Comprehensive Guide to Conveyor Belt Pulley Types Explained
Conveyor belt pulley types are crucial components in various industrial settings, ensuring the smooth and efficient operation of conveyor systems. These pulleys play a pivotal role in adjusting the direction of the conveyor belt, maintaining optimal tension, and providing the necessary drive to move materials. Understanding the different conveyor belt pulley types and their specific functions is essential for selecting the right pulley for your system. This selection can significantly enhance efficiency, safety, and overall performance in industrial operations. By grasping the significance of these pulley types, industries can optimize their conveyor systems to meet specific operational demands and improve productivity.
The Significance of Conveyor Belt Pulley Types
Types of pulley in belt conveyor are essential components in any conveyor system, and understanding their significance is crucial for optimizing industrial operations. These pulleys are not just simple mechanical elements; they are designed to cater to specific functions and operating conditions, ensuring the efficient and safe transportation of materials.
Different Pulley Types and Their Functions
- Drive Pulley (Head Pulley)
The drive pulley, also known as the head pulley, is responsible for driving the conveyor belt and moving the material along the system. Its surface is often coated with materials like chevron or diamond patterns to increase friction and grip. This ensures that the belt does not slip, providing a stable and continuous movement of materials. - Tension Pulley (Take-Up Pulley)
The tension pulley, or take-up pulley, is crucial for maintaining the correct tension in the conveyor belt. It ensures that the belt remains taut, preventing sagging and slippage, which can lead to inefficiencies and potential damage. By adjusting the belt’s tension, the take-up pulley helps in maintaining optimal performance and extending the life of the conveyor belt. - Motorized Pulley (Motor Drum)
The motorized pulley, or motor drum, integrates the roller and the transmission device into a single unit. This design enhances efficiency and saves space, making it ideal for environments where space is limited. The motorized pulley simplifies the installation process and reduces maintenance requirements, as the motor is enclosed within the pulley, protecting it from dust and debris. - Snub Pulley
The snub pulley is positioned close to the drive pulley and increases the contact area between the belt and the drive pulley. This additional contact helps to maximize the drive power and is particularly useful in high-torque environments or where contamination is a concern. The snub pulley ensures that the belt has sufficient grip to handle heavy loads without slipping. - Wing Pulley
The wing pulley, also known as a self-cleaning pulley, is designed to maintain belt traction by preventing material build-up. It features a unique design that allows debris to be expelled from the pulley’s surface, ensuring that the belt remains clean and operational. This type of pulley is especially useful in applications where the conveyor belt is exposed to loose or sticky materials.
Importance of Selecting the Right Pulley Type
- Enhanced Efficiency
Choosing the appropriate types of conveyor belt pulleys can significantly enhance the efficiency of a conveyor system. For example, selecting a drive pulley with the right surface coating can reduce slippage, ensuring smooth and continuous operation. This minimizes downtime and maximizes throughput, leading to increased productivity. - Safety Improvements
Safety is a paramount concern in any industrial setting. Selecting the right tension pulley, for instance, ensures that the belt is properly tensioned, preventing potential hazards such as belt breakage or misalignment. A well-tensioned belt reduces the risk of accidents, protecting both personnel and equipment. - Operational Suitability
Each pulley type is designed to cater to specific operating conditions. For instance, a motorized pulley is ideal for environments where space is limited and maintenance needs to be minimized. By choosing pulleys that match the operational requirements, businesses can ensure that their conveyor systems operate smoothly and efficiently. - Extended Equipment Life
The right pulley type can extend the life of both the pulleys and the conveyor belt. For example, a snub pulley increases the belt’s contact with the drive pulley, reducing wear and tear by providing better grip and reducing slippage. This leads to less frequent replacements and lower maintenance costs. - Cost-Effectiveness
While the initial investment in high-quality pulleys may be higher, the long-term benefits in terms of reduced maintenance, fewer replacements, and improved efficiency make it a cost-effective choice. For example, a wing pulley that prevents material build-up reduces the need for frequent cleaning and maintenance, thereby lowering operational costs.
Understanding the significance of conveyor belt pulley types is essential for optimizing the performance, safety, and cost-effectiveness of conveyor systems. By selecting the appropriate pulley types for specific functions and operating conditions, businesses can enhance their operational efficiency, ensure safety, and extend the lifespan of their equipment.
Classification and Functions of Conveyor Belt Pulley Types
Understanding the various belt conveyor pulley types is essential for optimizing the performance and efficiency of conveyor systems. Each type of pulley plays a specific role in the operation of the conveyor belt, from driving the belt to maintaining its tension and direction. Here we delve into the classification and functions of the main types of conveyor belt pulleys.
Drive Pulley (Head Pulley)
The drive pulley, also known as the head pulley, is a key component in driving the conveyor belt and moving the material. This pulley is usually located at the discharge end of the conveyor belt and is driven by a motor. It provides the necessary force to keep the belt moving.
- Role in Driving the Conveyor Belt and Moving the Material
The drive pulley transmits power from the motor to the conveyor belt, allowing the belt to move and transport materials. It plays a crucial role in the overall efficiency of the conveyor system, ensuring a continuous and smooth movement of the belt. - Surface Coatings for Increased Friction
To enhance grip and prevent slippage, drive pulleys often feature surface coatings such as chevron and diamond patterns. These coatings increase friction between the pulley and the belt, ensuring reliable operation even under heavy loads and adverse conditions.
Tension Pulley (Take-Up Pulley)
The tension pulley, or take-up pulley, functions as a mechanism to adjust the belt’s tension. Proper tension is critical for the conveyor belt to operate effectively and avoid issues such as slippage and misalignment.
- Functions as a Mechanism to Adjust the Belt’s Tension
The tension pulley is designed to maintain the correct tension in the conveyor belt. It compensates for changes in belt length due to stretch or wear and helps in keeping the belt tight and aligned. - Importance in Maintaining Optimal Tension
Maintaining optimal tension is essential to prevent slippage and ensure smooth operation. Examples include:
- Preventing the belt from sagging, which can cause misalignment and operational inefficiencies.
- Reducing wear and tear on the belt and other components, extending their lifespan.
- Ensuring consistent contact with drive and snub pulleys for effective power transmission.
- Minimizing the risk of belt breakage by distributing tension evenly across the belt.
- Enhancing overall system reliability by maintaining a stable and efficient conveyor belt operation.
Motorized Pulley (Motor Drum)
The motorized pulley, or motor drum, integrates the roller and the transmission device into a single unit. This design offers several benefits, particularly in terms of efficiency and space-saving.
- Integrated Design Combining the Roller and the Transmission Device
The motorized pulley encapsulates the motor within the pulley itself, eliminating the need for external motors and gearboxes. This integration simplifies the conveyor system and reduces installation and maintenance efforts. - Benefits like Enhanced Efficiency and Space-Saving Designs
Examples include:
- Reducing the overall footprint of the conveyor system, making it suitable for compact spaces.
- Enhancing system efficiency by minimizing power loss between the motor and the pulley.
- Providing better protection for the motor against dust, dirt, and moisture, leading to increased durability.
- Lowering maintenance requirements due to fewer exposed moving parts.
- Simplifying the installation process, as fewer components need to be aligned and connected.
Snub Pulley
The snub pulley increases the contact area between the belt and the drive pulley. This additional contact is essential for maximizing the drive power and ensuring efficient operation in high-torque environments or where contamination is a concern.
- Increases the Contact Area Between the Belt and the Drive Pulley
By wrapping the belt around a larger portion of the drive pulley, the snub pulley enhances the frictional grip, reducing the risk of slippage. - Essential for High Drive Power Environments or Where Contamination is a Concern
In environments with high drive power requirements or potential contamination, the snub pulley ensures that the belt maintains adequate contact with the drive pulley, providing reliable operation.
Bend Pulley
The bend pulley facilitates changing the direction of the belt in looped conveyor systems. Its design is typically lighter due to lower tension requirements compared to drive and snub pulleys.
- Facilitates Changing the Direction of the Belt
The bend pulley allows the conveyor belt to change direction smoothly, ensuring that the material flow is continuous and uninterrupted. - Lighter Design Due to Less Tension Requirements
Since bend pulleys are not subjected to the same tension levels as drive pulleys, they are often designed to be lighter and more cost-effective.
Wing Pulley
The wing pulley focuses on self-cleaning properties to maintain belt traction. Various types, including spiral wing and herringbone wing pulleys, are designed for different clearing needs.
- Focus on Self-Cleaning Properties
The wing pulley’s design allows debris to be expelled from the pulley surface, preventing build-up and ensuring that the belt remains clean and operational. - Various Types for Different Clearing Needs
Types like spiral wing and herringbone wing pulleys are tailored to specific applications, providing efficient cleaning and maintaining optimal belt performance.
Magnetic Pulley
The magnetic pulley is utilized for magnetic or iron removal in beneficiation lines. It is built with quality steel and permanent magnets to efficiently remove ferrous debris from the material stream.
- Utilized for Magnetic or Iron Removal
Magnetic pulleys are essential in industries where removing iron and other magnetic materials from the conveyor belt is necessary to protect downstream equipment and ensure product purity. - Built with Quality Steel and Permanent Magnets
These pulleys are constructed using high-quality materials to ensure durability and effective operation in harsh industrial environments.
Understanding the classification and functions of various conveyor belt pulley types is crucial for optimizing conveyor system performance. Each pulley type serves a specific purpose, and selecting the right type based on operational needs can enhance efficiency, safety, and reliability in industrial applications.
Heavy-Duty Conveyor Belt Pulley Types
Heavy-duty conveyor belt pulley types are designed to withstand the rigorous demands of industrial environments. These pulleys are built to handle strenuous conditions, ensuring the reliability and efficiency of conveyor systems even under the most challenging circumstances. In this section, we will provide an overview of these robust pulleys and discuss their significance in minimizing downtime and extending their operational life.
Heavy-Duty Pulleys Designed for Strenuous Conditions
Heavy-duty conveyor belt pulleys are specifically engineered to endure the stresses of high-load, high-speed, and continuous operation settings. They are commonly used in industries such as mining, construction, and heavy manufacturing, where the demands on conveyor systems are exceptionally high. These pulleys are characterized by their durable construction, which includes features such as reinforced shafts, heavy-duty bearings, and high-quality materials.
The Significance of Robust Construction in Minimizing Downtime and Extending Pulley Life
Reinforced Shafts
Heavy-duty pulleys are equipped with reinforced shafts that provide extra strength and durability. This reinforcement is crucial in preventing shaft bending or breaking under heavy loads, ensuring that the pulley can handle continuous operation without failure.
Heavy-Duty Bearings
The use of heavy-duty bearings in these pulleys is essential for handling high rotational speeds and loads. These bearings reduce friction and wear, allowing the pulley to operate smoothly and efficiently for extended periods.
High-Quality Materials
Heavy-duty conveyor belt pulleys are constructed from high-quality materials such as alloy steel or stainless steel. These materials offer superior resistance to wear, corrosion, and impact, which are common in harsh industrial environments.
Enhanced Lagging
The lagging on heavy-duty pulleys is often enhanced with materials like ceramic or rubber composites. This enhancement increases the friction between the pulley and the conveyor belt, preventing slippage and improving traction.
Precision Engineering
Heavy-duty pulleys benefit from precision engineering, which ensures that all components are manufactured to exact specifications. This precision reduces the likelihood of mechanical failures and improves the overall performance of the pulley.
The significance of robust construction in heavy-duty conveyor belt pulley types cannot be overstated. These pulleys are designed to endure the most demanding industrial conditions, offering enhanced durability, reliability, and efficiency. By minimizing downtime and extending the operational life of the pulleys, industries can achieve greater productivity and cost-effectiveness. Understanding the features and benefits of heavy-duty pulleys is essential for selecting the right components for any high-demand conveyor system.
Conveyor Belt Pulley Types:Conveyor Head and Tail Pulley Dynamics
Understanding the dynamics of head and tail pulleys is crucial for optimizing the performance of conveyor systems. These pulleys play essential roles in material discharge and belt tensioning, which directly affect the efficiency and reliability of the conveyor. This section examines the specific functions of head and tail pulleys and discusses the types of lagging and materials used to enhance their performance.
The Roles of Head and Tail Pulleys in Material Discharge and Belt Tensioning
Head Pulley
The head pulley, also known as the drive pulley, is located at the discharge end of the conveyor belt. Its primary role is to drive the belt and facilitate the discharge of materials.
- Driving the Conveyor Belt
The head pulley is connected to a motor, which powers the conveyor belt. By transmitting power from the motor to the belt, the head pulley ensures continuous movement of the belt and the materials it carries. This movement is critical for maintaining a steady flow of materials in industrial operations. - Facilitating Material Discharge
At the discharge end, the head pulley helps in the smooth unloading of materials from the conveyor belt. The design and position of the head pulley ensure that materials are discharged efficiently, reducing spillage and ensuring that the process remains clean and orderly.
Tail Pulley
The tail pulley is located at the loading end of the conveyor system. Its primary role is to provide tension to the belt and guide it back to the loop for continuous operation.
- Providing Belt Tension
The tail pulley helps maintain the appropriate tension in the conveyor belt. Proper tension is essential to prevent the belt from sagging or slipping off the track, ensuring smooth operation and reducing wear and tear on the belt. - Guiding the Belt
As the belt moves back from the discharge end to the loading end, the tail pulley ensures that it remains aligned and properly guided. This alignment is crucial for preventing misalignments that can lead to operational inefficiencies and increased maintenance needs.
Specific Types of Lagging and Materials Used for Each Pulley
Types of Lagging
Lagging refers to the material applied to the surface of pulleys to increase friction and grip between the pulley and the conveyor belt. Different types of lagging are used depending on the operational requirements and environmental conditions.
Rubber Lagging
Rubber lagging is commonly used for both head and tail pulleys. It provides excellent grip and is suitable for general-purpose applications.
Ceramic Lagging
Ceramic lagging is used in high-tension and heavy-load applications. It offers superior abrasion resistance and durability.
Diamond Lagging
Diamond lagging, characterized by its diamond-shaped pattern, enhances grip and water-shedding capabilities.
Materials Used
The materials used for constructing head and tail pulleys significantly impact their performance and longevity. High-quality materials ensure that the pulleys can withstand the operational stresses they encounter.
Steel
Steel is a common material for pulley construction due to its strength and durability. It is suitable for most industrial applications where heavy loads and high speeds are common.
Stainless Steel
Stainless steel is used in environments where corrosion resistance is crucial, such as food processing and pharmaceuticals.
Aluminum
Aluminum is used for pulleys in lightweight applications where reducing the overall weight of the conveyor system is essential.
Composite Materials
Composite materials combine different materials to enhance specific properties such as strength, weight, and corrosion resistance.
Rubber-Coated Pulleys
Rubber coatings are applied to pulleys to improve their grip and protect them from wear and tear.
Understanding the dynamics of conveyor head and tail pulleys is essential for optimizing material discharge, belt tensioning, and overall conveyor system efficiency. By selecting the appropriate types of pulleys in belt conveyor, lagging, and materials, industries can enhance the performance and longevity of their conveyor systems, ensuring reliable and efficient operations.
Selection Criteria for Conveyor Belt Pulley Types
Selecting the right types of pulley in conveyor belt is crucial for ensuring the efficient and reliable operation of conveyor systems. The choice of pulleys can significantly impact the performance, maintenance, and lifespan of the conveyor system. In this section, we will explore the factors to consider when selecting pulleys for different conveyor setups and how material, environmental conditions, and operational requirements influence pulley choice.
Factors to Consider When Selecting Pulleys for Different Conveyor Setups
Load Requirements
The load that the conveyor system will handle is a primary factor in selecting the appropriate pulley. Heavy-duty applications require pulleys with higher load capacities and reinforced construction.
Speed of Operation
The speed at which the conveyor belt operates influences the type of pulley needed. High-speed operations require pulleys that can maintain stability and reduce vibrations.
Belt Tension
Proper belt tension is critical for preventing slippage and maintaining alignment. The pulley must be able to withstand the tension forces exerted by the belt.
Environmental Conditions
The operating environment, including temperature, moisture, and exposure to chemicals, affects the choice of pulley materials and coatings.
Maintenance Requirements
The ease of maintenance and availability of spare parts are important considerations. Pulleys that require minimal maintenance and have readily available parts reduce downtime.
Influence of Material, Environmental Conditions, and Operational Requirements on Pulley Choice
Material Selection
The material of the pulley affects its durability, weight, and resistance to wear and corrosion. Common materials include steel, stainless steel, aluminum, and composites.
Environmental Conditions
Different environments present unique challenges such as extreme temperatures, humidity, and exposure to chemicals. The chosen pulley must withstand these conditions without compromising performance.
Operational Requirements
The specific requirements of the operation, such as continuous use, heavy loads, and precise movement, dictate the type of pulley needed. Each application may require specialized pulleys to meet these demands.
Lagging Type
The type of lagging on the pulley surface can enhance grip, reduce wear, and improve performance in specific applications. Options include rubber, ceramic, and diamond-patterned lagging.
Customizability and Adaptability
The ability to customize pulleys to specific needs and the adaptability of the pulley design to different setups are crucial for optimizing performance.
The selection of conveyor belt pulley types is influenced by various factors including load requirements, speed of operation, belt tension, environmental conditions, and maintenance needs. By carefully considering these factors and the influence of materials, environmental conditions, and operational requirements, industries can select pulleys that optimize the performance, reliability, and longevity of their conveyor systems. Understanding these criteria ensures that the right pulleys are chosen for specific applications, leading to improved efficiency and reduced operational costs.
FAQs About Conveyor Belt Pulley Types
Conveyor belt pulleys come in various types, each designed for specific functions within a conveyor system. The primary types include:
Drive Pulley (Head Pulley): This pulley is located at the discharge end of the conveyor. It drives the conveyor belt and moves the material along the system.
Tension Pulley (Take-Up Pulley): This pulley adjusts the tension of the conveyor belt, ensuring it remains taut and aligned.
Motorized Pulley (Motor Drum): Integrates the motor and the pulley into a single unit, enhancing efficiency and saving space.
Snub Pulley: Increases the belt’s contact area with the drive pulley, improving grip and preventing slippage.
Wing Pulley: Designed for self-cleaning, it prevents material build-up on the pulley surface, maintaining belt traction.
Magnetic Pulley: Used for removing ferrous contaminants from the material stream, commonly found in recycling and beneficiation applications.
Each type plays a crucial role in maintaining the efficiency and functionality of conveyor systems, tailored to meet specific operational needs.
The head pulley and tail pulley are two essential components of a conveyor belt system, each serving distinct functions:
Head Pulley (Drive Pulley): The head pulley is positioned at the discharge end of the conveyor belt. Its primary function is to drive the belt and facilitate the discharge of materials. Connected to a motor, it powers the conveyor system and ensures the continuous movement of the belt.
Tail Pulley: The tail pulley is located at the loading end of the conveyor system. Its main role is to provide tension to the conveyor belt, ensuring it remains taut and aligned. The tail pulley helps guide the belt back into the system loop for consistent and smooth operation.
The head pulley is responsible for the driving force and material discharge, whereas the tail pulley focuses on maintaining belt tension and alignment, both crucial for the efficient operation of the conveyor system.
A deflector pulley, also known as a guide or deflection pulley, is used in conveyor belt systems to change the direction of the belt or to guide it along a specific path. Unlike drive or tension pulleys, deflector pulleys do not impart motion or tension to the belt. Instead, they ensure that the belt follows a predetermined route, especially in complex conveyor setups where space constraints or operational requirements necessitate changes in direction.
Deflector pulleys are typically used in situations where the conveyor belt needs to navigate around obstacles or machinery, ensuring smooth transitions and maintaining the belt’s alignment. By strategically placing deflector pulleys, operators can optimize the conveyor layout for maximum efficiency and space utilization, making them an essential component in versatile conveyor system designs.
A snub pulley is an integral component in belt conveyor systems, primarily used to increase the belt’s contact area with the drive pulley. This increased contact enhances the frictional grip between the belt and the drive pulley, preventing slippage and improving the overall efficiency of the conveyor system.
The snub pulley is typically positioned close to the drive pulley, on the return side of the belt. By wrapping the belt around a larger portion of the drive pulley, the snub pulley ensures that the belt maintains adequate tension and traction. This is especially important in high-torque applications or environments with heavy loads, where maintaining consistent power transmission is crucial.
Additionally, snub pulleys help in adjusting the belt’s path and alignment, contributing to the smooth operation of the conveyor system. Their use is vital in applications requiring precise control and reliability, reducing the risk of operational disruptions and maintenance issues.
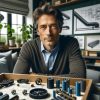
Jordan Smith, a seasoned professional with over 20 years of experience in the conveyor system industry. Jordan’s expertise lies in providing comprehensive solutions for conveyor rollers, belts, and accessories, catering to a wide range of industrial needs. From initial design and configuration to installation and meticulous troubleshooting, Jordan is adept at handling all aspects of conveyor system management. Whether you’re looking to upgrade your production line with efficient conveyor belts, require custom conveyor rollers for specific operations, or need expert advice on selecting the right conveyor accessories for your facility, Jordan is your reliable consultant. For any inquiries or assistance with conveyor system optimization, Jordan is available to share his wealth of knowledge and experience. Feel free to reach out at any time for professional guidance on all matters related to conveyor rollers, belts, and accessories.