Gravity Roller Conveyor Manufacturers: A Comparative Guide
Gravity roller conveyors are essential components in the world of material handling and logistics, providing an efficient, low-cost solution for moving goods across warehouses, distribution centers, and production lines. These systems leverage the force of gravity to propel items forward, minimizing the need for manual labor or electrical power. The market boasts a wide array of gravity roller conveyor manufacturers, each offering unique designs and features tailored to meet diverse operational needs. This blog post aims to shed light on these manufacturers, delving into the critical design considerations they take into account and the variety of options they provide to businesses. By understanding the landscape of gravity roller conveyor manufacturers, companies can make informed decisions that enhance their operations, improve workflow efficiency, and ultimately contribute to their bottom line.
To Understand Gravity Roller Conveyors by Gravity Roller Conveyor Manufacturers
Gravity roller conveyors, engineered and produced by a diverse array of gravity roller conveyor manufacturers, stand as a testament to the ingenuity in the field of material handling and logistics. These systems, through their simplicity and efficiency, have become indispensable in the seamless operation of various industrial environments. Below, we explore the foundational aspects that define gravity roller conveyors and the mechanics that drive their functionality, as well as the distinct advantages they offer to industrial settings.
Definition and Basic Mechanics
At the heart of many material handling systems lie gravity roller conveyors, a solution provided by numerous gravity roller conveyor manufacturers to facilitate the effortless transport of goods. These conveyors are characterized by:
- Simplicity in Design: Comprising a series of cylindrical rollers affixed to a frame, gravity roller conveyors provide a straightforward path for goods to traverse.
- Gravity-Powered Movement: Capitalizing on the natural force of gravity, these conveyors are typically inclined at a strategic angle, allowing items to move from a higher elevation to a lower one without the need for external power.
- Adaptability: Thanks to the versatility in design options offered by gravity roller conveyor manufacturers, these systems can accommodate a wide variety of goods, from lightweight packages to heavier industrial components.
- Modular Nature: The modular design ethos embraced by manufacturers allows for easy customization and scalability, catering to the specific needs of any operation.
- Maintenance Efficiency: The mechanical simplicity of gravity roller conveyors translates to lower maintenance requirements, ensuring long-term operational reliability.
- Seamless Integration: These systems can be effortlessly incorporated into existing material handling setups, including those that are powered, to enhance overall efficiency.
Advantages of Using Gravity Roller Conveyors in Industrial Settings
The adoption of gravity roller conveyors across various sectors is not without reason. Engineered for performance and reliability, these systems, as developed by leading gravity roller conveyor manufacturers, offer a multitude of benefits:
- Cost Efficiency: They represent one of the most cost-effective methods for transporting goods, significantly reducing the need for powered assistance and, by extension, operational expenses.
- Environmental Friendliness: The passive nature of gravity conveyors means they operate without consuming electricity, aligning with eco-friendly operational goals.
- Installation Simplicity: Designed for ease, these conveyors can be quickly installed, minimizing downtime and facilitating immediate improvements in material handling processes.
- Enhanced Safety: The absence of electrical components not only reduces maintenance concerns but also minimizes the risk of accidents, promoting a safer workplace.
- Operational Flexibility: Gravity roller conveyors are adept at handling a broad spectrum of materials, making them suitable for a wide range of industrial applications.
- Scalable Solutions: The ability to easily expand or modify the conveyor layout ensures that growing operational demands can be met with minimal fuss.
- Productivity Gains: The efficient movement of goods facilitated by these conveyors can significantly boost throughput and operational speed.
- Built to Last: Durability is a hallmark of systems provided by gravity roller conveyor manufacturers, with many models designed to withstand intensive use.
- Customizable Features: Recognizing the varied needs of different industries, manufacturers offer customizable conveyor solutions, including adjustable conveyor heights and lengths to suit specific operational requirements.
Through the innovative designs and robust manufacturing standards upheld by gravity roller conveyor manufacturers, these conveyors have cemented their role as a cornerstone of efficient, reliable, and cost-effective material handling in industrial settings worldwide.
Key Gravity Roller Conveyor Manufacturers
The landscape of gravity roller conveyor manufacturers is diverse, with several key players leading the industry through innovation, quality, and customer service. These manufacturers have developed a range of solutions to meet the varied needs of material handling across different sectors. Below, we explore some of the key manufacturers of gravity roller conveyors, highlighting their contributions and product offerings.
Ashland Conveyor
Ashland Conveyor stands out among gravity roller conveyor manufacturers for its comprehensive range of conveyor solutions and accessories. Known for its customer-centric approach, Ashland Conveyor offers products designed to enhance efficiency and productivity in material handling operations.
- Wide Product Range: Offers a variety of gravity roller conveyors, including the innovative FlexExtend Skatewheel Conveyor.
- Customization Options: Provides an extensive selection of rollers, catering to different industry needs.
- Customer-Oriented Solutions: Focuses on delivering solutions that meet specific customer requirements.
- Extensive Product Selection Guide: Helps customers choose the right conveyor solutions for their operations.
- Durability and Quality: Known for manufacturing conveyors that are both durable and reliable.
- Innovative Designs: Continuously introduces new and improved conveyor designs to the market.
- Support and Service: Offers excellent customer support and after-sales service.
Dorner Conveyors
Dorner Conveyors is renowned for its high-quality, customizable conveyor systems, making it a leading name among gravity roller conveyor manufacturers. Dorner’s solutions are tailored to meet the unique demands of various applications, ensuring optimal efficiency and productivity.
- Customizable Solutions: Specializes in designing gravity roller conveyors that can be tailored to specific operational needs.
- Application-Specific Designs: Offers designs that are specifically suited to the needs of different industries and applications.
- Integration Capabilities: Excels in integrating gravity and powered conveyors for comprehensive material handling solutions.
- Innovative Technology: Incorporates the latest technologies in its conveyor designs for enhanced performance.
- Quality and Reliability: Products are known for their quality, reliability, and long service life.
- Customer Support: Provides exceptional customer support and technical assistance.
- Global Presence: Has a strong global presence, serving customers worldwide.
Hytrol
Hytrol is a key player in the gravity conveyor market, recognized for its cost-effective and easily installed conveyor solutions. Hytrol’s conveyors are designed to be durable and versatile, meeting the needs of various material handling applications.
- Cost-Effective Solutions: Offers a range of gravity conveyor options that are economical and efficient.
- Ease of Installation: Designs conveyors that are easy to install, reducing downtime and installation costs.
- Durable Construction: Known for the durability and versatility of its conveyor solutions.
- Wide Range of Options: Provides a broad selection of gravity conveyors to suit different applications.
- Innovative Design: Continuously innovates to improve conveyor efficiency and functionality.
- Excellent Customer Service: Offers reliable customer service and support.
- Industry Expertise: Brings years of industry expertise to its conveyor solutions, ensuring high-quality and performance.
Conveyor Dynamics Corporation
Conveyor Dynamics Corporation is renowned for its engineering excellence and the manufacturing of heavy-duty gravity roller conveyors. Their solutions are designed to withstand the most demanding industrial environments, making them a preferred choice for heavy-duty applications.
- Heavy-Duty Focus: Specializes in conveyors capable of handling heavy loads with exceptional durability.
- Engineering Excellence: Utilizes advanced engineering techniques to design superior gravity roller conveyors.
- Custom Solutions: Offers custom-designed conveyor systems to meet unique operational challenges.
- Robust Construction: Products feature robust construction for extended longevity in harsh conditions.
- Innovative Features: Incorporates innovative features to enhance performance and ease of use.
- Comprehensive Support: Provides comprehensive technical support and customer service.
- Global Reach: Serves a global market, with solutions in use in numerous industries worldwide.
Interroll Group
Interroll Group is a global leader among gravity roller conveyor manufacturers, offering a wide range of conveyor solutions that cater to various sectors. Known for their innovation and energy-efficient designs, Interroll’s conveyors are crafted to boost productivity and sustainability.
- Energy Efficiency: Leads in the design of energy-efficient gravity roller conveyors.
- Global Presence: Boasts a strong global presence, serving customers around the world.
- Wide Product Range: Offers an extensive range of conveyor solutions, including modular conveyor platforms.
- Innovation Leader: Continuously innovates to provide advanced material handling solutions.
- Sustainability Focus: Emphasizes sustainable and eco-friendly manufacturing practices.
- High-Quality Standards: Maintains high-quality standards across all products and services.
- Customer-Centric Approach: Dedicated to understanding and meeting the needs of its customers.
Ultimation Industries
Ultimation Industries is a key figure in the gravity roller conveyor market, known for its versatile and cost-effective conveyor solutions. Their products are designed to improve efficiency in a wide range of industrial, retail, and commercial applications.
- Versatility: Offers a wide range of gravity roller conveyors suitable for various applications.
- Cost-Effectiveness: Focuses on providing affordable conveyor solutions without compromising quality.
- Ease of Installation: Designs conveyors for quick and easy installation, enhancing operational efficiency.
- Customization Options: Provides extensive customization options to meet specific customer requirements.
- Innovative Design: Employs innovative design principles to enhance conveyor functionality and performance.
- Quality Assurance: Committed to quality, ensuring all products meet strict standards.
- Exceptional Service: Offers outstanding customer service and support throughout the purchase and installation process.
These key manufacturers of gravity roller conveyors have significantly contributed to the advancement of material handling technologies. Their commitment to quality, innovation, and customer satisfaction has made them leaders in the industry, offering a range of solutions to meet the diverse needs of their clients.
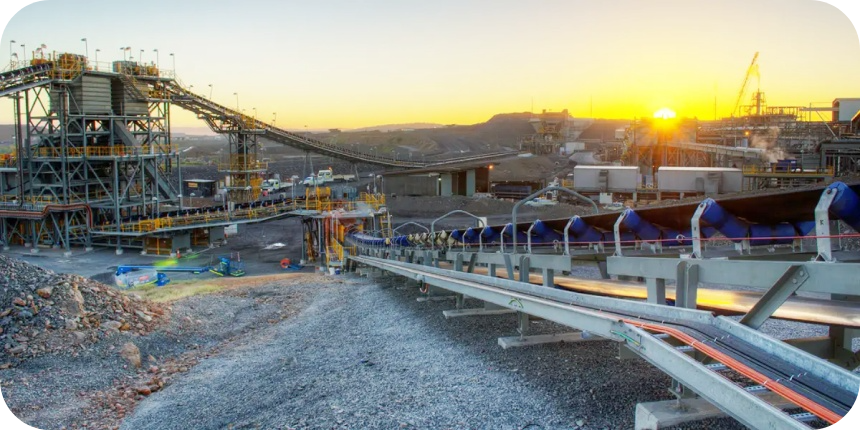
Considerations When Choosing a Gravity Roller Conveyor by Gravity Roller Conveyor Manufacturers
When selecting a gravity roller conveyor, diving deeper into the considerations can help ensure that the investment enhances operational efficiency and aligns with business objectives. Here are expanded insights into each factor, drawing from the expertise of leading gravity roller conveyor manufacturers:
- Tailored Solutions: Customization is key to addressing unique operational challenges. Look for manufacturers that can adjust conveyor dimensions, roller spacing, and material types to match your specific product handling requirements, ensuring optimal performance and minimal product damage.
- Robust Systems for Heavy-Duty Use: Heavy-duty conveyors are engineered to handle larger loads and withstand the rigors of industrial environments. Evaluate the construction materials, roller diameter, and bearing types, as these elements significantly impact the conveyor’s ability to manage heavy or bulky items over time.
- Cost Analysis for Budgeting: Beyond the initial purchase price, consider the total cost of ownership, which includes maintenance, repairs, and potential upgrades. A higher upfront cost might be justified by lower long-term expenses and greater reliability. Comparing new and used options requires assessing the condition and longevity of pre-owned equipment versus the benefits of the latest technology and warranties offered with new equipment.
- Compatibility with Load and Product Type: The diversity of goods handled necessitates a conveyor system capable of accommodating various sizes, shapes, and weights. Assess the need for specialized rollers or coatings to improve grip and reduce slippage for irregularly shaped items or those prone to shifting during transport.
- Facility Fit and Space Optimization: Space constraints demand innovative solutions. Consider conveyors that offer flexible configurations, such as telescoping or bendable sections, to navigate tight spaces or change direction efficiently. The ability to modify the conveyor layout as needs evolve is a valuable feature.
- Seamless Integration with Existing Systems: The new conveyor should complement and enhance your current setup. This might involve compatibility with automated systems, synchronized operation speeds, or the ability to integrate with digital tracking and management tools for a cohesive workflow.
- Ease of Maintenance and Durability: Durable conveyors reduce downtime and maintenance costs. Look for designs that facilitate easy access to components for cleaning and repairs, as well as manufacturers that provide comprehensive guides and support for routine maintenance.
- Reliable Supplier and Manufacturer Reputation: Research manufacturer track records, seeking out those with a history of innovation, quality craftsmanship, and positive customer feedback. A strong reputation in the industry often translates to reliable products and services.
- Environmental Considerations for Sustainability: Environmentally conscious operations are increasingly important. Opt for conveyors made from recyclable materials, those that operate efficiently with minimal energy consumption, and manufacturers committed to sustainable practices.
Benefits of Sourcing from Gravity Roller Conveyor Manufacturers in the USA
Choosing American-made gravity roller conveyors brings additional benefits, reinforcing the value of investing in domestic manufacturing:
- Shorter Lead Times: Domestic production typically means shorter shipping distances, resulting in faster delivery times that can keep projects on schedule.
- Simplified Communication: Engaging with local manufacturers eliminates language barriers and time zone differences, facilitating clearer communication and quicker responses to inquiries or issues.
- Comprehensive Support and Service: Proximity to manufacturers enhances the availability of after-sales support, including on-site maintenance, training, and easy access to replacement parts, ensuring your conveyor system remains operational with minimal disruption.
- Adherence to Quality and Safety Standards: Products manufactured in the USA are subject to stringent quality controls and safety standards, offering peace of mind that the equipment is safe and reliable.
- Supporting the Local Economy: Investing in domestic products supports American jobs and contributes to the national economy, fostering growth and innovation within the industry.
- Logistical Convenience: Closer geographical proximity simplifies logistics, potentially reducing shipping costs and making it easier to address any transportation challenges that arise.
In-depth consideration of these factors, coupled with the advantages of partnering with domestic manufacturers, positions businesses to make informed decisions that optimize their material handling operations with gravity roller conveyors.
Certainly, let’s refine the structure with introductory remarks for each section before delving into the detailed points.
Innovative Features and Trends by Gravity Roller Conveyor Manufacturers
In the dynamic world of material handling, gravity roller conveyor manufacturers are not just keeping pace with technological advancements; they are leading the charge. By integrating innovative features into their designs and aligning with the latest trends, these manufacturers ensure that gravity roller conveyors remain indispensable tools in the efficient movement of goods across various industries. Below, we explore the cutting-edge features and significant trends that are shaping the future of gravity roller conveyors.
Innovative Features in Gravity Roller Conveyor Design
The design of gravity roller conveyors has evolved significantly, thanks to continuous innovation by manufacturers. These enhancements not only improve the functionality and efficiency of conveyors but also address specific operational challenges, making them more adaptable to a wide range of industrial applications. Here are some of the standout features:
- Adjustable Legs: Modern conveyors come with legs that can be adjusted in height, allowing for ergonomic customization to suit different operators and processes.
- Modular Sections: Flexibility is key in today’s dynamic production environments. Modular conveyor sections can be quickly reassembled, expanded, or modified, offering unparalleled adaptability.
- Special Coatings for Rollers: Rollers now feature special coatings that minimize noise and increase traction, enhancing the handling of sensitive or delicate items.
- Integrated Scales: Incorporating scales directly into conveyor sections streamlines the weighing process, facilitating accurate shipping and inventory management without disrupting the flow of goods.
- Tool-Free Assembly: The latest designs promote ease of assembly and disassembly, often requiring no tools, which significantly reduces setup times and facilitates rapid reconfiguration.
- Energy-Efficient Drives: For sections where powered assistance is necessary, energy-efficient drives reduce electricity consumption, lowering operational costs and environmental impact.
- Smart Rollers: The introduction of rollers equipped with sensors offers real-time monitoring capabilities, from tracking loads to predictive maintenance alerts.
- Impact Zones: Enhanced with cushioning materials, these zones are designed to absorb shocks, protecting both the conveyor system and the products from damage.
Trends Affecting the Gravity Roller Conveyor Market
The gravity roller conveyor market is influenced by several key trends, reflecting broader shifts in industry, technology, and societal expectations. These trends not only guide the development of new features but also shape the strategic direction of manufacturers in the sector:
- Integration of Smart Technology: The adoption of IoT and smart sensors in conveyor systems is revolutionizing how operations are monitored, controlled, and optimized.
- Eco-Friendly Materials: There’s a growing emphasis on sustainability, with manufacturers increasingly turning to recycled or eco-friendly materials in conveyor construction.
- Customization and Flexibility: The demand for conveyors that can be tailored to specific operational needs is rising, driving manufacturers to offer more customizable and flexible solutions.
- Safety Enhancements: Innovations in safety features aim to protect workers and reduce the risk of accidents, becoming a standard expectation in conveyor design.
- Increased Automation: As automation becomes more prevalent, conveyors are being designed to seamlessly integrate with automated systems, including robotics and AGVs.
- Data Analytics and AI: Leveraging advanced analytics and artificial intelligence, manufacturers are optimizing conveyor performance and predictive maintenance capabilities.
- Lean Manufacturing Compatibility: Conveyors are evolving to support lean manufacturing principles, helping businesses to minimize waste and enhance operational efficiency.
- Global Supply Chain Resilience: In response to recent challenges, there is a focused effort on building more resilient supply chains for conveyor components to ensure reliability and mitigate disruptions.
Through these innovative features and by staying ahead of market trends, gravity roller conveyor manufacturers are ensuring that their products continue to play a critical role in the efficient and effective movement of goods across industries.
Case Studies and Success Stories by Gravity Roller Conveyor Manufacturers
The practical application of gravity roller conveyors in various industries has led to numerous success stories and case studies that highlight the efficiency, adaptability, and cost-effectiveness of these systems. Here, we explore several instances where businesses have successfully integrated solutions from leading gravity roller conveyor manufacturers, showcasing the transformative impact on their operations.
- E-Commerce Fulfillment Center: A major e-commerce company collaborated with a renowned gravity roller conveyor manufacturer to overhaul its fulfillment center. The integration of modular gravity conveyors allowed for rapid sorting and dispatching of orders, significantly reducing processing times and increasing throughput by 40%.
- Automotive Parts Manufacturer: Facing challenges with parts movement across its assembly line, an automotive parts manufacturer implemented heavy-duty gravity roller conveyors. The solution provided a robust, low-maintenance system that enhanced production flow and reduced manual handling requirements.
- Food and Beverage Distribution: A food and beverage distributor implemented a gravity roller conveyor system to streamline its packaging and distribution process. The custom-designed system, featuring special coatings on rollers for hygiene, improved the handling of fragile goods and increased operational efficiency by 30%.
- Retail Warehouse Optimization: A retail giant worked with gravity roller conveyor manufacturers to optimize its warehouse operations. By installing adjustable and modular conveyors, the company was able to adapt to seasonal demand fluctuations, improving space utilization and worker productivity.
- Pharmaceutical Logistics: In the pharmaceutical industry, where precision and handling care are paramount, a logistics company introduced gravity roller conveyors with integrated scales and smart technology. This innovation enabled precise tracking and weighing of sensitive products, ensuring compliance and safety.
- Manufacturing Facility Upgrade: A manufacturing facility facing bottlenecks in its production line integrated a series of energy-efficient, smart gravity roller conveyors. The new system facilitated a smoother product flow, reduced energy costs, and provided valuable data insights for continuous improvement.
- Airport Baggage Handling System: An airport upgraded its baggage handling system with heavy-duty gravity roller conveyors designed to withstand high volumes and heavy loads. The upgrade resulted in a more reliable, efficient system that enhanced passenger satisfaction through faster, more secure baggage processing.
- Agricultural Cooperative: An agricultural cooperative needing to handle and sort various produce types without damage implemented customizable gravity roller conveyors. The system’s flexibility and gentle handling increased sorting efficiency and reduced product damage, leading to higher market prices for their goods.
These case studies and success stories from businesses across different sectors demonstrate the versatility and effectiveness of gravity roller conveyors. By partnering with leading gravity roller conveyor manufacturers, these organizations have achieved significant operational improvements, showcasing the critical role these systems play in modern material handling and logistics.
Ready to enhance your conveyor system? Contact us here!
FAQs about Gravity Roller Conveyor Manufacturers
Gravity roller conveyor systems are essential components in material handling, facilitating the movement of goods across various distances without the use of power. These systems come in several types, each designed to meet specific operational needs and applications. The most common types include:
Straight Roller Conveyors: These are the standard conveyor systems used to transport items in a straight line over short to medium distances. They are versatile and can be used in a variety of settings.
Curved Roller Conveyors: Designed to change the direction of material flow, curved roller conveyors are often used in conjunction with straight conveyors to navigate corners or redirect goods within a facility.
Flexible Roller Conveyors: These systems are designed for versatility and can be expanded, contracted, and curved, allowing them to fit into various spaces and accommodate different layouts.
Incline/Decline Roller Conveyors: Used to move items between different heights, these conveyors are equipped with rollers set at an angle, facilitating upward or downward movement without manual lifting.
Accumulation Conveyors: While not powered themselves, these systems allow for the accumulation of goods without back pressure, meaning products can be collected at the end of the conveyor without causing damage or requiring manual intervention.
Each type of gravity roller conveyor system offers unique benefits and is suitable for different applications, depending on the specific requirements of the operation, such as space constraints, product type, and the need for directional changes or elevation adjustments.
The angle of a gravity roller conveyor is a critical factor in its design and operation, directly influencing the system’s efficiency in moving goods. Typically, the angle is determined based on the weight of the items being transported and the desired speed of movement. For most applications, the angle ranges from 2 to 5 degrees. This slight incline uses gravity to move items along the conveyor while ensuring control and preventing items from moving too quickly. However, the exact angle can vary based on specific operational needs, such as the type of items being moved, their weight, and the surface material of the rollers. In some cases, especially when moving very light or very heavy items, custom angles may be necessary to achieve optimal performance. Consulting with gravity roller conveyor manufacturers is advisable to determine the most effective angle for a particular application.
The capacity of a gravity roller conveyor refers to the maximum weight it can safely and effectively transport over its surface. This capacity can vary widely depending on the design, materials used, and the spacing of the rollers. Generally, standard gravity roller conveyors can handle loads ranging from a few kilograms up to several hundred kilograms per meter. Heavy-duty models are designed to accommodate even greater weights, often required in industrial settings, such as manufacturing plants or distribution centers. The key factors influencing a conveyor’s capacity include the diameter and material of the rollers, the strength of the frame, and the roller spacing. Closer roller spacing can support heavier loads by distributing the weight more evenly across the surface of the conveyor. It’s essential to choose a conveyor with a capacity that exceeds the maximum weight of the goods it will carry to ensure longevity and prevent system failure.
Gravity rollers can be made from various materials, each selected for its durability, cost-effectiveness, and suitability for the items being transported. The most common materials include:
Steel: Widely used for its strength and durability, steel rollers are suitable for heavy-duty applications and can handle substantial loads. They are particularly favored in industrial environments for their longevity and resistance to wear.
Aluminum: Offering a lighter alternative to steel, aluminum rollers are easier to install and maneuver. They are ideal for lighter loads and applications where noise reduction is a priority, as aluminum tends to operate more quietly than steel.
Plastic: Plastic rollers are the most cost-effective option and are suitable for lightweight applications. They are available in various compositions, allowing for flexibility in terms of load capacity and environmental resistance.
Stainless Steel: For applications requiring hygiene and corrosion resistance, such as food processing or pharmaceuticals, stainless steel rollers are preferred. They offer the strength of steel with added resistance to moisture and chemicals.
The choice of material depends on the specific requirements of the application, including the weight of the goods being transported, the operating environment, and budget constraints.
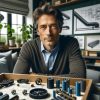
Jordan Smith, a seasoned professional with over 20 years of experience in the conveyor system industry. Jordan’s expertise lies in providing comprehensive solutions for conveyor rollers, belts, and accessories, catering to a wide range of industrial needs. From initial design and configuration to installation and meticulous troubleshooting, Jordan is adept at handling all aspects of conveyor system management. Whether you’re looking to upgrade your production line with efficient conveyor belts, require custom conveyor rollers for specific operations, or need expert advice on selecting the right conveyor accessories for your facility, Jordan is your reliable consultant. For any inquiries or assistance with conveyor system optimization, Jordan is available to share his wealth of knowledge and experience. Feel free to reach out at any time for professional guidance on all matters related to conveyor rollers, belts, and accessories.