Efficient Coal Handling with Coal Tripper Systems
Coal trippers are essential components in coal handling systems, responsible for transferring coal from main conveyors to various destinations such as bunkers or storage yards. Understanding the operation, design, and applications of coal trippers is crucial for optimizing coal handling processes. This article will explore the various aspects of coal trippers, including their relation to shuttle conveyors, reversing conveyors, and reversible conveyor belts. Additionally, it will cover shuttle conveyor design and insights from FEECO International. By examining these elements, readers will gain a comprehensive understanding of coal trippers and their significance in efficient coal handling operations.
Importance of Coal Tripper in Coal Handling
Coal trippers are indispensable in coal handling systems, ensuring the seamless transfer of coal from main conveyors to specific destinations such as bunkers or storage yards. Their role is crucial in maintaining the efficiency and effectiveness of coal handling operations. This section delves into the fundamental importance of coal trippers and their significant impact on coal handling systems.
Ensuring Efficient Coal Transfer
Coal trippers are designed to transfer coal from main conveyors to various points along the conveyor system. This capability is essential for distributing coal efficiently across different storage locations. For example, in a power plant, coal needs to be distributed evenly to multiple bunkers to ensure a steady supply of fuel for combustion. Coal trippers facilitate this distribution, ensuring that coal handling is uninterrupted and efficient.
In practical terms, coal trippers can be observed in the operations of companies like Arch Coal Inc., where they utilize advanced coal tripper systems to manage the distribution of coal within their facilities. By deploying coal trippers, they achieve a seamless transfer of large quantities of coal, thus maintaining a steady flow and avoiding bottlenecks in the handling process.
Enhancing Operational Flexibility
One of the key advantages of coal trippers is their ability to enhance the operational flexibility of coal handling systems. By enabling coal to be discharged at multiple points along the conveyor, coal trippers provide the flexibility to store coal in various locations within a facility. This flexibility is particularly beneficial in large-scale operations where coal needs to be stored and managed in different sections of the facility.
For instance, at the Peabody Energy Corporation, coal trippers are used to manage coal storage efficiently. The coal tripper systems allow for the precise control of coal discharge, enabling Peabody Energy to optimize their storage strategies and ensure that coal is readily available for processing and shipping.
Improving Safety and Reliability
Safety and reliability are paramount in coal handling operations, and coal trippers contribute significantly to these aspects. By ensuring that coal is distributed evenly and efficiently, coal trippers help prevent the accumulation of coal at single points, which can lead to blockages and potential safety hazards. Additionally, modern coal trippers are equipped with advanced control systems that allow for precise operation and monitoring, further enhancing the safety and reliability of coal handling systems.
A notable example is the use of coal trippers by CONSOL Energy. Their coal handling facilities are equipped with state-of-the-art coal trippers that not only improve operational efficiency but also incorporate safety features such as emergency stop mechanisms and automated monitoring systems. These enhancements ensure that the coal handling process is both safe and reliable, reducing the risk of accidents and downtime.
Optimizing Space Utilization
Coal trippers play a crucial role in optimizing space utilization within coal handling facilities. By allowing coal to be discharged at various points, coal trippers enable the efficient use of available space for storage. This is particularly important in facilities with limited storage areas, where maximizing the use of space is essential for operational efficiency.
At Alpha Natural Resources, coal trippers are integral to their space optimization strategies. The ability to distribute coal across multiple storage areas ensures that Alpha Natural Resources can make the most of their available space, reducing the need for additional storage infrastructure and minimizing operational costs.
Supporting Large-Scale Operations
Large-scale coal handling operations, such as those at BHP Billiton, rely heavily on coal trippers to manage the vast quantities of coal being handled. Coal trippers are capable of handling large volumes of coal, ensuring that these operations can maintain a steady flow of coal from extraction to processing and storage. This capability is essential for meeting the high demands of large-scale operations and ensuring continuous productivity.
For example, BHP Billiton utilizes coal trippers in their coal mines to manage the transfer of coal from the mining site to the processing plants. The coal trippers ensure that the coal is transported efficiently and without interruption, supporting the company’s large-scale production goals and contributing to their overall operational success.
Coal trippers are integral to the efficiency and effectiveness of coal handling systems. Their ability to transfer coal to multiple locations, enhance operational flexibility, improve safety and reliability, optimize space utilization, and support large-scale operations makes them a vital component in the coal handling industry. Companies like Arch Coal Inc., Peabody Energy Corporation, CONSOL Energy, Alpha Natural Resources, and BHP Billiton demonstrate the significant impact of coal trippers on their operations, underscoring the essential role these systems play in the coal industry.
Coal Tripper and Shuttle Conveyors
Functionality of Shuttle Conveyors in Coal Handling
Shuttle conveyors are integral to coal tripper systems, providing the flexibility to move coal across different locations. These conveyors are designed to move forward and backward along a track, allowing for the precise placement of coal in various storage areas. This ability to shuttle back and forth is especially useful in coal handling systems where coal needs to be distributed to multiple storage bunkers or silos efficiently.
Shuttle conveyors work by utilizing a motor-driven mechanism that allows them to travel along a set path, carrying coal from the main conveyor to designated drop-off points. The shuttle conveyor can be programmed to stop and discharge coal at specific intervals, ensuring even distribution across the storage area. This operation minimizes the need for manual handling, reduces the risk of spillage, and increases overall efficiency.
For example, at the Rio Tinto coal handling facility, shuttle conveyors are used to manage the distribution of coal from the main conveyor to various storage points. The use of shuttle conveyors in conjunction with coal trippers ensures that coal is evenly spread out, optimizing the storage capacity and maintaining a steady flow of coal to the processing plants.
The advantages of using shuttle conveyors in coal handling systems are numerous. They provide a high degree of flexibility, allowing coal to be transported to various locations without the need for additional conveyor systems. This flexibility not only improves operational efficiency but also reduces the costs associated with installing and maintaining multiple conveyor lines. Additionally, shuttle conveyors enhance safety by reducing the need for manual intervention in the coal handling process, thereby minimizing the risk of accidents and injuries.
Integration of Shuttle Conveyors with Coal Trippers
Understanding how shuttle conveyors integrate with coal trippers is essential for optimizing coal transport. The integration of these two systems allows for a seamless transfer of coal from the main conveyor to the shuttle conveyor, and then to the designated storage points via the coal tripper. This integration ensures that coal is handled efficiently and distributed evenly across the storage area.
The mechanics of integrating shuttle conveyors with coal trippers involve precise coordination between the movement of the shuttle conveyor and the operation of the coal tripper. The coal tripper discharges coal onto the shuttle conveyor, which then moves the coal to the desired location. This coordinated movement requires advanced control systems to ensure that the shuttle conveyor and coal tripper operate in sync, preventing any delays or interruptions in the coal handling process.
For instance, in the operations of Anglo American, a leading mining company, shuttle conveyors and coal trippers are integrated to enhance the efficiency of their coal handling systems. The coal tripper transfers coal from the main conveyor to the shuttle conveyor, which then distributes the coal to various storage bunkers. This integration allows Anglo American to manage their coal storage more effectively, ensuring that the coal is evenly distributed and readily available for processing.
The benefits of integrating shuttle conveyors with coal trippers extend beyond operational efficiency. This integration also improves the reliability of the coal handling system by reducing the likelihood of bottlenecks and ensuring a continuous flow of coal. Additionally, the use of shuttle conveyors and coal trippers together can help minimize wear and tear on the conveyor system, as the coal is evenly distributed and does not accumulate in a single location.
Another example of successful integration can be seen at the BHP Billiton coal handling facility. By combining the capabilities of shuttle conveyors and coal trippers, BHP Billiton has been able to optimize their coal handling processes, reducing downtime and increasing throughput. The integrated system allows for precise control over coal distribution, ensuring that the coal is efficiently transferred from the main conveyor to the storage bunkers.
The integration of shuttle conveyors with coal trippers is a critical component of modern coal handling systems. It enhances the flexibility, efficiency, and reliability of coal transport, ensuring that coal is effectively managed and distributed throughout the storage area. Companies like Rio Tinto, Anglo American, and BHP Billiton demonstrate the practical benefits of this integration, showcasing the significant improvements in coal handling operations that can be achieved through the use of shuttle conveyors and coal trippers.
Coal Tripper and Reversing Conveyor Systems
Overview of Reversing Conveyor Systems
Reversing conveyor systems are a pivotal component in modern coal handling operations, providing the ability to transport coal in both directions along a single conveyor path. This bidirectional capability significantly enhances the flexibility and efficiency of coal handling processes. By allowing coal to be moved to and from various points along the conveyor line, reversing conveyor systems facilitate better utilization of storage spaces and streamline coal distribution.
Reversing conveyor systems operate through a combination of motorized pulleys and control mechanisms that can change the direction of the belt’s movement. This adaptability is particularly useful in facilities where space is limited or where coal needs to be routed to multiple destinations from a central point. For instance, in a large-scale coal processing plant, reversing conveyors can transport coal from the unloading area to various storage silos and then reverse the flow to feed the coal into the processing units as needed.
One notable example of reversing conveyor systems in action is at the facilities of Murray Energy Corporation. Murray Energy employs these systems to manage the complex logistics of their coal handling operations. By using reversing conveyors, they can efficiently direct coal to different storage locations and ensure a steady supply to their processing plants, thereby optimizing their overall workflow and reducing downtime.
Role of Coal Trippers in Reversing Conveyor Systems
Directional Control of Coal Flow
Coal trippers play a crucial role in reversing conveyor systems by enabling the precise directional control of coal flow. Coal trippers are designed to divert coal from the main conveyor belt to specific drop-off points, which is essential for the effective distribution of coal within a facility. In a reversing conveyor system, coal trippers must be able to function seamlessly regardless of the direction of the belt’s movement. This capability ensures that coal can be distributed efficiently and accurately to various locations within the facility, enhancing overall operational efficiency.
Flexible and Efficient Transfer
The integration of coal trippers into reversing conveyor systems allows for the flexible and efficient transfer of coal to multiple storage points. For example, at Consol Energy’s Bailey Mine complex, coal trippers are used in conjunction with reversing conveyors to manage the distribution of coal from the main conveyor to various bunkers and silos. This setup ensures that coal is always available where it is needed, improving the reliability and efficiency of the coal handling process. By being able to direct coal flow to different locations, coal trippers enhance the flexibility of the system, allowing it to adapt to changing operational needs.
Advanced Control Systems
Coal trippers in reversing conveyor systems must be equipped with advanced control systems to synchronize with the directional changes of the conveyor belt. These controls ensure that the trippers can adjust their operations based on the current direction of the belt, maintaining consistent and accurate coal distribution. Additionally, modern coal trippers are designed with robust safety features, such as emergency stop mechanisms and automated diagnostics, to enhance operational safety and reliability. These advanced control systems are critical in preventing operational disruptions and ensuring the seamless transfer of coal, regardless of the direction of the conveyor belt.
Case Study: Peabody Energy’s North Antelope Rochelle Mine
At Peabody Energy’s North Antelope Rochelle Mine, one of the largest coal mines in the world, the use of coal trippers in their reversing conveyor systems has significantly boosted operational efficiency. The coal trippers allow for precise control over coal distribution, ensuring that coal is delivered to the right locations at the right times. This integration helps Peabody Energy maintain high levels of productivity and minimize the risk of coal handling bottlenecks. The ability to manage large volumes of coal efficiently and safely is a testament to the effectiveness of integrating coal trippers with reversing conveyor systems.
Customization for Operational Requirements
The design and engineering of coal trippers for reversing conveyor systems often involve customization to meet specific operational requirements. For instance, the coal trippers used by Arch Resources in their Leer Mine are specifically tailored to handle the high throughput demands and the unique layout of their facility. This customization ensures that the coal trippers can operate effectively within the reversing conveyor system, providing reliable and efficient coal handling. By customizing coal trippers to fit the specific needs of a facility, companies can optimize their coal handling processes, improve operational efficiency, and reduce downtime.
Practical Benefits and Industry Examples
Coal trippers are essential components of reversing conveyor systems, enabling the flexible and efficient distribution of coal within coal handling facilities. Companies like Murray Energy Corporation, Consol Energy, Peabody Energy, and Arch Resources demonstrate the practical benefits of integrating coal trippers with reversing conveyors. These integrations showcase improvements in operational efficiency, reliability, and safety. Through advanced control systems, robust design, and customization, coal trippers ensure that coal handling operations can meet the demands of modern coal processing and distribution. This capability is vital for maintaining high productivity levels and ensuring the smooth operation of coal handling systems across the industry.
Coal Tripper and Reversible Conveyor Belts
Benefits of Reversible Conveyor Belts
Reversible conveyor belts are a significant innovation in the coal handling industry, offering the ability to transport coal in both directions along the same conveyor path. This bidirectional capability increases operational efficiency and flexibility, allowing for better space utilization and more effective coal management. Reversible conveyor belts are particularly useful in facilities where coal needs to be transported to multiple locations, as they eliminate the need for multiple conveyor systems and reduce the complexity of coal handling operations.
One of the primary benefits of reversible conveyor belts is their ability to streamline the coal transport process. By allowing coal to be moved to and from different points along the conveyor line, these belts facilitate efficient coal distribution without requiring extensive infrastructure changes. For example, in a large coal processing plant operated by Consol Energy, reversible conveyor belts are used to transport coal from the unloading area to various storage silos and then reverse the direction to feed the coal into processing units. This setup ensures a continuous flow of coal, reducing downtime and improving overall productivity.
Additionally, reversible conveyor belts enhance the flexibility of coal handling systems. They can be easily adapted to changing operational needs, such as redirecting coal to different storage locations based on demand fluctuations. This adaptability is crucial for maintaining efficient operations in dynamic environments where coal supply and demand can vary. At Peabody Energy’s North Antelope Rochelle Mine, one of the world’s largest coal mines, reversible conveyor belts play a vital role in managing the vast quantities of coal extracted daily. The ability to reverse the direction of coal transport allows for more efficient stockpile management and optimized use of available storage space.
The operational efficiency provided by reversible conveyor belts also translates into cost savings. By reducing the need for multiple conveyor systems and simplifying the coal handling process, companies can lower maintenance costs and minimize the risk of equipment failure. Moreover, the enhanced control over coal distribution reduces the likelihood of spillage and waste, further contributing to cost savings. For instance, Arch Resources has implemented reversible conveyor belts at its Leer Mine to improve the efficiency and cost-effectiveness of its coal handling operations. This implementation has led to a significant reduction in operational costs and improved resource management.
Coal Trippers Enhancing Reversible Conveyor Belt Operations
Coal trippers play an essential role in enhancing the functionality of reversible conveyor belts by providing precise control over coal discharge locations. The integration of coal trippers with reversible conveyor belts allows for accurate and efficient coal distribution, ensuring that coal is delivered to the right locations at the right times.
Coal trippers are designed to divert coal from the main conveyor belt to specific drop-off points, which is crucial for effective coal handling in facilities with multiple storage locations. In a reversible conveyor belt system, coal trippers must be capable of operating seamlessly in both directions of belt movement. This bidirectional capability ensures that coal can be distributed evenly across the storage area, regardless of the conveyor belt’s direction.
For example, at BHP Billiton’s coal handling facilities, coal trippers are integrated with reversible conveyor belts to manage the distribution of coal from the main conveyor to various storage bunkers. The coal trippers allow for precise control over the discharge points, ensuring that coal is evenly distributed and readily available for processing. This integration not only enhances operational efficiency but also improves the reliability and safety of the coal handling process.
Coal trippers equipped with advanced control systems can synchronize with the directional changes of reversible conveyor belts, maintaining consistent and accurate coal distribution. These control systems allow for real-time monitoring and adjustments, ensuring optimal performance of the coal handling system. At the Alpha Natural Resources coal processing plant, the integration of coal trippers with reversible conveyor belts has resulted in improved operational control and reduced downtime. The advanced control systems used in these coal trippers enable precise adjustments to the coal discharge locations, ensuring efficient coal handling and distribution.
Furthermore, coal trippers contribute to the longevity and durability of reversible conveyor belt systems by preventing the accumulation of coal at single points. This even distribution reduces wear and tear on the conveyor belt, extending its operational life and reducing maintenance costs. For instance, the use of coal trippers in combination with reversible conveyor belts at the Murray Energy Corporation’s coal mines has led to significant improvements in equipment durability and reduced maintenance requirements.
The integration of coal trippers with reversible conveyor belts is a critical component of modern coal handling systems. By providing precise control over coal discharge locations, coal trippers enhance the efficiency, flexibility, and reliability of reversible conveyor belt operations. Companies like Consol Energy, Peabody Energy, Arch Resources, BHP Billiton, Alpha Natural Resources, and Murray Energy Corporation showcase the practical benefits of this integration, demonstrating significant improvements in coal handling efficiency, operational control, and cost-effectiveness.
Key Design Considerations for Coal Tripper Systems
Key Factors in Shuttle Conveyor Design for Coal Trippers
Designing shuttle conveyors for coal trippers involves several critical factors that ensure optimal performance and reliability. The effectiveness of a coal tripper system largely depends on the careful consideration of these design elements.
Load Capacity and Distribution
One of the primary factors in shuttle conveyor design for coal trippers is the load capacity. The conveyor must be capable of handling the weight and volume of coal being transported. This requires precise calculations and robust materials to ensure the conveyor can support heavy loads without compromising performance. For example, the shuttle conveyors used by Alpha Natural Resources are designed to handle high-capacity loads, ensuring efficient coal transport across their facilities.
Structural Integrity and Durability
The structural integrity and durability of the shuttle conveyor are paramount, especially given the harsh operating environments of coal handling. Materials used in the construction of these conveyors must be resistant to wear, corrosion, and impact. High-strength steel frames and reinforced components are commonly employed to enhance durability. At Arch Resources, shuttle conveyors with reinforced truss frames have been implemented to withstand the rigorous demands of their coal handling operations.
Mobility and Flexibility
Shuttle conveyors must be designed for mobility and flexibility to effectively integrate with coal tripper systems. This includes the ability to move along tracks or rails to different discharge points. Mobility is essential for ensuring that coal can be distributed to multiple storage locations efficiently. Companies like BHP Billiton utilize shuttle conveyors that can travel along extensive rail systems, providing the flexibility needed for large-scale coal handling operations.
Control Systems and Automation
Advanced control systems and automation play a crucial role in the operation of shuttle conveyors in coal tripper systems. These systems enable precise control over conveyor movement, speed, and coal discharge points. Integration with modern automation technologies allows for real-time monitoring and adjustments, enhancing the overall efficiency and safety of the coal handling process. For instance, Peabody Energy incorporates automated control systems in their shuttle conveyors to optimize coal distribution and minimize human intervention.
Safety Features
Safety is a critical consideration in the design of shuttle conveyors for coal trippers. Features such as emergency stop mechanisms, overload protection, and safety guards are essential to protect both the equipment and the operators. Ensuring that the conveyor meets all relevant safety standards and regulations is crucial for preventing accidents and ensuring smooth operations. Consol Energy’s coal handling facilities are equipped with shuttle conveyors that include comprehensive safety features, contributing to a safer working environment.
Customization and Efficiency in Coal Tripper Design
Customization in coal tripper design is essential for meeting specific operational needs and enhancing overall efficiency. Tailoring coal trippers to the unique requirements of a facility can lead to significant improvements in productivity and cost-effectiveness.
Tailored Design Solutions
Customizing coal tripper systems involves designing them to fit the specific layout, capacity, and operational requirements of the coal handling facility. This can include modifications to the size, shape, and configuration of the tripper to ensure optimal integration with existing infrastructure. For example, Murray Energy Corporation has implemented custom-designed coal trippers that are specifically tailored to the layout of their mines, resulting in improved coal transport and storage efficiency.
Enhanced Efficiency through Customization
Customized coal tripper designs can significantly enhance operational efficiency by optimizing the flow of coal and reducing bottlenecks. This includes designing trippers with features such as adjustable discharge points, variable speed controls, and integrated dust suppression systems. These enhancements help streamline the coal handling process, reducing downtime and increasing throughput. At the Leer Mine operated by Arch Resources, customized coal trippers with advanced control systems have led to a noticeable improvement in handling efficiency, contributing to higher productivity levels.
Case Study: FEECO International
FEECO International is renowned for its expertise in designing and manufacturing custom coal tripper systems. Their approach involves a detailed assessment of the client’s requirements, followed by the design and fabrication of tailored solutions. One notable example is the custom coal tripper system designed for a large coal processing facility in Australia. This system included a series of shuttle conveyors and coal trippers designed to maximize space utilization and improve the flow of coal from the mine to the processing plant. The result was a significant increase in operational efficiency and a reduction in overall handling costs.
Scalability and Future-Proofing
Another important aspect of customization is ensuring that coal tripper systems are scalable and future-proof. This involves designing trippers that can accommodate future expansions and changes in operational demands. By incorporating modular components and flexible design elements, coal tripper systems can be easily upgraded or modified as needed. At BHP Billiton’s coal handling facilities, scalable coal tripper systems have been implemented to allow for future growth and adaptability, ensuring long-term operational efficiency.
Data-Driven Design and Optimization
Utilizing data and advanced analytics in the design of coal tripper systems can further enhance customization and efficiency. By analyzing operational data, designers can identify areas for improvement and implement design changes that optimize performance. Companies like FEECO International use data-driven approaches to continuously refine their coal tripper designs, ensuring that they meet the evolving needs of the coal handling industry.
Key design considerations for coal trippers include load capacity, structural integrity, mobility, control systems, and safety features. Customizing these systems to meet specific operational needs can significantly enhance efficiency and productivity. Companies such as Alpha Natural Resources, Arch Resources, BHP Billiton, Peabody Energy, Consol Energy, Murray Energy Corporation, and FEECO International demonstrate the practical benefits of tailored coal tripper designs, showcasing improvements in coal handling operations, cost savings, and scalability.
Insights from FEECO International on Coal Trippers
Expertise of FEECO in Coal Tripper Systems
FEECO International is renowned for its expertise in designing and manufacturing coal tripper systems. With over six decades of experience, FEECO has established itself as a leader in providing innovative and efficient solutions for coal handling operations. Their coal tripper systems are designed to meet the specific needs of each client, ensuring optimal performance and reliability.
One of FEECO’s key contributions to the industry is their ability to customize coal tripper systems to suit various operational requirements. This customization is achieved through a detailed assessment of the client’s needs, followed by precise engineering and fabrication. For instance, FEECO developed a custom coal tripper system for a major coal processing plant in Australia. The system included a series of shuttle conveyors and coal trippers designed to maximize space utilization and improve the flow of coal from the mine to the processing plant. This tailored solution resulted in a significant increase in operational efficiency and a reduction in overall handling costs.
FEECO’s coal tripper systems are known for their durability and reliability. They use high-strength materials and advanced engineering techniques to ensure that their systems can withstand the harsh conditions of coal handling operations. This focus on durability is evident in the coal tripper systems used by Peabody Energy. By implementing FEECO’s robust coal trippers, Peabody Energy has been able to enhance the efficiency and reliability of their coal handling processes, reducing downtime and maintenance costs.
Another notable aspect of FEECO’s expertise is their integration of advanced control systems into their coal tripper designs. These control systems enable precise operation and monitoring, allowing for real-time adjustments and optimization. For example, at Consol Energy’s coal handling facilities, FEECO’s coal trippers are equipped with state-of-the-art control systems that provide operators with complete control over coal distribution. This integration has led to improved operational control and increased productivity.
FEECO also places a strong emphasis on safety in their coal tripper designs. Their systems are equipped with comprehensive safety features, such as emergency stop mechanisms, overload protection, and automated diagnostics. These features ensure that the coal handling process is safe for operators and reduces the risk of accidents. At the Alpha Natural Resources coal processing plant, FEECO’s coal trippers with enhanced safety features have contributed to a safer working environment, further demonstrating FEECO’s commitment to safety.
Contacting FEECO International for Coal Tripper Solutions
For personalized coal tripper solutions, FEECO International provides comprehensive support and consultation. They work closely with clients to understand their specific needs and develop tailored solutions that enhance efficiency and productivity. FEECO’s team of experts is available to assist with everything from initial design and engineering to installation and ongoing support.
Clients interested in FEECO’s coal tripper systems can contact them through their official email address at [email protected]. This email address provides direct access to FEECO’s customer service and technical support teams, ensuring that clients receive timely and effective assistance.
FEECO’s commitment to customer satisfaction is evident in their approach to client engagement. They offer on-site consultations and assessments to better understand the operational challenges faced by their clients. This hands-on approach allows FEECO to develop customized coal tripper solutions that address specific issues and improve overall efficiency. For example, FEECO conducted a site visit to a large coal mine operated by BHP Billiton to assess their coal handling needs. Based on this assessment, FEECO designed a custom coal tripper system that optimized coal flow and reduced operational costs, demonstrating the effectiveness of their personalized approach.
In addition to their email contact, FEECO maintains an informative website (www.feeco.com) where clients can learn more about their products and services. The website features detailed information on their coal tripper systems, including case studies, technical specifications, and client testimonials. This resource provides valuable insights into FEECO’s capabilities and the benefits of their coal tripper solutions.
FEECO International’s expertise in coal tripper systems, combined with their commitment to customization, durability, safety, and customer satisfaction, makes them a trusted partner in the coal handling industry. Companies like Peabody Energy, Consol Energy, Alpha Natural Resources, and BHP Billiton have benefited from FEECO’s innovative solutions and personalized approach. By contacting FEECO through their official channels, clients can access comprehensive support and tailored coal tripper solutions that enhance operational efficiency and productivity.
FAQs about Coal Tripper
A coal tripper is a mobile conveyor mechanism used in mining and coal handling operations. It is designed to distribute or “trip” coal to different locations along the conveyor system. The coal tripper allows for the precise placement of coal at designated points, ensuring efficient storage and processing. This equipment plays a crucial role in coal handling plants by enhancing the flexibility and functionality of conveyor belts, thus optimizing the overall workflow. Coal trippers are essential in maintaining consistent coal distribution, reducing manual labor, and increasing operational efficiency.
A tripper in mining refers to a movable conveyor system component that discharges material from the conveyor at designated points. Trippers are often used in bulk material handling operations, such as coal mining, to distribute materials evenly across storage areas or processing units. By directing the flow of mined materials to different locations, trippers enhance the efficiency and organization of mining operations. They are particularly valuable in ensuring that coal and other materials are evenly distributed, which helps in preventing blockages and maintaining a smooth production process.
A tripper conveyor works by incorporating a movable mechanism, known as a tripper, which travels along the length of the conveyor belt. This tripper is equipped with a discharge chute that can be positioned at various points along the belt. As the conveyor belt moves, the tripper can be activated to discharge material at the desired location. In coal handling, the tripper conveyor facilitates the controlled distribution of coal, ensuring that it is deposited precisely where needed. This system improves the efficiency of coal handling operations by minimizing the need for manual intervention and enabling automated control of material flow.
A coal conveyor is a system designed to transport coal from one location to another. These conveyors are a critical component of coal mining and handling operations, providing an efficient and reliable means of moving large quantities of coal. Coal conveyors can be either fixed or mobile and are often equipped with features such as trippers to enhance their functionality. The primary purpose of a coal conveyor is to ensure the continuous and smooth movement of coal, reducing the reliance on manual labor and improving overall operational efficiency. They play a vital role in the coal supply chain, from extraction to processing and storage.
Last Updated on August 8, 2024 by Jordan Smith
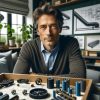
Jordan Smith, a seasoned professional with over 20 years of experience in the conveyor system industry. Jordan’s expertise lies in providing comprehensive solutions for conveyor rollers, belts, and accessories, catering to a wide range of industrial needs. From initial design and configuration to installation and meticulous troubleshooting, Jordan is adept at handling all aspects of conveyor system management. Whether you’re looking to upgrade your production line with efficient conveyor belts, require custom conveyor rollers for specific operations, or need expert advice on selecting the right conveyor accessories for your facility, Jordan is your reliable consultant. For any inquiries or assistance with conveyor system optimization, Jordan is available to share his wealth of knowledge and experience. Feel free to reach out at any time for professional guidance on all matters related to conveyor rollers, belts, and accessories.