks to idler roller assemblies, minimizes the risk of belt-related accidents and injuries.
- Optimizing Material Flow: The smooth operation of idler rollers contributes to a consistent and reliable flow of materials, preventing bottlenecks and downtime.
- Facilitating Maintenance and Repairs: Modular idler roller assemblies allow for easy replacement and maintenance, minimizing operational disruptions and maintenance time.
The idler roller assembly is a key element in the functionality and efficiency of conveyor systems, playing an indispensable role in supporting the conveyor belt, absorbing impacts, and ensuring the smooth and effective transport of materials.
Types of Idler Roller Assemblies
In the diverse world of conveyor systems, the idler roller assembly plays a critical role in maintaining the efficiency and longevity of the conveyor belt’s operation. There are several types of idler roller assemblies, each designed to meet specific operational needs and challenges. Understanding these types can help in selecting the right idler roller assembly for a particular application.
Plain Idler Rollers
Plain idler rollers are the most basic and widely used type of idler roller assembly. They consist of a simple cylindrical shape and are primarily used to support the weight of the conveyor belt and the materials being transported. The durability and performance of plain idler rollers are influenced by factors such as the belt conveyor belt material, roller diameter, bearing type, and seal type. Applications of plain idler rollers include:
- Light to Medium Duty Conveying: Ideal for applications where the load is not excessively heavy.
- Flat Belt Conveyors: Commonly used in packaging and assembly lines.
- Material Sorting Systems: Provides stable support for materials as they are sorted.
- Agricultural Equipment: Used in conveyors for transporting grain or other agricultural products.
- Mining Operations: Supports the conveyor belt in various stages of mineral processing.
- General Manufacturing: Utilized across a range of manufacturing environments for material handling.
Tapered Idler Rollers
Tapered idler rollers are designed with a slight conical shape, which assists in maintaining the conveyor belt’s alignment, preventing it from drifting off its intended path. They are particularly useful in:
- Curved Sections of Conveyors: Helps guide the belt around curves.
- Areas Prone to Misalignment: Reduces the risk of belt slippage and wear.
- Heavy-Duty Applications: Supports and aligns belts under heavy loads.
- Inclined Conveyors: Assists in belt tracking on slopes.
- Packaging Lines: Ensures smooth operation and alignment in critical sections.
- Automated Warehouses: Keeps conveyor systems running smoothly and efficiently.
Rubber-Coated Idler Rollers
Rubber-coated idler rollers feature a layer of rubber on the exterior, enhancing their durability and providing additional grip. Benefits include:
- Noise Reduction: The rubber coating absorbs operational noise.
- Increased Friction: Prevents slippage between the belt and the roller.
- Shock Absorption: Reduces the impact on the conveyor system.
- Corrosion Resistance: Protects the roller from moisture and chemicals.
- Wear Resistance: Extends the lifespan of the roller assembly.
- Vibration Damping: Minimizes vibrations, protecting sensitive materials.
Rubber Disc Idler Rollers
Rubber disc idler rollers have rubber discs attached along the roller’s length, focusing on supporting the conveyor belt’s edges and managing carryback. They are essential for:
- Preventing Belt Damage: Protects the edges of the belt from wear.
- Reducing Material Spillage: Helps keep materials on the conveyor.
- Facilitating Easy Cleaning: The discs help dislodge stuck materials.
- Enhancing Grip: Improves traction between the belt and roller.
- Minimizing Belt Mistracking: Keeps the belt aligned through its course.
- Improving Conveyor Efficiency: Ensures smooth operation of the conveyor system.
Rubber Screw and Steel Screw Idler Rollers
Rubber screw and steel screw idler rollers are characterized by their helical screw patterns, which are designed to aid in cleaning the belt and maintaining its alignment. Specific applications include:
- Material Cleaning: The screw pattern helps remove debris from the belt.
- Heavy-Duty Operations: Both types are suited for environments with high wear and tear.
- Wet or Sticky Materials: Rubber screw rollers are particularly effective in handling these materials.
- High-Temperature Applications: Steel screw rollers can withstand higher temperatures.
- Mining and Quarrying: Ideal for conveying raw extracted materials.
- Recycling Plants: Helps in the efficient transport and separation of recyclables.
Each type of idler roller assembly offers unique benefits and is suited to specific applications within conveyor systems. Selecting the appropriate idler roller assembly is crucial for optimizing conveyor performance, extending the lifespan of the conveyor belt, and ensuring the smooth and efficient transport of materials.
Selecting the Right Idler Roller Assembly
Choosing the appropriate idler roller assembly for your conveyor system is a critical decision that can significantly impact the efficiency, durability, and cost-effectiveness of your material handling operations. Several key factors must be considered to ensure that the selected idler roller assembly meets the specific requirements of your application.
Factors to Consider When Selecting an Idler Roller Assembly
- Material Type: The nature of the materials being conveyed (e.g., abrasive materials like sand or gentle products like grains) directly influences the choice of idler roller assembly to prevent wear and tear.
- Specific Gravity: The weight of the material being transported affects the required strength and durability of the idler rollers. Heavier materials may necessitate stronger, more robust assemblies.
- Lump Size: The size of the materials being conveyed can impact the type of idler roller assembly needed. Larger lumps might require idler rollers with higher impact resistance.
- Belt Speed: High-speed conveyor systems may need idler rollers designed to minimize vibration and noise.
- Operating Environment: Conditions such as temperature, humidity, and exposure to chemicals or UV light can dictate the material and design of the idler roller assembly.
- Load Capacity: The expected load on the conveyor belt determines the required load-bearing capacity of the idler rollers to ensure they do not deform or fail under pressure.
The Importance of Consistency in Idler Standards for Optimal Conveyor Performance
- Uniform Wear: Consistent idler standards across a conveyor system ensure uniform wear of the idler rollers, prolonging their lifespan and reducing maintenance costs.
- Reduced Belt Mistracking: Uniform idler roller assemblies contribute to consistent belt alignment, minimizing the risk of belt mistracking and associated downtime.
- Efficient Power Use: Consistency in idler design helps maintain optimal belt tension and alignment, reducing the power required to operate the conveyor system.
- Simplified Maintenance: Standardizing idler roller assemblies across the conveyor system simplifies maintenance procedures and inventory management, as replacement parts are interchangeable.
- Improved Safety: Consistent use of appropriate idler roller assemblies reduces the risk of conveyor belt failures, enhancing operational safety.
- Enhanced System Reliability: A conveyor system outfitted with consistently specified idler roller assemblies operates more reliably, with fewer interruptions due to component incompatibility or failure.
Selecting the right idler roller assembly involves a careful analysis of the materials being conveyed, the operational environment, and the specific requirements of the conveyor system. By considering these factors and ensuring consistency in idler standards, businesses can optimize the performance of their conveyor systems, extend the life of their components, and achieve a higher return on investment.
DYNA Engineering and Eastey: Innovations in Idler Roller Assembliy
In the field of conveyor system components, two companies stand out for their innovative approaches to idler roller assembly design and manufacturing: DYNA Engineering and Eastey. Both companies have made significant strides in enhancing the efficiency, durability, and cost-effectiveness of idler roller assemblies, setting new standards in the industry.
DYNA Engineering’s Approach to Idler Roller Assembly Design
DYNA Engineering is renowned for its commitment to producing idler roller assemblies that offer lifelong durability and reduced operating costs. Their innovative approach is evident in several key aspects:
- Material Selection: DYNA Engineering uses high-grade materials resistant to wear, corrosion, and impact, ensuring the idler roller assemblies can withstand harsh operating environments.
- Precision Engineering: Each idler roller assembly is designed with precision to ensure optimal fit and performance, reducing the risk of malfunction and extending the lifespan of the conveyor system.
- Innovative Sealing Technology: To protect against dust, water, and other contaminants, DYNA incorporates advanced sealing technologies, enhancing the durability of the bearings and rollers.
- Energy Efficiency: By focusing on reducing the rolling resistance of their idler roller assemblies, DYNA Engineering helps clients save on energy costs associated with conveyor operation.
- Customization Options: Understanding that each conveyor system has unique requirements, DYNA offers customized idler roller assemblies tailored to specific operational needs.
- Sustainability Focus: DYNA Engineering designs its idler roller assemblies with sustainability in mind, using recyclable materials and energy-efficient manufacturing processes to minimize environmental impact.
Introduction to Eastey’s Replacement Side Belt Idler Roller Assembly (IR-2AS) 5000141
Eastey’s contribution to the advancement of idler roller assembly technology is exemplified by their Replacement Side Belt Idler Roller Assembly (IR-2AS) 5000141. This product stands out for its quality, reliability, and ease of integration into existing conveyor systems. Key features and purchasing information include:
- Durability: The IR-2AS is built to last, using robust materials that ensure long-term reliability even in demanding operational conditions.
- Compatibility: Designed for versatility, this idler roller assembly is compatible with a wide range of conveyor systems, making it an ideal choice for businesses looking to upgrade their existing equipment.
- Ease of Installation: The IR-2AS model is engineered for straightforward installation, allowing for quick and efficient replacement without significant downtime.
- Maintenance-Friendly Design: With maintenance in mind, Eastey’s idler roller assembly allows for easy access to components that may require inspection or replacement, reducing overall maintenance costs.
- Cost-Effectiveness: Priced competitively, the IR-2AS offers an excellent balance of quality and affordability, providing value to businesses seeking to optimize their conveyor operations without overspending.
- Purchasing Information: Available directly from Eastey or through authorized distributors, the IR-2AS can be easily ordered with detailed product specifications and support available to ensure customer satisfaction.
Both DYNA Engineering and Eastey have demonstrated a commitment to innovation in idler roller assembly design and manufacturing. Their products not only enhance the performance and reliability of conveyor systems but also contribute to operational efficiency and cost reduction, benefiting industries worldwide.
Installation and Maintenance Tips for Idler Roller Assembly
Ensuring the efficiency and longevity of your conveyor system starts with the proper installation and maintenance of the idler roller assembly. Following best practices for installation and adhering to a regular maintenance schedule can significantly extend the life of your idler rollers and, by extension, your entire conveyor system.
Best Practices for Installing Idler Roller Assemblies
- Alignment Precision: Ensure that the idler roller assembly is perfectly aligned with the conveyor frame. Misalignment can cause uneven wear, belt mistracking, and increased energy consumption.
- Spacing Consideration: Follow the manufacturer’s recommendations for spacing between each idler roller assembly. Proper spacing supports effective weight distribution and optimal belt support.
- Secure Mounting: Verify that all components of the idler roller assembly are securely mounted to prevent any movement that could lead to wear or operational inefficiency.
- Belt Tension: After installation, check the conveyor belt tension to ensure it is neither too tight nor too loose. Incorrect tension can strain the idler rollers and the belt.
- Test Run: Conduct a test run without load to observe the operation of the idler roller assembly. Look for any signs of misalignment or unusual noises that could indicate installation issues.
- Load Testing: Finally, perform a test run with a load to ensure the conveyor system operates smoothly under operational conditions. Adjust as necessary for optimal performance.
Maintenance Tips to Keep Your Idler Roller Assemblies in Top Condition
- Regular Inspections: Schedule regular inspections of the idler roller assembly to identify wear, damage, or alignment issues early. Early detection can prevent more significant problems down the line.
- Lubrication: Ensure that all moving parts of the idler roller assembly are adequately lubricated according to the manufacturer’s specifications. Proper lubrication reduces friction, wear, and energy consumption.
- Cleaning: Keep the idler rollers and the surrounding area clean from debris and material build-up. Accumulation of materials can affect the rollers’ operation and potentially damage the conveyor belt.
- Replacement of Worn Parts: Replace any worn or damaged parts of the idler roller assembly immediately. Using damaged components can lead to further damage and operational inefficiency.
- Belt Alignment Checks: Regularly check the alignment of the conveyor belt. Misalignment can cause uneven wear on the idler rollers and the belt itself.
- Record Keeping: Maintain detailed records of all maintenance activities, including inspections, replacements, and adjustments. This documentation can help identify recurring issues and inform future maintenance schedules.
By following these installation and maintenance tips for your idler roller assembly, you can ensure the efficient and reliable operation of your conveyor system. Proper care and attention to the idler rollers not only extend their service life but also contribute to the overall performance and safety of the conveyor system.
FAQs About Idler Roller Assembly
The primary function of an idler roller is to support, guide, and adjust the tension of a belt, chain, or other flexible media within a system. By doing so, idler rollers help to ensure the efficient and smooth operation of the system, reduce the wear and tear on the belt and other components, and extend the overall lifespan of the system. In conveyor systems, for example, idler rollers are strategically placed along the length of the conveyor to support the weight of the materials being transported, prevent sagging of the belt, and facilitate the proper alignment and tracking of the belt. In automotive applications, idler rollers may be used to guide timing belts or chains, ensuring precise timing and operation of the engine’s moving parts.
The terms “roller” and “idler” are often used interchangeably, but they can refer to distinct components depending on the context of their application. Generally, a roller is a broad term that describes any cylindrical component that rotates around an axis to facilitate movement or support a load. Rollers can be powered (drive rollers) or unpowered. An idler, on the other hand, specifically refers to a type of unpowered roller that is used to guide, support, or adjust the tension of a moving belt or chain. The key difference lies in the function: while all idlers are rollers, not all rollers are idlers. Idlers do not directly drive or move the belt but play a supportive role in the system’s operation.
In a car, an idler roller, often referred to as an idler pulley or idler wheel, is a component of the engine’s belt drive system. It serves to guide and tension the drive belts, such as the serpentine belt, timing belt, or timing chain, ensuring they remain aligned and properly tensioned during operation. This is crucial for the smooth and efficient transfer of power from the engine to various accessories, such as the alternator, power steering pump, water pump, and air conditioning compressor. By maintaining the correct tension and alignment, idler rollers help prevent slippage and wear on the belts and pulleys, contributing to the longevity and reliability of the vehicle’s engine and accessory systems.
In a conveyor belt system, idlers are cylindrical rollers that support the conveyor belt and the materials being transported on it. They are mounted on a frame and spaced at intervals along the length of the conveyor. Idlers play several critical roles: they support the weight of the belt and the cargo it carries, help maintain the appropriate tension and alignment of the belt, and reduce friction and wear on the belt. There are different types of idlers designed for specific functions within the conveyor system, including carrying idlers that support the loaded side of the belt, return idlers that support the belt on its return journey, and impact idlers that absorb the shock of loading materials onto the conveyor. The proper selection, placement, and maintenance of idlers are essential for the efficient and reliable operation of a conveyor belt system.
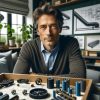
Jordan Smith, a seasoned professional with over 20 years of experience in the conveyor system industry. Jordan’s expertise lies in providing comprehensive solutions for conveyor rollers, belts, and accessories, catering to a wide range of industrial needs. From initial design and configuration to installation and meticulous troubleshooting, Jordan is adept at handling all aspects of conveyor system management. Whether you’re looking to upgrade your production line with efficient conveyor belts, require custom conveyor rollers for specific operations, or need expert advice on selecting the right conveyor accessories for your facility, Jordan is your reliable consultant. For any inquiries or assistance with conveyor system optimization, Jordan is available to share his wealth of knowledge and experience. Feel free to reach out at any time for professional guidance on all matters related to conveyor rollers, belts, and accessories.