Choosing the Best 24 Conveyor Belt
A 24 conveyor belt plays a crucial role in various industries, including manufacturing, mining, and agriculture. These belts are designed to transport materials efficiently, ensuring smooth operations and reduced downtime. The significance of a 24 conveyor belt lies in its ability to handle different types of materials, from heavy loads to delicate items, making it a versatile tool in the industrial sector. Choosing the right 24 conveyor belt can significantly streamline operations, enhancing productivity and overall efficiency. By selecting a belt that meets specific operational requirements, businesses can achieve optimal performance, reduce maintenance costs, and ensure long-term reliability.
What are 24 Conveyor Belts
A 24 conveyor belt is a type of conveyor system that is specifically designed with a 24-inch width. This width is considered standard for many industrial applications, offering a balance between space efficiency and the capacity to move substantial quantities of materials. The primary function of a 24 conveyor belt is to transport materials from one location to another, facilitating smooth and efficient workflow processes.
These belts are integral components in various industries due to their versatility and ability to handle a wide range of materials. The design and construction of a 24 belt conveyor often include features that enhance its durability, flexibility, and efficiency, making it suitable for continuous operation in demanding environments.
Common Uses of 24 Conveyor Belts
24 conveyor belts are widely used across multiple industries, providing a reliable solution for material handling.
- Manufacturing: In manufacturing plants, 24 conveyor belts are used to transport parts and finished products along the production line. This ensures a steady flow of materials and helps in maintaining production efficiency.
- Mining: In the mining industry, these belts are used to move extracted minerals and ores from the mining site to processing plants. They are designed to handle heavy loads and harsh conditions typical of mining operations.
- Agriculture: Farmers use 24 conveyor belts to transport harvested crops, such as grains, fruits, and vegetables, from the fields to storage facilities or processing units. These belts help in reducing manual labor and increasing productivity.
- Food Processing: In food processing plants, conveyor belts are used to move raw ingredients and finished food products through different stages of production, from washing and sorting to packaging. They are designed to meet hygiene standards and ensure food safety.
- Recycling: Recycling facilities use 24 conveyor belts to transport recyclable materials, such as plastics, metals, and paper, through sorting and processing lines. This helps in efficiently managing and processing large volumes of recyclables.
Types of Materials Transported Using 24 Conveyor Belts
The versatility of 24 conveyor belts allows them to handle a wide range of materials. Here are five examples of materials typically transported using these belts:
- Bulk Materials: These include grains, coal, ore, sand, and other loose materials that are transported in large quantities. The 24 conveyor belt’s width and durability make it ideal for moving bulk materials efficiently.
- Packaged Goods: Conveyor belts are used to transport packaged goods, such as boxes, bags, and containers, in industries like retail, logistics, and distribution. The consistent and controlled movement helps in maintaining the integrity of the packages.
- Raw Materials: Industries such as construction and manufacturing use conveyor belts to transport raw materials like steel, lumber, and building materials. This ensures a steady supply of essential materials to production sites.
- Finished Products: Conveyor belts are crucial in moving finished products, including electronics, machinery, and consumer goods, from production lines to packaging and shipping areas. This streamlines the process and enhances productivity.
- Recyclable Materials: Recycling facilities use conveyor belts to sort and transport recyclable materials like plastics, metals, and paper. The belts’ ability to handle different types of materials makes them indispensable in recycling operations.
Benefits of Using 24 Conveyor Belts
Using a 24 conveyor belt offers several advantages that can significantly impact operational efficiency and productivity:
- Increased Throughput: The 24-inch width allows for the transportation of a higher volume of materials compared to narrower belts, increasing overall throughput and efficiency.
- Versatility: The ability to handle a variety of materials makes 24 conveyor belts versatile tools in different industries, from heavy-duty mining operations to delicate food processing tasks.
- Durability: Constructed with high-quality materials, 24 conveyor belts are designed to withstand harsh conditions, heavy loads, and continuous operation, ensuring long-term reliability and reduced downtime.
- Cost-Effectiveness: By streamlining material handling processes, 24 conveyor belts can reduce labor costs and increase production efficiency, leading to overall cost savings for businesses.
- Safety: These conveyor belts are designed with safety features that minimize the risk of accidents and injuries, promoting a safer working environment for employees.
Factors to Consider When Choosing a 24 Conveyor Belt
When selecting a 24 conveyor belt for your operations, it’s important to consider several factors to ensure you choose the right belt for your specific needs:
- Material Compatibility: Ensure that the conveyor belt material is compatible with the type of materials you will be transporting. For instance, food-grade belts are necessary for food processing applications.
- Load Capacity: Consider the maximum load the belt will need to handle. This includes the weight and volume of the materials to ensure the belt can operate efficiently without overloading.
- Environmental Conditions: Take into account the operating environment, including temperature, humidity, and exposure to chemicals or abrasive materials. Choose a belt that can withstand these conditions without degrading.
- Maintenance Requirements: Evaluate the maintenance needs of the conveyor belt. Some belts may require regular cleaning and lubrication, while others are designed for low-maintenance operation.
- Cost: Consider the overall cost of the conveyor belt, including initial purchase price, installation, and ongoing maintenance costs. Balance these costs with the expected lifespan and performance of the belt to determine the best value for your investment.
Understanding the intricacies of a 24 conveyor belt is essential for making informed decisions about its use in various industrial applications. These belts offer a versatile and efficient solution for material handling, capable of transporting a wide range of materials in different environments. By considering the specific requirements of your operation and the characteristics of the conveyor belt, you can select a system that enhances productivity, reduces costs, and ensures long-term reliability.
Types of 24 Conveyor Belts
When it comes to selecting a 24 conveyor belt, understanding the various types available and their specific features is crucial for optimizing performance in different applications. The versatility of 24 conveyor belts makes them suitable for a wide range of industries, from manufacturing to mining, and understanding the nuances of each type can help in choosing the right one for your needs.
Overview of Different Types of 24″ Conveyor Belts
- Rubber Conveyor Belts Rubber conveyor belts are among the most commonly used types in various industries due to their durability and versatility. These belts are made from natural or synthetic rubber and are designed to withstand heavy loads and harsh conditions. They are ideal for applications where the belt needs to resist abrasion, impact, and wear, such as in mining and construction.
- Chevron Top Conveyor Belts Chevron top conveyor belts are characterized by their unique V-shaped patterns on the surface. These patterns, or chevrons, provide extra grip, making these belts suitable for transporting loose materials up inclined surfaces. The chevrons help prevent materials from slipping backward, ensuring efficient and safe transportation. Industries such as agriculture and quarrying commonly use Chevron top belts.
- Crescent Top Conveyor Belts Crescent top conveyor belts feature a series of crescent-shaped ridges across the belt’s surface. These ridges enhance grip and are particularly effective for handling materials that require gentle handling to avoid damage. Crescent top belts are often used in the food processing industry to move delicate items like fruits and vegetables.
- PVC Conveyor Belts PVC conveyor belts are known for their resistance to oil, grease, and chemicals. These belts are lightweight and easy to maintain, making them ideal for industries such as food processing, packaging, and pharmaceuticals. The smooth surface of PVC belts ensures easy cleaning and hygiene, which is critical in environments where contamination must be minimized.
- Modular Conveyor Belts Modular conveyor belts are constructed from interlocking plastic modules, creating a versatile and customizable conveyor solution. These belts can be configured to various widths and lengths, making them suitable for complex conveyor systems. They are commonly used in industries like automotive manufacturing and material handling, where flexibility and adaptability are essential.
Discussion on Special Features
Different 24 conveyor belts come with special features that enhance their performance in specific applications.
- Smooth Top Conveyor Belts Smooth top conveyor belts have a flat, even surface that provides excellent support for materials being transported. This feature is ideal for applications where the material needs to be stable and evenly distributed, such as in packaging and assembly lines. The smooth surface also makes these belts easy to clean, which is beneficial in industries requiring high levels of hygiene.
- Textured Back Conveyor Belts Textured back conveyor belts have a patterned or roughened surface on the underside of the belt. This texture increases friction between the belt and the conveyor rollers, preventing slippage and ensuring smooth operation. Textured back belts are useful in applications where the belt needs to handle high-speed or heavy-load conditions, such as in distribution centers and logistics.
- Cleated Conveyor Belts Cleated conveyor belts are equipped with raised sections, or cleats, across the belt’s surface. These cleats help in transporting loose or granular materials up steep inclines by preventing material rollback. Cleated belts are commonly used in agriculture for moving grains and seeds, in construction for transporting sand and gravel, and in recycling facilities for sorting materials.
- Perforated Conveyor Belts Perforated conveyor belts have holes or slots cut into the belt surface, allowing air or liquids to pass through. This feature is particularly useful in applications requiring drainage or air circulation, such as in food processing, where products may need to be washed or dried on the conveyor. Perforated belts also help reduce the belt’s overall weight, improving energy efficiency.
- Heat-Resistant Conveyor Belts Heat-resistant conveyor belts are designed to withstand high temperatures, making them suitable for transporting hot materials or operating in environments with elevated temperatures. These belts are often used in industries such as foundries, glass manufacturing, and metalworking, where materials can reach extreme temperatures. The heat-resistant properties ensure the belt maintains its integrity and performance despite prolonged exposure to heat.
Choosing the Right 24 Conveyor Belt
When selecting a 24 conveyor belt, it’s essential to consider the specific needs of your operation. The right belt type will depend on factors such as the nature of the material being transported, the operating environment, and the required belt features.
- Material Type Different materials require different belt types. For instance, rubber conveyor belts are ideal for abrasive and heavy materials, while PVC belts are better suited for light, oily, or chemically exposed environments.
- Load and Speed The load capacity and speed of the conveyor system are critical factors. Textured back belts are beneficial for high-speed operations, while cleated belts are necessary for steep inclines and heavy loads.
- Environmental Conditions The operating environment, including temperature, humidity, and exposure to chemicals, plays a significant role in belt selection. Heat-resistant belts are essential for high-temperature environments, while perforated belts are useful in applications requiring air or liquid flow.
- Maintenance and Longevity Consider the maintenance requirements and expected lifespan of the belt. Some belts may require more frequent maintenance but offer longer durability, while others may be easier to maintain but have a shorter lifespan.
- Cost-Effectiveness Balance the initial cost of the belt with its performance and maintenance requirements. A higher-priced belt may offer better performance and longer lifespan, providing better value in the long run.
Understanding the different types of 24 belt conveyors and their special features can help you make an informed decision when selecting the right belt for your application. Whether you need a belt for transporting heavy loads
Factors Affecting 24 Conveyor Belt Cost
Understanding the various factors that influence the cost of a 24 conveyor belt is essential for making informed purchasing decisions. Several elements contribute to the overall price, including the materials used, the length of the belt, and any special features or customizations. By comprehensively examining these factors, businesses can better budget and select the appropriate conveyor belt for their needs.
Material
The material of the 24 conveyor belt is a primary factor affecting its cost. Different materials offer various benefits and are suited to different applications, which can significantly influence the price.
- Rubber: Rubber conveyor belts are durable and ideal for heavy-duty applications. The cost of rubber belts is typically higher due to their robustness and ability to withstand harsh conditions. However, their longevity and reliability often justify the higher initial investment.
- PVC: PVC belts are more affordable compared to rubber belts and are commonly used in industries requiring resistance to oil, grease, and chemicals. The smooth surface of PVC belts also makes them easy to clean, which is crucial for maintaining hygiene in food processing and pharmaceutical industries.
- PU (Polyurethane): PU conveyor belts are known for their high resistance to abrasion, cuts, and impacts, making them suitable for food and packaging industries. They are more expensive than PVC belts but offer superior performance and longevity.
- Modular Plastic: Modular plastic belts are composed of interlocking plastic segments, which provide flexibility and ease of maintenance. These belts can be more costly due to their modular design and the ability to customize the belt layout.
- Metal: Metal conveyor belts, made from stainless steel or other metals, are used in high-temperature applications and environments requiring extreme durability. These belts are generally the most expensive due to their material properties and the precision required in their manufacturing.
Length
The length of the 24 conveyor belt directly affects the overall cost. Longer belts require more material and labor to produce, which increases the price. Additionally, longer belts may necessitate additional support structures and maintenance considerations.
- Standard Lengths: Conveyor belts are often sold in standard lengths, such as 100 feet or 250 feet. Purchasing belts in these standard lengths can sometimes result in cost savings due to economies of scale in manufacturing.
- Custom Lengths: Custom-length belts tailored to specific applications may incur additional costs. Customization involves precise measurements and potential alterations to the belt’s design, which can increase both material and labor costs.
- Jointing and Splicing: Longer conveyor belts may require jointing or splicing to ensure seamless operation. The process of jointing can add to the overall cost, depending on the type of joint and the labor involved.
Special Features
Special features and customizations can significantly impact the cost of a 24 conveyor belt. These features are designed to enhance performance, durability, and suitability for specific applications.
- Cleats: Adding cleats to a conveyor belt can help in transporting materials up steep inclines by preventing rollback. The additional material and labor required to install cleats increase the overall cost.
- Perforations: Perforated belts, with holes or slots for drainage or airflow, are often more expensive due to the additional processing required to create the perforations.
- Textured Surface: Textured surfaces, such as a rough top or chevron pattern, can provide extra grip and prevent slippage. These textures require specialized manufacturing processes, which can increase costs.
- Heat Resistance: Belts designed to withstand high temperatures are made from specialized materials and undergo treatments to enhance their heat resistance. This results in higher costs compared to standard belts.
- Food-Grade Certifications: Conveyor belts used in food processing must meet stringent hygiene and safety standards. Food-grade belts are often more expensive due to the materials used and the certification process required to ensure compliance with industry regulations.
Cost Per Meter
Understanding the cost per meter of a 24 conveyor belt is crucial for accurate budgeting and financial planning. The cost per meter can vary widely based on the factors mentioned above, but having a general idea can help businesses estimate their expenses.
- Rubber Belts: The cost of rubber conveyor belts can range from $25 to $50 per meter, depending on the quality and thickness of the rubber.
- PVC Belts: PVC conveyor belts are generally more affordable, with costs ranging from $15 to $30 per meter.
- PU Belts: Polyurethane belts fall in the mid-to-high price range, typically costing between $20 and $40 per meter.
- Modular Plastic Belts: The cost of modular plastic belts can vary significantly based on customization but generally falls between $30 and $60 per meter.
- Metal Belts: Metal conveyor belts are the most expensive, with costs often exceeding $100 per meter due to the material and manufacturing precision required.
Several factors influence the cost of a 24 conveyor belt, including the material, length, and special features. By understanding these factors, businesses can make informed decisions that balance cost with performance and suitability for their specific applications. Whether you need a durable rubber belt for heavy-duty operations or a food-grade PVC belt for a clean environment, considering these elements will help you choose the right conveyor belt and manage your budget effectively.
Buying New vs. Used 24 Conveyor Belts
When considering the purchase of a 24 conveyor belt, deciding between a new or used belt can significantly impact your budget, operational efficiency, and overall satisfaction. This section will compare the advantages and disadvantages of buying new versus used 24 conveyor belts, focusing on cost, availability, and suitability for different operations. Additionally, we will provide insights into where to find used conveyor belts for sale to help those looking to save on costs.
Cost Comparison
One of the primary factors in deciding between a new and used 24 conveyor belt is cost. New conveyor belts are typically more expensive than used ones, but they come with warranties and the assurance of optimal performance. Used belts, on the other hand, offer significant cost savings but may require more frequent maintenance and have a shorter lifespan.
Aspect | New 24 Conveyor Belt | Used 24 Conveyor Belt |
---|---|---|
Initial Cost | Higher ($1,000 - $5,000) | Lower ($200 - $2,000) |
Warranty | Yes (1-5 years) | No or Limited |
Maintenance | Lower Initial Maintenance | Higher Initial Maintenance |
Lifespan | Longer (10-15 years) | Shorter (3-7 years) |
Reliability | High (consistent performance) | Variable (depends on condition) |
Customization | Available for specific needs | Limited to existing features |
Availability
The availability of new versus used 24 conveyor belts can also influence the decision. New belts are readily available from manufacturers and suppliers, with the possibility of customization to meet specific operational needs. Used belts, while less readily available, can often be found through various channels such as auctions, surplus equipment dealers, and online marketplaces.
Aspect | New 24 Conveyor Belt | Used 24 Conveyor Belt |
---|---|---|
Lead Time | Shorter (ready stock) | Variable (depends on market) |
Customization Options | Extensive (tailored to need) | Limited (pre-existing specs) |
Supplier Availability | High (manufacturers, distributors) | Moderate (dealers, online) |
Condition | New (perfect condition) | Varies (used, refurbished) |
Suitability for Different Operations
The suitability of a new or used 24 conveyor belt for specific operations depends on the operational requirements, including the type of material being transported, the environment, and the expected lifespan of the belt.
Aspect | New 24 Conveyor Belt | Used 24 Conveyor Belt |
---|---|---|
Heavy-Duty Applications | Ideal (designed for durability) | Depends on previous usage |
Hygiene-Sensitive Industries | Best (meets industry standards) | May require thorough cleaning |
Temporary Projects | Costlier but reliable | More cost-effective option |
Customization Needs | Fully customizable | Limited to existing features |
Advantages of Buying New 24 Conveyor Belts
- Optimal Performance: New conveyor belts are designed to provide consistent and reliable performance, ensuring smooth operations.
- Warranty and Support: New belts come with warranties, offering peace of mind and protection against manufacturing defects.
- Customization: Manufacturers can tailor new belts to meet specific operational requirements, including unique sizes, materials, and features.
- Longer Lifespan: New belts typically have a longer lifespan and require less frequent maintenance, reducing long-term operational costs.
- Compliance: New belts are built to meet current industry standards and regulations, ensuring compliance and safety.
Advantages of Buying Used 24 Conveyor Belts
- Cost Savings: Used conveyor belts are significantly cheaper than new ones, making them an attractive option for budget-conscious buyers.
- Immediate Availability: Used belts can often be sourced quickly from local dealers or online marketplaces, reducing lead times.
- Sustainability: Purchasing used belts supports recycling and reduces waste, contributing to environmental sustainability.
- Suitable for Short-Term Projects: Used belts are ideal for temporary or short-term projects where long-term durability is less critical.
- Testing Before Purchase: Buyers can inspect and test used belts before purchasing to ensure they meet operational requirements.
Where to Find Used 24 Conveyor Belts for Sale Near Me
Finding used 24 conveyor belts for sale can be achieved through various channels:
- Online Marketplaces: Websites like eBay, Craigslist, and Alibaba offer a range of used conveyor belts from different sellers.
- Industrial Auctions: Auctions are a great place to find used industrial equipment, including conveyor belts, at competitive prices.
- Surplus Equipment Dealers: Many dealers specialize in surplus and used industrial equipment, offering a variety of conveyor belts.
- Local Classifieds: Check local classified ads in newspapers and online platforms for listings of used conveyor belts for sale.
- Industry Contacts: Networking with industry peers and attending trade shows can provide leads on where to find used conveyor belts.
Choosing between new and used 24 conveyor belts involves weighing the advantages and disadvantages of each option. New belts offer optimal performance, warranties, and customization, making them ideal for long-term and critical applications. Used belts, on the other hand, provide significant cost savings and are suitable for temporary projects or when budget constraints are a concern. By understanding the factors affecting the cost, availability, and suitability of new and used conveyor belts, businesses can make informed decisions that best meet their operational needs and budget constraints.
Price Guide: 24 Conveyor Belt for Sale
When considering the purchase of a 24 conveyor belt, understanding the pricing landscape is crucial for making informed decisions. Whether you are looking for a new or used conveyor belt, various factors influence the cost, including material, length, condition, and special features. This section provides a comprehensive pricing guide for new and used 24 conveyor belts, highlighting bulk roll options and market trends to help you budget effectively.
General Pricing Guide for New 24 Conveyor Belts
The price of new 24 conveyor belts can vary significantly based on the material and specifications. Here’s a breakdown of the general pricing range:
- Rubber Conveyor Belts: Rubber belts are known for their durability and versatility. The cost of new rubber 24 conveyor belts typically ranges from $25 to $50 per linear foot. This price can increase with added features like heat resistance or abrasion resistance.
- PVC Conveyor Belts: PVC belts are often used in industries requiring chemical resistance and easy cleaning. Prices for new PVC 24 conveyor belts generally range from $15 to $30 per linear foot, making them a more affordable option compared to rubber belts.
- Polyurethane (PU) Conveyor Belts: PU belts are highly durable and resistant to abrasion, making them suitable for food processing and packaging. The cost of new PU 24 conveyor belts typically falls between $20 and $40 per linear foot.
- Modular Plastic Conveyor Belts: These belts offer flexibility and ease of maintenance due to their interlocking design. Prices for new modular plastic 24 belt conveyors can range from $30 to $60 per linear foot, depending on the complexity and customization required.
- Metal Conveyor Belts: Metal belts, often made from stainless steel, are used in high-temperature and heavy-duty applications. New metal 24 conveyor belts are the most expensive, with prices starting around $100 per linear foot and going upwards depending on the specific requirements.
General Pricing Guide for Used 24″ Conveyor Belts
Used 24 conveyor belts are a cost-effective alternative for those looking to save money. The prices for used belts depend on their condition, length, and material. Here’s an overview of the typical pricing:
- Rubber Conveyor Belts: Used rubber belts can be found for $10 to $25 per linear foot. The condition and previous usage of the belt significantly influence the price. Refurbished belts with minor wear can be more expensive than heavily used ones.
- PVC Conveyor Belts: Used PVC belts are generally available for $7 to $20 per linear foot. These belts are often in good condition due to their chemical-resistant properties, which help them withstand wear and tear.
- Polyurethane (PU) Conveyor Belts: The cost of used PU belts typically ranges from $12 to $30 per linear foot. These belts are durable, and finding them in good condition is relatively common.
- Modular Plastic Conveyor Belts: Used modular plastic belts can range from $20 to $40 per linear foot. Their modular design makes them easier to refurbish and maintain, often resulting in good quality used options.
- Metal Conveyor Belts: Used metal belts are available from $50 per linear foot and can go up to $80 or more, depending on their condition and specific applications.
Bulk Roll Options for 24″ Conveyor Belts
Purchasing 24 conveyor belts in bulk rolls can offer significant cost savings, especially for large-scale operations. Here’s a look at the pricing and advantages of buying bulk rolls:
- 100’ Rolls: Bulk rolls of 24 conveyor belts are often available in 100-foot lengths. For rubber belts, a 100-foot roll can cost between $2,500 and $5,000. PVC belts in the same length might range from $1,500 to $3,000. PU belts can cost between $2,000 and $4,000, while modular plastic belts may range from $3,000 to $6,000. Metal belts are the priciest, starting around $10,000 for a 100-foot roll.
- 750’ Rolls: For larger operations, 750-foot rolls provide a bulk purchase option. Rubber conveyor belts in this length can cost between $18,000 and $35,000. PVC belts might range from $12,000 to $25,000, while PU belts can cost between $15,000 and $30,000. Modular plastic belts are priced between $22,000 and $45,000. Metal belts are significantly more expensive, often exceeding $70,000 for a 750-foot roll.
Market Trends and Considerations
Several market trends and considerations can affect the price of 24 conveyor belts:
- Material Costs: The cost of raw materials, such as rubber, PVC, and metal, fluctuates based on market conditions. These changes directly impact the price of conveyor belts.
- Supply and Demand: High demand for conveyor belts in specific industries, like mining and manufacturing, can drive up prices. Conversely, an oversupply can lead to price reductions.
- Technological Advancements: Innovations in conveyor belt technology, such as improved durability and energy efficiency, can influence prices. Newer, more advanced belts tend to be more expensive due to the added benefits they offer.
- Global Economic Factors: Economic conditions, including tariffs, trade policies, and currency exchange rates, can affect the cost of importing and exporting conveyor belts, thereby influencing prices.
- Environmental Regulations: Stricter environmental regulations can lead to increased production costs for conveyor belts, particularly those requiring specific certifications for safe use in food processing or chemical handling.
Understanding the price dynamics of new and used 24 conveyor belts is essential for making informed purchasing decisions. While new belts offer the advantage of warranties and customization, used belts provide significant cost savings and immediate availability. Bulk roll options can further reduce costs for large-scale operations. By considering factors such as material, length, condition, and market trends, businesses can budget effectively and select the most suitable conveyor belt for their needs.
Finding the Right Supplier for 24 Conveyor Belt
Selecting the right supplier for a 24 conveyor belt is crucial to ensure that you receive a high-quality product that meets your operational needs. The right supplier can make a significant difference in the performance, durability, and efficiency of your conveyor system. This section provides tips on what to look for in a supplier, how to locate suppliers nearby, and important questions to ask when comparing options.
Tips on Selecting the Right Supplier
When choosing a supplier for a 24 conveyor belt, consider the following factors to ensure you select a reliable and high-quality provider:
Quality of Products:
- Material Quality: Ensure the supplier offers conveyor belts made from high-quality materials that match your specific requirements. For example, rubber belts should be durable and abrasion-resistant, while PVC belts should be resistant to chemicals and easy to clean.
- Manufacturing Standards: Look for suppliers that adhere to industry standards and certifications, such as ISO 9001, which indicate a commitment to quality and continuous improvement.
Service and Support:
- Technical Support: A good supplier should provide comprehensive technical support, including installation guidance, troubleshooting, and maintenance advice. This support ensures that you can quickly resolve any issues that arise.
- Customer Service: Evaluate the supplier’s customer service responsiveness and willingness to address your concerns. Reliable customer service can help you navigate any challenges and ensure smooth operation.
Reliability:
- Track Record: Research the supplier’s track record in the industry. Look for reviews, testimonials, and case studies that demonstrate their reliability and success in delivering high-quality products.
- Delivery Time: Assess the supplier’s ability to meet delivery deadlines. Timely delivery is crucial to avoid disruptions in your operations.
Customization Options:
- Tailored Solutions: Choose a supplier that offers customization options to tailor the 24 conveyor belt to your specific needs. This includes custom lengths, widths, and features such as cleats or textured surfaces.
- Flexibility: The supplier should be flexible in accommodating your unique requirements and able to provide bespoke solutions.
Pricing and Value:
- Competitive Pricing: Compare prices among different suppliers to ensure you are getting competitive rates. However, avoid choosing based solely on price; consider the overall value, including quality and support.
- Cost Transparency: A trustworthy supplier should provide transparent pricing without hidden fees. Request detailed quotes to understand the cost breakdown.
Suggestions on How to Locate Suppliers Nearby
Finding local suppliers for a 24 conveyor belt can offer benefits such as faster delivery times and the ability to inspect products before purchase. Here are some suggestions on how to locate suppliers nearby:
Online Directories:
- Industry Portals: Use online industry portals and directories, such as ThomasNet or Yellow Pages, to search for local suppliers of conveyor belts. These platforms often include reviews and contact information.
- Manufacturer Websites: Visit the websites of major conveyor belt manufacturers. Many have distributor locator tools that allow you to find authorized suppliers near your location.
Trade Shows and Exhibitions:
- Industry Events: Attend trade shows and exhibitions related to material handling and manufacturing. These events provide opportunities to meet suppliers, see product demonstrations, and discuss your needs in person.
- Networking: Use these events to network with industry professionals who can recommend reliable suppliers.
Local Business Associations:
- Chambers of Commerce: Contact your local Chamber of Commerce or business associations. They can provide information on reputable suppliers in your area and facilitate introductions.
- Industry Groups: Join industry-specific groups and associations. Members can offer insights and recommendations based on their experiences.
Referrals and Recommendations:
- Peer Recommendations: Ask for referrals from industry peers and colleagues who have purchased conveyor belts. Their firsthand experiences can help you identify trustworthy suppliers.
- Customer Reviews: Read customer reviews and testimonials online to gauge the reputation and reliability of potential suppliers.
Online Marketplaces:
- B2B Platforms: Explore B2B platforms like Alibaba, Amazon Business, and eBay. These marketplaces often have listings from local suppliers and allow you to compare products and prices easily.
- Social Media: Use social media platforms, such as LinkedIn, to connect with suppliers and industry professionals. Join relevant groups and participate in discussions to gather information.
Questions to Ask When Comparing Options
When comparing suppliers, asking the right questions can help you make an informed decision. Here are five key questions to consider:
What is the quality and origin of the materials used in your 24 conveyor belts?
- This question ensures that the supplier uses high-quality materials and helps you understand the durability and suitability of their products for your needs.
Do you offer any customization options for the 24 conveyor belt?
- Understanding the supplier’s ability to customize the belt to your specific requirements is crucial for ensuring it meets your operational needs.
What kind of technical support and after-sales service do you provide?
- Assessing the level of support offered can help you determine how well the supplier will assist you in case of issues or maintenance needs.
Can you provide references or case studies from previous customers?
- References and case studies can give you insight into the supplier’s track record and reliability, helping you gauge their performance and customer satisfaction.
What are the delivery times and payment terms for your 24 conveyor belts?
- Clarifying delivery times ensures that the supplier can meet your schedule, while understanding payment terms helps you plan your budget effectively.
Finding the right supplier for a 24 conveyor belt involves careful consideration of factors such as quality, service, reliability, customization options, and pricing. By following the tips outlined in this section and asking the right questions, you can identify a supplier that meets your needs and provides high-quality conveyor belts to enhance your operations. Additionally, utilizing various methods to locate local suppliers can expedite the purchasing process and ensure you receive timely and effective support.
FAQs About 24 Conveyor Belt
The term “M 24 conveyor belt” refers to a specific grade of rubber conveyor belt that is designed to handle heavy-duty applications and harsh conditions. The “M” in M 24 stands for “mining,” indicating that these belts are suitable for mining and other industrial applications where durability and resistance to wear and tear are crucial. The number “24” represents the conveyor belt tensile strength, which is typically 24 MegaPascals (MPa). M 24 conveyor belts are made from a blend of natural and synthetic rubber, providing excellent resistance to abrasion, cuts, and impacts. They are widely used in industries such as mining, quarrying, and construction, where they transport bulk materials like coal, ores, and aggregates over long distances and under challenging conditions.
Conveyor belts come in a variety of standard sizes to accommodate different industrial applications. The width of conveyor belts typically ranges from 300 mm (12 inches) to 2400 mm (94 inches), with common widths including 400 mm (16 inches), 500 mm (20 inches), 600 mm (24 inches), 800 mm (32 inches), 1000 mm (40 inches), and 1200 mm (48 inches). The thickness of the belts can vary based on the type and intended use, ranging from 3 mm to 25 mm. Standard lengths can be adjusted according to the requirements of the conveyor system, but they often come in rolls of 50 meters, 100 meters, or even 200 meters. These sizes ensure that conveyor belts can be tailored to specific industrial needs, providing efficient and reliable material handling solutions.
The standard length of a conveyor belt varies depending on the application and the manufacturer. Conveyor belts are typically sold in rolls, and the length can be customized to fit the specific requirements of the conveyor system. Commonly, conveyor belts come in rolls of 50 meters (164 feet), 100 meters (328 feet), or 200 meters (656 feet). However, for larger industrial applications, belts can be made to longer lengths. The standard length also depends on the type of belt and the material it is designed to transport. Custom lengths can be ordered to match the exact specifications of the conveyor system, ensuring seamless integration and efficient operation. Proper measurement and consideration of the conveyor layout are essential when determining the appropriate belt length.
The M24 conveyor belt is designed to withstand a wide range of temperatures, making it suitable for various industrial applications. The typical temperature range for an M24 belt is from -20°C (-4°F) to +60°C (+140°F). This range ensures that the belt can perform effectively in both cold and hot environments, maintaining its structural integrity and performance under different operating conditions. The rubber compound used in M24 belts provides excellent resistance to heat, making it suitable for transporting materials in industries such as mining, construction, and processing plants where high temperatures are common. However, for extreme temperature applications, it is essential to consult with the manufacturer to ensure that the specific M24 belt selected meets the required temperature specifications.
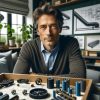
Jordan Smith, a seasoned professional with over 20 years of experience in the conveyor system industry. Jordan’s expertise lies in providing comprehensive solutions for conveyor rollers, belts, and accessories, catering to a wide range of industrial needs. From initial design and configuration to installation and meticulous troubleshooting, Jordan is adept at handling all aspects of conveyor system management. Whether you’re looking to upgrade your production line with efficient conveyor belts, require custom conveyor rollers for specific operations, or need expert advice on selecting the right conveyor accessories for your facility, Jordan is your reliable consultant. For any inquiries or assistance with conveyor system optimization, Jordan is available to share his wealth of knowledge and experience. Feel free to reach out at any time for professional guidance on all matters related to conveyor rollers, belts, and accessories.