The Cost of Conveyor Idler: Key Factors and Considerations
A conveyor idler is a crucial component in conveyor systems, responsible for supporting the belt and ensuring smooth and efficient material transport. These idlers come in various types, including carrying idlers, return idlers, and impact idlers, each serving a specific function within the system. The cost of conveyor idler is influenced by several factors such as material, size, type, and brand, making it essential for businesses to understand these elements when budgeting for conveyor systems. This blog post aims to provide a comprehensive overview of the cost of conveyor idler, exploring the different types available, their specifications, and the key factors that affect their pricing, helping you make informed decisions.
The Cost of Conveyor Idler
The Function of Conveyor Idlers
Conveyor idlers play a vital role in maintaining the efficiency and longevity of conveyor belts. Their primary function is to support the conveyor belt and the load being transported, ensuring minimal friction and wear.
- Support and Stability: Conveyor idlers provide crucial support to the conveyor belt, preventing it from sagging and ensuring that the belt runs smoothly. This support is essential for maintaining the integrity of the belt and preventing damage that could result from the belt coming into contact with other machinery parts.
- Load Distribution: Idlers help in evenly distributing the weight of the load across the conveyor belt. This even distribution minimizes the stress on the belt, reducing the likelihood of wear and tear and prolonging the lifespan of the belt. Proper load distribution is especially critical in industries where heavy materials are transported.
- Minimizing Friction: By providing a rolling surface for the conveyor belt, idlers significantly reduce friction between the belt and the support structure. This reduction in friction is essential for efficient operation, as it decreases the energy required to move the belt, leading to lower operational costs.
- Tracking and Alignment: Idlers play a crucial role in maintaining the alignment of the conveyor belt. Misalignment can cause the belt to run off-track, leading to operational disruptions and potential damage. Idlers ensure that the belt stays on its designated path, thereby enhancing the efficiency and reliability of the conveyor system.
- Shock Absorption: Some types of idlers, such as impact idlers, are designed to absorb the impact of heavy loads being dropped onto the conveyor belt. This shock absorption capability prevents damage to the belt and the idlers themselves, ensuring a longer service life and reducing maintenance costs.
Parts of a Conveyor Idler
Conveyor idlers are composed of several parts, each with a specific function. Understanding these components is essential for grasping how idlers contribute to the overall efficiency of conveyor systems.
- Rollers: Rollers are the cylindrical components that rotate around a fixed axis, providing a rolling surface for the conveyor belt. They are typically made from materials such as steel or plastic, depending on the application. The number and arrangement of rollers can vary, with some idlers featuring a single roller and others having multiple rollers arranged in a trough configuration.
- Pulleys: Pulleys are wheels with a grooved rim that guide and drive the conveyor belt. They are usually located at the ends of the conveyor system and are powered to move the belt. Pulleys are critical for maintaining belt tension and ensuring smooth movement. They can be made from various materials, including steel and aluminum, and are often coated with rubber to increase friction with the belt.
- Frames: The frame of a conveyor idler is the structure that holds the rollers and other components in place. It provides stability and support, ensuring that the rollers remain aligned and function correctly. Frames are typically made from metal, such as steel or aluminum, to provide the necessary strength and durability.
- Bearings: Bearings are essential components that allow the rollers to rotate smoothly around their axis. They reduce friction and wear, ensuring that the rollers can turn with minimal resistance. Bearings are usually sealed to protect them from dust and debris, which can cause premature wear and failure.
- Seals: Seals are used to protect the internal components of the idler, such as bearings, from contaminants like dust, dirt, and moisture. Effective sealing is crucial for preventing premature wear and ensuring the longevity of the idler. Seals are typically made from materials like rubber or plastic and are designed to provide a tight, reliable barrier.
Cost of Conveyor Idler: Key Factors
Understanding the cost of conveyor idler involves examining several factors that influence pricing. These factors can vary significantly depending on the specific requirements of the conveyor system and the industry in which it operates. Here are some key factors that affect the cost of conveyor idler:
- Material: The material used in the construction of conveyor idlers has a significant impact on cost. Idlers made from high-quality materials, such as stainless steel or specialized plastics, are generally more expensive but offer greater durability and resistance to wear and corrosion. Conversely, idlers made from lower-cost materials may have a shorter lifespan and require more frequent replacement.
- Size: The size of the conveyor idler is another crucial factor. Larger idlers, which are designed to support heavier loads and wider belts, tend to be more expensive due to the increased material and manufacturing requirements. Smaller idlers, while less costly, may not be suitable for all applications.
- Type: The type of conveyor idler also influences its cost. Different types of idlers, such as carrying idlers, return idlers, impact idlers, and self-training idlers, are designed for specific functions and environments. Impact idlers, for example, which are designed to absorb the impact of heavy loads, are typically more expensive than standard carrying idlers.
- Brand: The brand or manufacturer of the conveyor idler can affect its price. Established brands with a reputation for quality and reliability may charge a premium for their products. However, investing in idlers from reputable manufacturers can provide long-term cost savings by reducing the frequency of maintenance and replacement.
- Custom Specifications: Customization options, such as specific dimensions, materials, or additional features, can also impact the cost of conveyor idler. Custom idlers are often necessary for specialized applications but can be more expensive due to the tailored manufacturing process.
Understanding the cost of conveyor idler involves considering various factors such as material, size, type, brand, and custom specifications. Conveyor idlers are essential components that support the conveyor belt, distribute the load, minimize friction, maintain alignment, and absorb shock. By understanding the different parts of a conveyor idler, including rollers, pulleys, frames, bearings, and seals, businesses can make informed decisions about their conveyor systems. Investing in high-quality idlers can enhance the efficiency and longevity of conveyor belts, ultimately leading to cost savings and improved operational performance.
Types of Conveyor Idlers: the Cost of Conveyor Idler
Types of Conveyor Idlers
Conveyor idlers are critical components in conveyor systems, each type serving a specific function to ensure the smooth and efficient operation of the conveyor belt. The cost of conveyor idler varies significantly depending on the type and its intended application. In this section, we will introduce and explore the various types of conveyor idlers available in the market, including carrying idlers, return idlers, impact idlers, self-training idlers, and V-return idlers. Understanding these types and their specifications can help businesses select the right idlers for their needs and manage the associated costs effectively.
Carrying Idlers
Carrying idlers are among the most common types of idlers used in conveyor systems. They support the loaded conveyor belt and help maintain its alignment, ensuring smooth material transport. Carrying idlers are typically positioned on the carrying side of the belt and are designed to handle various load capacities.
Specifications and Applications:
- Roller Diameter: Carrying idlers come in various roller diameters, typically ranging from 89 mm to 219 mm, depending on the load and belt width.
- Frame Material: The frames are usually made from steel or aluminum to provide strength and durability.
- Bearing Type: Sealed bearings are commonly used to ensure smooth rotation and protect against dust and moisture.
- Spacing: The spacing between carrying idlers can vary, usually between 1 to 1.5 meters, depending on the load and belt tension.
- Applications: Carrying idlers are used in a wide range of industries, including mining, agriculture, and manufacturing, to transport materials such as ore, grain, and finished products.
Return Idlers
Return idlers support the empty conveyor belt on its return journey after it has discharged its load. These idlers are crucial for maintaining the belt’s alignment and preventing sagging, which can lead to operational inefficiencies and increased wear.
Specifications and Applications:
- Roller Diameter: Similar to carrying idlers, return idlers come in various diameters, typically between 76 mm and 159 mm.
- Frame Design: Return idlers often feature a flat or V-shaped frame to support the return belt effectively.
- Material: They are made from durable materials like steel or plastic to withstand wear and environmental conditions.
- Bearing Protection: Return idlers also use sealed bearings to ensure longevity and smooth operation.
- Applications: These idlers are used in systems where the return belt must be supported over long distances, such as in large-scale mining operations and bulk material handling facilities.
Impact Idlers
Impact idlers are designed to absorb the shock and impact of heavy materials being loaded onto the conveyor belt. They are typically installed at loading points where the belt is subjected to high-impact forces, preventing damage to the belt and extending its lifespan.
Specifications and Applications:
- Rubber Rings: Impact idlers are equipped with rubber rings or discs that cushion the belt against impact forces.
- Heavy-Duty Frame: The frame is reinforced to handle the additional stresses associated with impact loads.
- Roller Diameter: These idlers usually have larger roller diameters, ranging from 127 mm to 219 mm, to provide additional support.
- Spacing: Impact idlers are spaced closer together than regular idlers, typically between 0.5 to 1 meter.
- Applications: Impact idlers are essential in industries such as mining and construction, where heavy materials like rocks and debris are loaded onto conveyor belts.
Self-Training Idlers
Self-training idlers, also known as training idlers or aligning idlers, are designed to automatically correct any misalignment of the conveyor belt. They pivot or rotate to guide the belt back to its correct path, ensuring continuous and efficient operation.
Specifications and Applications:
- Pivot Mechanism: Self-training idlers have a pivoting mechanism that allows them to adjust to the belt’s position.
- Roller Design: These idlers often have tapered or crowned rollers to aid in realignment.
- Material: The rollers and frame are made from durable materials like steel or aluminum.
- Installation Points: They are installed at intervals along the conveyor system where misalignment is likely to occur.
- Applications: Self-training idlers are used in industries with long or complex conveyor systems, such as logistics and distribution centers, to minimize downtime and maintenance costs.
V-Return Idlers
V-return idlers are designed to support the return side of the conveyor belt in a V-shaped configuration. This design helps keep the belt centered and prevents it from wandering off track, ensuring efficient operation and reducing the risk of belt damage.
Specifications and Applications:
- V-Shape Design: The idlers are arranged in a V-shape to provide optimal belt support and alignment.
- Roller Diameter: V-return idlers typically have roller diameters between 76 mm and 159 mm.
- Frame Material: The frame is constructed from sturdy materials like steel to provide stability.
- Bearing Type: Sealed bearings are used to protect against contaminants and ensure smooth operation.
- Applications: V-return idlers are commonly used in industries with long conveyor systems, such as mining and bulk material handling, where maintaining belt alignment is critical.
The Cost of Conveyor Idler: Factors and Considerations
When considering the cost of conveyor idler, it is essential to understand the factors that influence pricing. Each type of idler has its unique specifications and applications, which can impact the overall cost. Here are some key considerations:
- Material Quality: Higher quality materials, such as stainless steel or specialized polymers, typically result in higher costs but offer better durability and performance.
- Customization: Custom specifications, such as specific roller diameters, frame designs, or bearing types, can increase the cost due to tailored manufacturing processes.
- Brand and Manufacturer: Reputable brands with a history of quality and reliability may charge a premium, but this investment can lead to long-term savings in maintenance and replacement costs.
- Application Requirements: The specific needs of the application, such as handling heavy loads, high impact forces, or maintaining strict alignment, can influence the type and cost of idler required.
- Maintenance and Longevity: Investing in higher-quality idlers can reduce maintenance costs and extend the lifespan of the conveyor system, leading to overall cost savings.
Understanding the different types of conveyor idlers and their respective applications is crucial for optimizing the efficiency and longevity of conveyor systems. By considering the specifications and functions of carrying idlers, return idlers, impact idlers, self-training idlers, and V-return idlers, businesses can select the appropriate idlers for their needs. Additionally, understanding the factors that influence the cost of conveyor idler can help in making informed purchasing decisions, ultimately leading to better operational efficiency and cost savings.
Factors That Affect Cost of Conveyor Idler
Key Factors Influencing the Cost of Conveyor Idler
Understanding the various factors that influence the cost of conveyor idler is essential for businesses looking to optimize their investment in conveyor systems. Several key factors play a significant role in determining the price of conveyor idlers, including material, size, type, brand, and custom specifications.
Material
The material used in the construction of conveyor idlers is a primary factor affecting their cost. Different materials offer varying levels of durability, resistance to wear, and suitability for specific environments.
- Steel: Steel is a common material for conveyor idlers due to its strength and durability. Idlers made from high-quality steel are ideal for heavy-duty applications but tend to be more expensive.
- Aluminum: Aluminum idlers are lighter and offer good corrosion resistance, making them suitable for environments where weight is a concern. However, they are generally more expensive than steel idlers.
- Plastic: Plastic idlers are often used in applications where corrosion resistance and weight reduction are essential. They are typically less expensive than metal idlers but may not be as durable.
- Stainless Steel: Stainless steel idlers are highly resistant to corrosion and ideal for use in harsh environments, such as food processing or marine applications. These idlers are usually more costly due to the material’s premium properties.
- Rubber-Coated: Idlers with rubber coatings are designed to absorb impact and reduce noise, which is crucial in specific applications. The added material and manufacturing process make these idlers more expensive.
Size
The size of the conveyor idler, including the roller diameter and length, also influences its cost. Larger idlers capable of supporting more significant loads and wider belts generally cost more due to the increased material and manufacturing requirements.
- Small Idlers: Small idlers with roller diameters ranging from 50 mm to 100 mm are suitable for light-duty applications and are typically less expensive.
- Medium Idlers: Medium-sized idlers with diameters between 100 mm and 150 mm are used in standard applications and have moderate costs.
- Large Idlers: Large idlers with diameters exceeding 150 mm are designed for heavy-duty applications, such as mining and bulk material handling, and are more expensive.
- Extended Length: Idlers with extended lengths are necessary for wider conveyor belts and larger loads, contributing to higher costs.
- Custom Sizes: Custom-sized idlers tailored to specific applications or conveyor systems can significantly increase the cost due to specialized manufacturing.
Type
The type of conveyor idler is another critical factor affecting its cost. Different idlers are designed for specific functions within a conveyor system, and their unique features can impact pricing.
- Carrying Idlers: These are standard idlers used to support the loaded belt and are generally less expensive.
- Return Idlers: Designed to support the empty belt on its return journey, return idlers have moderate costs.
- Impact Idlers: Impact idlers, equipped with rubber rings or discs to absorb shock, are more expensive due to their specialized design.
- Self-Training Idlers: These idlers have a pivot mechanism to correct belt misalignment, making them more costly than standard idlers.
- V-Return Idlers: V-return idlers support the return belt in a V-shaped configuration and are moderately priced.
Brand
The brand or manufacturer of conveyor idlers can influence their cost. Established brands with a reputation for quality and reliability may charge a premium for their products, but this investment can provide long-term benefits.
- Reputable Brands: Known for their high-quality products, reputable brands often come with higher price tags but offer better performance and durability.
- Generic Brands: Generic or lesser-known brands may offer lower prices but might not provide the same level of reliability and longevity.
- Custom Manufacturers: Manufacturers specializing in custom idlers can provide tailored solutions but usually at a higher cost due to specialized production.
- Local Manufacturers: Local manufacturers may offer competitive pricing and quicker delivery times, impacting overall costs.
- Imported Brands: Imported idlers might have higher shipping costs and longer lead times, affecting the total cost.
Custom Specifications
Custom specifications tailored to specific needs and applications can significantly impact the cost of conveyor idlers. Customization often involves additional design and manufacturing processes, leading to higher prices.
- Custom Materials: Idlers made from specialized materials, such as high-temperature resistant metals, can be more expensive.
- Unique Dimensions: Idlers with unique dimensions to fit specific conveyor systems require custom manufacturing, increasing costs.
- Additional Features: Features like enhanced sealing, dust protection, or noise reduction can add to the cost of the idler.
- Special Coatings: Custom coatings for specific environmental conditions, such as anti-corrosive coatings, can raise the price.
- Bulk Orders: While bulk orders can sometimes reduce the per-unit cost, the initial investment is higher, impacting the overall budget.
Industry-Specific Needs and Price Variations
Different industries have unique requirements for conveyor idlers, leading to variations in pricing based on the specific demands of each application.
Mining Industry
The mining industry requires heavy-duty idlers capable of handling large loads and harsh conditions. Idlers used in mining are typically more expensive due to their robust construction and specialized features.
- Heavy Load Capacity: Idlers designed for heavy loads and abrasive materials command higher prices.
- Impact Resistance: Impact idlers are essential in mining to absorb shock from heavy material loads, increasing their cost.
- Durability: Enhanced durability to withstand harsh mining conditions results in higher-priced idlers.
- Corrosion Resistance: Idlers with corrosion-resistant coatings are necessary in mining environments, adding to the cost.
- Customization: Custom idlers tailored to specific mining applications often come at a premium.
Food Processing Industry
In the food processing industry, idlers must meet strict hygiene and safety standards. Stainless steel idlers are commonly used due to their resistance to corrosion and ease of cleaning, but they are more expensive.
- Hygienic Design: Idlers designed to meet food safety standards have higher costs.
- Stainless Steel: The use of stainless steel, which is resistant to corrosion and easy to clean, increases the price.
- Smooth Surfaces: Idlers with smooth surfaces to prevent contamination are more expensive.
- Sealed Bearings: Sealed bearings to protect against moisture and contamination add to the cost.
- Certification: Idlers certified for use in food processing environments may have a higher price due to compliance costs.
Manufacturing Industry
The manufacturing industry uses conveyor idlers for various applications, from assembly lines to material handling. The cost of conveyor idler in this sector depends on the specific requirements of the manufacturing process.
- Load Capacity: Idlers designed for specific load capacities can vary in price based on their robustness.
- Speed Requirements: High-speed conveyor systems require idlers with precise specifications, impacting cost.
- Material Handling: Different materials handled in manufacturing processes necessitate idlers with varying features and prices.
- Customization: Custom idlers for specific manufacturing applications can increase costs.
- Maintenance Needs: Idlers designed for low-maintenance operation may have higher upfront costs but offer long-term savings.
The cost of conveyor idler is influenced by various factors, including material, size, type, brand, and custom specifications. Each of these factors plays a significant role in determining the price and suitability of idlers for specific applications. Additionally, the unique needs of different industries, such as mining, food processing, and manufacturing, can lead to variations in idler pricing based on the specific demands of each sector. Understanding these factors and their impact on the cost of conveyor idler can help businesses make informed purchasing decisions, ensuring they select the right idlers for their conveyor systems while optimizing their investment.
Average Cost of Conveyor Idler Rollers
Range of Average Prices for Conveyor Idler Rollers
Understanding the average cost of conveyor idler rollers is crucial for budgeting and optimizing investment in conveyor systems. The price of idler rollers can vary widely based on several factors, including material, size, type, brand, and custom specifications. Here, we provide a range of average prices for conveyor idler rollers and discuss what affects their cost.
Standard Steel Idler Rollers
Standard steel idler rollers are commonly used in various industries due to their durability and cost-effectiveness. These rollers typically range in price from $20 to $50 each, depending on the roller diameter and length. Factors influencing the cost include the thickness of the steel and the quality of the bearings used.
- Example: A standard 100 mm diameter steel idler roller with a length of 500 mm might cost around $30. Higher-quality steel or enhanced bearings can increase the price to $50.
Plastic Idler Rollers
Plastic idler rollers are used in applications where weight reduction and corrosion resistance are important. These rollers are generally priced between $15 and $40 each, with cost variations based on the type of plastic used and the roller dimensions.
- Example: A plastic idler roller with a 75 mm diameter and 400 mm length might cost $20. Using specialized plastics like UHMW (Ultra High Molecular Weight) polyethylene can increase the price to $35 or $40.
Impact Idler Rollers
Impact idler rollers are designed to absorb shock and are used in high-impact areas of conveyor systems. These rollers are more expensive due to their specialized construction, typically ranging from $50 to $150 each. The cost depends on the quality and number of impact rings or discs used.
- Example: An impact idler roller with rubber rings for a 200 mm diameter and 600 mm length might cost $80. High-end models with extra cushioning and superior materials can cost up to $150.
Stainless Steel Idler Rollers
Stainless steel idler rollers are preferred in environments where corrosion resistance is critical, such as in food processing or chemical industries. These rollers are priced between $50 and $100 each, depending on the grade of stainless steel and the roller dimensions.
- Example: A stainless steel idler roller with a 120 mm diameter and 500 mm length might cost $70. Using high-grade stainless steel like 316 can increase the price to $100.
Self-Aligning Idler Rollers
Self-aligning idler rollers help maintain belt alignment, reducing wear and tear on the conveyor system. These rollers are more complex and typically cost between $60 and $120 each. The price varies based on the alignment mechanism and the quality of materials used.
- Example: A self-aligning idler roller with a 150 mm diameter and 500 mm length might cost $90. Enhanced alignment features and premium materials can push the price to $120.
Factors Affecting the Cost of Conveyor Idler Rollers
Several factors can significantly impact the cost of conveyor idler rollers. Understanding these factors can help businesses make informed decisions when purchasing idlers for their conveyor systems.
Material
The material used in the construction of idler rollers is a primary cost driver. High-quality materials such as stainless steel or specialized plastics increase durability and resistance to wear and corrosion but also raise the price. Conversely, standard steel or lower-grade plastics are more affordable but may require more frequent replacement.
Size
The size of the idler roller, including its diameter and length, directly affects its cost. Larger rollers capable of supporting heavier loads and wider belts are generally more expensive due to the increased material and manufacturing requirements.
Type
Different types of idler rollers serve specific functions within a conveyor system, impacting their cost. For example, impact idlers designed to absorb shock are more expensive than standard carrying idlers due to their specialized construction. Self-aligning idlers, with mechanisms to correct belt misalignment, also come at a higher price.
Brand
The brand or manufacturer of the idler rollers can influence their cost. Established brands with a reputation for quality and reliability may charge a premium, but this investment can provide long-term benefits through reduced maintenance and longer service life. Generic or lesser-known brands may offer lower prices but might not provide the same level of performance and durability.
Custom Specifications
Custom specifications tailored to specific needs can significantly increase the cost of idler rollers. Customization may involve unique dimensions, materials, or additional features such as enhanced sealing or noise reduction. These tailored solutions often require specialized manufacturing processes, leading to higher prices.
Impact of Bulk Purchasing, Custom Specifications, and Additional Features
Bulk Purchasing
Purchasing idler rollers in bulk can lead to significant cost savings. Suppliers often offer discounts for large orders, reducing the per-unit price. This approach is beneficial for businesses with extensive conveyor systems requiring numerous idlers. However, the initial investment is higher, which can impact budgeting.
- Example: Purchasing 100 standard steel idler rollers at once might reduce the price from $30 each to $25 each, saving $500 overall.
Custom Specifications
Custom idler rollers tailored to specific applications can meet unique operational needs but at a higher cost. Customization can include dimensions, materials, or features like enhanced sealing or special coatings. While the initial cost is higher, these idlers can provide better performance and longer service life, potentially reducing long-term costs.
- Example: A custom stainless steel idler roller designed for high-temperature environments might cost $120, compared to a standard model at $70. However, its enhanced durability can lead to lower replacement costs over time.
Additional Features
Additional features such as noise reduction, improved sealing, or impact resistance can increase the cost of idler rollers. These features enhance the performance and longevity of the idlers, making them suitable for specific environments or applications. The higher initial investment can result in lower maintenance and operational costs.
- Example: An idler roller with advanced noise reduction features might cost $40 more than a standard model but can significantly reduce noise levels in a manufacturing facility, improving worker conditions and reducing noise-related maintenance issues.
The cost of conveyor idler rollers is influenced by various factors, including material, size, type, brand, and custom specifications. Understanding the range of average prices and what affects these costs can help businesses make informed purchasing decisions. Factors such as bulk purchasing, custom specifications, and additional features also play a significant role in determining the final price of idler rollers. By considering these elements, businesses can optimize their investment in conveyor systems, ensuring they select the right idlers for their specific needs while managing costs effectively.
Conveyor Idler Manufacturers: the Cost of Conveyor Idler
Leading Conveyor Idler Manufacturers
Selecting the right manufacturer is crucial when considering the cost of conveyor idler. Reputable manufacturers not only provide high-quality products but also offer reliable customer service and technical support, ensuring the longevity and efficiency of conveyor systems. Here, we highlight some of the leading conveyor idler manufacturers in the industry and discuss the importance of choosing reputable brands.
Metso Outotec
Metso Outotec is a globally recognized manufacturer specializing in mining and aggregate processing solutions. Their conveyor idlers are known for their durability, efficiency, and innovation.
Key Features:
- High-Quality Materials: Metso Outotec uses premium materials to ensure the durability and longevity of their idlers.
- Innovative Designs: Their idlers incorporate advanced design features that enhance performance and reduce maintenance requirements.
- Global Reach: With a robust global network, Metso Outotec provides extensive customer support and fast delivery times.
Importance:
Choosing metso conveyor idlers can significantly reduce the total cost of ownership due to their durable products and comprehensive support services, which can lead to fewer replacements and less downtime.
Rexnord
Rexnord is a leading manufacturer of power transmission and conveying components, including conveyor idlers. Their products are widely used in various industries, including mining, manufacturing, and logistics.
Key Features:
- Diverse Product Range: Rexnord offers a wide range of idlers designed for different applications and environments.
- Customization Options: They provide customized solutions to meet specific operational needs.
- Quality Assurance: Rigorous quality control processes ensure that each idler meets high standards of performance and reliability.
Importance:
Rexnord’s emphasis on quality and customization helps businesses reduce operational costs by providing idlers that are tailored to their specific needs, ensuring optimal performance and longevity.
Caterpillar
Caterpillar is a renowned manufacturer known for its heavy machinery and equipment. Their conveyor idlers are designed to withstand harsh conditions, making them ideal for heavy-duty applications in mining and construction.
Key Features:
- Heavy-Duty Construction: Caterpillar idlers are built to endure extreme conditions and heavy loads.
- Reliability: Known for their robustness, these idlers provide consistent performance even in the toughest environments.
- Comprehensive Support: Caterpillar offers extensive technical support and after-sales services to ensure customer satisfaction.
Importance:
Investing in Caterpillar idlers can lead to significant cost savings by minimizing downtime and reducing the frequency of replacements, thanks to their durability and reliable performance.
Joy Global (Komatsu Mining Corp.)
Joy Global, now part of Komatsu Mining Corp., is a prominent manufacturer of mining equipment, including conveyor idlers. Their products are engineered to enhance productivity and reduce operational costs.
Key Features:
- Advanced Engineering: Joy Global idlers are designed with cutting-edge technology to optimize performance.
- Efficiency: These idlers help improve conveyor system efficiency, reducing energy consumption and operational costs.
- Durability: Made from high-quality materials, they are built to last, even in demanding mining environments.
Importance:
Joy Global’s focus on efficiency and durability ensures that their idlers provide long-term value, helping businesses reduce the overall cost of conveyor idler by extending the lifespan of their conveyor systems.
Superior Industries
Superior Industries is a manufacturer specializing in conveyor components and material handling solutions. Their conveyor idlers are known for their high performance and cost-effectiveness.
Key Features:
- Cost-Effective Solutions: Superior Industries offers idlers that deliver excellent performance at competitive prices.
- Wide Selection: They provide a broad range of idlers to suit various applications and industries.
- Customer-Centric Approach: Superior Industries focuses on meeting customer needs with tailored solutions and reliable support.
Importance:
Superior Industries’ cost-effective and high-performance idlers can help businesses manage the cost of conveyor idler effectively, ensuring they get the best value for their investment.
Importance of Choosing Reputable Manufacturers
Selecting reputable conveyor idler manufacturers is critical for ensuring quality, durability, and long-term cost savings. Here are five reasons why choosing well-established manufacturers is essential:
Quality Assurance
Reputable manufacturers adhere to stringent quality control standards, ensuring that each idler meets high performance and reliability criteria. This quality assurance translates to fewer failures, reduced maintenance needs, and lower overall costs.
Example: Metso Outotec’s rigorous testing procedures ensure that their idlers perform reliably in demanding environments, reducing the likelihood of unexpected failures and costly downtime.
Durability
High-quality materials and advanced manufacturing processes used by reputable manufacturers result in durable idlers that can withstand harsh conditions and heavy use. This durability extends the lifespan of the idlers, leading to long-term cost savings.
Example: Caterpillar’s heavy-duty construction ensures that their idlers can handle extreme loads and conditions, minimizing the need for frequent replacements and repairs.
Technical Support and Services
Leading manufacturers offer comprehensive technical support and after-sales services, helping businesses troubleshoot issues and maintain optimal system performance. This support is crucial for minimizing downtime and operational disruptions.
Example: Rexnord provides extensive customer support, including installation guidance and maintenance tips, ensuring that their idlers continue to operate efficiently.
Innovation and Customization
Reputable manufacturers invest in research and development to create innovative solutions that enhance conveyor system performance. They also offer customization options to meet specific operational needs, ensuring that businesses get the most out of their investment.
Example: Joy Global’s advanced engineering and customization options allow businesses to optimize their conveyor systems for specific applications, improving efficiency and reducing costs.
Reputation and Reliability
Established manufacturers have a proven track record of delivering reliable products and services. Their reputation for quality and reliability provides peace of mind, knowing that the idlers will perform as expected.
Example: Superior Industries’ reputation for cost-effective and high-performance idlers gives businesses confidence in their investment, knowing they are choosing a trusted and reliable supplier.
Understanding the cost of conveyor idler involves not only considering the price of the idlers themselves but also evaluating the manufacturers behind them. Leading manufacturers like Metso Outotec, Rexnord, Caterpillar, Joy Global, and Superior Industries offer high-quality, durable, and reliable conveyor idlers that can significantly impact the total cost of ownership. By choosing reputable manufacturers, businesses can ensure they are investing in products that provide long-term value, reduce maintenance costs, and enhance the efficiency of their conveyor systems. This strategic approach to selecting conveyor idler manufacturers ultimately helps businesses manage the cost of conveyor idler effectively, ensuring optimal performance and cost savings.
Conveyor Idler Pulleys: the Cost of Conveyor Idler
What Are Conveyor Idler Pulleys?
Conveyor idler pulleys are essential components within the idler system of a conveyor belt. They are designed to guide and support the belt, ensuring smooth and efficient movement of materials. Unlike standard idler rollers, pulleys play a crucial role in driving and tensioning the conveyor belt, contributing significantly to the overall functionality of the conveyor system.
Functions of Conveyor Idler Pulleys:
- Belt Tensioning: Conveyor idler pulleys help maintain the proper tension of the conveyor belt, preventing slippage and ensuring smooth operation. Proper tensioning is crucial for minimizing wear and tear on both the belt and the idlers.
- Belt Tracking: Pulleys assist in keeping the conveyor belt aligned with the conveyor structure. Misalignment can cause operational inefficiencies and potential damage to the belt and other components.
- Driving Force: Some idler pulleys are used in conjunction with drive pulleys to provide the necessary driving force to move the belt. This function is essential for the efficient transport of materials.
- Load Support: Pulleys also support the weight of the belt and the load it carries, distributing the load evenly across the conveyor system to prevent excessive stress on individual components.
- Direction Changes: Pulleys can be used to change the direction of the conveyor belt, enabling the design of more complex conveyor systems that can navigate different layouts and terrains.
Factors Affecting the Cost of Conveyor Idler Pulleys
The cost of conveyor idler pulleys can vary significantly based on several factors. Understanding these factors is essential for businesses looking to optimize their investment in conveyor systems. Here, we discuss the key factors that affect the cost of conveyor idler pulleys, adding to the total idler cost.
Material
The material used in the construction of conveyor idler pulleys is one of the primary factors influencing their cost. Different materials offer varying levels of durability, resistance to wear, and suitability for specific environments.
Examples:
- Steel: Steel is a common material for conveyor idler pulleys due to its strength and durability. Steel pulleys are suitable for heavy-duty applications but are generally more expensive.
- Aluminum: Aluminum pulleys are lighter and offer good corrosion resistance, making them ideal for environments where weight is a concern. However, they are typically more costly than steel pulleys.
- Stainless Steel: Stainless steel pulleys provide excellent corrosion resistance and are often used in harsh environments, such as food processing or chemical industries. These pulleys are among the most expensive due to their premium properties.
- Plastic: Plastic pulleys are used in applications where corrosion resistance and weight reduction are important. They are generally less expensive than metal pulleys but may not be as durable.
- Rubber-Coated: Pulleys with rubber coatings offer additional grip and shock absorption, which can be crucial in specific applications. The added material and manufacturing complexity make these pulleys more expensive.
Size
The size of the pulley, including its diameter and width, directly impacts its cost. Larger pulleys capable of supporting more significant loads and wider belts are generally more expensive due to the increased material and manufacturing requirements.
Examples:
- Small Pulleys: Small pulleys with diameters ranging from 50 mm to 100 mm are suitable for light-duty applications and are typically less expensive.
- Medium Pulleys: Medium-sized pulleys with diameters between 100 mm and 200 mm are used in standard applications and have moderate costs.
- Large Pulleys: Large pulleys with diameters exceeding 200 mm are designed for heavy-duty applications, such as mining and bulk material handling, and are more expensive.
- Extended Width: Pulleys with extended widths are necessary for wider conveyor belts and larger loads, contributing to higher costs.
- Custom Sizes: Custom-sized pulleys tailored to specific applications or conveyor systems can significantly increase the cost due to specialized manufacturing.
Type and Design
The type and design of the pulley also influence its cost. Different pulleys serve specific functions within the conveyor system, and their unique features can impact pricing.
Examples:
- Drive Pulleys: Drive pulleys provide the necessary driving force to move the belt and are generally more expensive due to their critical function and design complexity.
- Snub Pulleys: Snub pulleys are used to increase the belt’s contact angle with the drive pulley, enhancing traction. They are moderately priced.
- Take-Up Pulleys: Take-up pulleys are used to maintain belt tension and are typically more costly due to their mechanical adjustment features.
- Wing Pulleys: Wing pulleys are designed to clean the belt and reduce material buildup, making them more expensive due to their specialized design.
- Lagged Pulleys: Lagged pulleys have a rubber coating to improve grip and reduce belt slippage, adding to their cost.
Brand
The brand or manufacturer of conveyor idler pulleys can influence their cost. Established brands with a reputation for quality and reliability may charge a premium for their products, but this investment can provide long-term benefits.
Examples:
- Reputable Brands: Known for their high-quality products, reputable brands often come with higher price tags but offer better performance and durability.
- Generic Brands: Generic or lesser-known brands may offer lower prices but might not provide the same level of reliability and longevity.
- Custom Manufacturers: Manufacturers specializing in custom pulleys can provide tailored solutions but usually at a higher cost due to specialized production.
- Local Manufacturers: Local manufacturers may offer competitive pricing and quicker delivery times, impacting overall costs.
- Imported Brands: Imported pulleys might have higher shipping costs and longer lead times, affecting the total cost.
Custom Specifications
Custom specifications tailored to specific needs and applications can significantly impact the cost of conveyor idler pulleys. Customization often involves additional design and manufacturing processes, leading to higher prices.
Examples:
- Custom Materials: Pulleys made from specialized materials, such as high-temperature resistant metals, can be more expensive.
- Unique Dimensions: Pulleys with unique dimensions to fit specific conveyor systems require custom manufacturing, increasing costs.
- Additional Features: Features like enhanced sealing, dust protection, or noise reduction can add to the cost of the pulley.
- Special Coatings: Custom coatings for specific environmental conditions, such as anti-corrosive coatings, can raise the price.
- Bulk Orders: While bulk orders can sometimes reduce the per-unit cost, the initial investment is higher, impacting the overall budget.
The cost of conveyor idler pulleys is influenced by various factors, including material, size, type, brand, and custom specifications. Each of these factors plays a significant role in determining the price and suitability of pulleys for specific applications. By understanding these elements and their impact on the cost of conveyor idler pulleys, businesses can make informed purchasing decisions, ensuring they select the right pulleys for their conveyor systems while managing costs effectively. This strategic approach to selecting conveyor idler pulleys ultimately helps businesses optimize their investment, enhance system performance, and achieve long-term cost savings.
Budgeting for Conveyor Idlers: Managing the Cost of Conveyor Idler
Insights into Budgeting for Conveyor Idlers
Budgeting for conveyor idlers is a critical aspect of managing the operational costs of conveyor systems. Businesses need to consider various factors to ensure they allocate sufficient resources while optimizing the cost of conveyor idler. A well-planned budget can help in maintaining the efficiency of conveyor systems, minimizing downtime, and extending the lifespan of conveyor components. Here, we provide insights into how businesses can effectively budget for conveyor idlers and include tips on cost-saving measures without compromising on quality.
1. Assessing Operational Needs
The first step in budgeting for conveyor idlers is to assess the operational needs of the conveyor system. This involves understanding the specific requirements based on the type of materials being transported, the load capacity, and the environmental conditions. By evaluating these factors, businesses can determine the type and quantity of idlers required, helping to allocate resources more accurately.
Example: For a mining operation that handles heavy, abrasive materials, investing in high-quality, heavy-duty idlers made from durable materials like stainless steel can reduce the frequency of replacements and maintenance, ultimately leading to cost savings.
2. Planning for Maintenance and Replacement
Maintenance and replacement costs are significant components of the overall cost of conveyor idler. Regular maintenance is essential for ensuring the longevity and efficient operation of idlers. Businesses should budget for routine inspections, lubrication, and part replacements to prevent unexpected failures and costly downtime.
Example: Establishing a maintenance schedule that includes regular checks and timely replacement of worn-out idlers can prevent more extensive damage to the conveyor system, saving money in the long run.
3. Leveraging Bulk Purchasing
Bulk purchasing is a strategic approach to reduce the cost of conveyor idler. Suppliers often offer discounts for large orders, lowering the per-unit price. Businesses with extensive conveyor systems can benefit from bulk purchasing, especially when they have predictable usage patterns.
Example: A manufacturing facility with multiple conveyor lines can negotiate bulk purchase agreements with suppliers, obtaining a better price per idler and reducing overall costs.
Tips on Cost-Saving Measures Without Compromising Quality
While budgeting for conveyor idlers, businesses can implement several cost-saving measures without compromising on the quality and performance of their conveyor systems. Here are five effective tips:
1. Choosing the Right Materials
Selecting the appropriate materials for conveyor idlers based on the specific application can lead to significant cost savings. While high-quality materials like stainless steel may have a higher upfront cost, they offer superior durability and resistance to wear and corrosion, reducing long-term expenses.
Example: In a food processing plant, using stainless steel idlers ensures compliance with hygiene standards and extends the lifespan of the idlers, reducing the need for frequent replacements and lowering maintenance costs.
2. Implementing Preventive Maintenance
Preventive maintenance is crucial for extending the life of conveyor idlers and minimizing unexpected downtime. Regular inspections, cleaning, and lubrication can prevent minor issues from developing into major problems that require costly repairs or replacements.
Example: Scheduling monthly maintenance checks to clean and lubricate idlers can prevent the buildup of debris and reduce friction, enhancing the efficiency and longevity of the idlers.
3. Investing in Quality Brands
While it may be tempting to opt for cheaper, generic idlers, investing in reputable brands known for their quality and reliability can result in long-term cost savings. High-quality idlers from trusted manufacturers typically have better performance, durability, and lower maintenance requirements.
Example: Purchasing idlers from a well-known brand like Rexnord can provide peace of mind and reduce the frequency of replacements, ensuring consistent performance and reducing overall costs.
4. Customizing Idlers for Specific Applications
Customizing idlers to meet specific operational needs can enhance their performance and lifespan. Tailored idlers that match the exact requirements of the conveyor system can operate more efficiently and reduce wear and tear on both the idlers and the conveyor belt.
Example: For a conveyor system handling sharp, heavy materials, using custom idlers with reinforced coatings can prevent damage and extend the idlers’ lifespan, reducing replacement costs.
5. Utilizing Energy-Efficient Idlers
Energy-efficient idlers can help reduce operational costs by lowering the energy consumption of the conveyor system. Idlers designed to minimize friction and improve belt tracking can enhance the overall efficiency of the conveyor, resulting in cost savings on energy bills.
Example: Implementing low-friction idlers that reduce the drag on the conveyor belt can decrease the energy required to operate the system, leading to lower energy costs and increased savings over time.
Budgeting for conveyor idlers requires a strategic approach that considers the specific operational needs, maintenance requirements, and potential for cost-saving measures. By assessing the needs of the conveyor system, planning for regular maintenance, and leveraging bulk purchasing, businesses can effectively manage the cost of conveyor idler. Additionally, implementing cost-saving measures such as choosing the right materials, preventive maintenance, investing in quality brands, customizing idlers, and utilizing energy-efficient options can help optimize the budget without compromising on quality. By taking these steps, businesses can ensure the efficient operation of their conveyor systems, reduce downtime, and achieve long-term cost savings, ultimately enhancing their overall productivity and profitability.
Maintenance and Operational Costs: the Cost of Conveyor Idler
Maintenance Costs Associated with Conveyor Idlers
Maintaining conveyor idlers is essential for ensuring the efficient and reliable operation of conveyor systems. The maintenance costs associated with conveyor idlers can significantly affect the total cost of ownership, influencing both operational expenses and the longevity of the conveyor system. Proper maintenance practices can help mitigate these costs by preventing premature wear and failure.
Regular Inspection and Monitoring
Regular inspection and monitoring of conveyor idlers are critical for identifying potential issues before they escalate into major problems. This proactive approach helps in minimizing downtime and reducing the need for expensive repairs or replacements.
Example: Conducting monthly inspections to check for signs of wear, misalignment, or unusual noise can help detect issues early. Using tools like vibration analysis and thermal imaging can provide deeper insights into the condition of the idlers.
Lubrication
Proper lubrication is vital for reducing friction and wear on conveyor idlers. Regular lubrication ensures that the idlers rotate smoothly, reducing the energy required to move the belt and preventing excessive heat buildup, which can cause damage.
Example: Implementing a lubrication schedule based on the manufacturer’s recommendations can prevent the bearings from drying out and reduce the risk of overheating. Automatic lubrication systems can also be installed to ensure consistent and efficient lubrication.
Cleaning and Debris Removal
Accumulated debris and contaminants can cause significant wear and tear on conveyor idlers. Regular cleaning helps maintain the idlers’ performance and extends their lifespan by preventing abrasive materials from causing damage.
Example: Establishing a cleaning routine that includes removing debris from the idlers and surrounding areas can prevent abrasive particles from damaging the rollers and bearings. Using compressed air or water jets can be effective for cleaning hard-to-reach areas.
Impact on Total Cost of Ownership
The maintenance costs associated with conveyor idlers are a critical component of the total cost of ownership. Regular maintenance helps extend the lifespan of the idlers, reducing the frequency of replacements and minimizing operational disruptions. However, neglecting maintenance can lead to increased wear, unexpected failures, and costly repairs, significantly impacting the overall operational budget.
Example: Investing in regular maintenance can reduce the total cost of ownership by preventing costly breakdowns and extending the service life of the conveyor idlers. A well-maintained idler can last several years longer than a neglected one, providing substantial cost savings over time.
Recommendations for Maintenance Practices
Implementing effective maintenance practices is essential for ensuring that conveyor idlers function properly and last longer. Here are five recommendations for maintenance practices that can help businesses optimize the cost of conveyor idler:
1. Develop a Maintenance Schedule
Creating a detailed maintenance schedule based on the manufacturer’s recommendations and the specific operating conditions of the conveyor system is crucial. This schedule should include regular inspections, lubrication, and cleaning tasks to ensure that all components are properly maintained.
Example: A weekly maintenance schedule that includes visual inspections, monthly lubrication, and quarterly cleaning can help keep the idlers in optimal condition, reducing the risk of unexpected failures.
2. Use High-Quality Lubricants
Selecting the right lubricants for conveyor idlers is essential for reducing friction and wear. High-quality lubricants designed for the specific operating conditions of the conveyor system can enhance performance and extend the lifespan of the idlers.
Example: Using synthetic lubricants for high-temperature applications can provide better protection against heat and oxidation, ensuring smooth operation and reducing the need for frequent re-lubrication.
3. Implement Predictive Maintenance Techniques
Predictive maintenance techniques, such as vibration analysis and thermal imaging, can help identify potential issues before they lead to failures. These advanced diagnostic tools provide valuable insights into the condition of the idlers, allowing for timely interventions.
Example: Regular vibration analysis can detect imbalances or misalignments in the idlers, enabling maintenance teams to address these issues before they cause significant damage or operational disruptions.
4. Train Maintenance Personnel
Ensuring that maintenance personnel are properly trained in the maintenance and inspection of conveyor idlers is essential for effective upkeep. Training programs should cover the specific maintenance requirements of the idlers and the use of diagnostic tools and lubricants.
Example: Providing training sessions on the proper techniques for inspecting and lubricating idlers can enhance the effectiveness of maintenance activities, reducing the risk of errors and improving overall system reliability.
5. Monitor and Document Maintenance Activities
Keeping detailed records of maintenance activities, including inspections, lubrication, and repairs, can help track the condition of the idlers and identify trends or recurring issues. This documentation can also support predictive maintenance efforts and ensure compliance with maintenance schedules.
Example: Using a computerized maintenance management system (CMMS) to record and track maintenance activities can provide valuable data for analyzing the performance of the idlers and making informed decisions about maintenance strategies.
Understanding the maintenance and operational costs associated with conveyor idlers is crucial for managing the total cost of ownership. Regular maintenance practices, such as inspections, lubrication, and cleaning, can significantly reduce these costs by preventing premature wear and failures. By implementing effective maintenance practices, businesses can ensure that their conveyor idlers function properly and last longer, ultimately optimizing the cost of conveyor idler and enhancing the efficiency and reliability of their conveyor systems. Investing in regular maintenance and training, using high-quality lubricants, and leveraging predictive maintenance techniques can provide substantial cost savings and improve the overall performance of the conveyor system.
Choosing the Right Conveyor Idler: Balancing the Cost of Conveyor Idler
Selecting the correct conveyor idler for your system is crucial for ensuring efficient operation, minimizing downtime, and controlling costs. The choice of conveyor idler impacts not only the initial purchase price but also maintenance and operational expenses, forming a significant part of the total cost of ownership. Here, we provide detailed tips on choosing the right conveyor idler type and specifications for specific applications, along with the importance of considering the overall cost of conveyor idler.
Tips for Selecting the Correct Conveyor Idler Type and Specifications
- Assessing Material and Load Requirements
Understanding the type of material being transported and the load requirements is essential for selecting the right conveyor idler. Different materials and loads place varying demands on the idlers.
Example: For transporting heavy, abrasive materials such as minerals or ores, heavy-duty steel idlers with reinforced bearings are ideal. These idlers can withstand high impact and reduce the frequency of replacements, thus lowering long-term costs.
- Considering Environmental Conditions
The operating environment plays a critical role in idler selection. Factors such as temperature, humidity, and exposure to corrosive substances should be considered.
Example: In a food processing plant where hygiene is paramount, stainless steel idlers are preferred due to their corrosion resistance and ease of cleaning. This ensures compliance with health standards and extends the lifespan of the idlers, providing cost savings over time.
- Choosing the Right Type of Idler
Different types of idlers serve specific functions within a conveyor system. Understanding these functions helps in selecting the most suitable idler type for your application.
Example: Impact idlers are ideal for conveyor systems where heavy materials are loaded, as they absorb shock and prevent damage to the belt. Self-aligning idlers are beneficial in systems prone to belt misalignment, as they help maintain proper tracking, reducing wear and operational disruptions.
- Evaluating Roller Diameter and Length
The diameter and length of the idler rollers affect the load capacity and durability. Larger diameters and longer lengths generally support heavier loads and offer greater durability but at a higher cost.
Example: For a conveyor system handling large bulk materials over long distances, idlers with larger diameters (e.g., 200 mm) and extended lengths (e.g., 1000 mm) are recommended. These idlers provide better support and stability, reducing the need for frequent maintenance and replacements.
- Opting for Energy-Efficient Idlers
Energy-efficient idlers help reduce the overall energy consumption of the conveyor system, leading to lower operational costs. These idlers are designed to minimize friction and improve belt tracking.
Example: Low-friction idlers with precision bearings can significantly decrease the energy required to move the belt, leading to substantial savings on energy bills. Implementing these idlers in a high-capacity manufacturing facility can enhance productivity while reducing operational costs.
Factoring in the Total Cost of Ownership
When choosing conveyor idlers, it is essential to consider the total cost of ownership, which includes the initial purchase price, maintenance expenses, and operational costs. Here’s how you can effectively factor in these components:
Initial Purchase Price
The initial cost of conveyor idler varies based on the material, size, type, and brand. While it might be tempting to choose the cheapest option, it’s important to weigh the benefits of investing in higher-quality idlers that offer better durability and performance.
Example: Investing in high-quality stainless steel idlers may have a higher upfront cost, but their extended lifespan and reduced maintenance requirements can lead to significant cost savings over time.
Maintenance Expenses
Regular maintenance is crucial for extending the lifespan of conveyor idlers and ensuring efficient operation. Budgeting for maintenance activities such as inspections, lubrication, and part replacements helps in preventing costly breakdowns.
Example: Establishing a preventive maintenance schedule that includes monthly inspections and lubrication can reduce the risk of unexpected failures and prolong the life of the idlers, thus lowering long-term maintenance costs.
Operational Costs
Operational costs include energy consumption, downtime due to idler failure, and the efficiency of the conveyor system. Selecting energy-efficient idlers and ensuring proper maintenance can optimize operational costs.
Example: Implementing low-friction, energy-efficient idlers can decrease the energy required to move the conveyor belt, leading to lower electricity bills. Additionally, well-maintained idlers reduce the likelihood of system downtime, ensuring continuous operation and productivity.
Encouraging Total Cost of Ownership Considerations
To make informed decisions when selecting conveyor idlers, it is crucial to adopt a holistic view that considers the total cost of ownership. Here are some strategies to encourage this approach:
- Long-Term Budget Planning
Develop a long-term budget that includes not only the initial purchase price of the idlers but also projected maintenance and operational costs. This comprehensive budget helps in understanding the true cost of the idlers over their lifespan.
Example: A five-year budget plan for a mining conveyor system might include the costs of purchasing high-quality idlers, regular maintenance expenses, and potential energy savings from using low-friction idlers.
- Cost-Benefit Analysis
Conduct a cost-benefit analysis to compare different idler options. This analysis should factor in the initial cost, expected lifespan, maintenance requirements, and operational efficiency to determine the most cost-effective solution.
Example: Comparing the total cost of ownership of standard steel idlers versus stainless steel idlers in a corrosive environment can highlight the long-term savings and efficiency benefits of investing in stainless steel.
- Supplier Collaboration
Work closely with suppliers to understand the benefits and drawbacks of different idler types. Suppliers can provide valuable insights and recommendations based on their expertise and the specific needs of your conveyor system.
Example: Collaborating with a reputable supplier like Rexnord can help identify the most suitable idler options for a heavy-duty conveyor system, ensuring optimal performance and cost savings.
- Training and Education
Educate maintenance and operations teams about the importance of proper idler selection and maintenance practices. Training programs can enhance their understanding of how to optimize the performance and lifespan of conveyor idlers.
Example: Conducting regular training sessions on idler maintenance and inspection techniques can improve the effectiveness of maintenance activities, reducing the overall cost of ownership.
- Regular Review and Adjustment
Regularly review and adjust your conveyor idler selection and maintenance strategies based on performance data and changing operational needs. This proactive approach ensures that you continue to optimize costs and performance.
Example: Analyzing maintenance records and operational efficiency metrics can help identify areas for improvement and adjust maintenance schedules or idler types accordingly.
Choosing the right conveyor idler involves more than just selecting the cheapest option. It requires a thorough understanding of the specific needs of your conveyor system, considering factors such as material, load, environmental conditions, and energy efficiency. By focusing on the total cost of ownership, including initial purchase price, maintenance expenses, and operational costs, businesses can make informed decisions that optimize performance and cost savings. Implementing best practices in idler selection and maintenance, conducting cost-benefit analyses, collaborating with suppliers, and educating maintenance teams are all essential strategies for managing the cost of conveyor idler effectively and ensuring the long-term success of your conveyor system.
FAQs About Cost of Conveyor Idler
The cost of a conveyor line can vary significantly depending on several factors, including the length and complexity of the system, the type of conveyor (e.g., belt, roller, or chain), and the specific requirements of the application. Basic conveyor lines for small operations might start at around $5,000 to $10,000. However, for more extensive and complex systems, such as those used in large manufacturing or distribution facilities, costs can easily exceed $100,000. Custom features, such as advanced automation, specific material handling needs, and specialized controls, can also add to the overall cost. It’s essential to work with a reputable supplier to get an accurate estimate based on your specific needs and to ensure the system is designed for optimal efficiency and longevity.
An idler on a conveyor is a crucial component that supports and guides the conveyor belt. Idlers are typically cylindrical rollers that are mounted on a frame and positioned along the length of the conveyor belt to provide support for the belt and the material being transported. There are various types of idlers, including carrying idlers, return idlers, impact idlers, and self-aligning idlers, each serving a specific purpose. Carrying idlers support the loaded belt, while return idlers support the empty belt on its return journey. Impact idlers are used at loading points to absorb shock, and self-aligning idlers help maintain belt alignment. Proper selection and maintenance of idlers are essential for ensuring the efficiency, reliability, and longevity of the conveyor system.
The cost of a new conveyor belt can vary widely depending on several factors, such as the type of belt, its length and width, the material it’s made from, and the specific requirements of the application. Basic conveyor belts used in light-duty applications may cost as little as $10 to $50 per linear foot. For more specialized belts, such as those made from high-temperature resistant materials, food-grade belts, or heavy-duty mining belts, prices can range from $100 to $500 per linear foot or more. It’s important to consider the total cost of ownership, including installation, maintenance, and potential downtime, when budgeting for a new conveyor belt. Consulting with a supplier or manufacturer can help you determine the most cost-effective solution for your needs.
The cost of a warehouse conveyor belt system depends on various factors, including the type of conveyor, the length and width of the belt, the level of automation, and the specific requirements of the warehouse operation. Basic belt conveyor systems for small warehouses might start at around $5,000 to $10,000. For more extensive systems with advanced features such as automated sorting, integrated controls, and higher capacity, costs can range from $50,000 to $200,000 or more. Factors such as installation, customization, and the inclusion of safety features can also affect the overall cost. To get an accurate estimate, it’s essential to work with a reputable supplier who can assess your specific needs and provide a tailored solution that maximizes efficiency and productivity while managing costs effectively.
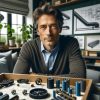
Jordan Smith, a seasoned professional with over 20 years of experience in the conveyor system industry. Jordan’s expertise lies in providing comprehensive solutions for conveyor rollers, belts, and accessories, catering to a wide range of industrial needs. From initial design and configuration to installation and meticulous troubleshooting, Jordan is adept at handling all aspects of conveyor system management. Whether you’re looking to upgrade your production line with efficient conveyor belts, require custom conveyor rollers for specific operations, or need expert advice on selecting the right conveyor accessories for your facility, Jordan is your reliable consultant. For any inquiries or assistance with conveyor system optimization, Jordan is available to share his wealth of knowledge and experience. Feel free to reach out at any time for professional guidance on all matters related to conveyor rollers, belts, and accessories.