Mastering Belt Conveyor Design Steps and Types
Designing a belt conveyor system requires a meticulous approach to ensure efficiency, safety, and durability. This blog series, titled “Exploring Belt Conveyor Design Steps,” aims to guide you through each crucial stage of the conveyor design process, from initial consultations with industry handbooks to the application of complex design calculations. We’ll cover structural considerations, material selections, and integrate the latest technological advancements. Each section of this series is crafted to help you understand the integral components and techniques essential for successful conveyor system implementation. Join us as we delve into the intricate belt conveyor design steps, ensuring you have the knowledge to develop a system tailored to your operational needs. Through this series, gain a deep understanding of the steps involved in designing an efficient and durable belt conveyor system.
Belt Conveyor Design Steps: Consulting the Handbook for Comprehensive Guidance
In the initial phase of the belt conveyor design steps, consulting the essential resources is crucial. The belt conveyor design handbook pdf serves as a cornerstone document, offering extensive information and guidelines necessary for understanding the full spectrum of conveyor design. This handbook includes detailed insights into industry standards, best practices, and technical specifications that are essential for designing an effective conveyor system.
Importance of the Handbook
Understanding the “belt conveyor design handbook pdf” is fundamental in grasping the core concepts and requirements of conveyor system design. It provides a solid foundation of knowledge that ensures all aspects of conveyor design are considered, from material selection to component specifications. The handbook lays out industry standards that help in maintaining consistency and safety across designs, making it an invaluable resource for both novice and experienced engineers.
Utilizing the Handbook Effectively
To maximize the utility of the belt conveyor design handbook during the design steps, it’s essential to integrate its guidelines from the start of the project. Here are some tips on how to use the handbook effectively:
- Start with a Thorough Read: Before beginning any design calculations or drawings, thoroughly read through the handbook to ensure you understand the basic principles and requirements.
- Refer Back Often: Use the handbook as a reference throughout the design process to check your work against industry standards and to ensure compliance with safety regulations.
- Apply Best Practices: Implement the best practices recommended in the handbook to enhance the efficiency and reliability of your conveyor system.
Belt Conveyor Design Steps: Applying Calculations from the Design Manual to Ensure Precision
In the belt conveyor design steps, applying precise calculations is critical for developing safe and effective conveyor systems. The “belt conveyor design guide calculations pdf” provides a detailed guide that covers all necessary mathematical formulas and approaches needed to accurately determine the dimensions, load capacities, and power requirements of a conveyor belt system.
Significance of Precise Calculations
Accurate calculations are the backbone of effective belt conveyor design steps. They ensure that the conveyor not only fits the intended space and handles the expected load but also operates efficiently and safely under all conditions. Precise calculations help in:
- Determining Load Capacity: Ensuring the conveyor can handle the maximum expected load without failure.
- Selecting Motor and Drive Configurations: Calculating the power requirements to choose the right motor size and drive mechanism to achieve optimal speed and torque.
- Designing for Safety and Durability: Incorporating safety factors and considering wear and tear over the conveyor’s lifespan.
Examples of Common Calculations
The “belt conveyor design calculations pdf” typically includes several types of essential calculations, which are pivotal in the belt conveyor design steps. Some common examples include:
- Belt Speed Calculation: Determines how fast the belt should move to efficiently transport material without spillage or excessive wear.
- Belt Width and Composition: Calculations to determine the optimal width and material of the belt based on the type and volume of material to be transported.
- Drive Force Calculations: Involves determining the necessary force required to move the conveyor belt and the load it carries, which influences motor and gearbox selection.
Utilizing these calculations during the belt conveyor design steps not only optimizes the efficiency of the system but also enhances its reliability and safety. By rigorously applying the principles outlined in the “belt conveyor design calculations pdf,” designers can ensure that their conveyor systems are well-suited to meet the operational demands of their specific industrial environments. This section of the blog highlights how crucial accurate calculations are to the successful implementation of a conveyor system design.
Belt Conveyor Design Steps: Structuring the Conveyor Belt System for Optimal Stability and Efficiency
One of the crucial belt conveyor design steps is structuring the conveyor belt system to ensure it is stable, efficient, and capable of meeting operational demands. This phase heavily relies on the principles laid out in the “design of belt conveyor pdf,” which provides extensive guidelines on how to construct a conveyor belt system with robust structural integrity.
Importance of Structural Design
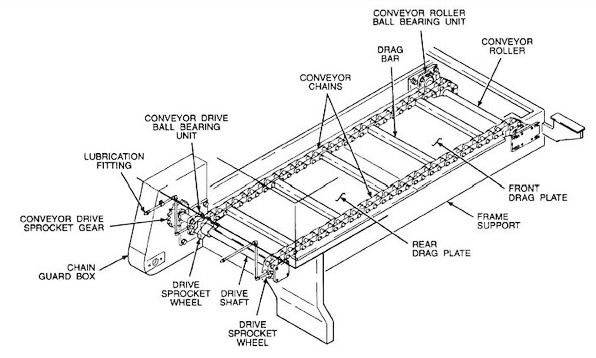
The structure of the conveyor belt is fundamental to the overall performance and longevity of the system. Key considerations in this aspect of the belt conveyor design steps include:
- Load Support: Ensuring the structure can support both static and dynamic loads without excessive deflection.
- Accessibility for Maintenance: Designing the structure so that critical components are easily accessible for maintenance and repair.
- Adaptability: Allowing for modifications such as expansions or changes in layout to accommodate future needs.
Utilizing Design of Belt Conveyor PDF
The “design of belt conveyor pdf” serves as an essential resource during this step. It offers detailed instructions and criteria for:
- Material Selection: Choosing the right materials for the frame and supports to ensure durability and resist environmental challenges like corrosion.
- Geometric Configuration: Guidelines on the arrangement of rollers, idlers, and pulleys to optimize the belt’s performance and minimize wear.
- Dynamic Analysis: Providing methods for analyzing the dynamic behavior of the conveyor under various loading conditions to predict potential issues before they occur.
By meticulously applying the guidance from the “design of belt conveyor pdf” during these belt conveyor design steps, engineers can create a conveyor system that not only meets the specific needs of their application but also operates reliably under anticipated working conditions. This section of the blog emphasizes how critical a well-thought-out structural design is to the success of a conveyor belt system, ensuring that it operates efficiently and remains stable throughout its service life.
Belt Conveyor Design Steps: Material and Component Selection for Long-Term Efficiency
In the belt conveyor design steps, selecting the right materials and components is crucial for ensuring the system’s long-term efficiency and durability. This part of the design process benefits greatly from insights provided in the “conveyor belt design book,” which offers comprehensive guidance on choosing materials that best suit the operational demands and environmental conditions of the conveyor system.
Selecting Materials with Guidance from the Conveyor Belt Design Book
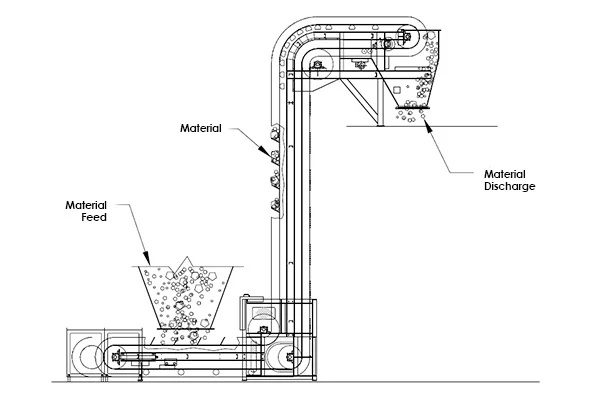
The “conveyor belt design book” plays a pivotal role in this phase of the belt conveyor design steps, as it contains detailed analyses of different materials used in conveyor belts, along with their pros and cons in various applications. Key material selection considerations include:
- Wear Resistance: Selecting materials that can withstand the specific types of wear to which the conveyor will be subjected, such as abrasion, corrosion, or impact.
- Environmental Compatibility: Choosing materials that are suited to the environmental conditions of the installation site, whether it involves exposure to chemicals, extreme temperatures, or moisture.
Factors in Choosing Durable and Efficient Components
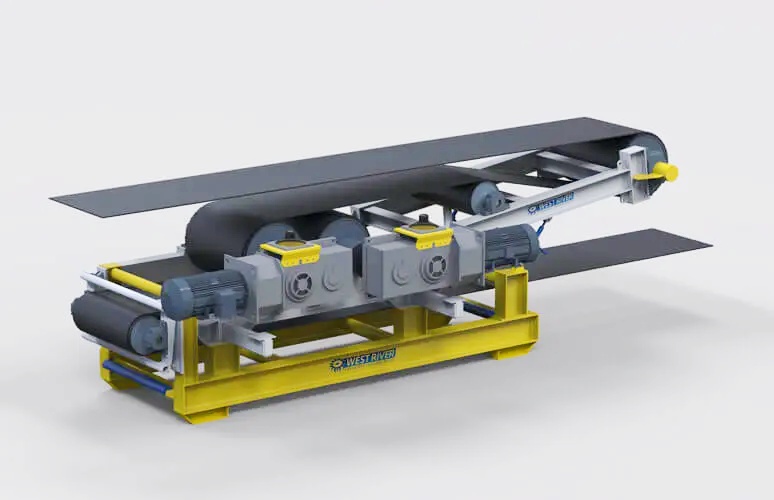
In addition to material selection, choosing the right components is equally important for the durability and efficiency of the conveyor system. These components include rollers, bearings, motors, and drive systems. Factors to consider include:
- Load Capacity: Components should be selected based on their ability to handle the expected load without failure.
- Energy Efficiency: Components such as motors and drives should be chosen for their energy efficiency to reduce operational costs and environmental impact.
- Maintenance Requirements: Selecting components that are easy to maintain and replace can significantly reduce downtime and maintenance costs.
Belt Conveyor Design Steps: Incorporating Advanced Techniques and Innovations for Optimal Performance
As part of the belt conveyor design steps, incorporating the latest advancements and innovative techniques is essential for enhancing the system’s performance and maintenance efficiency. This section explores how cutting-edge technologies can be integrated into conveyor belt design to address both current and future operational challenges.
Incorporating Cutting-Edge Technologies
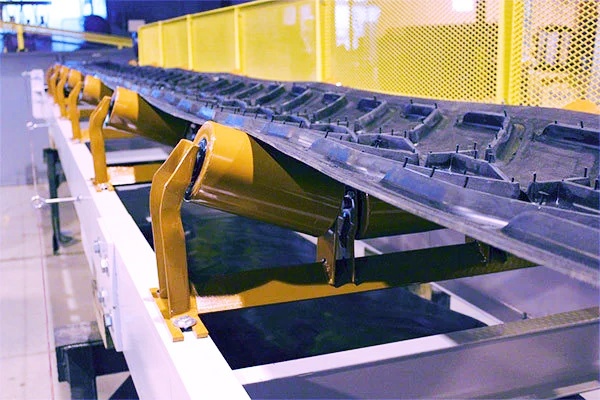
The latest technological innovations play a transformative role in the belt conveyor design steps. These include:
- Smart Conveyor Belts: Utilizing IoT (Internet of Things) sensors and RFID (Radio Frequency Identification) technology to monitor belt health, track materials, and optimize maintenance schedules.
- Energy-Efficient Motors: Applying the latest developments in motor technology to reduce energy consumption and increase the overall efficiency of the conveyor system.
- Self-Adjusting Systems: Implementing automated systems that can adjust belt tension and alignment in real-time to prevent slippage and reduce wear.
Optimizing Conveyor Belt Performance and Maintenance
Advanced techniques not only improve the performance of conveyor systems but also enhance their maintenance protocols, which are crucial for long-term operation. Innovations in this area include:
- Predictive Maintenance Tools: Advanced analytics and machine learning algorithms that predict when maintenance is needed, thereby preventing unexpected breakdowns and extending the lifespan of conveyor components.
- Modular Design Elements: Designs that allow for quick and easy replacement of parts and adaptability to changing operational needs without requiring a complete system overhaul.
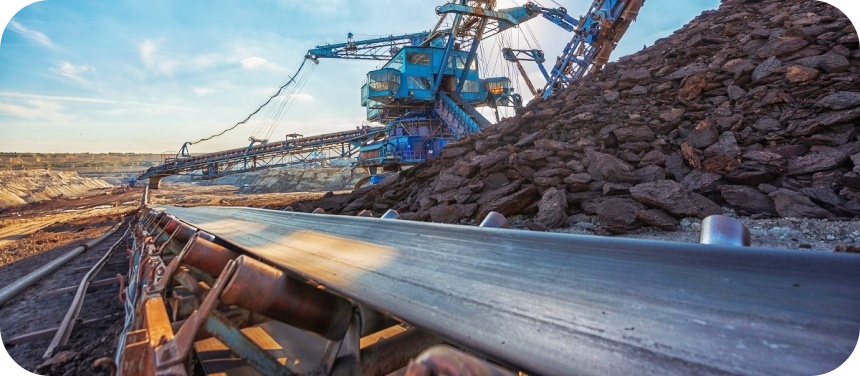
Belt Conveyor Design Steps: Implementing, Testing, and Refining the Conveyor System for Optimal Functionality
In the final phase of the belt conveyor design steps, the focus shifts to implementing, testing, and refining the conveyor system. This meticulous process ensures that the conveyor not only meets design specifications but also operates efficiently and effectively in real-world conditions.
Implementing the Conveyor Belt System
A structured, step-by-step process is critical in the belt conveyor design steps for the successful implementation of the conveyor system. This includes:
- Assembly and Installation: Following detailed instructions for setting up the conveyor components and integrating them into the existing infrastructure.
- System Integration: Ensuring that the conveyor system interfaces seamlessly with other equipment and software systems for automated operations.
- Safety Checks: Conducting initial safety evaluations to comply with all regulatory standards and internal safety protocols.
Rigorous Testing of the Conveyor System
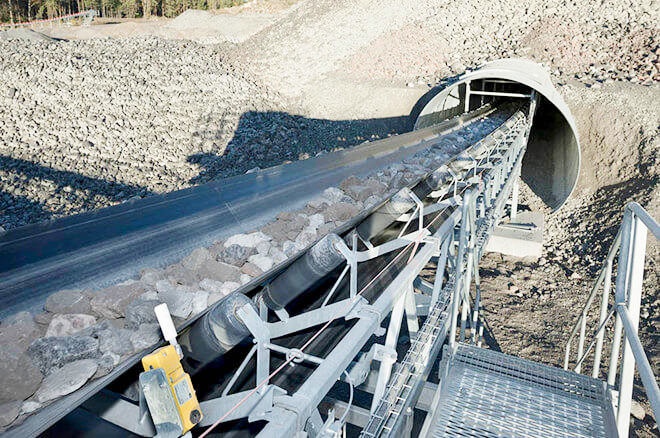
Testing is a pivotal part of the belt conveyor design steps, vital for validating the design and functionality of the system:
- Performance Testing: Running the conveyor under expected load conditions to observe performance and identify any issues in throughput or handling.
- Stress Testing: Applying loads and operational speeds beyond normal levels to test the robustness and endurance of the system.
- Operational Testing: Simulating day-to-day operations to ensure the system performs reliably under typical working conditions.
Refining Based on Testing and Feedback
The final aspect of the belt conveyor design steps involves continuous improvement and refinement:
- Analyzing Test Results: Careful analysis of the data gathered during testing to identify any deviations from expected performance metrics.
- Making Adjustments: Implementing changes to the design or operation based on test results and initial operational feedback.
- Ongoing Optimization: Establishing a protocol for continuous monitoring and refinement, using operational data and feedback to enhance system performance and efficiency over time.
Applications of Belt Conveyor Systems
Industry Applications
Belt conveyor systems are versatile and widely used across various industries due to their efficiency and ability to handle a wide range of materials. Key industry applications include:
- Warehouses
- Material Handling: Belt conveyors streamline the movement of goods within warehouses, ensuring efficient handling and reducing manual labor.
- Order Fulfillment: Facilitates quick and accurate order picking and packing, enhancing the overall productivity of warehouse operations.
- Distribution Centers
- Sorting and Distribution: Essential for sorting and distributing products efficiently, ensuring that items are directed to the correct locations with minimal delays.
- Cross-Docking: Supports cross-docking operations by moving inbound shipments directly to outbound shipping areas, minimizing storage time and enhancing throughput.
- Manufacturing
- Production Lines: Integral to assembly lines, moving parts and products through different stages of the manufacturing process.
- Process Integration: Can be integrated with other machinery and processes, such as robotic arms and quality control stations, to create a seamless production flow.
- Packaging Facilities
- Packaging Process: Used to transport products through various packaging stages, including wrapping, labeling, and sealing.
- Customization: Customizable to handle different packaging requirements, from small items to bulky packages.
- Airports
- Baggage Handling: Critical for efficient baggage check-in, security screening, and claim processes, ensuring that luggage is transported smoothly and securely.
- Passenger Convenience: Enhances passenger experience by reducing wait times and ensuring reliable luggage handling.
- Food Industry
- Food Processing: Designed with sanitary features to meet stringent hygiene standards, ensuring safe and efficient handling of food products.
- Versatile Applications: Used in various stages of food processing, packaging, and distribution, from raw ingredient handling to finished product transportation.
Specific Use Cases
Belt conveyor systems are tailored to handle specific tasks and challenges within these industries. Some common use cases include:
- Transport of Bins, Cardboard Boxes, and Parcels
- Smooth Movement: Ensures the smooth and stable transport of items, preventing damage and maintaining product integrity.
- Flexible Layouts: Adaptable to different layouts, allowing for efficient use of space and optimizing workflow.
- Handling Heavy-Duty Loads
- Robust Construction: Built to handle heavy and bulky items, such as machinery parts, construction materials, and large packages.
- Enhanced Capacity: Designed to support and transport heavy loads efficiently, reducing the need for multiple handling stages and improving throughput.
- Elevation Changes
- Incline and Decline Conveyors: Configured to handle changes in elevation, making it easy to move products between different levels within a facility.
- Space-Saving Solutions: Optimizes vertical space, allowing for efficient use of available area and minimizing the conveyor system’s footprint.
- Handling Irregular Loads
- Custom Adaptations: Designed to accommodate irregularly shaped or fragile items, ensuring safe and stable transport.
- Versatile Applications: Used in industries where products vary in shape and size, such as recycling centers, automotive parts manufacturing, and furniture production.
Explore our conveyor belts – get in touch now!
FAQs about Belt Conveyor Design Steps
Designing a belt conveyor system involves several critical steps to ensure it meets operational requirements efficiently and safely. Initially, one must determine the purpose of the conveyor, which influences the design parameters such as the type of material being transported, the distance the material must travel, and the load capacity. Next, select the appropriate conveyor belt type based on material, durability, and environmental conditions. Important components like motors, rollers, and frames must be chosen with consideration for the load and usage intensity. Designing also requires detailed calculations for belt speed, power requirements, and structural support, often guided by engineering handbooks or software. Finally, incorporate safety features and compliance with industry standards, ensuring the system’s long-term reliability and functionality. Effective design not only considers technical specifications but also operational efficiency and maintenance needs.
The process of a conveyor belt involves several key stages: transport, sorting, and processing. Initially, materials are loaded onto the conveyor belt, which is designed to transport items from one location to another. This movement can be powered by motors or gravity, depending on the system’s design. As materials move along the belt, sorting mechanisms—such as scanners and diverters—may be employed to organize items based on size, weight, or type. In some systems, additional processing such as heating, cooling, or coating occurs directly while the materials are on the belt. Finally, materials are offloaded at the end of the conveyor path, either manually or through automated systems. Throughout this process, continuous monitoring and adjustments ensure the conveyor operates smoothly and meets throughput requirements.
Setting up a conveyor belt system requires careful planning and execution to ensure optimal performance. Start by assembling the structure according to the manufacturer’s instructions, which typically involve constructing the frame, mounting the rollers, and installing the motor and drive units. Once the physical setup is complete, install the conveyor belt itself, ensuring it is properly tensioned and aligned to prevent slippage or tracking issues. Electrical connections must be secured, and control systems set up to manage the operations of the conveyor. After assembly, conduct thorough testing to check for any mechanical issues or misalignments. This includes running the belt at different speeds, checking for smooth transitions, and verifying safety features are functional. Regular maintenance should be scheduled to keep the conveyor in optimal condition after setup.
The methodology of belt conveyor design involves a systematic approach to ensure that the conveyor system is efficient, safe, and tailored to specific operational needs. This methodology starts with a comprehensive analysis of the operational requirements, including understanding the material characteristics, transport distances, and environmental conditions. Based on these factors, engineers select appropriate belt materials, design the conveyor layout, and choose suitable components such as rollers, motors, and frames. Calculations for belt speed, load capacity, and power requirements are conducted to ensure the conveyor’s efficiency and operational safety. The design process also incorporates simulations or modeling to predict how the conveyor will perform under different scenarios. Once the design is finalized, it’s translated into detailed engineering drawings and specifications for construction and assembly, ensuring every aspect of the conveyor meets the defined requirements.
Load Capacity: Determining the maximum weight the conveyor can handle.
Material Characteristics: Considering the type, size, shape, and abrasiveness of the material being conveyed.
Belt Speed: Selecting an appropriate speed for the conveyor to ensure efficient material handling.
Conveyor Length and Width: Designing the conveyor to fit the space and accommodate the required material flow.
Incline or Decline Angle: Deciding if the conveyor will be horizontal or at an angle, and determining the maximum angle for safe operation.
Environment: Considering the operating environment, including temperature, humidity, and potential exposure to chemicals or other harsh conditions.
Maintenance and Accessibility: Ensuring the design allows for easy maintenance and accessibility for repairs and inspections.
Energy Efficiency: Optimizing the design for minimal energy consumption.
Safety Features: Incorporating safety measures to protect workers, such as guards, emergency stop buttons, and safety switches.
Compliance with Standards: Ensuring the design meets industry standards and regulations, such as OSHA or ISO requirements.
Integration with Existing Systems: Designing the conveyor to integrate seamlessly with other equipment and processes in the facility.
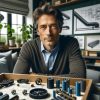
Jordan Smith, a seasoned professional with over 20 years of experience in the conveyor system industry. Jordan’s expertise lies in providing comprehensive solutions for conveyor rollers, belts, and accessories, catering to a wide range of industrial needs. From initial design and configuration to installation and meticulous troubleshooting, Jordan is adept at handling all aspects of conveyor system management. Whether you’re looking to upgrade your production line with efficient conveyor belts, require custom conveyor rollers for specific operations, or need expert advice on selecting the right conveyor accessories for your facility, Jordan is your reliable consultant. For any inquiries or assistance with conveyor system optimization, Jordan is available to share his wealth of knowledge and experience. Feel free to reach out at any time for professional guidance on all matters related to conveyor rollers, belts, and accessories.