Key Features of Diamond Pattern Conveyor Belt Explained
Conveyor belts are crucial components in various industries, facilitating the efficient movement of goods and materials. Among the diverse types available, the diamond pattern conveyor belt stands out for its unique design and functionality. These belts feature a distinctive diamond-shaped pattern on their surface, which enhances grip and reduces slippage, making them ideal for transporting items on inclined surfaces. The diamond pattern conveyor belt is particularly valued in industries such as mining, agriculture, and manufacturing for its durability and reliability. This introduction highlights the significance of these specialized conveyor belts and sets the stage for exploring top manufacturers in Japan who excel in producing high-quality diamond pattern conveyor belts.
What is a Diamond Pattern Conveyor Belt?
Definition and Description
A diamond pattern conveyor belt is a specialized type of conveyor belt that features a diamond-shaped surface pattern. This design is created by embossing or molding a series of raised diamonds onto the belt’s surface, which significantly enhances its grip and traction capabilities. The diamond pattern, often referred to as a “rough top” or “profiled” surface, is engineered to prevent slippage and ensure stable transportation of materials, especially on inclined planes. This unique pattern makes the diamond pattern conveyor belt a preferred choice in various industries that require efficient and reliable material handling solutions.
Advantages of the Diamond Pattern Design
The diamond pattern conveyor belt offers several distinct advantages due to its innovative surface design. These benefits make it a versatile and effective tool in numerous industrial applications. Here are five key advantages:
High Friction
One of the primary advantages of the diamond pattern conveyor belt is its high friction surface. The raised diamond shapes increase the contact area between the belt and the conveyed materials, significantly improving grip. This enhanced friction ensures that items remain securely in place during transport, reducing the risk of slippage and product loss. Industries such as packaging, logistics, and manufacturing benefit from this feature, as it enhances operational efficiency and safety.
Suitability for Steep Inclines
The diamond pattern conveyor belt is exceptionally well-suited for use on steep inclines. The raised diamond pattern provides additional grip, preventing materials from sliding back when the belt is operating on an incline. This makes it ideal for applications in mining, construction, and agriculture, where materials often need to be transported up steep slopes. The ability to handle inclined transport efficiently helps reduce the need for additional equipment and labor, streamlining processes and cutting costs.
Non-Marking Property
Another significant advantage of the diamond pattern conveyor belt is its non-marking property. The diamond-shaped protrusions are designed to be gentle on the conveyed materials, preventing any damage or marking during transport. This feature is particularly important in industries where the appearance and integrity of the products are critical, such as the food, pharmaceutical, and electronics sectors. By ensuring that products remain in pristine condition, the diamond pattern conveyor belt helps maintain high-quality standards and customer satisfaction.
Durability and Longevity
The diamond pattern conveyor belt is known for its durability and longevity. The robust design and high-quality materials used in its construction enable it to withstand harsh operating conditions, including heavy loads, abrasive materials, and extreme temperatures. This durability translates to a longer service life, reducing the frequency of belt replacements and minimizing downtime. Industries that demand high reliability, such as mining and quarrying, greatly benefit from the long-lasting performance of diamond pattern conveyor belts.
Versatility in Applications
The versatility of the diamond pattern conveyor belt is another notable advantage. Its unique surface design makes it suitable for a wide range of applications across various industries. Whether it’s transporting bulk materials in agriculture, moving packaged goods in warehouses, or conveying delicate items in manufacturing, the diamond pattern conveyor belt can handle diverse tasks with ease. This adaptability makes it a valuable asset for companies looking to optimize their material handling processes and improve overall productivity.
The diamond pattern conveyor belt is an innovative solution that offers numerous benefits due to its specialized design. The high friction surface, suitability for steep inclines, non-marking property, durability, and versatility make it an indispensable tool in many industrial applications. By understanding these advantages, companies can make informed decisions about incorporating diamond pattern conveyor belts into their operations, ultimately enhancing efficiency, safety, and product quality.
The Construction of Diamond Pattern Conveyor Belts
Materials and Construction
The construction of diamond pattern conveyor belts is a meticulous process that ensures durability, strength, and efficiency in material handling. These belts are designed to meet the rigorous demands of various industries, with specific focus on two popular variants: the 2-Ply Tan Diamond Top Conveyor Belt and the 2-Ply Black Diamond Top Conveyor Belt. Each type is crafted using high-quality materials and advanced manufacturing techniques to deliver superior performance.
Synthetic Carcass Strength and Flexibility
The core of a diamond pattern conveyor belt is its synthetic carcass, which provides the necessary strength and flexibility for reliable operation. The synthetic materials, typically polyester or nylon, offer several advantages:
- High Tensile Strength: The synthetic fibers used in the carcass provide exceptional tensile strength, allowing the belt to handle heavy loads without stretching or breaking.
- Flexibility: The flexible nature of synthetic materials ensures that the belt can bend and flex over pulleys and rollers without cracking or delaminating, which is crucial for smooth operation.
- Resistance to Wear and Tear: Synthetic carcasses are highly resistant to abrasion, chemicals, and moisture, extending the belt’s service life even in harsh environments.
- Lightweight: Despite their strength, synthetic materials are lightweight, reducing the overall weight of the conveyor system and improving energy efficiency.
- Consistency: Synthetic fibers provide consistent performance without the variability seen in natural fibers, ensuring reliable and predictable belt behavior.
Molded Diamond Top Surface and Its Benefits
The diamond top surface of these conveyor belts is molded to create a raised, textured pattern.
- Enhanced Traction: The diamond pattern increases surface friction, preventing materials from slipping, especially on inclined conveyors.
- Improved Material Handling: The raised pattern helps in handling bulk materials and packages more efficiently by providing better grip and stability.
- Reduced Product Damage: The textured surface is gentle on the materials being transported, minimizing the risk of damage or marking, which is crucial in industries like food processing and electronics.
- Versatile Performance: The diamond top surface performs well in various environmental conditions, including wet, dry, and dusty environments, ensuring consistent operation.
- Ease of Cleaning: The molded design allows for easier cleaning and maintenance, which helps in maintaining hygiene standards in industries such as pharmaceuticals and food production.
Color Significance (Tan and Black) and Applications
The color of the diamond pattern conveyor belt not only differentiates between product lines but also indicates specific properties and suitable applications.
2-Ply Tan Diamond Top Conveyor Belt
- Applications in Food Industry: The tan color is often associated with food-grade belts, suitable for applications in food processing and packaging where hygiene and cleanliness are paramount.
- Visibility and Inspection: The light tan color makes it easier to spot contaminants and perform visual inspections, enhancing quality control processes.
- Non-Marking Property: Tan belts are designed to be non-marking, making them ideal for transporting delicate or finished products without leaving any marks or residues.
- Indoor Use: These belts are commonly used in indoor environments where temperature and humidity are controlled, ensuring optimal performance.
- Aesthetic Appeal: The tan color provides a neutral, professional appearance suitable for industries where presentation matters, such as pharmaceuticals and cosmetics.
2-Ply Black Diamond Top Conveyor Belt
- Heavy-Duty Applications: The black color is typically used for belts designed for heavy-duty applications, such as mining, construction, and aggregate handling, where durability is a priority.
- UV Resistance: Black belts are often UV-resistant, making them suitable for outdoor use where exposure to sunlight can degrade other materials.
- Heat Resistance: The black color can indicate a higher resistance to heat, making these belts suitable for applications involving high temperatures or exposure to hot materials.
- Oil and Chemical Resistance: Black belts are often treated to resist oils, chemicals, and solvents, making them ideal for industrial environments where such substances are present.
- Cost-Effective: Black belts are generally more cost-effective for heavy-duty and general-purpose applications, providing a durable and economical solution for material handling needs.
The construction of diamond pattern conveyor belts involves careful selection of materials and meticulous design to meet the specific needs of various industries. The synthetic carcass provides the necessary strength and flexibility, while the molded diamond top surface offers enhanced traction, improved material handling, reduced product damage, versatile performance, and ease of cleaning. The color of the belts, whether tan or black, signifies their specific properties and suitable applications, ensuring that industries can choose the right belt for their particular needs. Understanding these construction elements helps in selecting the appropriate diamond pattern conveyor belt, ultimately enhancing efficiency, safety, and productivity in material handling operations.
Key Features and Technical Specifications of Diamond Pattern Conveyor Belt
Comparison of #58: 2-Ply Tan and #57: 2-Ply Black Diamond Top Conveyor Belts
Feature/Specification | #58: 2-Ply Tan Diamond Top Conveyor Belt | #57: 2-Ply Black Diamond Top Conveyor Belt |
---|---|---|
Thickness | 6mm (moderate for balance of flexibility and strength) | 7mm (thicker for increased durability) |
Pulley Diameter | Minimum 75mm (smooth operation) | Minimum 100mm (supports robust construction) |
Belt Weight | 1.3 kg/m² (lightweight yet robust) | 1.5 kg/m² (sturdy, suitable for heavy-duty use) |
Operational Temperature | -20°C to 70°C (moderately cold to warm conditions) | -30°C to 90°C (versatile for cold and high temperatures) |
Plies | Two layers of synthetic fabric (strength and flexibility) | Two layers of synthetic fabric (durability and flexibility) |
Top Cover Material | High-quality, non-marking rubber compound | Heat and oil-resistant rubber compound |
Bottom Cover Material | Friction-resistant rubber (enhances grip, reduces slippage) | Friction-resistant rubber (excellent traction, operational efficiency) |
Unique Features
Both the #58 and #57 diamond pattern conveyor belts boast several unique features that make them stand out in their respective applications.
Non-Marking Property
The non-marking property is a critical feature of the #58: 2-Ply Tan Diamond Top Conveyor Belt. This characteristic ensures that the belt does not leave marks or residues on the transported materials. This is particularly important in industries such as food processing, pharmaceuticals, and electronics, where product integrity and appearance are paramount. For instance, transporting packaged food items, pharmaceutical products, or delicate electronic components without leaving marks ensures the products reach their destination in pristine condition.
Anti-Static
The anti-static feature is another significant advantage, especially in environments where static electricity can pose a risk. Both the Tan and Black diamond pattern conveyor belts can be treated to dissipate static electricity, preventing the build-up of static charge. This is essential in industries like electronics manufacturing, where static discharge can damage sensitive components. It also enhances safety in environments where combustible materials are present, reducing the risk of static-induced sparks.
Suitability for Different Conveyor Systems
- Flat Conveyors: Both belts are suitable for flat conveyor systems, providing stable and reliable transportation of goods across horizontal surfaces.
- Inclined Conveyors: The diamond pattern provides enhanced grip, making these belts ideal for inclined conveyors where slippage needs to be minimized.
- Curved Conveyors: The flexibility and strength of these belts make them suitable for use on curved conveyor systems, ensuring smooth transitions and continuous material flow.
- High-Speed Conveyors: The lightweight yet durable construction of the #58 Tan belt makes it suitable for high-speed conveyor applications, where efficiency and speed are crucial.
- Heavy-Duty Conveyors: The #57 Black belt’s robust build is perfect for heavy-duty conveyor systems, handling large volumes of materials with ease.
The #58: 2-Ply Tan and #57: 2-Ply Black Diamond Top Conveyor Belts each offer distinct technical specifications and unique features tailored to meet diverse industrial needs. The tan belt’s non-marking property and suitability for high-speed conveyors make it ideal for food processing and packaging industries, while the black belt’s durability, heat, and oil resistance make it perfect for heavy-duty applications in harsh environments. Understanding these key features and technical specifications ensures the selection of the right diamond pattern conveyor belt for optimizing material handling processes, enhancing efficiency, and maintaining product quality across various industrial sectors.
Applications of Diamond Pattern Conveyor Belts
Overview of Industries and Specific Applications
Diamond pattern conveyor belts are versatile and indispensable in various industries due to their unique design and functional advantages. Their application ranges from packaging to heavy industrial use, demonstrating their adaptability and effectiveness in enhancing operational efficiency and safety.
Packaging and Bagged Goods Conveying
One of the primary applications of the diamond pattern conveyor belt is in the packaging industry. The unique surface pattern ensures secure handling of packaged and bagged goods, preventing slippage and maintaining the integrity of the products.
- Automated Packaging Lines: In automated packaging lines, diamond pattern conveyor belts are used to transport boxes, bags, and other packaged goods from one station to another. The high friction surface ensures that products do not slide off the belt, even at high speeds.
- Bagging Operations: For bagging operations involving grains, seeds, or other small items, these belts provide the necessary grip to move bags efficiently through filling and sealing machines without causing jams or slippage.
- Product Inspection: The non-marking property of the diamond pattern conveyor belt is crucial in inspection lines where products need to be examined for quality. The gentle grip ensures products remain in place without damage.
- Sorting and Distribution: In sorting and distribution centers, the belts help in the efficient handling and sorting of various packages, ensuring they are directed to the correct destinations.
- Retail Packaging: For retail packaging operations, where aesthetic appeal is important, the non-marking feature ensures that packaging remains clean and presentable.
Bulk Product, General Conveying, and Industrial Uses
Diamond pattern conveyor belts are also widely used in the transportation of bulk products and in general industrial conveying applications. The robust construction and high friction surface make them suitable for a variety of demanding environments.
- Agriculture: In the agricultural sector, these belts are used for transporting grains, seeds, and other bulk agricultural products. The diamond pattern provides the necessary grip to move these materials efficiently, even on inclined conveyors.
- Mining: In mining operations, diamond pattern conveyor belts are used to convey mined materials such as coal, ore, and gravel. The high durability and resistance to abrasion make them ideal for harsh mining environments.
- Construction: For construction sites, these belts are used to transport construction materials like sand, cement, and bricks. The ability to handle heavy loads and rough materials ensures efficient material handling.
- Food Processing: In food processing plants, these belts transport raw and processed food items. The non-marking property ensures food products are moved without contamination, maintaining high hygiene standards.
- Manufacturing: In manufacturing units, diamond pattern conveyor belts are used for general conveying tasks, moving parts and finished products through different stages of production and assembly.
The Role of the Diamond Pattern in Enhancing Efficiency and Safety
The diamond pattern on these conveyor belts plays a crucial role in enhancing both efficiency and safety in various applications. Here’s how:
- Enhanced Grip and Traction: The raised diamond-shaped patterns on the belt surface increase friction, providing better grip on transported items. This is particularly beneficial in preventing slippage and ensuring that materials stay in place during transit, even on inclined or curved conveyor paths.
- Improved Efficiency: By reducing the risk of slippage and ensuring smooth transport of goods, the diamond pattern helps maintain a consistent flow of materials. This leads to improved efficiency in production lines and reduces downtime caused by jams or misplaced items.
- Safety: The enhanced grip provided by the diamond pattern reduces the likelihood of accidents caused by slipping materials. This is especially important in environments where heavy or hazardous materials are being transported. The secure handling of these materials ensures the safety of both the products and the workers.
- Versatility: The diamond pattern conveyor belt is versatile enough to be used in various environmental conditions, including wet, dry, and dusty environments. This adaptability ensures consistent performance and reliability across different industrial settings.
- Product Integrity: The non-marking and gentle gripping nature of the diamond pattern conveyor belt ensures that transported goods are not damaged during handling. This is crucial for maintaining product quality and reducing wastage, particularly in industries like food processing and pharmaceuticals where product integrity is essential.
The diamond pattern conveyor belt is a critical component in numerous industries due to its unique design and functional benefits. From packaging and bagged goods conveying to handling bulk products and general industrial applications, these belts enhance operational efficiency and safety. The diamond pattern’s role in providing enhanced grip, improved efficiency, and maintaining product integrity makes it an indispensable tool in modern material handling processes. By understanding the diverse applications and advantages of these conveyor belts, industries can optimize their operations, ensuring smooth and reliable material transport while maintaining high standards of safety and quality.
Diamond Pattern Conveyor Belt Price Overview
Factors Influencing the Price of Diamond Pattern Conveyor Belts
When considering the purchase of a diamond pattern conveyor belt, it is essential to understand the various factors that influence its price. These factors ensure that the belts are tailored to meet specific needs and industry standards, justifying their cost through performance and longevity. Here are five key factors:
1. Material Quality
The quality of materials used in the construction of diamond pattern conveyor belts significantly impacts their price. High-grade synthetic materials like polyester or nylon for the carcass and durable rubber compounds for the top cover increase the belt’s durability, flexibility, and resistance to wear and tear. These high-quality materials, while more expensive, ensure longer belt life and better performance, justifying the initial investment.
2. Belt Construction and Ply Count
The construction of the conveyor belt, including the number of plies, also affects the price. A 2-ply belt, for instance, is constructed with two layers of synthetic fabric, providing extra strength and flexibility. The more plies a belt has, the more robust and durable it becomes, which can be crucial for heavy-duty applications. However, this also means higher manufacturing costs, leading to a higher purchase price. Additionally, specialized constructions, such as reinforced edges or anti-static properties, further influence the cost.
3. Surface Design and Pattern
The complexity of the diamond pattern and the precision in its molding process play a significant role in pricing. A well-defined, consistently molded diamond pattern ensures superior grip and traction, essential for preventing slippage and enhancing the belt’s functionality. The technology and precision required to produce such high-quality patterns add to the manufacturing costs, thereby affecting the overall price.
4. Customization and Specifications
Customization options, such as specific dimensions, tailored plies, and unique surface treatments (e.g., heat, oil, or chemical resistance), directly impact the price of diamond pattern conveyor belts. Industries often require belts that are specifically designed to meet unique operational needs. These customized specifications ensure that the belts perform optimally in their intended applications but also result in higher production costs and, consequently, higher prices.
5. Brand and Manufacturer
The reputation and expertise of the manufacturer can significantly influence the price of a diamond pattern conveyor belt. Established brands with a track record of producing reliable and high-quality belts may charge a premium for their products. These manufacturers invest in research and development, use superior materials, and employ stringent quality control measures, all of which contribute to the higher cost but also ensure better performance and longevity.
Why Investing in a Quality Conveyor Belt is Cost-Effective in the Long Term
Investing in a high-quality diamond pattern conveyor belt might seem expensive initially, but it proves to be cost-effective in the long run. Here are several reasons why this investment is worthwhile:
1. Durability and Longevity
High-quality conveyor belts are built to last. They can withstand harsh working conditions, heavy loads, and constant operation without significant wear and tear. This durability reduces the frequency of belt replacements, leading to lower maintenance costs and less downtime. Over time, the initial higher investment in a quality belt pays off through reduced operational interruptions and extended service life.
2. Operational Efficiency
Quality diamond pattern conveyor belts ensure smooth and efficient operation. The enhanced grip and traction provided by the diamond pattern reduce the risk of slippage, ensuring continuous material flow. This efficiency translates to higher productivity and throughput, optimizing the overall performance of the conveyor system. An efficient system also reduces energy consumption, contributing to cost savings.
3. Safety
Investing in a quality conveyor belt enhances workplace safety. High-quality belts with precise diamond patterns minimize the risk of slippage and material spillage, which can lead to accidents and injuries. Safety is paramount in any industrial setting, and reducing the risk of incidents helps avoid costly legal liabilities, insurance claims, and potential damage to the company’s reputation.
4. Product Quality and Integrity
The non-marking property of high-quality diamond pattern conveyor belts ensures that products are transported without damage or contamination. This is crucial in industries such as food processing, pharmaceuticals, and electronics, where product integrity is essential. Maintaining high product quality reduces wastage and returns, leading to cost savings and increased customer satisfaction.
5. Reduced Maintenance and Repair Costs
High-quality conveyor belts require less frequent maintenance and repairs. They are designed to withstand challenging conditions, which means fewer breakdowns and less need for extensive maintenance work. This reduction in maintenance efforts translates to cost savings and allows maintenance teams to focus on other critical areas of the operation.
The price of diamond pattern conveyor belts is influenced by several factors, including material quality, construction, surface design, customization options, and the manufacturer’s reputation. While the initial investment in a high-quality conveyor belt may be higher, it proves to be cost-effective in the long term. Durability, operational efficiency, safety, product quality, and reduced maintenance costs all contribute to the overall value and return on investment. By understanding these factors and benefits, businesses can make informed decisions when purchasing diamond pattern conveyor belts, ensuring they optimize their material handling processes and achieve long-term operational success.
Section 6: Conveyor Belts
Essential Maintenance Tips for Longevity and Efficiency
Maintaining a diamond pattern conveyor belt properly is crucial for ensuring its longevity and operational efficiency. Regular maintenance not only extends the belt’s life but also enhances its performance, reducing the likelihood of unexpected downtime. Here are five essential maintenance tips:
1. Regular Inspections
Conducting regular inspections is vital for identifying potential issues before they become serious problems. Inspect the belt for signs of wear and tear, such as fraying edges, cracks, or unusual stretching. Pay close attention to the diamond pattern surface for any wear that could affect traction. Regular inspections help in early detection of issues, allowing for timely repairs and preventing major failures.
2. Proper Cleaning
Keeping the diamond pattern conveyor belt clean is essential for maintaining its functionality. Accumulated dirt, debris, and residues can impact the belt’s grip and cause slippage. Use appropriate cleaning agents and methods to remove any buildup from the belt’s surface without damaging the diamond pattern. Regular cleaning ensures that the belt operates smoothly and maintains its traction capabilities.
3. Correct Tensioning
Proper tensioning is critical for the optimal performance of the conveyor belt. Over-tensioning can cause excessive wear and stress on the belt and conveyor components, while under-tensioning can lead to slippage and misalignment. Regularly check and adjust the tension according to the manufacturer’s guidelines to ensure the belt operates efficiently and lasts longer.
4. Lubrication of Moving Parts
Lubricating the moving parts of the conveyor system, such as rollers and bearings, is essential for reducing friction and wear. Use the recommended lubricants to ensure smooth operation. Regular lubrication helps prevent overheating and prolongs the life of the conveyor components, contributing to the overall efficiency and longevity of the diamond pattern conveyor belt.
5. Alignment Checks
Misalignment of the conveyor belt can lead to uneven wear, increased energy consumption, and potential damage to the belt and other components. Regularly check the alignment of the belt and make necessary adjustments to keep it centered and running straight. Proper alignment reduces the risk of edge damage and ensures the belt operates smoothly and efficiently.
Common Parts and Replacements
The efficient operation of a diamond pattern conveyor belt relies on the availability and proper selection of common parts and replacements. Here are some essential parts and considerations for maintaining and replacing them:
1. Belt Fasteners
Belt fasteners are crucial for joining the ends of the conveyor belt and ensuring a continuous loop. Over time, fasteners can wear out or become damaged, necessitating replacement. Selecting high-quality, compatible fasteners is essential for maintaining the integrity and performance of the belt. Ensure that the fasteners are correctly installed and regularly inspected for signs of wear.
2. Rollers and Idlers
Rollers and idlers support the conveyor belt and help it move smoothly along the conveyor frame. These components can wear out due to constant friction and load. Regularly check for signs of wear, such as uneven rotation or noise, and replace them as needed. Using high-quality rollers and idlers that match the specifications of the diamond pattern conveyor belt ensures optimal performance and reduces downtime.
3. Drive Pulleys and Lagging
Drive pulleys and their lagging play a critical role in transmitting power to the conveyor belt. Worn or damaged pulleys can cause slippage and reduced efficiency. Inspect the drive pulleys for wear and replace them if necessary. The lagging, which provides additional grip, should also be checked and replaced when worn to maintain proper traction and drive efficiency.
4. Bearings
Bearings support the rotating components of the conveyor system and reduce friction. Worn or damaged bearings can lead to increased friction, overheating, and potential failure of the conveyor components. Regularly inspect and lubricate the bearings to ensure they are in good condition. Replace any bearings that show signs of wear or damage to maintain smooth and efficient operation.
5. Belt Scrapers and Cleaners
Belt scrapers and cleaners are essential for removing material buildup on the belt’s surface, particularly in applications where sticky or abrasive materials are conveyed. Regularly inspect and replace scrapers and cleaners to ensure they effectively remove debris without damaging the diamond pattern. Proper maintenance of these components helps in maintaining the belt’s cleanliness and operational efficiency.
Maintaining a diamond pattern conveyor belt involves regular inspections, proper cleaning, correct tensioning, lubrication of moving parts, and alignment checks. These maintenance practices ensure the belt’s longevity and efficiency, reducing the risk of unexpected downtime and costly repairs. Additionally, the availability and proper selection of common parts and replacements, such as belt fasteners, rollers, drive pulleys, bearings, and belt scrapers, are crucial for the belt’s optimal performance. By following these maintenance tips and ensuring the availability of high-quality replacement parts, industries can maximize the lifespan and efficiency of their diamond pattern conveyor belts, ultimately enhancing their operational productivity and reliability.
Choosing the Right Diamond Pattern Conveyor Belt for Your Needs
Selecting the appropriate diamond pattern conveyor belt for your application is crucial for maximizing efficiency, safety, and longevity. There are several key considerations to keep in mind when making this decision. This section will guide you through the essential factors to consider and provide tips on how to collaborate effectively with suppliers to find the best conveyor belt solution.
Considerations to Keep in Mind
Choosing the right diamond pattern conveyor belt involves evaluating several critical factors to ensure it meets your specific needs. Here are five important considerations:
Application Specifics
The first step in selecting the right diamond pattern conveyor belt is understanding the specifics of your application. Consider the type of materials being conveyed, the required belt speed, and the nature of the process. For example:
- Food Processing: If you are in the food processing industry, you will need a belt that meets stringent hygiene standards and is easy to clean. A 2-ply tan diamond pattern conveyor belt with non-marking properties would be ideal for this application.
- Mining and Aggregate: For heavy-duty applications like mining, where the belt will be exposed to abrasive materials, a more robust 2-ply black diamond pattern conveyor belt with enhanced durability and resistance to wear is necessary.
Load Requirements
Understanding the load requirements is essential for choosing a conveyor belt that can handle the weight and volume of the materials being transported. Factors to consider include:
- Maximum Load Capacity: Ensure the belt can support the maximum load it will carry without excessive stretching or damage.
- Frequency of Use: For continuous, high-volume operations, select a belt designed for heavy-duty use to ensure it withstands the constant load without frequent replacements.
Environmental Conditions
The operating environment plays a significant role in determining the appropriate diamond pattern conveyor belt. Consider the following environmental factors:
- Temperature: If the belt will be used in high-temperature environments, such as in baking or industrial processing, choose a belt that can withstand the heat without degrading.
- Moisture and Chemicals: For applications involving exposure to moisture, oils, or chemicals, select a belt with appropriate resistance properties to prevent damage and ensure longevity.
Belt Material and Construction
The material and construction of the belt are crucial for its performance and durability. Consider the following aspects:
- Synthetic Carcass: Choose a belt with a strong synthetic carcass, such as polyester or nylon, for enhanced strength and flexibility.
- Surface Pattern: Ensure the diamond pattern is well-defined and consistent for optimal grip and traction.
Compliance and Standards
Ensure the conveyor belt complies with industry standards and regulations, especially in sectors like food processing and pharmaceuticals. Look for certifications and quality assurances from the manufacturer to ensure the belt meets the necessary safety and performance standards.
How to Work with Suppliers to Find the Best Conveyor Belt Solution
Working closely with suppliers is essential to finding the right diamond pattern conveyor belt for your needs. Here are some tips for effective collaboration:
1. Clear Communication of Requirements
Provide suppliers with detailed information about your application, including load requirements, environmental conditions, and specific challenges you face. Clear communication helps suppliers recommend the most suitable belt for your needs.
2. Request for Customization
If standard conveyor belts do not meet your requirements, discuss customization options with suppliers. Many manufacturers offer tailored solutions, such as specific dimensions, special coatings, or enhanced features, to address unique application needs.
3. Evaluate Supplier Expertise
Choose suppliers with extensive experience and a strong track record in producing high-quality diamond pattern conveyor belts. Evaluate their technical expertise, customer service, and ability to provide support and maintenance services.
4. Request Samples and Prototypes
Before making a large investment, request samples or prototypes of the conveyor belt to test in your operational environment. This allows you to evaluate the belt’s performance and ensure it meets your requirements.
5. Consider Long-Term Partnerships
Establishing a long-term partnership with a reliable supplier can provide ongoing benefits, such as consistent supply, better pricing, and continuous support. A trusted supplier can also keep you informed about new technologies and innovations in conveyor belt solutions.
Choosing the right diamond pattern conveyor belt involves careful consideration of application specifics, load requirements, environmental conditions, belt material and construction, and compliance with industry standards. By working closely with experienced suppliers, you can find a conveyor belt solution that enhances efficiency, safety, and longevity in your operations. Effective communication, customization options, and evaluating supplier expertise are key to making an informed decision. Investing in the right conveyor belt ensures optimal performance, reducing downtime and maintenance costs while supporting the smooth and efficient flow of materials in your industrial processes.
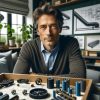
Jordan Smith, a seasoned professional with over 20 years of experience in the conveyor system industry. Jordan’s expertise lies in providing comprehensive solutions for conveyor rollers, belts, and accessories, catering to a wide range of industrial needs. From initial design and configuration to installation and meticulous troubleshooting, Jordan is adept at handling all aspects of conveyor system management. Whether you’re looking to upgrade your production line with efficient conveyor belts, require custom conveyor rollers for specific operations, or need expert advice on selecting the right conveyor accessories for your facility, Jordan is your reliable consultant. For any inquiries or assistance with conveyor system optimization, Jordan is available to share his wealth of knowledge and experience. Feel free to reach out at any time for professional guidance on all matters related to conveyor rollers, belts, and accessories.